1
/
of
5
PayPal, credit cards. Download editable-PDF & invoice In 1 second!
GB/T 36173-2018 English PDF (GBT36173-2018)
GB/T 36173-2018 English PDF (GBT36173-2018)
Regular price
$120.00 USD
Regular price
Sale price
$120.00 USD
Unit price
/
per
Shipping calculated at checkout.
Couldn't load pickup availability
Delivery: 3 seconds. Download true-PDF + Invoice.
Get Quotation: Click GB/T 36173-2018 (Self-service in 1-minute)
Historical versions (Master-website): GB/T 36173-2018
Preview True-PDF (Reload/Scroll-down if blank)
GB/T 36173-2018: Restrained joint systems for ductile iron pipelines -- Design rules and type testing
GB/T 36173-2018
Restrained joint systems for ductile iron pipelines--Design rules and type testing
ICS 23.040.10; 23.040.60
H48
National Standards of People's Republic of China
Self-anchoring interface system for ductile iron pipeline
Design regulations and type tests
(ISO 10804..2010, MOD)
Published on.2018-05-14
Implementation of.2019-02-01
State Market Supervisory Administration
China National Standardization Administration issued
Content
Foreword III
1 range 1
2 Normative references 1
3 Terms and Definitions 1
4 Design Regulations 1
5 type test 2
Appendix A (informative) Structural changes in this standard compared to ISO 10804.2010 4
Appendix B (informative) The technical differences between this standard and ISO 10804.2010 and their causes 5
Foreword
This standard was drafted in accordance with the rules given in GB/T 1.1-2009.
This standard uses the redrafting method to modify the design and type of ISO 10804.2010 self-anchoring interface system for ductile iron pipelines.
Test.
Compared with ISO 10804.2010, this standard has more adjustments in structure. Appendix A lists this standard and ISO 10804.2010.
The chapter number change comparison checklist.
There are technical differences between this standard and ISO 10804.2010, and the terms involved in these differences have been passed in the margins of their outer margins.
The vertical single line (|) is marked, and a list of the corresponding technical differences and their causes is given in Appendix B.
This standard was proposed by the China Iron and Steel Association.
This standard is under the jurisdiction of the National Steel Standardization Technical Committee (SAC/TC183).
This standard is mainly drafted by. Xinxing Casting Pipe Co., Ltd., Saint-Gobain Pipeline System Co., Ltd., Metallurgical Industry Information Standards Research
Research Institute.
The main drafters of this standard. Li Chengzhang, Shen Yong, Wang Wei, Sun Shu, Hou Jie, Xu Jun, Zuo Chao, Che Lei, He Gen, Li Jun.
Self-anchoring interface system for ductile iron pipeline
Design regulations and type tests
1 Scope
This standard specifies the terms and definitions, design regulations and type tests for self-anchoring interface systems for ductile iron pipelines.
This standard applies to ductile iron pipe pipelines in accordance with GB/T 13295 and GB/T 26081.
Note. Self-anchor interfaces are sometimes referred to as constraint interfaces or stop-off interfaces.
2 Normative references
The following documents are indispensable for the application of this document. For dated references, only dated versions apply to this article.
Pieces. For undated references, the latest edition (including all amendments) applies to this document.
GB/T 13295 Ductile iron pipes and fittings for water and gas (GB/T 13295-2013, ISO 2531.2009, MOD)
GB/T 26081 Ductile iron pipe, fittings and accessories for sewage (GB/T 26081-2010, ISO 7186.1996, MOD)
3 Terms and definitions
The following terms and definitions as defined in GB/T 13295 apply to this document.
3.1
Allowable deflection angle alowableangulardeflection
Under the action of the working pressure, the interface between the two ductile iron pipes can safely withstand the deflection angle.
3.2
Allow working pressure alowableoperatingpressure; PFA
The maximum internal pressure that the part can withstand for a long time, excluding the impact pressure.
3.3
Maximum allowable working pressure maximumalowableoperatingpressure; PMA
The maximum internal pressure that the part can safely with during use, including impact pressure.
4 Design regulations
4.1 All self-anchoring interfaces for ductile iron pipes, fittings and other components shall be designed in accordance with the requirements of this chapter. If one is self
The anchor interface design has been validated and successfully used for more than 10 years, with only major design changes that adversely affect interface performance.
Type test according to the requirements of Chapter 5.
4.2 The minimum wall thickness of the socket of the self-anchoring interface shall be such that it is required for welding or can withstand from other components (such as steel teeth on the seal ring).
effect. The wall thickness and allowable working pressure (PFA) of the self-anchoring interface tube should be determined by the manufacturer to meet the interface performance and manufacturing process requirements.
4.3 The self-anchor interface shall be subjected to a positive internal pressure test with a test pressure of (1.5PFA 0.5) MPa. The self-anchoring interface shall be able to withstand the internal water pressure safely.
The resulting axial pull-out force.
4.4 The self-anchoring interface shall be subjected to a negative internal pressure test with a test pressure of 0.01 MPa absolute (ie 0.09 MPa lower than the standard atmospheric pressure). when
The use of a certain sealing rubber ring has been verified by the negative internal pressure test in GB/T 13295, then the self-anchoring interface using the sealing rubber ring is not
A negative internal pressure test must be performed.
4.5 The self-anchoring interface shall be subjected to cyclic internal pressure type test. The test pressure is at the maximum allowable working pressure (PMA) and (PMA-0.5) MPa.
Inter-cycle, the number of cycles is not less than 24,000 times.
4.6 For seismic areas, ductile iron pipes and self-anchoring interfaces specified in this standard have good adaptability. However at the intersection of the fault, the liquid
Certain locations, such as areas and connections to buildings, require special design and should be evaluated by the pipeline manufacturer or seismic safety.
