1
/
of
9
PayPal, credit cards. Download editable-PDF and invoice in 1 second!
GB/T 41663-2022 English PDF (GBT41663-2022)
GB/T 41663-2022 English PDF (GBT41663-2022)
Regular price
$380.00 USD
Regular price
Sale price
$380.00 USD
Unit price
/
per
Shipping calculated at checkout.
Couldn't load pickup availability
Delivery: 3 seconds. Download true-PDF + Invoice.
Get QUOTATION in 1-minute: Click GB/T 41663-2022
Historical versions: GB/T 41663-2022
Preview True-PDF (Reload/Scroll if blank)
GB/T 41663-2022: Road vehicles - Brake lining friction materials - Scale inertia dynamometer test method
GB/T 41663-2022
NATIONAL STANDARD OF THE
PEOPLE’S REPUBLIC OF CHINA
ICS 43.040.40
CCS Q 69
Road Vehicles - Brake Lining Friction Materials - Scale
Inertia Dynamometer Test Method
ISSUED ON: JULY 11, 2022
IMPLEMENTED ON: FEBRUARY 1, 2023
Issued by: State Administration for Market Regulation;
Standardization Administration of the People’s Republic of China.
Table of Contents
Foreword ... 3
Introduction ... 4
1 Scope ... 6
2 Normative References ... 6
3 Terms and Definitions ... 6
4 Symbols and Abbreviations ... 11
5 Test Conditions and Preparations ... 13
6 Test Items and Procedures ... 15
7 Test Report ... 19
Appendix A (informative) Technical Parameters of Scale Inertia Test Bench ... 21
Appendix B (informative) Technical Conditions of Cooling Air (environmental control
system) of Scale Test ... 24
Appendix C (informative) Temperature Measurement Method of Scale Test ... 28
Appendix D (informative) Wear Measurement of Brake Lining and Brake Disc ... 29
Appendix E (informative) Technical Conditions of Scale Brake Disc ... 32
Appendix F (informative) Outline of Scale Test ... 34
Appendix G (informative) Examples of Test Report Format ... 36
Bibliography ... 38
Road Vehicles - Brake Lining Friction Materials - Scale
Inertia Dynamometer Test Method
1 Scope
This document specifies the test conditions and preparation, specimen items and procedures,
and test reports of the scale inertia dynamometer test method for the brake lining friction
materials of road vehicles.
This document is applicable to the scale inertia dynamometer test of disc brake linings of
passenger cars. On the basis of familiarity with the principle of scale reduction, this document
may also be taken as a reference for the brake lining test of other types of vehicles. This
document is applicable to raw material screening and inspection, early development of friction
materials, quality control of production processes and test of foreign samples.
2 Normative References
This document does not have normative references.
3 Terms and Definitions
The following terms and definitions are applicable to this document.
3.1 Scale Ratio
3.1.1 Scale ratio of effective friction radius
SRf
The ratio of the effective friction radius of the full-scale brake disc to the effective friction
radius of the scale brake disc, which shall be calculated in accordance with Formula (1).
Where,
Rf---the effective friction radius of the full-scale brake disc, expressed in (m);
RfS---the effective friction radius of the scale brake disc, expressed in (m).
3.1.2 Scale ratio of brake lining area
ve---10% of the initial brake speed (v0), expressed in (km/h);
v0---the initial brake speed, expressed in (km/h);
25.92---the coefficient of unit conversion;
Se---the brake distance when the speed is 10% v0, expressed in (m);
Sb---the brake distance when the speed is 80% v0, expressed in (m).
NOTE: under the condition of deceleration braking, the calculation range of the mean fully
developed deceleration is related to the release speed.
[source: GB/T 29064-2012, 3.4]
3.4 Braking Modes
3.4.1 Brake loading mode
3.4.1.1 Constant input (line pressure) application mode
During the braking process, the line pressure remains unchanged at the set value.
3.4.1.2 Constant output (brake torque) application mode
During the braking process, the output brake torque remains at the set value, which is equivalent
to constant deceleration braking.
3.4.2 Brake release mode
3.4.2.1 Brake stop
A braking mode that decreases the test speed to less than 0.5 km/h or even lower.
NOTE: under the condition of constant output, perform a brake stop; the release speed may be set
to 1 km/h ~ 2 km/h.
3.4.2.2 Brake snub
A braking mode that decreases the test speed to not lower than 5 km/h.
4 Symbols and Abbreviations
The following symbls and abbreviations are applicable to this document (see Table 1).
During the scale test, the temprature and relative humidity of the cooling air shall be adjusted
and controlled; during each braking process, the average temperature, relative humidity and
cooling air speed shall be measured and recorded.
The technical parameters of the environmental control system are shown in Appendix B.
NOTE: generally speaking, the control range of the cooling air is: 20 C ~ 25 C, and the relative
humidity is: 60% ~ 65%.
5.1.7 Rotation speed between two brakes
During the cooling period between two brakes, the rotation speed of the test bench is 10 km/h;
for the recession test, the waiting speed is the initial speed of the next brake.
5.1.8 Initial brake temperature
The initial brake temperature refers to the real-time temprature of the brake disc at the start of
brake.
5.1.9 Test temperature measurement
In the center of the thickness of the brake disc, drill a 3.0 mm hole. Embed the K-type
thermocouple at the position of the effective friction radius, see Appendix C.
5.1.10 Sensor calibration
Every year, a third-party measurement institution performs the calibration of sensors measuring
rotation speed, temprature, pressure, torque, cooling air speed and humidity, and issues a
calibration certificate. Usually, users can self-check and record the measurement system in
accordance with the test condition.
5.1.11 Sample measurement
Before and after the test, measure the thickness and mass of the test sample and brake disc;
calculate the thickness wear and mass wear during the test. See Appendix D for the measurment
locations.
5.1.12 Data collection
During the test with the scale inertia test bench, the following data shall be automatically
collected in real time:
---brake time;
---rotation speed of main shaft;
---brake line pressure;
---brake torque;
---brake disc temperature;
---cooling air tempreature;
---cooling air speed;
---relative humidity of cooling air;
---test procedures and number of brakes.
