PayPal, credit cards. Download editable-PDF and invoice in 1 second!
GB/T 38023-2019 English PDF (GBT38023-2019)
GB/T 38023-2019 English PDF (GBT38023-2019)
Precio habitual
$95.00 USD
Precio habitual
Precio de oferta
$95.00 USD
Precio unitario
/
por
Los gastos de envío se calculan en la pantalla de pago.
No se pudo cargar la disponibilidad de retiro
Delivery: 3 seconds. Download true-PDF + Invoice.
Get QUOTATION in 1-minute: Click GB/T 38023-2019
Historical versions: GB/T 38023-2019
Preview True-PDF (Reload/Scroll if blank)
GB/T 38023-2019: Finishing requirements for parts and assemblies of the mechanical watch movements
GB/T 38023-2019
GB
NATIONAL STANDARD OF THE
PEOPLE’S REPUBLIC OF CHINA
ICS 39.040.10
Y 11
Finishing requirements for parts and assemblies of
the mechanical watch movements
ISSUED ON: AUGUST 30, 2019
IMPLEMENTED ON: MARCH 01, 2020
Issued by: State Administration for Market Regulation;
Standardization Administration of the People’s Republic of
China.
Table of Contents
Foreword ... 3
1 Scope ... 4
2 Normative references ... 4
3 Requirements ... 4
4 Inspection method ... 6
Finishing requirements for parts and assemblies of
the mechanical watch movements
1 Scope
This Standard specifies the requirements and inspection methods for parts and
assemblies of the mechanical watch movements.
This Standard applies to parts and assemblies of the mechanical watch
movements that have undergone finishing processing (hereinafter referred to
as "parts and assemblies").
2 Normative references
The following documents are indispensable for the application of this document.
For dated references, only the dated version applies to this document. For
undated references, the latest edition (including all amendments) applies to this
document.
GB/T 10610, Geometrical product specifications (GPS) - Surface texture:
Profile method - Rules and procedures for the assessment of surface texture
3 Requirements
3.1 Surface quality requirements of metal parts and assemblies
Metal parts and assemblies shall not have surface defects, such as indentation,
pits, scratches, burn marks, local highlights after polishing, and spots and
blisters after electroplating. The surface color of all parts and assemblies shall
be uniform and coordinated.
3.2 Finishing requirements for metal parts and assemblies
3.2.1 General
Mirror polishing for finishing of metal parts and assemblies means that the
surface roughness Ra value shall not be greater than 0.05 μm; polishing means
that the surface roughness Ra value shall not be greater than 0.2 μm.
As long as the finishing process meets the surface roughness requirements,
there is no limit for the processing method.
3.2.2 Gear train parts
3.2.5.3 The gem hole of the splint shall be chamfered and polished.
3.2.6 Automatic parts
3.2.6.1 The gear train and splint parts in the automatic train shall meet the
requirements in 3.2.2 and 3.2.5 respectively.
3.2.6.2 The surface of the automatic hammer shall be flat; the upper and lower
planes shall be eliminated from irregular processing patterns; the outer circle of
the hammer edge shall be chamfered and polished; the upper plane and
chamfers can be processed by ray grinding or sandblasting.
3.2.6.3 The exposed upper surface of the bearing of the automatic hammer
shall be polished.
3.2.7 Screw
3.2.7.1 The upper plane of the screw cap shall be mirror polished; the outer
circle of the screw cap shall be chamfered and polished.
3.2.7.2 The end face of the screw thread shall be flat.
3.2.8 Printing plate
3.2.8.1 The printing on the printing plate (such as calendar ring, weekly
calendar plate, moon phase plate) shall be clear, full and fast. There shall be
no broken lines, uneven thickness, and obvious shortage of fonts and numbers.
There shall be no defects such as brushed fonts, deformation, and white spots.
3.2.8.2 The spray paint color of the dial shall be uniform; the paint surface shall
be smooth and even. There shall be no discoloration, yellowing, peeling,
fingerprints, sticky silk, paint residue or other debris.