Engineer consultation.
4.7 The attachments or fittings of the self-anchoring interface shall be treated with anti-corrosion treatment, spray coating (such as spraying zinc or epoxy) or docking in the field.
The mouth is protected (such as on-site installation of heat shrink sleeves) to meet the anti-corrosion requirements of different operating environments.
5 type test
5.1 General
5.1.1 The self-anchor interface design shall be type tested. Type testing should be carried out under the most unfavorable conditions such as casting tolerances and interface movement.
To verify the mechanical strength and sealing performance of the interface.
5.1.2 Type test shall be carried out under the condition that the connecting part forms the maximum design radial clearance (minimum socket and maximum socket connection).
The self-anchoring interface of the steel teeth is set on the sealing ring, and should also be carried out under the condition of minimum design radial clearance (maximum socket and minimum socket connection).
Press type test.
5.1.3 The socket end face shall include the socket in the range of the welding ring and the attachment. The wall thickness shall be the minimum wall thickness of the design with a tolerance of 100%. Allow machine
Machine the inside diameter of the socket to the required wall thickness.
5.1.4 In the type test, the tolerance of the radial clearance should meet the following requirements, which can be machined or specially made by the socket.
Meet the size requirements.
--- When using the maximum design radial clearance, the upper limit of the radial clearance is 0mm, and the lower tolerance is the maximum design radial clearance.
5% or 0.5mm (small value);
--- When using the minimum design radial clearance, the upper limit of the radial clearance is 5% or 0.5mm of the minimum design radial clearance (taken
The smaller value), the lower tolerance is 0mm.
5.2 Test conditions
5.2.1 Table 1 shows the specification grouping of the type test. At least one type of each group is to be type tested. Usually, the recommended specifications are selected.
test. If the product design and/or manufacturing process in a group is different, the group should be subdivided. For the manufacturer, if a group only
A nominal diameter (DN) or nominal pressure (PN). This nominal diameter (DN) or nominal pressure (PN) can be considered as the same design and production.
Part of the art's neighboring group.
Note. When the interface performance of the same specification group is based on the same design parameters, the type test results of one specification can represent the entire group.
Table 1 Specification grouping of type test
Specification group DN40~DN250 DN300~DN600 DN700~DN1000 DN1100~DN2000 DN2200~DN2600
Recommended specifications DN200 DN400 DN800 DN1600 DN2400
5.2.2 Each type shall be type tested in the following two cases.
a) Install the tubes on both sides of the interface straight, and then deflect the pipes on both sides of the interface to meet the permissible deviations promised in the supplier's instruction manual.
Turn the corner and maintain this deflection during the test.
b) First install the tubes on both sides of the interface straight, then apply shear force to the interface. The value of shear force (unit. N) should not be less than 50 times.
Weigh the diameter DN.
5.2.3 Under the test pressure conditions described below, the joint may undergo axial movement, and these axial movements shall reach a constant value within 2 h.
After 2h, the components of all interfaces should have no obvious leakage and the structure is stable.
--- Positive internal pressure type test in accordance with 4.3 requirements;
--- Negative internal pressure type test in accordance with 4.4 requirements;
--- Cyclic internal pressure type test in accordance with 4.5 requirements.
5.3 Test methods
5.3.1 Positive internal pressure type test
5.3.1.1 The end shall be closed and shall not be axially constrained, regardless of whether the test device is in a straight state, deflected state or subjected to load.
The test device shall be such that the interface is subjected to the axial pull-out force generated by the internal water pressure. The test device shall be equipped with a pressure gauge with an accuracy of ± 3%.
5.3.1.2 The type test shall be carried out on an interface assembled by two sections of pipe, each of which shall be at least 1 m long.
5.3.1.3 For the type test in accordance with 5.2.2 b), the shear load W is applied to the socket through a 120° V-shaped block, and the V-shaped block is approximately
The nominal diameter DN (in mm) or.200mm from the surface of the mouth is 0.5 times, and the position of the block is taken as the larger value. The socket should be pressed
On the horizontal bracket.
5.3.1.4 The test components shall be filled with water and easily vented. The pressure shall be steadily increased to the test pressure, and the pressure increase rate shall not exceed 0.1 MPa/s.
5.3.1.5 The test pressure shall be kept constant for at least 2 h within ±0.05 MPa. During this period, the interface shall be thoroughly inspected every 15 minutes and measured.
Axial movement of the mouth.
5.3.2 Negative internal pressure type test
5.3.2.1 Test equipment and test equipment requirements As in 5.3.1, the pipe sections shall be axially constrained to prevent relative movement.
5.3.2.2 Test assembly The water shall be drained and the air shall be withdrawn to an absolute pressure of 0.01 MPa, then the vacuum pump shall be closed and the test assembly closed.
The test assembly was placed under vacuum for at least 2 h during which the pressure change did not exceed 0.009 MPa. The test temperature is 5 ° C ~ 40 ° C,
The temperature change of the test assembly during the test should not exceed 10 °C.
5.3.3 Cyclic internal pressure type test
5.3.3.1 The test device and test equipment are required to be the same as 5.3.1. The test device is filled with water and the gas is discharged.
5.3.3.2 The pressure continues to rise to the maximum allowable working pressure (PMA) and is then automatically monitored according to the following pressure cycle.
a) the pressure continues to drop to (PMA-0.5) MPa;
b) maintain (PMA-0.5) MPa pressure for at least 5s;
c) the pressure continues to rise to PMA;
d) Maintain PMA pressure for at least 5 s.
5.3.3.3 Record the number of cycles, if the interface leaks, the test should be stopped automatically. After the test, the axial movement of the socket end should be measured.
