1
/
of
11
www.ChineseStandard.us -- Field Test Asia Pte. Ltd.
GB/T 15344-2020 English PDF (GB/T15344-2020)
GB/T 15344-2020 English PDF (GB/T15344-2020)
Regular price
$245.00
Regular price
Sale price
$245.00
Unit price
/
per
Shipping calculated at checkout.
Couldn't load pickup availability
GB/T 15344-2020: Method for Physical Test of Talc
Delivery: 9 seconds. Download (& Email) true-PDF + Invoice.
Get Quotation: Click GB/T 15344-2020 (Self-service in 1-minute)
Historical versions (Master-website): GB/T 15344-2020
Preview True-PDF (Reload/Scroll-down if blank)
GB/T 15344-2020
GB
NATIONAL STANDARD OF THE
PEOPLE’S REPUBLIC OF CHINA
ICS 73.080
Q 64
Replacing GB/T 15344-2012
Method for Physical Test of Talc
ISSUED ON: MARCH 31, 2020
IMPLEMENTED ON: FEBRUARY 1, 2021
Issued by: State Administration for Market Regulation;
Standardization Administration of the People’s Republic of
China.
Table of Contents
Foreword ... 3
1 Scope ... 5
2 Normative References ... 5
3 Samples ... 5
3.1 Sampling ... 5
3.2 Sample Preparation ... 6
4 Test Methods ... 6
4.1 Method for Moisture Determination of Talc Powder ... 6
4.2 Method for Dust Determination of Talc Powder ... 7
4.3 Method for pH Value Determination of Water Extract of Talc Powder ... 9
4.4 Method for Sedimentation Velocity of Talc Powder ... 9
4.5 Method for True Density Determination of Talc Powder ... 11
4.6 Method for Fineness Determination of Grinded Talc Powder ... 13
4.7 Method for Wet Whiteness Determination of Talc Powder ... 17
4.8 Method for Bulk Density Determination of Talc Powder ... 18
4.9 Method for Fineness Determination of Fine and Ultrafine Talc Powder ... 20
4.10 Method for Magnet Extract Determination of Talc Powder ... 20
4.11 Method for Apparent Density Determination of Talc Powder ... 21
4.12 Method for Scraper Fineness Determination of Talc Powder ... 22
4.13 Method for Oil Absorption Determination of Talc Powder ... 23
4.14 Method for Burnt Whiteness Determination of Talc Powder ... 25
Appendix A (informative) Density of Water ... 26
Methods for Physical Test of Talc
1 Scope
This Standard specifies the methods for physical test of talc moisture, dust content, pH
value of water extract, sedimentation velocity, true density, fineness of grinded talc
powder, wet whiteness, bulk density, fineness of fine and ultrafine talc powder, magnet
extract, apparent density, scraper fineness, oil absorption and burnt whiteness, etc.
This Standard is applicable to natural talc lumps and talc powder.
2 Normative References
The following documents are indispensable to the application of this document. In
terms of references with a specified date, only versions with a specified date are
applicable to this document. In terms of references without a specified date, the latest
version (including all the modifications) is applicable to this document.
GB/T 2010 Method of Sampling and Sample Preparation of Talc in Bulk
GB/T 5950 Method for Measurement of Whiteness of Building Materials and Non-metal
Mineral Products
GB/T 6003.1 Test Sieves - Technical Requirements and Testing - Part 1: Test Sieves
of Metal Wire Cloth
GB/T 8170 Rules of Rounding off for Numerical Values and Expression and Judgement
of Limiting Values
GB/T 15342 Talc Powder
GB/T 19077 Particle Size Analysis - Laser Diffraction Methods
DZ/T 0118 The Specifications of the Standard Sieves Vibrating Screen for Laboratory
3 Samples
3.1 Sampling
3.1.1 The sampling of talc lumps shall be conducted in accordance with GB/T 2010.
3.1.2 The sampling of talc powder shall be conducted in accordance with GB/T 15342.
4.3 Method for pH Value Determination of Water Extract of Talc Powder
4.3.1 Materials and apparatuses
The materials and apparatuses required for the pH value determination of water extract
of talc powder are as follows:
a) Balance: the division value is not greater than 0.0001 g;
b) Temperature-adjustable electric furnace with asbestos net;
c) Acidity meter: the accuracy is 0.02;
d) Beaker: 250 mL; 100 mL;
e) Measuring cylinder: 100 mL;
f) Funnel;
g) Filter paper: slow speed;
h) Distilled water: remove carbon dioxide through boiling; cool it down to room
temperature; pH value is 6.8 ~ 7.2.
4.3.2 Test procedures
4.3.2.1 Weigh-take about 5 g of sample (accurate to 0.0001 g); place it in a 250 mL
beaker.
4.3.2.2 Pour 10 mL of distilled water into the beaker. Use a glass rod to carefully stir it,
so as to completely wet the sample. Then, pour in 90 mL of distilled water; mark the
height of the liquid level on the outer wall of the beaker.
4.3.2.3 Place the beaker on the electric furnace to boil it, then, adjust the temperature
control knob of the electric furnace to below 300 W. Slightly boil it at a low temperature
for 5 min (during the process of slight boiling, keep stirring it and supplement the
amount of water lost in evaporation); remove it, and cool it down to room temperature.
Use a pH meter to determine the pH value of the suspension liquid.
4.3.3 Result expression and tolerances
Take the arithmetic mean value of two parallel test results as the report value. In
addition, in accordance with GB/T 8170, round it off to two decimal places. If the
absolute error of two parallel test results is greater than 0.2, then, the samples shall be
re-prepared for the determination.
4.4 Method for Sedimentation Velocity of Talc Powder
4.4.1 Materials and apparatuses
addition, in accordance with GB/T 8170, round it off to one decimal place.
4.4.4 Tolerances
The absolute error of two parallel test results shall be not greater than 2 mL. Otherwise,
the determination shall be re-conducted.
4.5 Method for True Density Determination of Talc Powder
4.5.1 Materials and apparatuses
The materials and apparatuses required for the determination of true density of talc
powder are as follows:
a) Balance: the division value is not greater than 0.0001 g;
b) Electric-heated thermostatic water bath: the sensitivity is ± 1 °C;
c) Temperature-adjustable electric furnace with asbestos net;
d) Vacuum desiccator with vacuum air pump;
e) Pycnometer: 50 mL;
f) Thermometer;
g) Kerosene;
h) Distilled water.
4.5.2 Test procedures
4.5.2.1 Vacuuming method with pycnometer (Method A)
4.5.2.1.1 Use distilled water to fill a clean and dry pycnometer with an already-known
mass (if there are bubbles in the pycnometer, remove them).
4.5.2.1.2 Put on the cap of the pycnometer filled with liquid; place it in a 25 °C ± 1 °C
thermostatic water bath for 0.5 h (when the liquid level in the capillary tube of the
pycnometer drops, the same liquid shall be added in time to fill it up). Take out the
pycnometer; use filter paper to quickly dry the exterior part of the pycnometer. However,
DO NOT wipe off water on the capillary end. Weigh it (accurate to 0.0001 g) to obtain
m3.
4.5.2.1.3 Pour out the distilled water from the pycnometer, then, dry it again. Fill the
pycnometer with kerosene; repeat the steps of 4.5.2.1.2 to obtain m4.
4.5.2.1.4 After washing and drying the pycnometer again, weigh-take about 5 g of the
dried sample, put it into the pycnometer. Put on the cap, then, weigh it (accurate to
4.5.2.2.3 Remove the pycnometer; cool it down to room temperature. Then, pour in
freshly boiled distilled water that is cooled down to room temperature, so that the water
level in the bottle is 2 mm ~ 3 mm below the mouth of the pycnometer. Slowly put on
the stopper (at this moment, the capillary shall be filled with water, but there shall be
no bubbles); quickly dry the exterior part of the pycnometer. However, DO NOT wipe
off water on the capillary end. Weigh it (accurate to 0.0001 g) to obtain m8.
4.5.2.2.4 Pour out the sample and water in the pycnometer. After washing it, pour in
freshly boiled distilled water that is cooled down to room temperature, so that the water
level in the bottle is 2 mm ~ 3 mm below the mouth of the pycnometer. Use a stopper
to plug it; quickly dry the exterior part. DO NOT wipe off water on the capillary end.
Weigh it (accurate to 0.0001 g) to obtain m3. Record the temperature of the water at
room temperature.
