1
/
de
12
PayPal, credit cards. Download editable-PDF and invoice in 1 second!
NB/T 20015-2021 English PDF (NB/T20015-2021)
NB/T 20015-2021 English PDF (NB/T20015-2021)
Prix habituel
$740.00 USD
Prix habituel
Prix promotionnel
$740.00 USD
Prix unitaire
/
par
Frais d'expédition calculés à l'étape de paiement.
Impossible de charger la disponibilité du service de retrait
Delivery: 3 seconds. Download true-PDF + Invoice.
Get QUOTATION in 1-minute: Click NB/T 20015-2021
Historical versions: NB/T 20015-2021
Preview True-PDF (Reload/Scroll if blank)
NB/T 20015-2021: Nuclear power plant simulators for use in operator training and examination
NB/T 20015-2021
NB
ENERGY INDUSTRY STANDARD
ICS 27.120.10
CCS F 83
Replacing NB/T 20015-2010
Nuclear Power Plant Simulators for Use in Operator
Training and Examination
ISSUED ON. APRIL 26, 2021
IMPLEMENTED ON. JULY 26, 2021
Issued by. National Energy Administration
Table of Contents
Foreword... 3
1 Scope... 5
2 Normative References... 5
3 Terms and Definitions... 5
4 General... 9
5 Test Requirements... 19
6 Configuration and Management of the Simulator... 28
Appendix A (Informative) Application Example of Steady-State Allowable Error of
Simulator... 31
Appendix B (Normative) Guidelines for the Implementation of Simulator Operability
Tests... 32
Appendix C (Informative) Guidelines for the Preparation of Simulator Design and Test
Documents... 38
Bibliography... 42
Nuclear Power Plant Simulators for Use in Operator
Training and Examination
1 Scope
This Document specifies the functional requirements of the full range simulator of the control
room of a pressurized water reactor nuclear power plant (hereinafter referred to as the simulator)
used for operator training and examination, as well as the simulation range, performance and
functional criteria of the simulator.
This Document is applicable to the simulator of a pressurized water reactor nuclear power plant,
and can also be used as a reference for simulators of non-pressurized water reactor nuclear
power plants and other nuclear facilities.
2 Normative References
There are no normative references in this Document.
3 Terms and Definitions
For the purposes of this Document, the following terms and definitions apply.
3.1 Reference unit
Determine the specific nuclear power plant unit on which the simulator control room
configuration, system control settings and design database are based.
3.1 Simulation
Use modeling techniques in a simulator development environment to replicate the systems or
subsystems of the reference unit.
NOTE. The performance and fidelity of the system being simulated are based on the functional and
operational limitations specified based on the design and operating data of the reference unit.
3.3 Stimulation
The simulator uses the actual hardware and software of the reference unit's system or subsystem
incorrectly respond to or interpret the reference unit.
3.30 Systematic approach to training
A commonly used process for establishing and maintaining a performance-based, quality-
qualified training program to meet the job requirements of the reference unit. It includes
analysis, design, development, implementation, evaluation and feedback of results.
3.31 Training needs assessment
An evaluation by an expert (3.18) of deviations, defects or changes in the simulator and their
relative impact on the operator's ability to perform specified tasks.
3.32 Distributed control system; DCS
Based on computer, communication and screen display technology, the multi-computer
monitoring system that realizes data collection, control and protection functions of the
production process and realizes data sharing.
(SOURCE. DL/T 1083-2008, 3.1)
3.33 DCS level 1
The control logic layer of the distributed control system (3.32), which is used to execute the
control and protection logic of the I and C system.
3.34 DCS level 2
The human-machine interface layer of the distributed control system (3.32), which is mainly
used for status monitoring and command operation during the run of the power plant.
4 General
4.1 Overview
Nuclear power plant simulators used for initial training, retraining and examination of operators
shall use a specific unit as the reference unit. The simulation range shall enable operators to
take the same operation through the operating procedures of the reference unit to handle a
certain change process on the simulator as the operation taken on the reference unit. The
simulation range shall allow all the change processes specified in this Clause to be handled until
a stable operating condition is obtained.
A structured software design and testing process shall be established to control the modification
of the simulator. The overall design of the simulator should consider measures for examination
confidentiality. In addition, the capabilities of simulator verification and confirmation testing,
performance testing, and configuration management shall be provided.
4.2 Capabilities of the simulator
4.2.1 General requirements
The simulator response caused by the operator's operation, no operator operation, improper
operator operation and the reference unit automatic control and inherent characteristics shall be
realistic; it shall not violate the natural physical laws such as mass, motion and energy
conservation; and shall comply with the provisions of the verification, confirmation and
performance test criteria specified in Clause 5.
4.2.2 Simulator startup and shutdown time
The time to start up the simulator software (excluding the startup time of each simulator
computer) should be no more than 15 min; the time to shut down the simulator software
(excluding the shutdown time of each simulator computer) should be no more than 5 min.
4.2.3 Real-time and repeatability
When processing the change process specified in this Clause, the simulator shall be able to run
in real time and have repeatability.
4.2.4 Simulation limit
In order to meet the requirements of real-time simulation, it is sometimes necessary to simplify
the mathematical model of the physical process. This simplification may limit the simulator's
ability to handle certain dynamic processes. In addition, simulation processes that exceed the
design limits of the reference unit may also appear on the simulator, and the simulation may be
incorrect at this time. To avoid possible negative training, when the model parameter reaches
or exceeds a certain value, and this value indicates that the event exceeds the executable
simulation range or the expected state of the reference unit, there shall be automatic or
administrative control measures to remind the trainer.
4.2.5 Normal operation
4.2.5.1 Overview
The simulator shall be able to continuously simulate the change procedures of the reference
units listed in 4.2.5.2 and 4.2.5.3 without changing the mathematical model or initial conditions.