5.4 Type test report
The type test report should include the following.
a) interface type;
b) the size range covered by the test;
c) nominal diameter;
d) the wall thickness of the test tube;
e) allow working pressure;
f) maximum allowable working pressure;
g) allow test pressure;
h) allow the deflection angle;
i) test results;
j) Test date.
Appendix A
(informative appendix)
Structural changes in this standard compared to ISO 10804.2010
Compared with ISO 10804.2010, this standard has more adjustments in structure. The specific chapter number comparison is shown in Table A.1.
Table A.1 Comparison of this standard with the ISO 10804.2010 chapter number
This standard chapter number corresponds to ISO 10804.2010 chapter number
3.1 3.6
5.1.1 5.1 First paragraph
5.1.2 5.1 second paragraph
5.1.3 5.1 second paragraph
5.1.4 5.4 third paragraph
5.2.1 5.2 first paragraph, second paragraph 5.2
5.2.2 5.2 third paragraph
5.2.3 5.2 fourth paragraph, 5.2 fifth paragraph
5.3.1.1 5.3 first paragraph
5.3.1.2 5.3 second paragraph
5.3.1.3 5.3 third paragraph
5.3.1.4 5.3 fourth paragraph
5.3.1.5 5.3 fifth paragraph
5.3.2.1 5.4 first paragraph
5.3.2.2 5.4 second paragraph
5.3.3.1 5.5 first paragraph
5.3.3.2 5.5 second paragraph
5.3.3.3 5.5 third paragraph
5.4 5.6
Appendix A -
Appendix B -
Appendix B
(informative appendix)
Technical differences between this standard and ISO 10804.2010 and their causes
Table B.1 gives the technical differences between this standard and ISO 10804.2010 and their causes.
Table B.1 Technical differences between this standard and ISO 10804.2010 and their causes
Reasons for technical differences in the numbering of this standard
Added "Note. Self-anchor interface is sometimes referred to as constraint connection
Or stop interface. ”
The name of the self-anchoring interface in China's industry is not uniform, and the note is added.
Easy to use standard
Chinese language with cons...
Get Quotation: Click GB/T 36173-2018 (Self-service in 1-minute)
Historical versions (Master-website): GB/T 36173-2018
Preview True-PDF (Reload/Scroll-down if blank)
GB/T 36173-2018: Restrained joint systems for ductile iron pipelines -- Design rules and type testing
GB/T 36173-2018
Restrained joint systems for ductile iron pipelines--Design rules and type testing
ICS 23.040.10; 23.040.60
H48
National Standards of People's Republic of China
Self-anchoring interface system for ductile iron pipeline
Design regulations and type tests
(ISO 10804..2010, MOD)
Published on.2018-05-14
Implementation of.2019-02-01
State Market Supervisory Administration
China National Standardization Administration issued
Content
Foreword III
1 range 1
2 Normative references 1
3 Terms and Definitions 1
4 Design Regulations 1
5 type test 2
Appendix A (informative) Structural changes in this standard compared to ISO 10804.2010 4
Appendix B (informative) The technical differences between this standard and ISO 10804.2010 and their causes 5
Foreword
This standard was drafted in accordance with the rules given in GB/T 1.1-2009.
This standard uses the redrafting method to modify the design and type of ISO 10804.2010 self-anchoring interface system for ductile iron pipelines.
Test.
Compared with ISO 10804.2010, this standard has more adjustments in structure. Appendix A lists this standard and ISO 10804.2010.
The chapter number change comparison checklist.
There are technical differences between this standard and ISO 10804.2010, and the terms involved in these differences have been passed in the margins of their outer margins.
The vertical single line (|) is marked, and a list of the corresponding technical differences and their causes is given in Appendix B.
This standard was proposed by the China Iron and Steel Association.
This standard is under the jurisdiction of the National Steel Standardization Technical Committee (SAC/TC183).
This standard is mainly drafted by. Xinxing Casting Pipe Co., Ltd., Saint-Gobain Pipeline System Co., Ltd., Metallurgical Industry Information Standards Research
Research Institute.
The main drafters of this standard. Li Chengzhang, Shen Yong, Wang Wei, Sun Shu, Hou Jie, Xu Jun, Zuo Chao, Che Lei, He Gen, Li Jun.
Self-anchoring interface system for ductile iron pipeline
Design regulations and type tests
1 Scope
This standard specifies the terms and definitions, design regulations and type tests for self-anchoring interface systems for ductile iron pipelines.
This standard applies to ductile iron pipe pipelines in accordance with GB/T 13295 and GB/T 26081.
Note. Self-anchor interfaces are sometimes referred to as constraint interfaces or stop-off interfaces.
2 Normative references
The following documents are indispensable for the application of this document. For dated references, only dated versions apply to this article.
Pieces. For undated references, the latest edition (including all amendments) applies to this document.
GB/T 13295 Ductile iron pipes and fittings for water and gas (GB/T 13295-2013, ISO 2531.2009, MOD)
GB/T 26081 Ductile iron pipe, fittings and accessories for sewage (GB/T 26081-2010, ISO 7186.1996, MOD)
3 Terms and definitions
The following terms and definitions as defined in GB/T 13295 apply to this document.
3.1
Allowable deflection angle alowableangulardeflection
Under the action of the working pressure, the interface between the two ductile iron pipes can safely withstand the deflection angle.
3.2
Allow working pressure alowableoperatingpressure; PFA
The maximum internal pressure that the part can withstand for a long time, excluding the impact pressure.
3.3
Maximum allowable working pressure maximumalowableoperatingpressure; PMA
The maximum internal pressure that the part can safely with during use, including impact pressure.
4 Design regulations
4.1 All self-anchoring interfaces for ductile iron pipes, fittings and other components shall be designed in accordance with the requirements of this chapter. If one is self
The anchor interface design has been validated and successfully used for more than 10 years, with only major design changes that adversely affect interface performance.
