1
/
von
12
PayPal, credit cards. Download editable-PDF & invoice in 1 second!
YY/T 0681.18-2020 English PDF (YYT0681.18-2020)
YY/T 0681.18-2020 English PDF (YYT0681.18-2020)
Normaler Preis
$350.00 USD
Normaler Preis
Verkaufspreis
$350.00 USD
Grundpreis
/
pro
Versand wird beim Checkout berechnet
Verfügbarkeit für Abholungen konnte nicht geladen werden
Delivery: 3 seconds. Download true-PDF + Invoice.
Get QUOTATION in 1-minute: Click YY/T 0681.18-2020
Historical versions: YY/T 0681.18-2020
Preview True-PDF (Reload/Scroll if blank)
YY/T 0681.18-2020: Test methods for sterile medical device package--Part 18: Nondestructive detection of leaks in packages by vacuum decay method
YY/T 0681.18-2020
YY
PHARMACEUTICAL INDUSTRY STANDARD
OF THE PEOPLE’S REPUBLIC OF CHINA
ICS 11.080.40
C 31
Test methods for sterile medical device package - Part 18:
Nondestructive detection of leaks in packages by vacuum
decay method
装泄露
ISSUED ON: MARCH 31, 2020
IMPLEMENTED ON: APRIL 01, 2021
Issued by: National Medical Products Administration
Table of Contents
Foreword ... 3
Introduction ... 5
1 Scope ... 7
2 Normative references ... 7
3 Terms and definitions ... 7
4 Overview ... 9
5 Significance and application ... 10
6 Instruments ... 10
7 Danger (source) ... 13
8 Instrument preparation ... 13
9 Calibration and standardization ... 14
10 Programs ... 14
11 Reports ... 15
Appendix A (Normative) Vacuum decay leak test theory ... 17
Appendix B (Normative) Determination of critical test parameters and verification of
test sensitivity ... 21
Appendix C (Informative) Precision and bias ... 23
References ... 31
Test methods for sterile medical device package - Part 18:
Nondestructive detection of leaks in packages by vacuum
decay method
1 Scope
This Part of YY/T 0681 specifies the test method for the non-destructive detection of
the leakage of the packaging system of sterile medical devices, by the vacuum decay
method.
This Part applies to rigid and semi-rigid trays without lids, trays or cups with porous
barrier covers, nonporous rigid packaging, nonporous flexible packaging.
2 Normative references
The following documents are essential to the application of this document. For the dated
documents, only the versions with the dates indicated are applicable to this document;
for the undated documents, only the latest version (including all the amendments) is
applicable to this standard.
GB/T 19633.1 Packaging for terminally sterilized medical devices - Part 1:
Requirements for materials, sterile barrier systems and packaging systems
3 Terms and definitions
The following terms and definitions apply to this document.
3.1
Baseline vacuum decay
The degree of change in vacuum within the test chamber over time, as evidenced by
non-leaking control packages.
3.2
Control, non-leaking packages
Defective packaging, which is properly sealed or closed, in accordance with the
manufacturer's specifications.
airflow rate into a test chamber, to verify instrument sensitivity. Airflow meters
should be calibrated to a suitable standard. The operating range of the airflow meter
should be such that the desired sensitivity limit for the intended leak test is obtained.
4 Overview
4.1 Place the test package in the test chamber, to apply vacuum. The test chamber is
isolated from the vacuum source; the pressure sensor (absolute pressure or gauge
pressure) is used alone or in combination with another differential pressure sensor, to
monitor the vacuum degree in the test chamber and the change of vacuum over time.
Vacuum decay, or pressure rise in the test chamber, is caused by the gas in the headspace
of the package being drawn out of the package through any leaks, as well as background
noise. Vacuum decay can also be caused by volatilization of liquid, within the package
that partially or completely enters the leak path. For this case, vacuum decay can only
occur, when the test pressure in the test chamber is lower than the vapor pressure of the
liquid.
4.2 For the tray or cup with the porous barrier cover material, the leakage located on
the tray or holder cup body, as well as the joint between the cover material and the tray,
can be tested. Leaks in the porous lid itself cannot be detected. When testing this type
of packaging, take measures to physically cover or block the surface of the porous
barrier material, to prevent the escape of packaging gases through the porous lid. This
may require some sample preparation, depending on the method of occlusion required,
BUT must be non-destructive and non-invasive. Vacuum decay in packages, which have
a porous barrier lid material, may include background noise from the gas, between the
lidding material and shielding surface, OR from lateral airflow through the porous
barrier material itself at the lid/tray's seal junction.
4.3 The sensitivity of the test depends on the design of the package under test, the
sensitivity of the sensor, the design of the test chamber, the design of the test system,
the critical test parameters of time and pressure. The choice of test system and leak test
parameters for any given product packaging system must be based on the contents of
the package (liquid/solid with large/small headspace gas) and the nature of the package
(soft or rigid, porous or nonporous). When the instrument has a more sensitive pressure
sensor AND the void volume in the test chamber is the smallest, the test system has the
potential to detect the smallest leak. Extended test times can detect smaller gas leaks.
Minimizing background noise pressure fluctuations also improves test sensitivity. For
packaging with a porous barrier lid material, occluder technology can minimize
background noise. For flexible packaging or semi-rigid packaging, the expansion of the
packaging can be limited to reduce noise, by rationally designing the test chamber.
Release of trapped gas or trapped water vapor, in the test system or between package
components under test, may also contribute to background noise. This noise can be
distinguished from an actual leak, by extending the test time, to allow the vacuum to
return to the initial level, OR by extending the equilibration time.
Note: See Appendix A for more information on "Leak test theory". Examples of experimental
methods and test instruments, which are used to obtain precision and bias data, are given in
Appendix C and summarized in Table C.1.
5 Significance and application
5.1 Leaks in medical device packaging may result in the ingress of unwanted gases
(most commonly oxygen), harmful microorganisms, or particulate contaminants.
Package leaks may manifest as defects in the package components themselves or in the
sealed joints between package components. Ensuring the consistency and integrity of
packaging is an essential capability for leak detection.
5.2 After initial setup and calibration, a test operation can be semi-automatic, fully
automatic or manual. This test method is capable of non-destructively detecting leaks,
that are not apparent. The test method does not require the introduction of any foreign
materials or substances, such as dye solutions or gases. However, it shall be noted that
the surface of all porous materials needs to be physically blocked during the test, to
prevent the gas from passing through the porous surface and causing the vacuum in the
test chamber to drop rapidly. Because this test method is only based on the detection of
pressure changes in the test chamber, which are affected by the leakage of gas or steam
from the challenge package.
5.3 This test is a useful research tool, for optimizing package sealing parameters and
for comparative evaluation of various packages and materials. Because of its rapidity,
non-invasiveness, non-destructiveness, this test method is also suitable for installation
on the production line, or for 100% online testing of products, or for statistical sampling
testing.
