1
/
of
12
PayPal, credit cards. Download editable-PDF & invoice in 1 second!
GB 19156-2003 English PDF
GB 19156-2003 English PDF
Regular price
$85.00 USD
Regular price
Sale price
$85.00 USD
Unit price
/
per
Shipping calculated at checkout.
Couldn't load pickup availability
Delivery: 3 seconds. Download true-PDF + Invoice.
Get QUOTATION in 1-minute: Click GB 19156-2003
Historical versions: GB 19156-2003
Preview True-PDF (Reload/Scroll if blank)
GB 19156-2003: General specifications for fire monitors
GB/T 16508.1-2013
NATIONAL STANDARD OF THE
PEOPLE’S REPUBLIC OF CHINA
ICS 27.060.30
J 98
Shell Boilers -- Part 1: General Requirements
ISSUED ON: DECEMBER 31, 2013
IMPLEMENTED ON: JULY 1, 2014
Issued by: General Administration of Quality Supervision, Inspection and
Quarantine;
Standardization Administration Committee.
Table of Contents
Foreword ... 3
Introduction ... 4
1 Scope ... 5
2 Normative References ... 5
3 Terms and Definitions ... 7
4 Qualification and responsibilities ... 10
5 Definition of the Boiler Range ... 12
6 General Technical Requirements ... 18
7 Steam-water Quality ... 27
8 Requirements for Energy Conservation and Environment Protection ... 27
Appendix A (Normative) Declaration of Conformity and Revision for the
Standard ... 28
Shell Boilers -- Part 1: General Requirements
1 Scope
1.1 This Part of GB/T 16508 specifies the general technical requirements for the
material, design, fabrication, inspection, safety accessories, combustion system,
installation, operation, energy-saving and environment protection of stationary shell
boilers.
1.2 This Part is applicable to the stationary pressure shell boilers with water as
medium, evaporating heating surface mainly arranged on shell OR boiler furnace
arranged in shell which meet the following conditions:
a) Steam boiler of which the water volume at the design normal water level is
greater than or equal to 30L, and the rated steam pressure is greater than or
equal to 0.1MPa (gauge pressure; the same below);
b) Hot-water boiler of which the rated outflow pressure is greater than or equal to
0.1Mpa, or the rated power is greater than or equal to 0.1MW.
1.3 This Part is not applicable to the following equipment:
a) Portable boiler (e.g. marine boiler, railway locomotive traction boiler);
b) Cooling devices required for equipment and process flow cooling;
c) Boiler for military use.
2 Normative References
The following referenced documents are indispensable for the application of this
document. For dated references, only the edition cited applies. For undated
references, the latest edition of the normative document (including any amendments)
applies.
GB/T 1576 Water Quality for Industrial Boilers
GB/T 1921 Parameters for Industrial Steam Boilers
GB/T 3166 Parameters for Hot Water Boilers
GB/T 2900.48 Electrotechnical Terminology of Boilers
GB 8978 Integrated Wastewater Discharge Standard
GB/T 10180 Thermal Performance Test Code for Industrial Boilers
GB/T 10863 Thermal Test Method for Gas Pass Heat Recovery Boiler
GB/T 12145 Quality Criterion of Water and Steam for Generating Unit and Steam
Power Equipment
GB 12348 Standard of Noise at Boundary of Industrial Enterprises
GB 13271 Emission Standard of Air Pollutants for Boiler
GB/T 16507 Water-tube Boilers
GB/T 16508.2 Shell Boilers - Part 2: Material
GB/T 16508.3 Shell Boilers - Part 3: Design and Strength Calculation
GB/T 16508.4 Shell Boilers - Part 4: Fabrication, Inspection and Acceptance
GB/T 16508.5 Shell Boilers - Part 5: Safety Appurtenances and Instruments
GB/T 16508.6 Shell Boilers - Part 6: Combustion Systems
GB/T 16508.7 Shell Boilers - Part 7: Installation
GB/T 16508.8 Shell Boilers - Part 8: Operation
GB/T 22395 Specification for Design of Boiler Steel Structures
GB 24747 Safety Technology Conditions for Heat Transfer Fluids
JB/T 6734 Strength Calculation Method for Boiler Fillet Weld
JB/T 6735 Calculation Method for Strength of Boiler Hanger Rod
NB/T 47013
(JB/T 4730)
Nondestructive Testing of Pressure Equipment
3.5
Safety release pressure
The pressure of safety valve upon releasing, also referred to as set pressure of safety
valve.
3.6
Hydrostatic test pressure
The pressure applied when conducting hydrostatic test for boiler system or pressure
component (part) as required.
3.7
Rated temperature
The working fluid temperature at the outlet which shall be ensured for long-term
continuous operation under specified design conditions.
3.8
Calculating temperature
The metal temperature of part set under normal operating conditions (the mean
temperature along the metal section of part).
3.9
Test temperature
The metal temperature of pressure part in pressure test.
3.10
Required thickness
The thickness of pressure part determined according to theoretical calculation formula.
Where necessary, thickness required by other loads shall also be calculated.
3.11
Design thickness
3.18
The highest fire line
The highest point of water-side under the erosion of flame or high-temperature flue
gas on the evaporating heating surface of boiler.
3.19
Component space
It means that adequate space must be provided between adjacent parts of different
wall temperatures on the tube plate so as to avoid overlarge temperature difference
stress.
4 Qualification and responsibilities
4.1 Qualification
4.1.1 Organization qualification
The fabrication, inspection, testing and installation organizations of boilers shall obtain
corresponding special equipment license qualification according to the requirements
of "Regulations on Safety Supervision over Special Equipment".
4.1.2 Personnel qualification
4.1.2.1 The welding personnel of the boiler pressure parts shall be assessed
according to the requirements of relevant safety technical codes such as
"Examination Rules for Welding Operators of Special Equipment" and may be
engaged in the welding work within the acceptable project scope within the period of
validity after obtaining the "Special Equipment Operator Certificate".
4.1.2.2 The non-destructive inspection personnel may only undertake
non-destructive testing with type and technical level corresponding to the qualification
certificate after obtaining the special equipment operator qualification certificate
according to the requirements of relevant technical codes.
4.1.2.3 The operation personnel of boiler using organization shall be provided with
corresponding qualification required by safety technical codes.
4.2 Responsibilities
main pressure part, welding quality certificate, non-destructive testing report
and hydrostatic test report, etc.);
e) Installation instructions and operating instructions of boiler;
f) Significant design change information of pressure part;
g) Water flow diagram and hydrodynamic calculation sheet of hot-water boiler
(except natural-circulation shell boiler);
h) Fabrication, supervision and inspection certificate;
i) Technical information concerned with safety and energy conservation.
4.2.2.5 For the fabricated boilers within the design service life, the fabrication
organization shall not only preserve the above technical information of delivery, but
also properly preserve the following technical documents for future reference:
a) Boiler design detail;
b) Material utilization list;
c) Fabrication process diagram or fabrication process card;
d) Welding process document;
e) Heat treatment process document;
f) Inspection and test record during fabrication process and after completion;
g) Fabrication, supervision and inspection certificate;
h) Permissible project selection record, etc.
4.2.3 Installation Organization
The installation organization shall carry out installation construction according to
relevant safety technical codes and standards as well as the boiler drawings and
installation instructions provided by...