3.2.9 Additional mechanism parts
3.2.9.1 The gear train and splint parts in the additional mechanism shall meet
the requirements in 3.2.2 and 3.2.5 respectively.
3.2.9.2 The upper surface of rod-type parts shall be polished; the surface shall
be smooth and the contour lines shall be smooth.
4 Inspection method
4.1 Inspection conditions
Except for special requirements, the ambient temperature for inspection is
18 °C ~ 25 °C; during the entire inspection process, the temperature fluctuation
is not more than 2 °C; the relative humidity is not more than 70%.
Get QUOTATION in 1-minute: Click GB/T 38023-2019
Historical versions: GB/T 38023-2019
Preview True-PDF (Reload/Scroll if blank)
GB/T 38023-2019: Finishing requirements for parts and assemblies of the mechanical watch movements
GB/T 38023-2019
GB
NATIONAL STANDARD OF THE
PEOPLE’S REPUBLIC OF CHINA
ICS 39.040.10
Y 11
Finishing requirements for parts and assemblies of
the mechanical watch movements
ISSUED ON: AUGUST 30, 2019
IMPLEMENTED ON: MARCH 01, 2020
Issued by: State Administration for Market Regulation;
Standardization Administration of the People’s Republic of
China.
Table of Contents
Foreword ... 3
1 Scope ... 4
2 Normative references ... 4
3 Requirements ... 4
4 Inspection method ... 6
Finishing requirements for parts and assemblies of
the mechanical watch movements
1 Scope
This Standard specifies the requirements and inspection methods for parts and
assemblies of the mechanical watch movements.
This Standard applies to parts and assemblies of the mechanical watch
movements that have undergone finishing processing (hereinafter referred to
as "parts and assemblies").
2 Normative references
The following documents are indispensable for the application of this document.
For dated references, only the dated version applies to this document. For
undated references, the latest edition (including all amendments) applies to this
document.
GB/T 10610, Geometrical product specifications (GPS) - Surface texture:
Profile method - Rules and procedures for the assessment of surface texture
3 Requirements
3.1 Surface quality requirements of metal parts and assemblies
Metal parts and assemblies shall not have surface defects, such as indentation,
pits, scratches, burn marks, local highlights after polishing, and spots and
blisters after electroplating. The surface color of all parts and assemblies shall
be uniform and coordinated.
3.2 Finishing requirements for metal parts and assemblies
3.2.1 General
Mirror polishing for finishing of metal parts and assemblies means that the
surface roughness Ra value shall not be greater than 0.05 μm; polishing means
that the surface roughness Ra value shall not be greater than 0.2 μm.
As long as the finishing process meets the surface roughness requirements,
there is no limit for the processing method.
3.2.2 Gear train parts
3.2.5.3 The gem hole of the splint shall be chamfered and polished.
3.2.6 Automatic parts
3.2.6.1 The gear train and splint parts in the automatic train shall meet the
requirements in 3.2.2 and 3.2.5 respectively.
3.2.6.2 The surface of the automatic hammer shall be flat; the upper and lower
planes shall be eliminated from irregular processing patterns; the outer circle of
the hammer edge shall be chamfered and polished; the upper plane and
chamfers can be processed by ray grinding or sandblasting.
3.2.6.3 The exposed upper surface of the bearing of the automatic hammer
shall be polished.
3.2.7 Screw
3.2.7.1 The upper plane of the screw cap shall be mirror polished; the outer
circle of the screw cap shall be chamfered and polished.
3.2.7.2 The end face of the screw thread shall be flat.
3.2.8 Printing plate
3.2.8.1 The printing on the printing plate (such as calendar ring, weekly
calendar plate, moon phase plate) shall be clear, full and fast. There shall be
no broken lines, uneven thickness, and obvious shortage of fonts and numbers.
There shall be no defects such as brushed fonts, deformation, and white spots.
3.2.8.2 The spray paint color of the dial shall be uniform; the paint surface shall
be smooth and even. There shall be no discoloration, yellowing, peeling,
fingerprints, sticky silk, paint residue or other debris.