5.4 For the vacuum decay test, leak test results exceeding allowable limits may be
indicated by an acoustic or optical signal response (or both).
6 Instruments
6.1 Vacuum dec...
Get QUOTATION in 1-minute: Click YY/T 0681.18-2020
Historical versions: YY/T 0681.18-2020
Preview True-PDF (Reload/Scroll if blank)
YY/T 0681.18-2020: Test methods for sterile medical device package--Part 18: Nondestructive detection of leaks in packages by vacuum decay method
YY/T 0681.18-2020
YY
PHARMACEUTICAL INDUSTRY STANDARD
OF THE PEOPLE’S REPUBLIC OF CHINA
ICS 11.080.40
C 31
Test methods for sterile medical device package - Part 18:
Nondestructive detection of leaks in packages by vacuum
decay method
装泄露
ISSUED ON: MARCH 31, 2020
IMPLEMENTED ON: APRIL 01, 2021
Issued by: National Medical Products Administration
Table of Contents
Foreword ... 3
Introduction ... 5
1 Scope ... 7
2 Normative references ... 7
3 Terms and definitions ... 7
4 Overview ... 9
5 Significance and application ... 10
6 Instruments ... 10
7 Danger (source) ... 13
8 Instrument preparation ... 13
9 Calibration and standardization ... 14
10 Programs ... 14
11 Reports ... 15
Appendix A (Normative) Vacuum decay leak test theory ... 17
Appendix B (Normative) Determination of critical test parameters and verification of
test sensitivity ... 21
Appendix C (Informative) Precision and bias ... 23
References ... 31
Test methods for sterile medical device package - Part 18:
Nondestructive detection of leaks in packages by vacuum
decay method
1 Scope
This Part of YY/T 0681 specifies the test method for the non-destructive detection of
the leakage of the packaging system of sterile medical devices, by the vacuum decay
method.
This Part applies to rigid and semi-rigid trays without lids, trays or cups with porous
barrier covers, nonporous rigid packaging, nonporous flexible packaging.
2 Normative references
The following documents are essential to the application of this document. For the dated
documents, only the versions with the dates indicated are applicable to this document;
for the undated documents, only the latest version (including all the amendments) is
applicable to this standard.
GB/T 19633.1 Packaging for terminally sterilized medical devices - Part 1:
Requirements for materials, sterile barrier systems and packaging systems
3 Terms and definitions
The following terms and definitions apply to this document.
3.1
Baseline vacuum decay
The degree of change in vacuum within the test chamber over time, as evidenced by
non-leaking control packages.
3.2
Control, non-leaking packages
Defective packaging, which is properly sealed or closed, in accordance with the
manufacturer's specifications.
airflow rate into a test chamber, to verify instrument sensitivity. Airflow meters
should be calibrated to a suitable standard. The operating range of the airflow meter
should be such that the desired sensitivity limit for the intended leak test is obtained.
4 Overview
4.1 Place the test package in the test chamber, to apply vacuum. The test chamber is
isolated from the vacuum source; the pressure sensor (absolute pressure or gauge
pressure) is used alone or in combination with another differential pressure sensor, to
monitor the vacuum degree in the test chamber and the change of vacuum over time.
Vacuum decay, or pressure rise in the test chamber, is caused by the gas in the headspace
of the package being drawn out of the package through any leaks, as well as background
noise. Vacuum decay can also be caused by volatilization of liquid, within the package
that partially or completely enters the leak path. For this case, vacuum decay can only
occur, when the test pressure in the test chamber is lower than the vapor pressure of the
liquid.
4.2 For the tray or cup with the porous barrier cover material, the leakage located on
the tray or holder cup body, as well as the joint between the cover material and the tray,
can be tested. Leaks in the porous lid itself cannot be detected. When testing this type
of packaging, take measures to physically cover or block the surface of the porous
barrier material, to prevent the escape of packaging gases through the porous lid. This
may require some sample preparation, depending on the method of occlusion required,
BUT must be non-destructive and non-invasive. Vacuum decay in packages, which have
a porous barrier lid material, may include background noise from the gas, between the
lidding material and shielding surface, OR from lateral airflow through the porous
barrier material itself at the lid/tray's seal junction.
4.3 The sensitivity of the test depends on the design of the package under test, the
sensitivity of the sensor, the design of the test chamber, the design of the test system,
the critical test parameters of time and pressure. The choice of test system and leak test
parameters for any given product packaging system must be based on the contents of
the package (liquid/solid with large/small headspace gas) and the nature of the package
(soft or rigid, porous or nonporous). When the instrument has a more sensitive pressure
sensor AND the void volume in the test chamber is the smallest, the test system has the
potential to detect the smallest leak. Extended test times can detect smaller gas leaks.
Minimizing background noise pressure fluctuations also improves test sensitivity. For
packaging with a porous barrier lid material, occluder technology can minimize
background noise. For flexible packaging or semi-rigid packaging, the expansion of the
packaging can be limited to reduce noise, by rationally designing the test chamber.
Release of trapped gas or trapped water vapor, in the test system or between package
components under test, may also contribute to background noise. This noise can be
distinguished from an actual leak, by extending the test time, to allow the vacuum to
return to the initial level, OR by extending the equilibration time.
Note: See Appendix A for more information on "Leak test theory". Examples of experimental
methods and test instruments, which are used to obtain precision and bias data, are given in
Appendix C and summarized in Table C.1.
5 Significance and application
5.1 Leaks in medical device packaging may result in the ingress of unwanted gases
(most commonly oxygen), harmful microorganisms, or particulate contaminants.
Package leaks may manifest as defects in the package components themselves or in the
sealed joints between package components. Ensuring the consistency and integrity of
packaging is an essential capability for leak detection.
5.2 After initial setup and calibration, a test operation can be semi-automatic, fully
automatic or manual. This test method is capable of non-destructively detecting leaks,
that are not apparent. The test method does not require the introduction of any foreign
materials or substances, such as dye solutions or gases. However, it shall be noted that
the surface of all porous materials needs to be physically blocked during the test, to
prevent the gas from passing through the porous surface and causing the vacuum in the
test chamber to drop rapidly. Because this test method is only based on the detection of
pressure changes in the test chamber, which are affected by the leakage of gas or steam
from the challenge package.
5.3 This test is a useful research tool, for optimizing package sealing parameters and
for comparative evaluation of various packages and materials. Because of its rapidity,
non-invasiveness, non-destructiveness, this test method is also suitable for installation
on the production line, or for 100% online testing of products, or for statistical sampling
testing.
5.4 For the vacuum decay test, leak test results exceeding allowable limits may be
indicated by an acoustic or optical signal response (or both).