Get QUOTATION in 1-minute: Click GB 19156-2003
Historical versions: GB 19156-2003
Preview True-PDF (Reload/Scroll if blank)
GB 19156-2003: General specifications for fire monitors
GB/T 16508.1-2013
NATIONAL STANDARD OF THE
PEOPLE’S REPUBLIC OF CHINA
ICS 27.060.30
J 98
Shell Boilers -- Part 1: General Requirements
ISSUED ON: DECEMBER 31, 2013
IMPLEMENTED ON: JULY 1, 2014
Issued by: General Administration of Quality Supervision, Inspection and
Quarantine;
Standardization Administration Committee.
Table of Contents
Foreword ... 3
Introduction ... 4
1 Scope ... 5
2 Normative References ... 5
3 Terms and Definitions ... 7
4 Qualification and responsibilities ... 10
5 Definition of the Boiler Range ... 12
6 General Technical Requirements ... 18
7 Steam-water Quality ... 27
8 Requirements for Energy Conservation and Environment Protection ... 27
Appendix A (Normative) Declaration of Conformity and Revision for the
Standard ... 28
Shell Boilers -- Part 1: General Requirements
1 Scope
1.1 This Part of GB/T 16508 specifies the general technical requirements for the
material, design, fabrication, inspection, safety accessories, combustion system,
installation, operation, energy-saving and environment protection of stationary shell
boilers.
1.2 This Part is applicable to the stationary pressure shell boilers with water as
medium, evaporating heating surface mainly arranged on shell OR boiler furnace
arranged in shell which meet the following conditions:
a) Steam boiler of which the water volume at the design normal water level is
greater than or equal to 30L, and the rated steam pressure is greater than or
equal to 0.1MPa (gauge pressure; the same below);
b) Hot-water boiler of which the rated outflow pressure is greater than or equal to
0.1Mpa, or the rated power is greater than or equal to 0.1MW.
1.3 This Part is not applicable to the following equipment:
a) Portable boiler (e.g. marine boiler, railway locomotive traction boiler);
b) Cooling devices required for equipment and process flow cooling;
c) Boiler for military use.
2 Normative References
The following referenced documents are indispensable for the application of this
document. For dated references, only the edition cited applies. For undated
references, the latest edition of the normative document (including any amendments)
applies.
GB/T 1576 Water Quality for Industrial Boilers
GB/T 1921 Parameters for Industrial Steam Boilers
GB/T 3166 Parameters for Hot Water Boilers
GB/T 2900.48 Electrotechnical Terminology of Boilers
GB 8978 Integrated Wastewater Discharge Standard
GB/T 10180 Thermal Performance Test Code for Industrial Boilers
GB/T 10863 Thermal Test Method for Gas Pass Heat Recovery Boiler
GB/T 12145 Quality Criterion of Water and Steam for Generating Unit and Steam
Power Equipment
GB 12348 Standard of Noise at Boundary of Industrial Enterprises
GB 13271 Emission Standard of Air Pollutants for Boiler
GB/T 16507 Water-tube Boilers
GB/T 16508.2 Shell Boilers - Part 2: Material
GB/T 16508.3 Shell Boilers - Part 3: Design and Strength Calculation
GB/T 16508.4 Shell Boilers - Part 4: Fabrication, Inspection and Acceptance
GB/T 16508.5 Shell Boilers - Part 5: Safety Appurtenances and Instruments
GB/T 16508.6 Shell Boilers - Part 6: Combustion Systems
GB/T 16508.7 Shell Boilers - Part 7: Installation
GB/T 16508.8 Shell Boilers - Part 8: Operation
GB/T 22395 Specification for Design of Boiler Steel Structures
GB 24747 Safety Technology Conditions for Heat Transfer Fluids
JB/T 6734 Strength Calculation Method for Boiler Fillet Weld
JB/T 6735 Calculation Method for Strength of Boiler Hanger Rod
NB/T 47013
(JB/T 4730)
Nondestructive Testing of Pressure Equipment
3.5
Safety release pressure
The pressure of safety valve upon releasing, also referred to as set pressure of safety
valve.
3.6
Hydrostatic test pressure
The pressure applied when conducting hydrostatic test for boiler system or pressure
component (part) as required.
3.7
Rated temperature
The working fluid temperature at the outlet which shall be ensured for long-term
continuous operation under specified design conditions.
3.8
Calculating temperature
The metal temperature of part set under normal operating conditions (the mean
temperature along the metal section of part).
3.9
Test temperature
The metal temperature of pressure part in pressure test.
3.10
Required thickness
The thickness of pressure part determined according to theoretical calculation formula.
Where necessary, thickness required by other loads shall also be calculated.
3.11
Design thickness
3.18
The highest fire line
The highest point of water-side under the erosion of flame or high-temperature flue
gas on the evaporating heating surface of boiler.
3.19
Component space
It means that adequate space must be provided between adjacent parts of different
wall temperatures on the tube plate so as to avoid overlarge temperature difference
stress.
4 Qualification and responsibilities
4.1 Qualification
4.1.1 Organization qualification
The fabrication, inspection, testing and installation organizations of boilers shall obtain
corresponding special equipment license qualification according to the requirements
of "Regulations on Safety Supervision over Special Equipment".
4.1.2 Personnel qualification
4.1.2.1 The welding personnel of the boiler pressure parts shall be assessed
according to the requirements of relevant safety technical codes such as
"Examination Rules for Welding Operators of Special Equipment" and may be
engaged in the welding work within the acceptable project scope within the period of
validity after obtaining the "Special Equipment Operator Certificate".
4.1.2.2 The non-destructive inspection personnel may only undertake
non-destructive testing with type and technical level corresponding to the qualification
certificate after obtaining the special equipment operator qualification certificate
according to the requirements of relevant technical codes.
4.1.2.3 The operation personnel of boiler using organization shall be provided with
corresponding qualification required by safety technical codes.
4.2 Responsibilities
main pressure part, welding quality certificate, non-destructive testing report
and hydrostatic test report, etc.);
e) Installation instructions and operating instructions of boiler;
f) Significant design change information of pressure part;
g) Water flow diagram and hydrodynamic calculation sheet of hot-water boiler
(except natural-circulation shell boiler);
h) Fabrication, supervision and inspection certificate;
i) Technical information concerned with safety and energy conservation.
4.2.2.5 For the fabricated boilers within the design service life, the fabrication
organization shall not only preserve the above technical information of delivery, but
also properly preserve the following technical documents for future reference:
a) Boiler design detail;
b) Material utilization list;
c) Fabrication process diagram or fabrication process card;
d) Welding process document;
e) Heat treatment process document;
f) Inspection and test record during fabrication process and after completion;
g) Fabrication, supervision and inspection certificate;
h) Permissible project selection record, etc.
4.2.3 Installation Organization
The installation organization shall carry out installation construction according to
relevant safety technical codes and standards as well as the boiler drawings and
installation instructions provided by...