Type test according to the requirements of Chapter 5.
4.2 The minimum wall thickness of the socket of the self-anchoring interface shall be such that it is required for welding or can withstand from other components (such as steel teeth on the seal ring).
effect. The wall thickness and allowable working pressure (PFA) of the self-anchoring interface tube should be determined by the manufacturer to meet the interface performance and manufacturing process requirements.
4.3 The self-anchor interface shall be subjected to a positive internal pressure test with a test pressure of (1.5PFA 0.5) MPa. The self-anchoring interface shall be able to withstand the internal water pressure safely.
The resulting axial pull-out force.
4.4 The self-anchoring interface shall be subjected to a negative internal pressure test with a test pressure of 0.01 MPa absolute (ie 0.09 MPa lower than the standard atmospheric pressure). when
The use of a certain sealing rubber ring has been verified by the negative internal pressure test in GB/T 13295, then the self-anchoring interface using the sealing rubber ring is not
A negative internal pressure test must be performed.
4.5 The self-anchoring interface shall be subjected to cyclic internal pressure type test. The test pressure is at the maximum allowable working pressure (PMA) and (PMA-0.5) MPa.
Inter-cycle, the number of cycles is not less than 24,000 times.
4.6 For seismic areas, ductile iron pipes and self-anchoring interfaces specified in this standard have good adaptability. However at the intersection of the fault, the liquid
Certain locations, such as areas and connections to buildings, require special design and should be evaluated by the pipeline manufacturer or seismic safety.
Engineer consultation.
4.7 The attachments or fittings of the self-anchoring interface shall be treated with anti-corrosion treatment, spray coating (such as spraying zinc or epoxy) or docking in the field.
The mouth is protected (such as on-site installation of heat shrink sleeves) to meet the anti-corrosion requirements of different operating environments.
5 type test
5.1 General
5.1.1 The self-anchor interface design shall be type tested. Type testing should be carried out under the most unfavorable conditions such as casting tolerances and interface movement.
To verify the mechanical strength and sealing performance of the interface.
5.1.2 Type test shall be carried out under the condition that the connecting part forms the maximum design radial clearance (minimum socket and maximum socket connection).
The self-anchoring interface of the steel teeth is set on the sealing ring, and should also be carried out under the condition of minimum design radial clearance (maximum socket and minimum socket connection).
Press type test.
5.1.3 The socket end face shall include the socket in the range of the welding ring and the attachment. The wall thickness shall be the minimum wall thickness of the design with a tolerance of 100%. Allow machine
Machine the inside diameter of the socket to the required wall thickness.
5.1.4 In the type test, the tolerance of the radial clearance should meet the following requirements, which can be machined or specially made by the socket.
Meet the size requirements.
--- When using the maximum design radial clearance, the upper limit of the radial clearance is 0mm, and the lower tolerance is the maximum design radial clearance.
5% or 0.5mm (small value);
--- When using the minimum design radial clearance, the upper limit of the radial clearance is 5% or 0.5mm of the minimum design radial clearance (taken
The smaller value), the lower tolerance is 0mm.
5.2 Test conditions
5.2.1 Table 1 shows the specification grouping of the type test. At least one type of each group is to be type tested. Usually, the recommended specifications are selected.
test. If the product design and/or manufacturing process in a group is different, the group should be subdivided. For the manufacturer, if a group only
A nominal diameter (DN) or nominal pressure (PN). This nominal diameter (DN) or nominal pressure (PN) can be considered as the same design and production.
Part of the art's neighboring group.
Note. When the interface performance of the same specification group is based on the same design parameters, the type test results of one specification can represent the entire group.
Table 1 Specification grouping of type test
Specification group DN40~DN250 DN300~DN600 DN700~DN1000 DN1100~DN2000 DN2200~DN2600
Recommended specifications DN200 DN400 DN800 DN1600 DN2400
5.2.2 Each type shall be type tested in the following two cases.
a) Install the tubes on both sides of the interface straight, and then deflect the pipes on both sides of the interface to meet the permissible deviations promised in the supplier's instruction manual.
Turn the corner and maintain this deflection during the test.
b) First install the tubes on both sides of the interface straight, then apply shear force to the interface. The value of shear force (unit. N) should not be less than 50 times.
Weigh the diameter DN.
5.2.3 Under the test pressure conditions described below, the joint may undergo axial movement, and these axial movements shall reach a constant value within 2 h.
After 2h, the components of all interfaces should have no obvious leakage and the structure is stable.
--- Positive internal pressure type test in accordance with 4.3 requirements;
--- Negative internal pressure type test in accordance with 4.4 requirements;
--- Cyclic internal pressure type test in accordance with 4.5 requirements.
5.3 Test methods
5.3.1 Positive internal pressure type test
5.3.1.1 The end shall be closed and shall not be axially constrained, regardless of whether the test device is in a straight state, deflected state or subjected to load.
The test device shall be such that the interface is subjected to the axial pull-out force generated by the internal water pressure. The test device shall be equipped with a pressure gauge with an accuracy of ± 3%.
5.3.1.2 The type test shall be carried out on an interface assembled by two sections of pipe, each of which shall be at least 1 m long.
5.3.1.3 For the type test in accordance with 5.2.2 b), the shear load W is applied to the socket through a 120° V-shaped block, and the V-shaped block is approximately
The nominal diameter DN (in mm) or.200mm from the surface of the mouth is 0.5 times, and the position of the block is taken as the larger value. The socket should be pressed
On the horizontal bracket.
5.3.1.4 The test components shall be filled with water and easily vented. The pressure shall be steadily increased to the test pressure, and the pressure increase rate shall not exceed 0.1 MPa/s.