6 Instruments
6.1 Vacuum dec...
Share
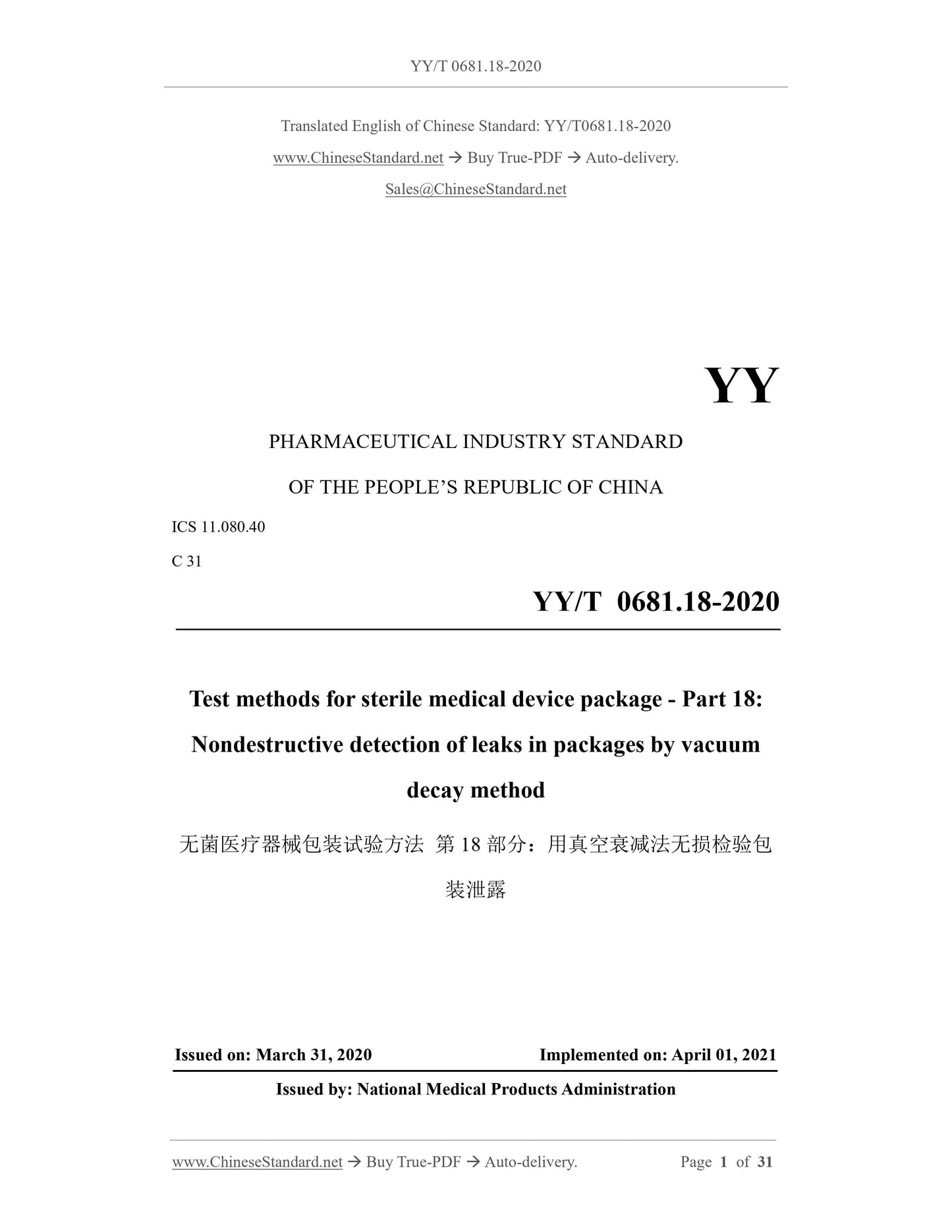