4.5.2.2.5 The density 1 [expressed in (g/cm3)] of the sample shall be calculated in
accordance with Formula (5):
Where,
2---water density at t (°C), expressed in (g/cm3), see Appendix A;
m8---the mass of the pycnometer and the distilled water and the sample, expressed in
(g).
4.5.3 Results and tolerances
Take the arithmetic mean value of two parallel test results as the report value. In
addition, in accordance with GB/T 8170, round it off to two decimal places. The
absolute error of two parallel test results shall be not greater than 0.1 g/cm3. Otherwise,
the determination shall be re-conducted.
4.6 Method for Fineness Determination of Grinded Talc Powder
4.6.1 Materials and apparatuses
The materials and apparatuses required for the fineness determination of grinded talc
powder are as follows:
a) Test sieve: it shall comply with GB/T 6003.1; the diameter of the sieve frame
is 200 mm;
b) Vibrating sieving machine: the number of vibrations is 147 times/min; the
radius of gyration is 125 mm; the others shall comply with the stipulations of
DZ/T 0118;
the end of sieving has been reached. The duration of the rinsing is about 10 min.
4.6.2.1.5 Use distilled water to transfer all the residue on the sieve to a beaker with an
already-known mass; place the beaker on the temperature-adjustable electric furnace;
conduct low-temperature evaporation, till it reaches dryness.
4.6.2.1.6 Place the beaker in the electrothermal drying oven. At the temperature of
105 °C ~ 110 °C, dry it for 0.5 h ~ 1 h, then, take it out. Place it in a desiccator; cool it
down to room temperature, then, weigh it (accurate to 0.0001 g).
4.6.2.2 Vibrating sieving machine method (Method B)
4.6.2.2.1 Weigh-take about 20 g of the dried sample (accurate to 0.01 g); place it into
a test sieve with a sieve bottom of a specified pore size. Gently shake it, so as to evenly
spread the sample on the sieve. Put on the sieve cover; place it on the vibrating sieving
machine frame; properly fix it.
4.6.2.2.2 Turn on the vibrating sieving machine; simultaneously, press the stopwatch
for timekeeping.
4.6.2.2.3 After sieving for 5 min, cut off the power supply and stop sieving.
NOTE: if manual sieving can reach the same effect, you may also directly sieve by hands
without using the vibrating sieving machine.
4.6.2.2.4 Take out the test sieve, together with the sieve cover and the sieve bottom.
Use a small brush (without lint) to sweep the talc powder attached to the inner side of
the sieve cover and the inner periphery of the sieve frame into the sieve. Conduct
manual sieving for 15 s; tap for about 20 times.
4.6.2.2.5 In accordance with 4.6.2.4, check the end point of the sieving. When the ratio
of the mass of the sieve residue to the mass of the sample is less than 0.035%, then,
it is considered that the end of sieving has been reached. Otherwise, in accordance
with the steps of 4.6.2.2.2, continue the sieving for 2 min, then, check the end point of
the sieving. Repeat this process, until the end point has been reached.
4.6.2.2.6 After reaching the end of the sieving, transfer all the sieve residue to a watch
glass with an already-known mass; weigh it (accurate to 0.0001 g).
4.6.2.3 Airflow sieving method (Method C)
4.6.2.3.1 Weigh-take about 20 g of the dried sample (accurate to 0.01 g); put it into a
test sieve with a specified pore size. Gently shake it, so as to evenly spread the sample
on the sieve.
4.6.2.3.2 Place the sieve on the sieve base of the rotary airflow screen; put on the
sieve cover.
4.6.2.3.3 Turn on the airflow screen; simultaneously, press the stopwatch for
timekeeping. During sieving, control the negative work pressure to 3 103 Pa; use a
small wooden hammer to gently tap the screen cover or the screen frame, so that the
talc powder attached to the screen cover or the screen frame may fall into the sieve.
4.6.2.3.4 After sieving for 30 s, cut off the power supply and stop sieving.
4.6.2.3.5 Take out the test sieve, together with the sieve cover. Use a small brush
(without lint) to sweep the talc powder attached to the inner side of the sieve cover and
the inner periphery of the sieve frame into the test sieve. Conduct manual sieving for
15 s; tap for about 20 times.
4.6.2.3.6 In accordance with 4.6.2.4, check the end point of the sieving. When the ratio
of the mass of the sieve residue to the mass of the sample is less than 0.035%, then,
it is considered that the end of sieving has been reached. Otherwise, in accordance
with the steps of 4.6.2.3.2 ~ 4.6.2.3.4, continue the sieving for 15 s, then, check the
end point of the sieving. Repeat this process, until the end point has been reached.
4.6.2.3.7 After reaching the end of the sieving, transfer all the sieve residue to a watch
glass with an already-known mass; weigh it (accurate to 0.0001 g).
4.6.2.4 Sieving endpoint check
4.6.2.4.1 Put the test sieve with sieve residue on the clean bottom of the sieve. Lift the
sieve; lightly tap the sieve frame; tap for about 80 times per minute. After sieving for 1
min, stop the sieving.
4.6.2.4.2 Remove the bottom of the sieve; use a small wool sieve to transfer the sieve
residue on the bottom of the sieve into a watch glass with an already-known mass;
weigh it (accurate to 0.0001 g).
4.6.2.4.3 When the ratio of the mass of the sieve residue to the mass of the sample is
less than 0.035%, then, it is considered that the end of sieving has been reached.
4.6.3 Result calculation
The passing rate X2 [expressed in (%)] shall be calculated in accordance with Formula
(6):
Where,
m9---the mass of the beaker (or the watch glass) and the sieve residue, expressed in
(g);
m10---the mass of the beaker (or the watch glass), expressed in (g);
4.9 Method for Fineness Determination of Fine and Ultrafine Talc Powder
4.9.1 Materials and apparatuses
The materials and apparatuses required for the fineness determination of fine and
ultrafine talc powder are as follows:
a) Ultrasonic disperser;
b) Beaker: 200 mL;
c) Laser particle size analyzer: 0.1 μm ~ 1,000 μm;
d) Dispersion medium: sodium hexametaphosphate solution (2 g/L) or other
appropriate dispersing agents.
4.9.2 Test procedures
In accordance with GB/T 19077, conduct the test.
4.10 Method for Magnet Extract Determination of Talc Powder
4.10.1 Materials and apparatuses
The materials and apparatuses required for the determinatio...
Delivery: 9 seconds. Download (& Email) true-PDF + Invoice.
Get Quotation: Click GB/T 15344-2020 (Self-service in 1-minute)
Historical versions (Master-website): GB/T 15344-2020
Preview True-PDF (Reload/Scroll-down if blank)
GB/T 15344-2020
GB
NATIONAL STANDARD OF THE
PEOPLE’S REPUBLIC OF CHINA
ICS 73.080
Q 64
Replacing GB/T 15344-2012
Method for Physical Test of Talc
ISSUED ON: MARCH 31, 2020
IMPLEMENTED ON: FEBRUARY 1, 2021
Issued by: State Administration for Market Regulation;
Standardization Administration of the People’s Republic of
China.
Table of Contents
Foreword ... 3
1 Scope ... 5
2 Normative References ... 5
3 Samples ... 5
3.1 Sampling ... 5
3.2 Sample Preparation ... 6
4 Test Methods ... 6
4.1 Method for Moisture Determination of Talc Powder ... 6
4.2 Method for Dust Determination of Talc Powder ... 7
4.3 Method for pH Value Determination of Water Extract of Talc Powder ... 9
4.4 Method for Sedimentation Velocity of Talc Powder ... 9
4.5 Method for True Density Determination of Talc Powder ... 11
4.6 Method for Fineness Determination of Grinded Talc Powder ... 13
4.7 Method for Wet Whiteness Determination of Talc Powder ... 17
4.8 Method for Bulk Density Determination of Talc Powder ... 18
4.9 Method for Fineness Determination of Fine and Ultrafine Talc Powder ... 20
4.10 Method for Magnet Extract Determination of Talc Powder ... 20
4.11 Method for Apparent Density Determination of Talc Powder ... 21
4.12 Method for Scraper Fineness Determination of Talc Powder ... 22
4.13 Method for Oil Absorption Determination of Talc Powder ... 23
4.14 Method for Burnt Whiteness Determination of Talc Powder ... 25
Appendix A (informative) Density of Water ... 26
Methods for Physical Test of Talc
1 Scope
This Standard specifies the methods for physical test of talc moisture, dust content, pH
value of water extract, sedimentation velocity, true density, fineness of grinded talc
powder, wet whiteness, bulk density, fineness of fine and ultrafine talc powder, magnet
extract, apparent density, scraper fineness, oil absorption and burnt whiteness, etc.
