1
/
de
9
PayPal, credit cards. Download editable-PDF and invoice in 1 second!
NB/SH/T 0944.1-2017 English PDF (NB/SH/T0944.1-2017)
NB/SH/T 0944.1-2017 English PDF (NB/SH/T0944.1-2017)
Prix habituel
$220.00 USD
Prix habituel
Prix promotionnel
$220.00 USD
Prix unitaire
/
par
Frais d'expédition calculés à l'étape de paiement.
Impossible de charger la disponibilité du service de retrait
Delivery: 3 seconds. Download true-PDF + Invoice.
Get QUOTATION in 1-minute: Click NB/SH/T 0944.1-2017
Historical versions: NB/SH/T 0944.1-2017
Preview True-PDF (Reload/Scroll if blank)
NB/SH/T 0944.1-2017: Standard test method for wear preventive characteristics of lubricating fluid. FE8 rolling bearing method. Part 1: Lubricating oil
NB/SH/T 0944.1-2017
PETROCHEMICAL INDUSTRY STANDARD
ICS 75.100
E 34
Standard test method for wear preventive characteristics of
lubricating fluid - FE8 rolling bearing method - Part 1.
Lubricating oil
润滑油
ISSUED ON. DECEMBER 27, 2017
IMPLEMENTED ON. JUNE 01, 2018
Issued by. National Energy Administration
Table of Contents
Foreword... 3
1 Scope... 4
2 Normative references... 4
3 Terms and definitions... 4
4 Method overview... 7
5 Test equipment... 7
6 Reagents and materials... 10
7 Preparation of test bearings... 10
8 Test steps... 10
9 Report of results... 13
10 Precision... 14
Appendix A (Normative) Safety measures and precautions... 15
Appendix B (Normative) Maintenance and repair... 16
Standard test method for wear preventive characteristics of
lubricating fluid - FE8 rolling bearing method - Part 1.
Lubricating oil
WARNING. The application of this Part may involve certain hazardous materials,
operations, equipment. But not all safety issues related to this are advised. It is the
user's responsibility to formulate appropriate safety and protection measures,
meanwhile determine the applicability of relevant regulatory restrictions, before
using this Part (see Appendix A for details).
1 Scope
This Part specifies the test method for determining the wear preventive performance of
lubricating oil, by the use of thrust cylindrical rolling bearings, on the FE8 bearing wear
testing machine.
This Part applies to the evaluation of bearing's wear preventive performance of
lubricating oils, under mixed friction conditions.
2 Normative references
The following documents are essential to the application of this document. For the dated
documents, only the versions with the dates indicated are applicable to this document;
for the undated documents, only the latest version (including all the amendments) is
applicable to this standard.
GB 1922-2006 Petroleum solvents for paints and cleaning
GB/T 6391 Rolling bearings - Dynamic load ratings and rating life
GB/T 17754-2012 Tribology terminology
DIN 722 Rolling bearings - Single direction thrust cylindrical roller bearings
3 Terms and definitions
The following terms and definitions apply to this document.
3.1
3.8
Cage wear
The wear amount of the bearing cage, during the loading time, expressed in mk.
3.9
Test speed
The rotational speed of the test bearing, expressed by n.
3.10
Axial bearing load
The axial load, which is applied to the test bearing, expressed by Fa.
3.11
Test temperature
The temperature (T), which is measured at the position of the outer ring spring
assembly of the test bearing, during the test.
Note. Due to the high heat loss at the drive end of the test bearing, the temperature, which
is measured here may be 2 °C ~ 5 °C lower.
3.12
Operating temperature
Test temperature (Tb), at the end of the running-in time.
3.13
Running-in time
The time, from the start of the test to the establishment of a steady state.
Note. During the running-in period, the grease is evenly distributed to the surface of each
test piece, with the rotation of the motor, meanwhile a certain amount of wear is generated.
Due to the mutual contact of the bearing test pieces on the working surface, the working
surface gradually tends to be smooth, resulting in an increase in the ratio, between the
thickness of the lubricating film and the roughness of the contact surface, so does the
isolation effect of the lubricating film. The reduction in sliding friction, which is caused by
this smoothing action, results in a downward trend in friction torque, during the running-in.
During the loading time, wear also generally decreases.
3.14
Wear
The phenomenon and process of surface deformation, damage or gradual loss of
surface material, due to friction.
[GB/T 17754-2012, definition 2.3]
3.15
Wear loss
The amount of deformation of the material contact surface of the friction pair OR
loss of surface material, during wear.
[GB/T 17754-2012, definition 5.1]
4 Method overview
4.1 When using the FE8 bearing wear testing machine for the lubricating oil test, first
install two test bearings on the testing machine. Apply a certain amount of test oil into
the lubricating oil circulation system. Through the lubricating oil circulation system, it
supplies oil, at a rate of 0.1 L/min ± 0.02 L/min, to each test bearing. The test is carried
out, under the specified conditions (motor speed 7.5 r/min, axial load 80 kN, test
temperature 80 °C). Weigh the mass of each component of the test bearing, before and
after the test. The wear performance of the lubricant is evaluated, by the wear mass loss.
4.2 During the test, when the friction torque of the bearing continuously exceeds 60
N·m for more than 10 s, due to poor lubrication, OR the continuous running time
reaches 80 h, the test ends. After the test, weigh the bearing components and calculate
the wear loss (mg). Each lubricating oil sample is tested twice; the wear performance
of the lubricating oil is evaluated by the wear loss of the bearing components.
5 Test equipment
5.1 FE8 testing machine
5.1.1 The test equipment adopts FE8 bearing wear testing machine, which consists of
test head, drive unit, control system. The test head (see Figure 1) is detachably
connected to the drive unit, through the cone seat of the test head shaft (7). The drive
shaft (1) of the drive unit is installed in two auxiliary bearings (2), which is driven
directly by a motor (not shown in the Figure), at different speeds in the range of 7.5
r/min ~ 3000 r/min, OR through gear meshing. The test bearing (3) is installed in the
test head. A certain axial load is applied, through the butterfly spring assembly (4).
5.4.4 Brush. The size shall be suitable for the cleaning of the test bearing.
5.4.5 Special rag. No lint or fibers falling off, during the process of use.
5.4.6 Balance. It is used to weigh the test piece. The recommended weighing range is 0
kg ~ 2 kg; the division value is 1 mg.