Share
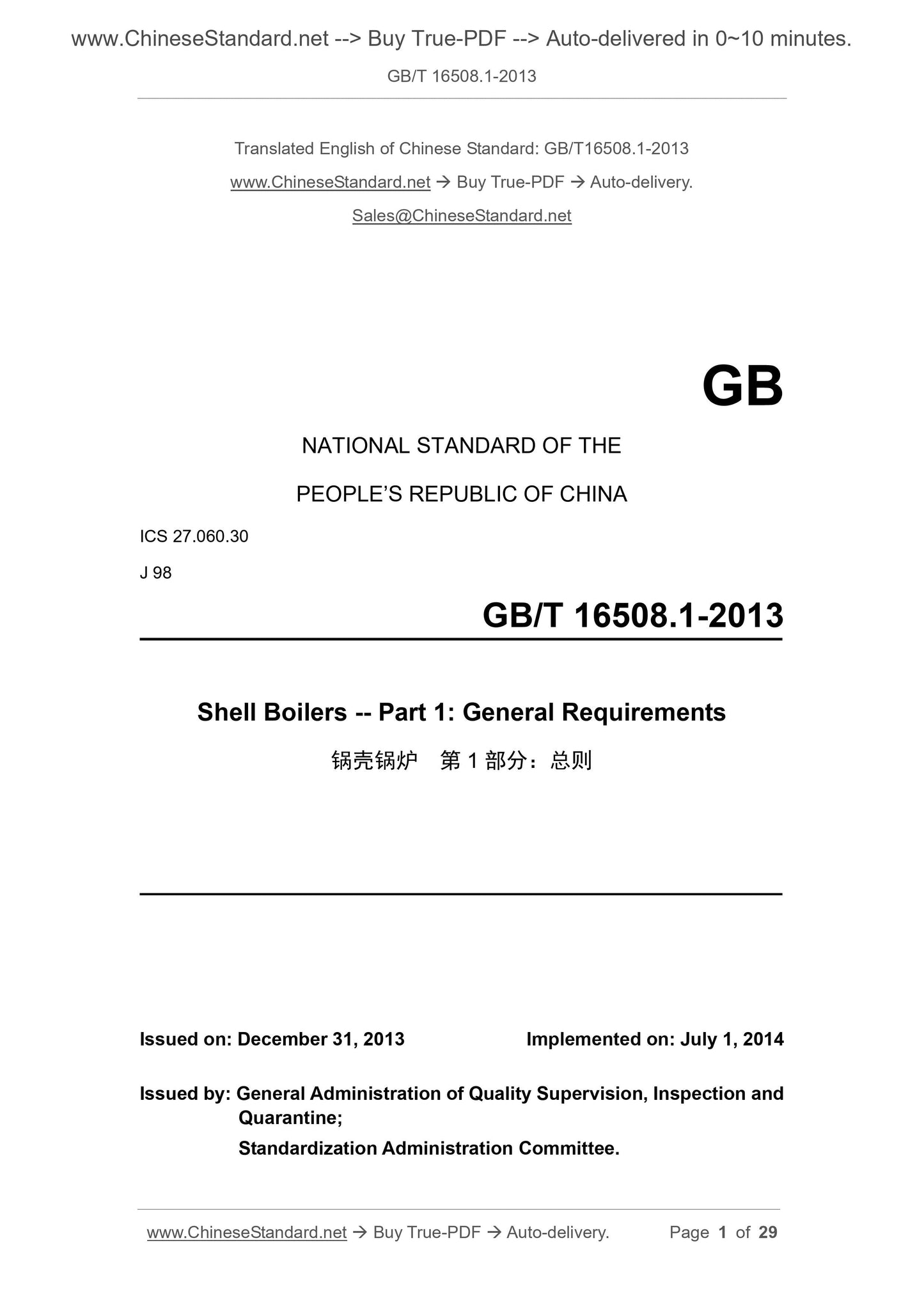
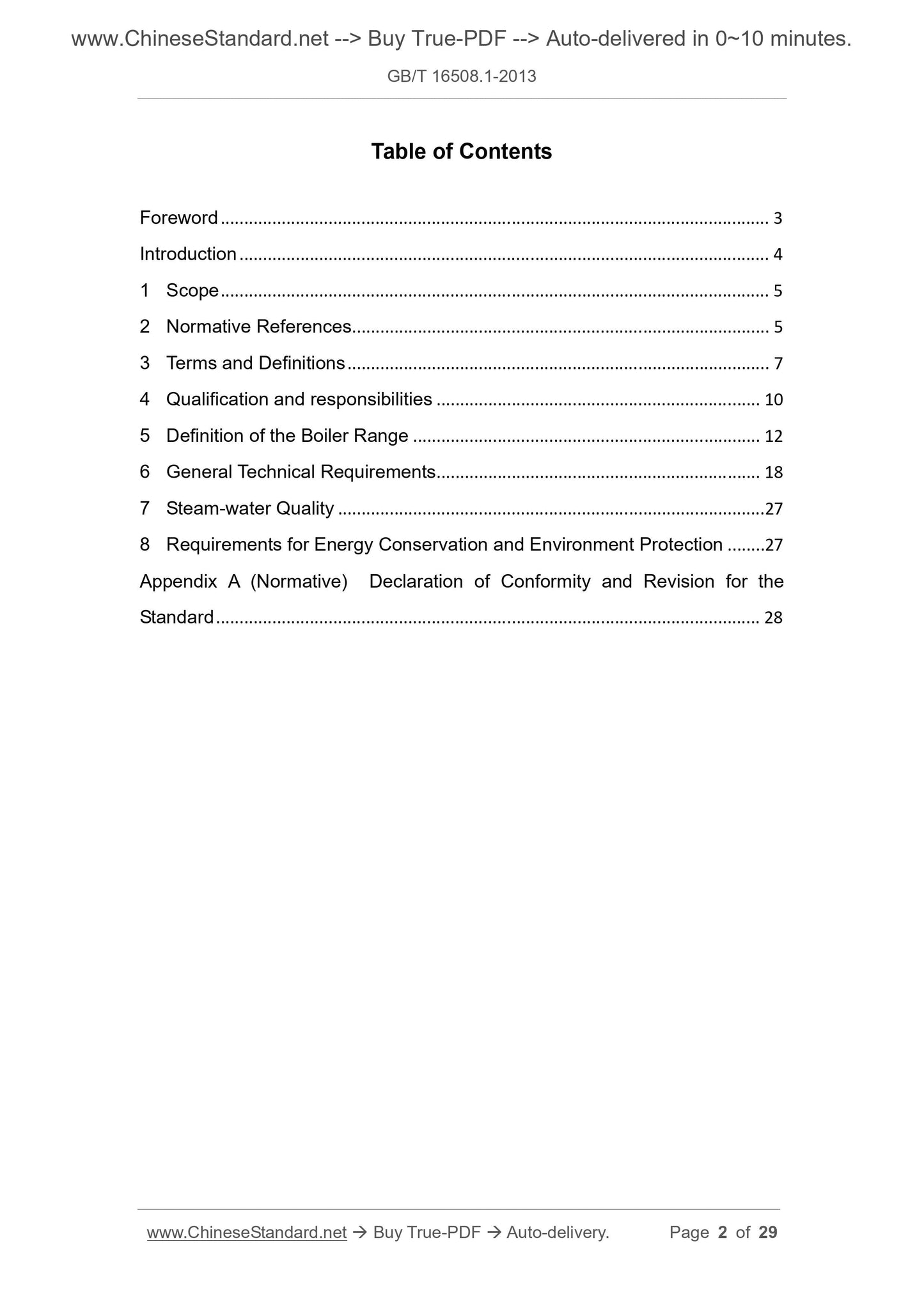
