1
/
of
8
PayPal, credit cards. Download editable-PDF & invoice in 1 second!
GB/T 40212-2021 English PDF (GBT40212-2021)
GB/T 40212-2021 English PDF (GBT40212-2021)
Regular price
$175.00 USD
Regular price
Sale price
$175.00 USD
Unit price
/
per
Shipping calculated at checkout.
Couldn't load pickup availability
Delivery: 3 seconds. Download true-PDF + Invoice.
Get QUOTATION in 1-minute: Click GB/T 40212-2021
Historical versions: GB/T 40212-2021
Preview True-PDF (Reload/Scroll if blank)
GB/T 40212-2021: The classification and reference architecture of cloud service platform for industrial robot
GB/T 40212-2021
GB
NATIONAL STANDARD OF THE
PEOPLE’S REPUBLIC OF CHINA
ICS 25.040.30
L 67
The classification and reference architecture of cloud
service platform for industrial robot
ISSUED ON: MAY 21, 2021
IMPLEMENTED ON: DECEMBER 01, 2021
Issued by: State Administration for Market Regulation;
Standardization Administration of the People’s Republic of
China.
Table of Contents
Foreword ... 3
1 Scope ... 4
2 Normative references ... 4
3 Terms and definitions ... 4
4 Abbreviations ... 6
5 Overview of cloud service platform for industrial robot ... 6
6 Classification of cloud service platform for industrial robot ... 8
7 Reference architecture of cloud service platform for industrial robot ... 9
References ... 15
The classification and reference architecture of cloud
service platform for industrial robot
1 Scope
This Standard gives the characteristics, classification and reference
architecture (physical access layer, communication layer, base layer, platform
layer and application layer) of the cloud service platform for industrial robot.
This Standard applies to robot manufacturers, robot integrators and robot users,
and provides guidance for them in the process of building and using cloud
service platform for industrial robot.
2 Normative references
The following documents are indispensable for the application of this document.
For dated references, only the dated version applies to this document. For
undated references, the latest edition (including all amendments) applies to this
document.
GB/T 11457-2006, Information technology - Software engineering
terminology
GB/T 12643-2013, Robots and robotic devices - Vocabulary
GB/T 16656.1-2008, Industrial automation systems and integration - Product
data representation and exchange - Part 1: Overview and fundamental
principles
GB/T 37393-2019, Digital factory - General technical requirements
3 Terms and definitions
Terms and definitions determined by GB/T 12643-2013, GB/T 11457-2006 and
GB/T 16656.1-2008, and the following ones are applicable to this document.
3.1
Industrial robot
The automatic control, reprogrammable, multi-purpose manipulator which is
used in industrial automation, fixed or mobile, that can program three or more
axes.
probability simulation processes, to complete the mapping in the virtual space,
thereby reflecting the full life cycle process of the corresponding physical
equipment.
3.7
Model
A representation of a process, equipment, or concept in the real world.
[GB/T 11457-2006, definition 2.964]
4 Abbreviations
The following abbreviations apply to this document.
ERP: Enterprise Resource Planning
IaaS: Infrastructure as a Service
MES: Manufacturing Execution System
OPC: OPC Foundation (a non-profit industry association)
UA: Unified Architecture
PLM: Product Lifecycle Management
5 Overview of cloud service platform for industrial
robot
5.1 Applicable objects and goals
The cloud service platform for industrial robot is applicable to robot
manufacturers, robot integrators and robot users.
The cloud service platform for industrial robot has different goals according to
its applicable objects:
-- For robot manufacturers, it realizes product value-added through services,
and realizes robot product design optimization and equipment health
management;
-- For robot integrators, it researches the application innovation of industrial
robots and carries out engineering implementation verification;
-- For robot users, it makes field equipment easy to manage, stabilizes
product quality, and performs predictive maintenance.
5.2 Demand scenarios
5.2.1 Demand scenarios of robot manufacturers
The demand scenarios of robot manufacturers are as follows:
a) Realize product value-added through services: apply big data analysis,
mobile Internet and other technologies, to automatically generate product
operation and application status reports, and push them to the user side,
so as to provide users with online monitoring, remote services, fault
prediction and diagnosis, health status evaluations and other value-added
services;
b) Realize the optimization of industrial robot product design: perform
technical optimization of common equipment failures and problems in
product design and production, through industrial robot operating data
statistics and failure analysis;
c) Realize the health management of industrial robot equipment: based on
industrial robot big data and failure models, predict robot and production
line operation failures; ensure the stable operation of customer production
lines; avoid unplanned equipment shutdown due to damage to key parts.
5.2.2 Demand scenarios of robot integrators
The demand scenarios of robot integrators are as follows:
a) Research the application innovation of industrial robots through big data
processing analysis, data mining and data visualization display of
equipment applications;
b) Establish application requirements for industrial robots and build new
robot application scenarios;
c) Build a robot application data processing model; put forward solutions for
industry big data; verify project implementation.
5.2.3 Demand scenarios of robot users
The demand scenarios of robot users are as follows:
a) Field equipment management: through data collection, monitor the
operating status of factory/workshop robots; get equipment start-up rate,
operating rate, utilization rate, failure rate, and statistical information of
overall equipment effectiveness in real time, so that the production
7.2 Physical access layer
The physical access layer is the entrance for industrial robots to connect to the
cloud service platform, to directly connect to the industrial robot control system,
perception system or driving system, so that various industrial robots and their
supporting equipment can access the cloud service platform network.