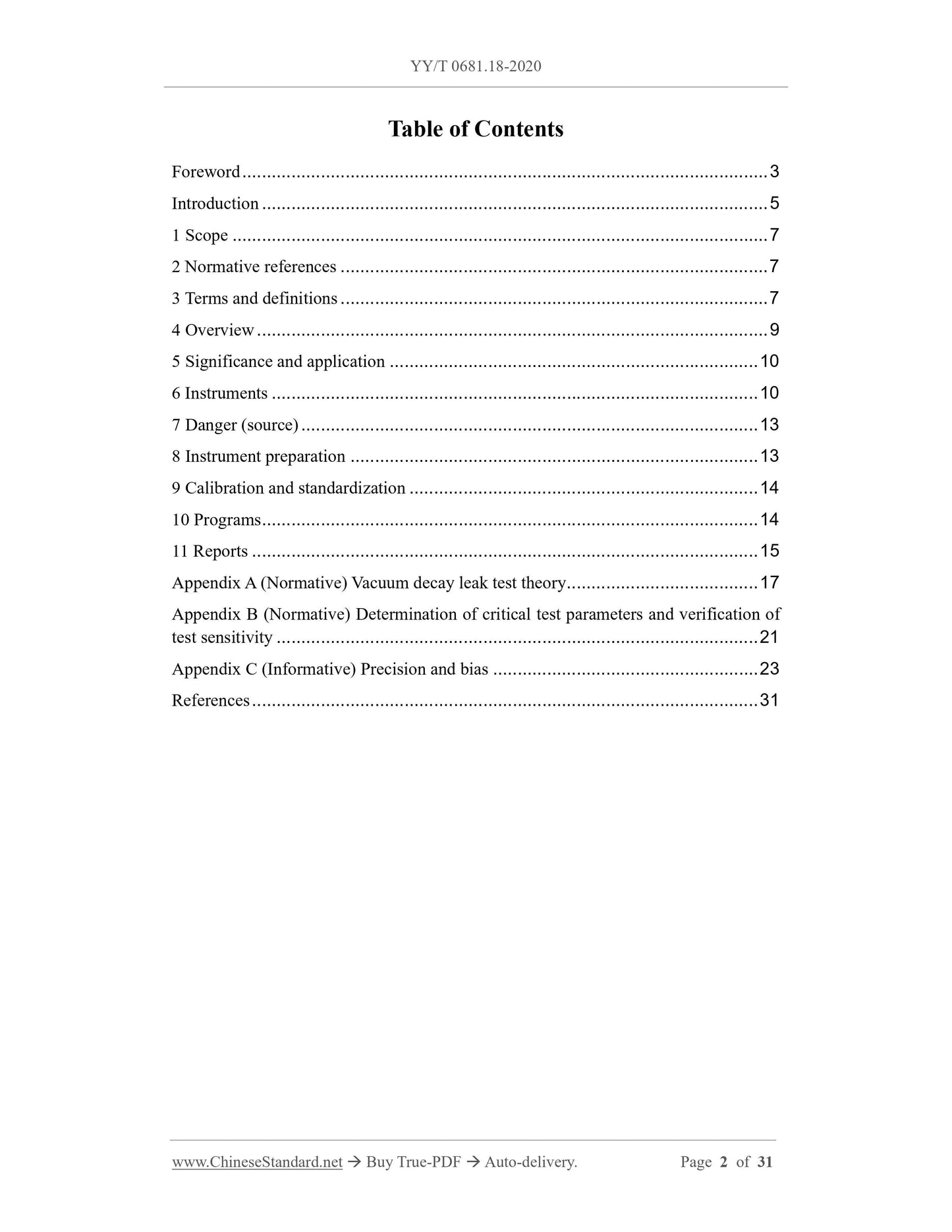
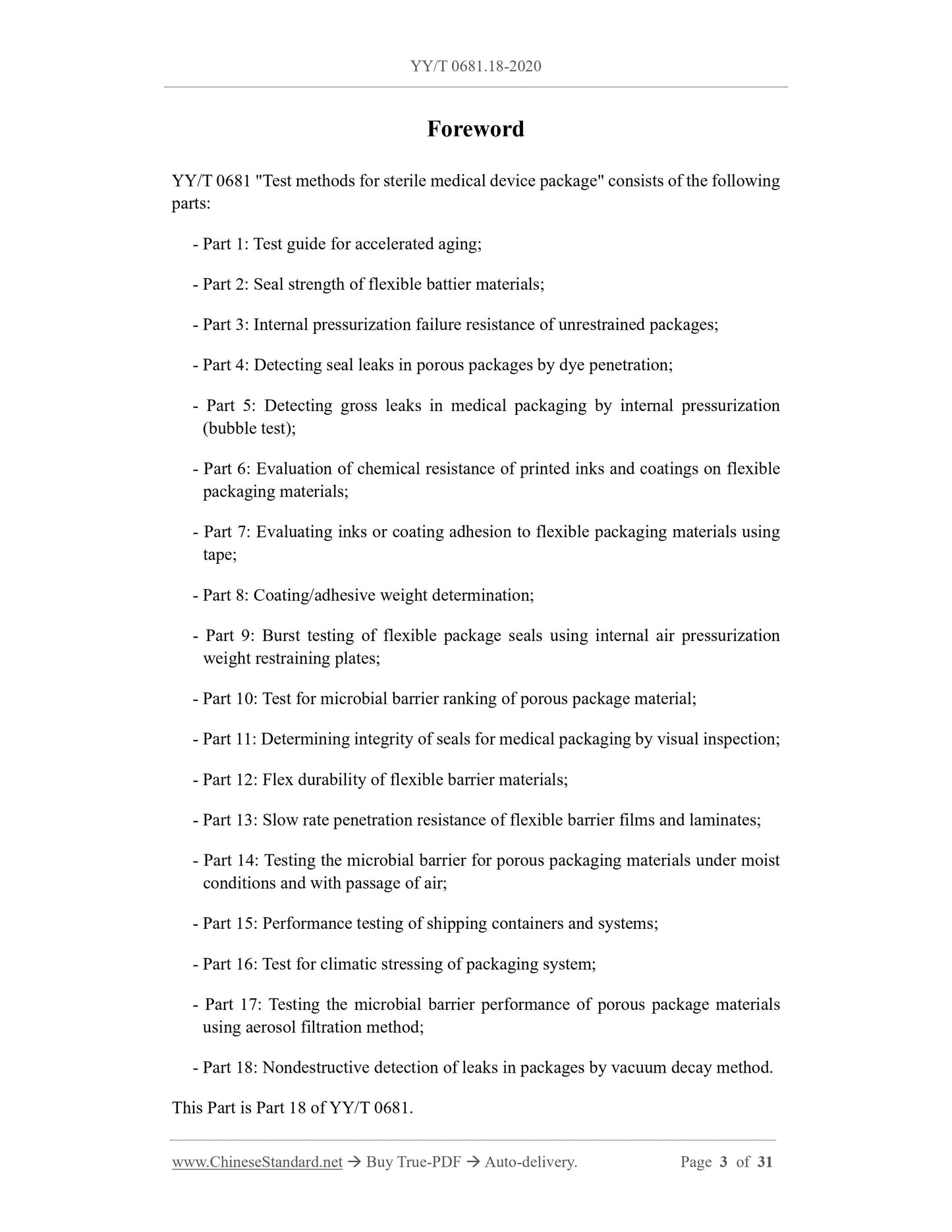