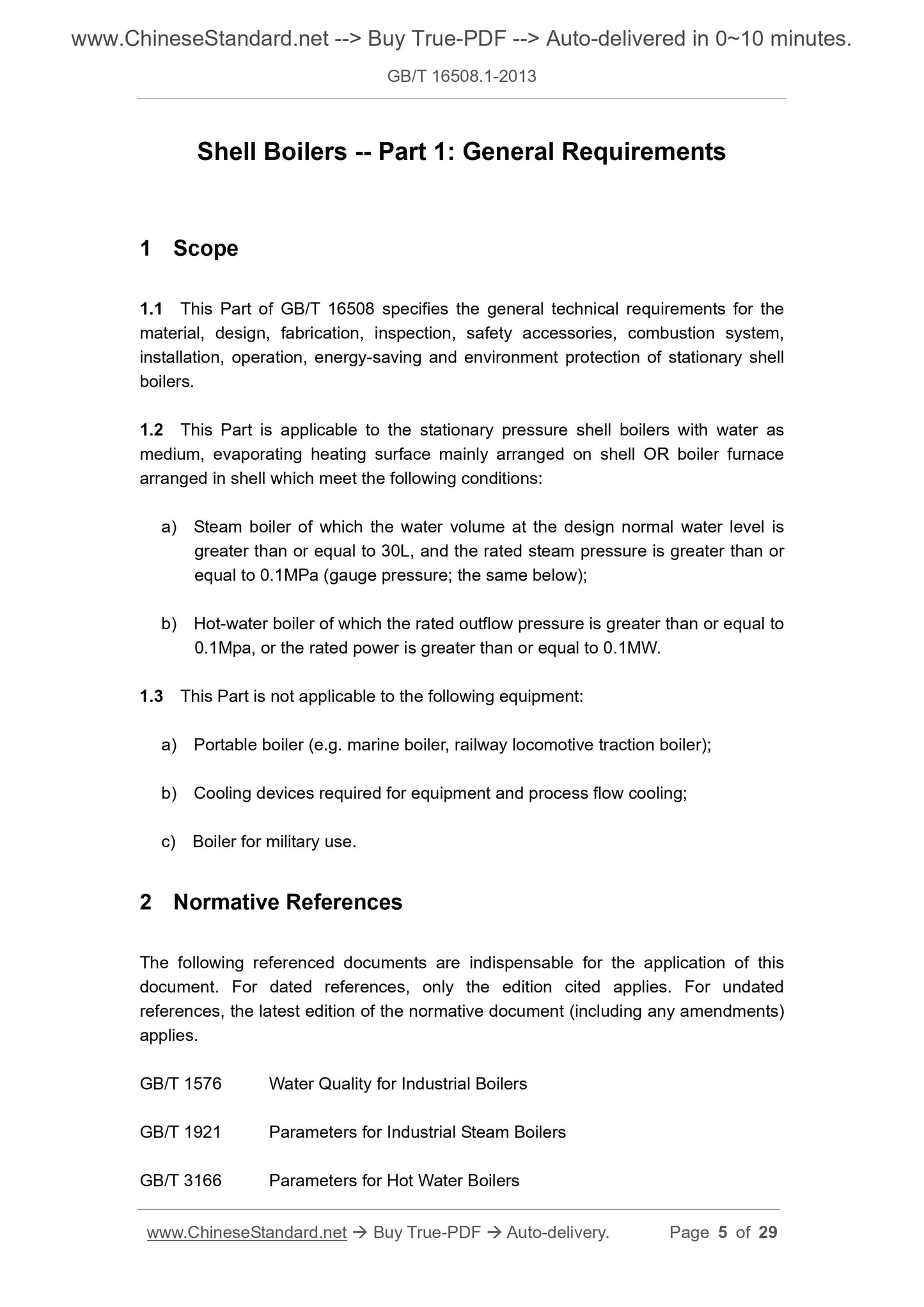
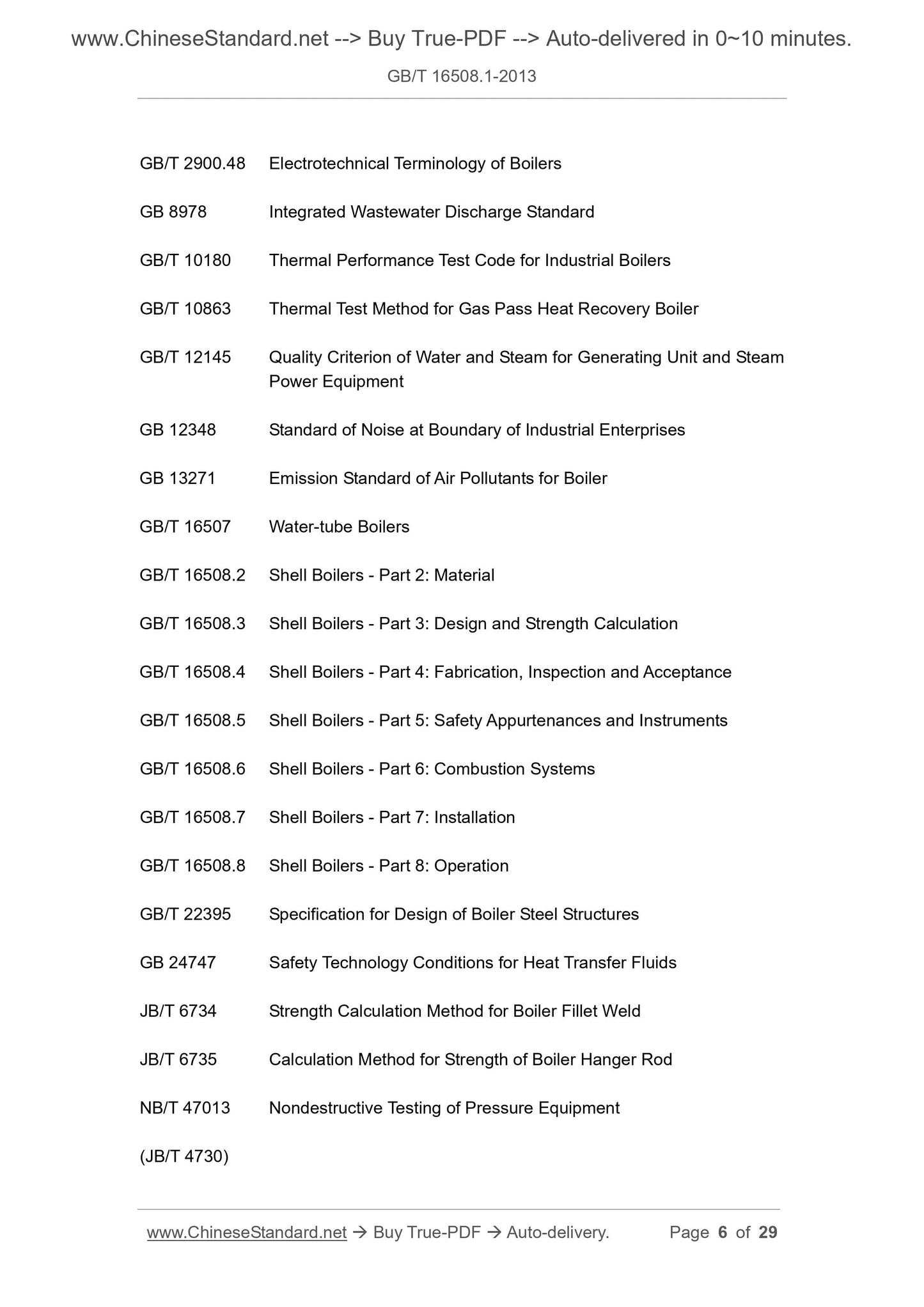