7.3 Communication layer
Different industrial robots usually use different physical interfaces and
communication protocols. The communication layer connects the industrial
robot to the digital workshop interconnection network through the field network,
and connects the industrial robot to the cloud network through the local
intelligent gateway/server, to realize the interconnection and
intercommunication of the industrial robot with other production equipment and
cloud service platforms. The communication layer mainly includes:
a) Field network. Use network technologies such as fieldbus, industrial
Ethernet, industrial wireless, to realize the interconnection and
intercommunication of industrial robots and digital workshop
interconnection networks. Combined with the situation of the industrial site,
make full use of the existing communication interfaces of industrial robots;
modify the existing robot equipment and network environment according
to local conditions, to realize the network foundation for industrial robot
access;
b) WAN/LAN. Use smart gateways, servers, and the like, to connect robots
to the cloud through a WAN/LAN through a mobile network or a wired
network, to realize the interconnection and intercommunication between
industrial robots and cloud service platforms, and establish a unified
communication mechanism between industrial robots and cloud service
platforms, so as to achieve mutual data exchange. The intelligent gateway
can be used as an independent enti...
Get QUOTATION in 1-minute: Click GB/T 40212-2021
Historical versions: GB/T 40212-2021
Preview True-PDF (Reload/Scroll if blank)
GB/T 40212-2021: The classification and reference architecture of cloud service platform for industrial robot
GB/T 40212-2021
GB
NATIONAL STANDARD OF THE
PEOPLE’S REPUBLIC OF CHINA
ICS 25.040.30
L 67
The classification and reference architecture of cloud
service platform for industrial robot
ISSUED ON: MAY 21, 2021
IMPLEMENTED ON: DECEMBER 01, 2021
Issued by: State Administration for Market Regulation;
Standardization Administration of the People’s Republic of
China.
Table of Contents
Foreword ... 3
1 Scope ... 4
2 Normative references ... 4
3 Terms and definitions ... 4
4 Abbreviations ... 6
5 Overview of cloud service platform for industrial robot ... 6
6 Classification of cloud service platform for industrial robot ... 8
7 Reference architecture of cloud service platform for industrial robot ... 9
References ... 15
The classification and reference architecture of cloud
service platform for industrial robot
1 Scope
This Standard gives the characteristics, classification and reference
architecture (physical access layer, communication layer, base layer, platform
layer and application layer) of the cloud service platform for industrial robot.
This Standard applies to robot manufacturers, robot integrators and robot users,
and provides guidance for them in the process of building and using cloud
service platform for industrial robot.
2 Normative references
The following documents are indispensable for the application of this document.
For dated references, only the dated version applies to this document. For
undated references, the latest edition (including all amendments) applies to this
document.
GB/T 11457-2006, Information technology - Software engineering
terminology
GB/T 12643-2013, Robots and robotic devices - Vocabulary
GB/T 16656.1-2008, Industrial automation systems and integration - Product
data representation and exchange - Part 1: Overview and fundamental
principles
GB/T 37393-2019, Digital factory - General technical requirements
3 Terms and definitions
Terms and definitions determined by GB/T 12643-2013, GB/T 11457-2006 and
GB/T 16656.1-2008, and the following ones are applicable to this document.
3.1
Industrial robot
The automatic control, reprogrammable, multi-purpose manipulator which is
used in industrial automation, fixed or mobile, that can program three or more
axes.
probability simulation processes, to complete the mapping in the virtual space,
thereby reflecting the full life cycle process of the corresponding physical
equipment.
3.7
Model
A representation of a process, equipment, or concept in the real world.
[GB/T 11457-2006, definition 2.964]
4 Abbreviations
The following abbreviations apply to this document.
ERP: Enterprise Resource Planning
IaaS: Infrastructure as a Service
MES: Manufacturing Execution System
OPC: OPC Foundation (a non-profit industry association)
UA: Unified Architecture
PLM: Product Lifecycle Management
5 Overview of cloud service platform for industrial
robot
5.1 Applicable objects and goals
The cloud service platform for industrial robot is applicable to robot
manufacturers, robot integrators and robot users.
The cloud service platform for industrial robot has different goals according to
its applicable objects:
-- For robot manufacturers, it realizes product value-added through services,
and realizes robot product design optimization and equipment health
management;
-- For robot integrators, it researches the application innovation of industrial
robots and carries out engineering implementation verification;
-- For robot users, it makes field equipment easy to manage, stabilizes
product quality, and performs predictive maintenance.
5.2 Demand scenarios
5.2.1 Demand scenarios of robot manufacturers
The demand scenarios of robot manufacturers are as follows:
a) Realize product value-added through services: apply big data analysis,
mobile Internet and other technologies, to automatically generate product
operation and application status reports, and push them to the user side,
so as to provide users with online monitoring, remote services, fault
prediction and diagnosis, health status evaluations and other value-added
services;
b) Realize the optimization of industrial robot product design: perform
technical optimization of common equipment failures and problems in
product design and production, through industrial robot operating data
statistics and failure analysis;
c) Realize the health management of industrial robot equipment: based on
industrial robot big data and failure models, predict robot and production
line operation failures; ensure the stable operation of customer production
lines; avoid unplanned equipment shutdown due to damage to key parts.
5.2.2 Demand scenarios of robot integrators
The demand scenarios of robot integrators are as follows:
a) Research the application innovation of industrial robots through big data
processing analysis, data mining and data visualization display of
equipment applications;
b) Establish application requirements for industrial robots and build new
robot application scenarios;
c) Build a robot application data processing model; put forward solutions for
industry big data; verify project implementation.