5.3.1.5 The test pressure shall be kept constant for at least 2 h within ±0.05 MPa. During this period, the interface shall be thoroughly inspected every 15 minutes and measured.
Axial movement of the mouth.
5.3.2 Negative internal pressure type test
5.3.2.1 Test equipment and test equipment requirements As in 5.3.1, the pipe sections shall be axially constrained to prevent relative movement.
5.3.2.2 Test assembly The water shall be drained and the air shall be withdrawn to an absolute pressure of 0.01 MPa, then the vacuum pump shall be closed and the test assembly closed.
The test assembly was placed under vacuum for at least 2 h during which the pressure change did not exceed 0.009 MPa. The test temperature is 5 ° C ~ 40 ° C,
The temperature change of the test assembly during the test should not exceed 10 °C.
5.3.3 Cyclic internal pressure type test
5.3.3.1 The test device and test equipment are required to be the same as 5.3.1. The test device is filled with water and the gas is discharged.
5.3.3.2 The pressure continues to rise to the maximum allowable working pressure (PMA) and is then automatically monitored according to the following pressure cycle.
a) the pressure continues to drop to (PMA-0.5) MPa;
b) maintain (PMA-0.5) MPa pressure for at least 5s;
c) the pressure continues to rise to PMA;
d) Maintain PMA pressure for at least 5 s.
5.3.3.3 Record the number of cycles, if the interface leaks, the test should be stopped automatically. After the test, the axial movement of the socket end should be measured.
5.4 Type test report
The type test report should include the following.
a) interface type;
b) the size range covered by the test;
c) nominal diameter;
d) the wall thickness of the test tube;
e) allow working pressure;
f) maximum allowable working pressure;
g) allow test pressure;