5.4.7 Demagnetizer. It is used for demagnetization, after the test piece is magnetized.
The power-on continuity rate is 60%; the power is 100 W; the voltage is 220 V.
6 Reagents and materials
Cleaning solvent. The solvent oil for cleaning meets the requirements of No.2 solvent
oil in GB 1922-2006.
Warning. It is flammable material, whose volatile gases are harmful. It shall keep
away from fire, sparks, open flames; avoid prolonged or frequent skin exposure.
7 Preparation of test bearings
7.1 Take the roller of the test bearing out of the cage. Put it into the cleaning cup. Use
a brush, which is dipped in cleaning solvent, to clean it. In the same way, clean the
bearing's outer ring, bearing's inner ring, bearing cage, etc. Place the cleaned bearing
parts in a drying oven, which was preheated to 80 °C, for 30 minutes. Place the dried
bearing parts in a clean container, to naturally dry it to room temperature. Protective
gloves shall be used, when doing the above.
7.2 Use balance to weigh the mass of the roller and the cage. Record it, accurate to 1
mg. Install the rollers into the cage housing, at room temperature. Before installation,
use cleaning solvent and special cloth, to clean the installation tool. Check for free
movement of the temperature sensor and friction torque measurement connections.
Before starting the test run, calibrate the friction sensor.
8 Test steps
Get QUOTATION in 1-minute: Click NB/SH/T 0944.1-2017
Historical versions: NB/SH/T 0944.1-2017
Preview True-PDF (Reload/Scroll if blank)
NB/SH/T 0944.1-2017: Standard test method for wear preventive characteristics of lubricating fluid. FE8 rolling bearing method. Part 1: Lubricating oil
NB/SH/T 0944.1-2017
PETROCHEMICAL INDUSTRY STANDARD
ICS 75.100
E 34
Standard test method for wear preventive characteristics of
lubricating fluid - FE8 rolling bearing method - Part 1.
Lubricating oil
润滑油
ISSUED ON. DECEMBER 27, 2017
IMPLEMENTED ON. JUNE 01, 2018
Issued by. National Energy Administration
Table of Contents
Foreword... 3
1 Scope... 4
2 Normative references... 4
3 Terms and definitions... 4
4 Method overview... 7
5 Test equipment... 7
6 Reagents and materials... 10
7 Preparation of test bearings... 10
8 Test steps... 10
9 Report of results... 13
10 Precision... 14
Appendix A (Normative) Safety measures and precautions... 15
Appendix B (Normative) Maintenance and repair... 16
Standard test method for wear preventive characteristics of
lubricating fluid - FE8 rolling bearing method - Part 1.
Lubricating oil
WARNING. The application of this Part may involve certain hazardous materials,
operations, equipment. But not all safety issues related to this are advised. It is the
user's responsibility to formulate appropriate safety and protection measures,
meanwhile determine the applicability of relevant regulatory restrictions, before
using this Part (see Appendix A for details).
1 Scope
This Part specifies the test method for determining the wear preventive performance of
lubricating oil, by the use of thrust cylindrical rolling bearings, on the FE8 bearing wear
testing machine.
This Part applies to the evaluation of bearing's wear preventive performance of
lubricating oils, under mixed friction conditions.
2 Normative references
The following documents are essential to the application of this document. For the dated
documents, only the versions with the dates indicated are applicable to this document;
for the undated documents, only the latest version (including all the amendments) is
applicable to this standard.
GB 1922-2006 Petroleum solvents for paints and cleaning
GB/T 6391 Rolling bearings - Dynamic load ratings and rating life
GB/T 17754-2012 Tribology terminology
DIN 722 Rolling bearings - Single direction thrust cylindrical roller bearings
3 Terms and definitions
The following terms and definitions apply to this document.
3.1
3.8
Cage wear
The wear amount of the bearing cage, during the loading time, expressed in mk.
3.9
Test speed
The rotational speed of the test bearing, expressed by n.
3.10
Axial bearing load
The axial load, which is applied to the test bearing, expressed by Fa.
3.11
Test temperature
The temperature (T), which is measured at the position of the outer ring spring
assembly of the test bearing, during the test.
Note. Due to the high heat loss at the drive end of the test bearing, the temperature, which
is measured here may be 2 °C ~ 5 °C lower.
3.12
Operating temperature
Test temperature (Tb), at the end of the running-in time.
3.13
Running-in time
The time, from the start of the test to the establishment of a steady state.
Note. During the running-in period, the grease is evenly distributed to the surface of each
test piece, with the rotation of the motor, meanwhile a certain amount of wear is generated.
Due to the mutual contact of the bearing test pieces on the working surface, the working
surface gradually tends to be smooth, resulting in an increase in the ratio, between the
thickness of the lubricating film and the roughness of the contact surface, so does the
isolation effect of the lubricating film. The reduction in sliding friction, which is caused by
this smoothing action, results in a downward trend in friction torque, during the running-in.
During the loading time, wear also generally decreases.
3.14
Wear
The phenomenon and process of surface deformation, damage or gradual loss of
surface material, due to friction.
[GB/T 17754-2012, definition 2.3]
3.15
Wear loss
The amount of deformation of the material contact surface of the friction pair OR
loss of surface material, during wear.
[GB/T 17754-2012, definition 5.1]
4 Method overview
4.1 When using the FE8 bearing wear testing machine for the lubricating oil test, first
install two test bearings on the testing machine. Apply a certain amount of test oil into
the lubricating oil circulation system. Through the lubricating oil circulation system, it
supplies oil, at a rate of 0.1 L/min ± 0.02 L/min, to each test bearing. The test is carried
out, under the specified conditions (motor speed 7.5 r/min, axial load 80 kN, test
temperature 80 °C). Weigh the mass of each component of the test bearing, before and
after the test. The wear performance of the lubricant is evaluated, by the wear mass loss.
4.2 During the test, when the friction torque of the bearing continuously exceeds 60
N·m for more than 10 s, due to poor lubrication, OR the continuous running time
reaches 80 h, the test ends. After the test, weigh the bearing components and calculate
the wear loss (mg). Each lubricating oil sample is tested twice; the wear performance
of the lubricating oil is evaluated by the wear loss of the bearing components.
