1
/
of
7
PayPal, credit cards. Download editable-PDF & invoice In 1 second!
GB/T 37309-2019 English PDF (GBT37309-2019)
GB/T 37309-2019 English PDF (GBT37309-2019)
Regular price
$150.00 USD
Regular price
Sale price
$150.00 USD
Unit price
/
per
Shipping calculated at checkout.
Couldn't load pickup availability
Delivery: 3 seconds. Download true-PDF + Invoice.
Get QUOTATION in 1-minute: Click GB/T 37309-2019
Historical versions: GB/T 37309-2019
Preview True-PDF (Reload/Scroll if blank)
GB/T 37309-2019: Anti-corrosion technical specification for marine steel structures by high velocity arc spraying
GB/T 37309-2019
NATIONAL STANDARD OF THE
PEOPLE’S REPUBLIC OF CHINA
ICS 25.220.99
A 29
Anti-corrosion Technical Specification for Marine
Steel Structures by High Velocity Arc Spraying
ISSUED ON: MARCH 25, 2019
IMPLEMENTED ON: FEBRUARY 01, 2020
Issued by: State Administration for Market Regulation;
Standardization Administration of the People's Republic of
China.
Table of Contents
Foreword ... 3
1 Scope ... 4
2 Normative references ... 4
3 Terms and definitions ... 5
4 Coating classification ... 5
5 High velocity arc spraying system ... 7
6 Spraying materials and operation ... 7
7 Test method ... 10
Appendix A (Normative) Test method of the coating thickness -- cross-section
microscopy ... 12
Appendix B (Normative) Test method of bond strength ... 15
Anti-corrosion Technical Specification for Marine
Steel Structures by High Velocity Arc Spraying
1 Scope
This Standard specifies the classification, spraying system, spraying materials,
operation and test methods of anti-corrosion coating for marine steel structures
by high velocity arc spraying.
This Standard applies to thermal-sprayed zinc-aluminum and zinc-aluminum-
magnesium rare-earth coatings on the steal surface of marine steel structures.
This Standard does not apply to the repair of damaged surfaces and other metal
coatings.
2 Normative references
The following documents are indispensable for the application of this document.
For dated references, only the dated version applies to this document. For
undated references, the latest edition (including all amendments) applies to this
document.
GB/T 3190-2008, Wrought aluminum and aluminum alloy. Chemical
composition
GB/T 4956, Non-magnetic coatings on magnetic substrates - Measurement
of coating thickness - Magnetic method
GB/T 6462, Metallic and oxide coatings. Measurement of coating thickness
- Microscopical method
GB/T 8923.1-2011, Preparation of steel substrates before application of
paints and related products. Visual assessment of surface cleanliness. Part
1: Rust grades and preparation grades of uncoated steel substrates and of
steel substrates after overall removal of previous coatings
GB/T 9793, Thermal spraying. Metallic and other inorganic coatings. Zinc,
aluminum and their alloys
GB/T 11373-2017, Thermal spraying. Pre-treatment of surfaces of metallic
parts and components
GB/T 11374, Thermal spraying coating. Nondestructive methods for
alloy that contains 5% of Mg, which is codenamed Al-Mg5 or LF5.
6.2 Operation
6.2.1 Workpiece surface pretreatment
6.2.1.1 General rules
For the to-be-sprayed surface which is heavily polluted, before sandblasting,
the workpiece shall be cleaned, and special methods shall be used to remove
deposits such as oil stains; for the to-be-sprayed surface which is lightly
contaminated, sandblasting pretreatment can be performed directly. For
workpieces which are locally sprayed, not only the dirt at the spraying site, but
also the contaminants in the adjacent spraying area, shall be removed, so as
to prevent the contaminants from being sprayed into the spraying area during
the spraying process. The workpiece surface which has been pretreated shall
be a metal surface that has an off-white homogeneity, on which, there is neither
oil, nor rust, nor other contaminants.
6.2.1.2 Sandblasting pretreatment
Sandblasting pretreatment uses sands, of which the particle size is 10 mesh ~
20 mesh, and which is dry, high-hardness and multi-angle, such as brown
corundum sand, copper ore or steel sand. When a thinner metal substrate is
sprayed, the pressure shall be 0.3 MPa ~ 0.4 MPa; when a thicker substrate is
sprayed, the pressure shall be ≥ 0.6 MPa, the sandblasting angle shall usually
be 70°, and the sandblasting time shall not be too long. After the sandblasting
pretreatment, the oil stain and rust layer on the surface of the substrate shall
be removed, and the de-rusting quality shall reach level-Sa2.5.
6.2.1.3 Inspection of surface roughness
The surface roughness of the workpiece, after sandblasting, shall meet the
requirements of Rz 25 μm ~ 100 μm in GB/T 11373-2017.
