1
/
of
12
www.ChineseStandard.us -- Field Test Asia Pte. Ltd.
GB/T 24533-2019 English PDF (GB/T24533-2019)
GB/T 24533-2019 English PDF (GB/T24533-2019)
Regular price
$365.00
Regular price
Sale price
$365.00
Unit price
/
per
Shipping calculated at checkout.
Couldn't load pickup availability
GB/T 24533-2019: Graphite negative electrode materials for lithium ion battery
Delivery: 9 seconds. Download (& Email) true-PDF + Invoice.
Get Quotation: Click GB/T 24533-2019 (Self-service in 1-minute)
Historical versions (Master-website): GB/T 24533-2019
Preview True-PDF (Reload/Scroll-down if blank)
GB/T 24533-2019
GB
NATIONAL STANDARD OF THE
PEOPLE’S REPUBLIC OF CHINA
ICS 29.050
Q 51
Replacing GB/T 24533-2009
Graphite negative electrode materials for lithium ion
battery
ISSUED ON: MARCH 25, 2019
IMPLEMENTED ON: FEBRUARY 01, 2020
Issued by: State Administration for Market Regulation;
Standardization Administration of PRC.
Table of Contents
Foreword ... 4
1 Scope ... 8
2 Normative references ... 8
3 Terms and definitions ... 9
4 Classification and code ... 9
5 Technical requirements ... 11
6 Test methods ... 11
7 Inspection rules ... 13
8 Packaging, marking ... 14
9 Storage and transportation ... 15
Appendix A (Normative) Method for determination of particle size distribution
... 21
Appendix B (Normative) Method for determination of moisture content ... 25
Appendix C (Normative) Method for determination of pH ... 28
Appendix D (Normative) Method for determination of true density ... 30
Appendix E (Normative) Method for determination of interlayer spacing d002
... 33
Appendix F (Normative) Method for determination of graphite orientation ... 35
Appendix G (Normative) Method for determination of first coulomb efficiency
and first discharge specific capacity ... 38
Appendix H (Normative) Method for determination of trace metal elements .. 42
Appendix I (Normative) Method for determination of anions ... 45
Appendix J (Normative) Method for determination of sulfur content ... 49
Appendix K (Normative) Method for determination of magnetic substances .. 52
Appendix L (Normative) Method for determination of powder compaction
density ... 56
Appendix M (Normative) Method for determination of tap density ... 58
Graphite negative electrode materials for lithium ion
battery
1 Scope
This standard specifies the terms and definitions, classification and code,
technical requirements, test methods and inspection rules for graphite negative
electrode materials for lithium ion battery.
This standard applies to graphite-based negative electrode materials used as
negative electrodes for lithium ion batteries.
2 Normative references
The following documents are essential to the application of this document. For
the dated documents, only the versions with the dates indicated are applicable
to this document; for the undated documents, only the latest version (including
all the amendments) are applicable to this standard.
GB/T 191 Packaging - Pictorial marking for handling of goods
GB/T 1427 Sampling method for carbon material
GB/T 3120 Nickel wire
GB/T 3521 Method for chemical analysis of graphite
GB/T 3782 Acetylene black
GB/T 4369 Lithium
GB/T 5187 Foil of copper and copper alloy
GB/T 6388 Sign for transport packaging receipt and delivery
GB/T 6682 Water for analytical laboratory use - Specification and test
methods
GB/T 8170 Rules of rounding off for numerical values and expression and
judgement of limiting values
GB/T 9724 Chemical reagent - General rule for the determination of pH
- When the production equipment is shut down for more than half a year and
production is started again;
- When the customer has special requirements.
7.3 Acceptance rules
7.3.1 The product complies with all the technical indicators in Table 1, Table 3,
Table 4 and Table 5 as qualified products. If one of the indicators does not meet
the requirements of this standard, it shall be doubled from the sampling bag of
the same batch of products for re-inspection of the unqualified items. If all the
re-inspections are qualified, it is qualified; if one item fails, it is unqualified.
7.3.2 The manufacturer shall ensure that the exit-factory products meet the
requirements as stipulated in this standard. Each batch of products shall be
accompanied by an inspection report when exit-factory.
7.3.3 The re-inspection period of the consignee shall be two months. If there is
any objection, it shall be double-sampled and re-inspected. If there is still
dispute, it shall be inspected by a qualified third-party testing agency.
8 Packaging, marking
8.1 The packaging and marking of the product shall comply with the provisions
of GB/T 191. The net weight shall be negotiated between the supplier and the
purchaser.
8.2 The packaging shall be carried out under dry conditions. The product is first
placed into a waterproof packaging bag (PE sealed bag, aluminum plastic
sealed bag is recommended). Special packaging requirements are agreed
upon by the supplier and the purchaser.
8.3 The packaged product is then packaged by the outer packaging material,
which is agreed by the supplier and the purchaser.
8.4 The marking shall comply with the provisions of GB/T 6388, and generally
shall include the following contents, or may be marked according to customer
needs:
- Product name;
- Product code and specifications;
- This standard number;
- Net weight;
Appendix B
(Normative)
Method for determination of moisture content
B.1 Scope
This Appendix applies to the Karl Fischer Coulometric titrator to measure the
moisture content of the specimen.
B.2 Principle
The following reactions occur in the presence of water, iodine and sulfur dioxide
in the presence of organic bases and methanol:
H2O + I2 + SO2 + CH3OH + 3RN → [RHN]SO4CH3 + 2[RHN]I
The iodine therein is produced by electrochemically oxidizing the electrolytic
cell.
2I- → I2 + 2e-
The amount of iodine produced is proportional to the electric quantity passing
through the electrolytic cell, so the electric quantity consumed by electrolysis is
recorded, and according to Faraday's law, the moisture content of the specimen
(10.72 mC ≈ 1 µg H2O) can be obtained. Moisture content is expressed as a
percentage:
Water [%] = {(consumption [mC] ÷ 10.72 [mC/μg] - (drift [μg/min] × duration
[min]) - blank value [μg]) × 100 [%]} / {mass [g] × 106[mg/g]}
In order to obtain the moisture content expressed in ppm, it may be multiplied
by 10000. In order to obtain the moisture content expressed in grams/kilograms
(g/kg), it may be multiplied by 10.
B.3 Reagents and materials
B.3.1 Desiccant: 3A molecular sieve.
B.3.2 Electrolyte: Diaphragm-free electrolyte (commodity: shelf life, 5 years;
storage conditions: moisture-proof sealed).
B.4 Instruments and equipment
B.4.1 Karl Fischer coulometric titrator: The measurement range is 0.0001% ~
1%.
Appendix C
(Normative)
Method for determination of pH
C.1 Scope
This Appendix applies to the use of pH meter to test the pH value of the graphite
negative electrode materials.
C.2 Principle
Mix the specimen and the distilled water. Use pH meter to determine the pH
value of the specimen.
C.3 Reagents and materials
C.3.1 Pure water (GB/T 6682), grade-III.
Before use, put it in a chemically resistant glass container and boil for 5 min ~
10 min. Cover it to cool to room temperature. Let it be standing for not more
than 30 min.
C.3.2 In the analysis, unless otherwise specified, analytically pure or superior
grade reagents are used. The bagged pH standard substance with certificate
may be used according to the instruction manual. It may also be prepared
according to the provisions of GB/T 9724.
C.4 Instruments and equipment
C.4.1 Analytical balance: Sensitivity 0.0001 g.
C.4.2 pH meter: measuring range, 0 ~ 14, accuracy 0.02.
C.4.3 Glass beaker: 100 mL.
C.4.4 Ultrasonic cleaning instrument: Ultrasonic power 240 W.
C.4.5 Measuring cylinder: Capacity 50 mL.
C.4.6 The test environment is free of pollution by chemical gas such as acid
and alkali. During determination, the temperature of the specimen shall be
consistent with that of the buffer solution.
C.5 Preparation of specimens
C.5.1 Weigh 5.00 g of specimen, accurate to 0.01 g. Place it in a 100 mL glass
Appendix D
(Normative)
Method for determination of true density
D.1 Scope
This Appendix applies to the use of a true density tester to test the true density
of the specimens.
D.2 Principle
True density refers to the density as obtained through dividing the powder mass
(W) by the volume (true volume Vt) that does not include the voids inside and
outside the particle. Place the sample material into the true density tester. Use
helium as a medium. Gradually increase the pressure in the measurement
chamber to a specified value. Then the helium expands and enters the
expansion chamber. Use instrument to automatically record the equilibrium
pressure of the two processes. According to the law of conservation of mass,
after using the standard ball to calibrate the volume of the measurement
chamber and the expansion chamber, determine the true volume of the sample
material. Calculate the true density.
D.3 Reagents and materials
Helium, the purity of which is not less than 99.9%.
D.4 Instruments and equipment
D.4.1 True density tester.
D.4.2 Standard balls, the volume of which is about 7.0699 cm3, 70.699 cm3
respectively.
D.4.3 Series sample cells, the volume of which is about 10 cm3, 50 cm3, 135
cm3.
D.4.4 Electronic balance: The sensitivity is 0.0001 g.
D.5 Analytical procedures
D.5.1 Turn on the true density tester. Lead in the helium gas. Warm it up for 30
min. Check the air tightness of the gas path.