5 Test equipment
5.1 FE8 testing machine
5.1.1 The test equipment adopts FE8 bearing wear testing machine, which consists of
test head, drive unit, control system. The test head (see Figure 1) is detachably
connected to the drive unit, through the cone seat of the test head shaft (7). The drive
shaft (1) of the drive unit is installed in two auxiliary bearings (2), which is driven
directly by a motor (not shown in the Figure), at different speeds in the range of 7.5
r/min ~ 3000 r/min, OR through gear meshing. The test bearing (3) is installed in the
test head. A certain axial load is applied, through the butterfly spring assembly (4).
5.4.4 Brush. The size shall be suitable for the cleaning of the test bearing.
5.4.5 Special rag. No lint or fibers falling off, during the process of use.
5.4.6 Balance. It is used to weigh the test piece. The recommended weighing range is 0
kg ~ 2 kg; the division value is 1 mg.
5.4.7 Demagnetizer. It is used for demagnetization, after the test piece is magnetized.
The power-on continuity rate is 60%; the power is 100 W; the voltage is 220 V.
6 Reagents and materials
Cleaning solvent. The solvent oil for cleaning meets the requirements of No.2 solvent
oil in GB 1922-2006.
Warning. It is flammable material, whose volatile gases are harmful. It shall keep
away from fire, sparks, open flames; avoid prolonged or frequent skin exposure.
7 Preparation of test bearings
7.1 Take the roller of the test bearing out of the cage. Put it into the cleaning cup. Use
a brush, which is dipped in cleaning solvent, to clean it. In the same way, clean the
bearing's outer ring, bearing's inner ring, bearing cage, etc. Place the cleaned bearing
parts in a drying oven, which was preheated to 80 °C, for 30 minutes. Place the dried