6.2.1.4 Surface cleanliness
The surface cleanliness of the workpiece, after sandblasting, shall comply with
level-Sa2.5 in GB/T 8923.1-2011.
6.2.1.5 Sandblasting roughening treatment
The workpiece surface after sandblasting roughening treatment is easily
contaminated by the outside; therefore, it is necessary to avoid touching by
hand and blowing. The treated surface shall be sprayed within 2h ~ 3h. If the
spraying cannot be performed on time, it’s necessary to use a clean plastic film
to cover and protect it. If it is to be moved, avoid secondary pollution on the
surface.
firstly be used to pretreat the coating. Frequently-used sealing agents include
paraffin, vinyl, silicone resin, phenolic, modified boxwood phenolic,
polyurethane, titanium nano-polymer coatings and so on. When sealing,
different sealing agents shall be selected according to different ambient
temperatures.
6.2.3.1.3.2 Spraying of zinc-aluminum-magnesium-rare earth alloy coating
plays a role of self-sealing, which leaves out manual sealing.
6.2.3.2 Coating
The coating, through sealing treatment, can be coated for its aesthetic
appearance or extended life.
6.2.3.3 Compatibility
Whether the metal coating is sealed or not shall be resolved by mutual
agreement. The coating system shall be compatible with the metal coating or
the sealant; when needed, perform a test to confirm the compatibility between
the metal coating and the material.
7 Test method
7.1 Thickness measurement
7.1.1 Magnetic measurement
Magnetic measurement has the advantage of non-destructive, fast and being
capable to directly measure any part of any to-be-test surface. In addition, both
the properties and the standard thickness values of the coating (Zn, Al) which
is sprayed on the steel substrate are beneficial to achieve a satisfactory
measurement accuracy for the method. Therefore, for a given sample, as long
as the magnetic thickness gauge is properly calibrated according to the
standard regulations and the agreement between the supplier and the buyer,
the magnetic measurement can provide an effective and accurate acceptance
check result. Perform the specific method according to the requirements of
GB/T 4956.
7.1.2 Cross-section microscopy
Cross-section microscopy refers to the measurement of the coating thickness
on the cross-section under a microscope, which is also a method that is used
to examine the thickness of a metal coating. The sample preparation method is
specified in GB/T 6462. In order to prevent the coating from peeling off from the
substrate and the edges, use a plastic or a low-melting-point alloy to fix the
sample, and use a polishing agent to inspect the surface. The specific
Appendix A
(Normative)
Test method of the coating thickness -- cross-section microscopy
A.1 Thickness test
A.1.1 Coating of which the area is 1 m2
When the coating area is within 1 cm2, the local thickness at any given point
shall be the coating thickness that is measured on the base level of 1 cm2.
Since various methods which are suitable for the measurement of coating
thickness are performed on measuring surfaces of different sizes; therefore, the
following methods are used to determine the local thickness of any part of the
coating (see Table A.1):
-- W...
Get QUOTATION in 1-minute: Click GB/T 37309-2019
Historical versions: GB/T 37309-2019
Preview True-PDF (Reload/Scroll if blank)
GB/T 37309-2019: Anti-corrosion technical specification for marine steel structures by high velocity arc spraying
GB/T 37309-2019
NATIONAL STANDARD OF THE
PEOPLE’S REPUBLIC OF CHINA
ICS 25.220.99
A 29
Anti-corrosion Technical Specification for Marine
Steel Structures by High Velocity Arc Spraying
ISSUED ON: MARCH 25, 2019
IMPLEMENTED ON: FEBRUARY 01, 2020
Issued by: State Administration for Market Regulation;
Standardization Administration of the People's Republic of
China.
Table of Contents
Foreword ... 3
1 Scope ... 4
2 Normative references ... 4
3 Terms and definitions ... 5
4 Coating classification ... 5
5 High velocity arc spraying system ... 7
6 Spraying materials and operation ... 7
7 Test method ... 10
Appendix A (Normative) Test method of the coating thickness -- cross-section
microscopy ... 12
Appendix B (Normative) Test method of bond strength ... 15
Anti-corrosion Technical Specification for Marine
Steel Structures by High Velocity Arc Spraying
1 Scope
This Standard specifies the classification, spraying system, spraying materials,
operation and test methods of anti-corrosion coating for marine steel structures
by high velocity arc spraying.
This Standard applies to thermal-sprayed zinc-aluminum and zinc-aluminum-
magnesium rare-earth coatings on the steal surface of marine steel structures.
This Standard does not apply to the repair of damaged surfaces and other metal
coatings.
2 Normative references
The following documents are indispensable for the application of this document.
For dated references, only the dated version applies to this document. For
undated references, the latest edition (including all amendments) applies to this
document.