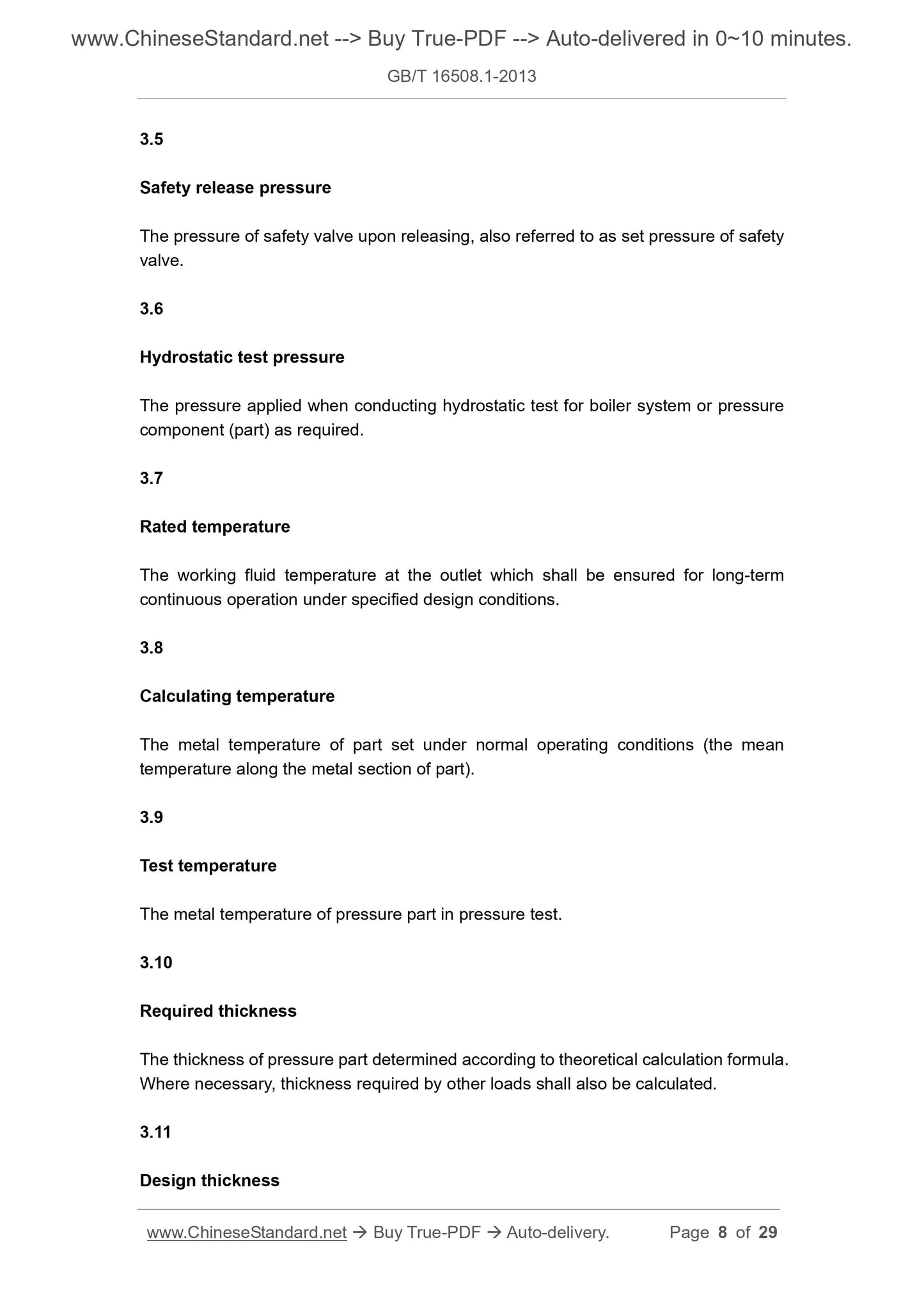
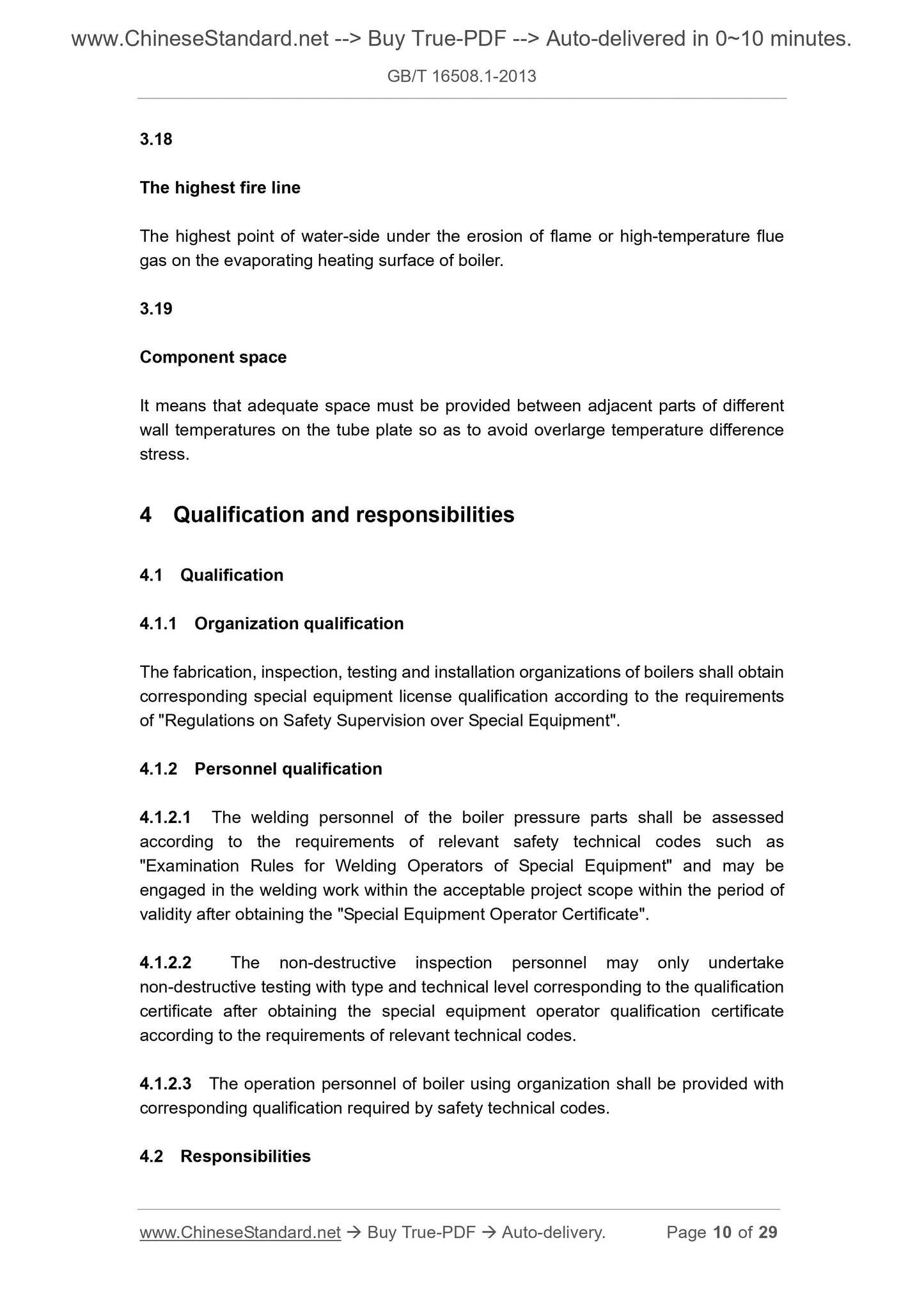
