1
/
of
11
www.ChineseStandard.us -- Field Test Asia Pte. Ltd.
JB/T 7016-2017 English PDF (JB/T7016-2017)
JB/T 7016-2017 English PDF (JB/T7016-2017)
Regular price
$305.00
Regular price
Sale price
$305.00
Unit price
/
per
Shipping calculated at checkout.
Couldn't load pickup availability
JB/T 7016-2017: Storage/retrieval machine
Delivery: 9 seconds. Download (& Email) true-PDF + Invoice.
Get Quotation: Click JB/T 7016-2017 (Self-service in 1-minute)
Historical versions (Master-website): JB/T 7016-2017
Preview True-PDF (Reload/Scroll-down if blank)
JB/T 7016-2017
JB
MACHINERY INDUSTRY STANDARD
OF THE PEOPLE’S REPUBLIC OF CHINA
ICS 53.080
J 83
Record No.: 57881-2017
Replacing JB/T 2960-1999, JB/T 7016-1993
Storage/Retrieval Machine
ISSUED ON: JANUARY 09, 2017
IMPLEMENTED ON: JULY 01, 2017
Issued by: Ministry of Industry and Information Technology of the People’s
Republic of China
Table of Contents
Foreword ... 4
1 Scope ... 5
2 Normative References ... 5
3 Terms and Definitions ... 7
4 Basic Parameters ... 8
5 Basic Compositions ... 8
5.1 Lower beam ... 8
5.2 Upright column ... 9
5.3 Upper beam ... 9
5.4 Pallet ... 9
5.5 Operating mechanism ... 9
5.6 Lifting mechanism ... 9
5.7 Load handling device ... 10
5.8 Rail ... 10
5.9 Control system ... 10
5.10 Others ... 10
6 Technical Requirements ... 10
6.1 General requirements ... 10
6.2 Manufacturing and installation requirements ... 12
6.3 Performance requirements ... 22
7 Test Methods ... 24
7.1 Preparation before the test ... 24
7.2 Test instrument and test load ... 24
7.3 Working performance test of fork ... 25
7.4 Operating performance test... 25
7.5 Lifting performance test of pallet ... 26
7.6 Static load test ... 26
7.7 Dynamic load test ... 26
7.8 Static stiffness test ... 27
7.9 Safety performance test ... 27
7.10 Determination of noise ... 28
7.11 Operational performance test ... 29
7.12 Assessment of availability ... 30
8 Inspection Rules ... 31
8.1 Exit-factory inspection ... 31
8.2 Type inspection ... 32
9 Marking, Packaging, Transportation and Storage ... 32
Storage/Retrieval Machine
1 Scope
This Standard specifies the terms and definitions, basic parameters, basic composition,
technical requirements, test methods, inspection rules, marking, packaging, transportation and
storage of storage/retrieval machine.
This Standard applies to storage/retrieval machine (hereinafter referred to as "stackers") used
in three-dimensional warehouses.
2 Normative References
The following documents are essential to the application of this document. For the dated
documents, only the versions with the dates indicated are applicable to this document; for the
undated documents, only the latest version (including all the amendments) is applicable to this
document.
GB/T 191 Packaging – Pictorial Marking for Handling of Goods
GB/T 699-2015 Quality Carbon Structural Steels
GB/T 700-2006 Carbon Structural Steels
GB/T 1231 Specifications of High Strength Bolts with Large Hexagon Head, Large
Hexagon Nuts, Plain Washers for Steel Structures
GB/T 1243 Short-pitch Transmission Precision Roller and Bush Chains, Attachments and
Associated Chain Sprockets
GB/T 3077 Alloy Structure Steels
GB/T 3098.1 Mechanical Properties of Fasteners - Bolts, Screws and Studs
GB/T 3098.2 Mechanical Properties of Fasteners - Nuts
GB/T 3323-2005 Radiographic Examination of Fusion Welded Joints in Metallic Materials
GB/T 3632 Sets of Torshear Type High Strength Bolt Hexagon Nut and Plain Washer for
Steel Structures
GB 5226.1 Electrical Safety of Machinery - Electrical Equipment of Machines - Part 1:
General Requirements
GB/T 6074 Leaf Chains Clevises and Sheaves - Dimensions Measuring Forces and Tensile
Strengths
GB/T 6417.1 Classification and Explanation of Imperfections in Fusion Welded Joints
GB/T 8918 Steel Wire Ropes for Important Purposes
GB/T 8923.1-2011 Preparation of Steel Substrates before Application of Paints and
Related Products - Visual Assessment of Surface Cleanliness - Part 1: Rust Grades and
Preparation Grades of Uncoated Steel Substrates and of Steel Substrates after Overall
Removal of Previous Coatings
GB/T 9286-1998 Paints and Varnishes - Cross Cut Test for Films
GB/T 9439-2010 Grey Iron Castings
GB/T 10095.1-2008 Cylindrical Gears - System of Accuracy - Part 1: Definitions and
Allowable Values of Deviations Relevant to Corresponding Flanks of Gear Teeth
GB/T 10095.2-2008 Cylindrical Gears - System of Accuracy - Part 2: Definitions and
Allowable Values of Deviations Relevant to Radial Composite Deviations and Runout
Information
GB/T 10096-1988 Accuracy of Rack
GB/T 11352-2009 Carbon Steel Castings for General Engineering Purpose
GB/T 13306 Plates
GB/T 13384 General Specifications for Packing of Mechanical and Electrical Product
GB 50254 Code for Construction and Acceptance of Low-Voltage Apparatus Electric
Equipment Installation Engineering
GB 50256 Code for Construction and Acceptance of Electric Device of Crane Electrical
Equipment Installation Engineering
JB/T 5319.1 Storage/Retrieval Machine – Vocabulary
JB/T 5323-2017 Welded Type Steel Structure Rack for Tiered Warehouse Facility –
Technical Conditions
JB/T 6392-2008 Rail Wheels for Crane
JB/T 9005.1 Casting Sheaves for Cranes - Groove Profiles
JB/T 9005.2 Casting Sheaves for Cranes - Selected Series and Matching of Diameters
consultation between the user and the manufacturer.
6.1.2 Materials
6.1.2.1 When the important components (including the upper beam, the lower beam, the upright
column, the pallet and the lifting mechanism) of the stacker are made of steel, the material shall
be selected with a mechanical property no lower than Q235-B specified in GB/T 700-2006.
6.1.2.2 The material of main parts (such as wheels, gears, pulleys, drums, forks, etc.) shall be
determined according to their functional requirements. Selection principle: The mechanical
properties of iron castings shall be no lower than HT200 specified in GB/T 9439-2010; the
mechanical properties of steel castings shall be no lower than ZG230-450 specified in GB/T
11352-2009; and the mechanical properties of forgings shall be no lower than 45 steel specified
in GB/T 699-2015.
6.1.3 Welding
6.1.3.1 There shall be no obvious defects visible by visual inspection specified in GB/T 6417.1
on the outside of the welding seam.
6.1.3.2 The quality grade of the butt welds in the main stress-bearing parts of important
components shall be no lower than Grade II specified in GB/T 3323-2005.
6.1.4 Common parts
6.1.4.1 Lifting wire rope
6.1.4.1.1 The round strand wire rope specified in GB/T 8918 shall be used for the steel wire
rope.
6.1.4.1.2 The wire rope shall be made of at least 114 wire rope strands. The tensile strength of
the steel wire is 1570 N/mm2 ~ 1960 N/mm2.
6.1.4.1.3 Wire rope safety factor: It shall be no less than 5 when there is no lift cab; and it shall
be no less than 9 when there is a lift cab.
6.1.4.2 Chains and sprockets
6.1.4.2.1 The chain shall generally adopt the short-pitch precision roller chain specified in GB/T
1243 or the plate chain specified in GB/T 6074.
6.1.4.2.2 The tooth shape and tolerance of the sprocket shall comply with the provisions of
GB/T 1243.
6.1.4.2.3 The teeth and grooves of the sprocket shall not have surface defects that can cause
damage to the chain.
6.1.4.2.4 All moving chains and sprockets shall be easy to lubricate.
6.1.4.2.5 Lifting chain safety factor: It shall be no less than 5 when there is no lift cab; and it
shall be no less than 10 when there is a lift cab.
6.1.4.3 Buffer
For a stacker with a forced speed limiting device, the buffer shall be selected according to the
actual maximum speed (but no lower than 70% of the rated speed) that may occur after forced
deceleration; for a stacker without a forced speed limiting device, the buffer shall be selected
at 100% rated speed.