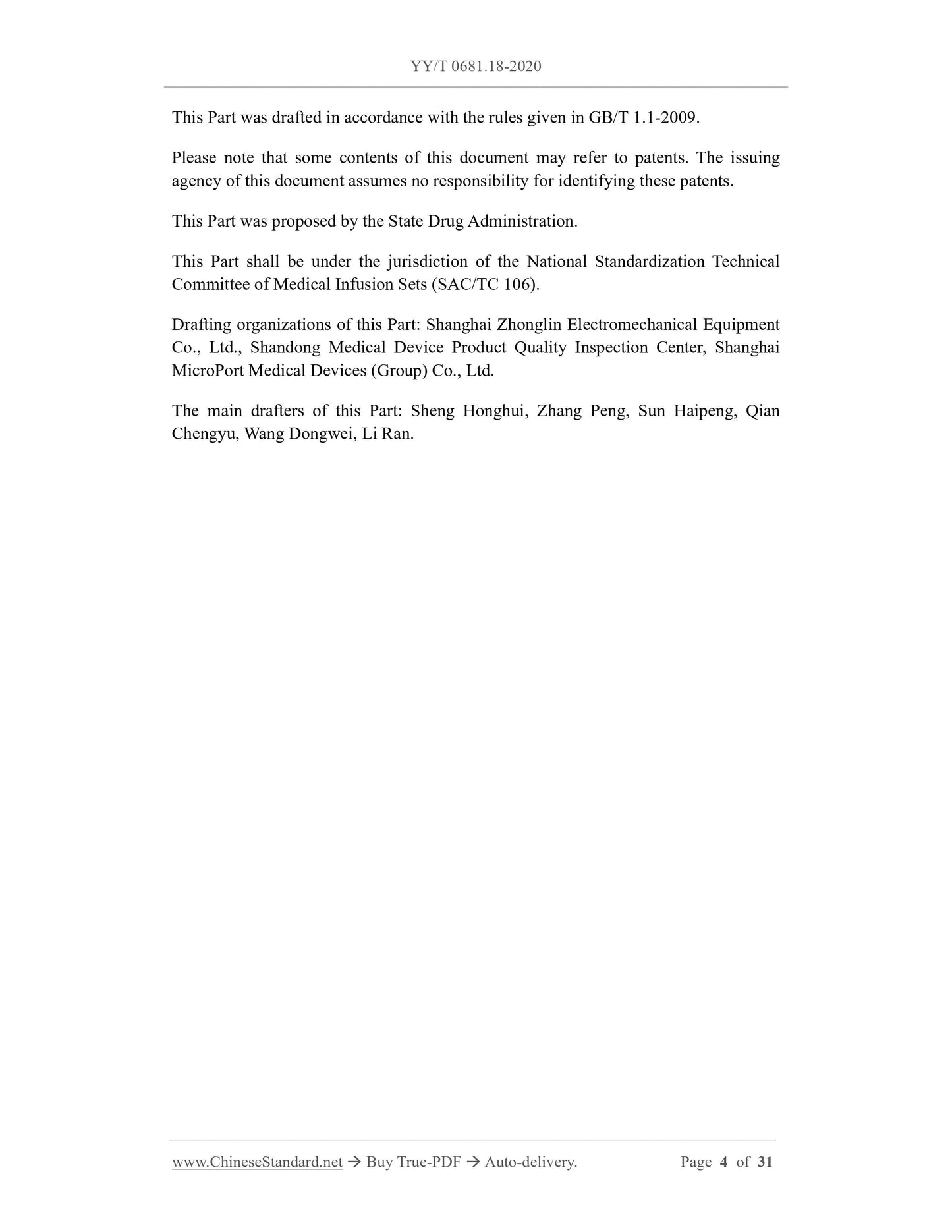
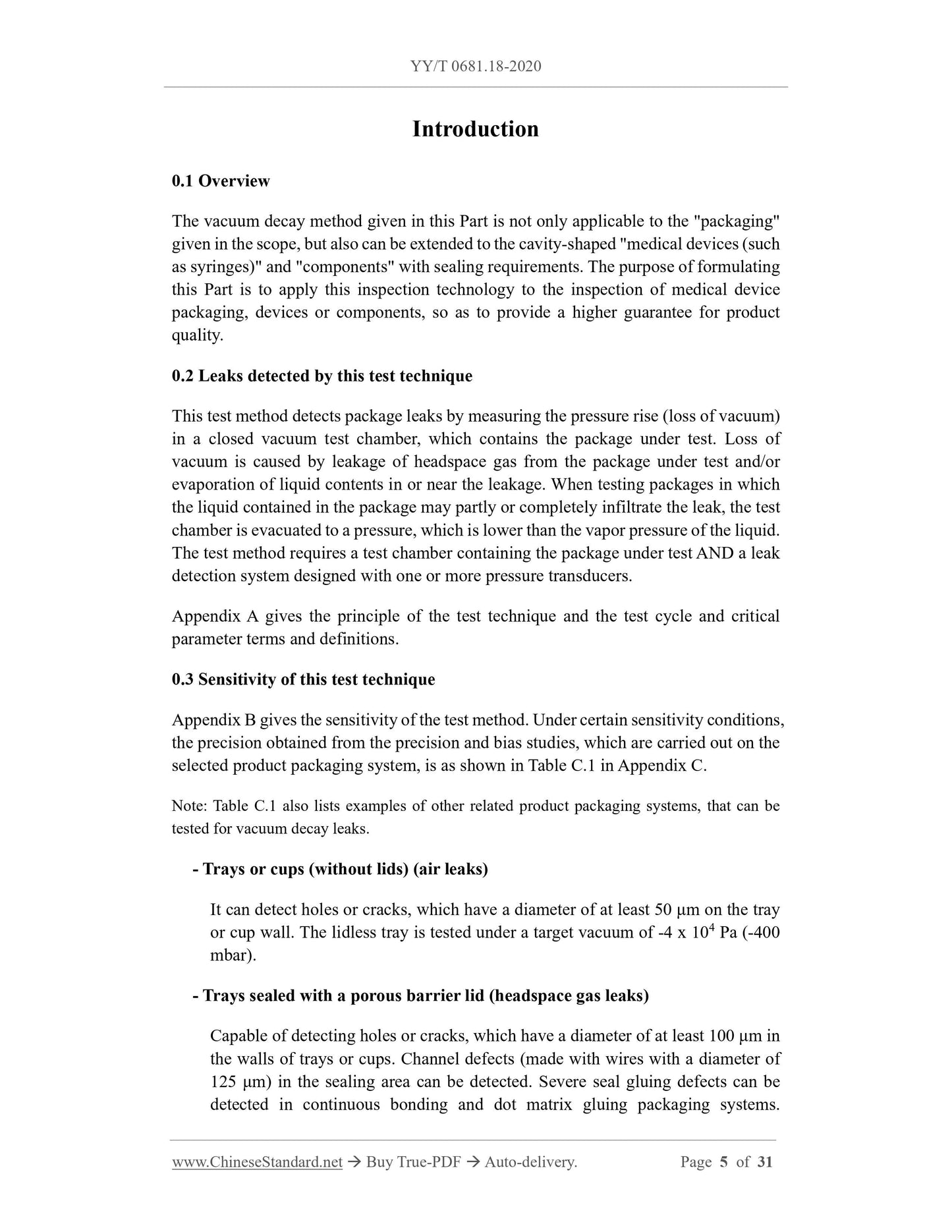
