1
/
of
6
PayPal, credit cards. Download editable-PDF and invoice in 1 second!
GB/T 39330-2020 English PDF (GBT39330-2020)
GB/T 39330-2020 English PDF (GBT39330-2020)
Regular price
$135.00 USD
Regular price
Sale price
$135.00 USD
Unit price
/
per
Shipping calculated at checkout.
Couldn't load pickup availability
Delivery: 3 seconds. Download true-PDF + Invoice.
Get QUOTATION in 1-minute: Click GB/T 39330-2020
Historical versions: GB/T 39330-2020
Preview True-PDF (Reload/Scroll if blank)
GB/T 39330-2020: Technical specification for surface treatment of titanium alloy castings
GB/T 39330-2020
GB
NATIONAL STANDARD OF THE
PEOPLE’S REPUBLIC OF CHINA
ICS 77.120.50
J 31
Technical specification for surface treatment of
titanium alloy castings
ISSUED ON: NOVEMBER 19, 2020
IMPLEMENTED ON: JUNE 1, 2021
Issued by: State Administration for Market Regulation;
Standardization Administration of the People's Republic of
China.
Table of Contents
Foreword ... 3
1 Scope ... 4
2 Normative references ... 4
3 Surface treatment ... 4
4 Quality inspection ... 9
5 Quality control ... 11
6 Technical safety ... 12
Technical specification for surface treatment of
titanium alloy castings
1 Scope
This Standard specifies surface treatment, quality inspection, quality control
and technical safety of surface of titanium and titanium alloy castings.
This Standard is applicable to surface treatment of titanium and titanium alloy
castings produced by graphite processing molds, sand molds, metal molds and
investment casting molds.
2 Normative references
The following referenced documents are indispensable for the application of
this document. For dated references, only the edition cited applies. For undated
references, the latest edition of the referenced document (including any
amendments) applies.
GB/T 337.1, Concentrated nitric acid for industrial use
GB/T 4698.15, Methods for chemical analysis of titanium sponge, titanium
and titanium alloys - Determination of hydrogen content
GB/T5750.1, Standard Examination Methods for Drinking Water - General
Principles
GB/T 6614, Titanium and titanium alloy castings
GB/T 7744, Hydrofluoric Acid for Industrial Use
3 Surface treatment
3.1 Sandblasting
3.1.1 General requirements
3.1.1.1 The gas used for drying, sandblasting or other processes shall be
dehydrated and de-oiled.
3.1.1.2 During the sandblasting process and the processing operations of the
v - Corrosion rate, in milligrams per square millimeter hour [mg/(mm2·h)];
Δm – Mass loss, in milligrams (mg);
δ0 - Original thickness, in millimeters (mm);
m0 - Original mass, in milligrams (mg).
3.2.4.4 Rinse with water after pickling. Washing temperature: below
temperature for cold water, 30°C~60°C for warm water. Washing water
resistivity ≥1200Ω·cm (25°C). Total soluble solids (TDS) ≤600mg/L. PH value
is 5.5~8.5 (generally tap water requirements). The determination method is
according to GB/T 5750.1. Ensure that there is sufficient water flowing into the
cleaning tank. It shall be rinsed in the final stage of cleaning to ensure that the
casting surface is not contaminated.
3.2.4.5 Blow dry with clean, oil-free dry compressed air, or dry in an oven. Put
on clean gloves to remove the casting. Use clean packaging materials to protect
castings.
3.2.5 Pickling solution preparation, analysis, maintenance and
adjustment
3.2.5.1 When preparing the solution, add chemicals according to the ratio. Stir
evenly after preparation. The depth of the tank solution is generally not more
than two-thirds of the depth of the tank.
3.2.5.2 The concentration of titanium ions in acid solutions shall be analyzed
regularly. The interval period generally does not exceed 4 weeks. It can use
inductively coupled plasma atomic emission spectrometer to analyze.
3.2.5.3 Adjust the solution according to the analysis result of the solution. Adjust
according to the composition specified in 3.2.3.1. Add the required amount after
the loss of each component. Then stir well.
3.2.5.4 If the titanium ion content in the pickling solution is more than 25g/L and
the pickling rate cannot meet the demand, the pickling liquid shall be scrapped.
The waste pickling liquid shall be packed into a sealed container and
transported to a qualified professional institution for disposal. The emissions
shall not be handled by themselves.
3.2.6 Purification of acid gas
The acid gas generated during the pickling process shall be purified before
being discharged into the atmosphere. Discharge only after meeting
environmental discharge standards.