6.1.4.4 Material of high-strength bolt pair and pin
The materials of high-strength bolts, nuts and washers shall comply with the provisions of GB/T
1231 or GB/T 3632. For torsional shear type high-strength bolts larger than M24 and high-
strength bolt pairs larger than M30, their materials shall comply with the provisions of GB/T
3098.1 and GB/T 3098.2. In addition to selecting the bolt pair materials that comply with the
provisions of GB/T 1231, 40Cr for Grade 8.8, and 35CrMo, 42CrMo, etc. for Grade 10.9 that
comply with the provisions of GB/T 3077 can also be used.
The material that mainly bears the connecting pin should be 45 steel that complies with the
provisions of GB/T 699-2015, and 40Cr, 35CrMo, 42CrMo steel that comply with the
provisions of GB/T 3077; and conduct necessary heat treatment.
6.1.5 Surface coating
6.1.5.1 Surface rust removal treatment shall be carried out before coating, and the surface rust
removal quality grade shall reach Level-Sa2 or Level-St2 as specified in GB/T 8923.1-2011.
6.1.5.2 The adhesion of the paint film shall not be lower than the Grade 2 quality requirements
specified in GB/T 9286-1998.
6.1.6 Safety signs
The safety signs should be painted on both sides of the pallet. Safety signs are yellow and black
ramps. The width of the yellow and black ramps is equal, generally 100 mm. Depending on the
size of the machine and the location of the safety sign, different widths can be used. On the
smaller surface, there shall be no less than two ramps for each color. The ramp is generally at a
45° angle to the horizontal. The oblique direction of the yellow and black ramps is symmetrical
with the centerline of the machine as the axis of symmetry.
6.2 Manufacturing and installation requirements
6.2.1 Metal structural parts
6.2.1.1 The lifting guide rails of stacker are allowed to be soldered in sections. After assembly,
The stacker shall set various safety protection devices and measures according to the
requirements in Clause 6 of JB/T 11269-2011.
6.3.8 Noise
The sound pressure level noise of the stacker should not exceed 80 dB CA).
6.3.9 Operation performance
The stacker shall be able to complete its operation according to the operation mode and control
mode specified in the design requirements.
6.3.10 Availability
6.3.10.1 The availability of the stacker refers to the probability that the stacker is in a state of
normal operation and no accidental drop at any given point in the operation period. Availability
is generally calculated based on test records for 2 consecutive working days.
6.3.10.2 The availability of the stacker shall be no less than 97%.
7 Test Methods
7.1 Preparation before the test
7.1.1 The inspection of appearance quality shall conform to the design drawings and the
requirements of this Standard.
7.1.2 The inspection of assembly accuracy shall conform to the design drawings and the
requirements of this Standard, which shall be recorded.
7.1.3 All lubrication points and reducers shall be filled with grease or lubricating oil as required.
7.1.4 The inspection of all electrical circuits shall meet the requirements of 6.2.8.
7.2 Test instrument and test load
Test instrument includes steel ruler, steel tape (with accuracy not exceeding ±0.1%), jack,
theodolite, stopwatch (with accuracy no greater than 0.01s), fifth wheel meter, sound level
meter (with accuracy not exceeding ±2 dB). All instruments and utensils shall be verified by
qualified organization and can only be used within the validity period.
The test load shall be suitable for the actual situation of the load handling device, and the weight
accuracy range shall be within ±2%. The test load of the static load test is 1.25 times the rated
lifting capacity; and the test load of the dynamic load test is 1.1 times the rated lifting capacity.
7.3 Working performance test of fork
The test procedures are as follows:
a) Based on the base zero plane of the warehouse, measure the lowest working position and
the highest working position of the upper plane of the fork when it is no-load.
b) For the stacker with location for lifting and lowering, one row of racks can be selected
arbitrarily during the test; and determine the access position of the upper plane of the
fork against each layer of cargo compartments.
c) Based on the middle position of the fork, extend the fork left and right, and measure the
working stroke of the fork by a steel tape.
d) Drive the stacker to the access of the warehouse platform, take the rated lifting capacity
and return to the middle position, and then lift the pallet to the middle position of the
height of the upright column. Set up a steel ruler at one end of the upper fork, use the
theodolite to take a reading; and then re-take the reading on the steel ruler when the fork
is extended to the maximum stroke. The difference between the two readings is the fork
deflection value. Use the same method to measure the deflection value at the other end
of the upper fork.
e) In the case of no-load and rated lifting capacity, respectively, measure the speed of
extending fork left and right; measure three times each; and take the average value.
f) In the case of no-load and rated lifting capacity, respectively, measure the left and right
parking accuracy and the parking accuracy of returning to the middle position, each of
which shall be measured three times.
g) Add a heavy object of rated lifting capacity to the fork, and set the blocking force in
accordance with the provisions of Table 1 in the front of the fork extending direction;
and then operate the fork.
7.4 Operating performance test
The test procedures are as follows:
a) Take a section in the middle of the laneway to measure the length and make a mark. When
the stacker has no load and rated lifting capacity, pass through this measurement section
at high speed and low speed, respectively; and measure its speed; measure three times
each; and take the average value;
b) The stacker operates at high speed and low speed respectively under no-load and rated
lifting capacity; and implements braking; measures the braking distance and time; and
calculates the respective acceleration and deceleration:
c) The stacker with automatic parking device operates at high speed under no-load and rated
7.8 Static stiffness test
The test load of the static stiffness test is the rated lifting capacity of the stacker plus additional
loads (such as driver and passenger), and the test is performed when the pallet is raised to the
upper limit of the upright column. The test procedures are as follows: ...
Delivery: 9 seconds. Download (& Email) true-PDF + Invoice.
Get Quotation: Click JB/T 7016-2017 (Self-service in 1-minute)
Historical versions (Master-website): JB/T 7016-2017
Preview True-PDF (Reload/Scroll-down if blank)
JB/T 7016-2017
JB
MACHINERY INDUSTRY STANDARD
OF THE PEOPLE’S REPUBLIC OF CHINA
ICS 53.080
J 83
Record No.: 57881-2017
Replacing JB/T 2960-1999, JB/T 7016-1993
Storage/Retrieval Machine
ISSUED ON: JANUARY 09, 2017
IMPLEMENTED ON: JULY 01, 2017
Issued by: Ministry of Industry and Information Technology of the People’s
Republic of China
Table of Contents
Foreword ... 4
1 Scope ... 5
2 Normative References ... 5
3 Terms and Definitions ... 7
4 Basic Parameters ... 8
5 Basic Compositions ... 8
5.1 Lower beam ... 8
5.2 Upright column ... 9
5.3 Upper beam ... 9
5.4 Pallet ... 9
5.5 Operating mechanism ... 9
5.6 Lifting mechanism ... 9
5.7 Load handling device ... 10
5.8 Rail ... 10
5.9 Control system ... 10
5.10 Others ... 10
6 Technical Requirements ... 10
6.1 General requirements ... 10
6.2 Manufacturing and installation requirements ... 12
6.3 Performance requirements ... 22
7 Test Methods ... 24
7.1 Preparation before the test ... 24
7.2 Test instrument and test load ... 24
7.3 Working performance test of fork ... 25
7.4 Operating performance test... 25
7.5 Lifting performance test of pallet ... 26
7.6 Static load test ... 26
7.7 Dynamic load test ... 26
7.8 Static stiffness test ... 27
7.9 Safety performance test ... 27
7.10 Determination of noise ... 28
7.11 Operational performance test ... 29
7.12 Assessment of availability ... 30
8 Inspection Rules ... 31
8.1 Exit-factory inspection ... 31
8.2 Type inspection ... 32
9 Marking, Packaging, Transportation and Storage ... 32
Storage/Retrieval Machine
1 Scope
This Standard specifies the terms and definitions, basic parameters, basic composition,
technical requirements, test methods, inspection rules, marking, packaging, transportation and
storage of storage/retrieval machine.
This Standard applies to storage/retrieval machine (hereinafter referred to as "stackers") used
in three-dimensional warehouses.
2 Normative References
The following documents are essential to the application of this document. For the dated
documents, only the versions with the dates indicated are applicable to this document; for the
undated documents, only the latest version (including all the amendments) is applicable to this
document.