3.2.9 Additional mechanism parts
3.2.9.1 The gear train and splint parts in the additional mechanism shall meet
the requirements in 3.2.2 and 3.2.5 respectively.
3.2.9.2 The upper surface of rod-type parts shall be polished; the surface shall
be smooth and the contour lines shall be smooth.
4 Inspection method
4.1 Inspection conditions
Except for special requirements, the ambient temperature for inspection is
18 °C ~ 25 °C; during the entire inspection process, the temperature fluctuation
is not more than 2 °C; the relative humidity is not more than 70%.
Share
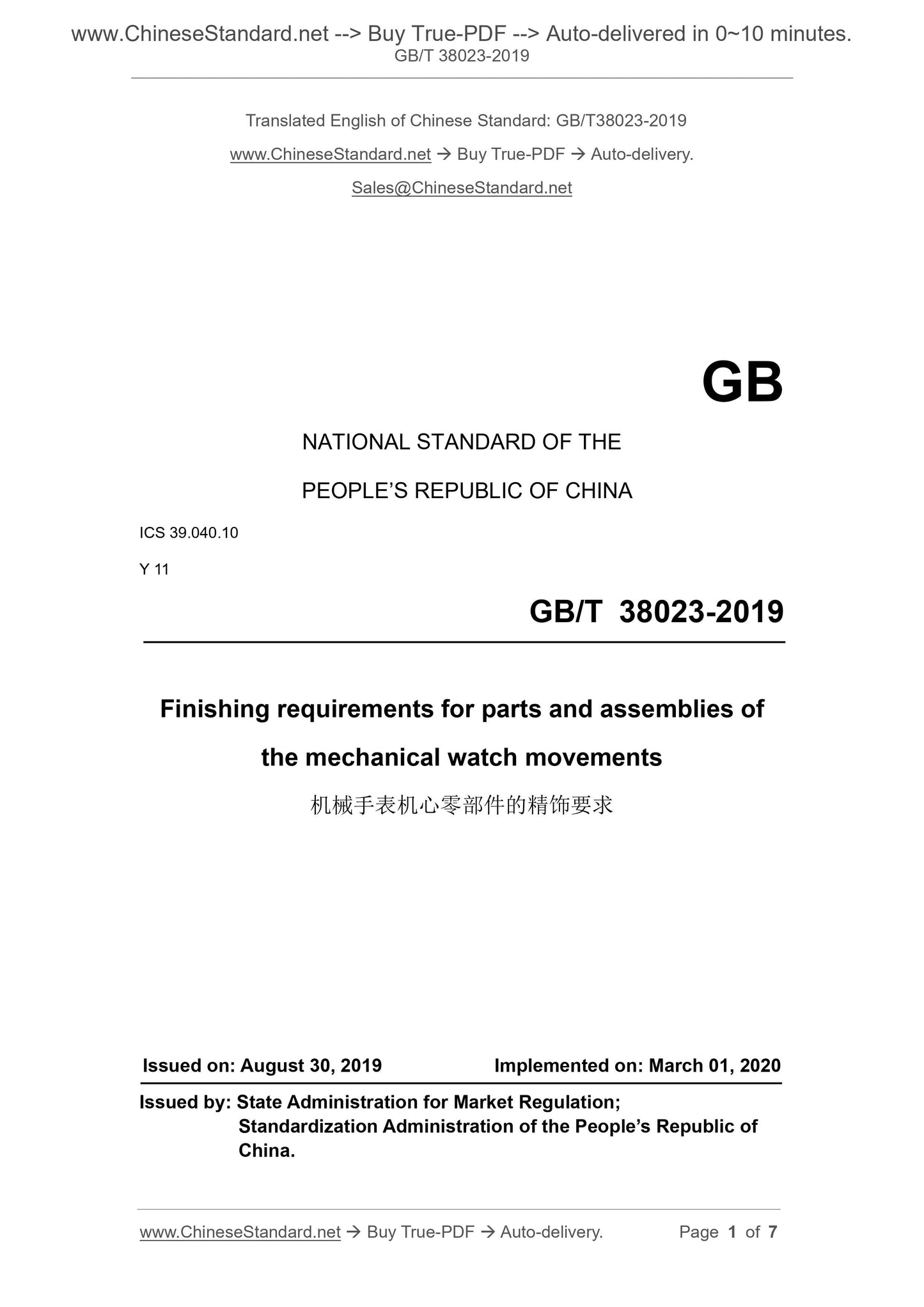
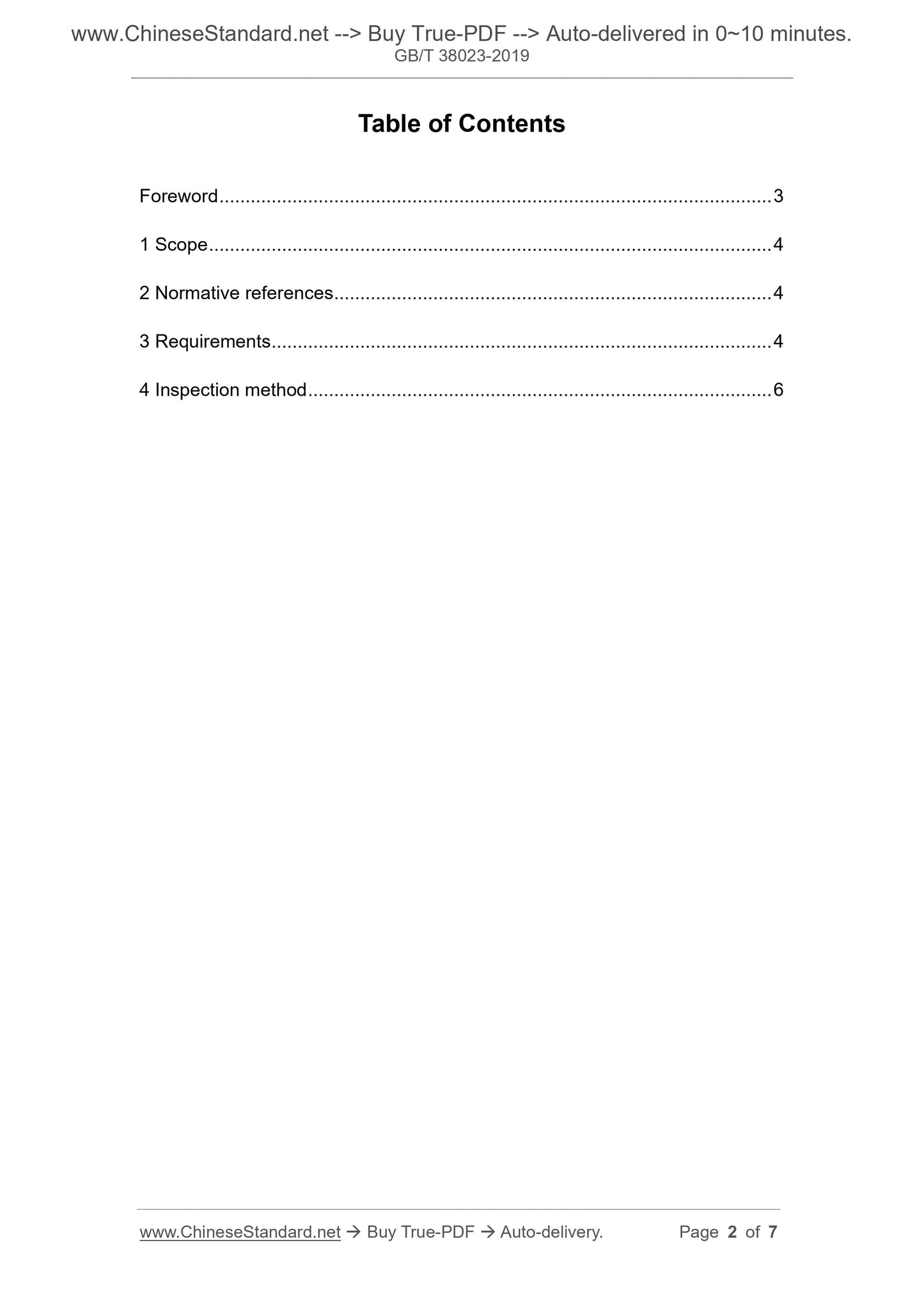
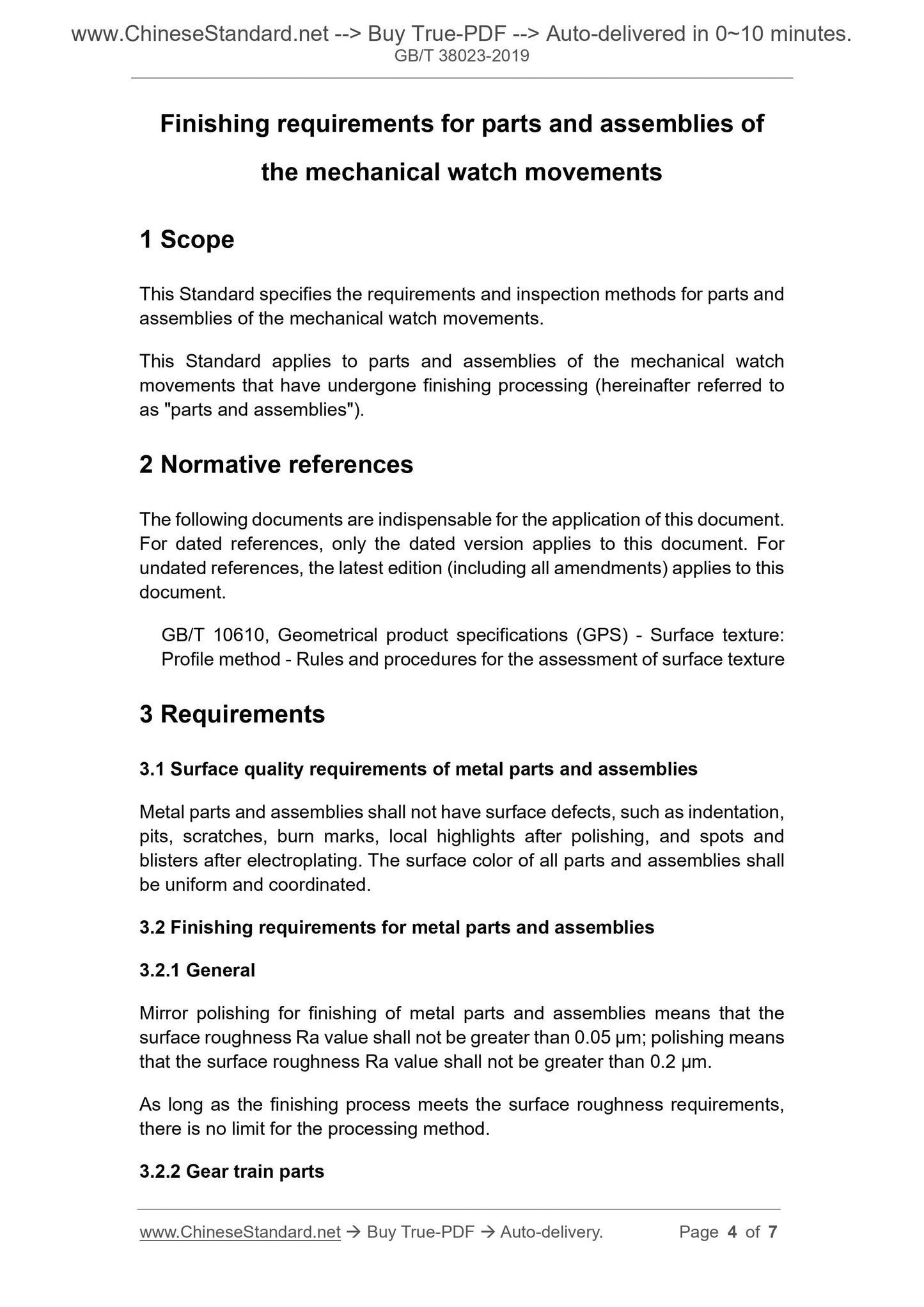
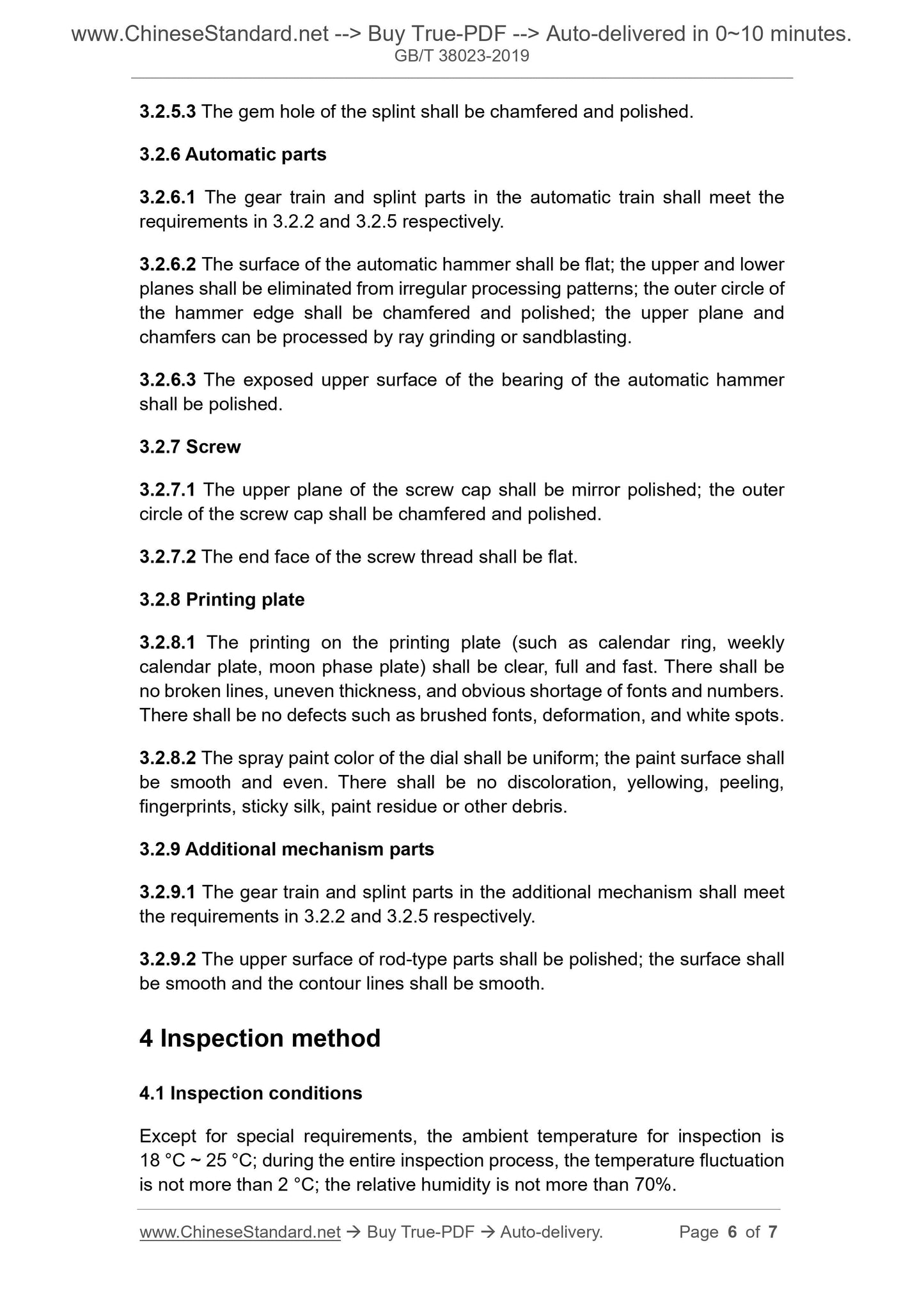