4 Quality inspection
4.1 Sandblasting quality
The castings after sandblasting shall meet the following requirements:
a) The surface roughness shall reach Ra3.2μm ~Ra12.5μm.
b) The surface roughness shall be uniform and free of scale, no sandblasting
debris, no discoloration, no oily materials, no fingerprints and other
contaminants.
c) If the above situation occurs, it shall be sandblasted again.
d) When the casting is deformed, it shall be sandblasted again after
correction.
e) The abrasive used for sandblasting shall be checked regularly and meet
the requirements of 3.1.2. If it does not meet the requirements, the blasting
material shall be replaced.
4.2 Pickling quality
4.2.1 Appearance
4.2.1.1 The surface quality of the pickled castings shall be 100% visually
inspected. The surface shall be smooth, with metallic luster or silvery white or
off-white.
4.2.1.2 The surface of the casting shall not have corroded defects such as pits
or spots that have not been washed away by acid.
4.2.1.3 There shall be no oil stains, handprints, seal marks and handwriting on
the surface of the casting.
4.2.1.4 There shall be no mechanical damage such as pressure pits, bumps,
and scratches on the surface of the casting.
4.2.2 Hydrogen content and increase in hydrogen
4.2.2.1 Under the condition of ensuring the composition of the tank liquid and
the specified temperature, pickling shall not exceed the prescribed time to avoid
adding more hydrogen. The hydrogen increase shall be checked regularly. The
thickness of the annealed ZTC4 alloy test piece is 1mm~1.5mm, and the weight
is about 0.3g. When each side is pickled at 0.025mm, the hydrogen increase
shall not exceed 0.003%. When the hydrogen increase exceeds 0.003%,
production shall be stopped immediately and the cause shall be found.
discoloration, oily materials, fingerprints or other contaminants.
b) Immerse in pure water with a resistivity of not less than 50Ω·m for several
seconds. After being taken out of the water, there shall be no water film
broke on the surface.
c) If the above situation occurs, clean it again.
d) The casting must not be deformed during the sandblasting process.
e) The blasting material used for blasting shall be checked regularly to
ensure that it meets the requirements.
5 Quality control
5.1 Equipment and instruments
5.1.1 The equipment and instruments shall have certificates. Perform
verification or calibration according to the specified cycle.
5.1.2 The equipment and instruments that have not been verified or calibrated,
have failed verification, and have exceeded their effective period of use shall
not be used.
5.2 Workshop environment
5.2.1 The workshop casting warehouse shall be isolated from the production
room to prevent corrosion of the castings.
5.2.2 In addition to effective air intake and exhaust systems, the workshop shall
also have good natural ventilation.
5.2.3 The workshop shall have good natural light or lighting. Local lighting shall
be provided for inspection and other important work stations in the workshop.
5.2.4 The workshop production site shall be kept clean and tidy. The main
pickling tank shall be covered when it is not working. Bridge plates shall be
placed between each pickling tank to prevent the solution from dripping on the
ground.
5.2.5 In the design of the new plant, the workshop temperature shall not be <...
Get QUOTATION in 1-minute: Click GB/T 39330-2020
Historical versions: GB/T 39330-2020
Preview True-PDF (Reload/Scroll if blank)
GB/T 39330-2020: Technical specification for surface treatment of titanium alloy castings
GB/T 39330-2020
GB
NATIONAL STANDARD OF THE
PEOPLE’S REPUBLIC OF CHINA
ICS 77.120.50
J 31
Technical specification for surface treatment of
titanium alloy castings
ISSUED ON: NOVEMBER 19, 2020
IMPLEMENTED ON: JUNE 1, 2021
Issued by: State Administration for Market Regulation;
Standardization Administration of the People's Republic of
China.
Table of Contents
Foreword ... 3
1 Scope ... 4
2 Normative references ... 4
3 Surface treatment ... 4
4 Quality inspection ... 9
5 Quality control ... 11
6 Technical safety ... 12
Technical specification for surface treatment of
titanium alloy castings
1 Scope
This Standard specifies surface treatment, quality inspection, quality control
and technical safety of surface of titanium and titanium alloy castings.
This Standard is applicable to surface treatment of titanium and titanium alloy
castings produced by graphite processing molds, sand molds, metal molds and
investment casting molds.
2 Normative references
The following referenced documents are indispensable for the application of
this document. For dated references, only the edition cited applies. For undated
references, the latest edition of the referenced document (including any
amendments) applies.
GB/T 337.1, Concentrated nitric acid for industrial use
GB/T 4698.15, Methods for chemical analysis of titanium sponge, titanium
and titanium alloys - Determination of hydrogen content
GB/T5750.1, Standard Examination Methods for Drinking Water - General
Principles
GB/T 6614, Titanium and titanium alloy castings
GB/T 7744, Hydrofluoric Acid for Industrial Use
3 Surface treatment
3.1 Sandblasting
3.1.1 General requirements
3.1.1.1 The gas used for drying, sandblasting or other processes shall be
dehydrated and de-oiled.