GB/T 191 Packaging – Pictorial Marking for Handling of Goods
GB/T 699-2015 Quality Carbon Structural Steels
GB/T 700-2006 Carbon Structural Steels
GB/T 1231 Specifications of High Strength Bolts with Large Hexagon Head, Large
Hexagon Nuts, Plain Washers for Steel Structures
GB/T 1243 Short-pitch Transmission Precision Roller and Bush Chains, Attachments and
Associated Chain Sprockets
GB/T 3077 Alloy Structure Steels
GB/T 3098.1 Mechanical Properties of Fasteners - Bolts, Screws and Studs
GB/T 3098.2 Mechanical Properties of Fasteners - Nuts
GB/T 3323-2005 Radiographic Examination of Fusion Welded Joints in Metallic Materials
GB/T 3632 Sets of Torshear Type High Strength Bolt Hexagon Nut and Plain Washer for
Steel Structures
GB 5226.1 Electrical Safety of Machinery - Electrical Equipment of Machines - Part 1:
General Requirements
GB/T 6074 Leaf Chains Clevises and Sheaves - Dimensions Measuring Forces and Tensile
Strengths
GB/T 6417.1 Classification and Explanation of Imperfections in Fusion Welded Joints
GB/T 8918 Steel Wire Ropes for Important Purposes
GB/T 8923.1-2011 Preparation of Steel Substrates before Application of Paints and
Related Products - Visual Assessment of Surface Cleanliness - Part 1: Rust Grades and
Preparation Grades of Uncoated Steel Substrates and of Steel Substrates after Overall
Removal of Previous Coatings
GB/T 9286-1998 Paints and Varnishes - Cross Cut Test for Films
GB/T 9439-2010 Grey Iron Castings
GB/T 10095.1-2008 Cylindrical Gears - System of Accuracy - Part 1: Definitions and
Allowable Values of Deviations Relevant to Corresponding Flanks of Gear Teeth
GB/T 10095.2-2008 Cylindrical Gears - System of Accuracy - Part 2: Definitions and
Allowable Values of Deviations Relevant to Radial Composite Deviations and Runout
Information
GB/T 10096-1988 Accuracy of Rack
GB/T 11352-2009 Carbon Steel Castings for General Engineering Purpose
GB/T 13306 Plates
GB/T 13384 General Specifications for Packing of Mechanical and Electrical Product
GB 50254 Code for Construction and Acceptance of Low-Voltage Apparatus Electric
Equipment Installation Engineering
GB 50256 Code for Construction and Acceptance of Electric Device of Crane Electrical
Equipment Installation Engineering
JB/T 5319.1 Storage/Retrieval Machine – Vocabulary
JB/T 5323-2017 Welded Type Steel Structure Rack for Tiered Warehouse Facility –
Technical Conditions
JB/T 6392-2008 Rail Wheels for Crane
JB/T 9005.1 Casting Sheaves for Cranes - Groove Profiles
JB/T 9005.2 Casting Sheaves for Cranes - Selected Series and Matching of Diameters
consultation between the user and the manufacturer.
6.1.2 Materials
6.1.2.1 When the important components (including the upper beam, the lower beam, the upright
column, the pallet and the lifting mechanism) of the stacker are made of steel, the material shall
be selected with a mechanical property no lower than Q235-B specified in GB/T 700-2006.
6.1.2.2 The material of main parts (such as wheels, gears, pulleys, drums, forks, etc.) shall be
determined according to their functional requirements. Selection principle: The mechanical
properties of iron castings shall be no lower than HT200 specified in GB/T 9439-2010; the
mechanical properties of steel castings shall be no lower than ZG230-450 specified in GB/T
11352-2009; and the mechanical properties of forgings shall be no lower than 45 steel specified
in GB/T 699-2015.
6.1.3 Welding
6.1.3.1 There shall be no obvious defects visible by visual inspection specified in GB/T 6417.1
on the outside of the welding seam.
6.1.3.2 The quality grade of the butt welds in the main stress-bearing parts of important
components shall be no lower than Grade II specified in GB/T 3323-2005.
6.1.4 Common parts
6.1.4.1 Lifting wire rope
6.1.4.1.1 The round strand wire rope specified in GB/T 8918 shall be used for the steel wire
rope.
6.1.4.1.2 The wire rope shall be made of at least 114 wire rope strands. The tensile strength of
the steel wire is 1570 N/mm2 ~ 1960 N/mm2.
6.1.4.1.3 Wire rope safety factor: It shall be no less than 5 when there is no lift cab; and it shall
be no less than 9 when there is a lift cab.
6.1.4.2 Chains and sprockets
6.1.4.2.1 The chain shall generally adopt the short-pitch precision roller chain specified in GB/T
1243 or the plate chain specified in GB/T 6074.
6.1.4.2.2 The tooth shape and tolerance of the sprocket shall comply with the provisions of
GB/T 1243.
6.1.4.2.3 The teeth and grooves of the sprocket shall not have surface defects that can cause
damage to the chain.
6.1.4.2.4 All moving chains and sprockets shall be easy to lubricate.
6.1.4.2.5 Lifting chain safety factor: It shall be no less than 5 when there is no lift cab; and it
shall be no less than 10 when there is a lift cab.
6.1.4.3 Buffer
For a stacker with a forced speed limiting device, the buffer shall be selected according to the
actual maximum speed (but no lower than 70% of the rated speed) that may occur after forced
deceleration; for a stacker without a forced speed limiting device, the buffer shall be selected
at 100% rated speed.
6.1.4.4 Material of high-strength bolt pair and pin
The materials of high-strength bolts, nuts and washers shall comply with the provisions of GB/T
1231 or GB/T 3632. For torsional shear type high-strength bolts larger than M24 and high-
strength bolt pairs larger than M30, their materials shall comply with the provisions of GB/T
3098.1 and GB/T 3098.2. In addition to selecting the bolt pair materials that comply with the
provisions of GB/T 1231, 40Cr for Grade 8.8, and 35CrMo, 42CrMo, etc. for Grade 10.9 that
comply with the provisions of GB/T 3077 can also be used.
The material that mainly bears the connecting pin should be 45 steel that complies with the
provisions of GB/T 699-2015, and 40Cr, 35CrMo, 42CrMo steel that comply with the
provisions of GB/T 3077; and conduct necessary heat treatment.
6.1.5 Surface coating
6.1.5.1 Surface rust removal treatment shall be carried out before coating, and the surface rust
removal quality grade shall reach Level-Sa2 or Level-St2 as specified in GB/T 8923.1-2011.
6.1.5.2 The adhesion of the paint film shall not be lower than the Grade 2 quality requirements
specified in GB/T 9286-1998.
6.1.6 Safety signs
The safety signs should be painted on both sides of the pallet. Safety signs are yellow and black
ramps. The width of the yellow and black ramps is equal, generally 100 mm. Depending on the
size of the machine and the location of the safety sign, different widths can be used. On the
smaller surface, there shall be no less than two ramps for each color. The ramp is generally at a
45° angle to the horizontal. The oblique direction of the yellow and black ramps is symmetrical
with the centerline of the machine as the axis of symmetry.
6.2 Manufacturing and installation requirements
6.2.1 Metal structural parts
6.2.1.1 The lifting guide rails of stacker are allowed to be soldered in sections. After assembly,
The stacker shall set various safety protection devices and measures according to the
requirements in Clause 6 of JB/T 11269-2011.
6.3.8 Noise
The sound pressure level noise of the stacker should not exceed 80 dB CA).
6.3.9 Operation performance
The stacker shall be able to complete its operation according to the operation mode and control
mode specified in the design requirements.
6.3.10 Availability
6.3.10.1 The availability of the stacker refers to the probability that the stacker is in a state of
normal operation and no accidental drop at any given point in the operation period. Availability
is generally calculated based on test records for 2 consecutive working days.
6.3.10.2 The availability of the stacker shall be no less than 97%.
7 Test Methods
7.1 Preparation before the test
7.1.1 The inspection of appearance quality shall conform to the design drawings and the
requirements of this Standard.
7.1.2 The inspection of assembly accuracy shall conform to the design drawings and the
requirements of this Standard, which shall be recorded.
7.1.3 All lubrication points and reducers shall be filled with grease or lubricating oil as required.
7.1.4 The inspection of all electrical circuits shall meet the requirements of 6.2.8.
7.2 Test instrument and test load
Test instrument includes steel ruler, steel tape (with accuracy not exceeding ±0.1%), jack,
theodolite, stopwatch (with accuracy no greater than 0.01s), fifth wheel meter, sound level
meter (with accuracy not exceeding ±2 dB). All instruments and utensils shall be verified by
qualified organization and can only be used within the validity period.
The test load shall be suitable for the actual situation of the load handling device, and the weight
accuracy range shall be within ±2%. The test load of the static load test is 1.25 times the rated
lifting capacity; and the test load of the dynamic load test is 1.1 times the rated lifting capacity.