D.5.2 Before each test, use the standard ball to calibrate the instrument.
Appendix E
(Normative)
Method for determination of interlayer spacing d002
E.1 Scope
This Appendix applies to the use of X-ray diffractometer to test the interplanar
spacing d002 of the specimen.
E.2 Principle
The X-ray diffractometer automatically records the 002, 004, 110, 112 diffraction
line patterns of carbon; simultaneously reads the diffraction angle (2θobs)c;
uses the internal standard method to obtain the corrected diffraction angle
(2θcor)c; uses the formula (E.1) to calculate the interlayer spacing d002 of the
specimen. It is calculated according to the Bragg equation (E.1):
E.3 Reagents and materials
Single-crystal silicon powder: purity ≥ 99.99%.
Use an agate mortar to pulverize it. Use the silica powder which all passes the
45 μm (325 mesh) standard sieve as an internal standard substance for X-rays.
E.4 Instruments and equipment
E.4.1 Automatic recording X-ray diffractometer, with copper target Kα X-ray.
E.4.2 Electronic balance: The sensitivity is 0.0001 g.
E.4.3 Agate mortar.
E.5 Preparation of specimen
E.5.1 Weigh 1.5 g of silicon powder and 3.5 g of specimen (accurate to 0.0001
g). Place them in a mortar to grind it.
E.5.2 Add the ground and uniformly mixed sample to the groove of the sample
holder. Use the slide to press it tightly and flatten it.
E.6 Analytical procedures
E.6.1 Place the sample holder on the test bench of the X-ray diffractometer.
Appendix F
(Normative)
Method for determination of graphite orientation
F.1 Scope
This Appendix applies to the use of X-ray diffractometer to test the orientation
of specimen.
F.2 Principle
Add the binder and thickener into the specimen. Stir to uniformly distribute it.
Spread it on an aluminum foil. Dry it. After drying, scrape off the sample. Use
an agate mortar to grind it finely. Make it pass through a 74 μm (200 mesh)
standard sieve. Use a compaction densitometer to compact the sample powder
into the tablet of a predetermined size. After the tablet is rebounded for a certain
period of time, measure the compaction density. Use the X-ray diffractometer
to test the orientation.
The X-ray diffractometer automatically record the 002, 004, 110, 112 diffraction
line patterns of the graphite samples. Read the heights of the 002, 004, 110
crystal plane diffraction peaks. Calculate the graphite orientations I002/I110 and
I004/I110.
F.3 Reagents and materials
F.3.1 Binder: Styrene-butadiene rubber (SBR) powder, superior grade, model
SN-307R, prepared with pure water to make 50% slurry.
F.3.2 Thickener: Sodium carboxymethylcellulose (CMC), analytically pure,
model BVH8, prepared with pure water to make 1.2% solution.
F.3.3 Pure water: It meets the requirements of the grade-III water or above in
the standard GB/T 6682.
F.3.4 Aluminum foil: The purity is more than 99.9%.
F.4 Instruments and equipment
F.4.1 Automatic recording type X-ray diffractometer, with copper target Kα X-
ray.
F.4.2 Electronic balance: The sensitivity is 0.0001 g.
F.4.3 Agate mortar.
F.4.4 High-speed disperser, or other mixing-dispersing equipment.
F.4.5 Constant temperature drying oven, with a working temperature above
95 °C.
F.4.6 Compaction densitometer, with a maximum pressure of more than 25 kN.
F.4.7 Standard screen, 74 μm (200 mesh).
F.4.8 Thickness gauge.
F.4.9 Dryer.
F.5 Preparation of specimen
F.5.1 Weigh 19.3 g of specimen, 25.0 g of thickener (see F.3.2), 0.8 g of binder
(see F.3.1) in a clean plastic container, accurate to 0.0001 g.
F.5.2 Use a high-speed disperser or other stirring-dispersing equipment to
disperse the above mixed sample fully and uniformly. Then uniformly spread it
on aluminum foil (see F.3.4). Place it in a constant temperature drying oven.
Dry it at 95 °C for more than 6 h.
F.5.3 Scrape off the dried sample into agate mortar. Fully grind it finely. Make it
pass through a standard sieve of 74 μm (200 mesh).
F.5.4 Weigh 4 parts of the ground and sieved sample 0.50 g ± 0.001 g, accurate
to 0.0001 g. Respectively, place them in the mold of the compaction
densitometer. Respectively at the pressure of 2.5 kN, 5.0 kN, 14.5 kN, 24.5 kN,
prepare it into tablet. The pressure is held for 30 s.
F.5.5 The prepared 4 tablets are separately packed in a clean sample bag and
placed in a desiccator. Avoid the tablet from bearing pressure. Let it be standing
for 16 h. Then take out the tablet. Use the thickness gauge to test the thickness
of the tablet. Calculate the compaction density of each tablet. Take records.
After finishing the test of compaction density of tablet, test the orientation within
8 h. Otherwise, it shall...
Delivery: 9 seconds. Download (& Email) true-PDF + Invoice.
Get Quotation: Click GB/T 24533-2019 (Self-service in 1-minute)
Historical versions (Master-website): GB/T 24533-2019
Preview True-PDF (Reload/Scroll-down if blank)
GB/T 24533-2019
GB
NATIONAL STANDARD OF THE
PEOPLE’S REPUBLIC OF CHINA
ICS 29.050
Q 51
Replacing GB/T 24533-2009
Graphite negative electrode materials for lithium ion
battery
ISSUED ON: MARCH 25, 2019
IMPLEMENTED ON: FEBRUARY 01, 2020
Issued by: State Administration for Market Regulation;
Standardization Administration of PRC.
Table of Contents
Foreword ... 4
1 Scope ... 8
2 Normative references ... 8
3 Terms and definitions ... 9
4 Classification and code ... 9
5 Technical requirements ... 11
6 Test methods ... 11
7 Inspection rules ... 13
8 Packaging, marking ... 14
9 Storage and transportation ... 15
Appendix A (Normative) Method for determination of particle size distribution
... 21
Appendix B (Normative) Method for determination of moisture content ... 25
Appendix C (Normative) Method for determination of pH ... 28
Appendix D (Normative) Method for determination of true density ... 30
Appendix E (Normative) Method for determination of interlayer spacing d002
... 33
Appendix F (Normative) Method for determination of graphite orientation ... 35
Appendix G (Normative) Method for determination of first coulomb efficiency
and first discharge specific capacity ... 38
Appendix H (Normative) Method for determination of trace metal elements .. 42
Appendix I (Normative) Method for determination of anions ... 45
Appendix J (Normative) Method for determination of sulfur content ... 49
Appendix K (Normative) Method for determination of magnetic substances .. 52
Appendix L (Normative) Method for determination of powder compaction
density ... 56
Appendix M (Normative) Method for determination of tap density ... 58
Graphite negative electrode materials for lithium ion
battery
1 Scope
This standard specifies the terms and definitions, classification and code,
technical requirements, test methods and inspection rules for graphite negative
electrode materials for lithium ion battery.
This standard applies to graphite-based negative electrode materials used as
negative electrodes for lithium ion batteries.
2 Normative references
The following documents are essential to the application of this document. For
the dated documents, only the versions with the dates indicated are applicable
to this document; for the undated documents, only the latest version (including
all the amendments) are applicable to this standard.
GB/T 191 Packaging - Pictorial marking for handling of goods
GB/T 1427 Sampling method for carbon material
GB/T 3120 Nickel wire
GB/T 3521 Method for chemical analysis of graphite
GB/T 3782 Acetylene black
GB/T 4369 Lithium
GB/T 5187 Foil of copper and copper alloy
GB/T 6388 Sign for transport packaging receipt and delivery
GB/T 6682 Water for analytical laboratory use - Specification and test
methods
GB/T 8170 Rules of rounding off for numerical values and expression and
judgement of limiting values
GB/T 9724 Chemical reagent - General rule for the determination of pH
- When the production equipment is shut down for more than half a year and
production is started again;
- When the customer has special requirements.
7.3 Acceptance rules
7.3.1 The product complies with all the technical indicators in Table 1, Table 3,
Table 4 and Table 5 as qualified products. If one of the indicators does not meet
the requirements of this standard, it shall be doubled from the sampling bag of
the same batch of products for re-inspection of the unqualified items. If all the
re-inspections are qualified, it is qualified; if one item fails, it is unqualified.
7.3.2 The manufacturer shall ensure that the exit-factory products meet the
requirements as stipulated in this standard. Each batch of products shall be
accompanied by an inspection report when exit-factory.
7.3.3 The re-inspection period of the consignee shall be two months. If there is
any objection, it shall be double-sampled and re-inspected. If there is still
dispute, it shall be inspected by a qualified third-party testing agency.
8 Packaging, marking
8.1 The packaging and marking of the product shall comply with the provisions
of GB/T 191. The net weight shall be negotiated between the supplier and the
purchaser.
8.2 The packaging shall be carried out under dry conditions. The product is first
placed into a waterproof packaging bag (PE sealed bag, aluminum plastic
sealed bag is recommended). Special packaging requirements are agreed
upon by the supplier and the purchaser.
8.3 The packaged product is then packaged by the outer packaging material,
which is agreed by the supplier and the purchaser.