This Standard is applicable to natural talc lumps and talc powder.
2 Normative References
The following documents are indispensable to the application of this document. In
terms of references with a specified date, only versions with a specified date are
applicable to this document. In terms of references without a specified date, the latest
version (including all the modifications) is applicable to this document.
GB/T 2010 Method of Sampling and Sample Preparation of Talc in Bulk
GB/T 5950 Method for Measurement of Whiteness of Building Materials and Non-metal
Mineral Products
GB/T 6003.1 Test Sieves - Technical Requirements and Testing - Part 1: Test Sieves
of Metal Wire Cloth
GB/T 8170 Rules of Rounding off for Numerical Values and Expression and Judgement
of Limiting Values
GB/T 15342 Talc Powder
GB/T 19077 Particle Size Analysis - Laser Diffraction Methods
DZ/T 0118 The Specifications of the Standard Sieves Vibrating Screen for Laboratory
3 Samples
3.1 Sampling
3.1.1 The sampling of talc lumps shall be conducted in accordance with GB/T 2010.
3.1.2 The sampling of talc powder shall be conducted in accordance with GB/T 15342.
4.3 Method for pH Value Determination of Water Extract of Talc Powder
4.3.1 Materials and apparatuses
The materials and apparatuses required for the pH value determination of water extract
of talc powder are as follows:
a) Balance: the division value is not greater than 0.0001 g;
b) Temperature-adjustable electric furnace with asbestos net;
c) Acidity meter: the accuracy is 0.02;
d) Beaker: 250 mL; 100 mL;
e) Measuring cylinder: 100 mL;
f) Funnel;
g) Filter paper: slow speed;
h) Distilled water: remove carbon dioxide through boiling; cool it down to room
temperature; pH value is 6.8 ~ 7.2.
4.3.2 Test procedures
4.3.2.1 Weigh-take about 5 g of sample (accurate to 0.0001 g); place it in a 250 mL
beaker.
4.3.2.2 Pour 10 mL of distilled water into the beaker. Use a glass rod to carefully stir it,
so as to completely wet the sample. Then, pour in 90 mL of distilled water; mark the
height of the liquid level on the outer wall of the beaker.
4.3.2.3 Place the beaker on the electric furnace to boil it, then, adjust the temperature
control knob of the electric furnace to below 300 W. Slightly boil it at a low temperature
for 5 min (during the process of slight boiling, keep stirring it and supplement the
amount of water lost in evaporation); remove it, and cool it down to room temperature.
Use a pH meter to determine the pH value of the suspension liquid.
4.3.3 Result expression and tolerances
Take the arithmetic mean value of two parallel test results as the report value. In
addition, in accordance with GB/T 8170, round it off to two decimal places. If the
absolute error of two parallel test results is greater than 0.2, then, the samples shall be
re-prepared for the determination.
4.4 Method for Sedimentation Velocity of Talc Powder
4.4.1 Materials and apparatuses
addition, in accordance with GB/T 8170, round it off to one decimal place.
4.4.4 Tolerances
The absolute error of two parallel test results shall be not greater than 2 mL. Otherwise,
the determination shall be re-conducted.
4.5 Method for True Density Determination of Talc Powder
4.5.1 Materials and apparatuses
The materials and apparatuses required for the determination of true density of talc
powder are as follows:
a) Balance: the division value is not greater than 0.0001 g;
b) Electric-heated thermostatic water bath: the sensitivity is ± 1 °C;
c) Temperature-adjustable electric furnace with asbestos net;
d) Vacuum desiccator with vacuum air pump;
e) Pycnometer: 50 mL;
f) Thermometer;
g) Kerosene;
h) Distilled water.
4.5.2 Test procedures
4.5.2.1 Vacuuming method with pycnometer (Method A)
4.5.2.1.1 Use distilled water to fill a clean and dry pycnometer with an already-known
mass (if there are bubbles in the pycnometer, remove them).
4.5.2.1.2 Put on the cap of the pycnometer filled with liquid; place it in a 25 °C ± 1 °C
thermostatic water bath for 0.5 h (when the liquid level in the capillary tube of the
pycnometer drops, the same liquid shall be added in time to fill it up). Take out the
pycnometer; use filter paper to quickly dry the exterior part of the pycnometer. However,
DO NOT wipe off water on the capillary end. Weigh it (accurate to 0.0001 g) to obtain
m3.
4.5.2.1.3 Pour out the distilled water from the pycnometer, then, dry it again. Fill the
pycnometer with kerosene; repeat the steps of 4.5.2.1.2 to obtain m4.
4.5.2.1.4 After washing and drying the pycnometer again, weigh-take about 5 g of the
dried sample, put it into the pycnometer. Put on the cap, then, weigh it (accurate to
4.5.2.2.3 Remove the pycnometer; cool it down to room temperature. Then, pour in
freshly boiled distilled water that is cooled down to room temperature, so that the water
level in the bottle is 2 mm ~ 3 mm below the mouth of the pycnometer. Slowly put on
the stopper (at this moment, the capillary shall be filled with water, but there shall be
no bubbles); quickly dry the exterior part of the pycnometer. However, DO NOT wipe
off water on the capillary end. Weigh it (accurate to 0.0001 g) to obtain m8.
4.5.2.2.4 Pour out the sample and water in the pycnometer. After washing it, pour in
freshly boiled distilled water that is cooled down to room temperature, so that the water
level in the bottle is 2 mm ~ 3 mm below the mouth of the pycnometer. Use a stopper
to plug it; quickly dry the exterior part. DO NOT wipe off water on the capillary end.
Weigh it (accurate to 0.0001 g) to obtain m3. Record the temperature of the water at
room temperature.
4.5.2.2.5 The density 1 [expressed in (g/cm3)] of the sample shall be calculated in
accordance with Formula (5):
Where,
2---water density at t (°C), expressed in (g/cm3), see Appendix A;
m8---the mass of the pycnometer and the distilled water and the sample, expressed in
(g).
4.5.3 Results and tolerances
Take the arithmetic mean value of two parallel test results as the report value. In
addition, in accordance with GB/T 8170, round it off to two decimal places. The
absolute error of two parallel test results shall be not greater than 0.1 g/cm3. Otherwise,
the determination shall be re-conducted.
4.6 Method for Fineness Determination of Grinded Talc Powder
4.6.1 Materials and apparatuses
The materials and apparatuses required for the fineness determination of grinded talc
powder are as follows:
a) Test sieve: it shall comply with GB/T 6003.1; the diameter of the sieve frame
is 200 mm;
b) Vibrating sieving machine: the number of vibrations is 147 times/min; the
radius of gyration is 125 mm; the others shall comply with the stipulations of
DZ/T 0118;
the end of sieving has been reached. The duration of the rinsing is about 10 min.
4.6.2.1.5 Use distilled water to transfer all the residue on the sieve to a beaker with an
already-known mass; place the beaker on the temperature-adjustable electric furnace;
conduct low-temperature evaporation, till it reaches dryness.
4.6.2.1.6 Place the beaker in the electrothermal drying oven. At the temperature of
105 °C ~ 110 °C, dry it for 0.5 h ~ 1 h, then, take it out. Place it in a desiccator; cool it
down to room temperature, then, weigh it (accurate to 0.0001 g).
4.6.2.2 Vibrating sieving machine method (Method B)
4.6.2.2.1 Weigh-take about 20 g of the dried sample (accurate to 0.01 g); place it into
a test sieve with a sieve bottom of a specified pore size. Gently shake it, so as to evenly
spread the sample on the sieve. Put on the sieve cover; place it on the vibrating sieving
machine frame; properly fix it.
4.6.2.2.2 Turn on the vibrating sieving machine; simultaneously, press the stopwatch
for timekeeping.
4.6.2.2.3 After sieving for 5 min, cut off the power supply and stop sieving.
NOTE: if manual sieving can reach the same effect, you may also directly sieve by hands
without using the vibrating sieving machine.
4.6.2.2.4 Take out the test sieve, together with the sieve cover and the sieve bottom.
Use a small brush (without lint) to sweep the talc powder attached to the inner side of
the sieve cover and the inner periphery of the sieve frame into the sieve. Conduct
manual sieving for 15 s; tap for about 20 times.