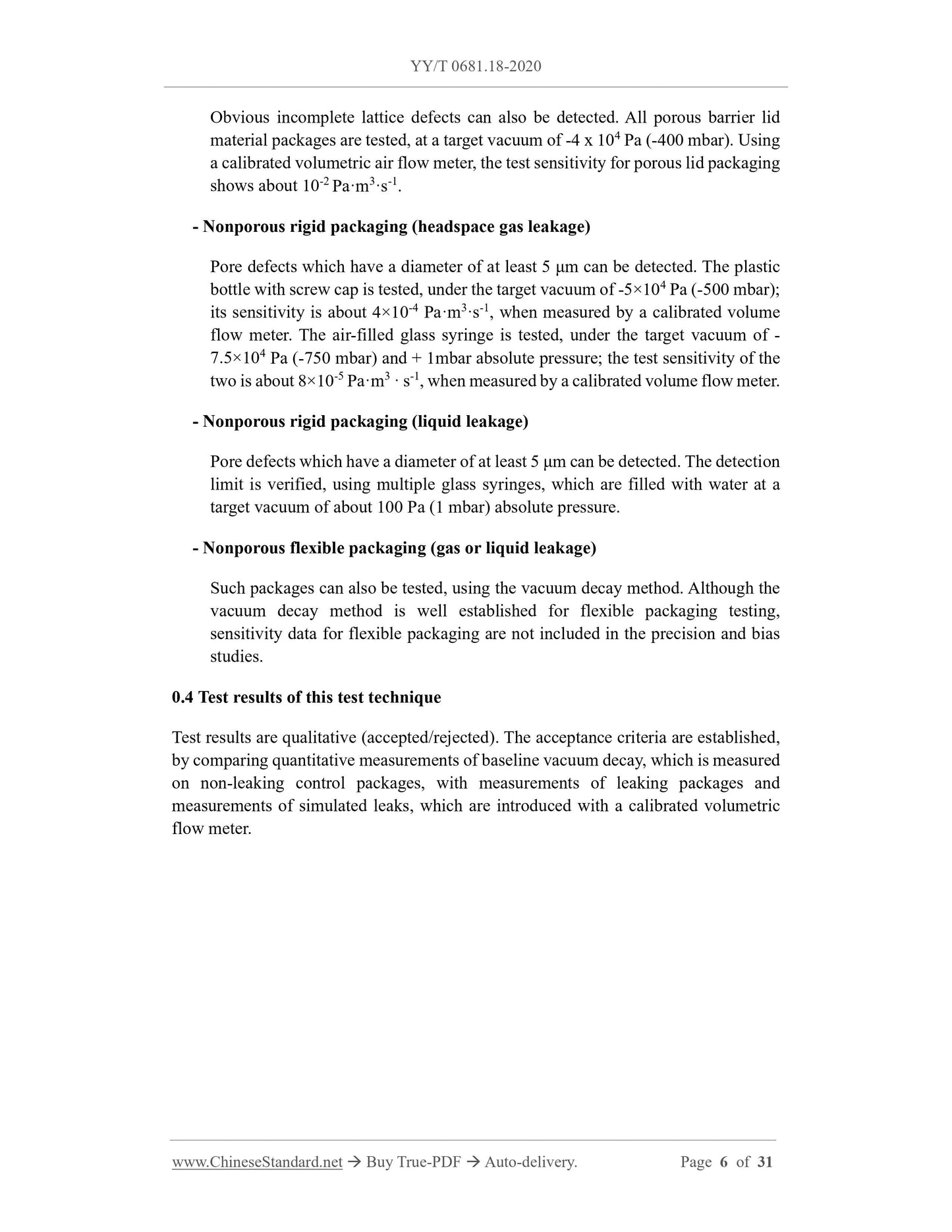
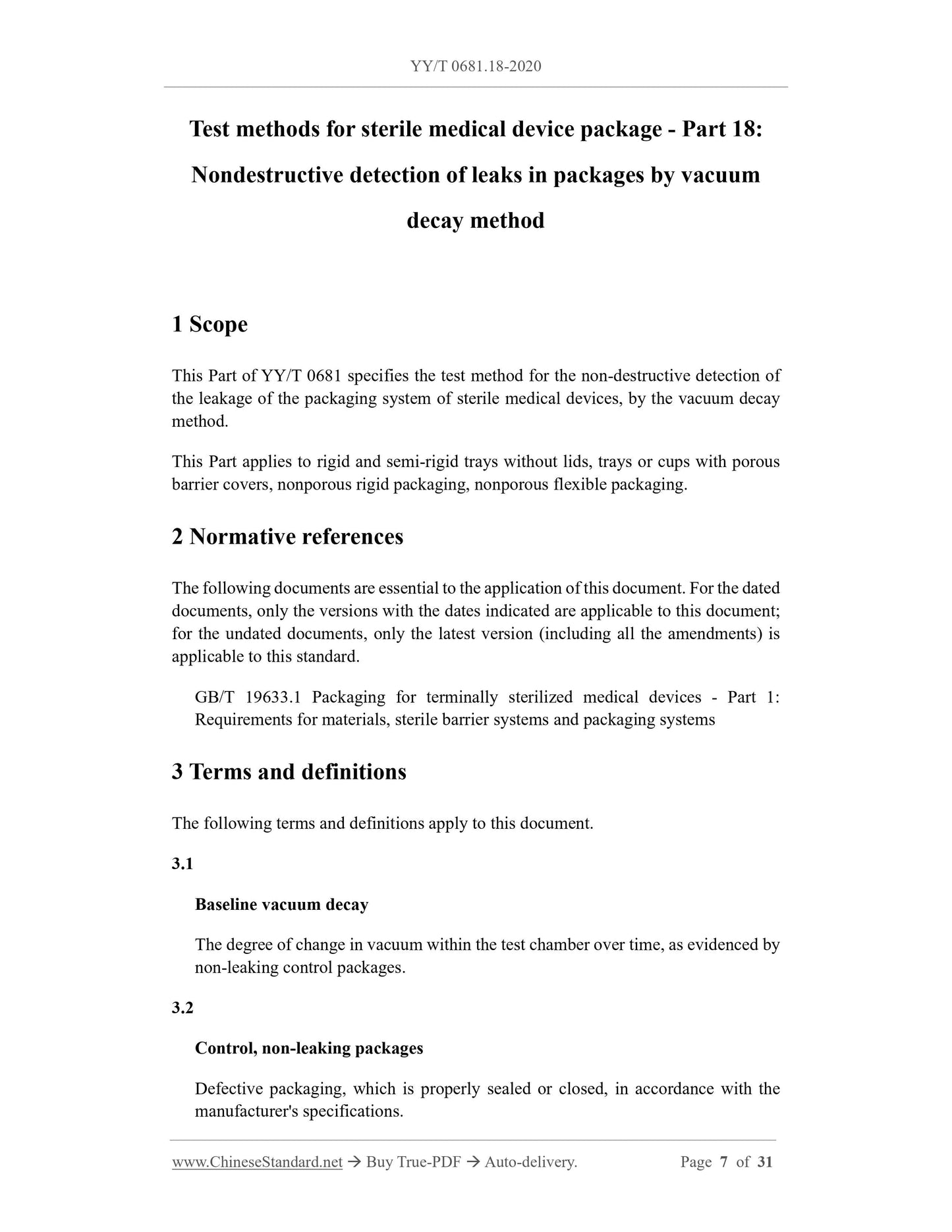