7.3 Working performance test of fork
The test procedures are as follows:
a) Based on the base zero plane of the warehouse, measure the lowest working position and
the highest working position of the upper plane of the fork when it is no-load.
b) For the stacker with location for lifting and lowering, one row of racks can be selected
arbitrarily during the test; and determine the access position of the upper plane of the
fork against each layer of cargo compartments.
c) Based on the middle position of the fork, extend the fork left and right, and measure the
working stroke of the fork by a steel tape.
d) Drive the stacker to the access of the warehouse platform, take the rated lifting capacity
and return to the middle position, and then lift the pallet to the middle position of the
height of the upright column. Set up a steel ruler at one end of the upper fork, use the
theodolite to take a reading; and then re-take the reading on the steel ruler when the fork
is extended to the maximum stroke. The difference between the two readings is the fork
deflection value. Use the same method to measure the deflection value at the other end
of the upper fork.
e) In the case of no-load and rated lifting capacity, respectively, measure the speed of
extending fork left and right; measure three times each; and take the average value.
f) In the case of no-load and rated lifting capacity, respectively, measure the left and right
parking accuracy and the parking accuracy of returning to the middle position, each of
which shall be measured three times.
g) Add a heavy object of rated lifting capacity to the fork, and set the blocking force in
accordance with the provisions of Table 1 in the front of the fork extending direction;
and then operate the fork.
7.4 Operating performance test
The test procedures are as follows:
a) Take a section in the middle of the laneway to measure the length and make a mark. When