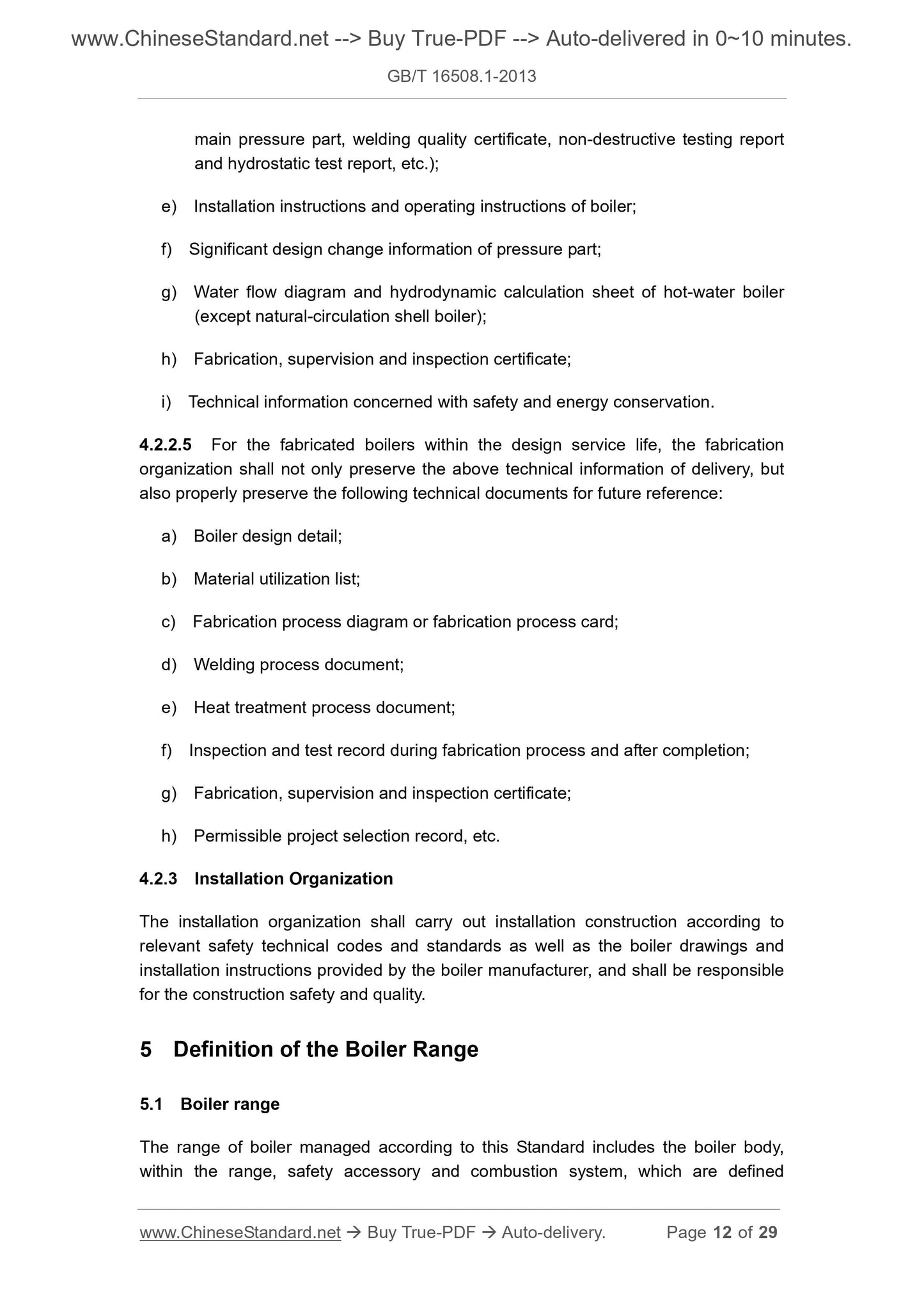
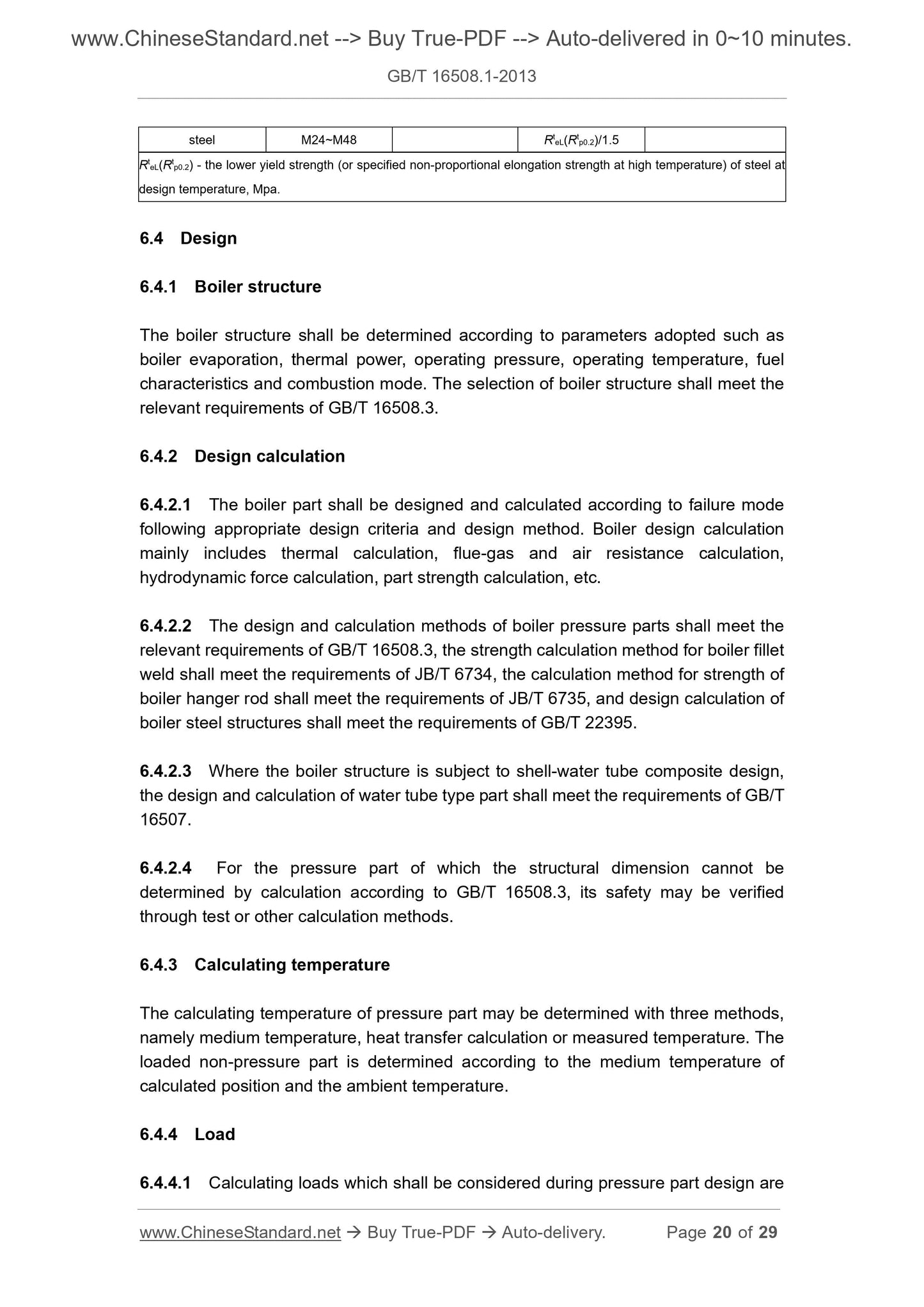