The simulator shall be able to calculate the system parameters of different operating conditions
and display these parameters on the corresponding instruments, while giving correct alarms and
protection system actions.
4.2.5.2 Steady-state operation
The simulator shall accurately simulate the steady-state response of the reference unit within
the operating range where the reference unit data can be obtained.
inside and outside the containment; large and small breach accidents showing multiphase
flow phenomena; failure of the pressurizer safety valve and pressure relief valve);
b) Failure of the power transmission and distribution system of the power plant, including
power failure of the entire plant, loss of external power supply, loss of emergency power
supply, emergency generator failure, electricity shutdown of power distribution bus of
the unit, electricity shutdown of a single AC or DC instrument power bus, electricity
shutdown of a single power cabinet and a single power load, and electricity shutdown of
control power of a single device;
c) Total loss of pressure of the instrument compressed air system or loss of pressure of the
isolable part, aff...
Get QUOTATION in 1-minute: Click NB/T 20015-2021
Historical versions: NB/T 20015-2021
Preview True-PDF (Reload/Scroll if blank)
NB/T 20015-2021: Nuclear power plant simulators for use in operator training and examination
NB/T 20015-2021
NB
ENERGY INDUSTRY STANDARD
ICS 27.120.10
CCS F 83
Replacing NB/T 20015-2010
Nuclear Power Plant Simulators for Use in Operator
Training and Examination
ISSUED ON. APRIL 26, 2021
IMPLEMENTED ON. JULY 26, 2021
Issued by. National Energy Administration
Table of Contents
Foreword... 3
1 Scope... 5
2 Normative References... 5
3 Terms and Definitions... 5
4 General... 9
5 Test Requirements... 19
6 Configuration and Management of the Simulator... 28
Appendix A (Informative) Application Example of Steady-State Allowable Error of
Simulator... 31
Appendix B (Normative) Guidelines for the Implementation of Simulator Operability
Tests... 32
Appendix C (Informative) Guidelines for the Preparation of Simulator Design and Test
Documents... 38
Bibliography... 42
Nuclear Power Plant Simulators for Use in Operator
Training and Examination
1 Scope
This Document specifies the functional requirements of the full range simulator of the control
room of a pressurized water reactor nuclear power plant (hereinafter referred to as the simulator)
used for operator training and examination, as well as the simulation range, performance and
functional criteria of the simulator.
This Document is applicable to the simulator of a pressurized water reactor nuclear power plant,
and can also be used as a reference for simulators of non-pressurized water reactor nuclear
power plants and other nuclear facilities.
2 Normative References
There are no normative references in this Document.
3 Terms and Definitions
For the purposes of this Document, the following terms and definitions apply.
3.1 Reference unit
Determine the specific nuclear power plant unit on which the simulator control room
configuration, system control settings and design database are based.
3.1 Simulation
Use modeling techniques in a simulator development environment to replicate the systems or
subsystems of the reference unit.
NOTE. The performance and fidelity of the system being simulated are based on the functional and
operational limitations specified based on the design and operating data of the reference unit.
3.3 Stimulation
The simulator uses the actual hardware and software of the reference unit's system or subsystem
incorrectly respond to or interpret the reference unit.
3.30 Systematic approach to training
A commonly used process for establishing and maintaining a performance-based, quality-
qualified training program to meet the job requirements of the reference unit. It includes
analysis, design, development, implementation, evaluation and feedback of results.
3.31 Training needs assessment
An evaluation by an expert (3.18) of deviations, defects or changes in the simulator and their
relative impact on the operator's ability to perform specified tasks.
3.32 Distributed control system; DCS
Based on computer, communication and screen display technology, the multi-computer
monitoring system that realizes data collection, control and protection functions of the
production process and realizes data sharing.
(SOURCE. DL/T 1083-2008, 3.1)
3.33 DCS level 1
The control logic layer of the distributed control system (3.32), which is used to execute the
control and protection logic of the I and C system.
3.34 DCS level 2
The human-machine interface layer of the distributed control system (3.32), which is mainly
used for status monitoring and command operation during the run of the power plant.
4 General
4.1 Overview
Nuclear power plant simulators used for initial training, retraining and examination of operators
shall use a specific unit as the reference unit. The simulation range shall enable operators to
take the same operation through the operating procedures of the reference unit to handle a
certain change process on the simulator as the operation taken on the reference unit. The
simulation range shall allow all the change processes specified in this Clause to be handled until
a stable operating condition is obtained.
A structured software design and testing process shall be established to control the modification
of the simulator. The overall design of the simulator should consider measures for examination
confidentiality. In addition, the capabilities of simulator verification and confirmation testing,
performance testing, and configuration management shall be provided.
4.2 Capabilities of the simulator
4.2.1 General requirements
The simulator response caused by the operator's operation, no operator operation, improper
operator operation and the reference unit automatic control and inherent characteristics shall be
realistic; it shall not violate the natural physical laws such as mass, motion and energy
conservation; and shall comply with the provisions of the verification, confirmation and
performance test criteria specified in Clause 5.
4.2.2 Simulator startup and shutdown time
The time to start up the simulator software (excluding the startup time of each simulator
computer) should be no more than 15 min; the time to shut down the simulator software
(excluding the shutdown time of each simulator computer) should be no more than 5 min.
4.2.3 Real-time and repeatability
When processing the change process specified in this Clause, the simulator shall be able to run
in real time and have repeatability.
4.2.4 Simulation limit
In order to meet the requirements of real-time simulation, it is sometimes necessary to simplify
the mathematical model of the physical process. This simplification may limit the simulator's
ability to handle certain dynamic processes. In addition, simulation processes that exceed the
design limits of the reference unit may also appear on the simulator, and the simulation may be
incorrect at this time. To avoid possible negative training, when the model parameter reaches
or exceeds a certain value, and this value indicates that the event exceeds the executable
simulation range or the expected state of the reference unit, there shall be automatic or
administrative control measures to remind the trainer.