4.6.2.2.5 In accordance with 4.6.2.4, check the end point of the sieving. When the ratio
of the mass of the sieve residue to the mass of the sample is less than 0.035%, then,
it is considered that the end of sieving has been reached. Otherwise, in accordance
with the steps of 4.6.2.2.2, continue the sieving for 2 min, then, check the end point of
the sieving. Repeat this process, until the end point has been reached.
4.6.2.2.6 After reaching the end of the sieving, transfer all the sieve residue to a watch
glass with an already-known mass; weigh it (accurate to 0.0001 g).
4.6.2.3 Airflow sieving method (Method C)
4.6.2.3.1 Weigh-take about 20 g of the dried sample (accurate to 0.01 g); put it into a
test sieve with a specified pore size. Gently shake it, so as to evenly spread the sample
on the sieve.
4.6.2.3.2 Place the sieve on the sieve base of the rotary airflow screen; put on the
sieve cover.
4.6.2.3.3 Turn on the airflow screen; simultaneously, press the stopwatch for
timekeeping. During sieving, control the negative work pressure to 3 103 Pa; use a
small wooden hammer to gently tap the screen cover or the screen frame, so that the
talc powder attached to the screen cover or the screen frame may fall into the sieve.
4.6.2.3.4 After sieving for 30 s, cut off the power supply and stop sieving.
4.6.2.3.5 Take out the test sieve, together with the sieve cover. Use a small brush
(without lint) to sweep the talc powder attached to the inner side of the sieve cover and
the inner periphery of the sieve frame into the test sieve. Conduct manual sieving for
15 s; tap for about 20 times.
4.6.2.3.6 In accordance with 4.6.2.4, check the end point of the sieving. When the ratio