8.4 The marking shall comply with the provisions of GB/T 6388, and generally
shall include the following contents, or may be marked according to customer
needs:
- Product name;
- Product code and specifications;
- This standard number;
- Net weight;
Appendix B
(Normative)
Method for determination of moisture content
B.1 Scope
This Appendix applies to the Karl Fischer Coulometric titrator to measure the
moisture content of the specimen.
B.2 Principle
The following reactions occur in the presence of water, iodine and sulfur dioxide
in the presence of organic bases and methanol:
H2O + I2 + SO2 + CH3OH + 3RN → [RHN]SO4CH3 + 2[RHN]I
The iodine therein is produced by electrochemically oxidizing the electrolytic
cell.
2I- → I2 + 2e-
The amount of iodine produced is proportional to the electric quantity passing
through the electrolytic cell, so the electric quantity consumed by electrolysis is
recorded, and according to Faraday's law, the moisture content of the specimen
(10.72 mC ≈ 1 µg H2O) can be obtained. Moisture content is expressed as a
percentage:
Water [%] = {(consumption [mC] ÷ 10.72 [mC/μg] - (drift [μg/min] × duration
[min]) - blank value [μg]) × 100 [%]} / {mass [g] × 106[mg/g]}
In order to obtain the moisture content expressed in ppm, it may be multiplied
by 10000. In order to obtain the moisture content expressed in grams/kilograms
(g/kg), it may be multiplied by 10.
B.3 Reagents and materials
B.3.1 Desiccant: 3A molecular sieve.
B.3.2 Electrolyte: Diaphragm-free electrolyte (commodity: shelf life, 5 years;
storage conditions: moisture-proof sealed).
B.4 Instruments and equipment
B.4.1 Karl Fischer coulometric titrator: The measurement range is 0.0001% ~
1%.
Appendix C
(Normative)
Method for determination of pH
C.1 Scope
This Appendix applies to the use of pH meter to test the pH value of the graphite
negative electrode materials.
C.2 Principle
Mix the specimen and the distilled water. Use pH meter to determine the pH
value of the specimen.
C.3 Reagents and materials
C.3.1 Pure water (GB/T 6682), grade-III.
Before use, put it in a chemically resistant glass container and boil for 5 min ~
10 min. Cover it to cool to room temperature. Let it be standing for not more
than 30 min.
C.3.2 In the analysis, unless otherwise specified, analytically pure or superior
grade reagents are used. The bagged pH standard substance with certificate
may be used according to the instruction manual. It may also be prepared
according to the provisions of GB/T 9724.
C.4 Instruments and equipment
C.4.1 Analytical balance: Sensitivity 0.0001 g.
C.4.2 pH meter: measuring range, 0 ~ 14, accuracy 0.02.
C.4.3 Glass beaker: 100 mL.
C.4.4 Ultrasonic cleaning instrument: Ultrasonic power 240 W.
C.4.5 Measuring cylinder: Capacity 50 mL.
C.4.6 The test environment is free of pollution by chemical gas such as acid
and alkali. During determination, the temperature of the specimen shall be
consistent with that of the buffer solution.
C.5 Preparation of specimens
C.5.1 Weigh 5.00 g of specimen, accurate to 0.01 g. Place it in a 100 mL glass
Appendix D
(Normative)
Method for determination of true density
D.1 Scope
This Appendix applies to the use of a true density tester to test the true density
of the specimens.
D.2 Principle
True density refers to the density as obtained through dividing the powder mass
(W) by the volume (true volume Vt) that does not include the voids inside and
outside the particle. Place the sample material into the true density tester. Use
helium as a medium. Gradually increase the pressure in the measurement
chamber to a specified value. Then the helium expands and enters the
expansion chamber. Use instrument to automatically record the equilibrium
pressure of the two processes. According to the law of conservation of mass,
after using the standard ball to calibrate the volume of the measurement
chamber and the expansion chamber, determine the true volume of the sample
material. Calculate the true density.
D.3 Reagents and materials
Helium, the purity of which is not less than 99.9%.
D.4 Instruments and equipment
D.4.1 True density tester.
D.4.2 Standard balls, the volume of which is about 7.0699 cm3, 70.699 cm3
respectively.
D.4.3 Series sample cells, the volume of which is about 10 cm3, 50 cm3, 135
cm3.
D.4.4 Electronic balance: The sensitivity is 0.0001 g.
D.5 Analytical procedures
D.5.1 Turn on the true density tester. Lead in the helium gas. Warm it up for 30
min. Check the air tightness of the gas path.
D.5.2 Before each test, use the standard ball to calibrate the instrument.
Appendix E
(Normative)
Method for determination of interlayer spacing d002
E.1 Scope
This Appendix applies to the use of X-ray diffractometer to test the interplanar
spacing d002 of the specimen.
E.2 Principle
The X-ray diffractometer automatically records the 002, 004, 110, 112 diffraction
line patterns of carbon; simultaneously reads the diffraction angle (2θobs)c;
uses the internal standard method to obtain the corrected diffraction angle
(2θcor)c; uses the formula (E.1) to calculate the interlayer spacing d002 of the
specimen. It is calculated according to the Bragg equation (E.1):
E.3 Reagents and materials
Single-crystal silicon powder: purity ≥ 99.99%.
Use an agate mortar to pulverize it. Use the silica powder which all passes the
45 μm (325 mesh) standard sieve as an internal standard substance for X-rays.
E.4 Instruments and equipment
E.4.1 Automatic recording X-ray diffractometer, with copper target Kα X-ray.
E.4.2 Electronic balance: The sensitivity is 0.0001 g.
E.4.3 Agate mortar.
E.5 Preparation of specimen
E.5.1 Weigh 1.5 g of silicon powder and 3.5 g of specimen (accurate to 0.0001
g). Place them in a mortar to grind it.
E.5.2 Add the ground and uniformly mixed sample to the groove of the sample
holder. Use the slide to press it tightly and flatten it.
E.6 Analytical procedures
E.6.1 Place the sample holder on the test bench of the X-ray diffractometer.
Appendix F
(Normative)
Method for determination of graphite orientation
F.1 Scope
This Appendix applies to the use of X-ray diffractometer to test the orientation
of specimen.
F.2 Principle
Add the binder and thickener into the specimen. Stir to uniformly distribute it.
Spread it on an aluminum foil. Dry it. After drying, scrape off the sample. Use
an agate mortar to grind it finely. Make it pass through a 74 μm (200 mesh)
standard sieve. Use a compaction densitometer to compact the sample powder
into the tablet of a predetermined size. After the tablet is rebounded for a certain
period of time, measure the compaction density. Use the X-ray diffractometer
to test the orientation.
The X-ray diffractometer automatically record the 002, 004, 110, 112 diffraction
line patterns of the graphite samples. Read the heights of the 002, 004, 110
crystal plane diffraction peaks. Calculate the graphite orientations I002/I110 and
I004/I110.
F.3 Reagents and materials
F.3.1 Binder: Styrene-butadiene rubber (SBR) powder, superior grade, model
SN-307R, prepared with pure water to make 50% slurry.
F.3.2 Thickener: Sodium carboxymethylcellulose (CMC), analytically pure,
model BVH8, prepared with pure water to make 1.2% solution.
F.3.3 Pure water: It meets the requirements of the grade-III water or above in
the standard GB/T 6682.
F.3.4 Aluminum foil: The purity is more than 99.9%.
F.4 Instruments and equipment
F.4.1 Automatic recording type X-ray diffractometer, with copper target Kα X-
ray.
F.4.2 Electronic balance: The sensitivity is 0.0001 g.
F.4.3 Agate mortar.
F.4.4 High-speed disperser, or other mixing-dispersing equipment.
F.4.5 Constant temperature drying oven, with a working temperature above
95 °C.
F.4.6 Compaction densitometer, with a maximum pressure of more than 25 kN.
F.4.7 Standard screen, 74 μm (200 mesh).
F.4.8 Thickness gauge.
F.4.9 Dryer.
F.5 Preparation of specimen
F.5.1 Weigh 19.3 g of specimen, 25.0 g of thickener (see F.3.2), 0.8 g of binder
(see F.3.1) in a clean plastic container, accurate to 0.0001 g.
F.5.2 Use a high-speed disperser or other stirring-dispersing equipment to
disperse the above mixed sample fully and uniformly. Then uniformly spread it
on aluminum foil (see F.3.4). Place it in a constant temperature drying oven.
Dry it at 95 °C for more than 6 h.
F.5.3 Scrape off the dried sample into agate mortar. Fully grind it finely. Make it
pass through a standard sieve of 74 μm (200 mesh).
F.5.4 Weigh 4 parts of the ground and sieved sample 0.50 g ± 0.001 g, accurate
to 0.0001 g. Respectively, place them in the mold of the compaction
densitometer. Respectively at the pressure of 2.5 kN, 5.0 kN, 14.5 kN, 24.5 kN,
prepare it into tablet. The pressure is held for 30 s.
F.5.5 The prepared 4 tablets are separately packed in a clean sample bag and
placed in a desiccator. Avoid the tablet from bearing pressure. Let it be standing
for 16 h. Then take out the tablet. Use the thickness gauge to test the thickness
of the tablet. Calculate the compaction density of each tablet. Take records.