GB/T 3190-2008, Wrought aluminum and aluminum alloy. Chemical
composition
GB/T 4956, Non-magnetic coatings on magnetic substrates - Measurement
of coating thickness - Magnetic method
GB/T 6462, Metallic and oxide coatings. Measurement of coating thickness
- Microscopical method
GB/T 8923.1-2011, Preparation of steel substrates before application of
paints and related products. Visual assessment of surface cleanliness. Part
1: Rust grades and preparation grades of uncoated steel substrates and of
steel substrates after overall removal of previous coatings
GB/T 9793, Thermal spraying. Metallic and other inorganic coatings. Zinc,
aluminum and their alloys
GB/T 11373-2017, Thermal spraying. Pre-treatment of surfaces of metallic
parts and components
GB/T 11374, Thermal spraying coating. Nondestructive methods for
alloy that contains 5% of Mg, which is codenamed Al-Mg5 or LF5.
6.2 Operation
6.2.1 Workpiece surface pretreatment
6.2.1.1 General rules
For the to-be-sprayed surface which is heavily polluted, before sandblasting,
the workpiece shall be cleaned, and special methods shall be used to remove
deposits such as oil stains; for the to-be-sprayed surface which is lightly
contaminated, sandblasting pretreatment can be performed directly. For
workpieces which are locally sprayed, not only the dirt at the spraying site, but
also the contaminants in the adjacent spraying area, shall be removed, so as
to prevent the contaminants from being sprayed into the spraying area during
the spraying process. The workpiece surface which has been pretreated shall
be a metal surface that has an off-white homogeneity, on which, there is neither
oil, nor rust, nor other contaminants.
6.2.1.2 Sandblasting pretreatment
Sandblasting pretreatment uses sands, of which the particle size is 10 mesh ~
20 mesh, and which is dry, high-hardness and multi-angle, such as brown
corundum sand, copper ore or steel sand. When a thinner metal substrate is
sprayed, the pressure shall be 0.3 MPa ~ 0.4 MPa; when a thicker substrate is
sprayed, the pressure shall be ≥ 0.6 MPa, the sandblasting angle shall usually
be 70°, and the sandblasting time shall not be too long. After the sandblasting
pretreatment, the oil stain and rust layer on the surface of the substrate shall
be removed, and the de-rusting quality shall reach level-Sa2.5.
6.2.1.3 Inspection of surface roughness
The surface roughness of the workpiece, after sandblasting, shall meet the
requirements of Rz 25 μm ~ 100 μm in GB/T 11373-2017.
6.2.1.4 Surface cleanliness
The surface cleanliness of the workpiece, after sandblasting, shall comply with
level-Sa2.5 in GB/T 8923.1-2011.
6.2.1.5 Sandblasting roughening treatment
The workpiece surface after sandblasting roughening treatment is easily
contaminated by the outside; therefore, it is necessary to avoid touching by
hand and blowing. The treated surface shall be sprayed within 2h ~ 3h. If the
spraying cannot be performed on time, it’s necessary to use a clean plastic film
to cover and protect it. If it is to be moved, avoid secondary pollution on the
surface.
firstly be used to pretreat the coating. Frequently-used sealing agents include
paraffin, vinyl, silicone resin, phenolic, modified boxwood phenolic,
polyurethane, titanium nano-polymer coatings and so on. When sealing,
different sealing agents shall be selected according to different ambient
temperatures.
6.2.3.1.3.2 Spraying of zinc-aluminum-magnesium-rare earth alloy coating
plays a role of self-sealing, which leaves out manual sealing.
6.2.3.2 Coating
The coating, through sealing treatment, can be coated for its aesthetic
appearance or extended life.
6.2.3.3 Compatibility
Whether the metal coating is sealed or not shall be resolved by mutual
agreement. The coating system shall be compatible with the metal coating or
the sealant; when needed, perform a test to confirm the compatibility between
the metal coating and the material.
7 Test method
7.1 Thickness measurement
7.1.1 Magnetic measurement
Magnetic measurement has the advantage of non-destructive, fast and being
capable to directly measure any part of any to-be-test surface. In addition, both
the properties and the standard thickness values of the coating (Zn, Al) which
is sprayed on the steel substrate are beneficial to achieve a satisfactory
measurement accuracy for the method. Therefore, for a given sample, as long
as the magnetic thickness gauge is properly calibrated according to the
standard regulations and the agreement between the supplier and the buyer,
the magnetic measurement can provide an effective and accurate acceptance
check result. Perform the specific method according to the requirements of
GB/T 4956.
7.1.2 Cross-section microscopy
Cross-section microscopy refers to the measurement of the coating thickness
on the cross-section under a microscope, which is also a method that is used
to examine the thickness of a metal coating. The sample preparation method is
specified in GB/T 6462. In order to prevent the coating from peeling off from the
substrate and the edges, use a plastic or a low-melting-point alloy to fix the
sample, and use a polishing agent to inspect the surface. The specific
Appendix A
(Normative)
Test method of the coating thickness -- cross-section microscopy
A.1 Thickness test
A.1.1 Coating of which the area is 1 m2
When the coating area is within 1 cm2, the local thickness at any given point
shall be the coating thickness that is measured on the base level of 1 cm2.