3.1.1.2 During the sandblasting process and the processing operations of the
v - Corrosion rate, in milligrams per square millimeter hour [mg/(mm2·h)];
Δm – Mass loss, in milligrams (mg);
δ0 - Original thickness, in millimeters (mm);
m0 - Original mass, in milligrams (mg).
3.2.4.4 Rinse with water after pickling. Washing temperature: below
temperature for cold water, 30°C~60°C for warm water. Washing water
resistivity ≥1200Ω·cm (25°C). Total soluble solids (TDS) ≤600mg/L. PH value
is 5.5~8.5 (generally tap water requirements). The determination method is
according to GB/T 5750.1. Ensure that there is sufficient water flowing into the
cleaning tank. It shall be rinsed in the final stage of cleaning to ensure that the
casting surface is not contaminated.
3.2.4.5 Blow dry with clean, oil-free dry compressed air, or dry in an oven. Put
on clean gloves to remove the casting. Use clean packaging materials to protect
castings.
3.2.5 Pickling solution preparation, analysis, maintenance and
adjustment
3.2.5.1 When preparing the solution, add chemicals according to the ratio. Stir
evenly after preparation. The depth of the tank solution is generally not more
than two-thirds of the depth of the tank.
3.2.5.2 The concentration of titanium ions in acid solutions shall be analyzed
regularly. The interval period generally does not exceed 4 weeks. It can use
inductively coupled plasma atomic emission spectrometer to analyze.
3.2.5.3 Adjust the solution according to the analysis result of the solution. Adjust
according to the composition specified in 3.2.3.1. Add the required amount after
the loss of each component. Then stir well.
3.2.5.4 If the titanium ion content in the pickling solution is more than 25g/L and
the pickling rate cannot meet the demand, the pickling liquid shall be scrapped.
The waste pickling liquid shall be packed into a sealed container and
transported to a qualified professional institution for disposal. The emissions
shall not be handled by themselves.
3.2.6 Purification of acid gas
The acid gas generated during the pickling process shall be purified before
being discharged into the atmosphere. Discharge only after meeting
environmental discharge standards.
4 Quality inspection
4.1 Sandblasting quality
The castings after sandblasting shall meet the following requirements:
a) The surface roughness shall reach Ra3.2μm ~Ra12.5μm.
b) The surface roughness shall be uniform and free of scale, no sandblasting
debris, no discoloration, no oily materials, no fingerprints and other
contaminants.
c) If the above situation occurs, it shall be sandblasted again.
d) When the casting is deformed, it shall be sandblasted again after
correction.
e) The abrasive used for sandblasting shall be checked regularly and meet
the requirements of 3.1.2. If it does not meet the requirements, the blasting
material shall be replaced.
4.2 Pickling quality
4.2.1 Appearance
4.2.1.1 The surface quality of the pickled castings shall be 100% visually
inspected. The surface shall be smooth, with metallic luster or silvery white or
off-white.
4.2.1.2 The surface of the casting shall not have corroded defects such as pits
or spots that have not been washed away by acid.
4.2.1.3 There shall be no oil stains, handprints, seal marks and handwriting on
the surface of the casting.
4.2.1.4 There shall be no mechanical damage such as pressure pits, bumps,
and scratches on the surface of the casting.
4.2.2 Hydrogen content and increase in hydrogen
4.2.2.1 Under the condition of ensuring the composition of the tank liquid and
the specified temperature, pickling shall not exceed the prescribed time to avoid
adding more hydrogen. The hydrogen increase shall be checked regularly. The
thickness of the annealed ZTC4 alloy test piece is 1mm~1.5mm, and the weight
is about 0.3g. When each side is pickled at 0.025mm, the hydrogen increase
shall not exceed 0.003%. When the hydrogen increase exceeds 0.003%,
production shall be stopped immediately and the cause shall be found.
discoloration, oily materials, fingerprints or other contaminants.
b) Immerse in pure water with a resistivity of not less than 50Ω·m for several
seconds. After being taken out of the water, there shall be no water film
broke on the surface.
c) If the above situation occurs, clean it again.
d) The casting must not be deformed during the sandblasting process.
e) The blasting material used for blasting shall be checked regularly to
ensure that it meets the requirements.
5 Quality control
5.1 Equipment and instruments
5.1.1 The equipment and instruments shall have certificates. Perform
verification or calibration according to the specified cycle.
5.1.2 The equipment and instruments that have not been verified or calibrated,
have failed verification, and have exceeded their effective period of use shall
not be used.
5.2 Workshop environment
5.2.1 The workshop casting warehouse shall be isolated from the production
room to prevent corrosion of the castings.
5.2.2 In addition to effective air intake and exhaust systems, the workshop shall
also have good natural ventilation.