the stacker has no load and rated lifting capacity, pass through this measurement section
at high speed and low speed, respectively; and measure its speed; measure three times
each; and take the average value;
b) The stacker operates at high speed and low speed respectively under no-load and rated
lifting capacity; and implements braking; measures the braking distance and time; and
calculates the respective acceleration and deceleration:
c) The stacker with automatic parking device operates at high speed under no-load and rated
7.8 Static stiffness test
The test load of the static stiffness test is the rated lifting capacity of the stacker plus additional
loads (such as driver and passenger), and the test is performed when the pallet is raised to the
upper limit of the upright column. The test procedures are as follows: ...
Share
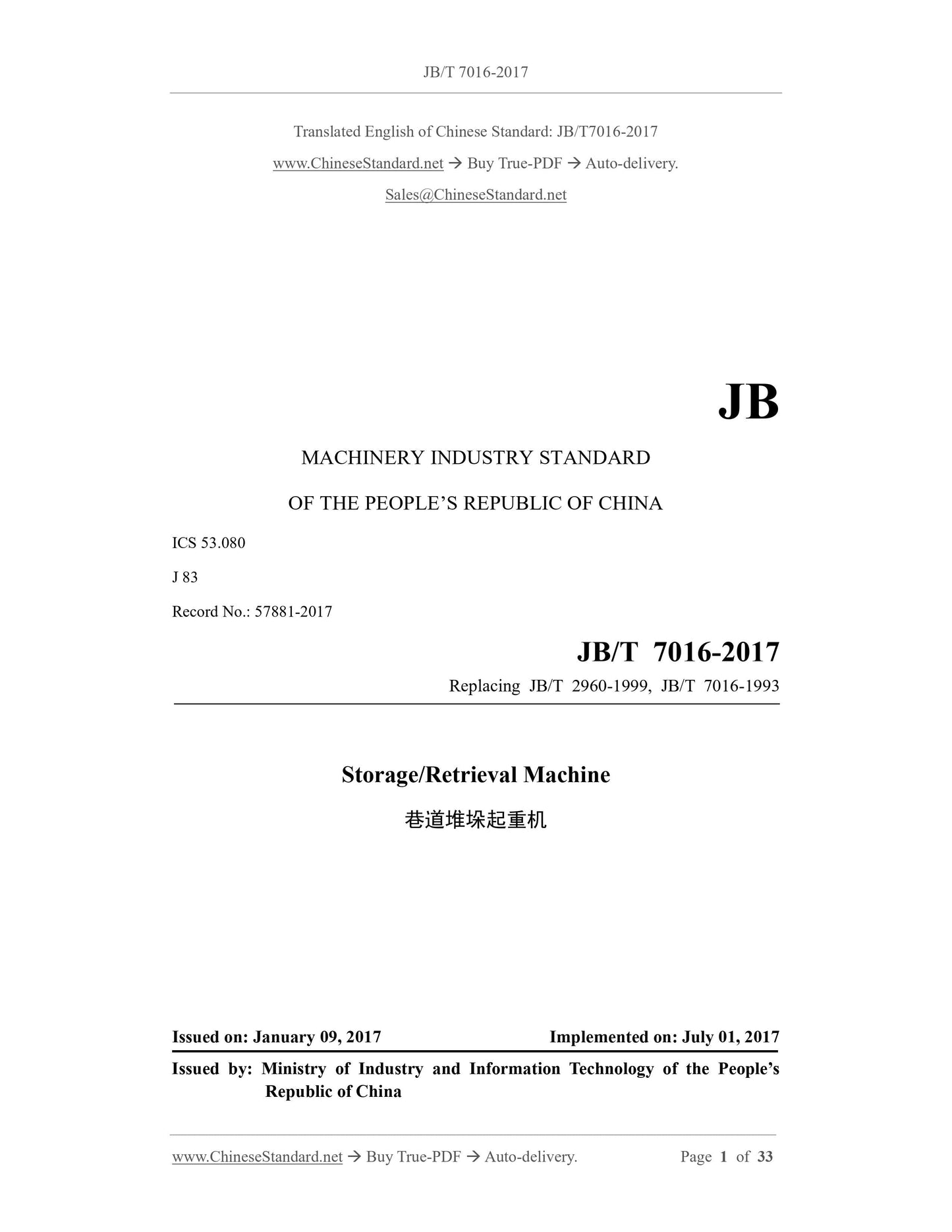
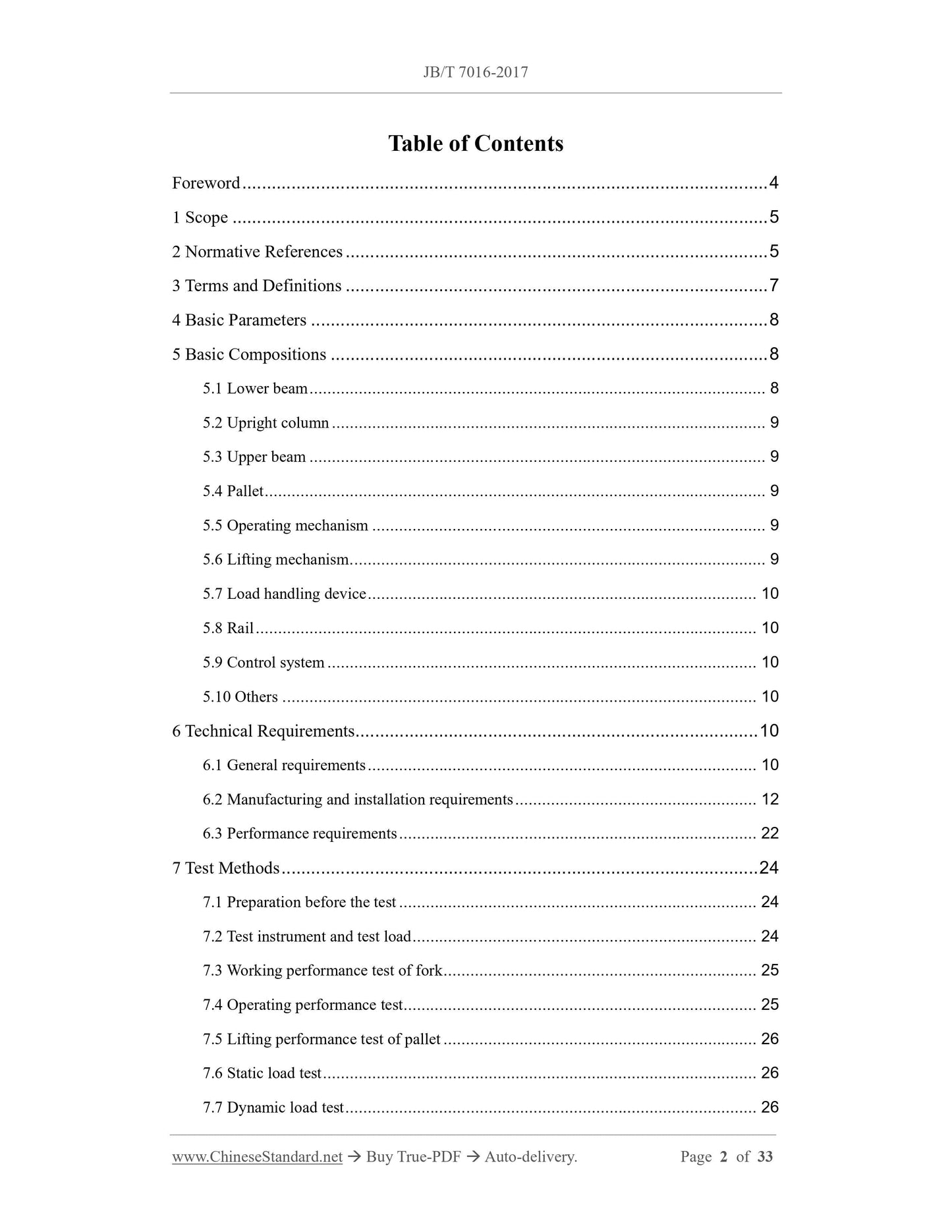
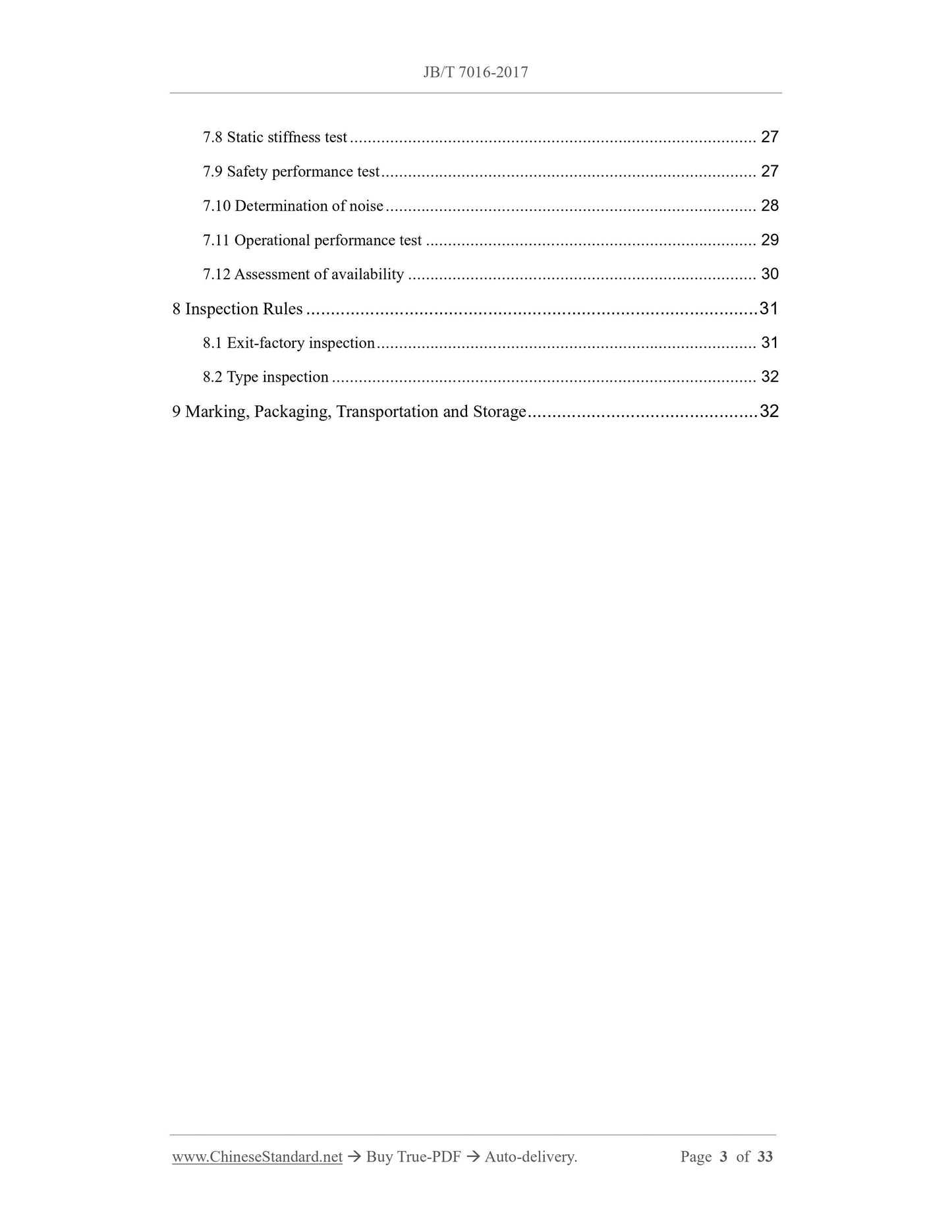
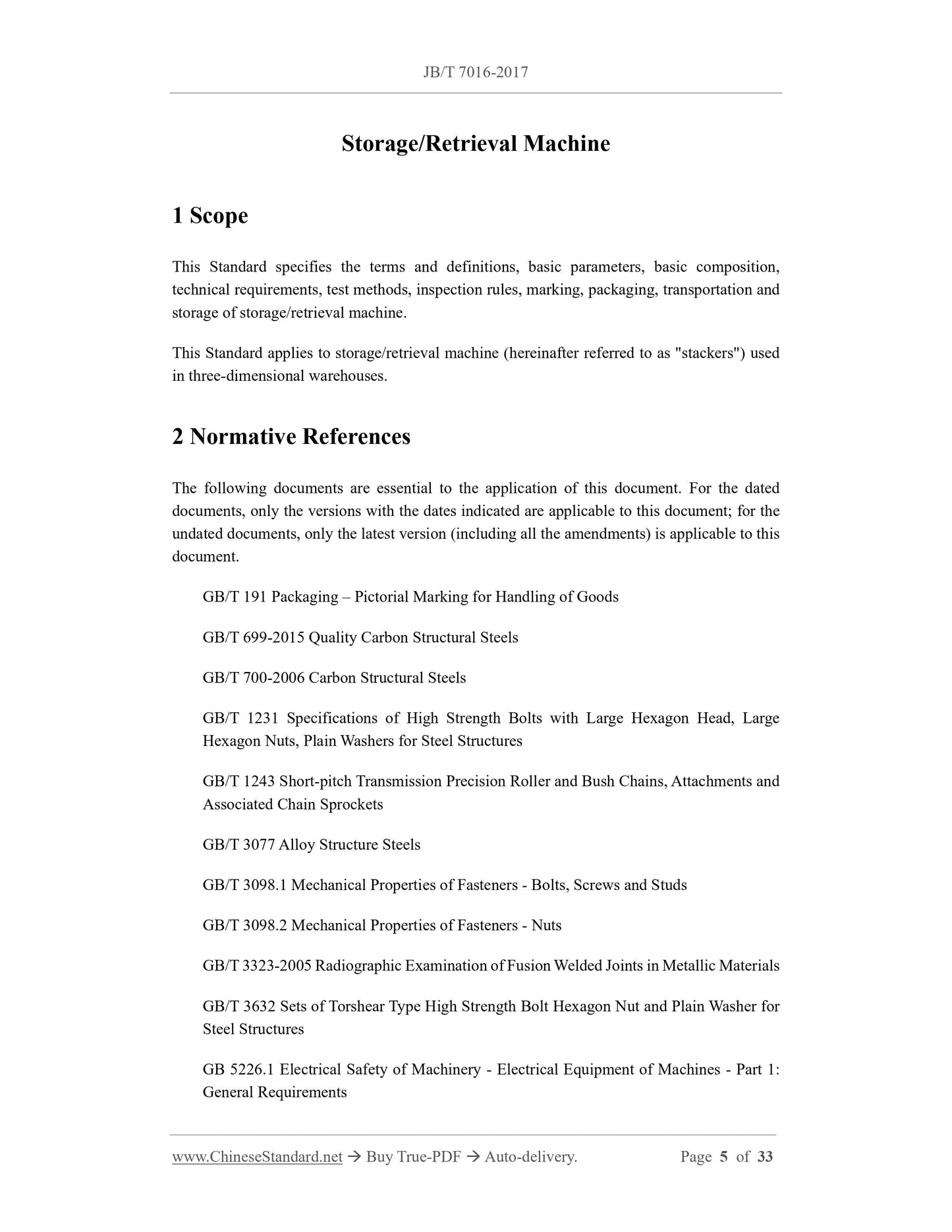
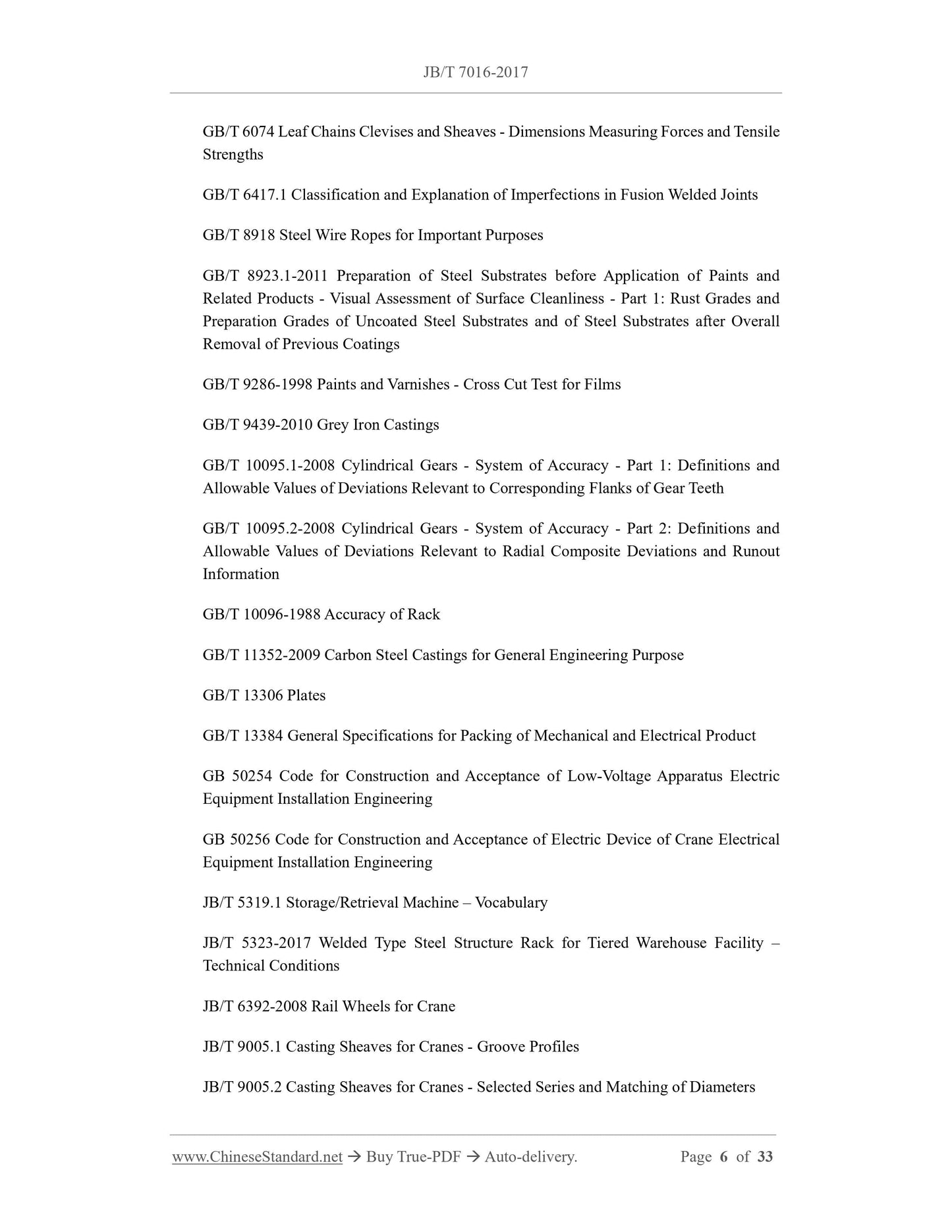
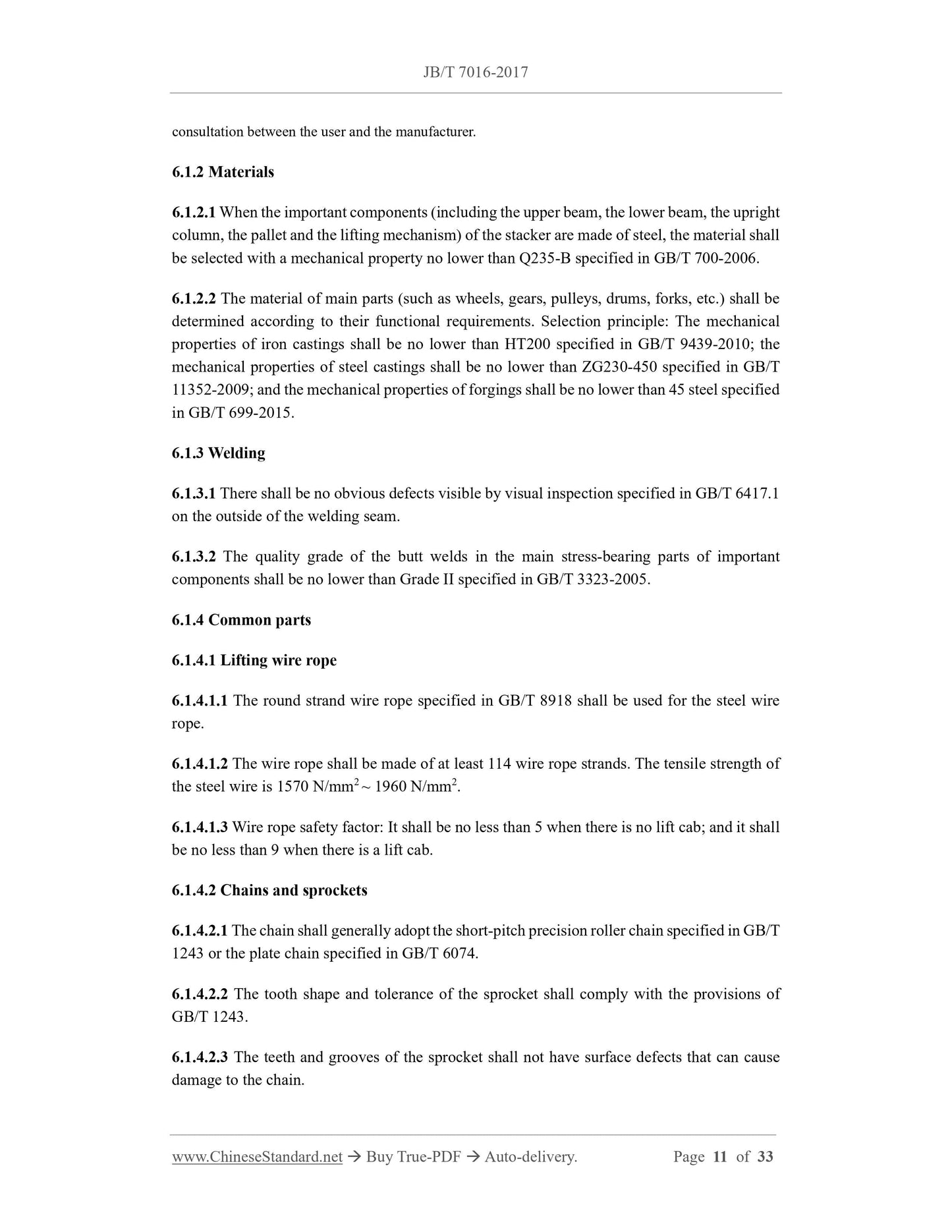
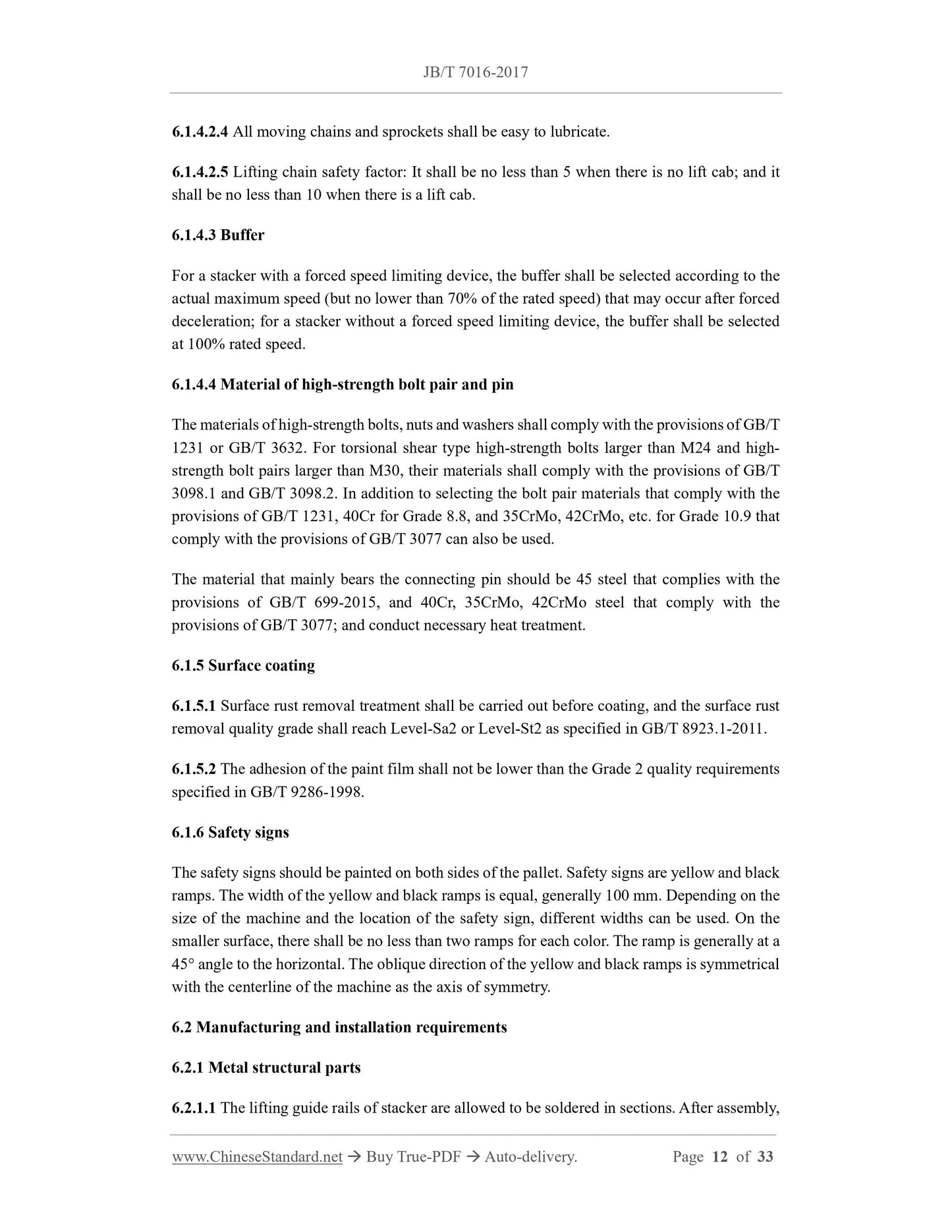
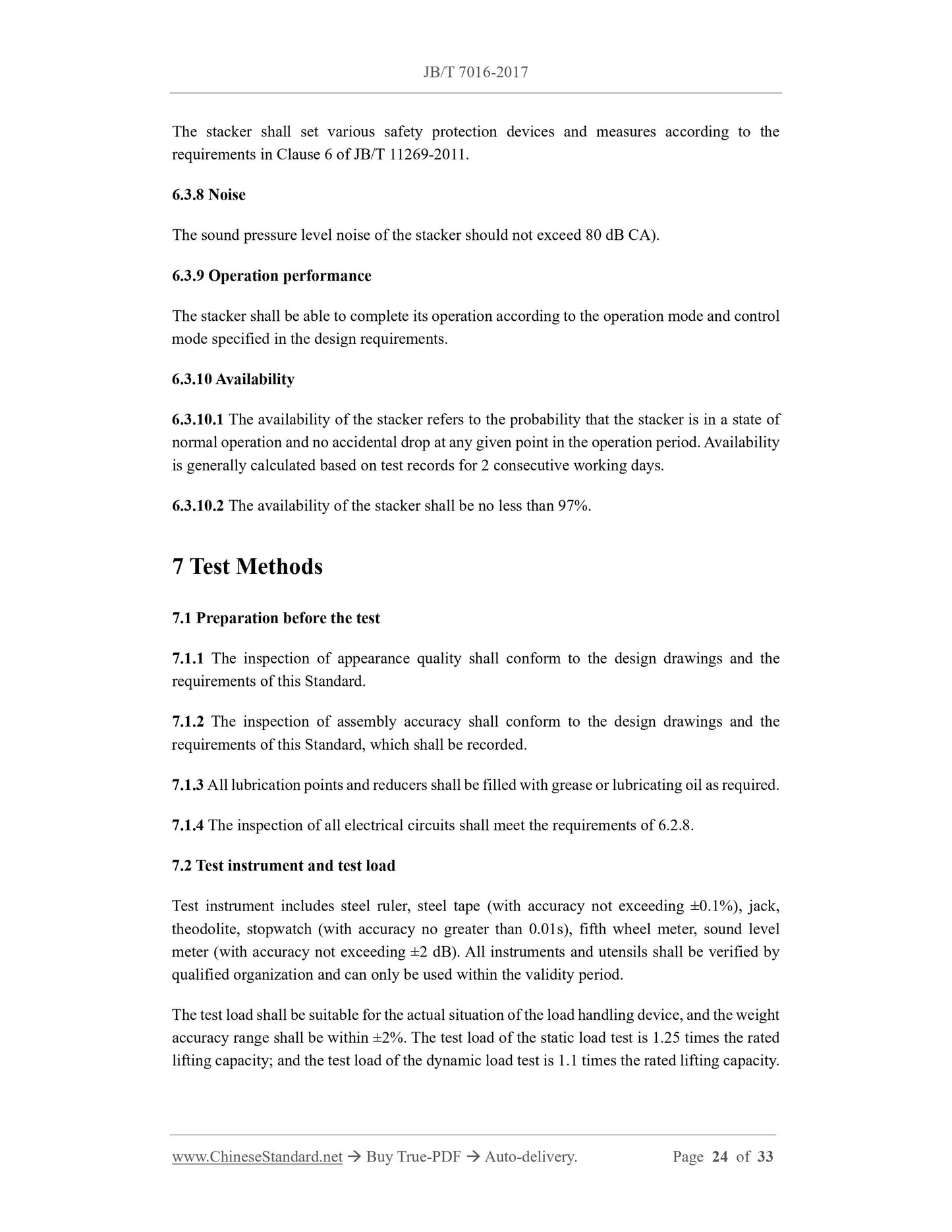
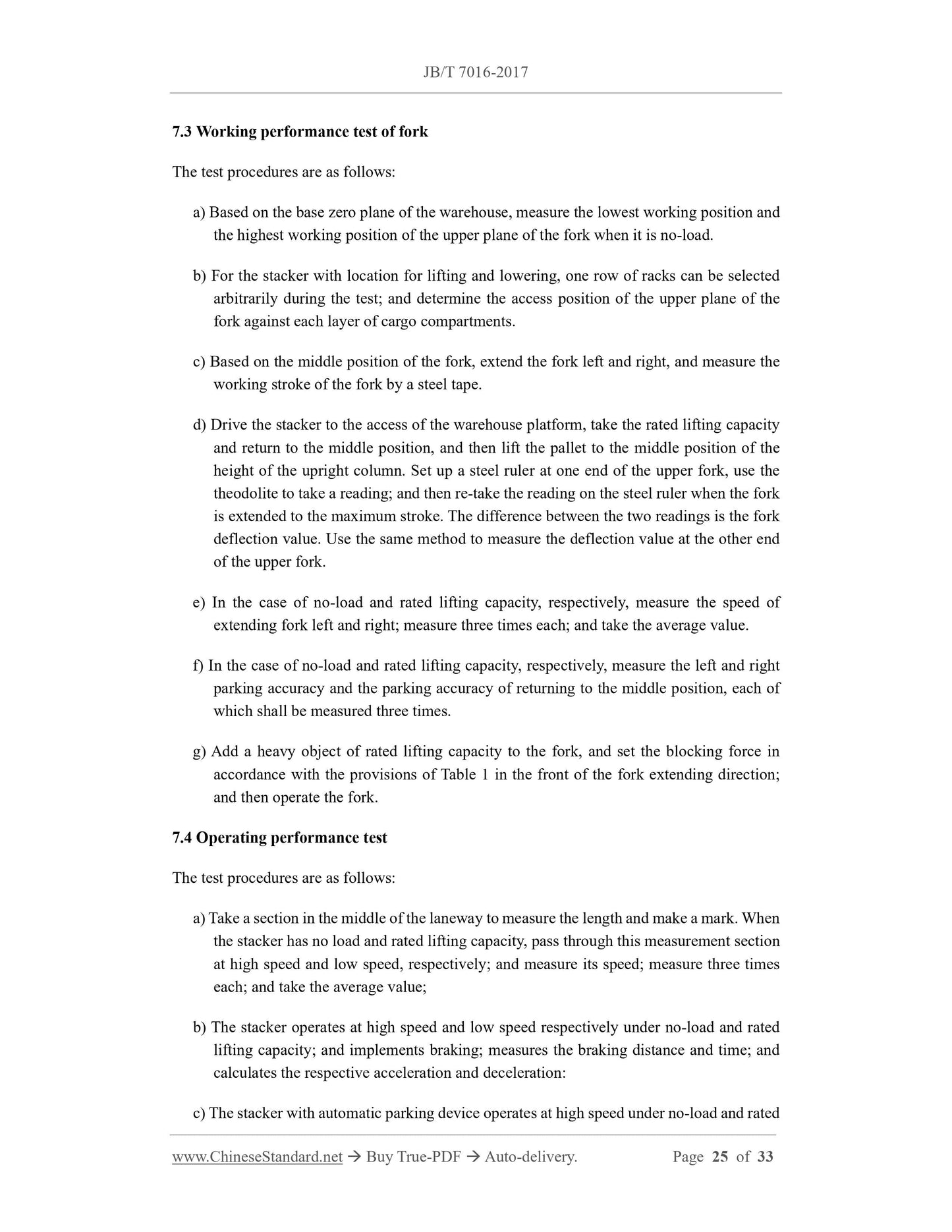
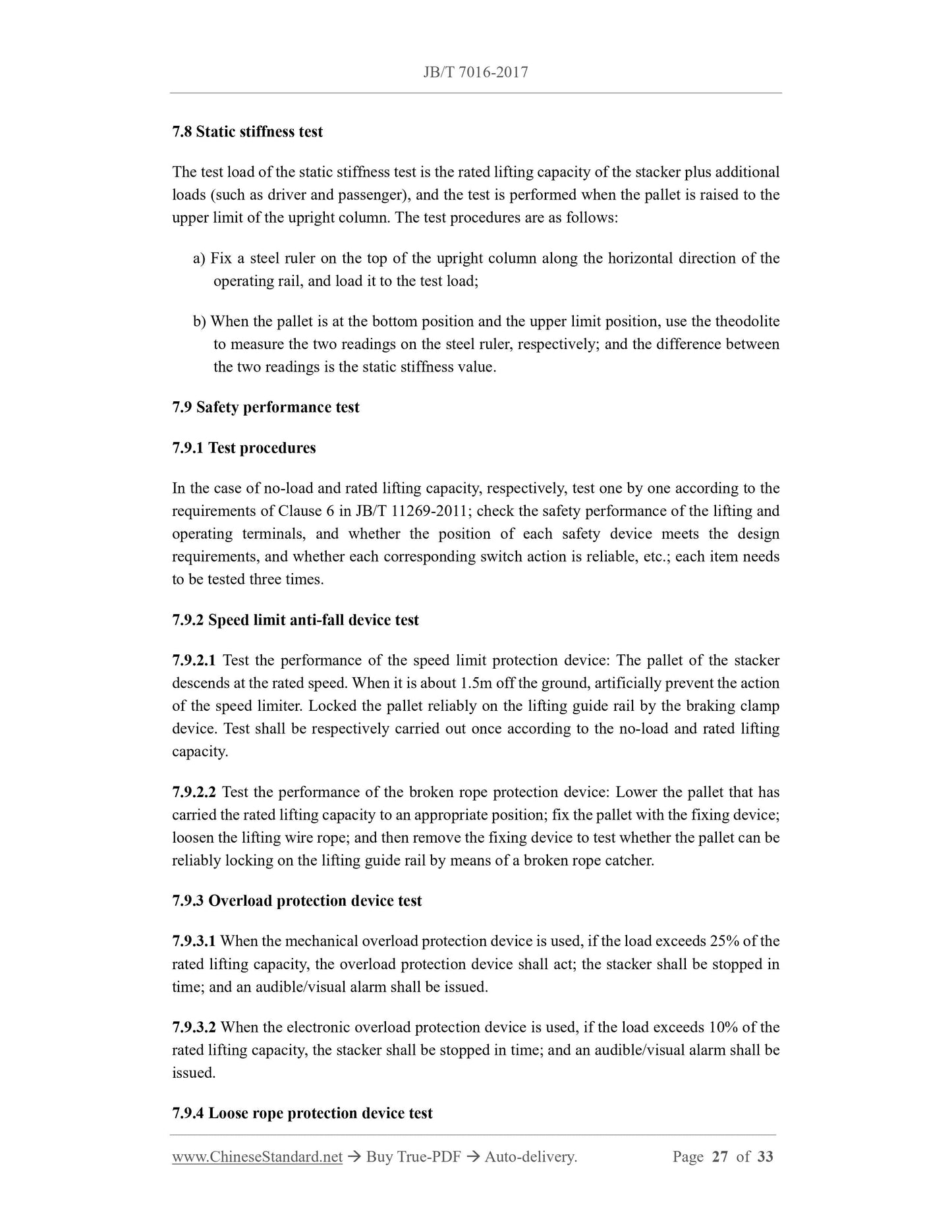
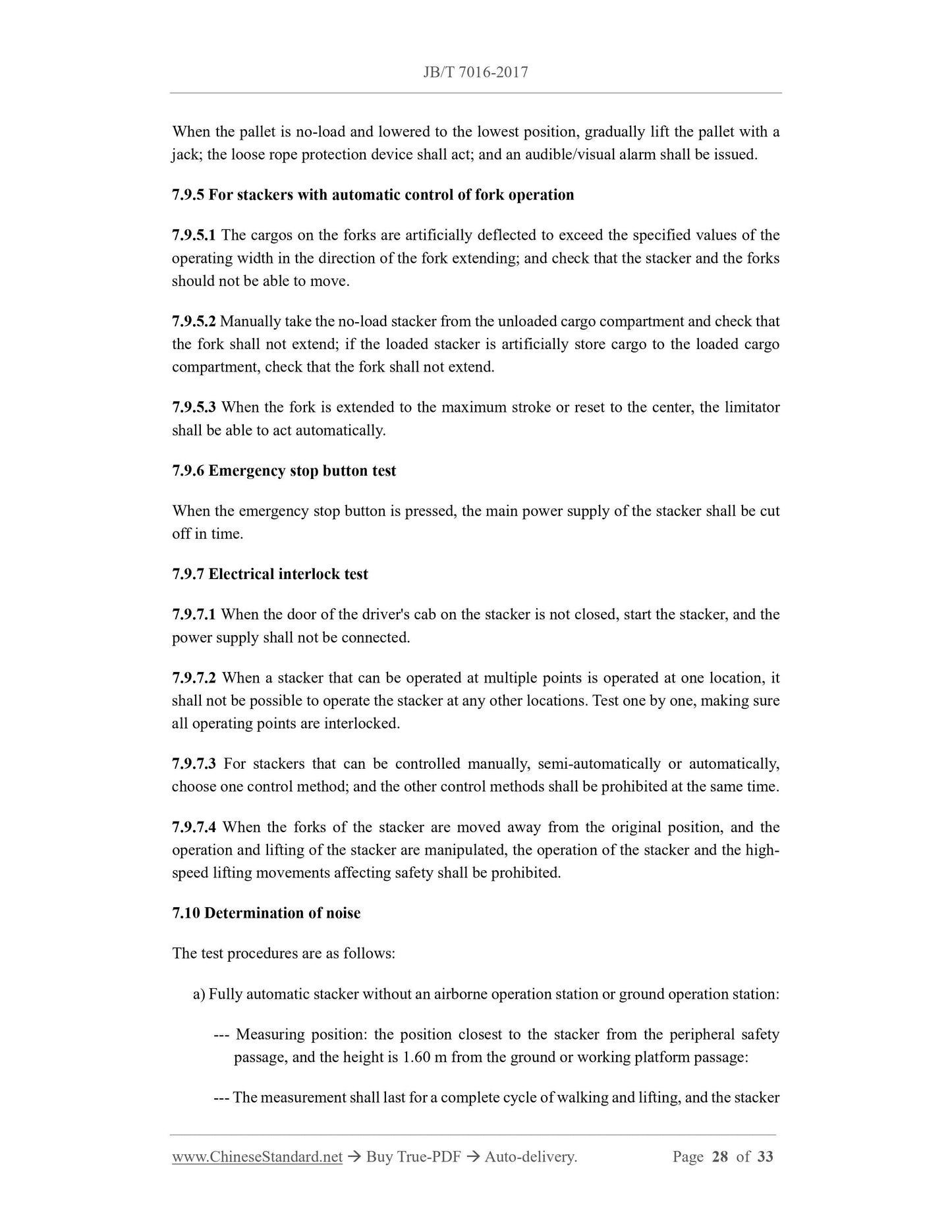