Since various methods which are suitable for the measurement of coating
thickness are performed on measuring surfaces of different sizes; therefore, the
following methods are used to determine the local thickness of any part of the
coating (see Table A.1):
-- W...
Share
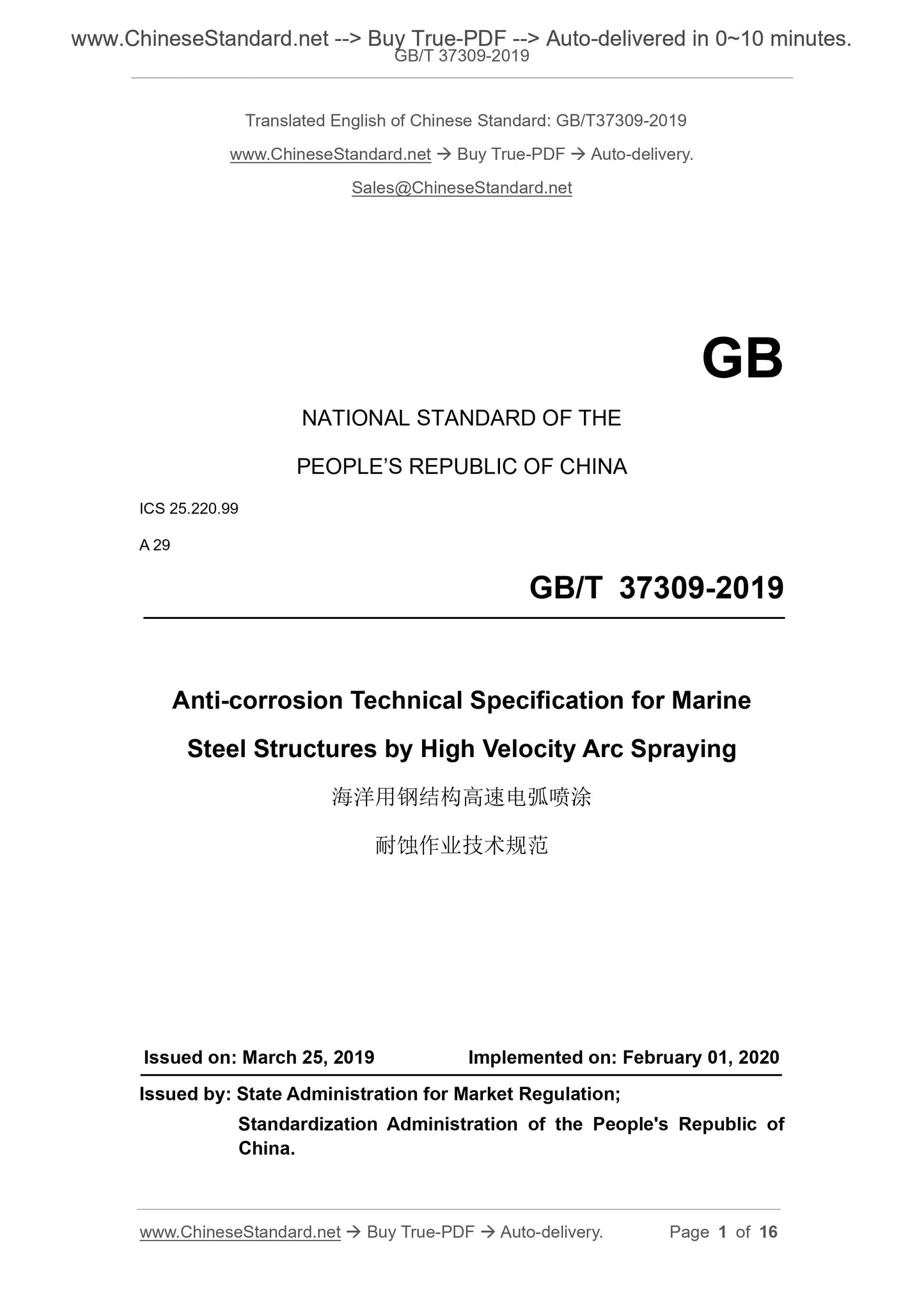