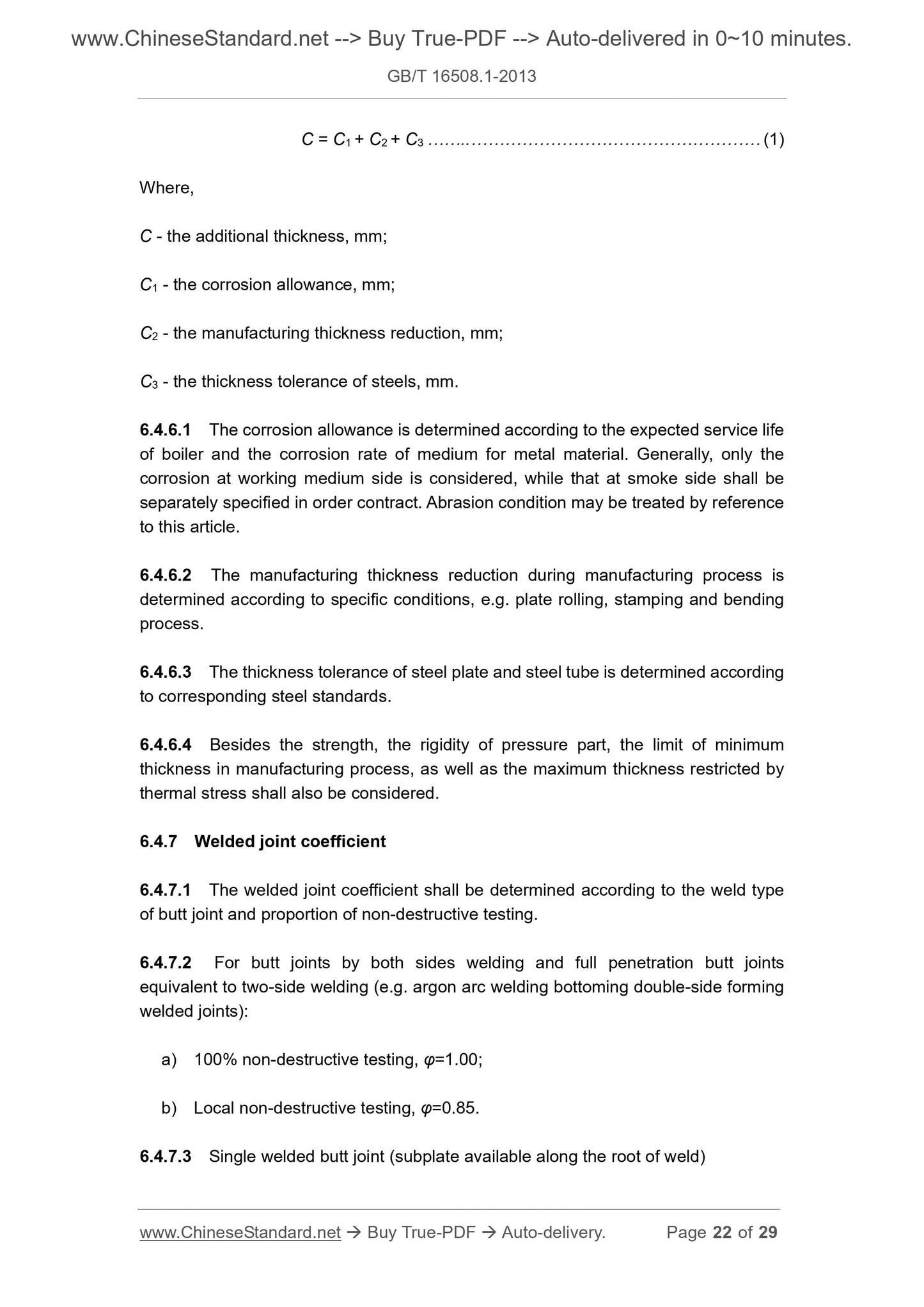
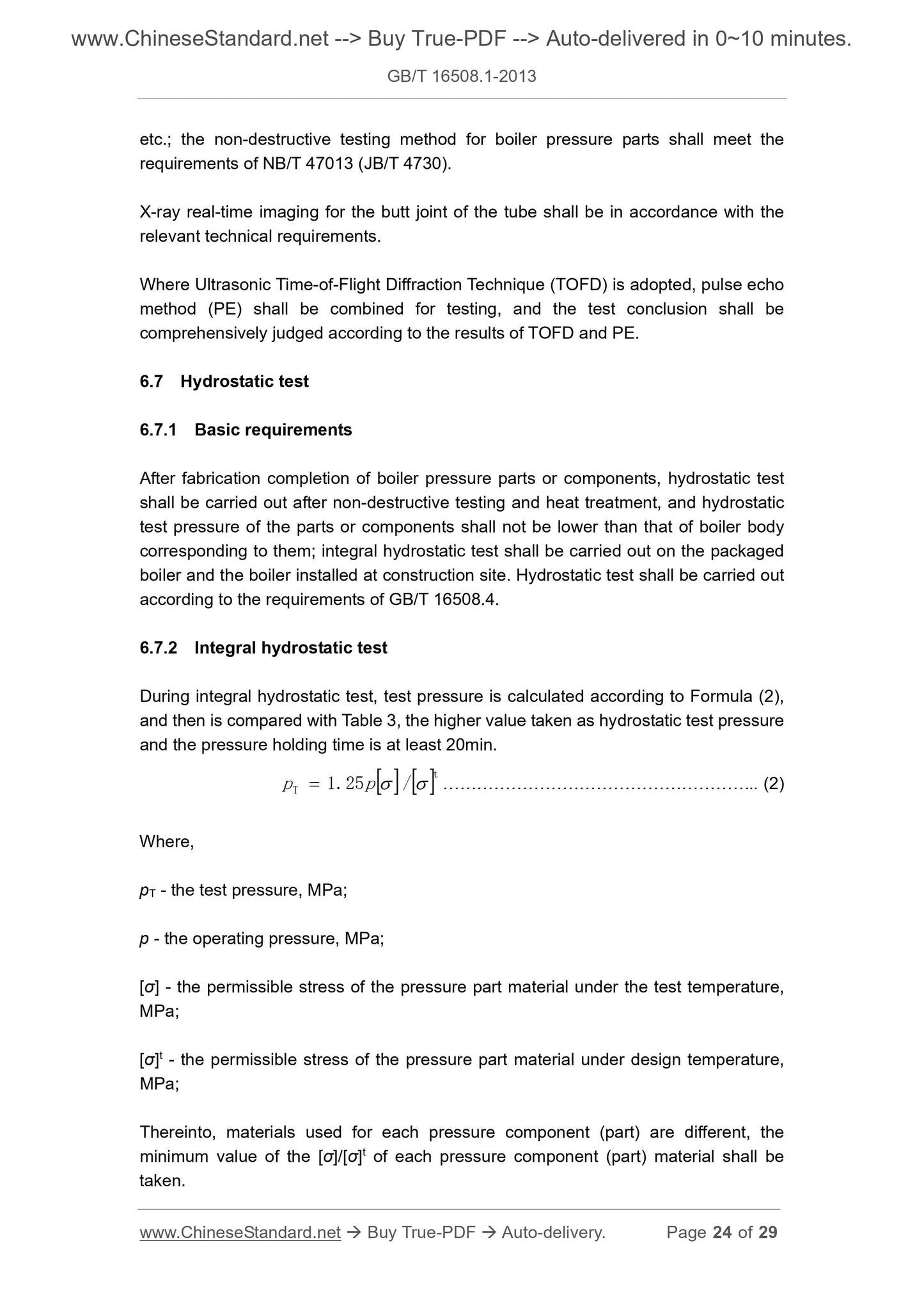