5.2.3 The workshop shall have good natural light or lighting. Local lighting shall
be provided for inspection and other important work stations in the workshop.
5.2.4 The workshop production site shall be kept clean and tidy. The main
pickling tank shall be covered when it is not working. Bridge plates shall be
placed between each pickling tank to prevent the solution from dripping on the
ground.
5.2.5 In the design of the new plant, the workshop temperature shall not be <...
Share
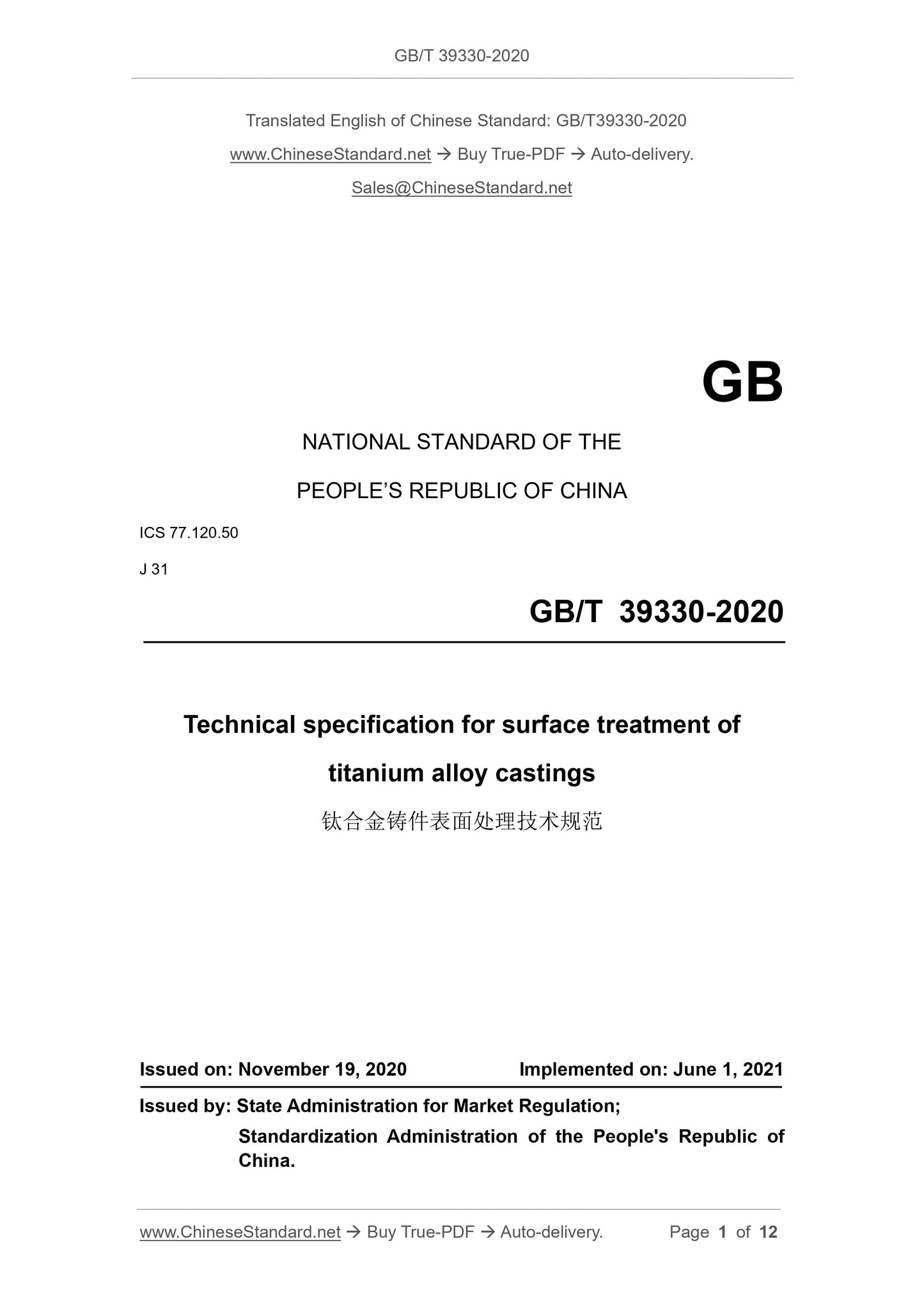
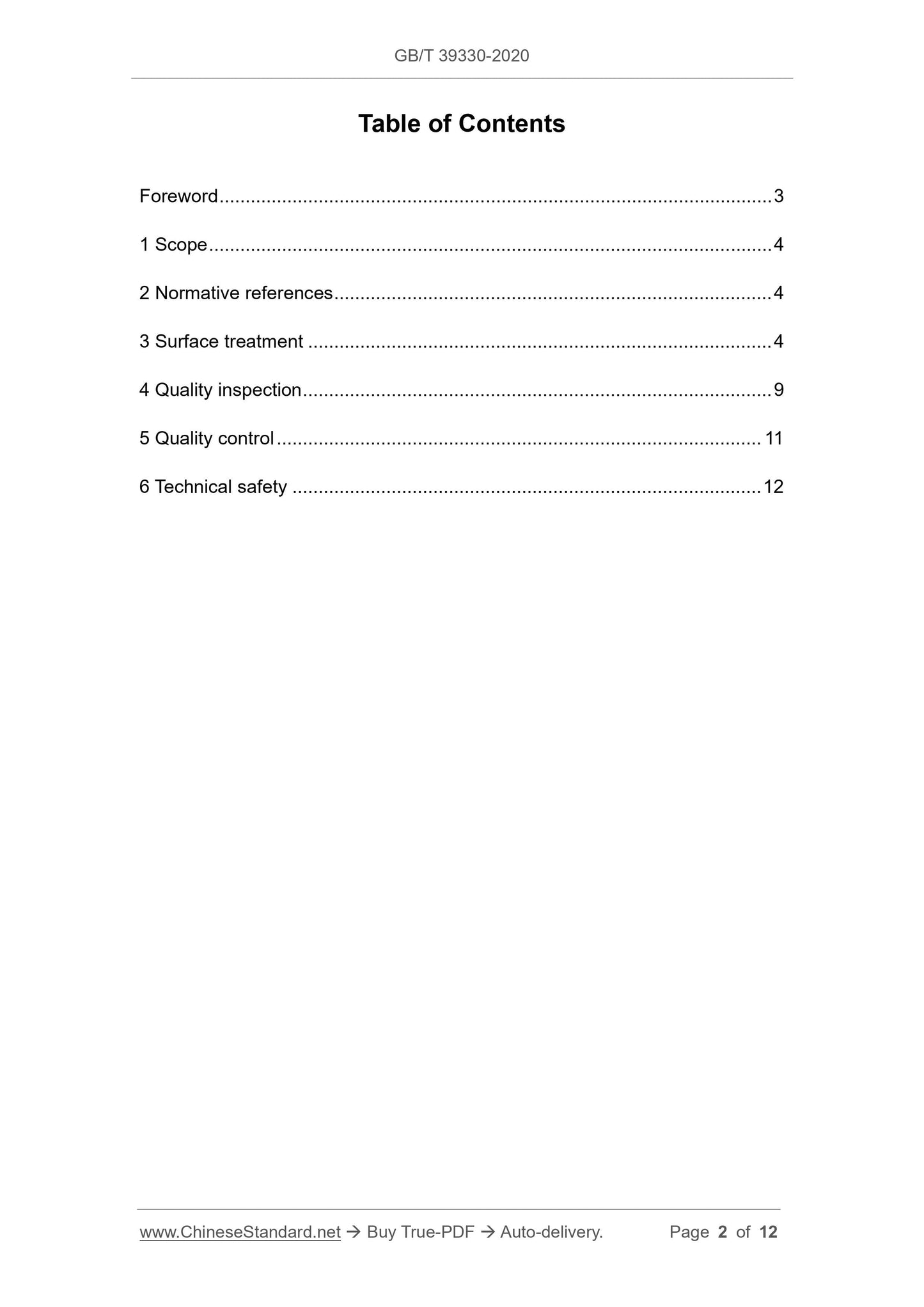