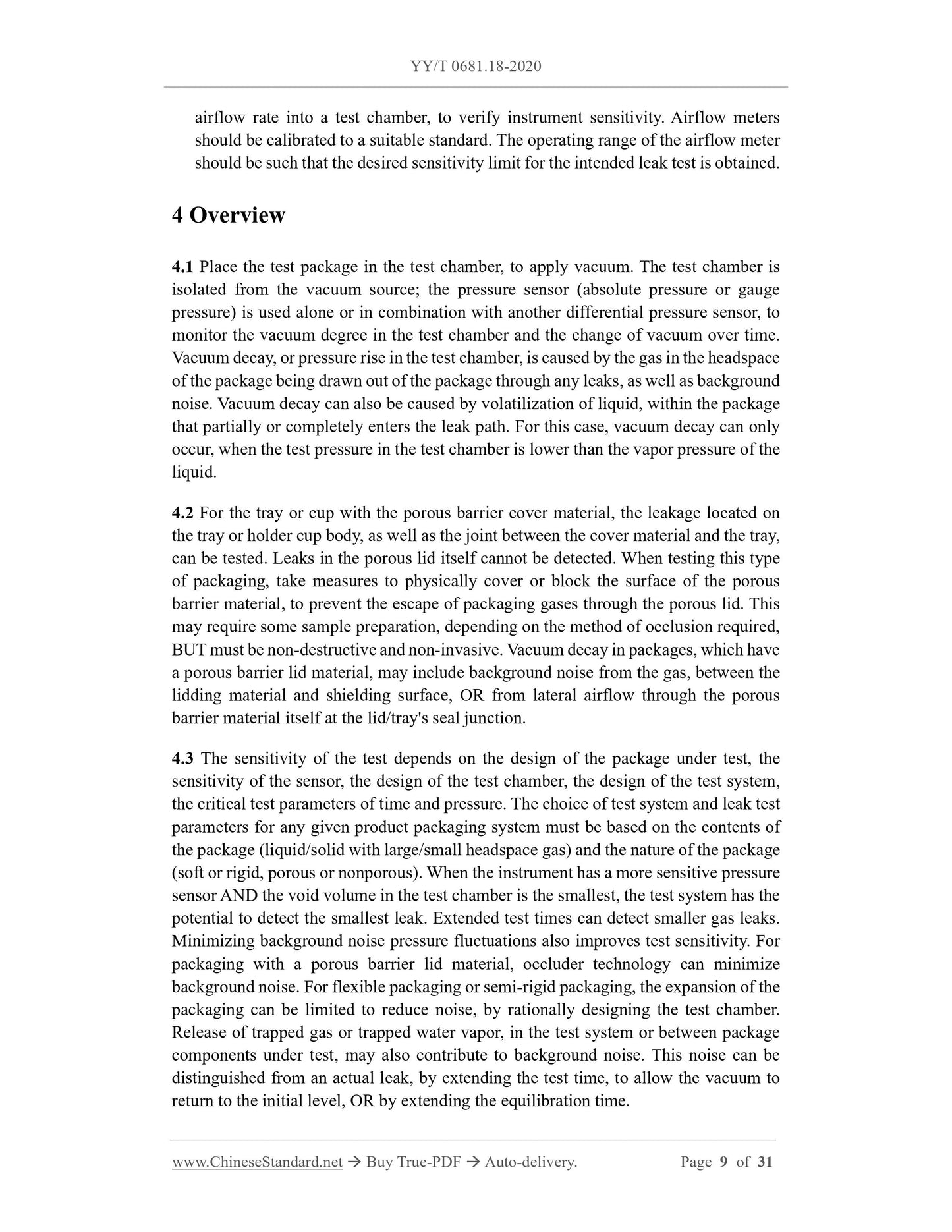
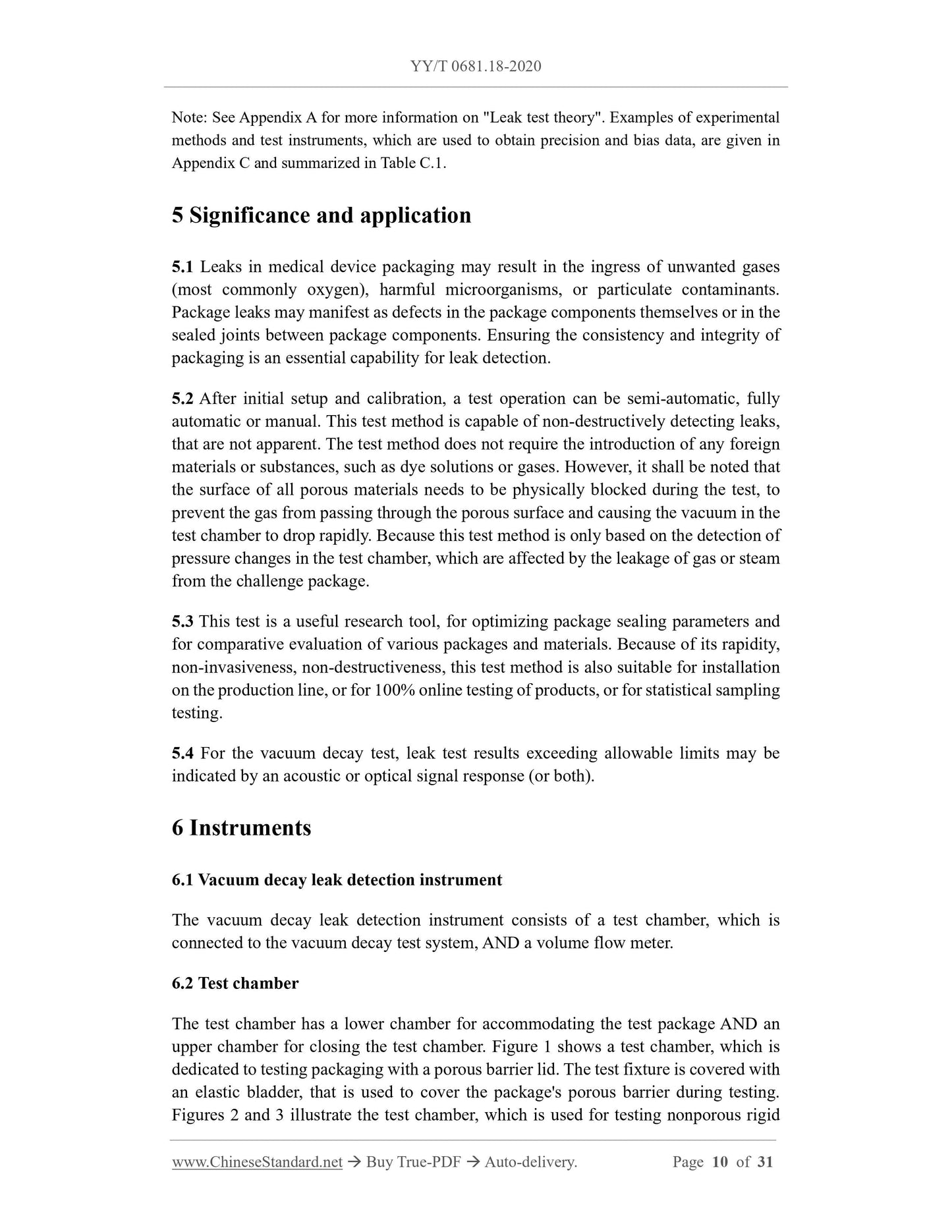