4.2.5 Normal operation
4.2.5.1 Overview
The simulator shall be able to continuously simulate the change procedures of the reference
units listed in 4.2.5.2 and 4.2.5.3 without changing the mathematical model or initial conditions.
The simulator shall be able to calculate the system parameters of different operating conditions
and display these parameters on the corresponding instruments, while giving correct alarms and
protection system actions.
4.2.5.2 Steady-state operation
The simulator shall accurately simulate the steady-state response of the reference unit within
the operating range where the reference unit data can be obtained.
inside and outside the containment; large and small breach accidents showing multiphase
flow phenomena; failure of the pressurizer safety valve and pressure relief valve);
b) Failure of the power transmission and distribution system of the power plant, including
power failure of the entire plant, loss of external power supply, loss of emergency power
supply, emergency generator failure, electricity shutdown of power distribution bus of
the unit, electricity shutdown of a single AC or DC instrument power bus, electricity
shutdown of a single power cabinet and a single power load, and electricity shutdown of
control power of a single device;
c) Total loss of pressure of the instrument compressed air system or loss of pressure of the
isolable part, aff...
Share
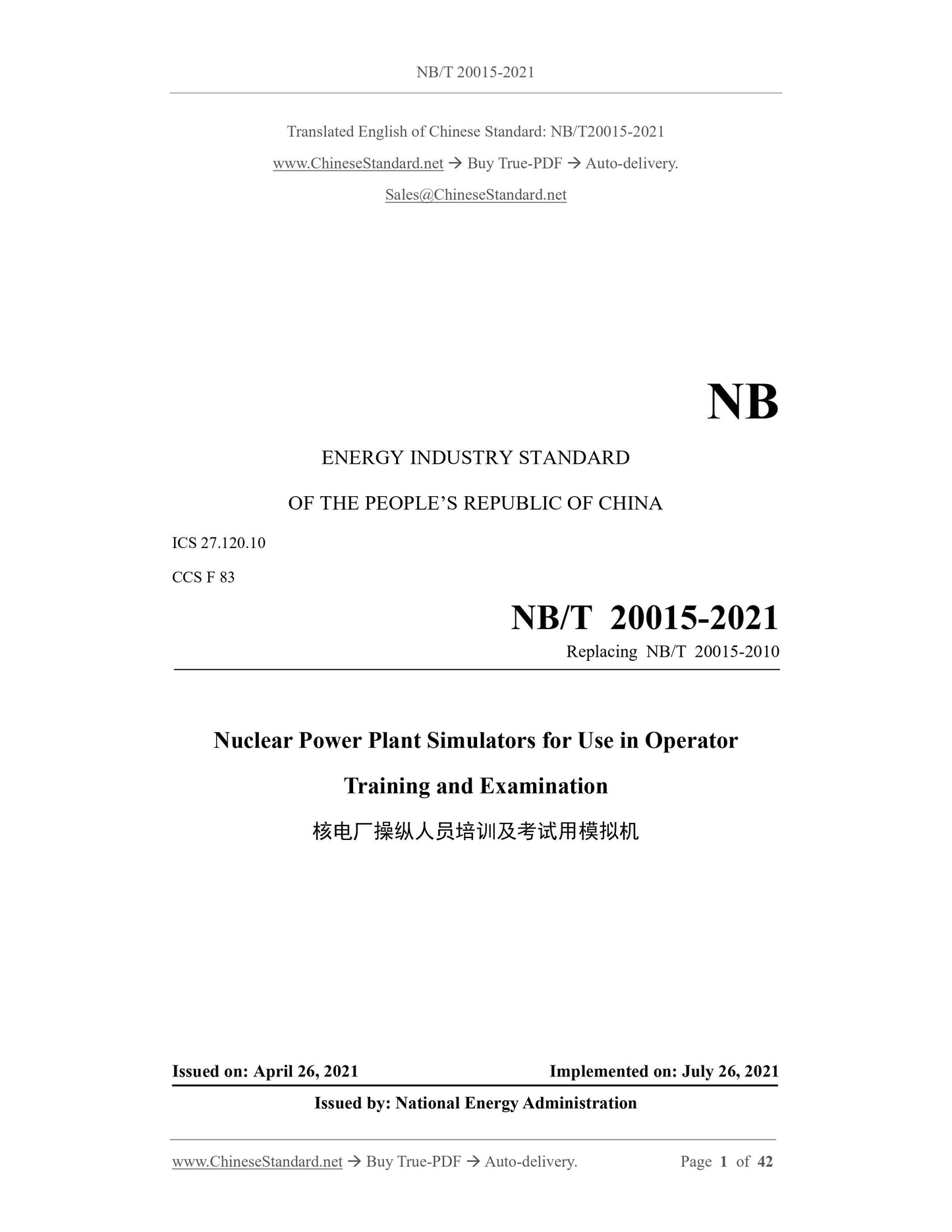
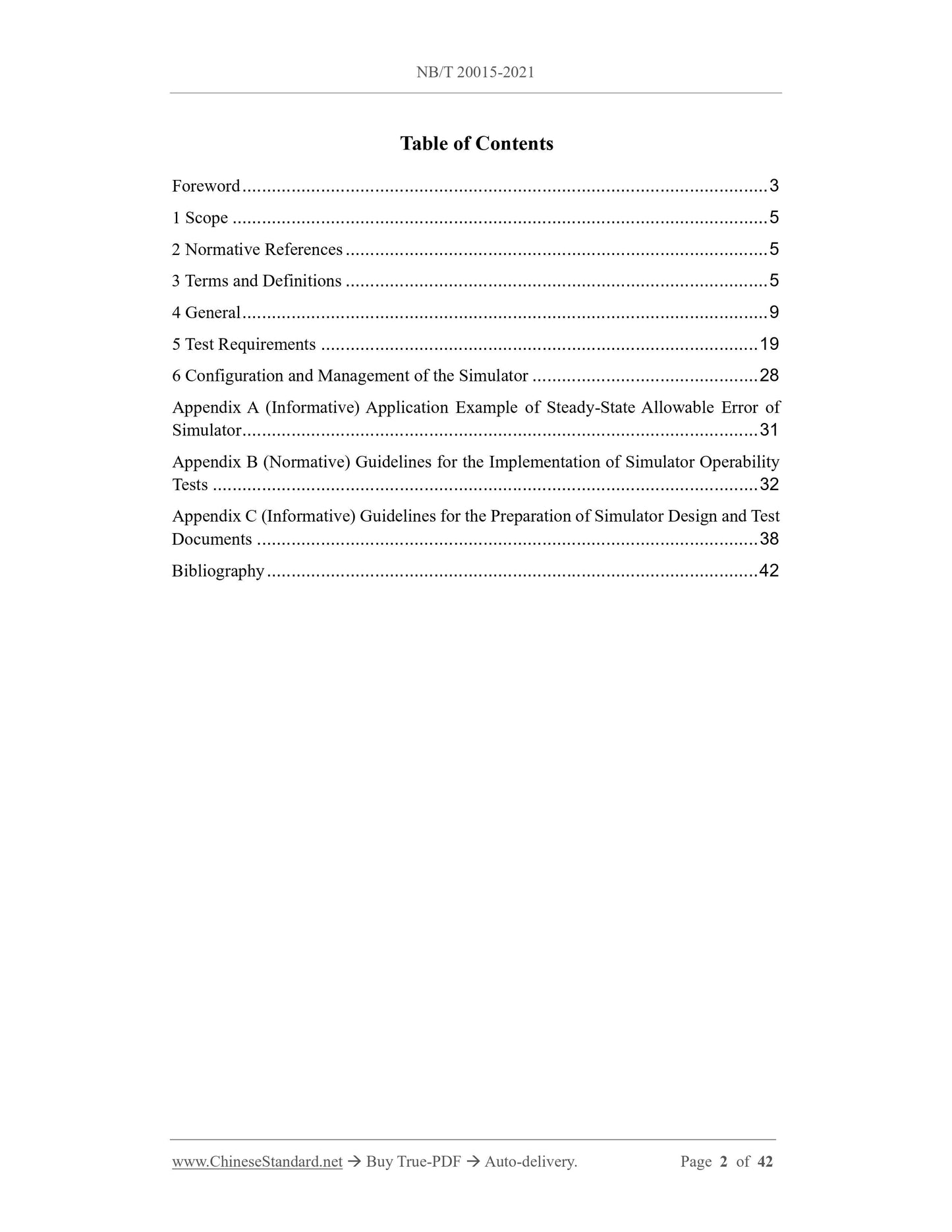