of the mass of the sieve residue to the mass of the sample is less than 0.035%, then,
it is considered that the end of sieving has been reached. Otherwise, in accordance
with the steps of 4.6.2.3.2 ~ 4.6.2.3.4, continue the sieving for 15 s, then, check the
end point of the sieving. Repeat this process, until the end point has been reached.
4.6.2.3.7 After reaching the end of the sieving, transfer all the sieve residue to a watch
glass with an already-known mass; weigh it (accurate to 0.0001 g).
4.6.2.4 Sieving endpoint check
4.6.2.4.1 Put the test sieve with sieve residue on the clean bottom of the sieve. Lift the
sieve; lightly tap the sieve frame; tap for about 80 times per minute. After sieving for 1
min, stop the sieving.
4.6.2.4.2 Remove the bottom of the sieve; use a small wool sieve to transfer the sieve
residue on the bottom of the sieve into a watch glass with an already-known mass;
weigh it (accurate to 0.0001 g).
4.6.2.4.3 When the ratio of the mass of the sieve residue to the mass of the sample is
less than 0.035%, then, it is considered that the end of sieving has been reached.
4.6.3 Result calculation
The passing rate X2 [expressed in (%)] shall be calculated in accordance with Formula
(6):
Where,
m9---the mass of the beaker (or the watch glass) and the sieve residue, expressed in
(g);
m10---the mass of the beaker (or the watch glass), expressed in (g);
4.9 Method for Fineness Determination of Fine and Ultrafine Talc Powder
4.9.1 Materials and apparatuses
The materials and apparatuses required for the fineness determination of fine and
ultrafine talc powder are as follows:
a) Ultrasonic disperser;
b) Beaker: 200 mL;
c) Laser particle size analyzer: 0.1 μm ~ 1,000 μm;
d) Dispersion medium: sodium hexametaphosphate solution (2 g/L) or other
appropriate dispersing agents.
4.9.2 Test procedures
In accordance with GB/T 19077, conduct the test.
4.10 Method for Magnet Extract Determination of Talc Powder
4.10.1 Materials and apparatuses
The materials and apparatuses required for the determinatio...
Share
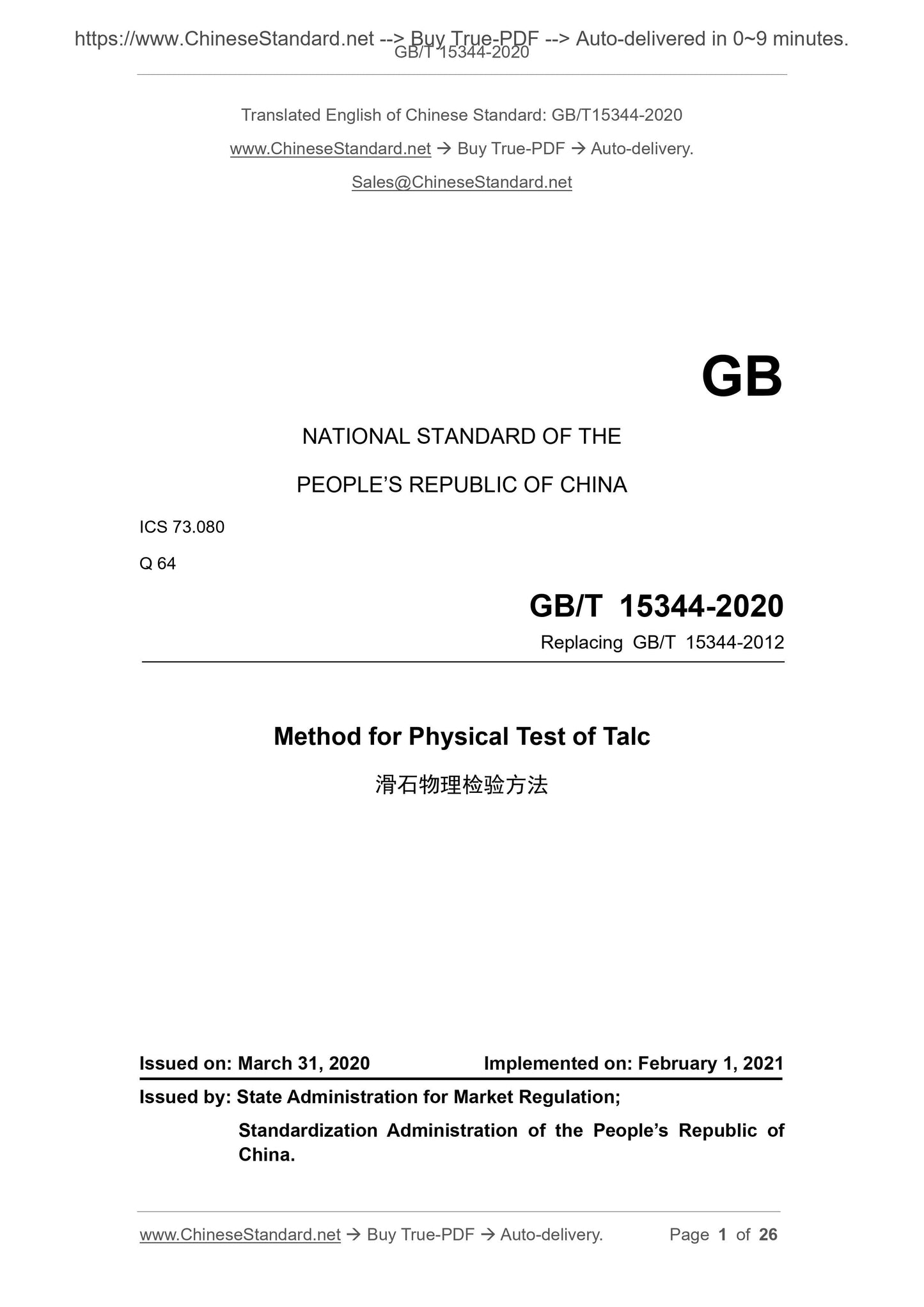
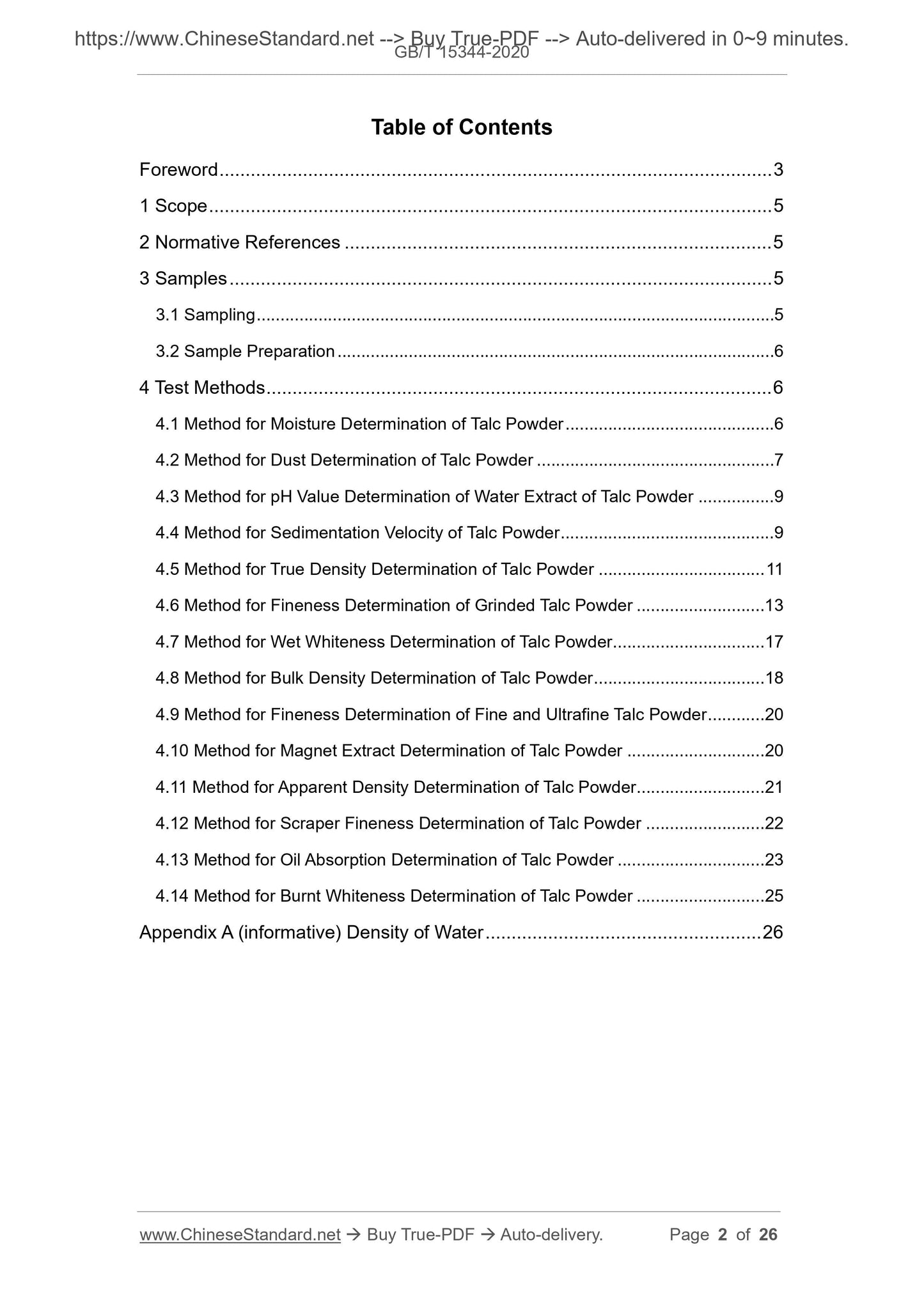
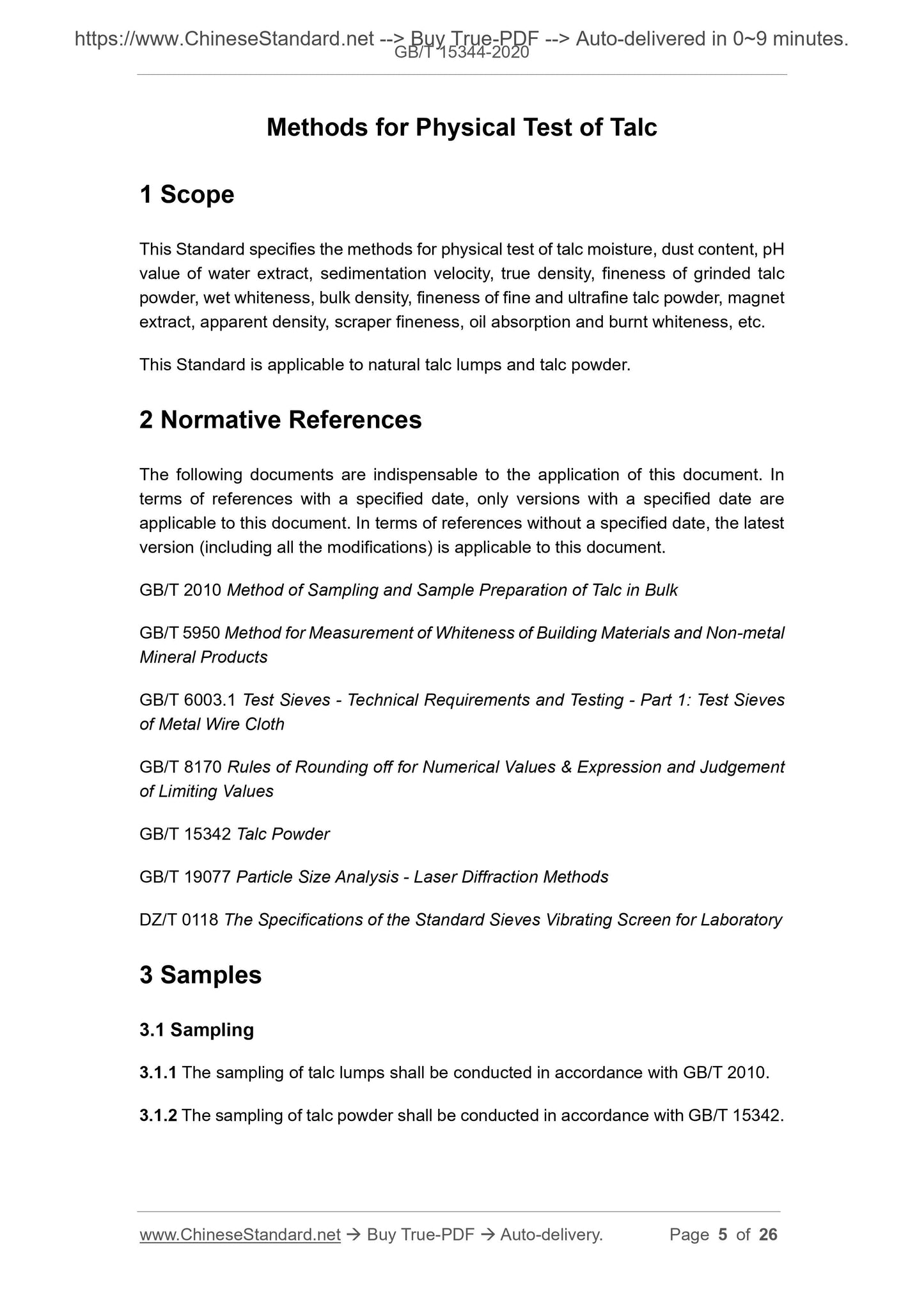

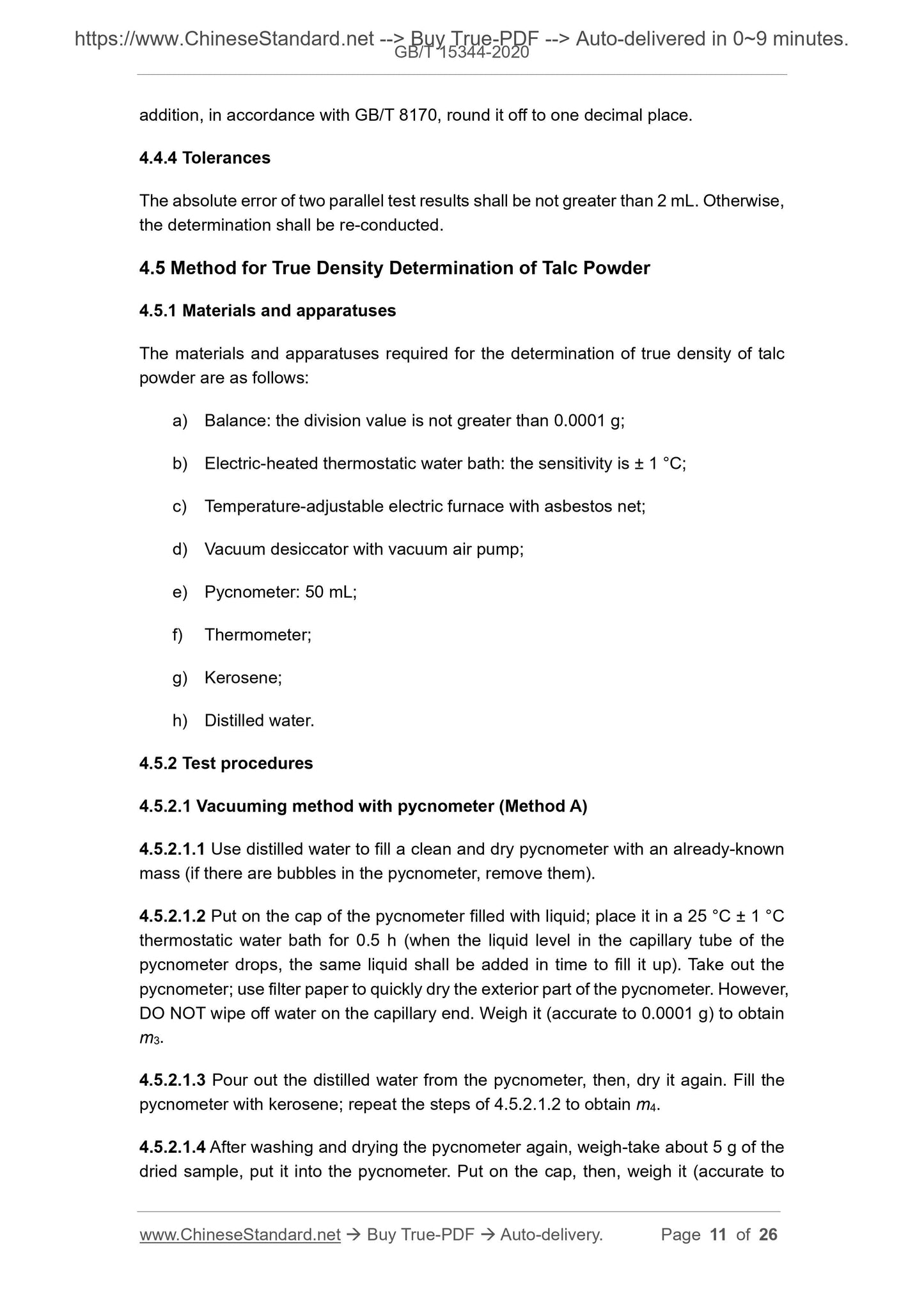
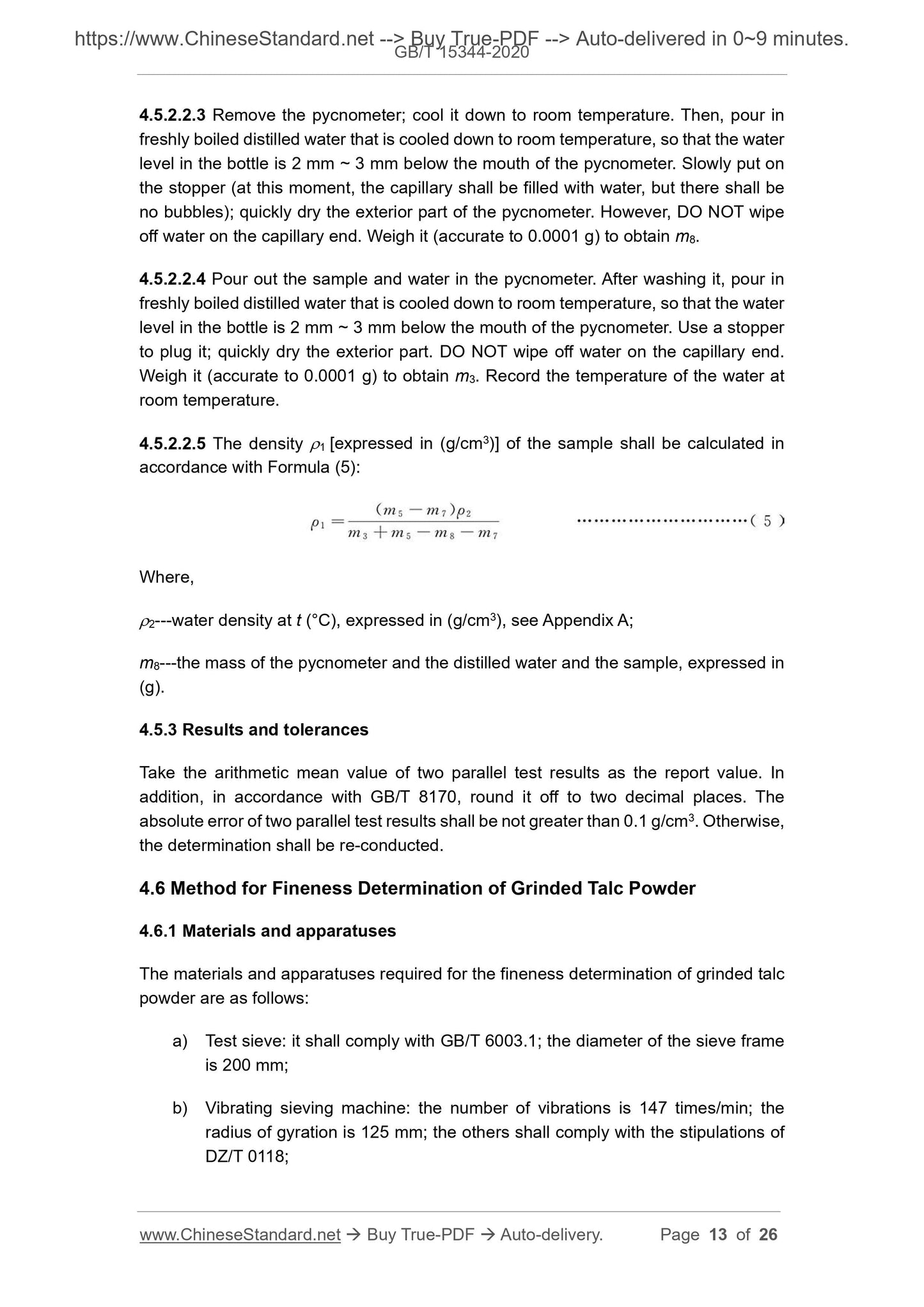
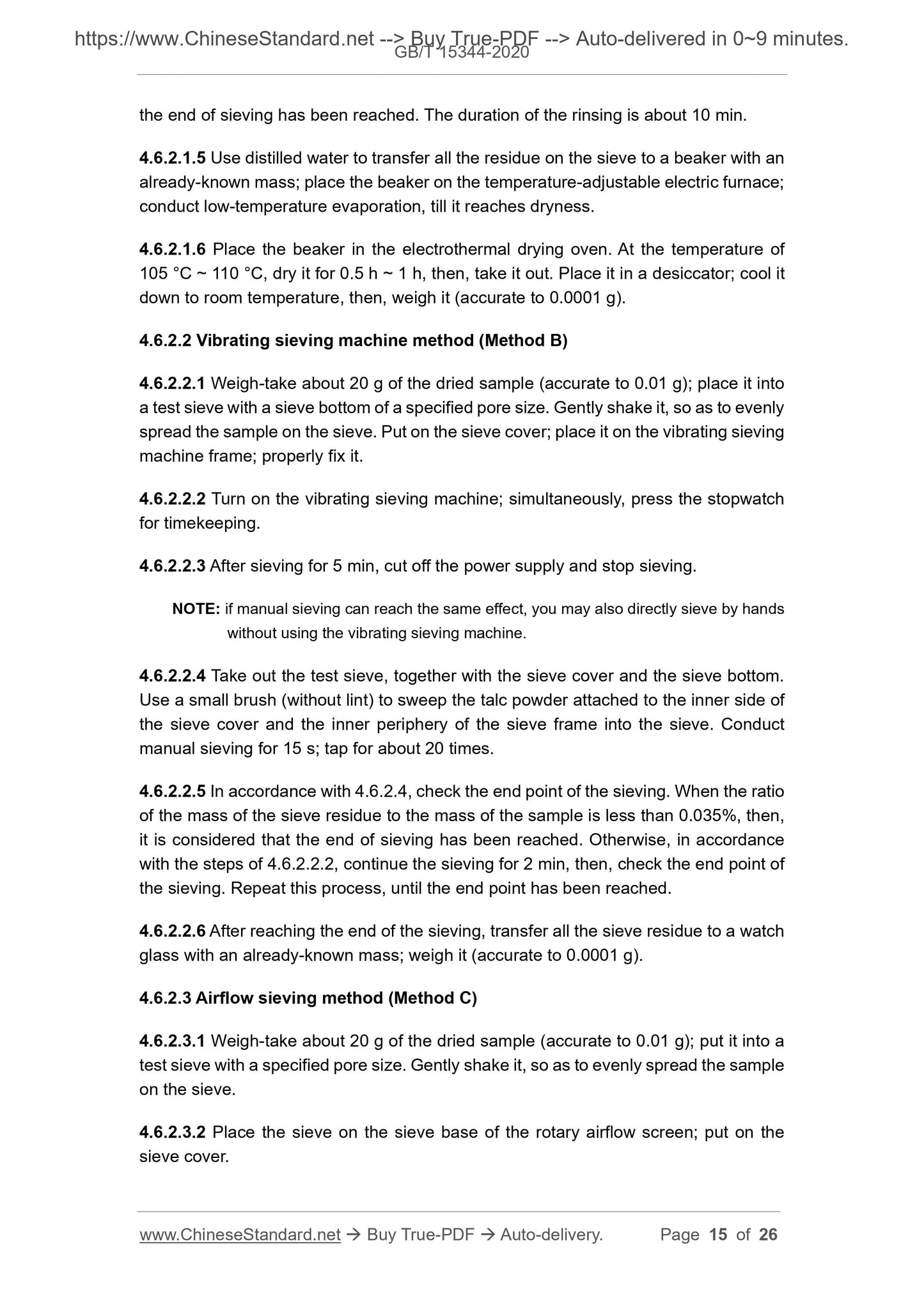
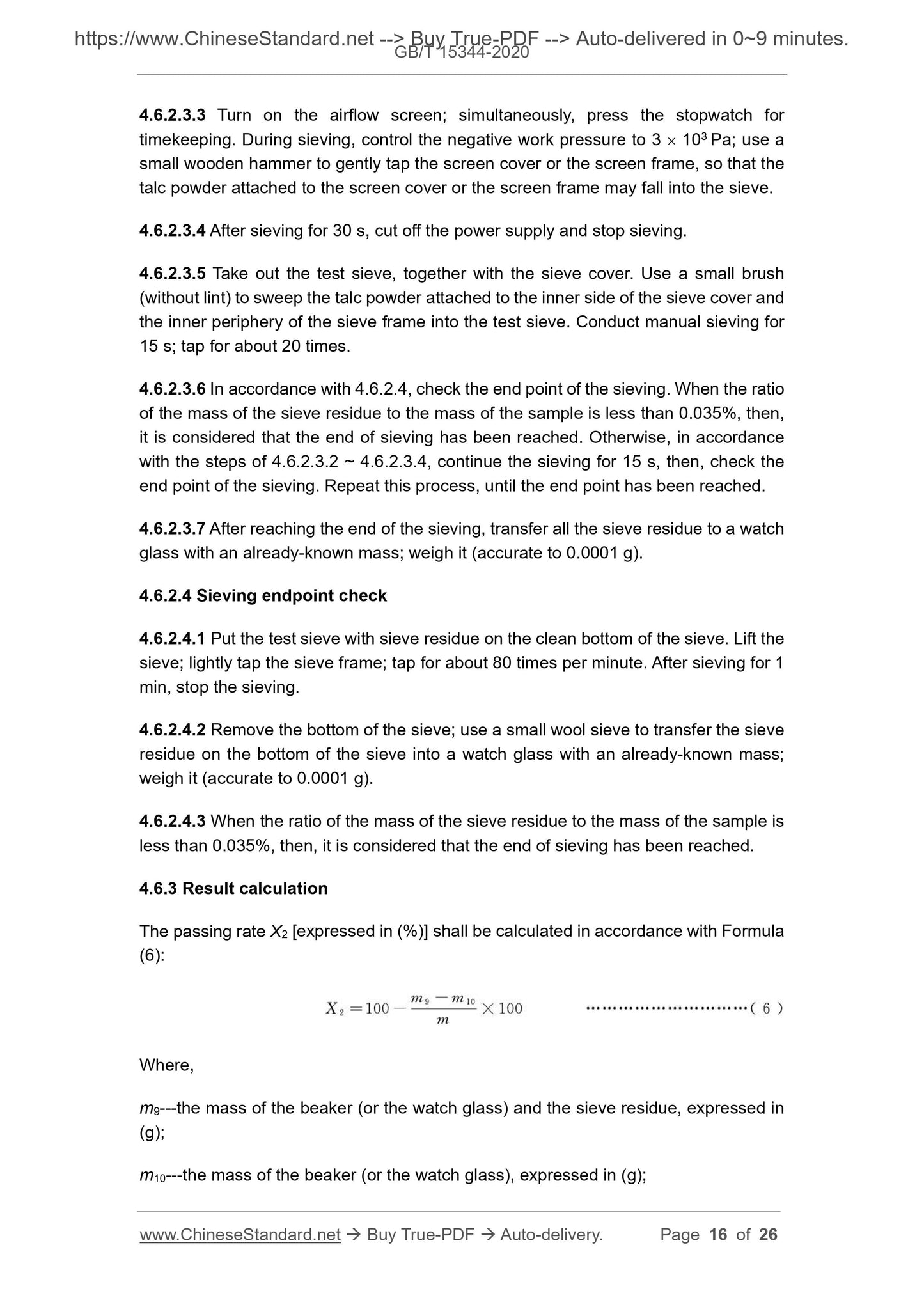
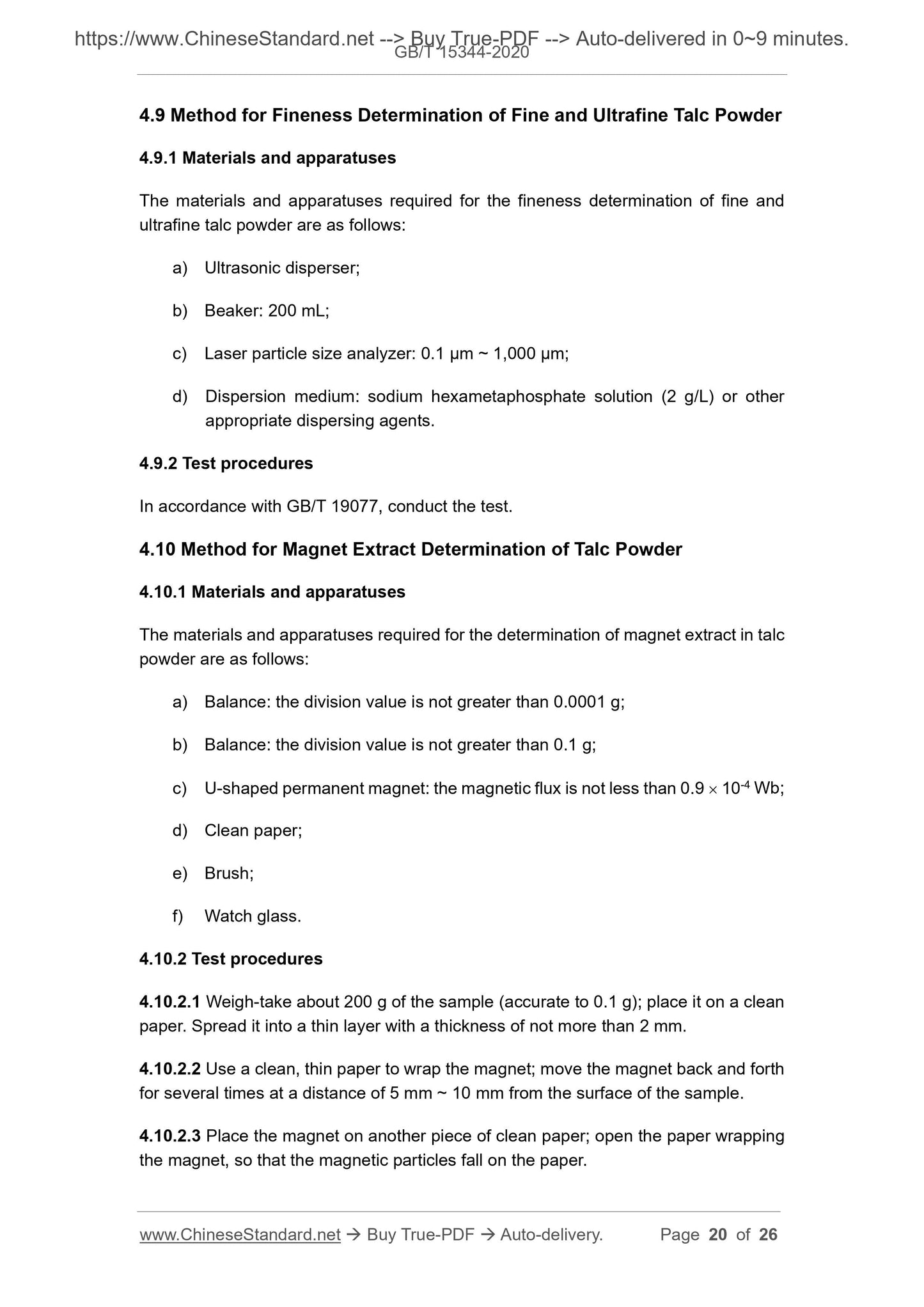
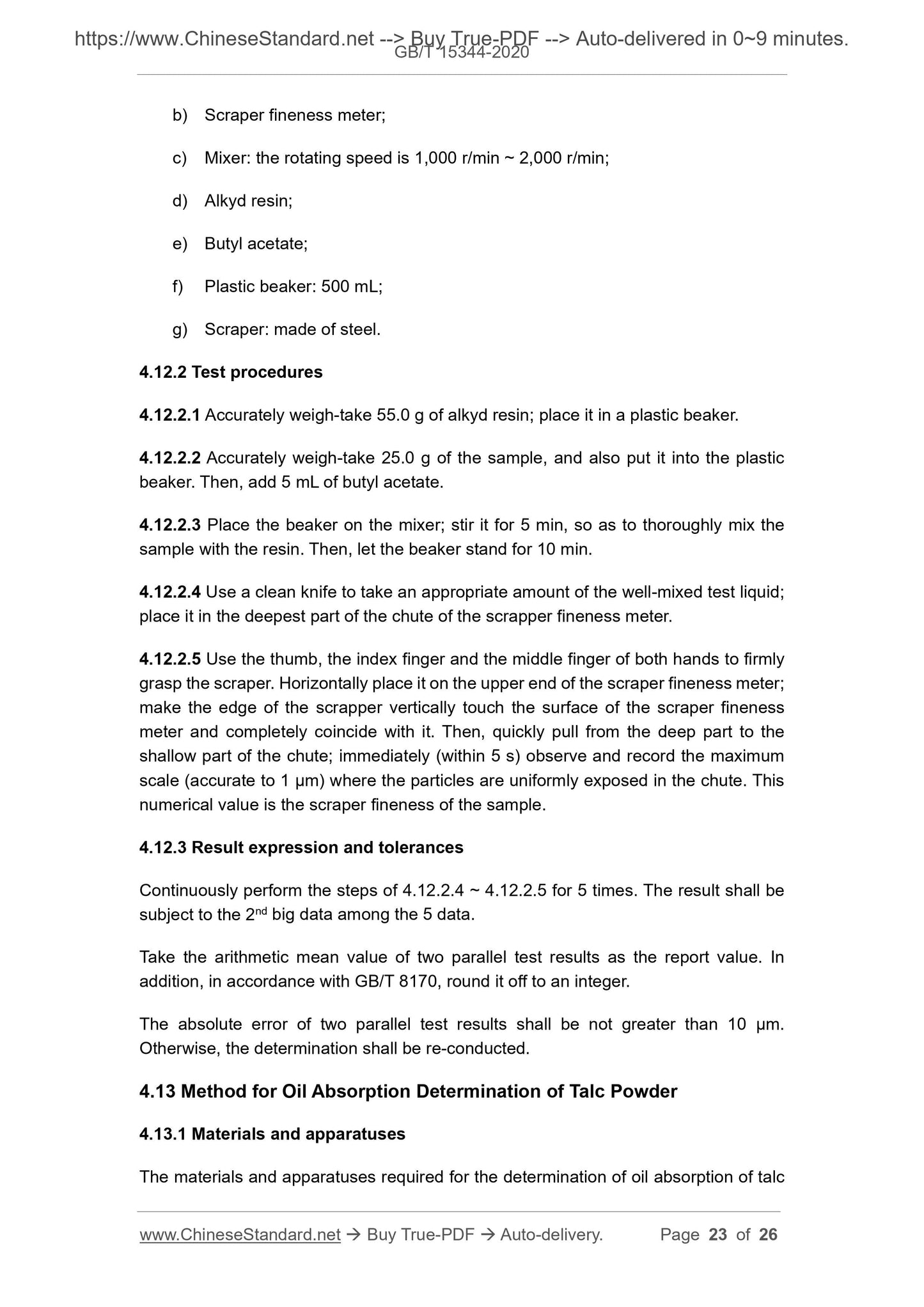
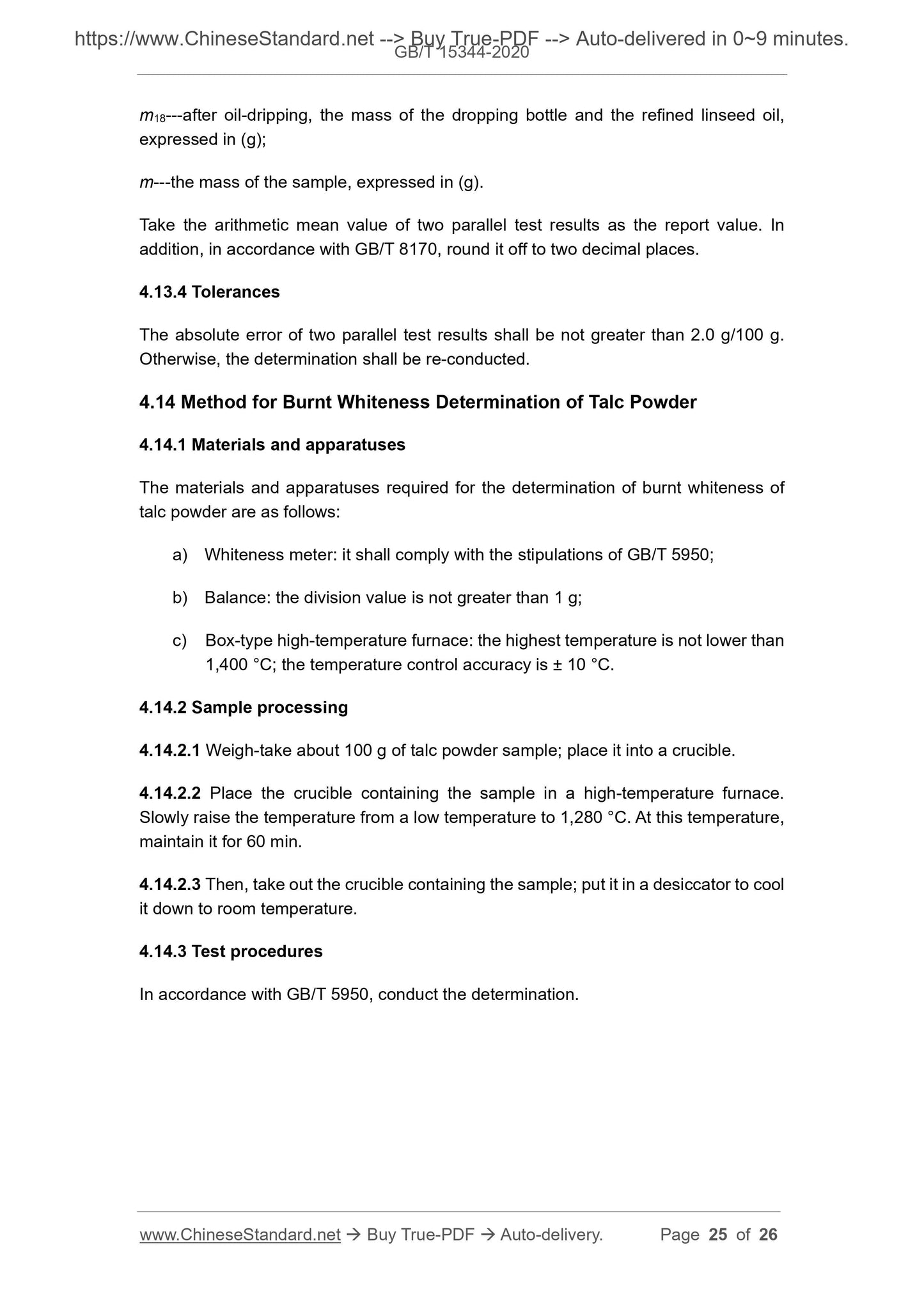