After finishing the test of compaction density of tablet, test the orientation within
8 h. Otherwise, it shall...
Share
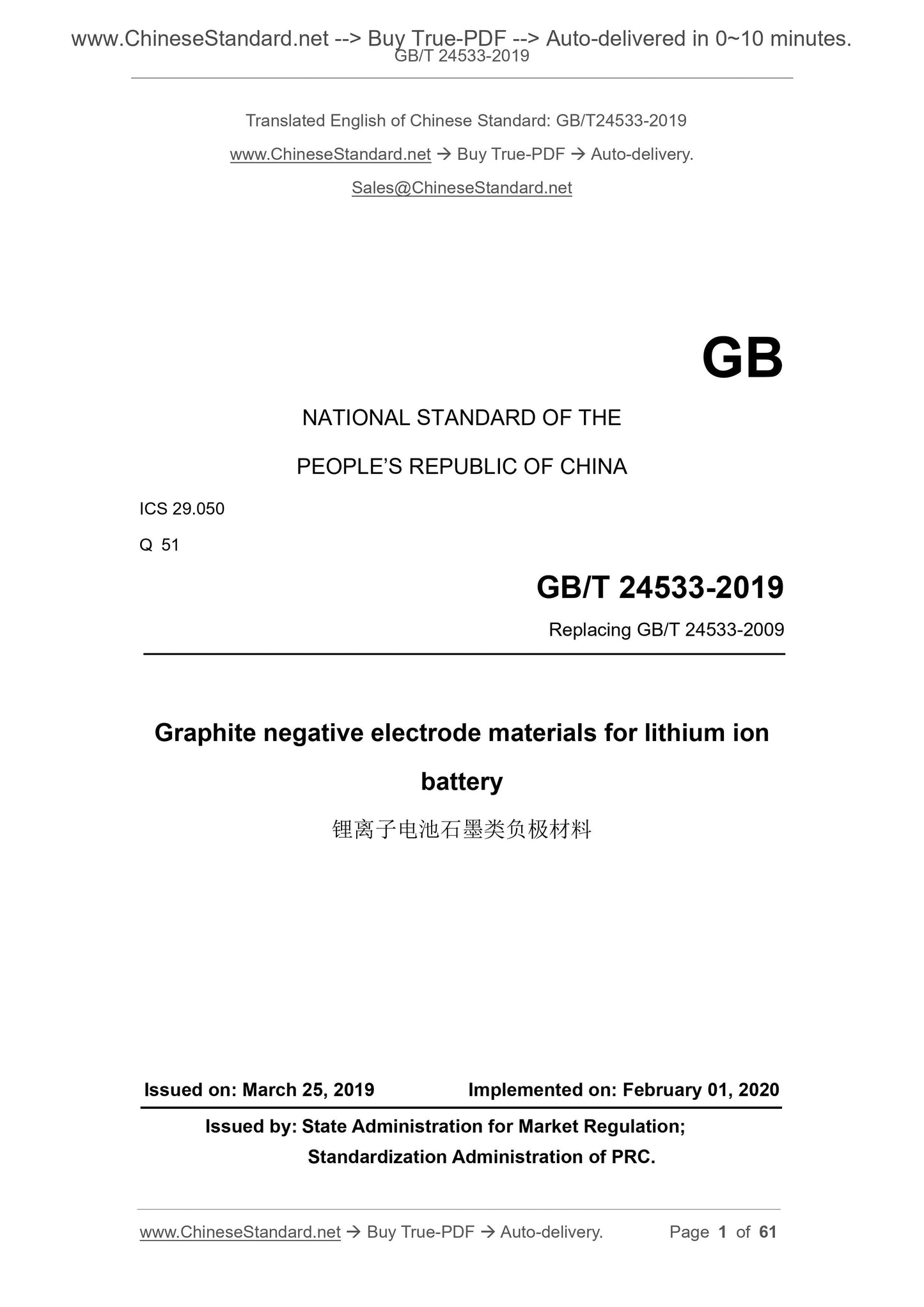
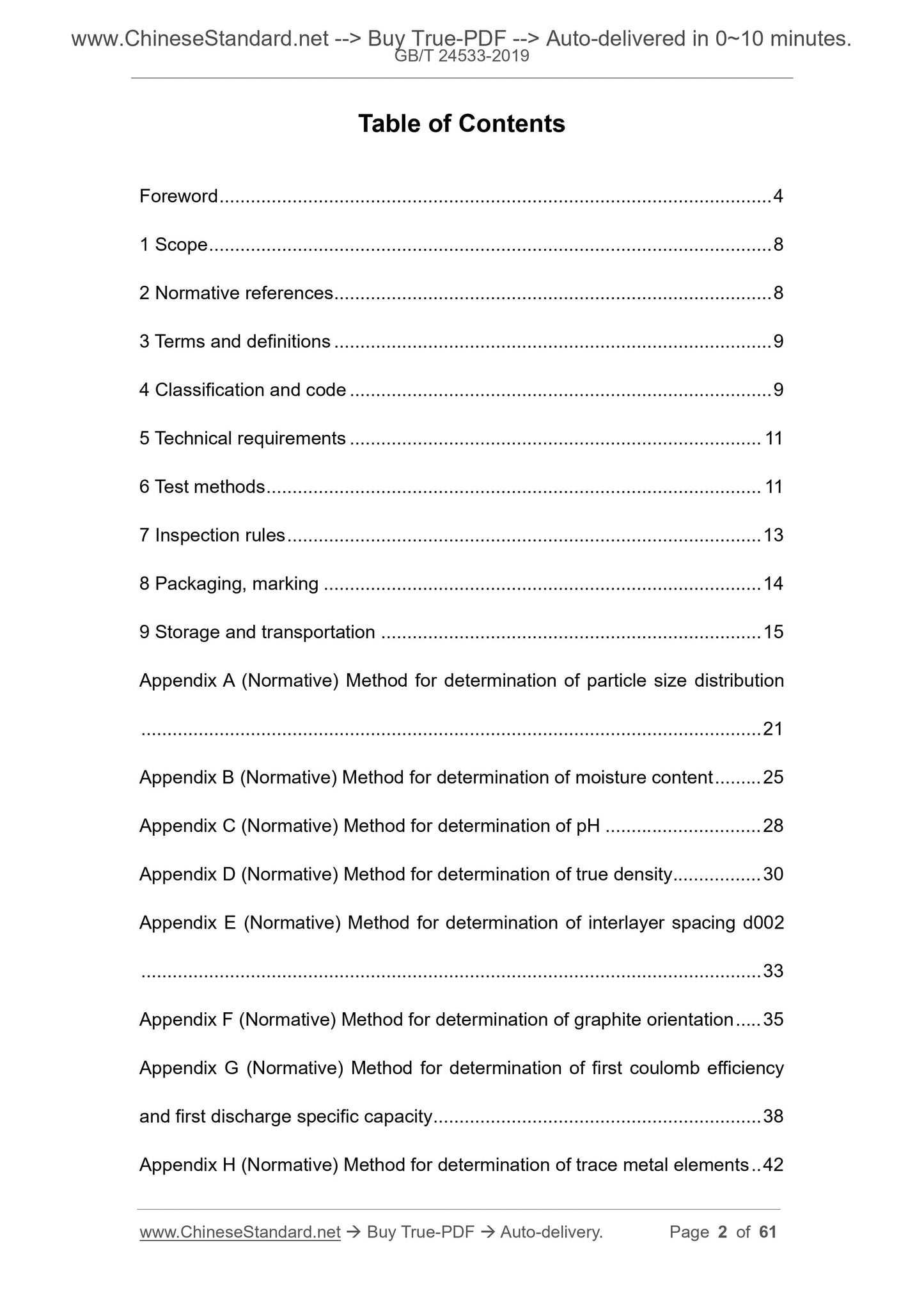
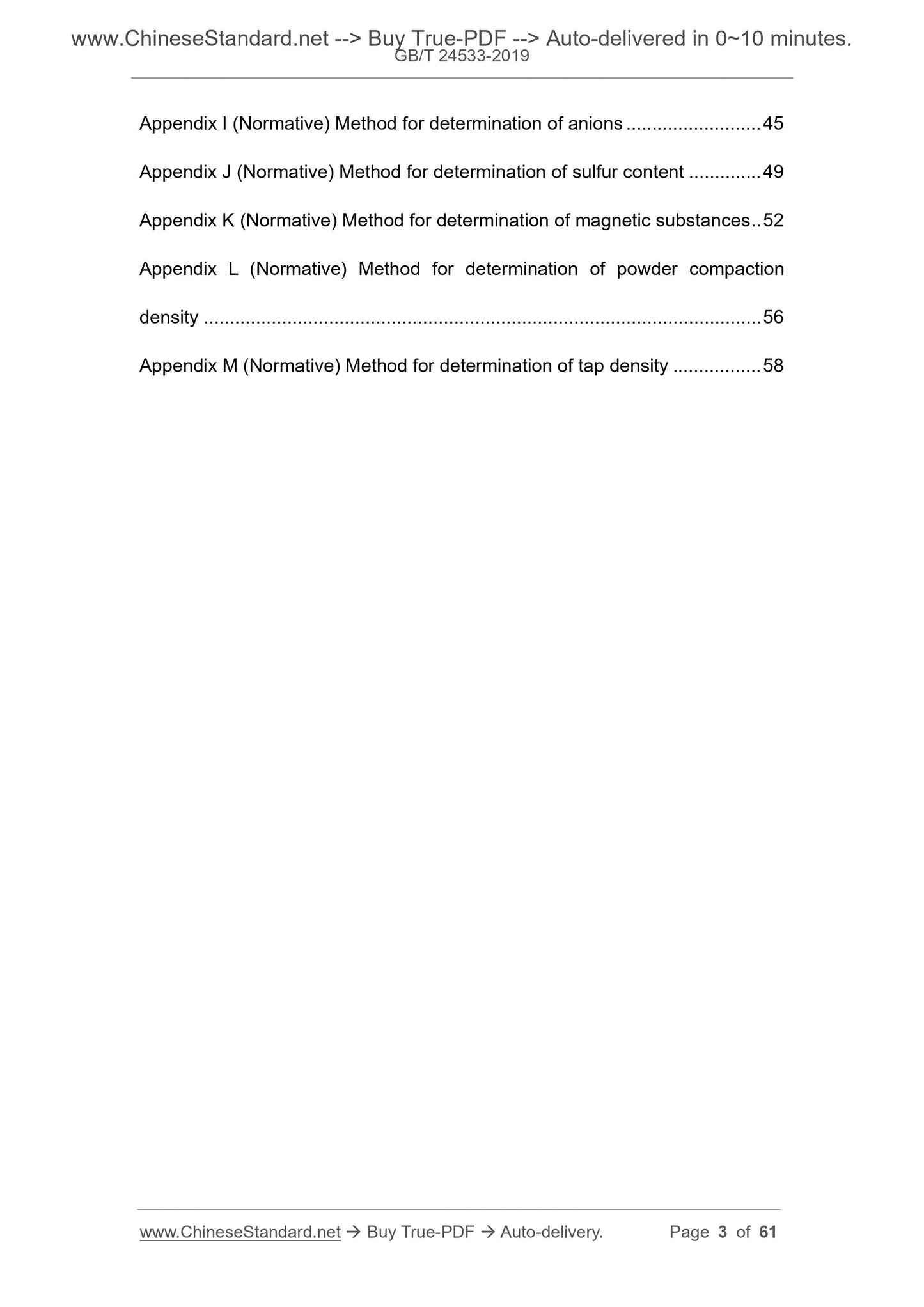