h) allow the deflection angle;
i) test results;
j) Test date.
Appendix A
(informative appendix)
Structural changes in this standard compared to ISO 10804.2010
Compared with ISO 10804.2010, this standard has more adjustments in structure. The specific chapter number comparison is shown in Table A.1.
Table A.1 Comparison of this standard with the ISO 10804.2010 chapter number
This standard chapter number corresponds to ISO 10804.2010 chapter number
3.1 3.6
5.1.1 5.1 First paragraph
5.1.2 5.1 second paragraph
5.1.3 5.1 second paragraph
5.1.4 5.4 third paragraph
5.2.1 5.2 first paragraph, second paragraph 5.2
5.2.2 5.2 third paragraph
5.2.3 5.2 fourth paragraph, 5.2 fifth paragraph
5.3.1.1 5.3 first paragraph
5.3.1.2 5.3 second paragraph
5.3.1.3 5.3 third paragraph
5.3.1.4 5.3 fourth paragraph
5.3.1.5 5.3 fifth paragraph
5.3.2.1 5.4 first paragraph
5.3.2.2 5.4 second paragraph
5.3.3.1 5.5 first paragraph
5.3.3.2 5.5 second paragraph
5.3.3.3 5.5 third paragraph
5.4 5.6
Appendix A -
Appendix B -
Appendix B
(informative appendix)
Technical differences between this standard and ISO 10804.2010 and their causes
Table B.1 gives the technical differences between this standard and ISO 10804.2010 and their causes.
Table B.1 Technical differences between this standard and ISO 10804.2010 and their causes
Reasons for technical differences in the numbering of this standard
Added "Note. Self-anchor interface is sometimes referred to as constraint connection
Or stop interface. ”
The name of the self-anchoring interface in China's industry is not uniform, and the note is added.
Easy to use standard
Chinese language with cons...
Share
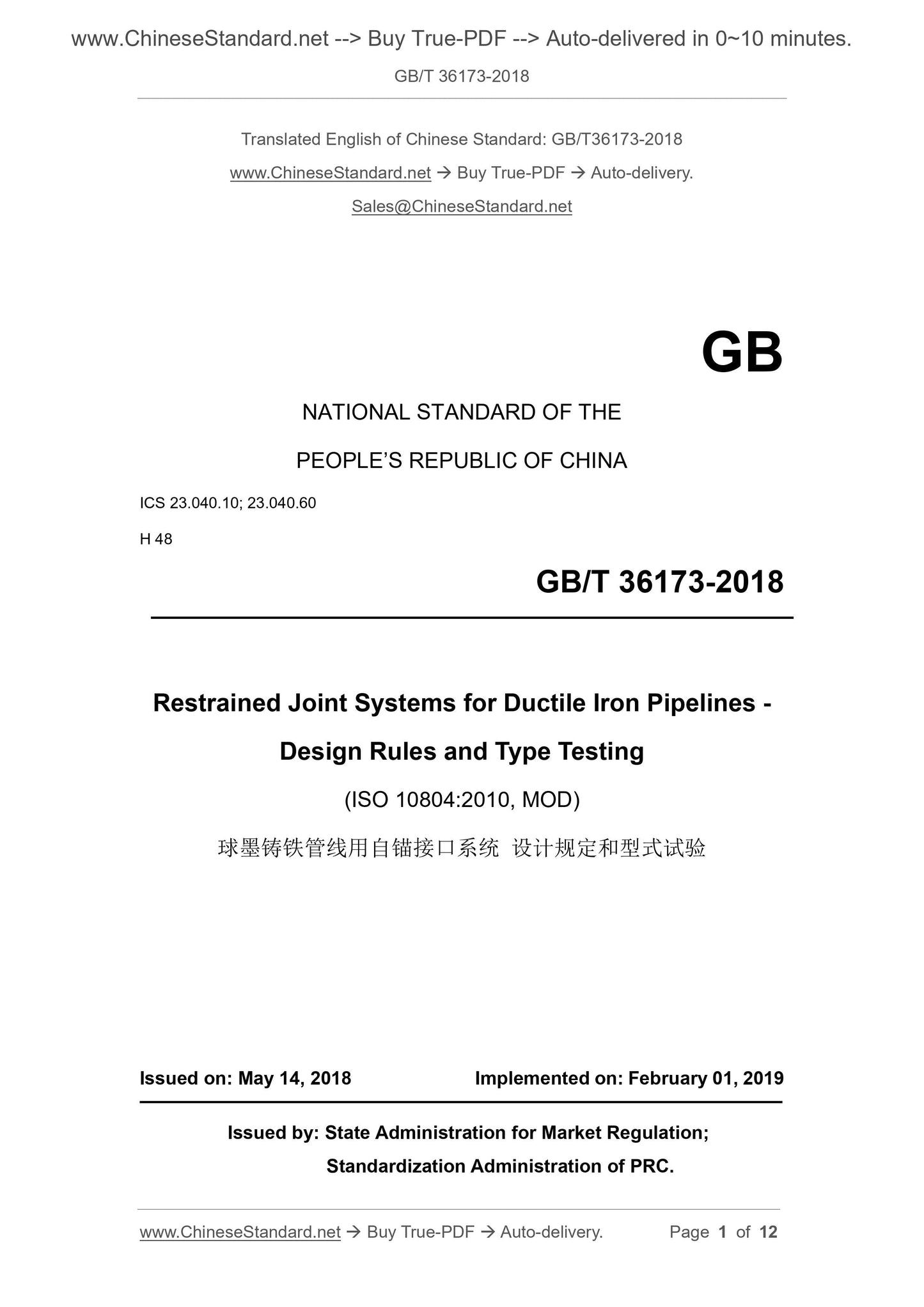
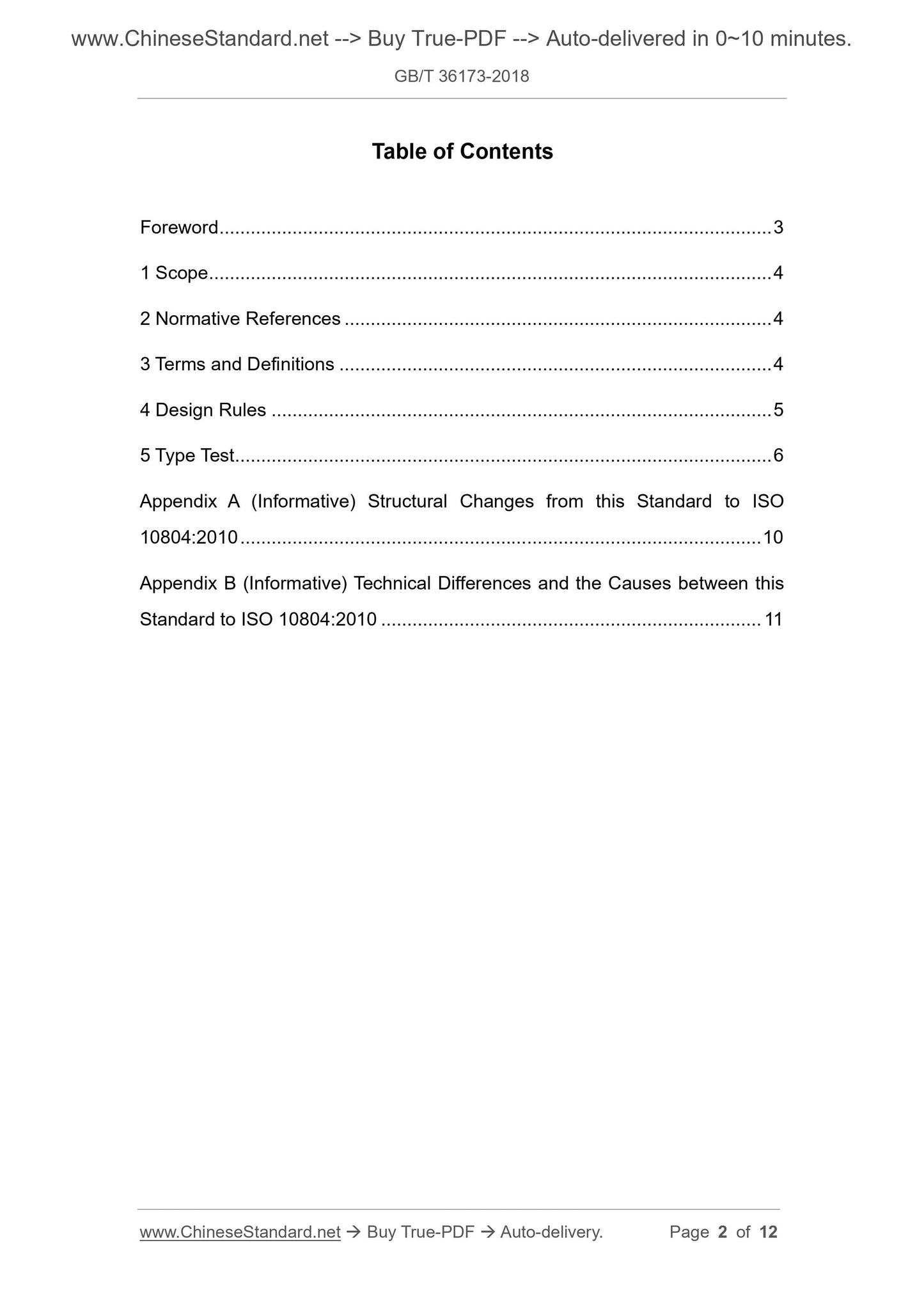
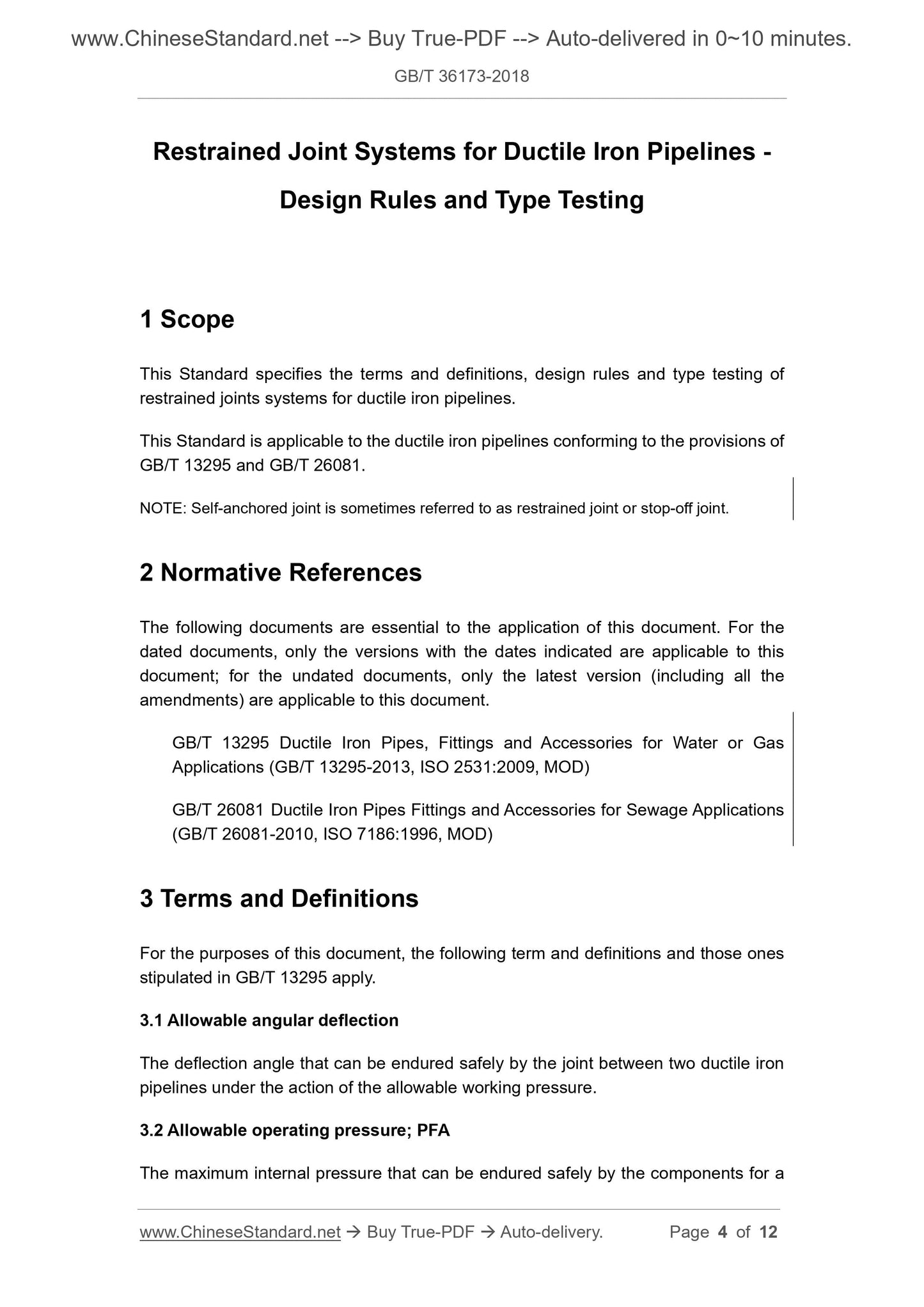
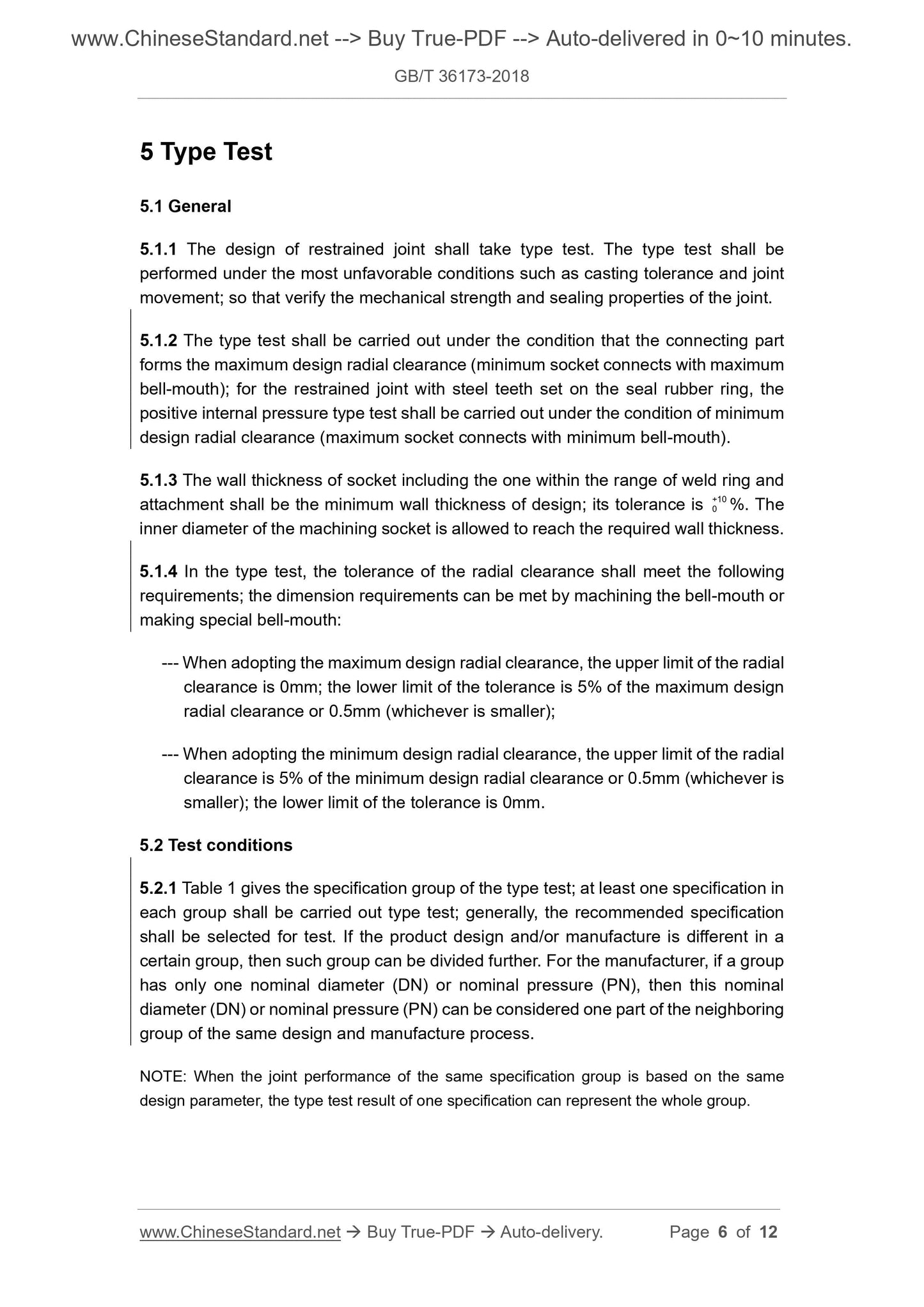
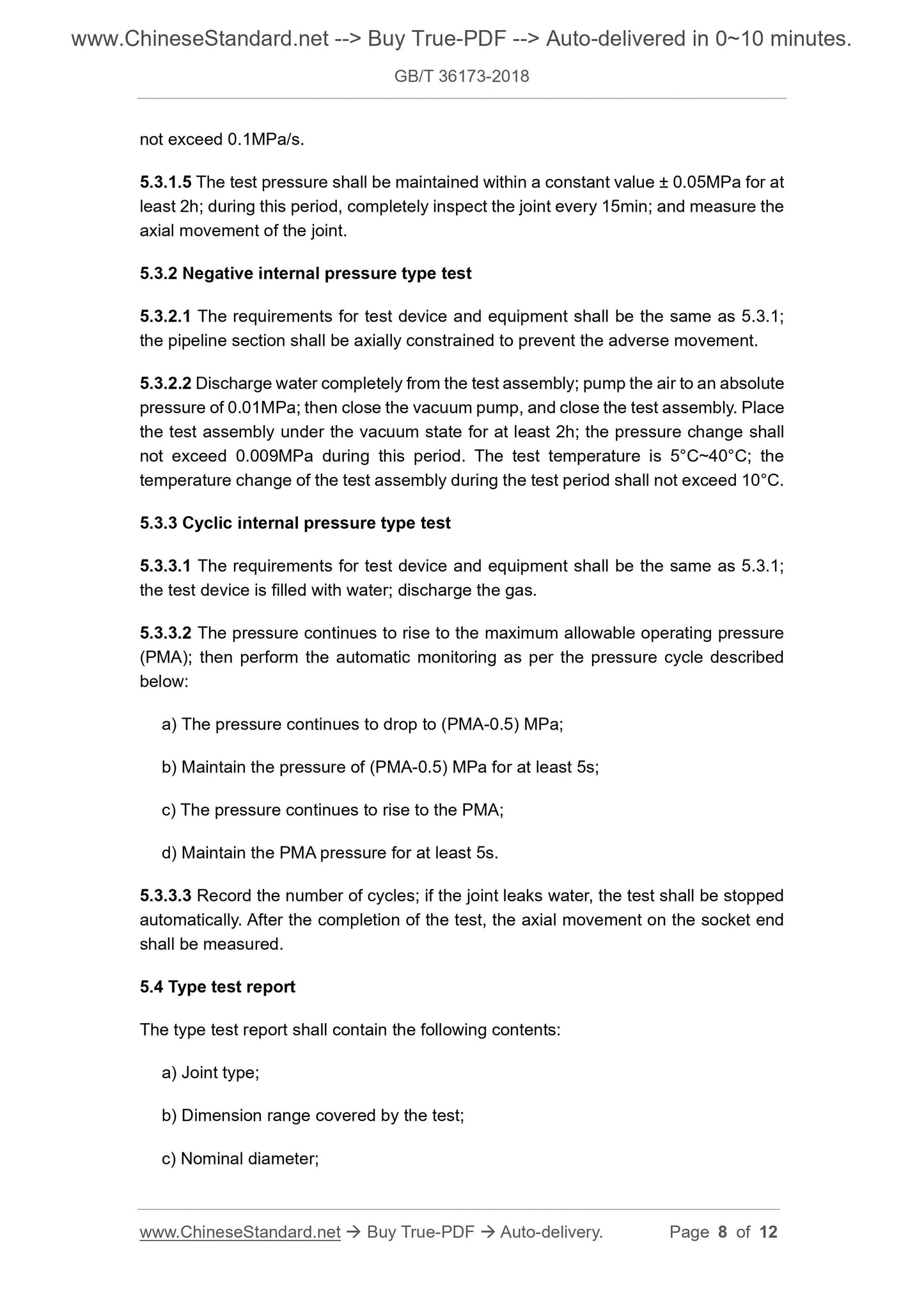