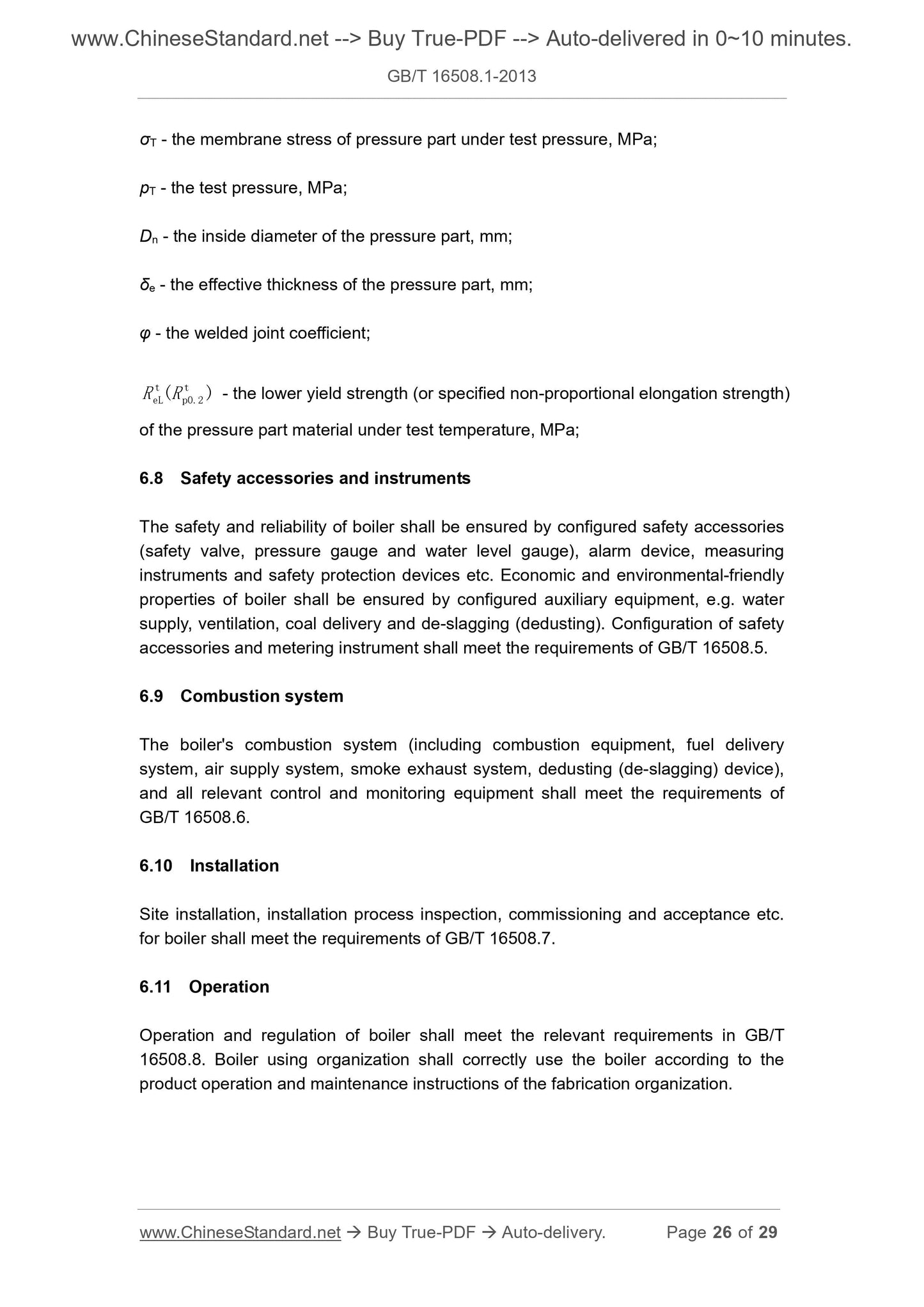
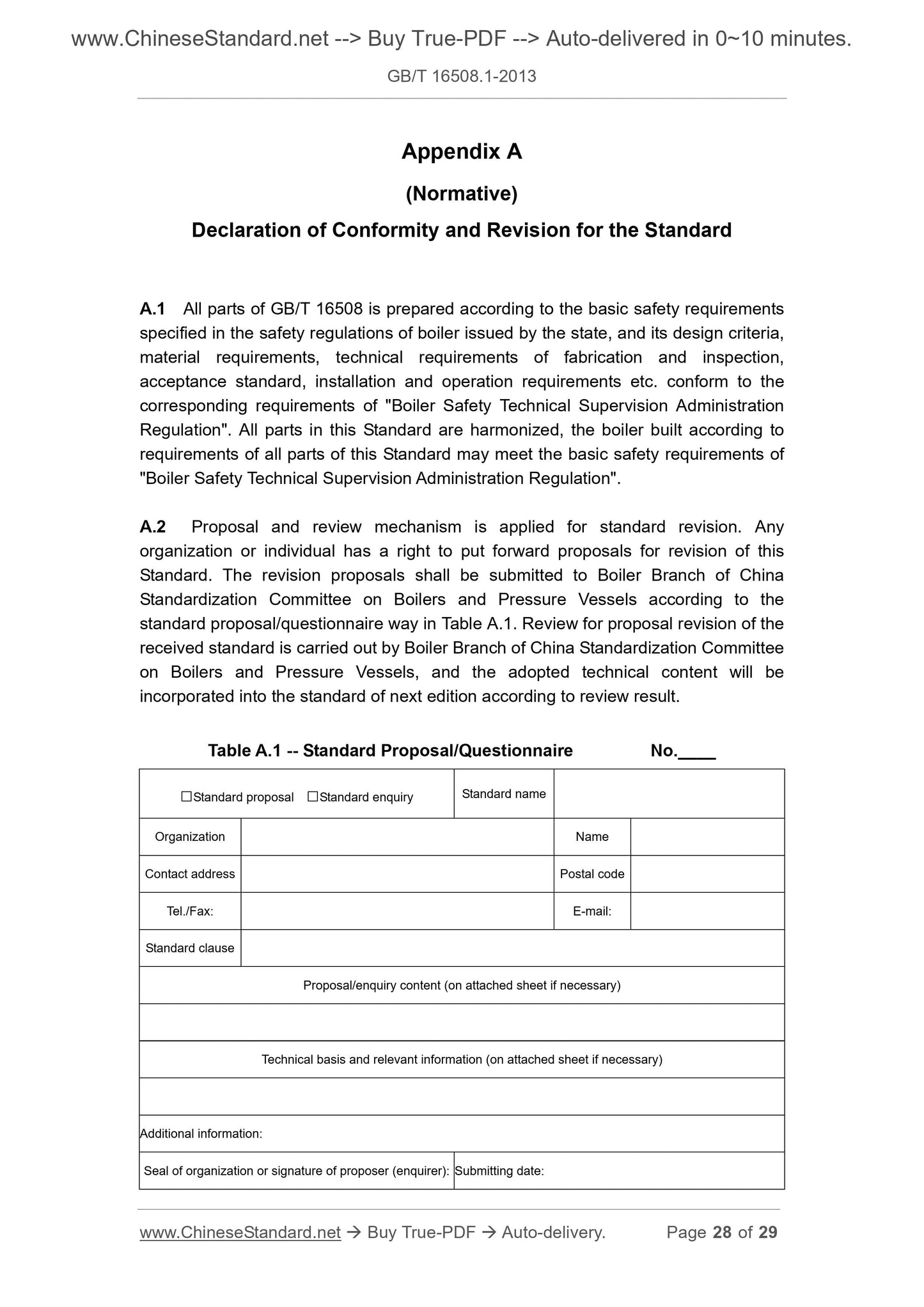