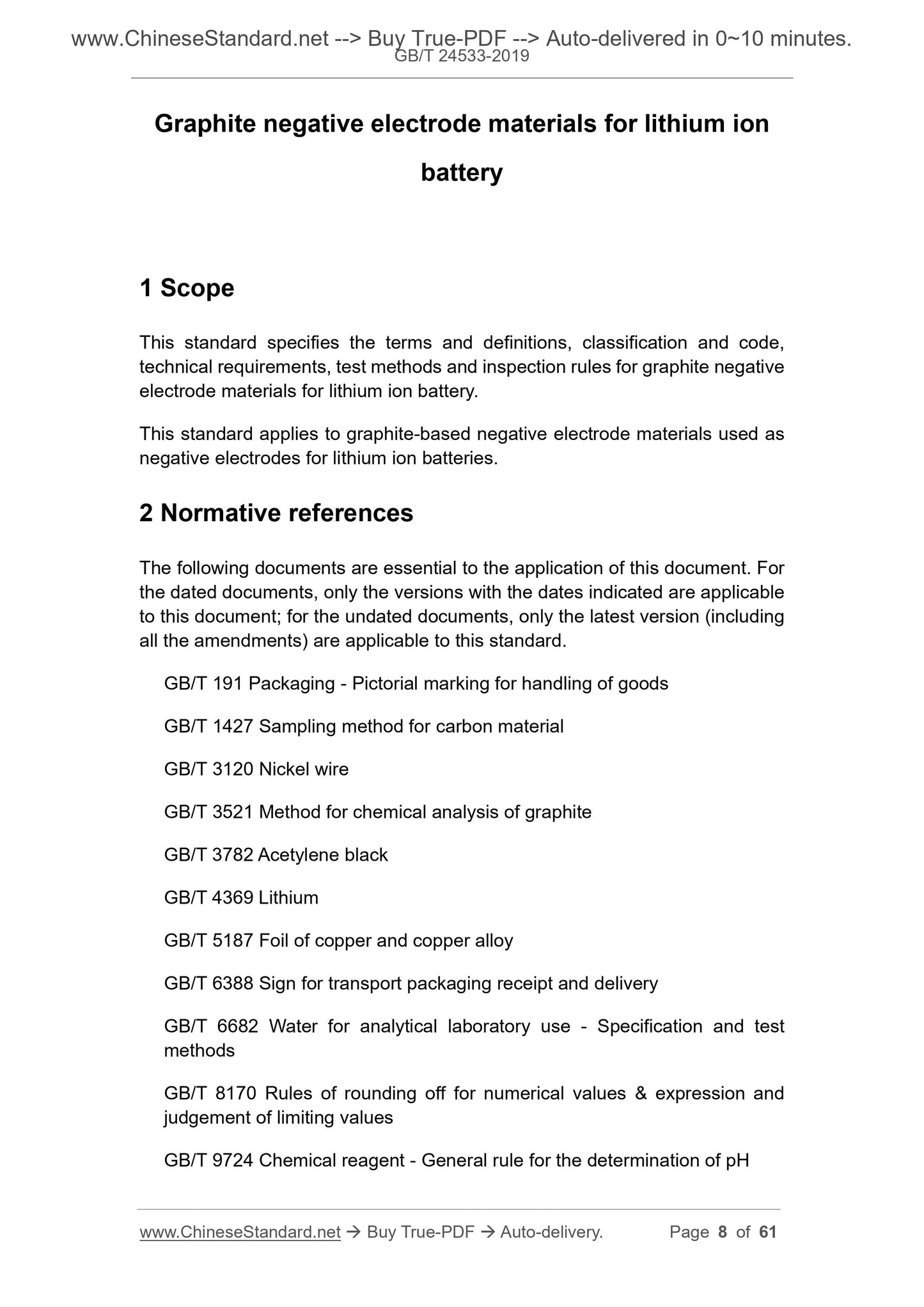
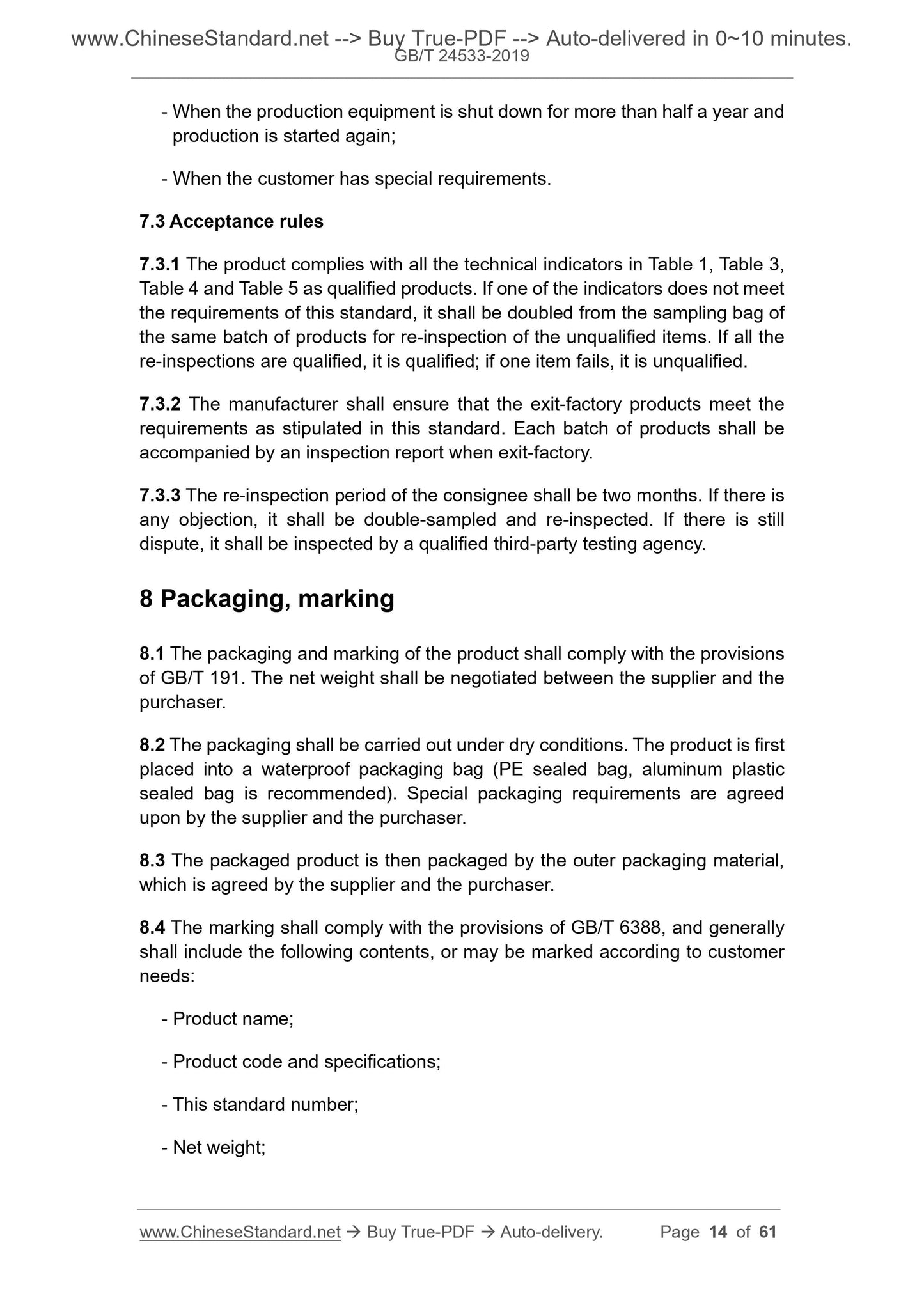
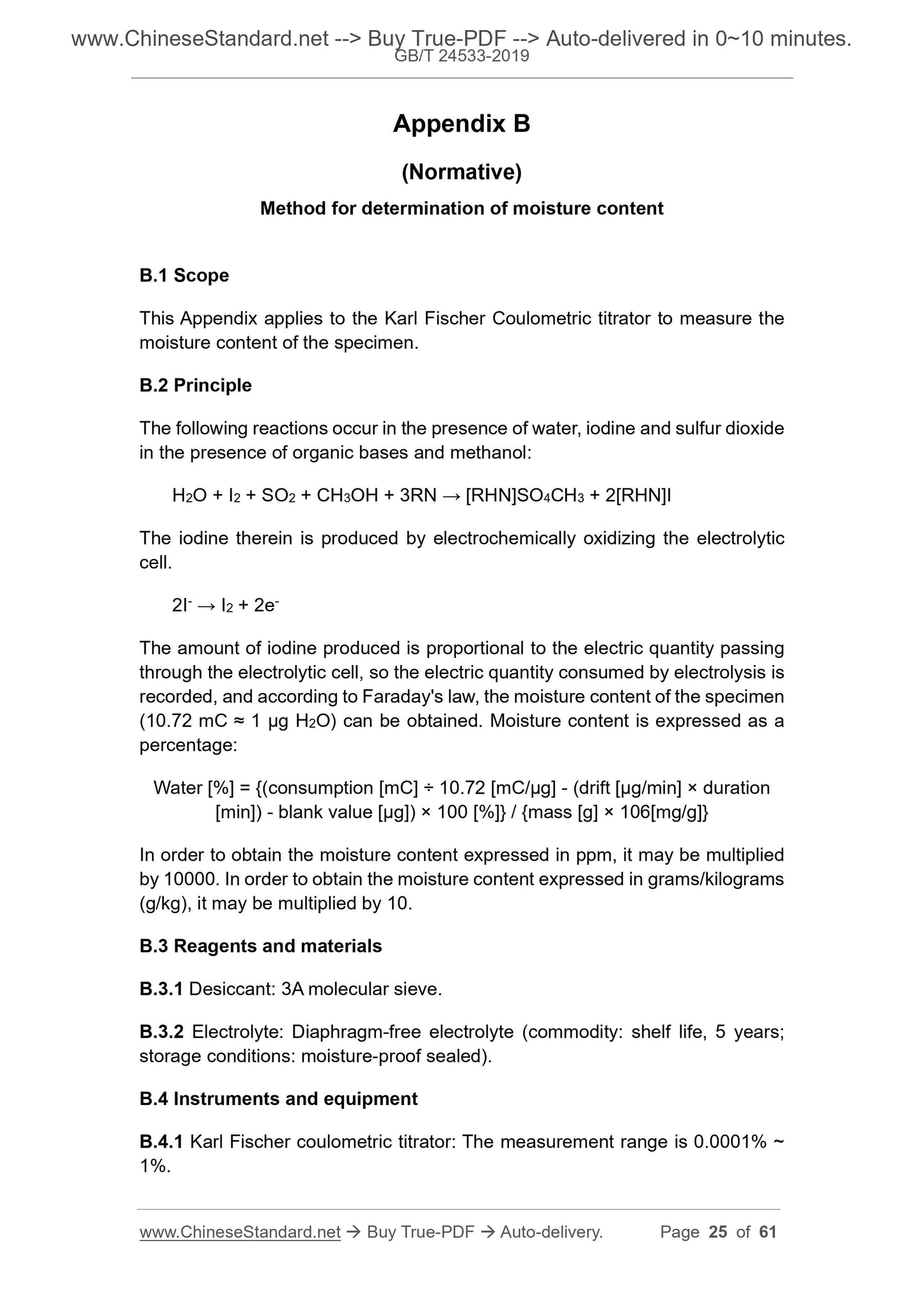