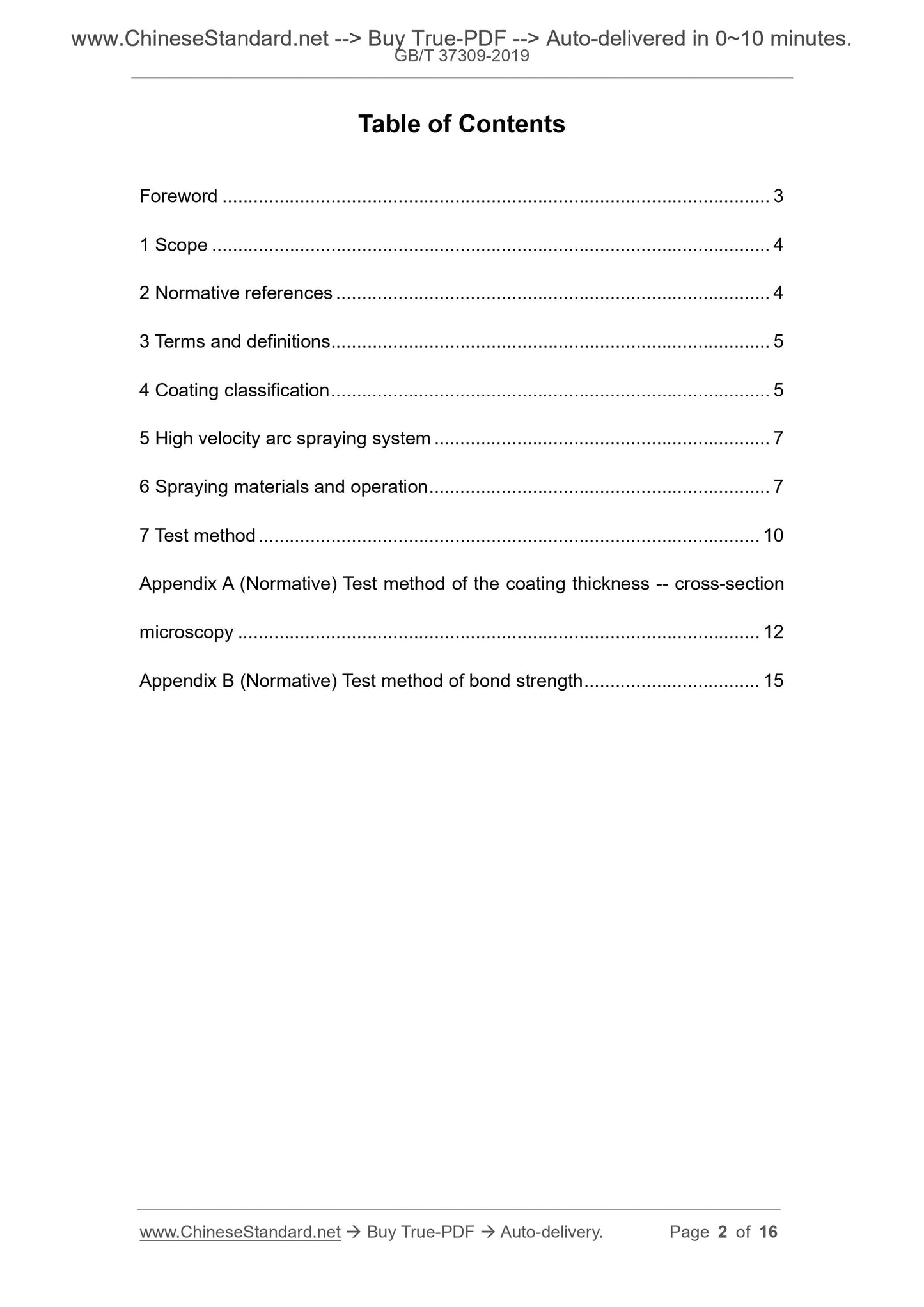
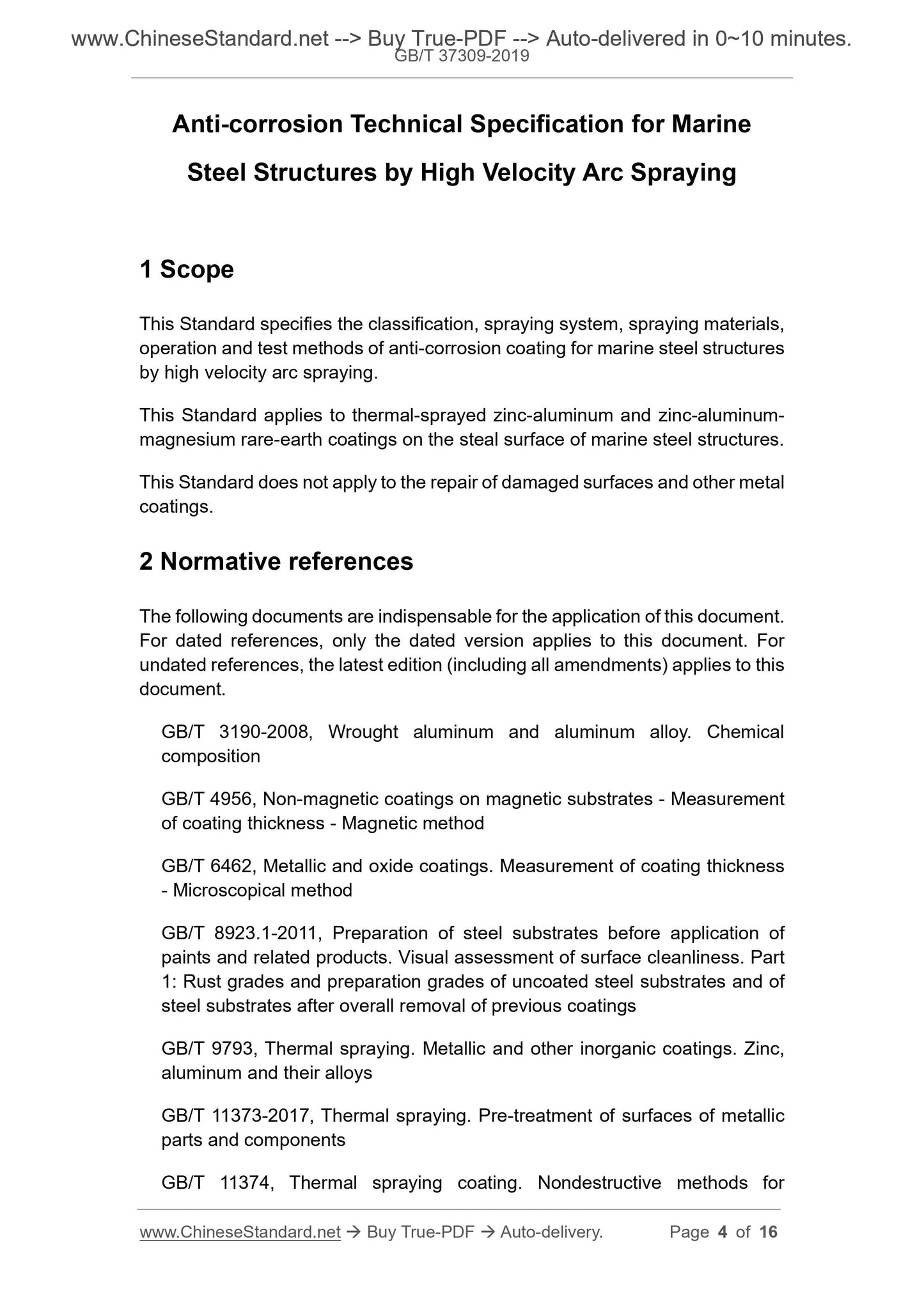