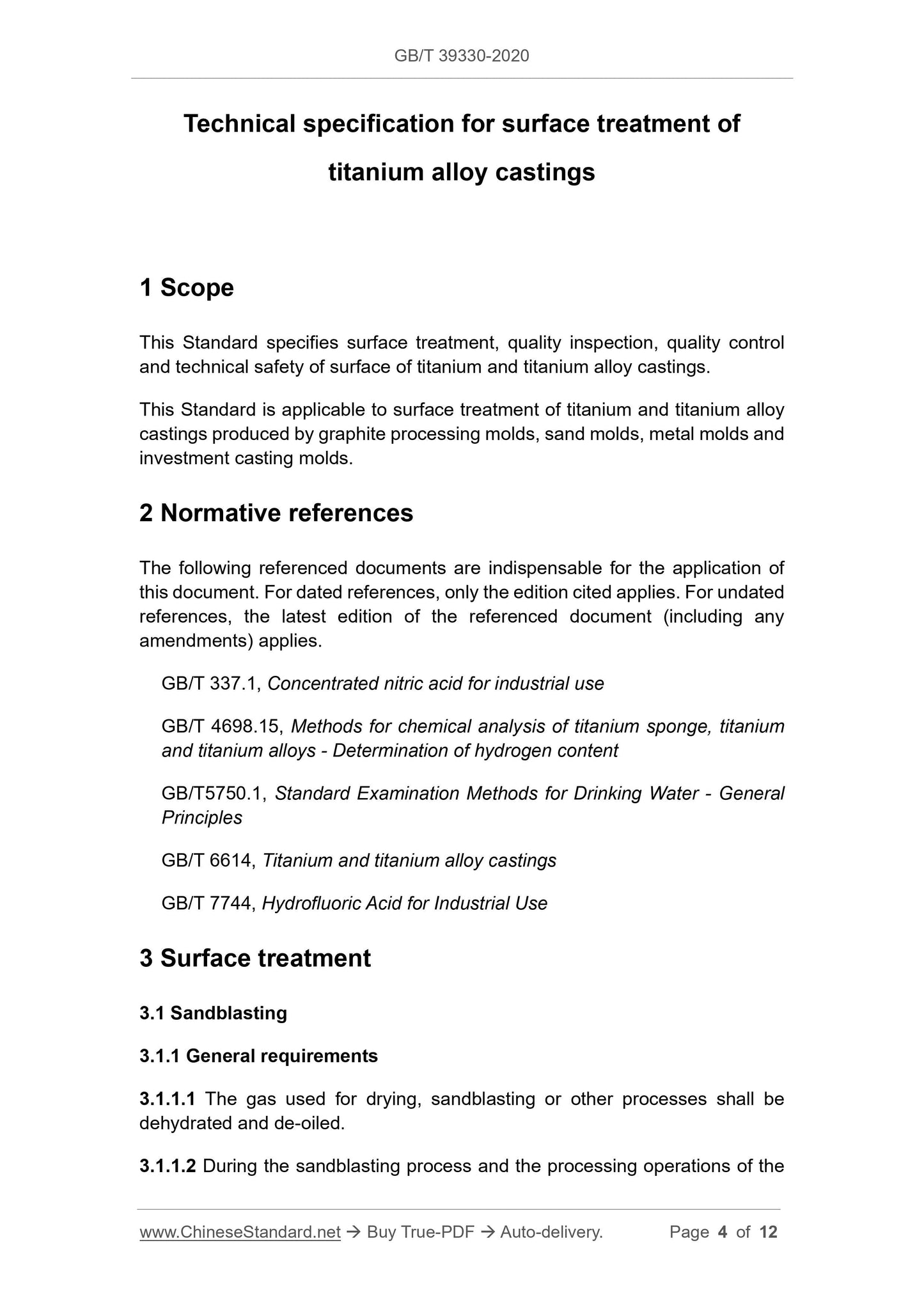
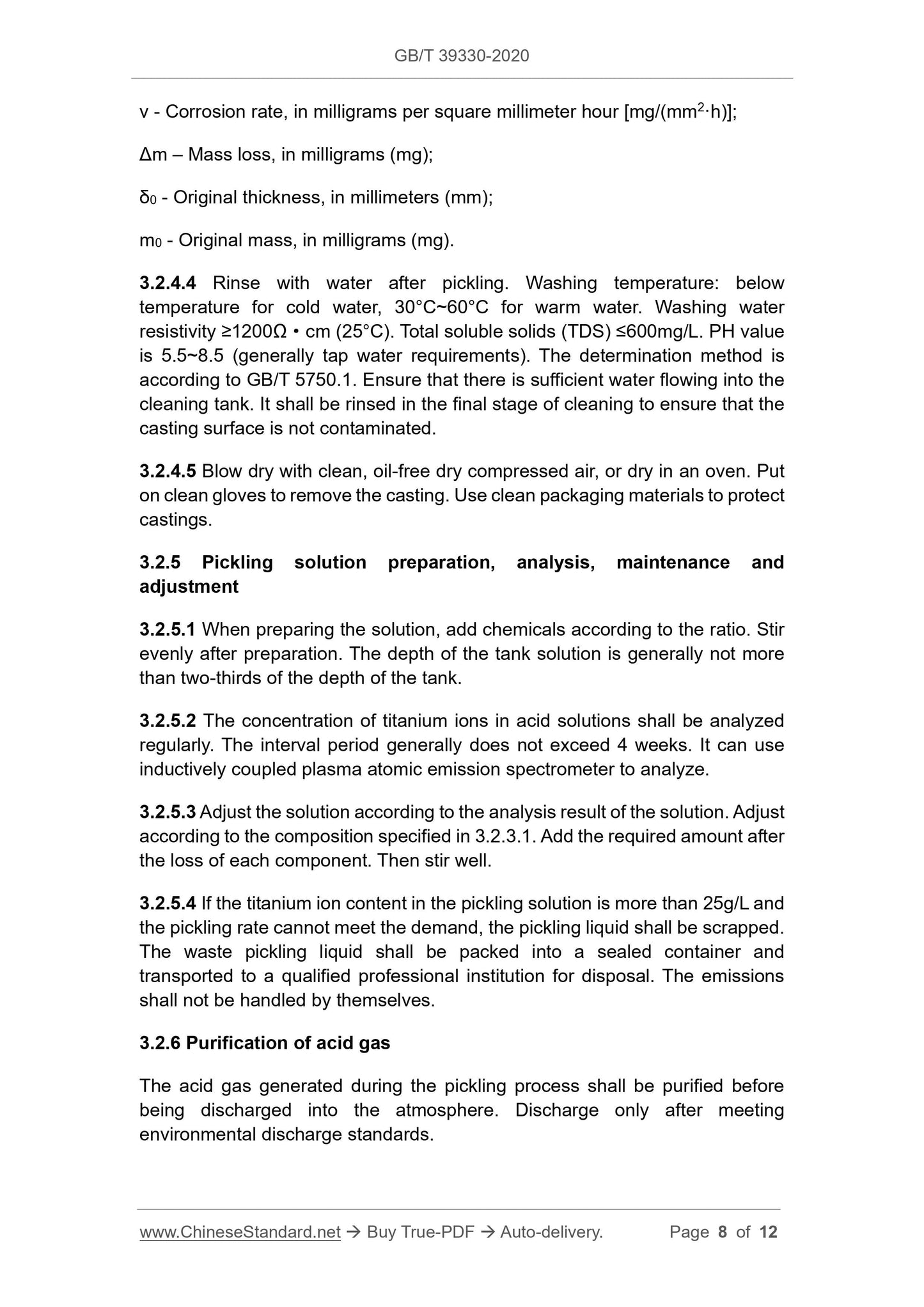
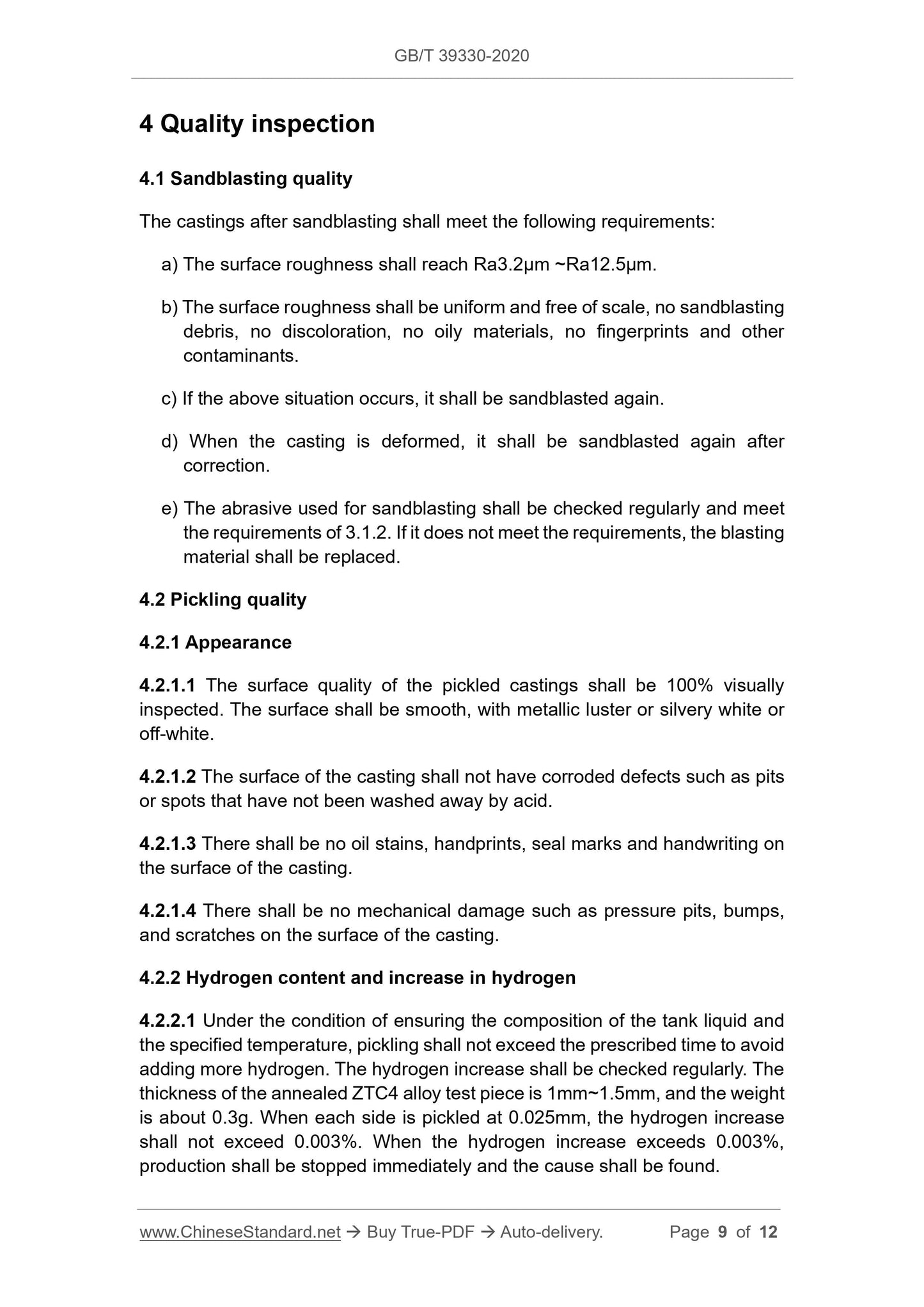
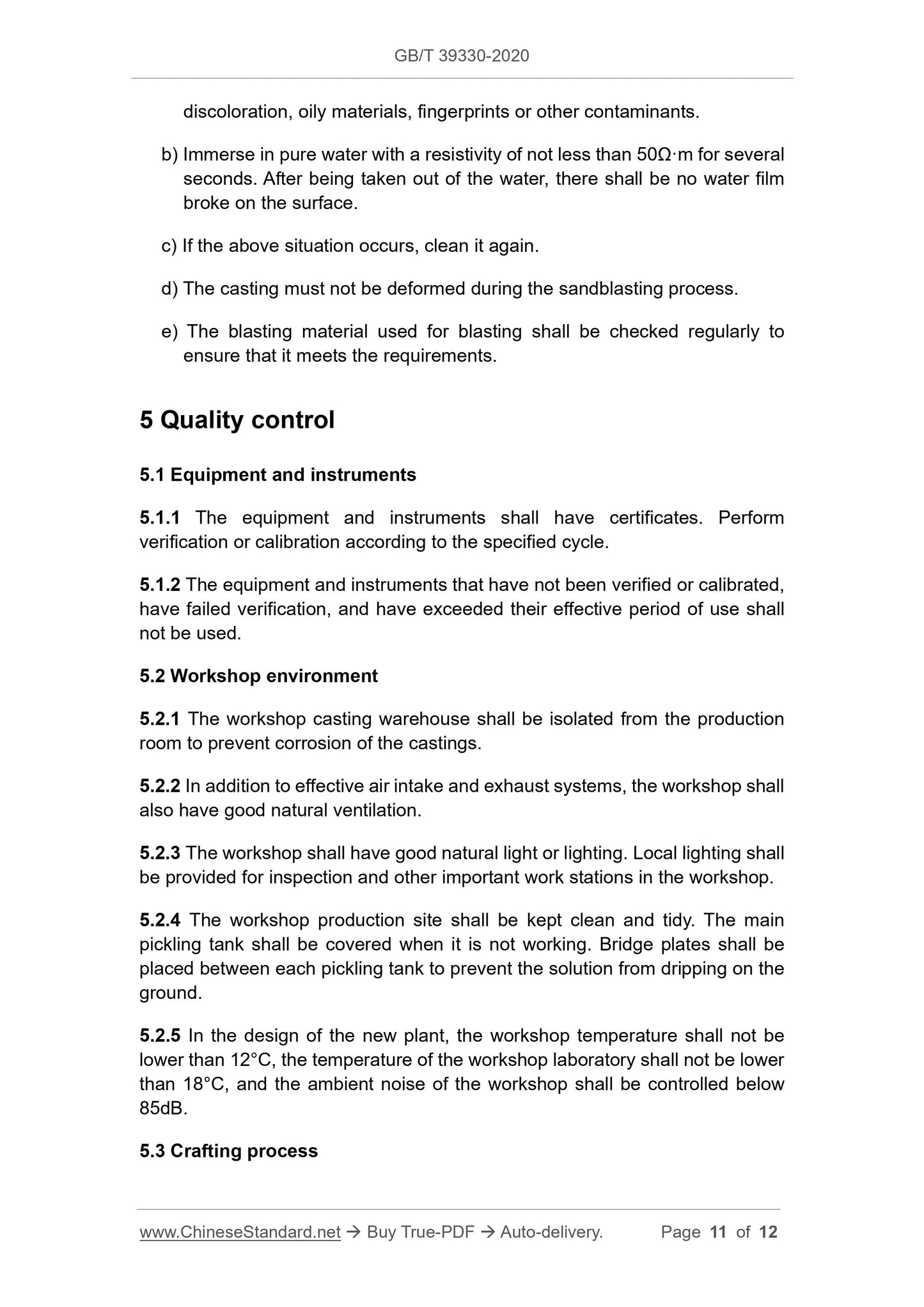