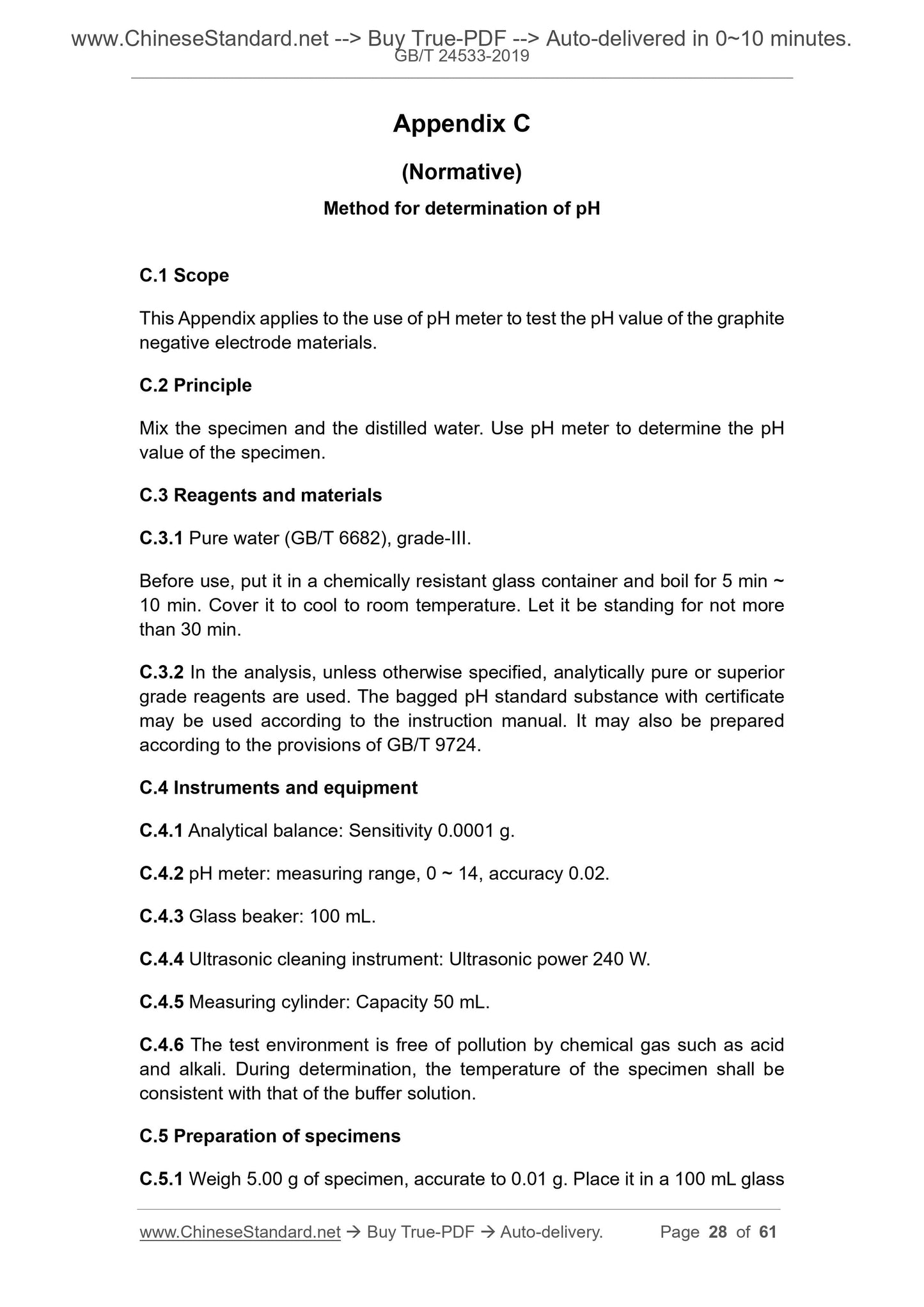
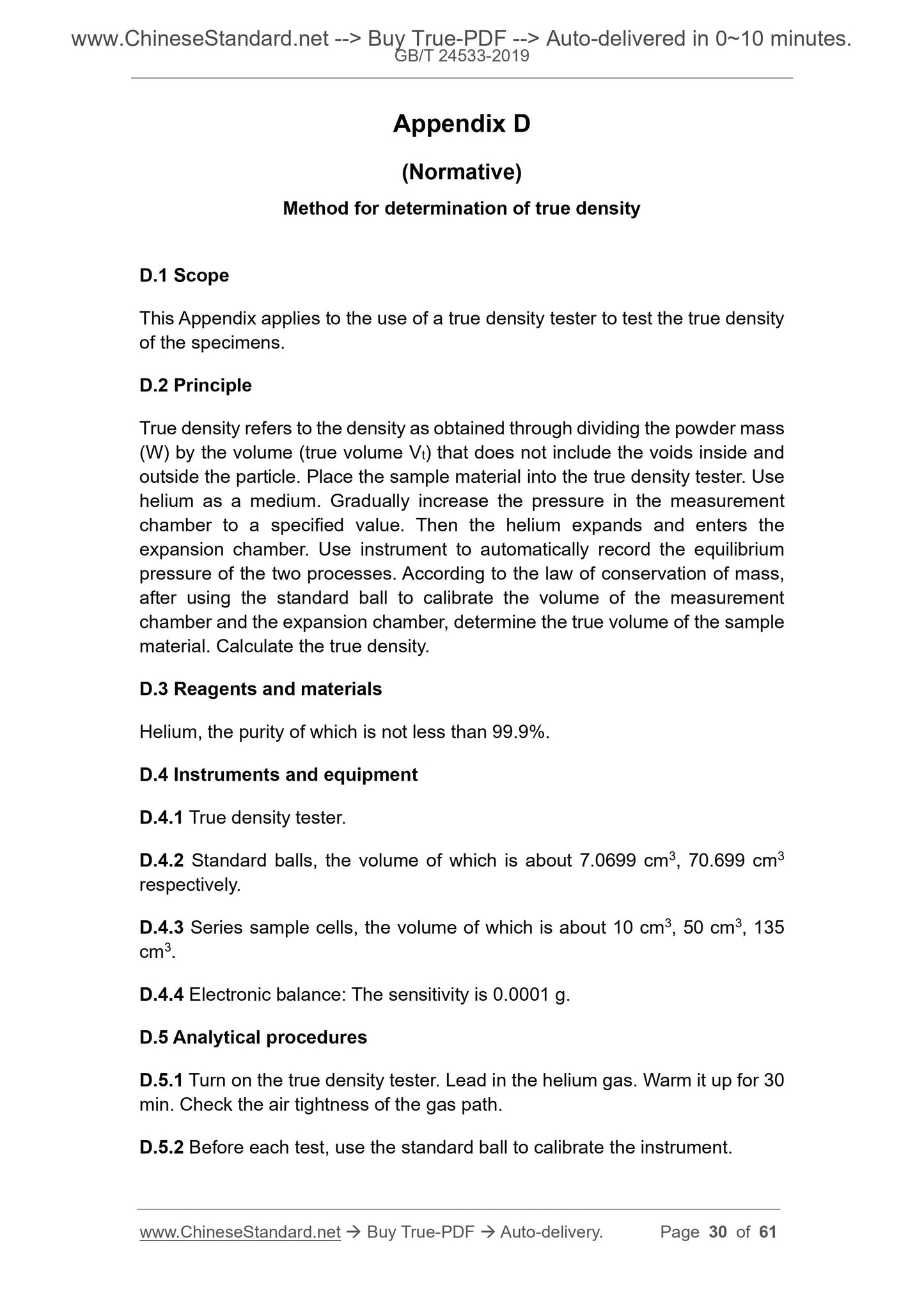
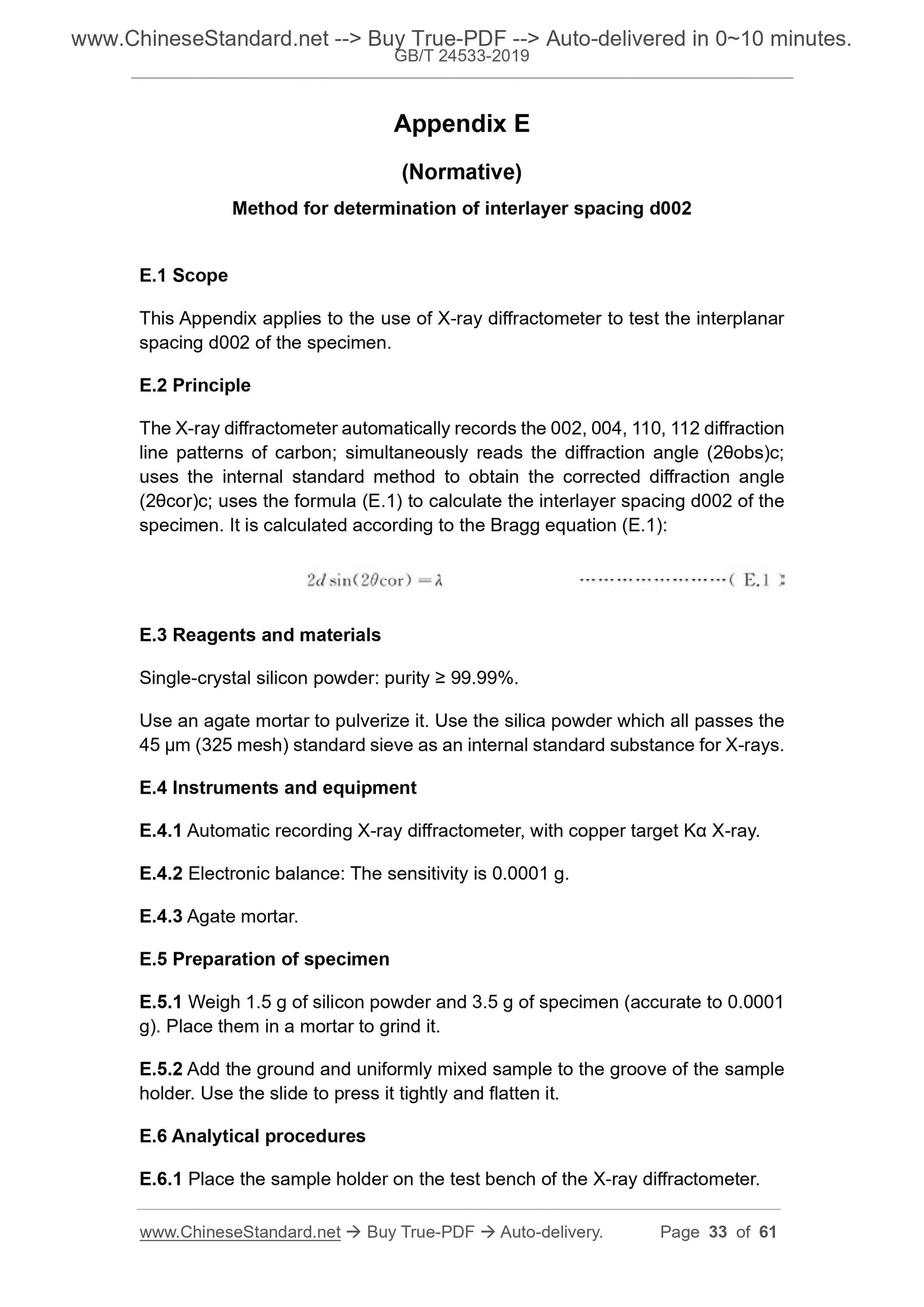