5.2.3 Demand scenarios of robot users
The demand scenarios of robot users are as follows:
a) Field equipment management: through data collection, monitor the
operating status of factory/workshop robots; get equipment start-up rate,
operating rate, utilization rate, failure rate, and statistical information of
overall equipment effectiveness in real time, so that the production
7.2 Physical access layer
The physical access layer is the entrance for industrial robots to connect to the
cloud service platform, to directly connect to the industrial robot control system,
perception system or driving system, so that various industrial robots and their
supporting equipment can access the cloud service platform network.
7.3 Communication layer
Different industrial robots usually use different physical interfaces and
communication protocols. The communication layer connects the industrial
robot to the digital workshop interconnection network through the field network,
and connects the industrial robot to the cloud network through the local
intelligent gateway/server, to realize the interconnection and
intercommunication of the industrial robot with other production equipment and
cloud service platforms. The communication layer mainly includes:
a) Field network. Use network technologies such as fieldbus, industrial
Ethernet, industrial wireless, to realize the interconnection and
intercommunication of industrial robots and digital workshop
interconnection networks. Combined with the situation of the industrial site,
make full use of the existing communication interfaces of industrial robots;
modify the existing robot equipment and network environment according
to local conditions, to realize the network foundation for industrial robot
access;
b) WAN/LAN. Use smart gateways, servers, and the like, to connect robots
to the cloud through a WAN/LAN through a mobile network or a wired
network, to realize the interconnection and intercommunication between
industrial robots and cloud service platforms, and establish a unified
communication mechanism between industrial robots and cloud service