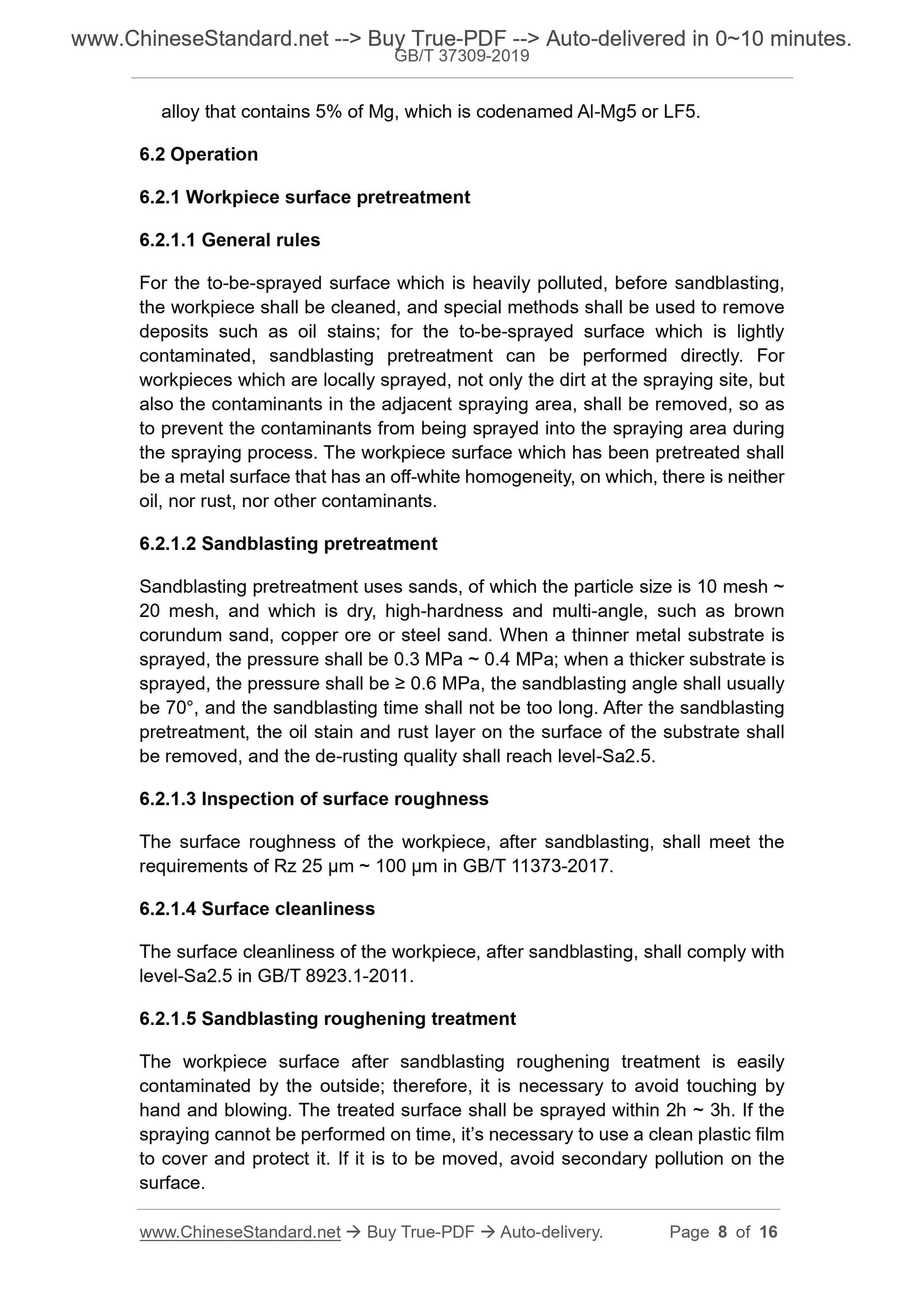
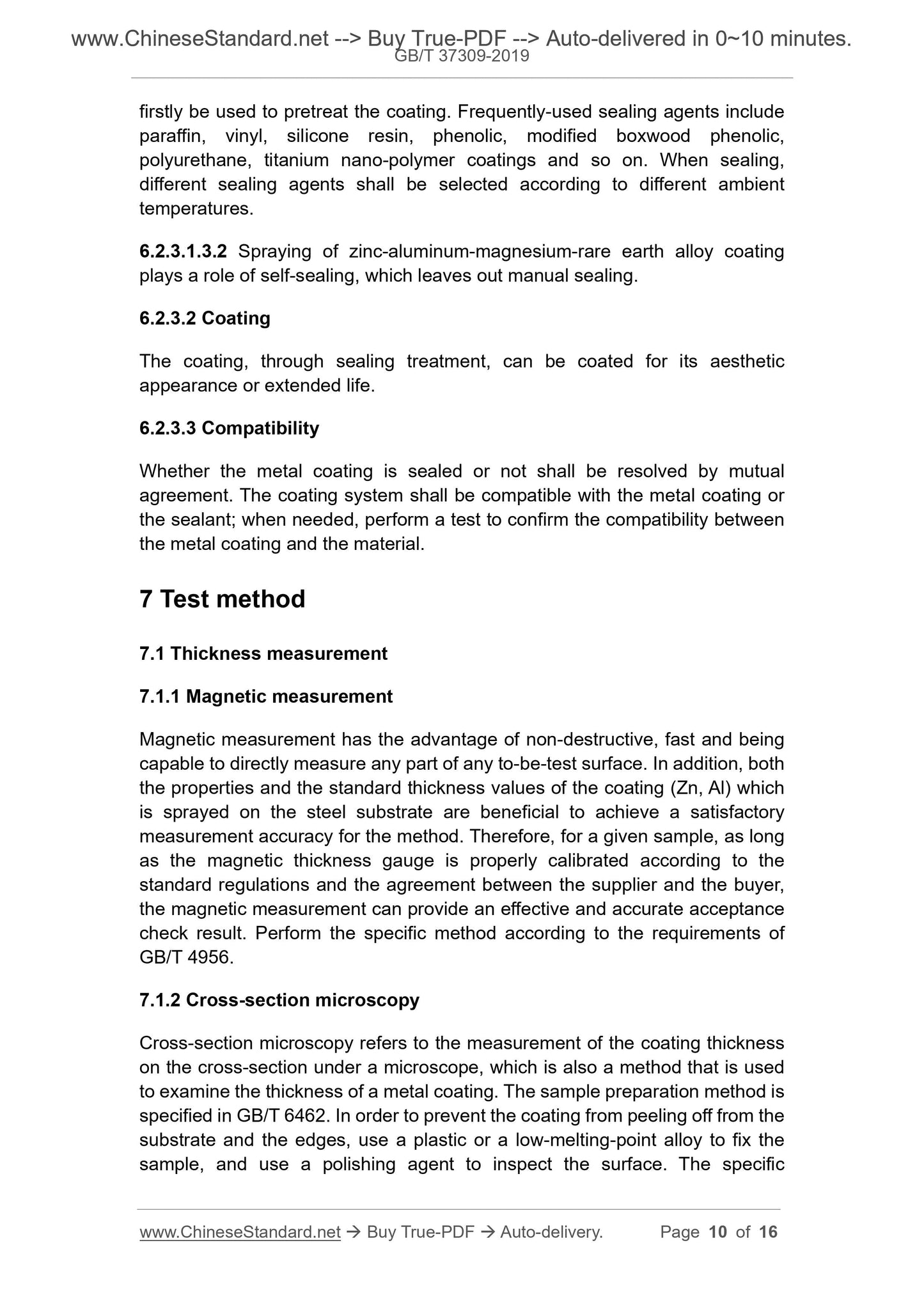

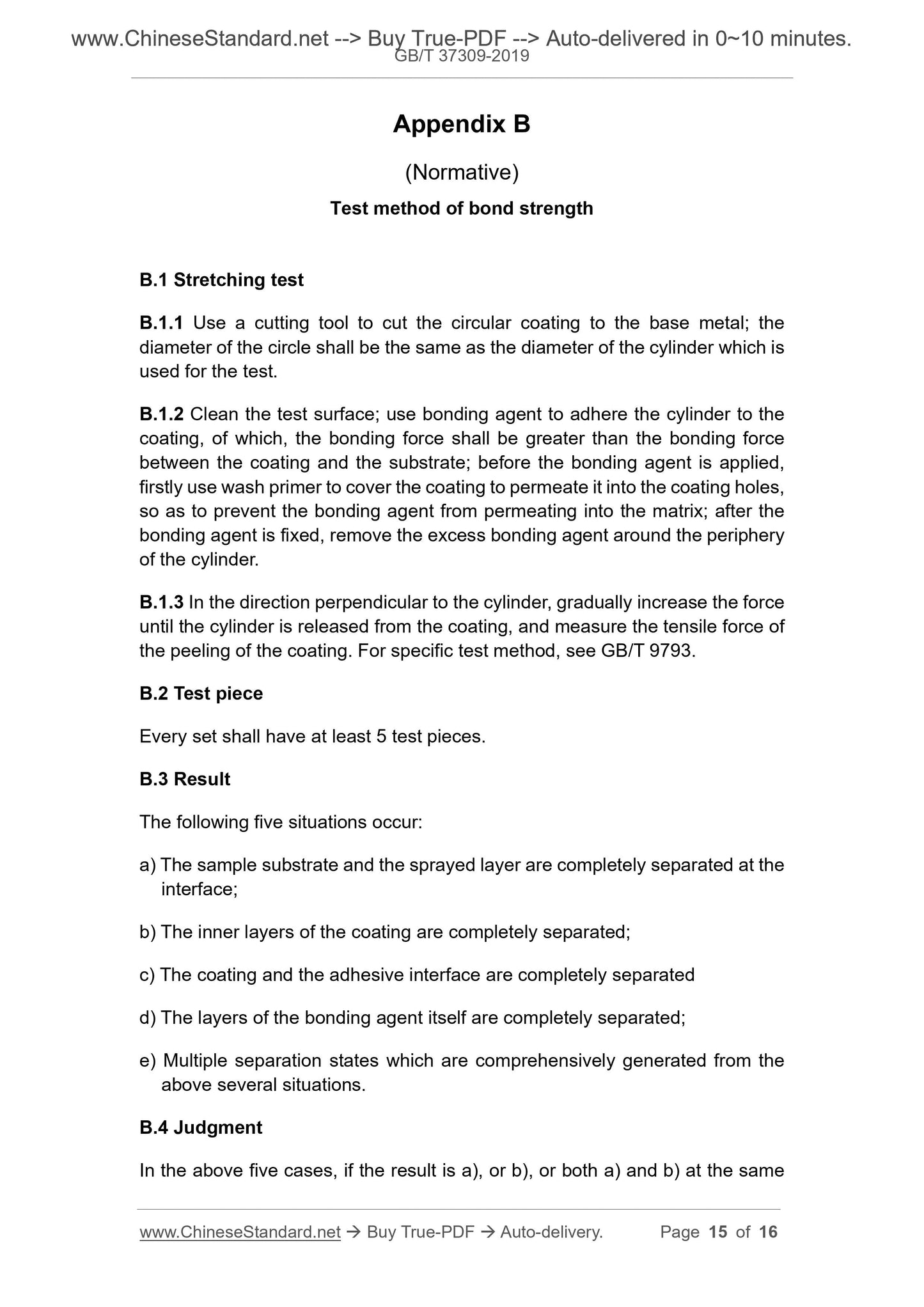