5.1.13 Technical requirements for scale brake disc
The brake disc of the scale test uses the same material as the brake disc of passenger cars. The
technical conditions for the brake disc are shown in Appendix E.
In principle, a new brake disc shall be used for each test. If the brake disc needs to be repeatedly
used, each side of the brake disc needs to be ground by 100 m; brake discs with a thickness of
less than 8.5 mm shall not be used again.
5.1.14 Axial runout of scale brake disc working surface
After the scale brake disc is installed, the initial axial runout (LRO) of the working surface shall
not exceed 20 m, and the measurement location is 5 mm away from the edge of the outer side
of the brake disc. Before and after each test, measure and record the axial runout of the working
surface of the brake disc.
5.2 Specimen Preparation
The specimens shall be prepared in accordance with the following requirements:
---the specimens shall be cut from the product (including metal backing);
---specimen size: width: 25െ0.10െ0.25 mm, length: 40െ0.10െ0.25 mm, thickness: 18 mm (not lower
than 8.5 mm);
---the surface of the specimens: maintain the original state of the product (including
coating and ablation, etc.) and avoid contamination;
---the measurement of specimens and brake dics before the test: see Appendix D; the
measurement is accurate to three decimal places;
---before the test, the specimens and the working surface of the brake discs shall be
respectively photograph...
Get QUOTATION in 1-minute: Click GB/T 41663-2022
Historical versions: GB/T 41663-2022
Preview True-PDF (Reload/Scroll if blank)
GB/T 41663-2022: Road vehicles - Brake lining friction materials - Scale inertia dynamometer test method
GB/T 41663-2022
NATIONAL STANDARD OF THE
PEOPLE’S REPUBLIC OF CHINA
ICS 43.040.40
CCS Q 69
Road Vehicles - Brake Lining Friction Materials - Scale
Inertia Dynamometer Test Method
ISSUED ON: JULY 11, 2022
IMPLEMENTED ON: FEBRUARY 1, 2023
Issued by: State Administration for Market Regulation;
Standardization Administration of the People’s Republic of China.
Table of Contents
Foreword ... 3
Introduction ... 4
1 Scope ... 6
2 Normative References ... 6
3 Terms and Definitions ... 6
4 Symbols and Abbreviations ... 11
5 Test Conditions and Preparations ... 13
6 Test Items and Procedures ... 15
7 Test Report ... 19
Appendix A (informative) Technical Parameters of Scale Inertia Test Bench ... 21
Appendix B (informative) Technical Conditions of Cooling Air (environmental control
system) of Scale Test ... 24
Appendix C (informative) Temperature Measurement Method of Scale Test ... 28
Appendix D (informative) Wear Measurement of Brake Lining and Brake Disc ... 29
Appendix E (informative) Technical Conditions of Scale Brake Disc ... 32
Appendix F (informative) Outline of Scale Test ... 34
Appendix G (informative) Examples of Test Report Format ... 36
Bibliography ... 38
Road Vehicles - Brake Lining Friction Materials - Scale
Inertia Dynamometer Test Method
1 Scope
This document specifies the test conditions and preparation, specimen items and procedures,
and test reports of the scale inertia dynamometer test method for the brake lining friction
materials of road vehicles.
This document is applicable to the scale inertia dynamometer test of disc brake linings of
passenger cars. On the basis of familiarity with the principle of scale reduction, this document
may also be taken as a reference for the brake lining test of other types of vehicles. This
document is applicable to raw material screening and inspection, early development of friction
materials, quality control of production processes and test of foreign samples.
2 Normative References
This document does not have normative references.
3 Terms and Definitions
The following terms and definitions are applicable to this document.
3.1 Scale Ratio
3.1.1 Scale ratio of effective friction radius
SRf
The ratio of the effective friction radius of the full-scale brake disc to the effective friction
radius of the scale brake disc, which shall be calculated in accordance with Formula (1).
Where,
Rf---the effective friction radius of the full-scale brake disc, expressed in (m);
RfS---the effective friction radius of the scale brake disc, expressed in (m).
3.1.2 Scale ratio of brake lining area
ve---10% of the initial brake speed (v0), expressed in (km/h);
v0---the initial brake speed, expressed in (km/h);
25.92---the coefficient of unit conversion;
Se---the brake distance when the speed is 10% v0, expressed in (m);
Sb---the brake distance when the speed is 80% v0, expressed in (m).
NOTE: under the condition of deceleration braking, the calculation range of the mean fully
developed deceleration is related to the release speed.
[source: GB/T 29064-2012, 3.4]
3.4 Braking Modes
3.4.1 Brake loading mode
3.4.1.1 Constant input (line pressure) application mode
During the braking process, the line pressure remains unchanged at the set value.
3.4.1.2 Constant output (brake torque) application mode
During the braking process, the output brake torque remains at the set value, which is equivalent
to constant deceleration braking.
3.4.2 Brake release mode
3.4.2.1 Brake stop
A braking mode that decreases the test speed to less than 0.5 km/h or even lower.
NOTE: under the condition of constant output, perform a brake stop; the release speed may be set
to 1 km/h ~ 2 km/h.
3.4.2.2 Brake snub
A braking mode that decreases the test speed to not lower than 5 km/h.
4 Symbols and Abbreviations
The following symbls and abbreviations are applicable to this document (see Table 1).
During the scale test, the temprature and relative humidity of the cooling air shall be adjusted
and controlled; during each braking process, the average temperature, relative humidity and
cooling air speed shall be measured and recorded.
The technical parameters of the environmental control system are shown in Appendix B.
NOTE: generally speaking, the control range of the cooling air is: 20 C ~ 25 C, and the relative
humidity is: 60% ~ 65%.
5.1.7 Rotation speed between two brakes
During the cooling period between two brakes, the rotation speed of the test bench is 10 km/h;
for the recession test, the waiting speed is the initial speed of the next brake.
5.1.8 Initial brake temperature
The initial brake temperature refers to the real-time temprature of the brake disc at the start of
brake.
5.1.9 Test temperature measurement
In the center of the thickness of the brake disc, drill a 3.0 mm hole. Embed the K-type
thermocouple at the position of the effective friction radius, see Appendix C.