platforms, so as to achieve mutual data exchange. The intelligent gateway
can be used as an independent enti...
Share
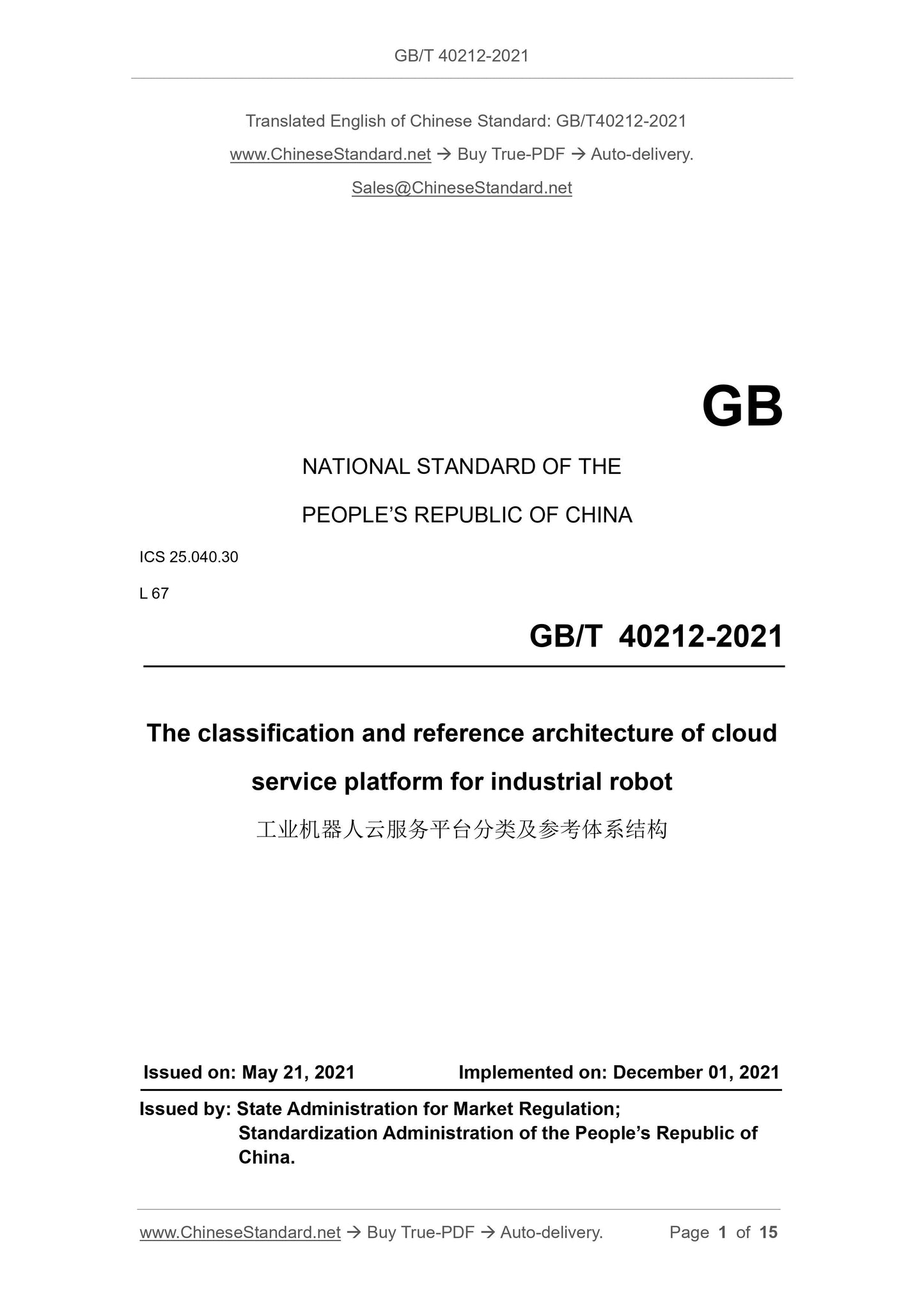
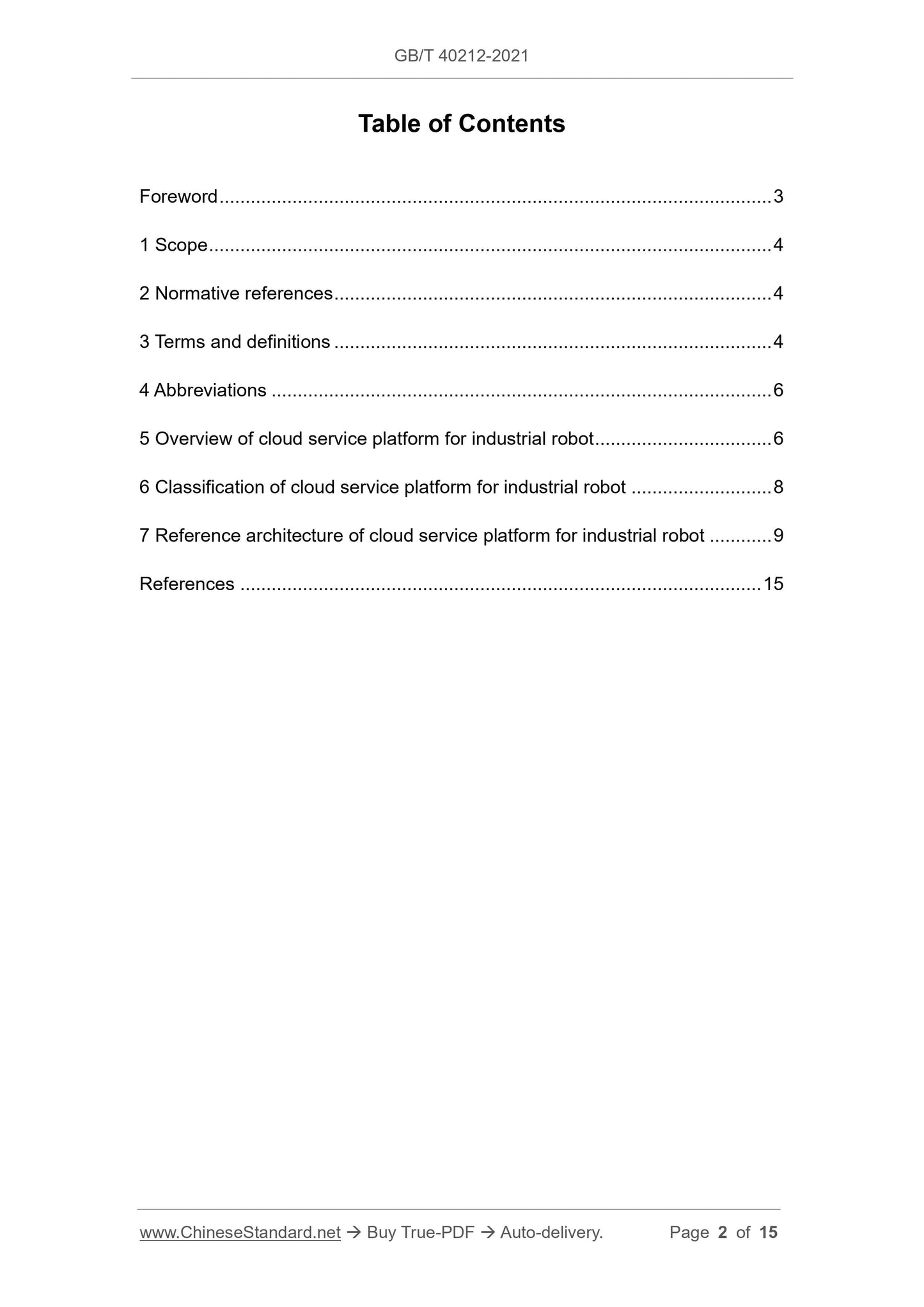
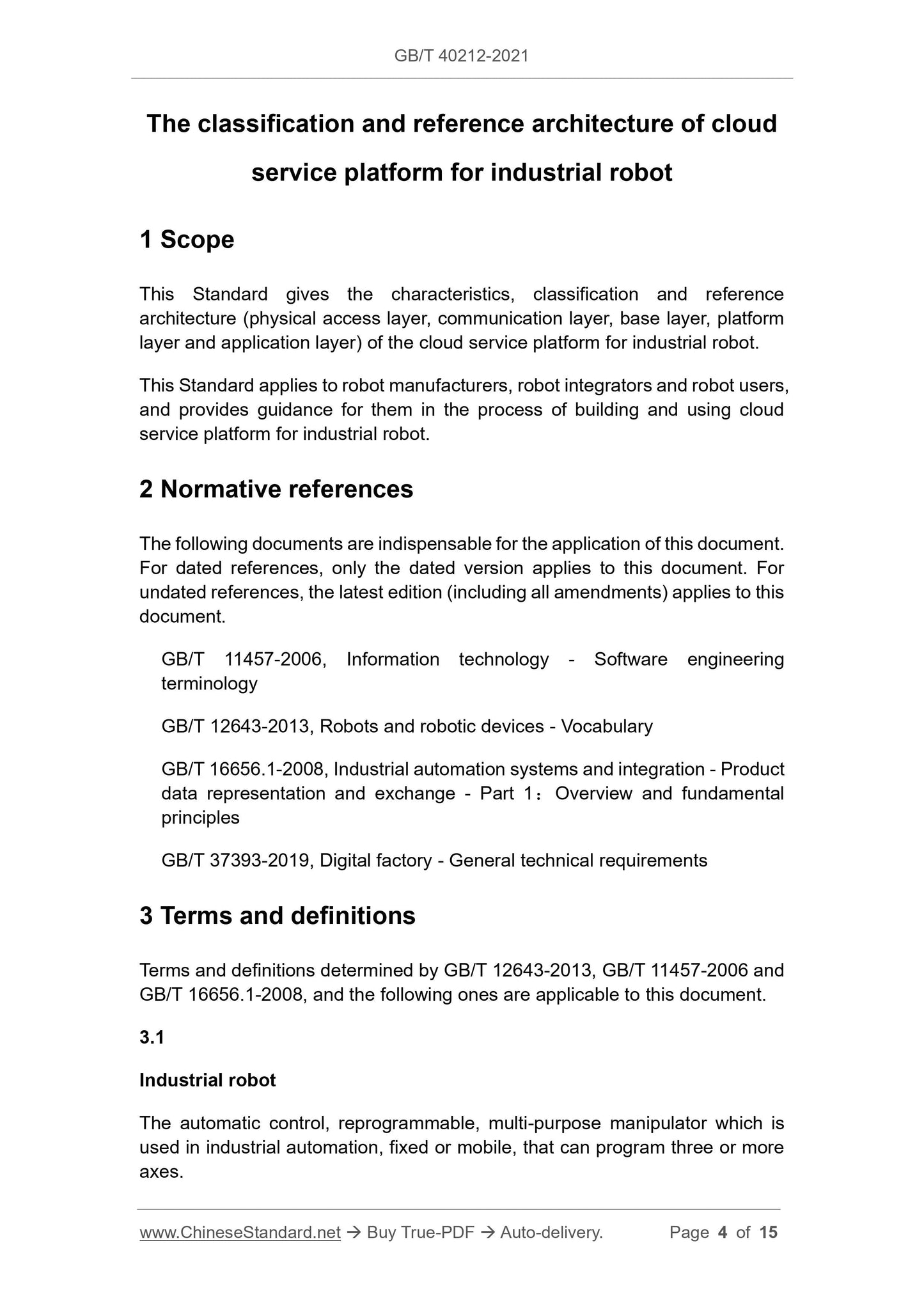
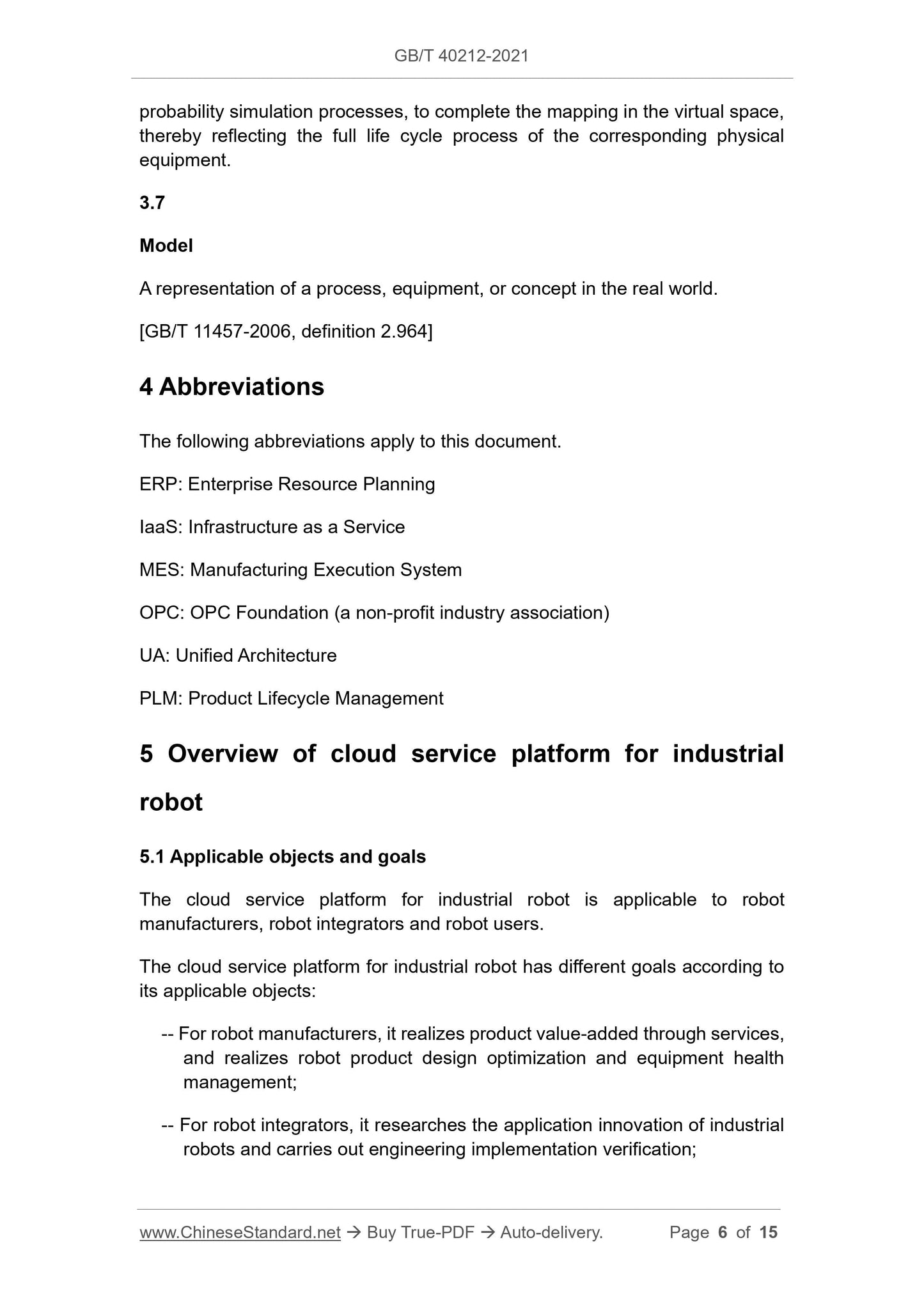
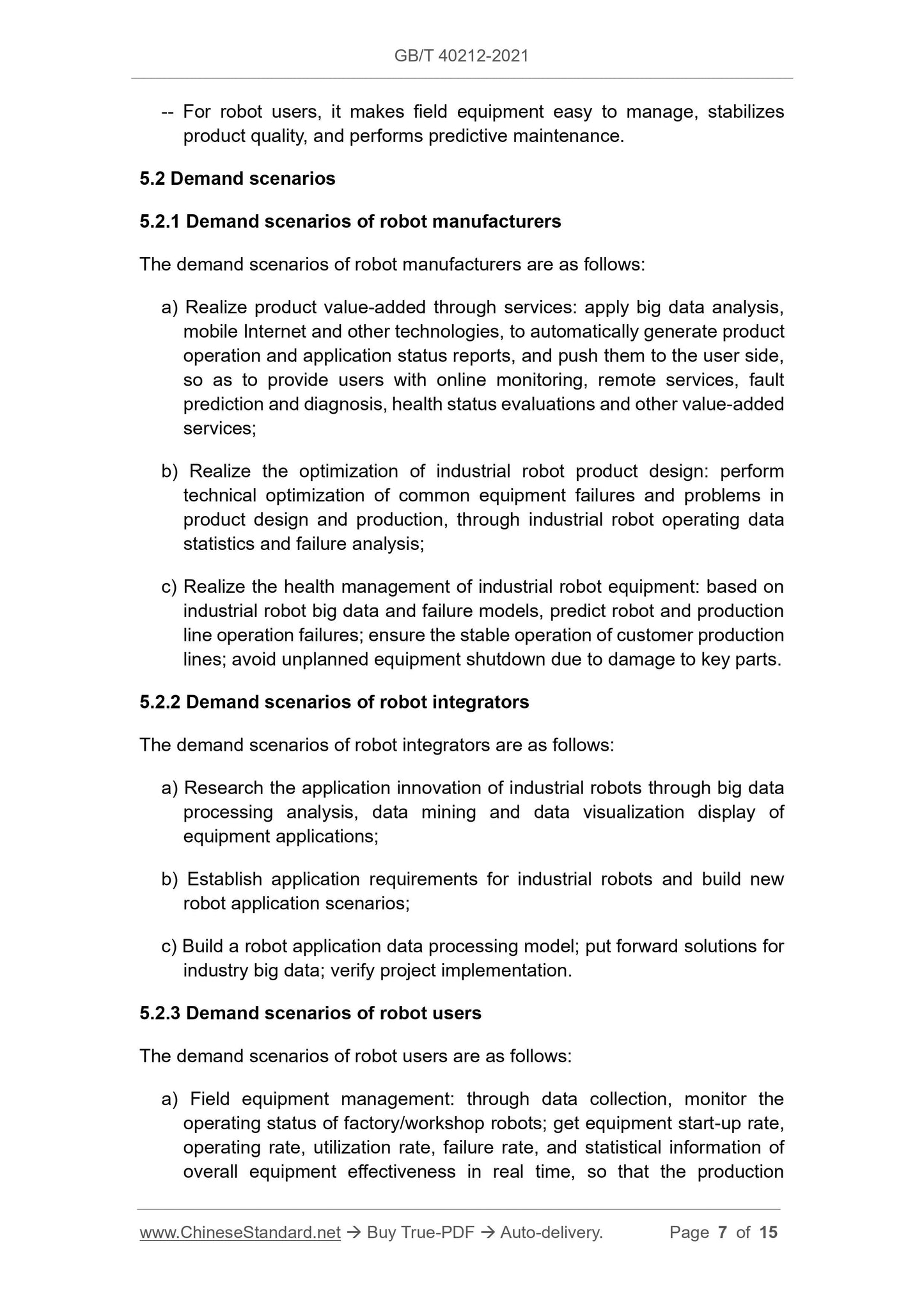
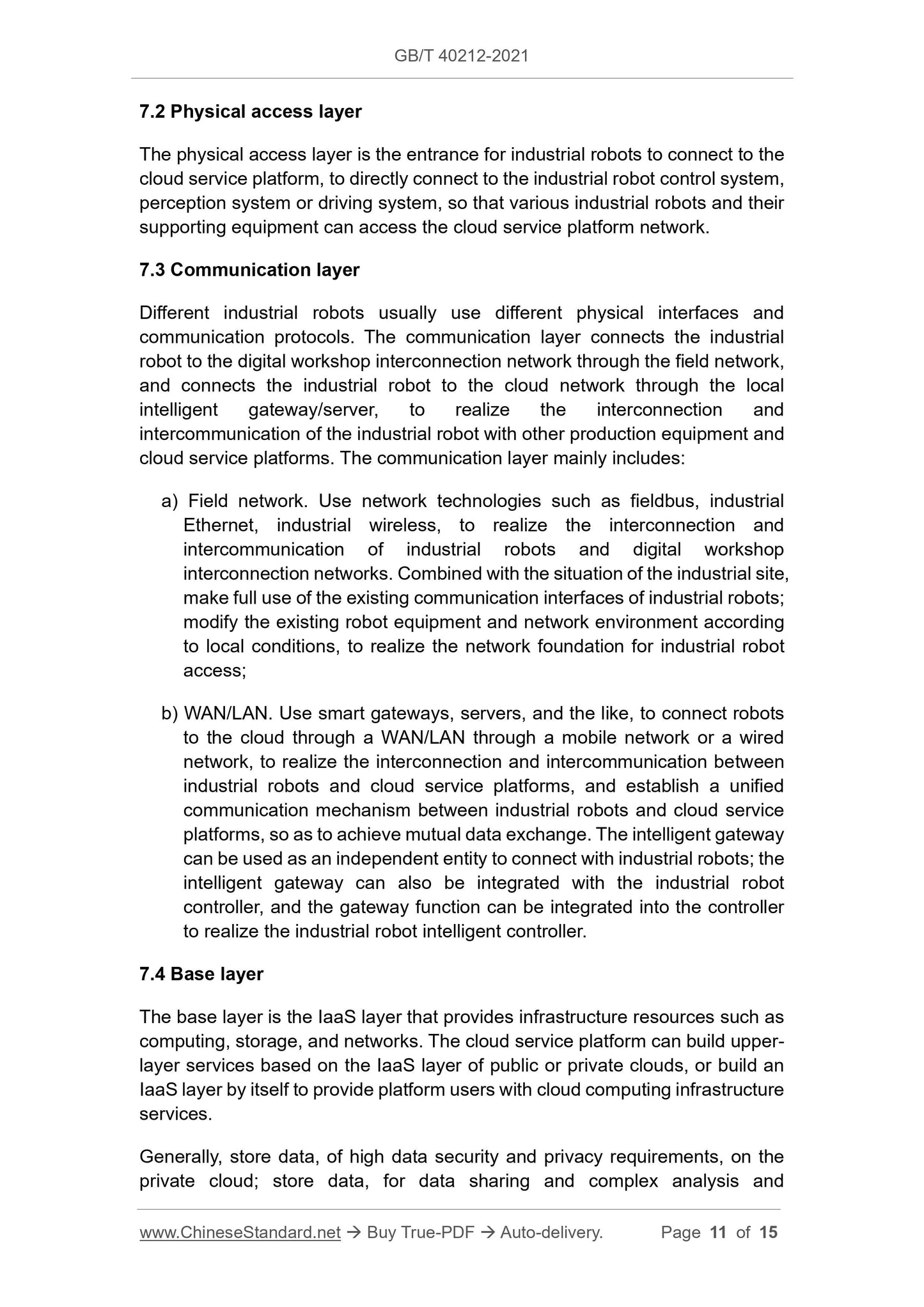
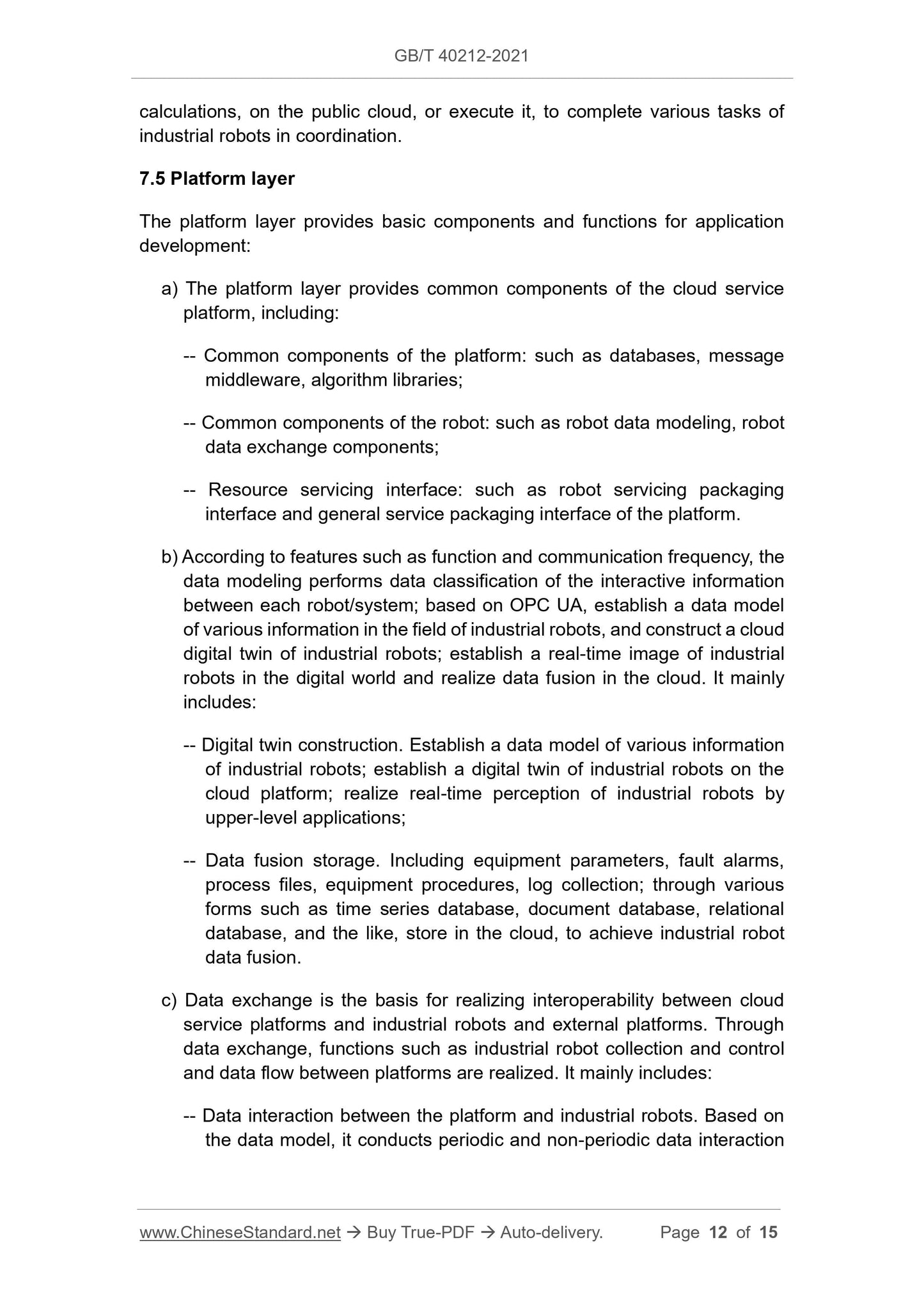
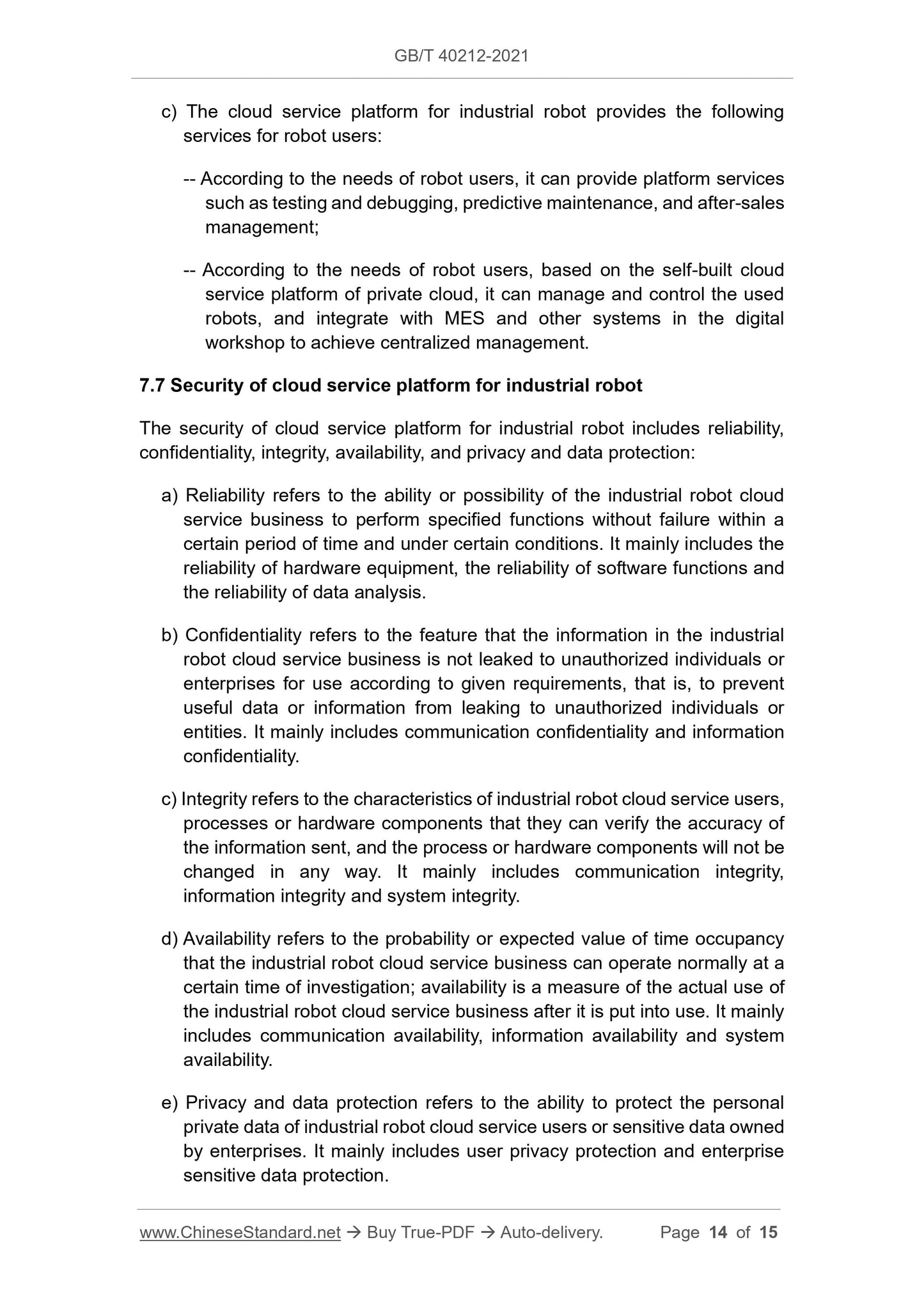