bearing parts in a clean container, to naturally dry it to room temperature. Protective
gloves shall be used, when doing the above.
7.2 Use balance to weigh the mass of the roller and the cage. Record it, accurate to 1
mg. Install the rollers into the cage housing, at room temperature. Before installation,
use cleaning solvent and special cloth, to clean the installation tool. Check for free
movement of the temperature sensor and friction torque measurement connections.
Before starting the test run, calibrate the friction sensor.
8 Test steps
Share
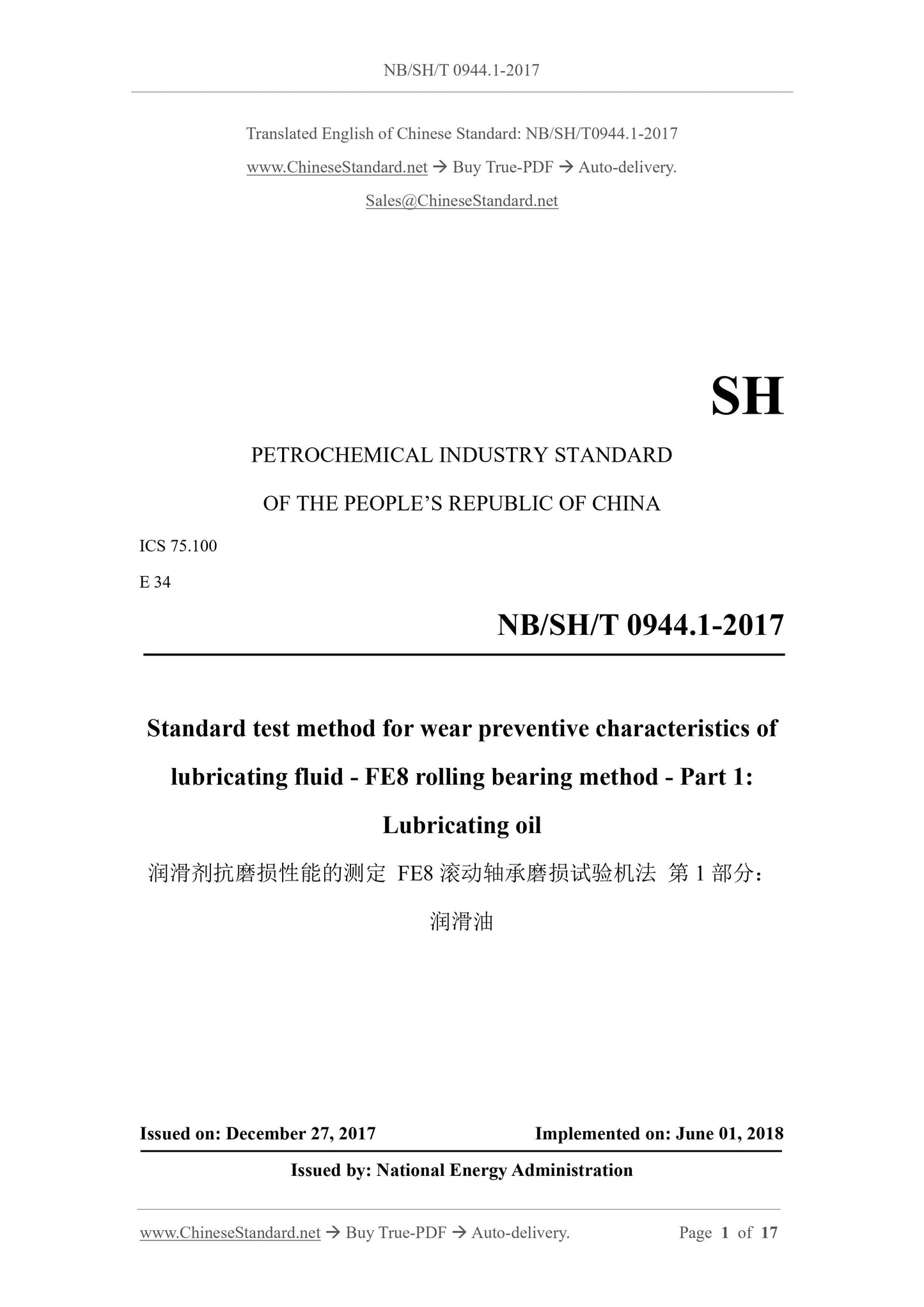
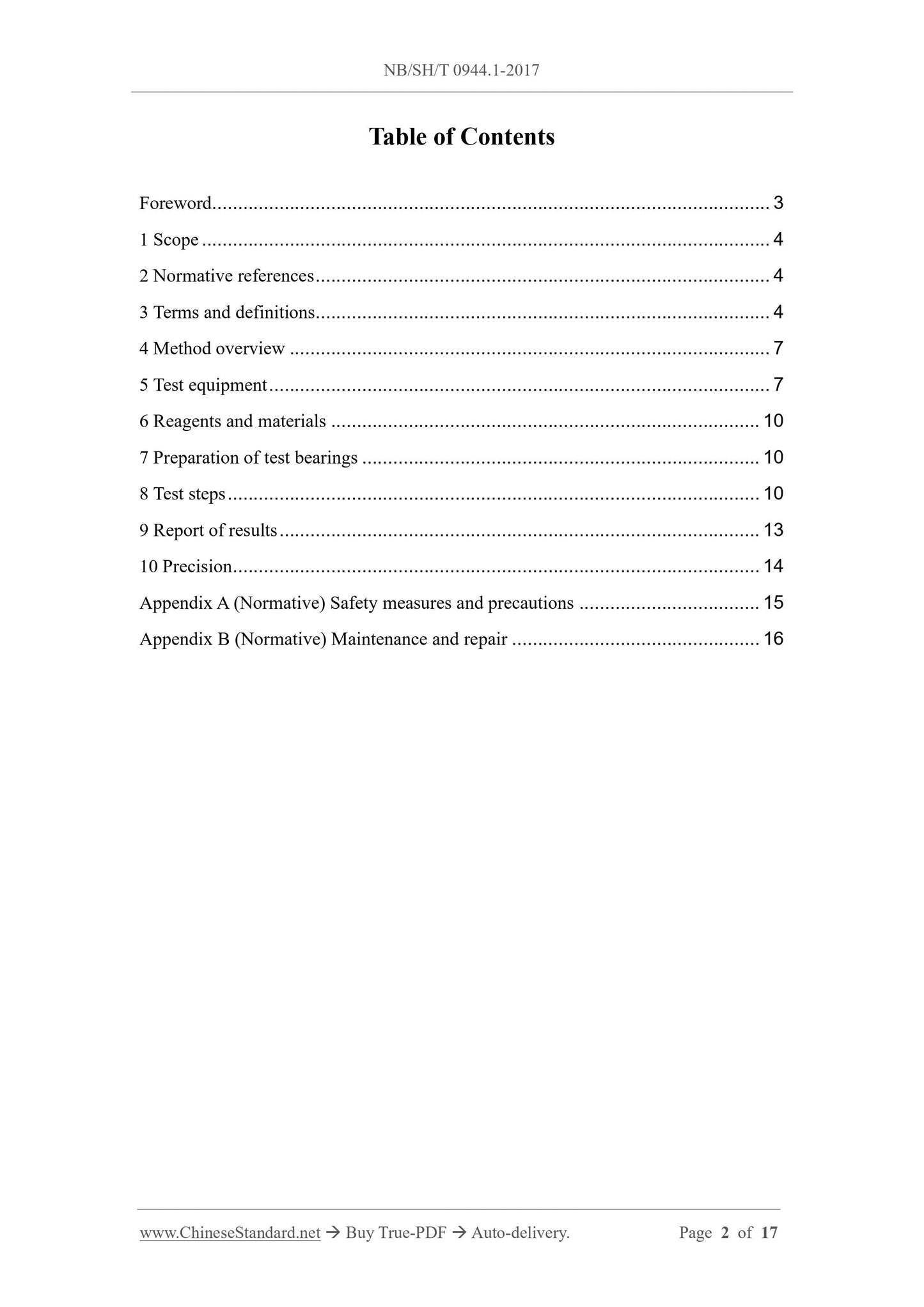
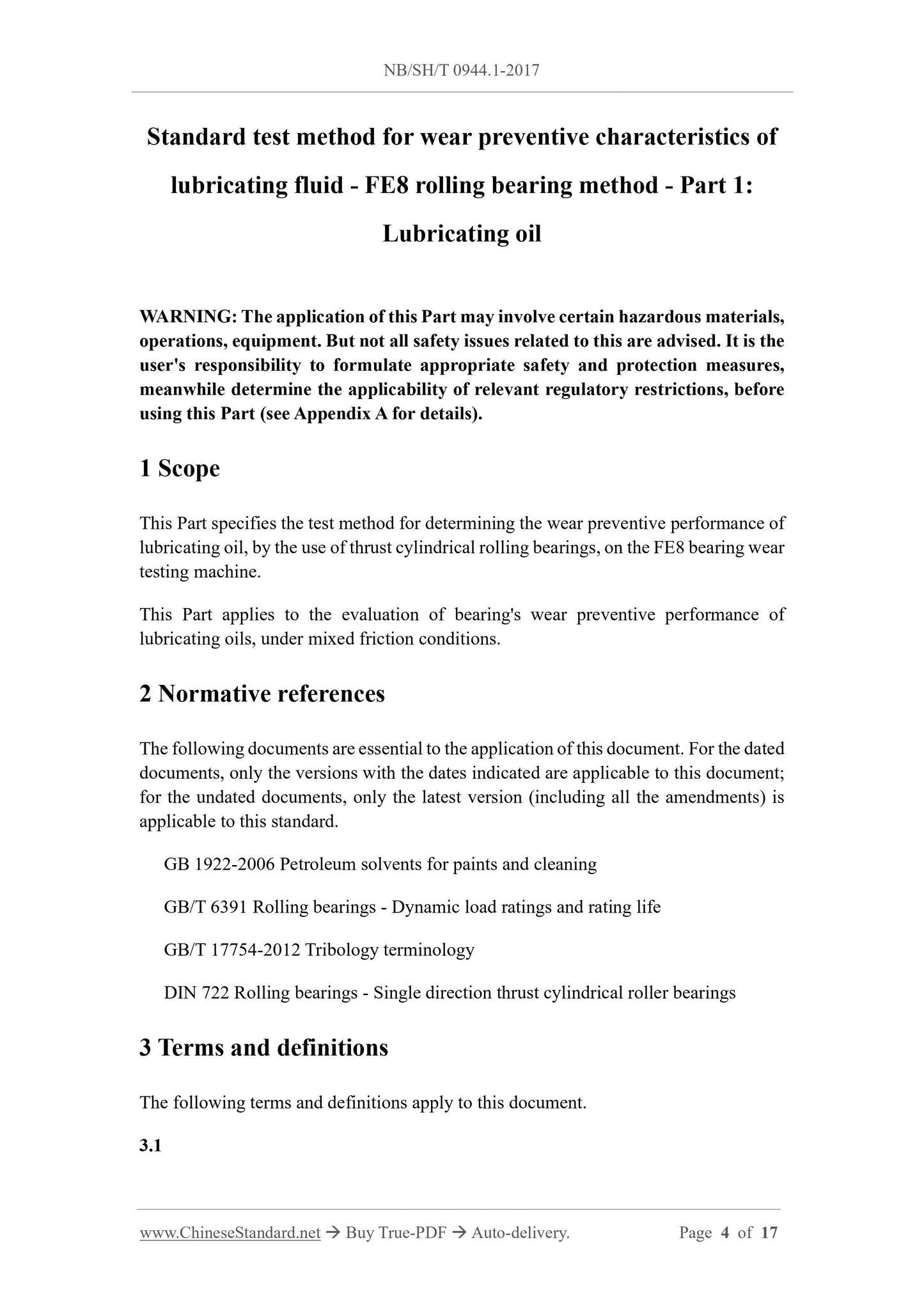
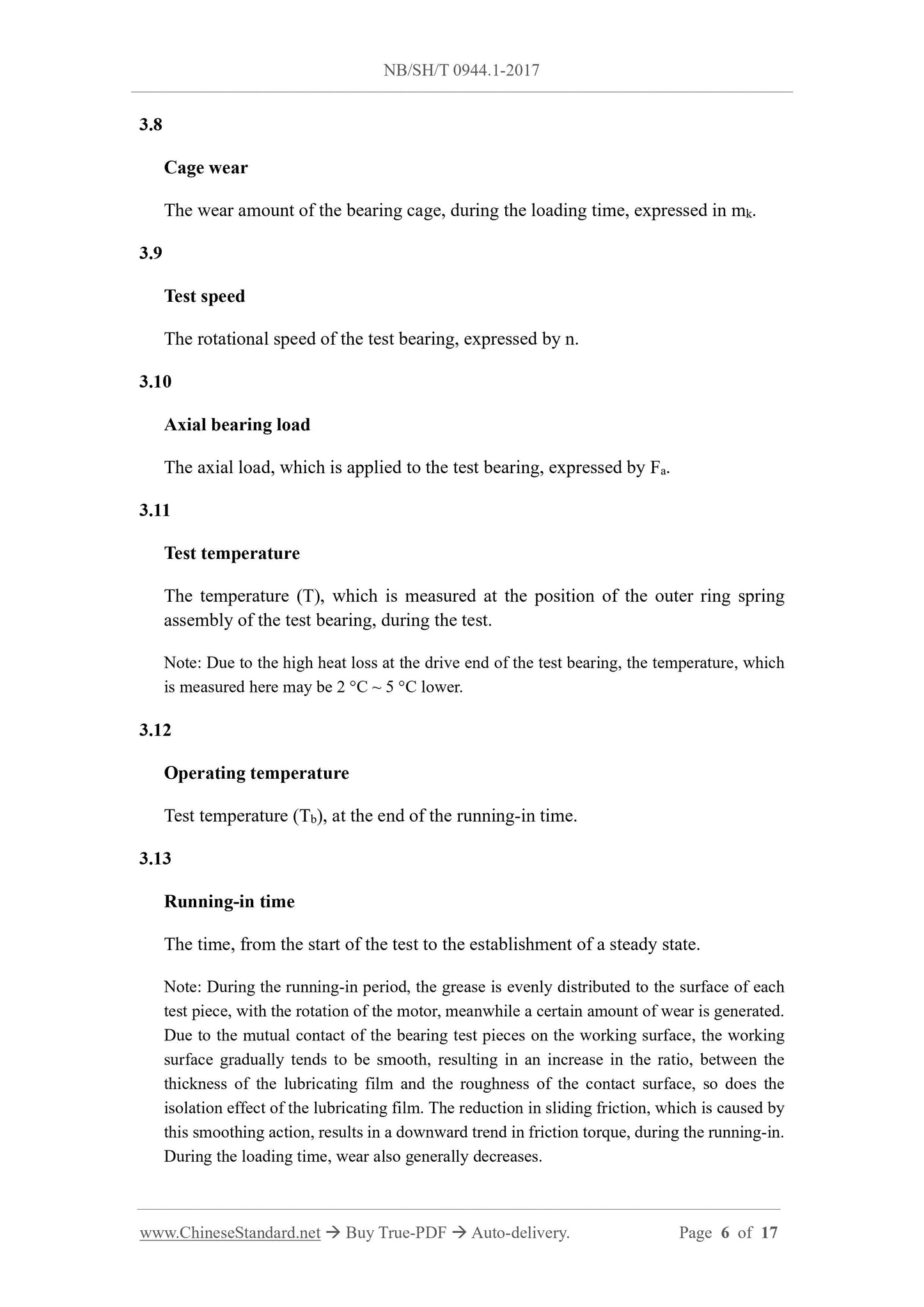
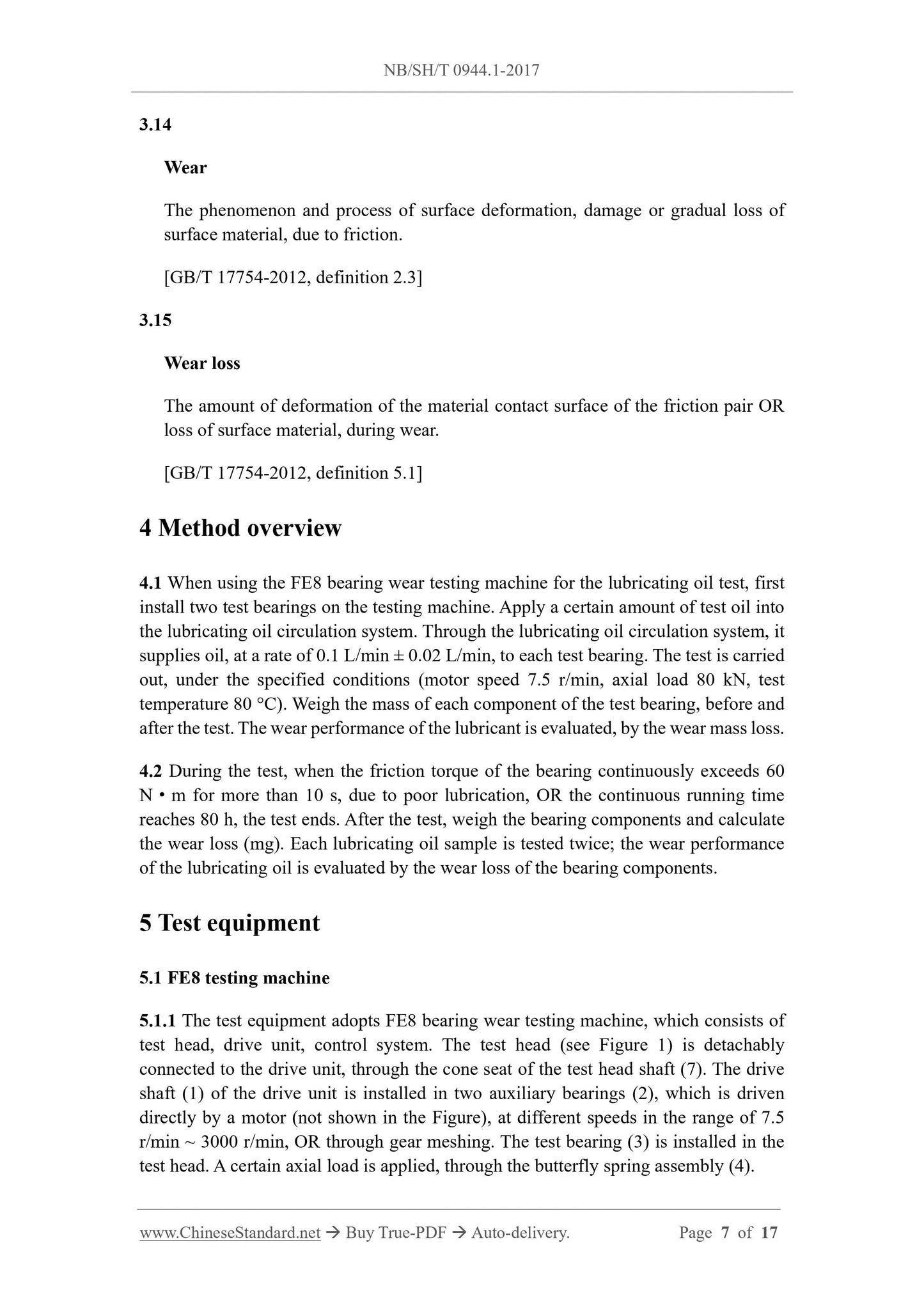
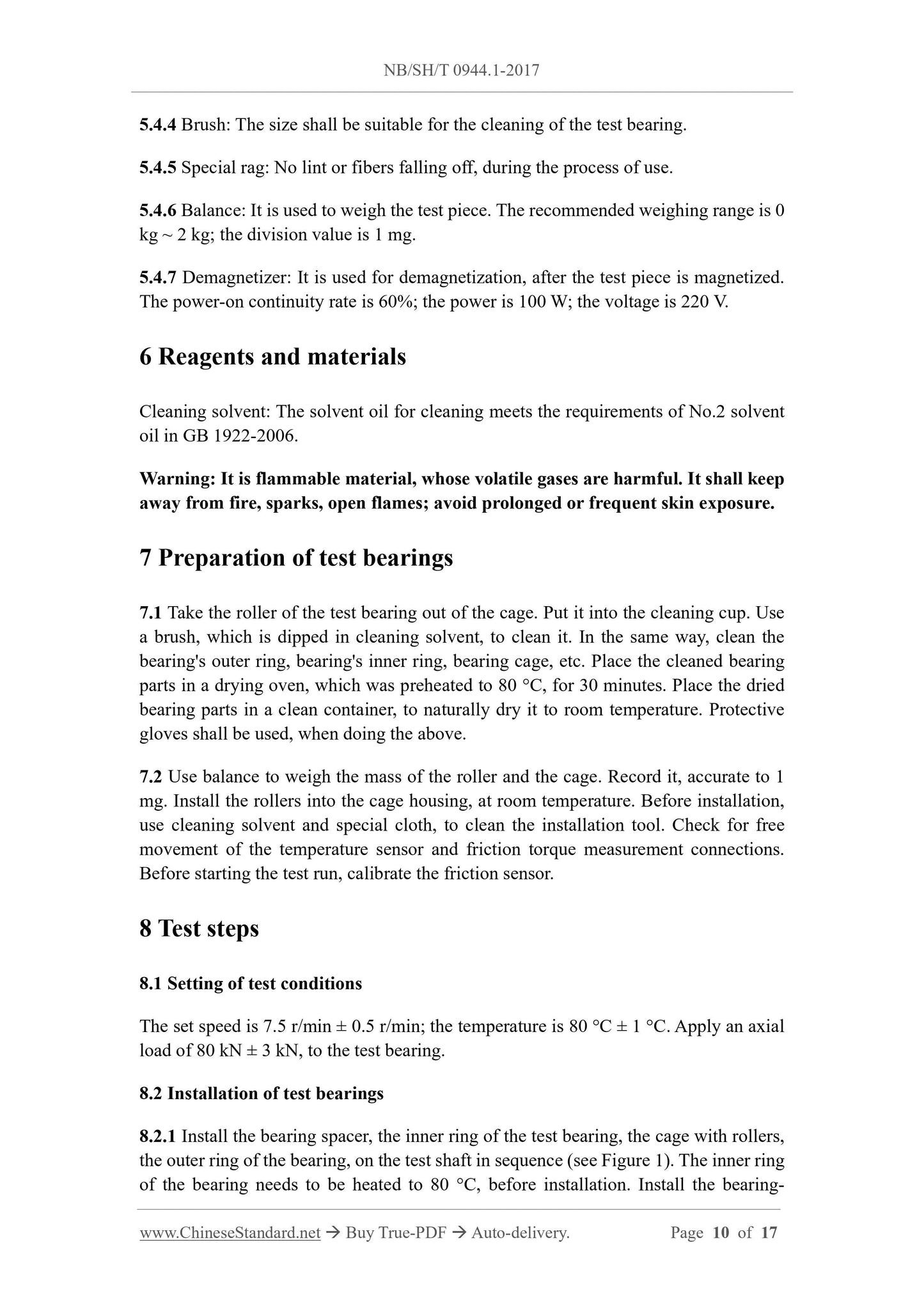
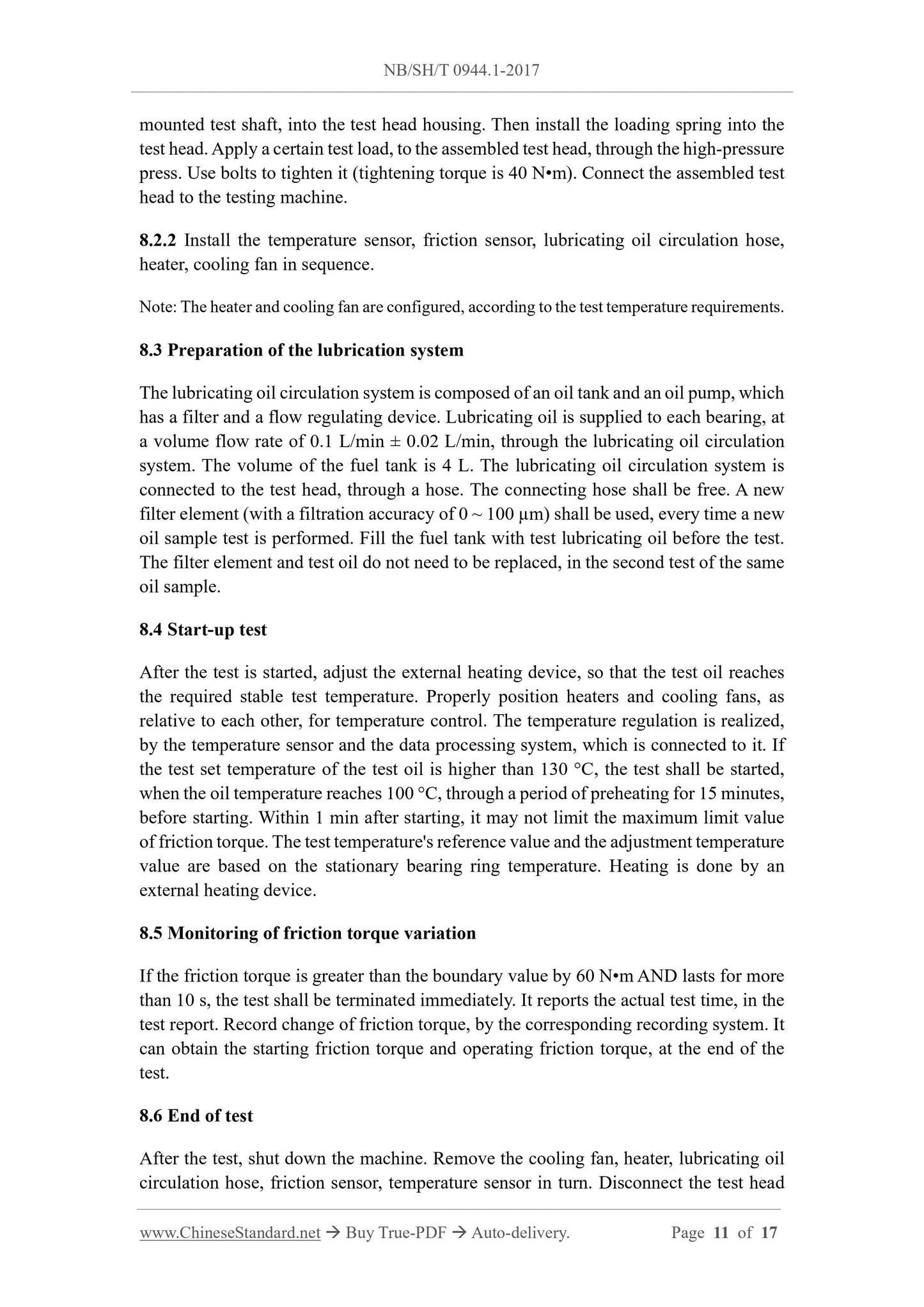
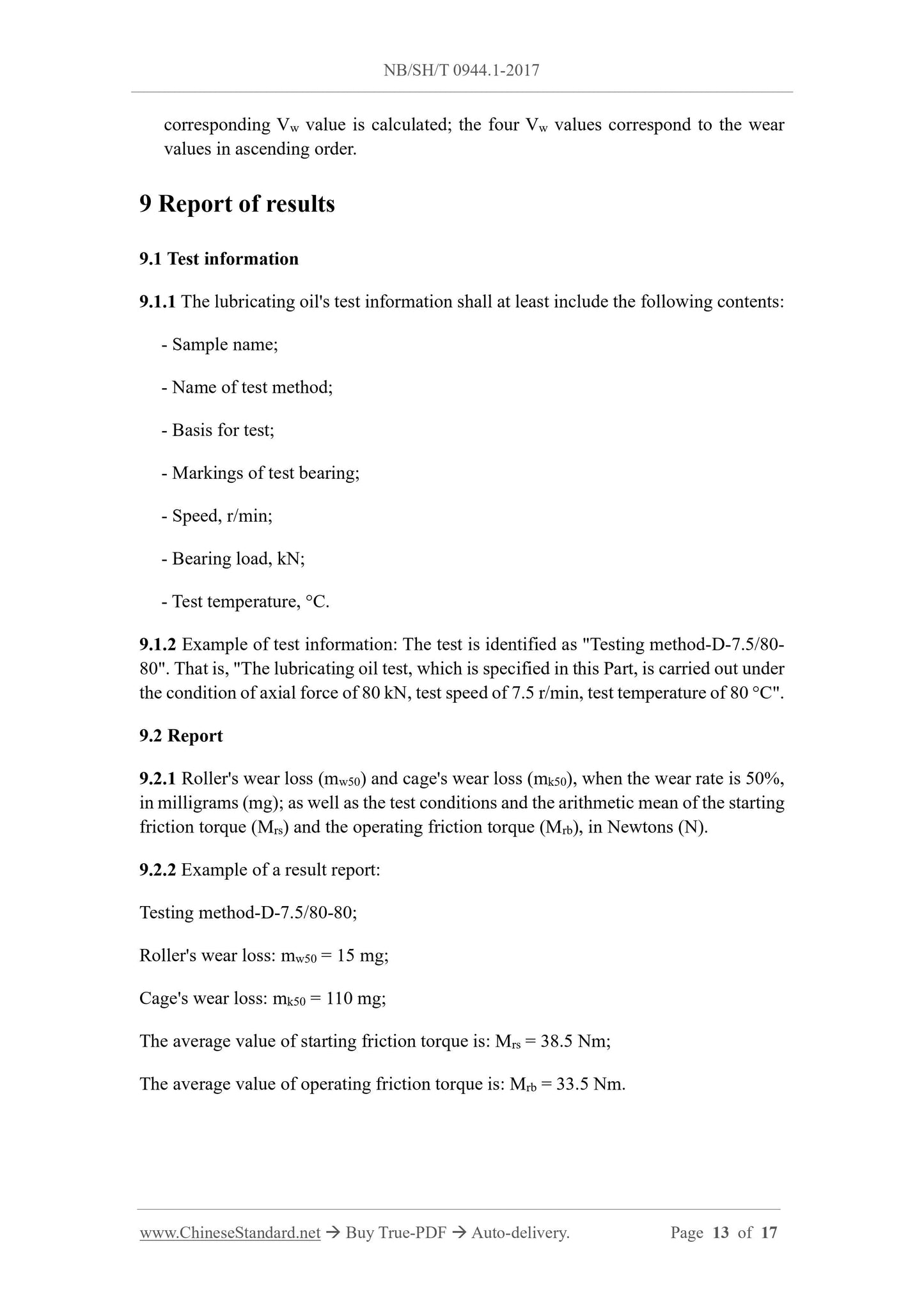
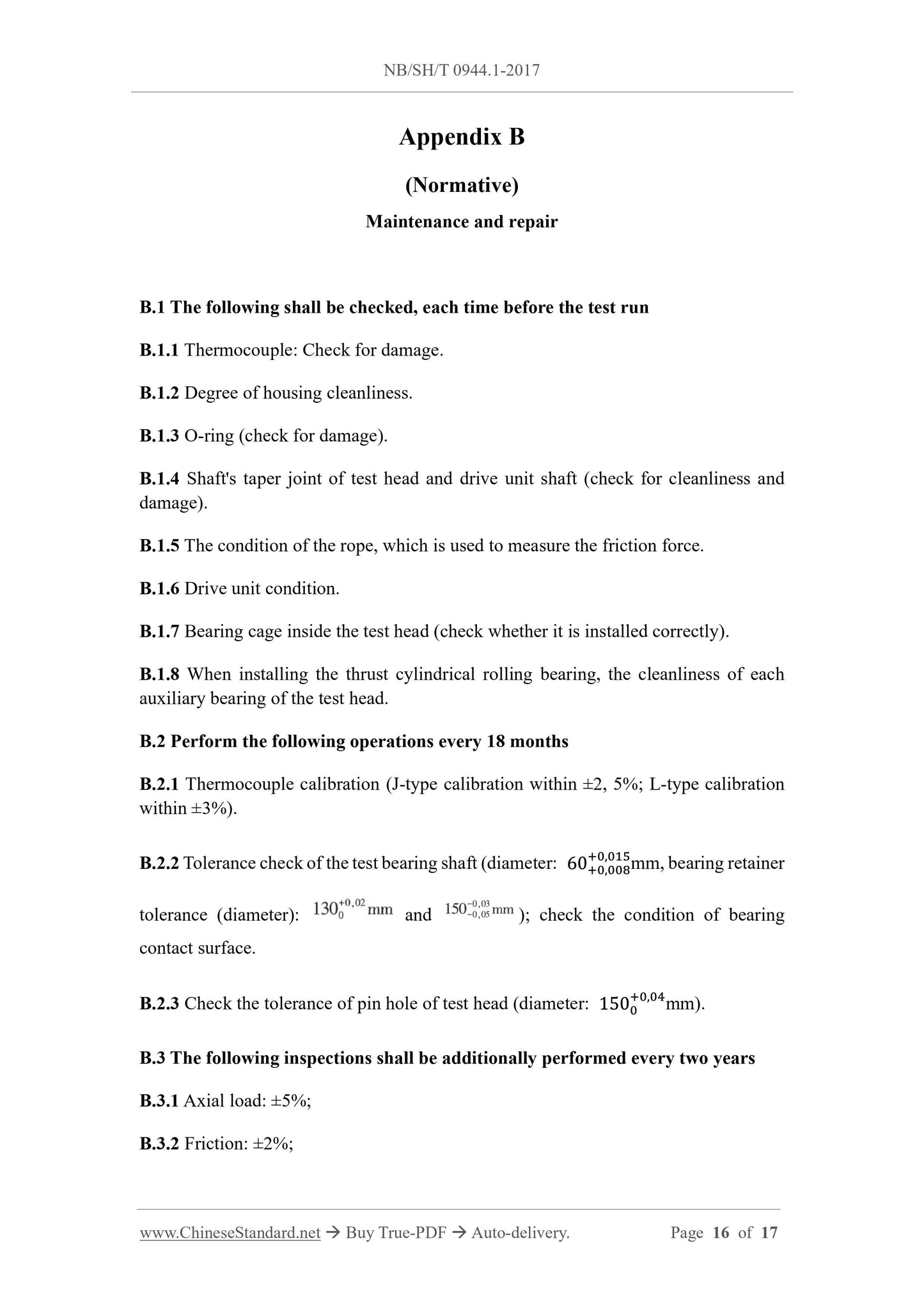