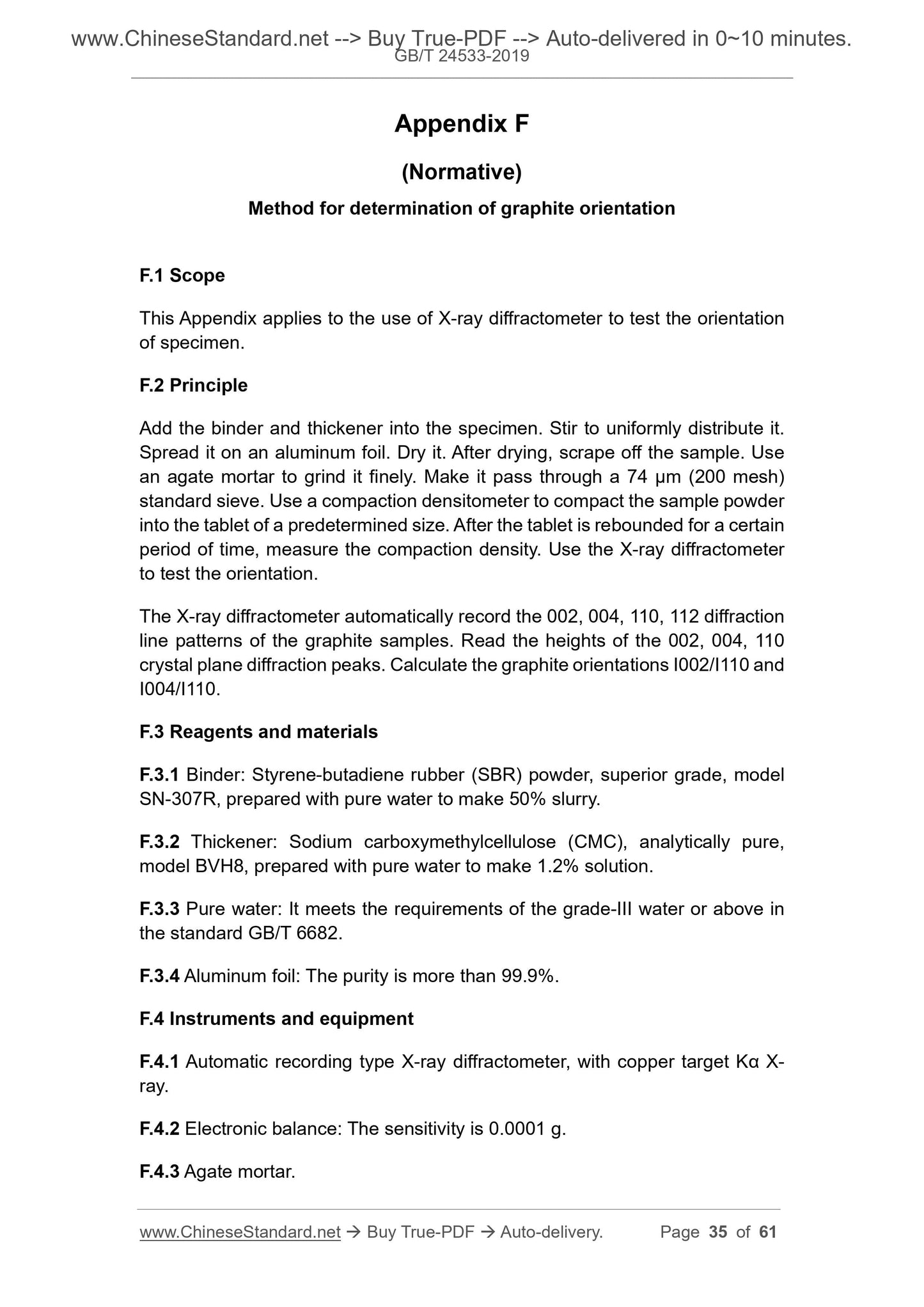
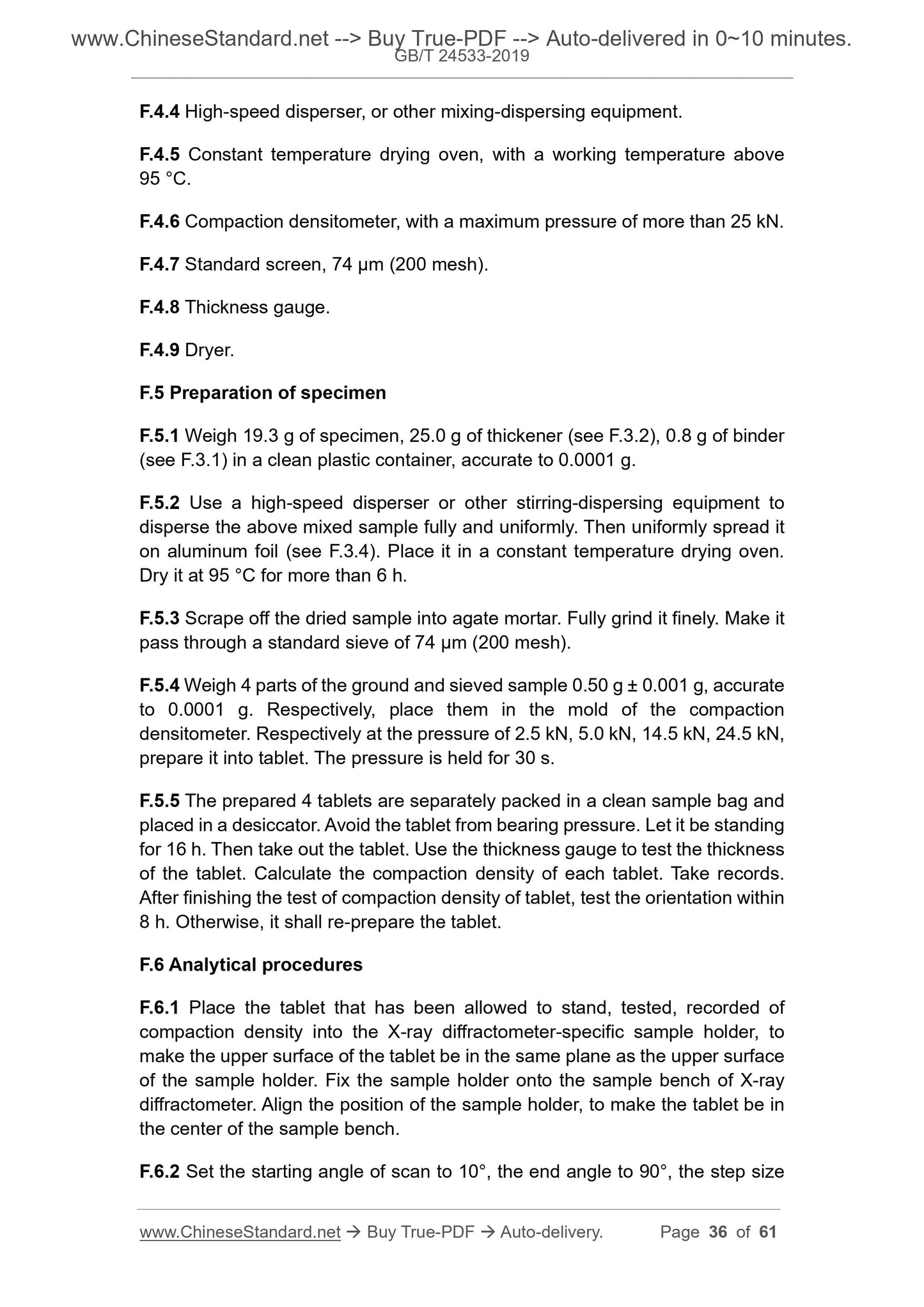
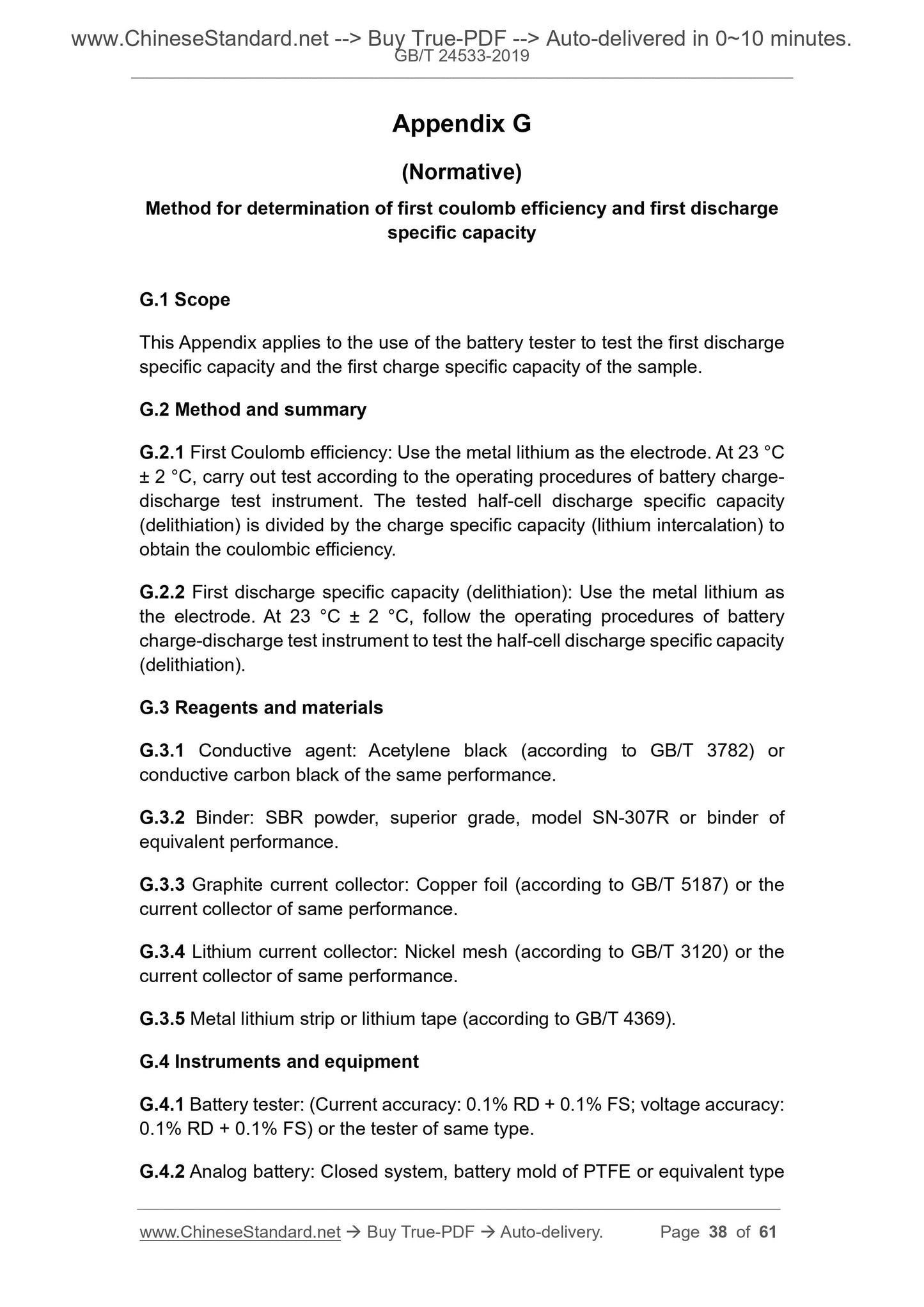