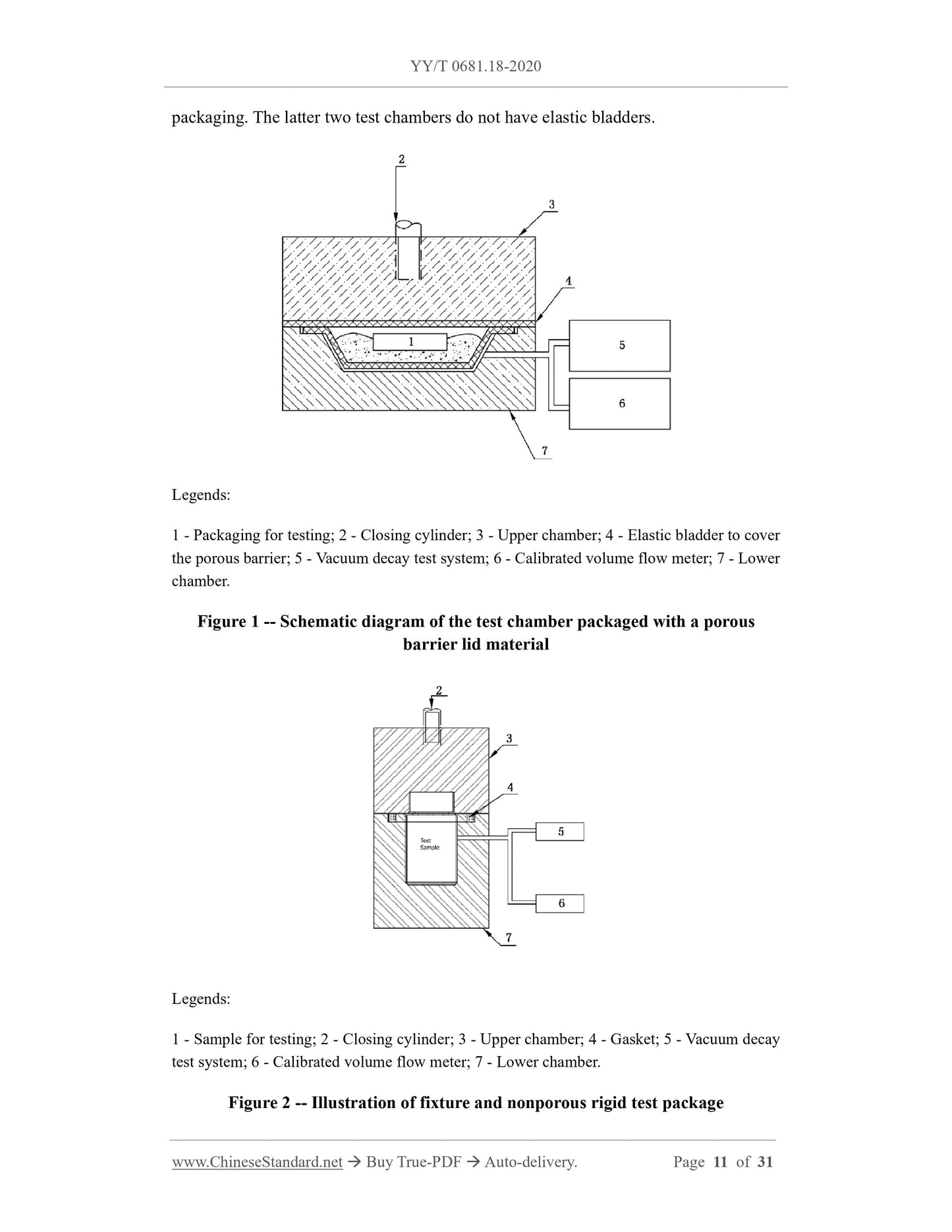
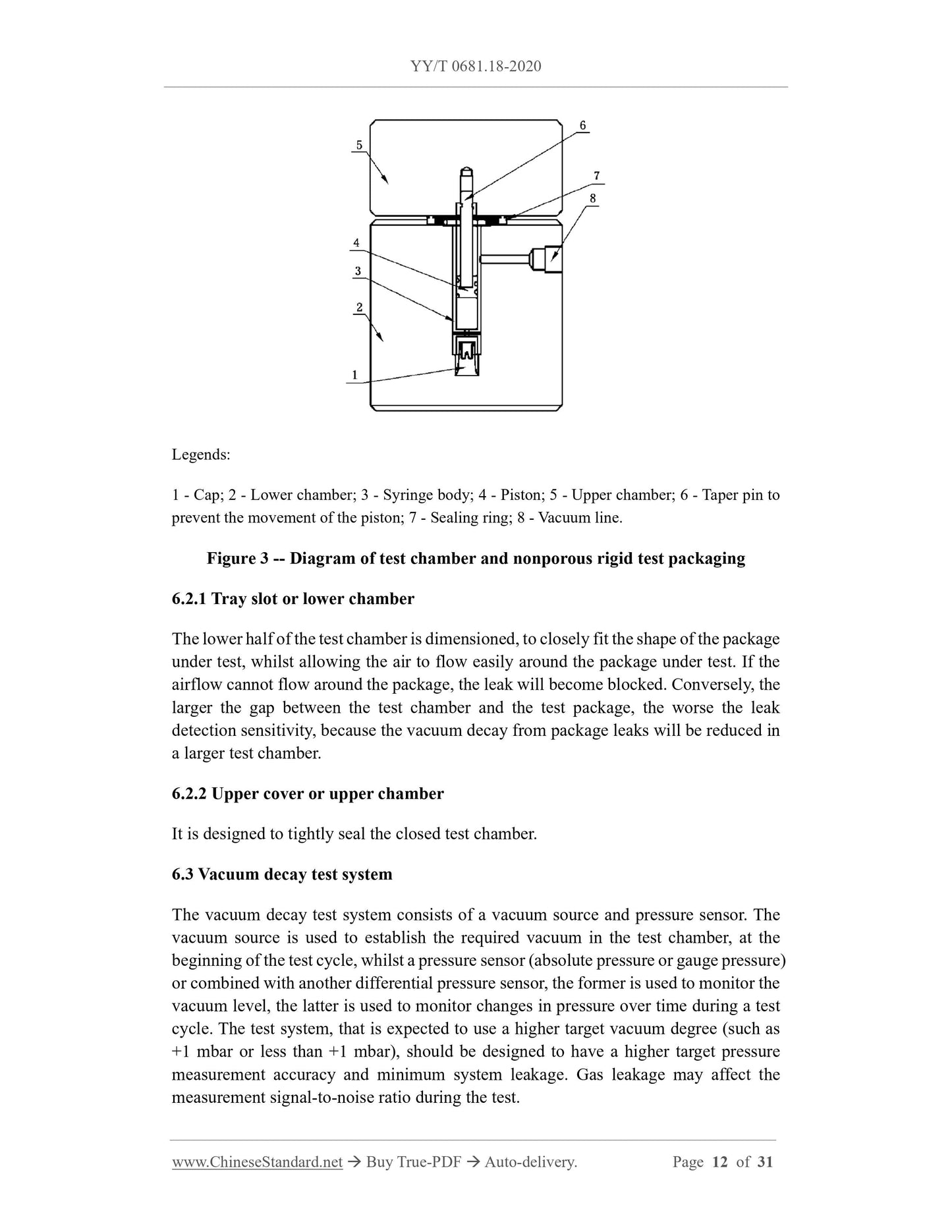