5.1.10 Sensor calibration
Every year, a third-party measurement institution performs the calibration of sensors measuring
rotation speed, temprature, pressure, torque, cooling air speed and humidity, and issues a
calibration certificate. Usually, users can self-check and record the measurement system in
accordance with the test condition.
5.1.11 Sample measurement
Before and after the test, measure the thickness and mass of the test sample and brake disc;
calculate the thickness wear and mass wear during the test. See Appendix D for the measurment
locations.
5.1.12 Data collection
During the test with the scale inertia test bench, the following data shall be automatically
collected in real time:
---brake time;
---rotation speed of main shaft;
---brake line pressure;
---brake torque;
---brake disc temperature;
---cooling air tempreature;
---cooling air speed;
---relative humidity of cooling air;
---test procedures and number of brakes.
5.1.13 Technical requirements for scale brake disc
The brake disc of the scale test uses the same material as the brake disc of passenger cars. The
technical conditions for the brake disc are shown in Appendix E.
In principle, a new brake disc shall be used for each test. If the brake disc needs to be repeatedly
used, each side of the brake disc needs to be ground by 100 m; brake discs with a thickness of
less than 8.5 mm shall not be used again.
5.1.14 Axial runout of scale brake disc working surface
After the scale brake disc is installed, the initial axial runout (LRO) of the working surface shall
not exceed 20 m, and the measurement location is 5 mm away from the edge of the outer side
of the brake disc. Before and after each test, measure and record the axial runout of the working
surface of the brake disc.
5.2 Specimen Preparation
The specimens shall be prepared in accordance with the following requirements:
---the specimens shall be cut from the product (including metal backing);
---specimen size: width: 25െ0.10െ0.25 mm, length: 40െ0.10െ0.25 mm, thickness: 18 mm (not lower
than 8.5 mm);
---the surface of the specimens: maintain the original state of the product (including
coating and ablation, etc.) and avoid contamination;
---the measurement of specimens and brake dics before the test: see Appendix D; the
measurement is accurate to three decimal places;
---before the test, the specimens and the working surface of the brake discs shall be
respectively photograph...
Share
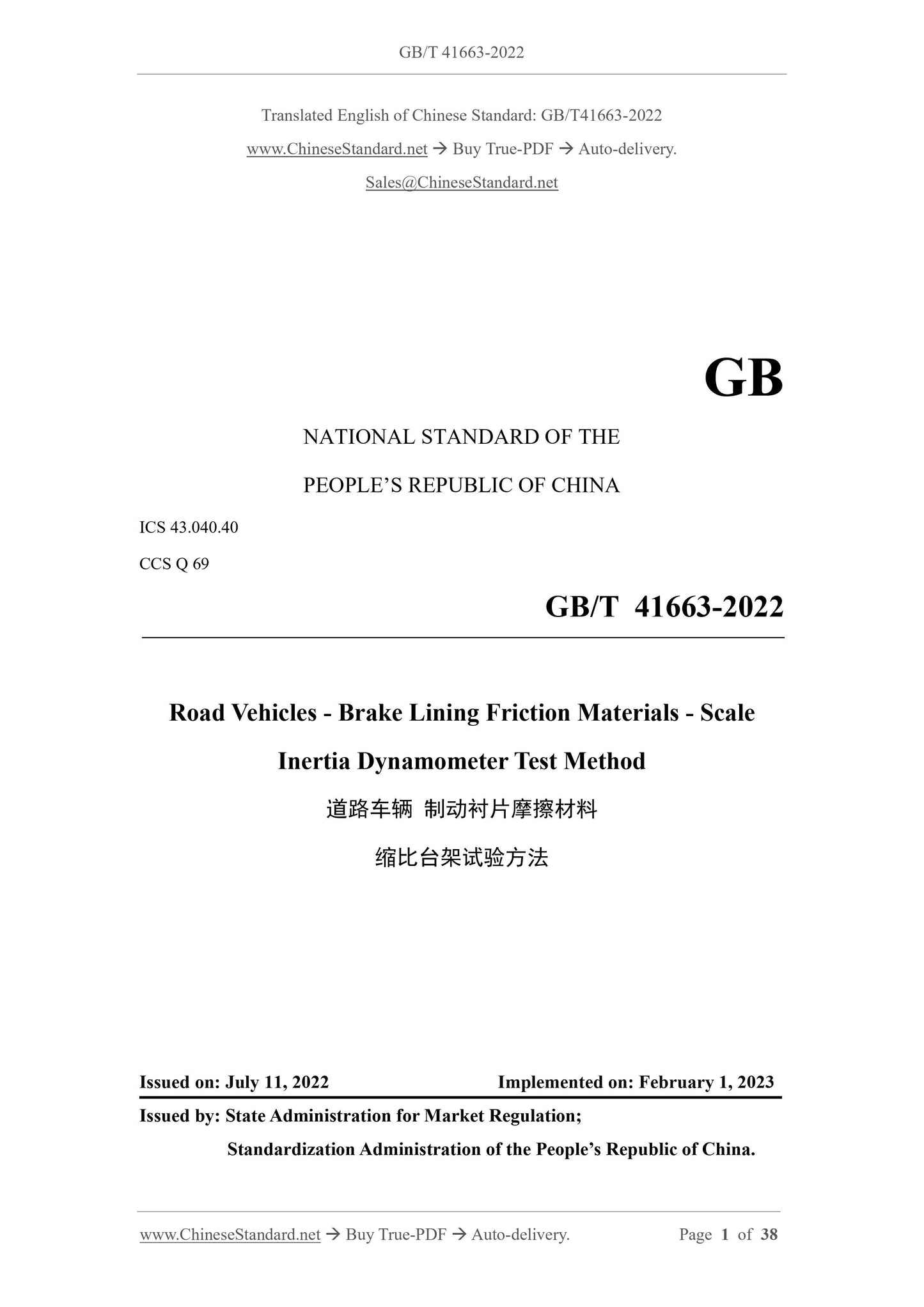
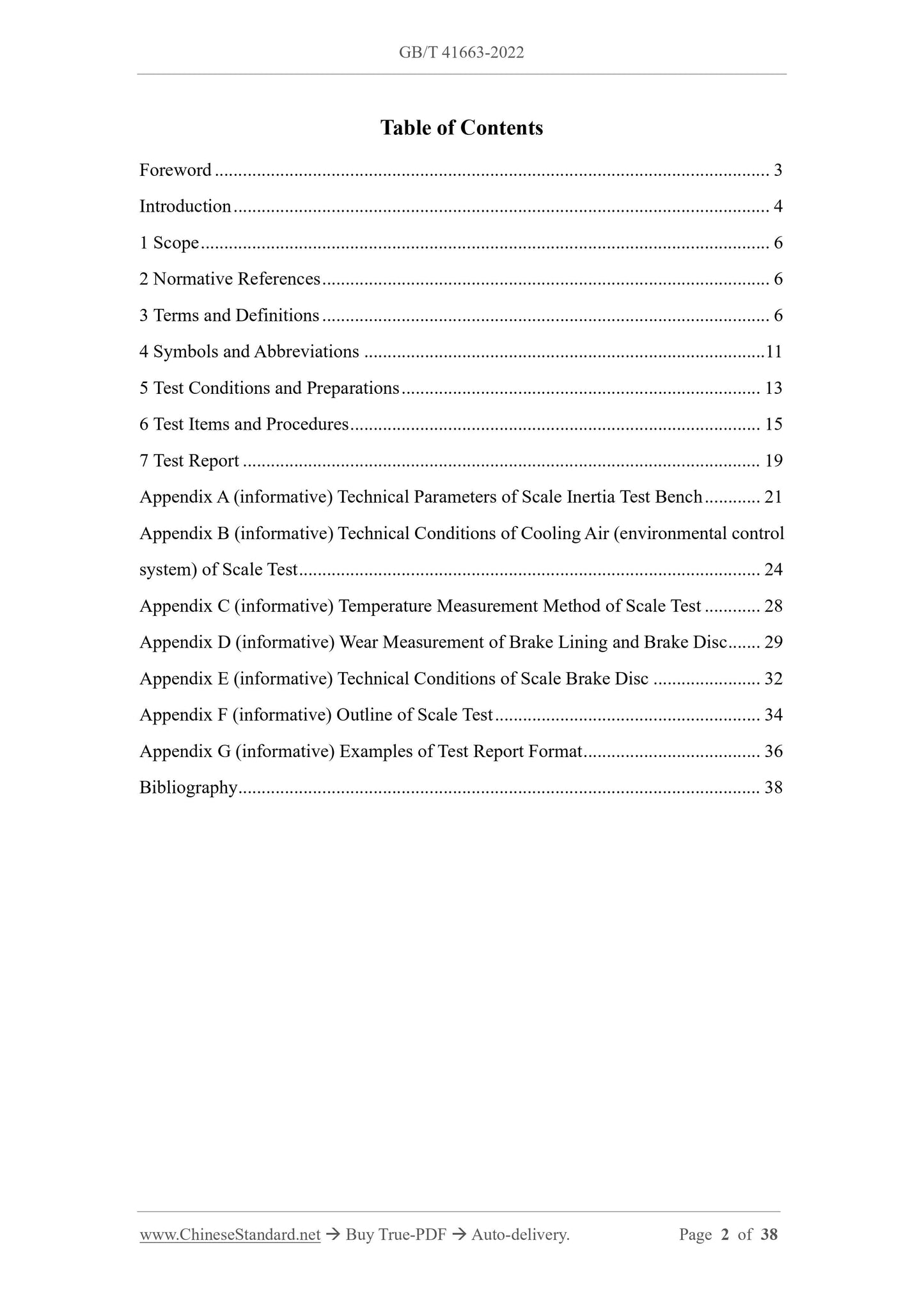
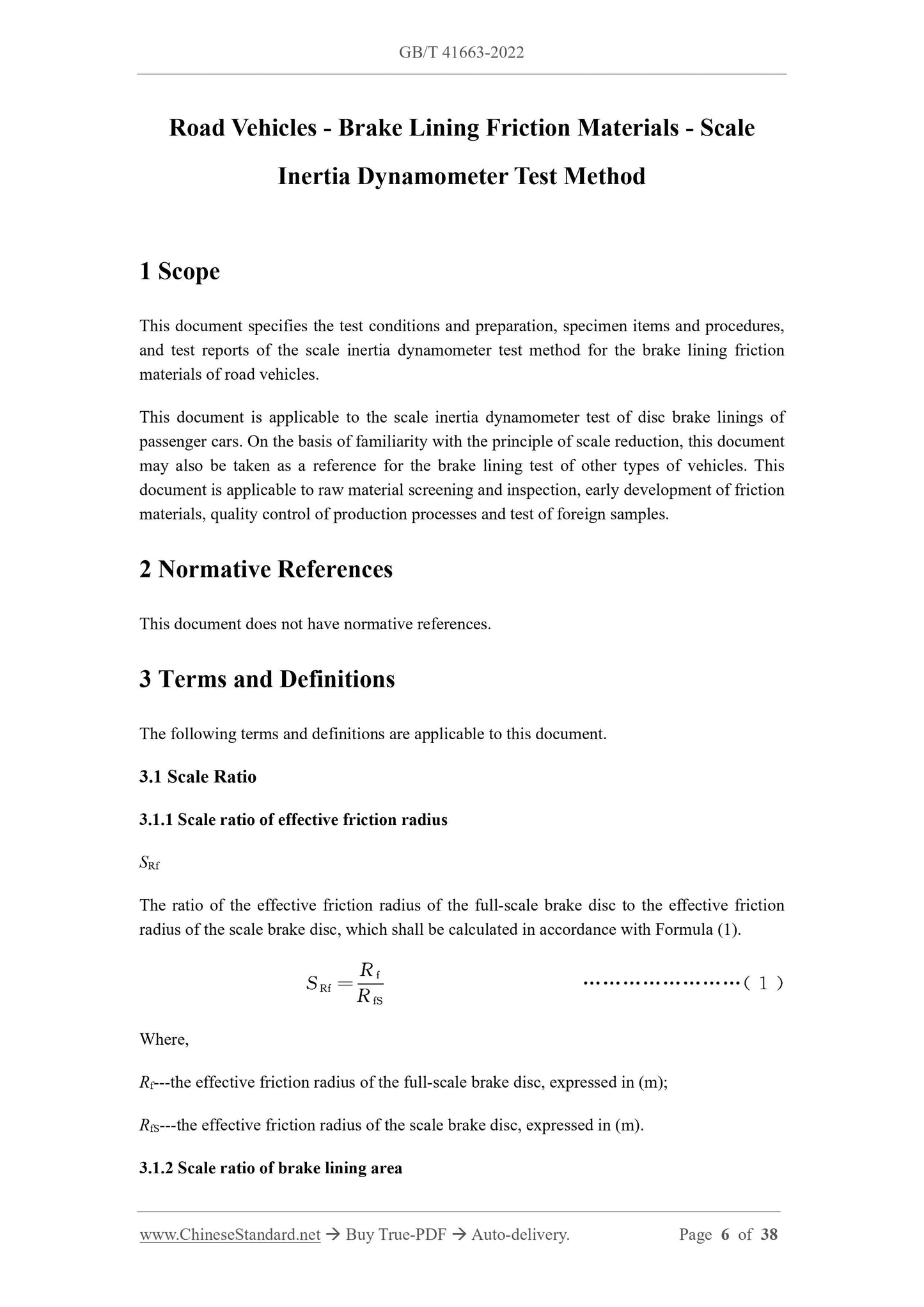
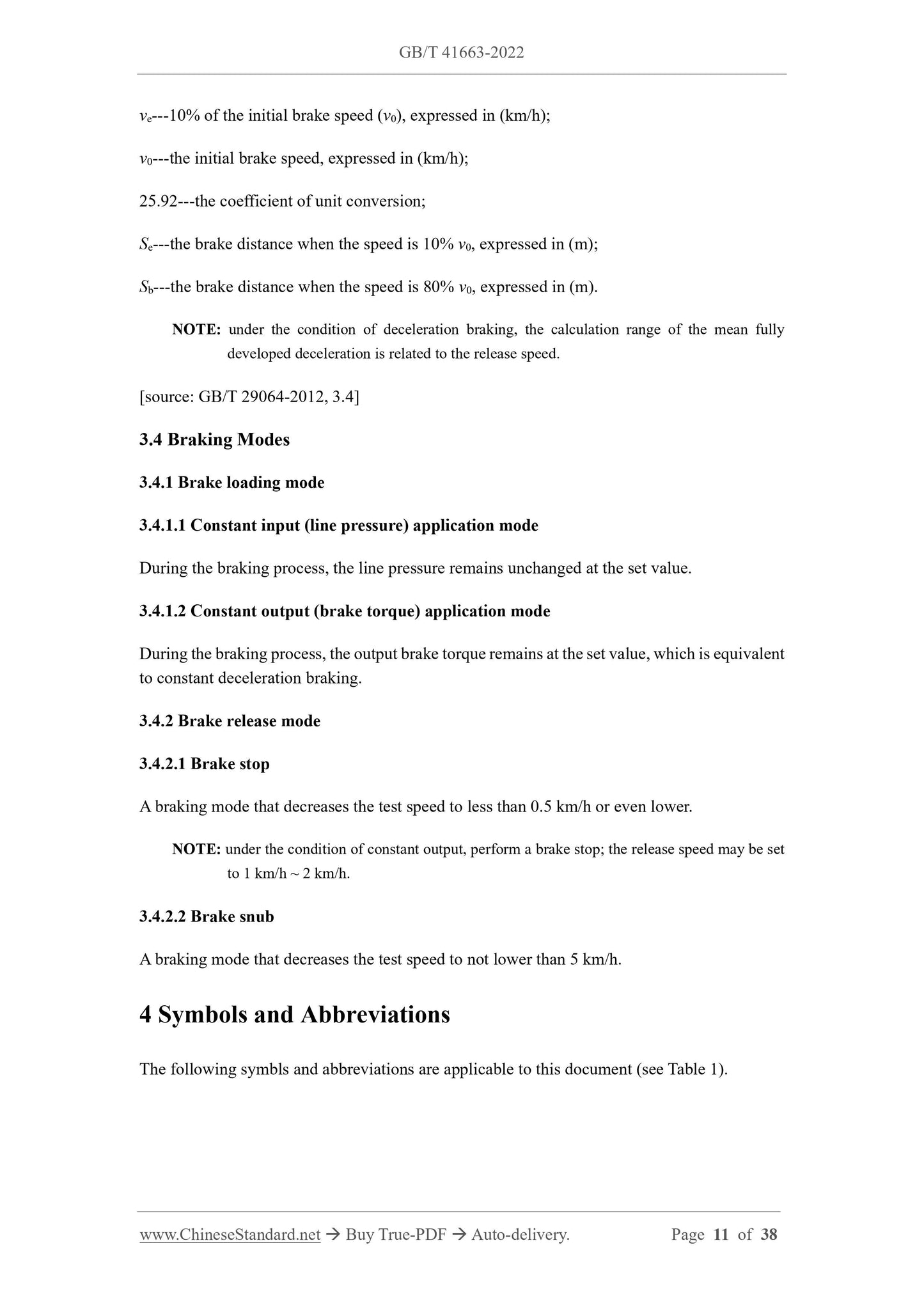
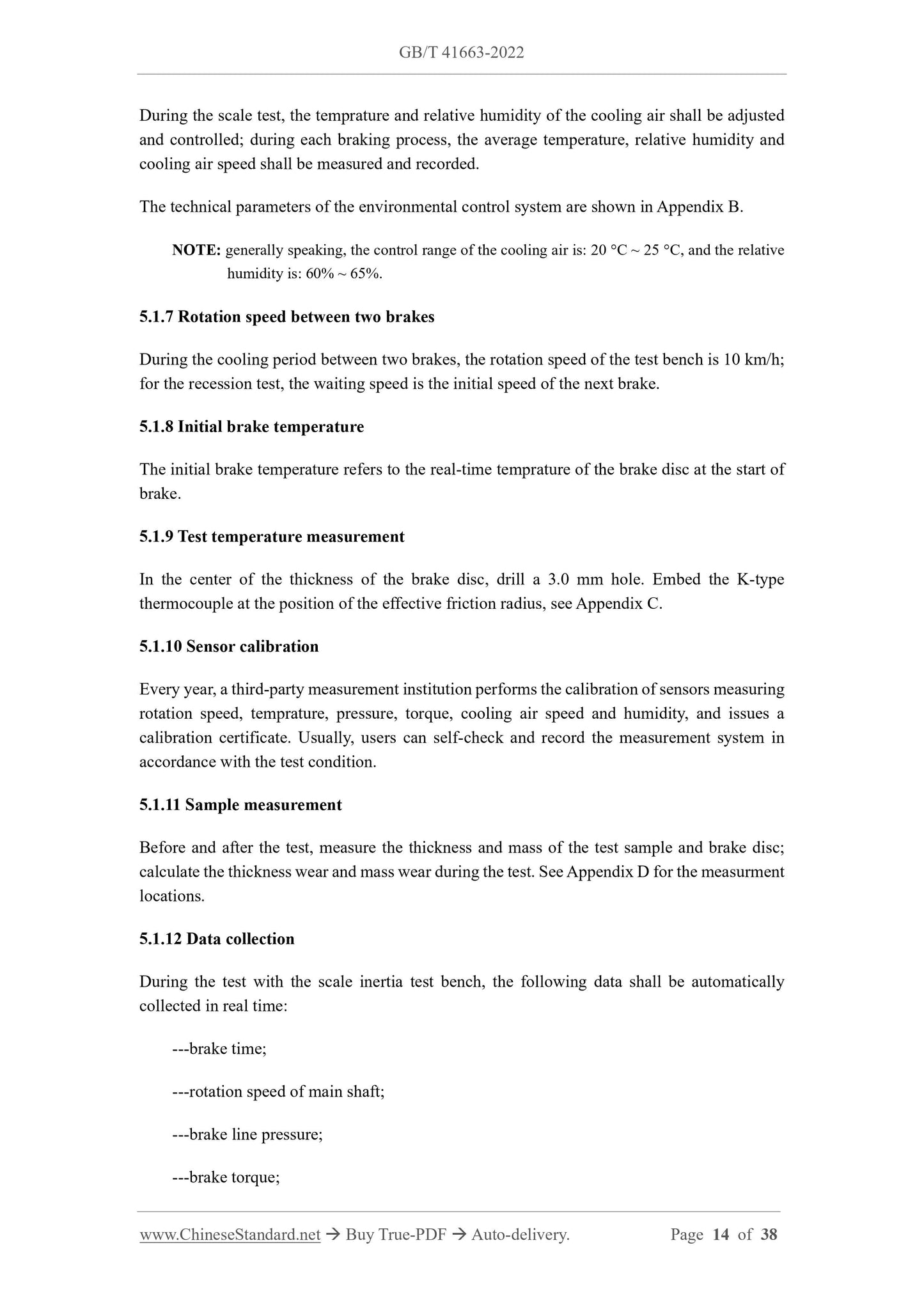
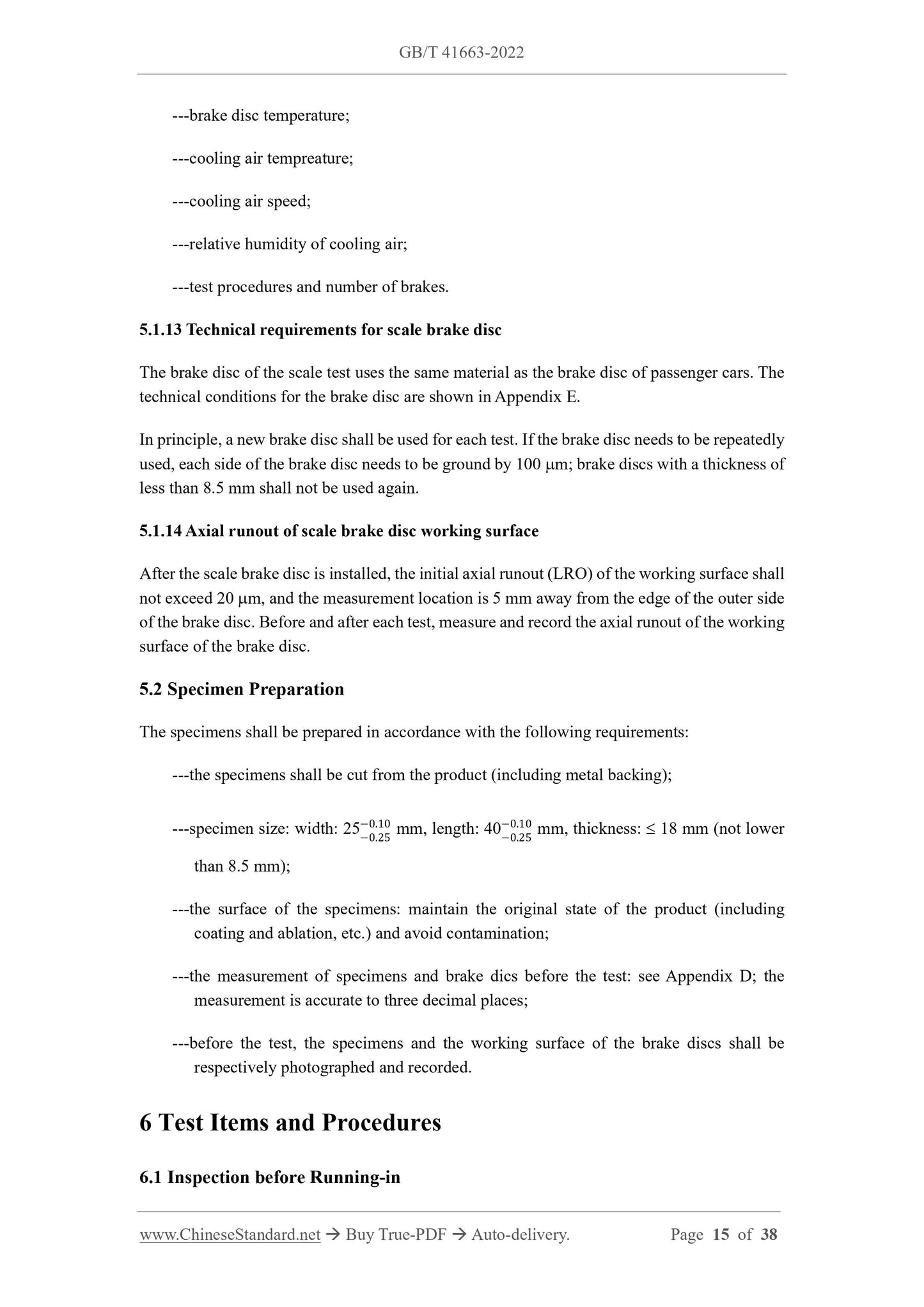
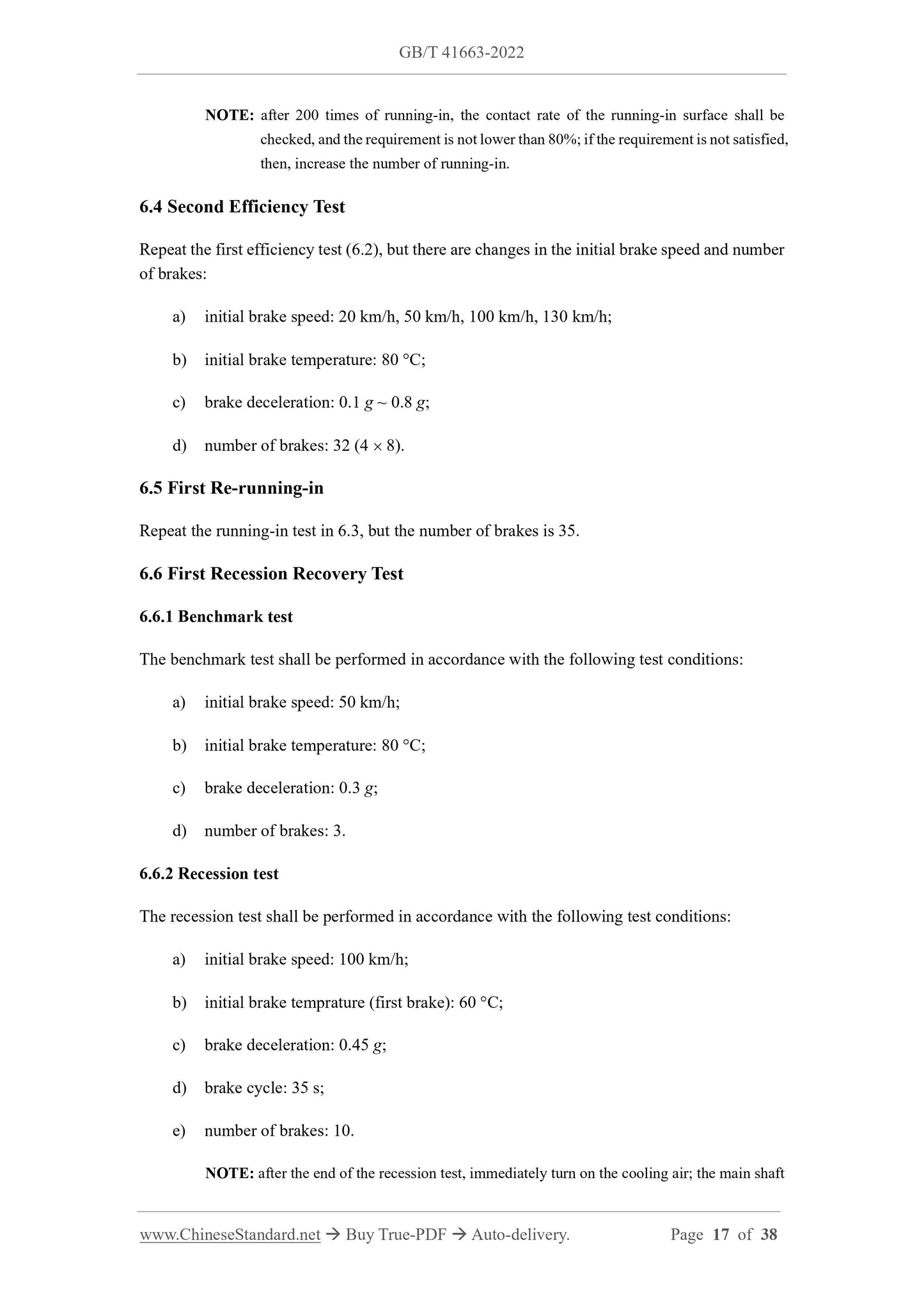
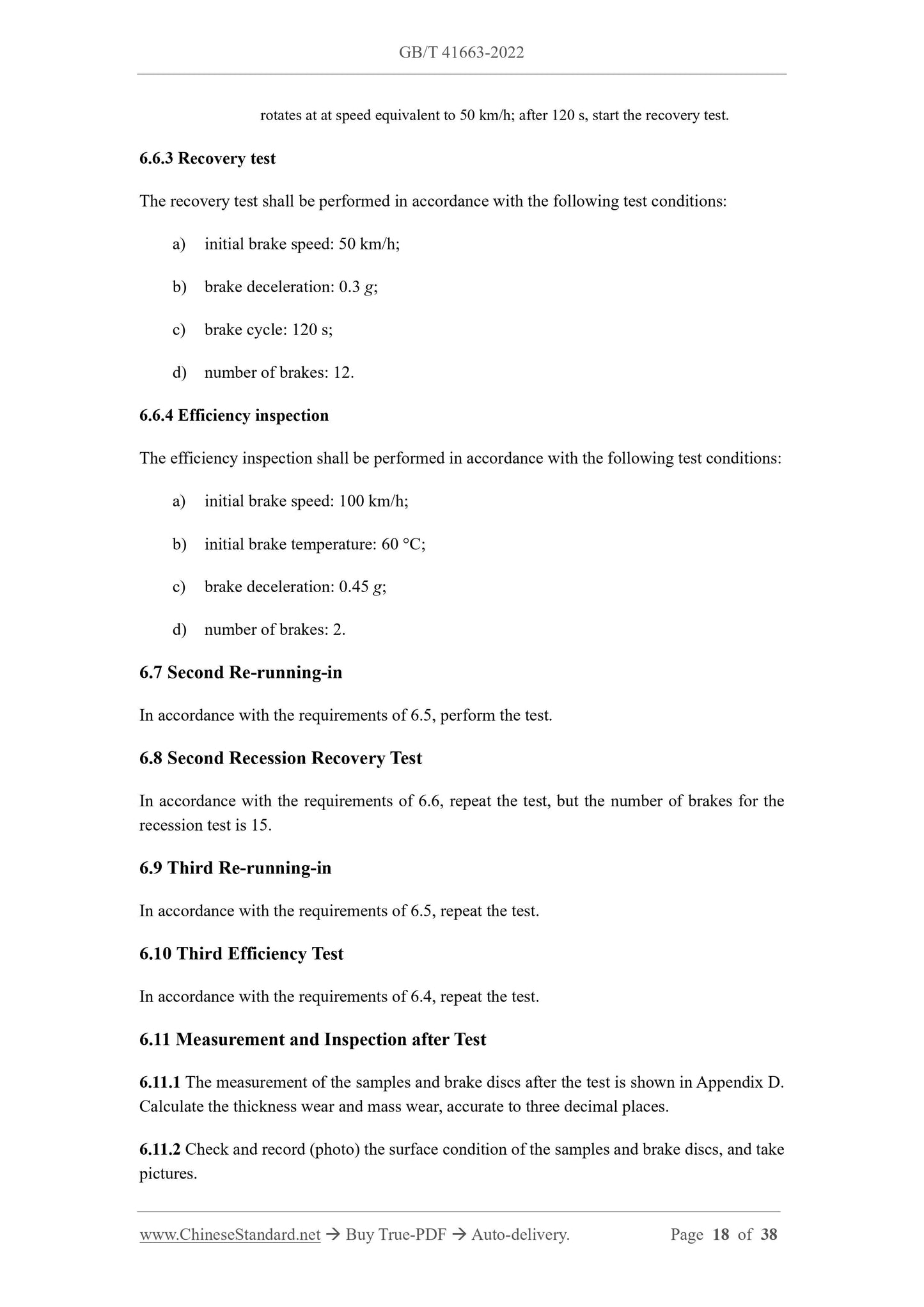
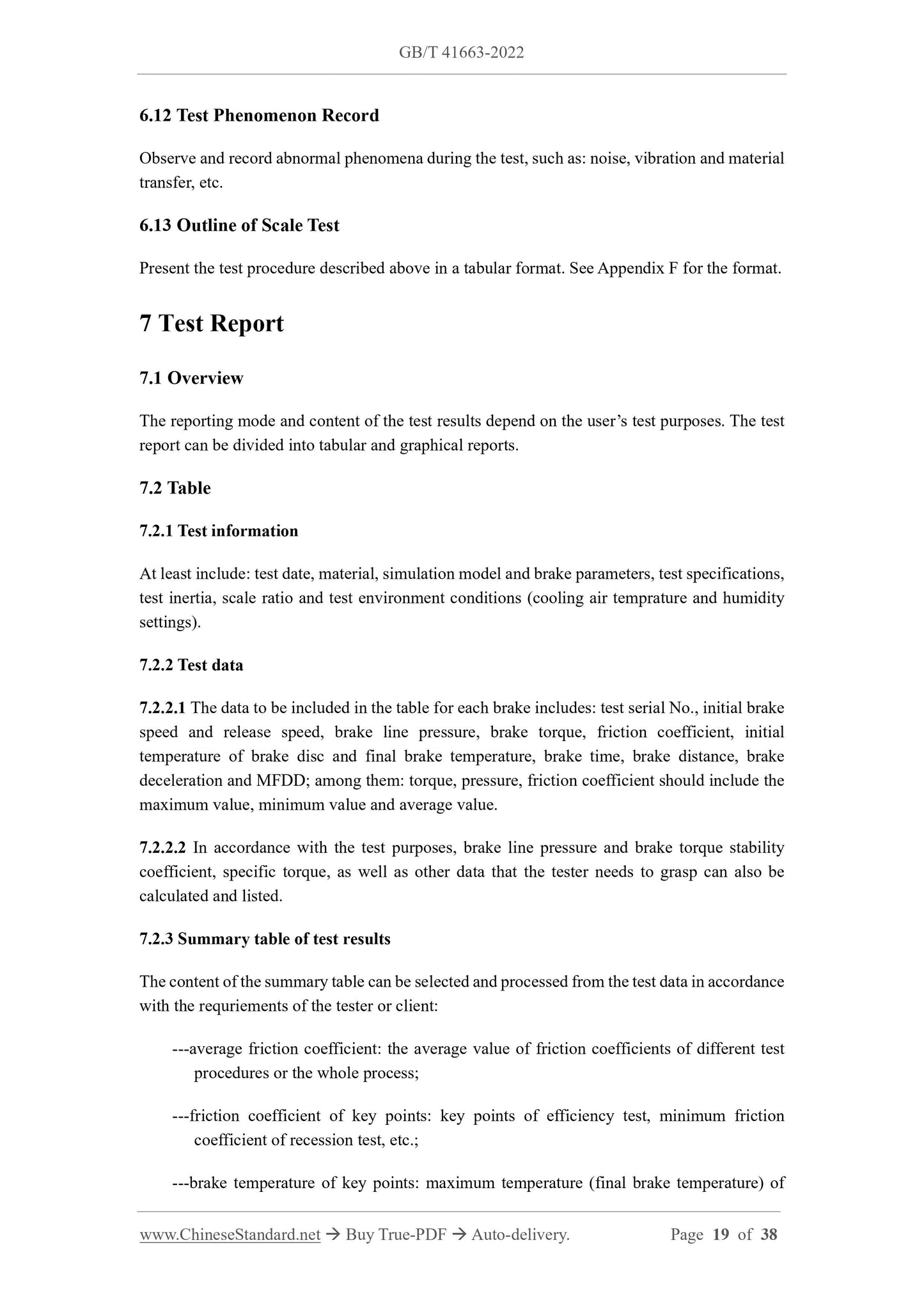