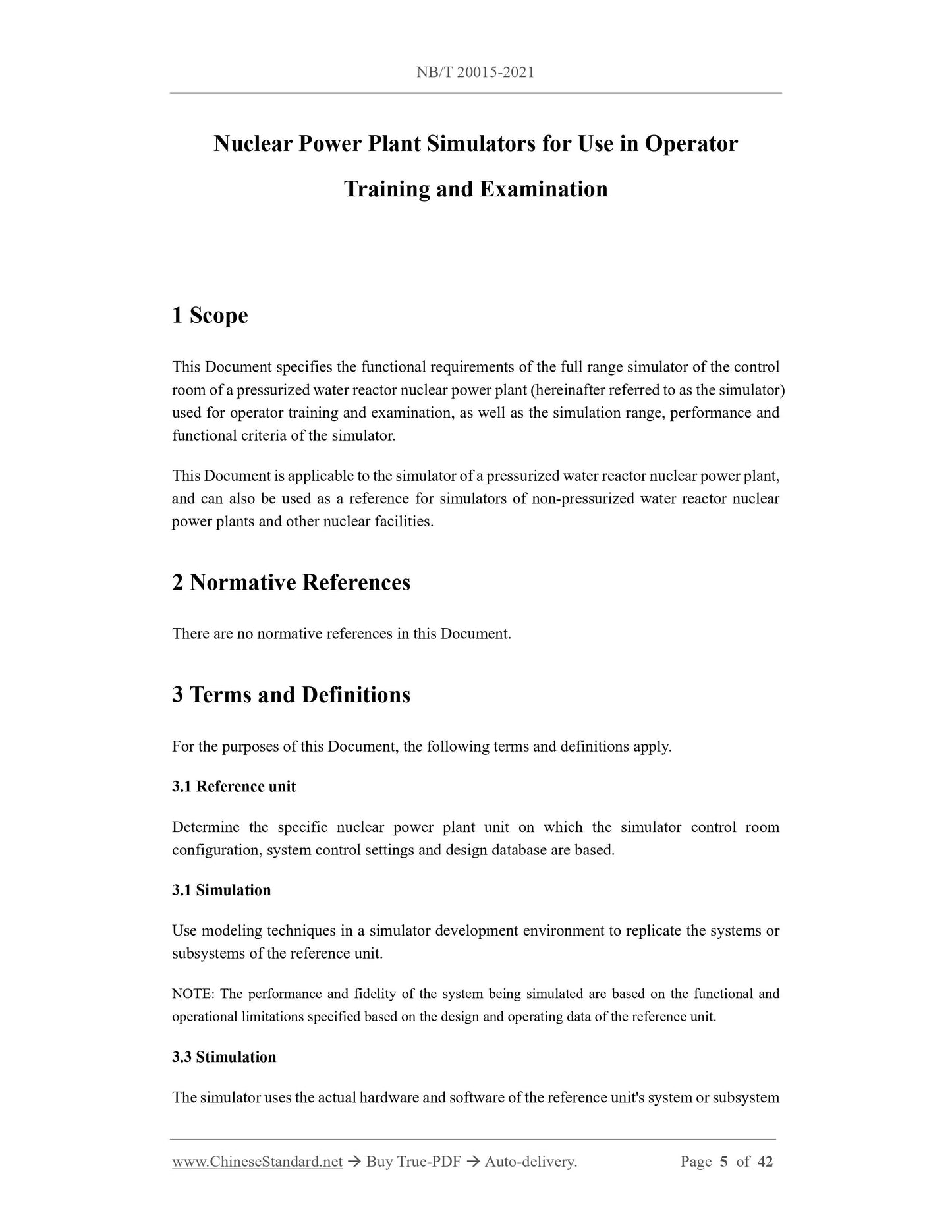
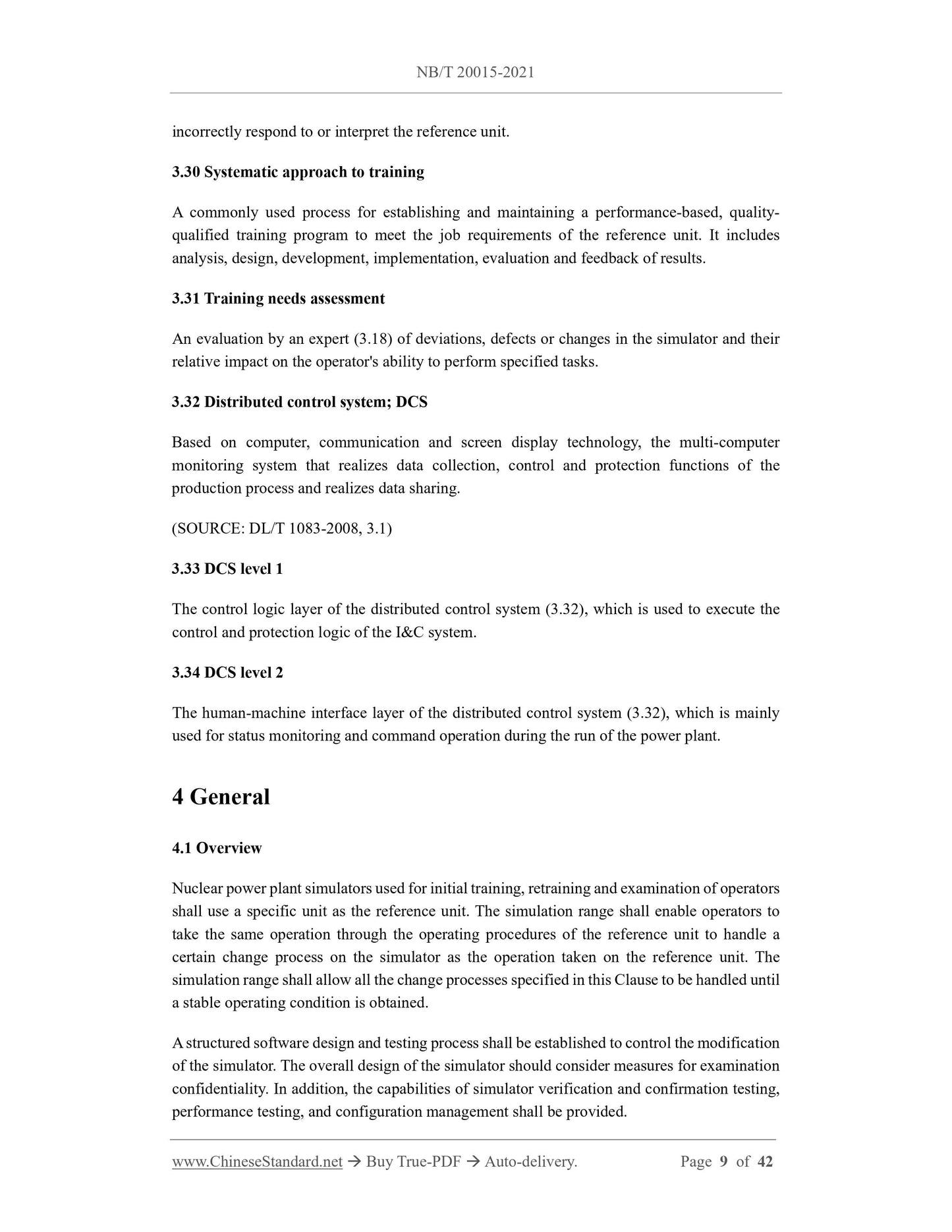
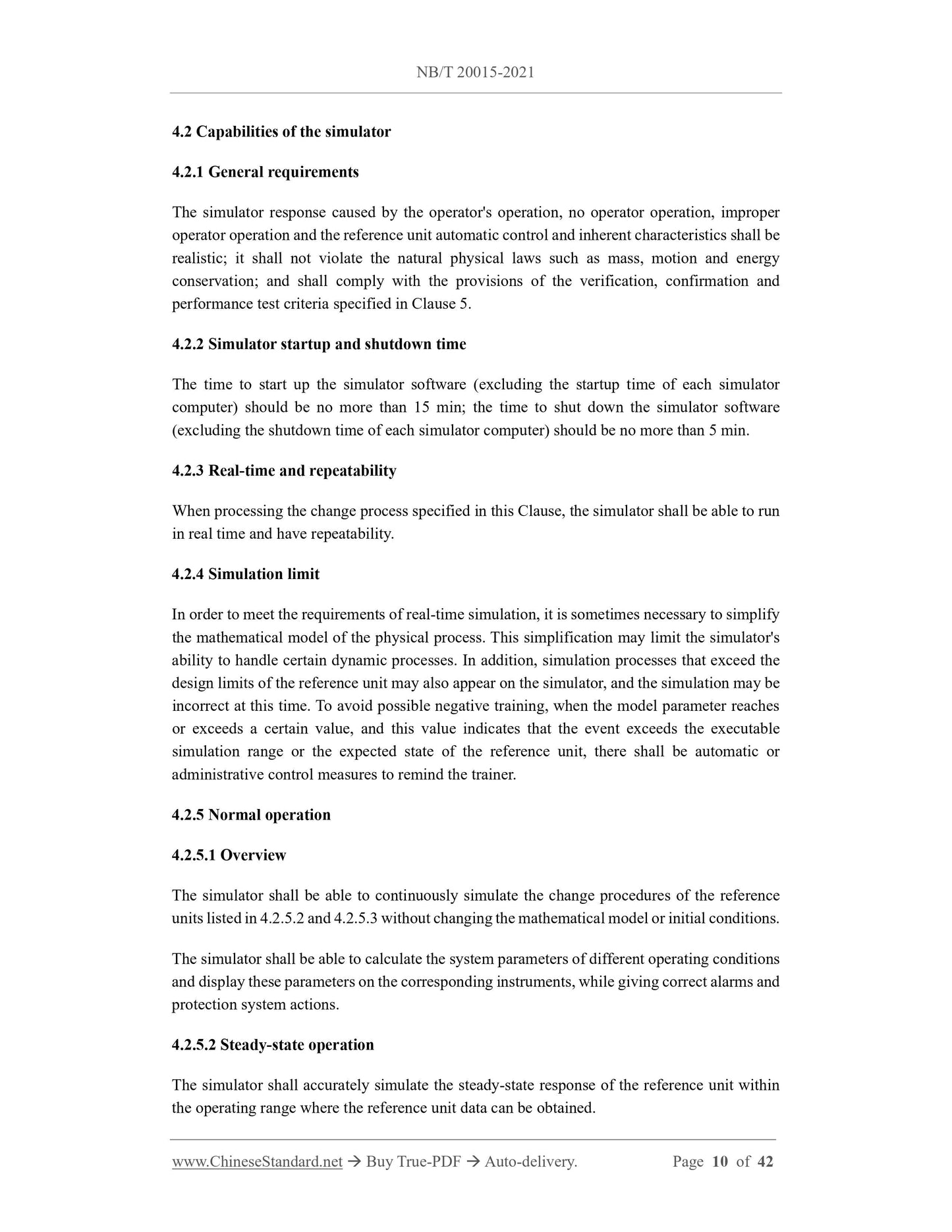
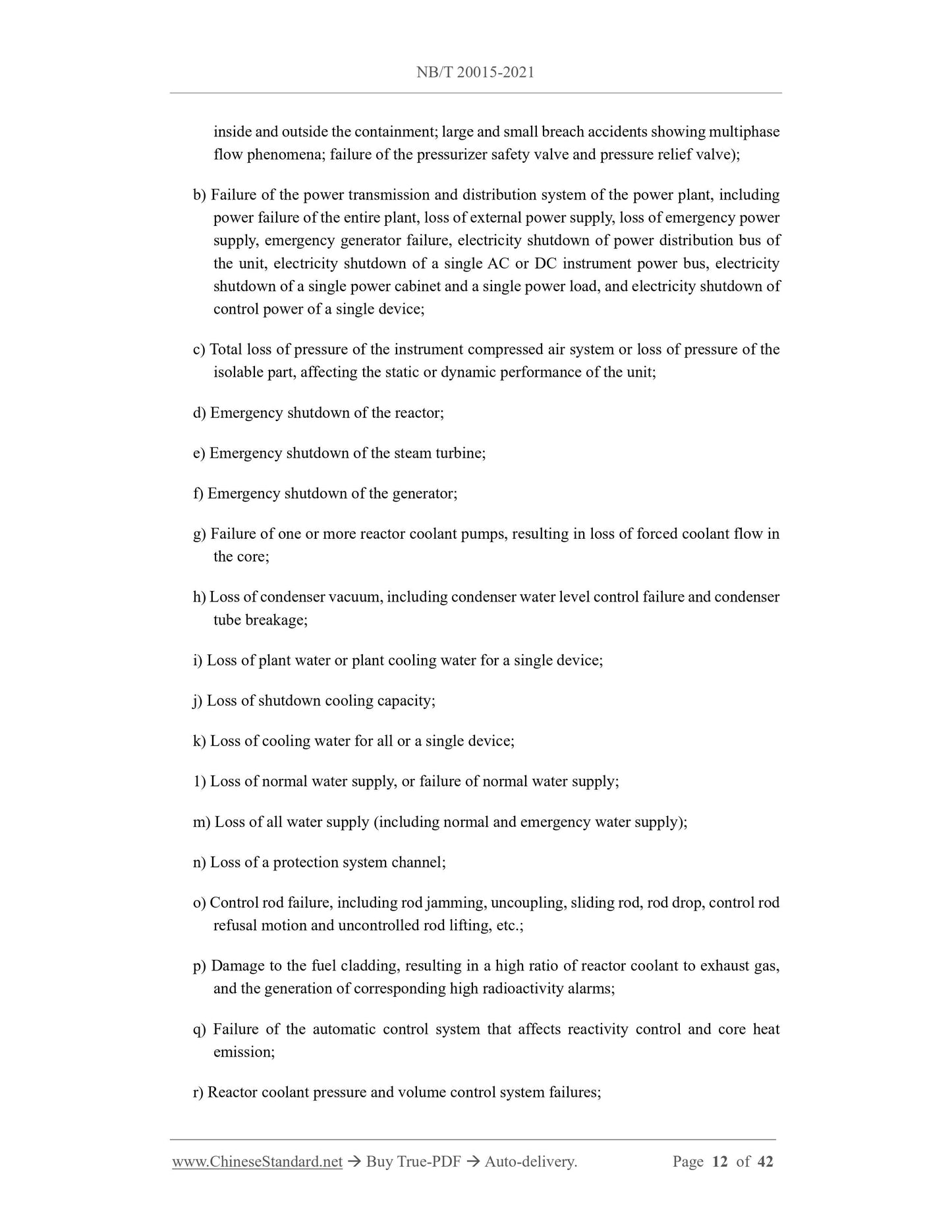
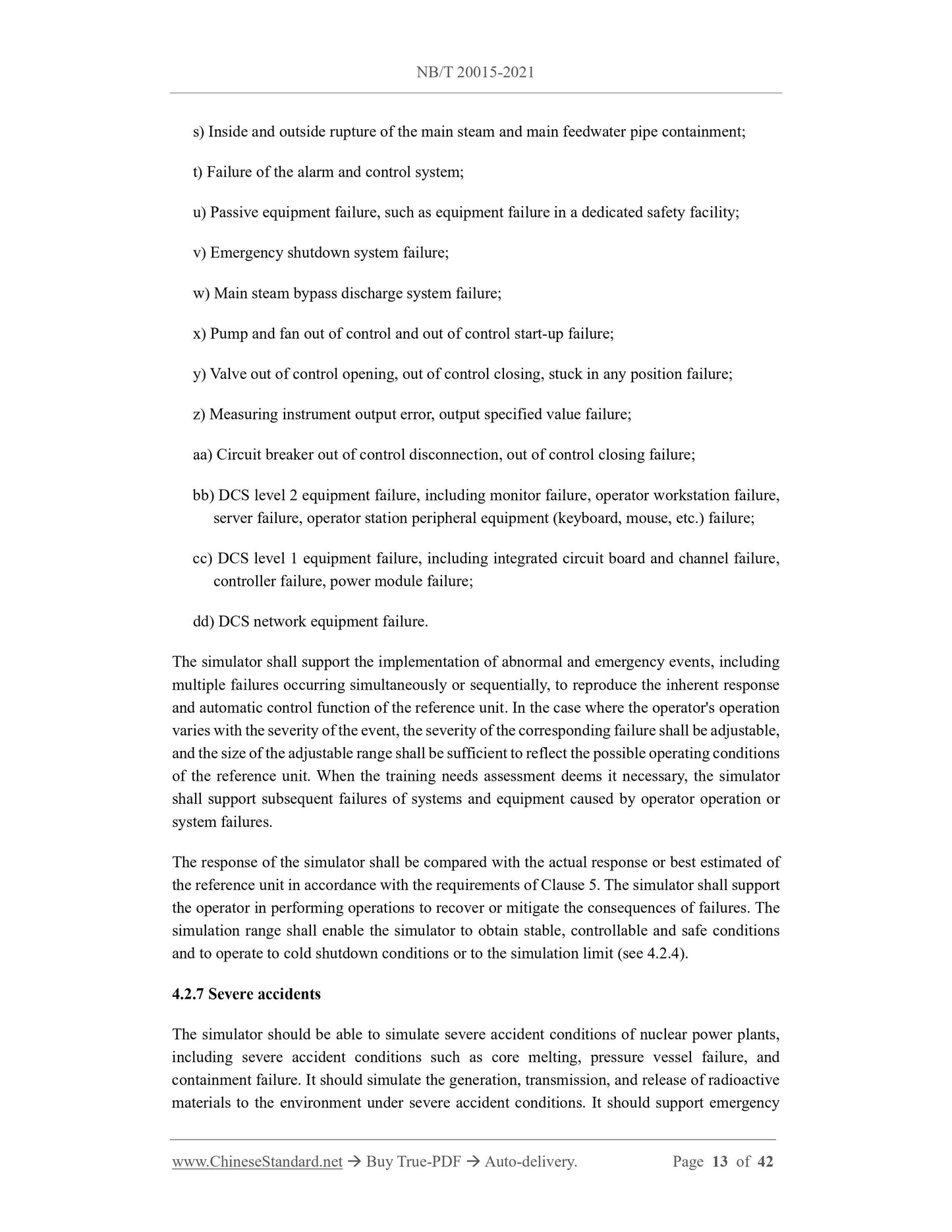
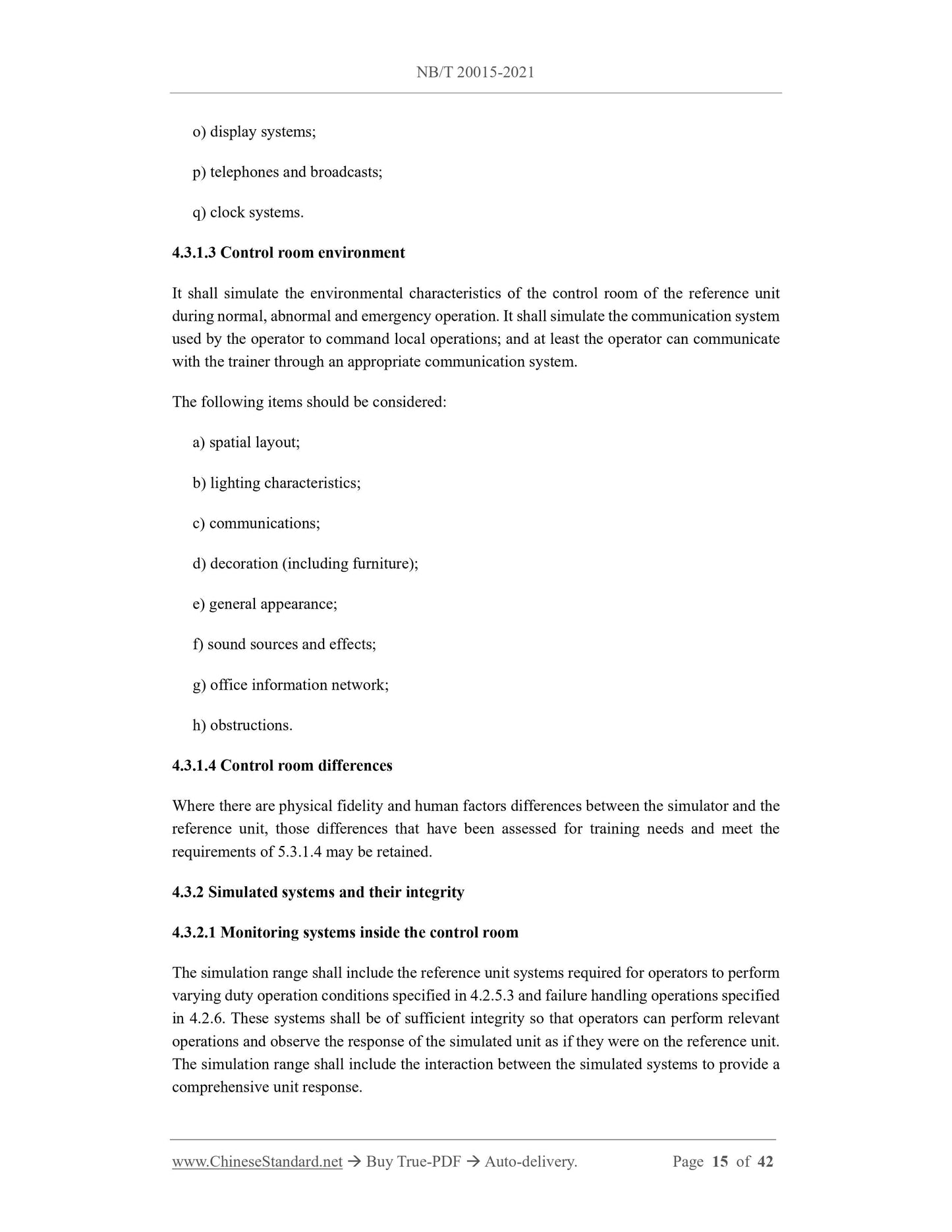
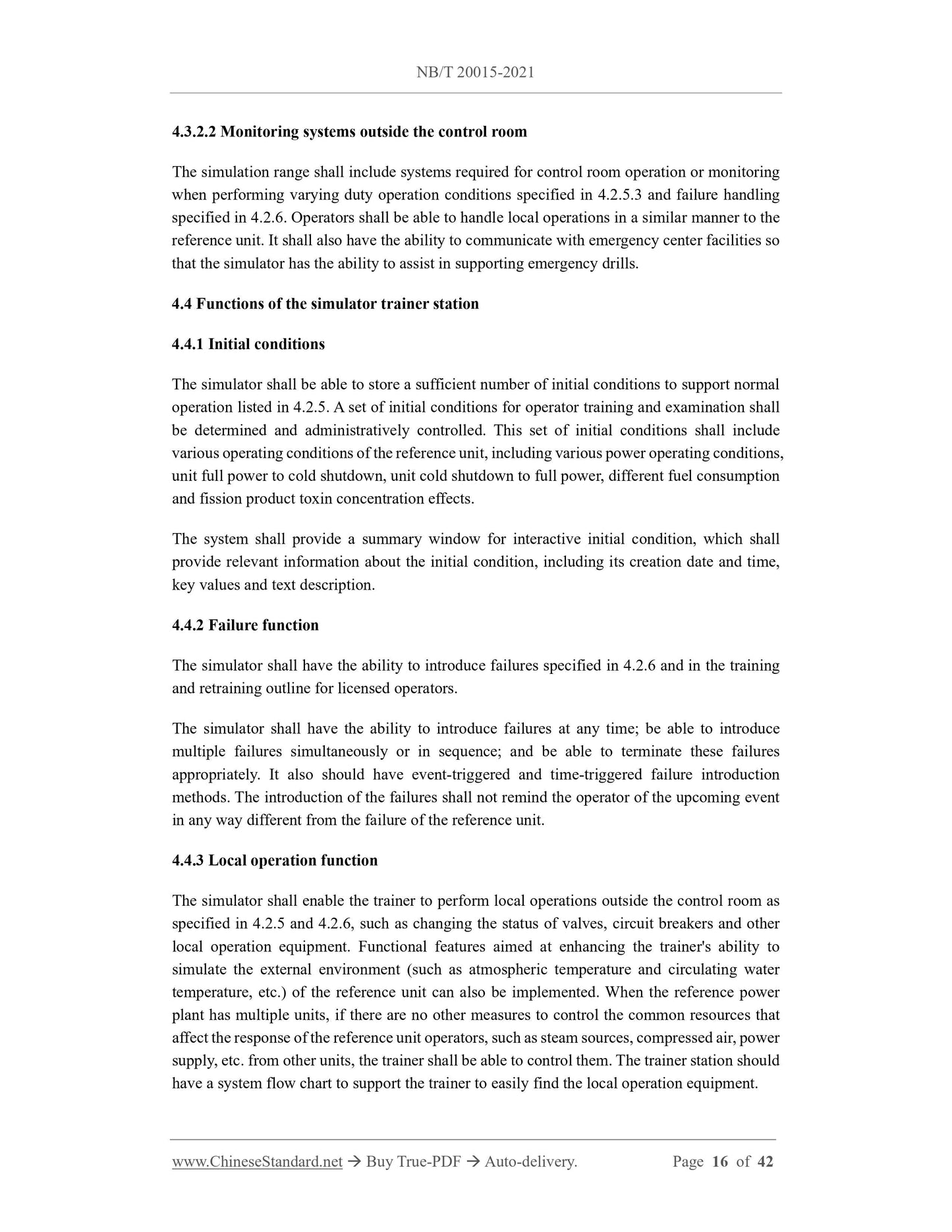
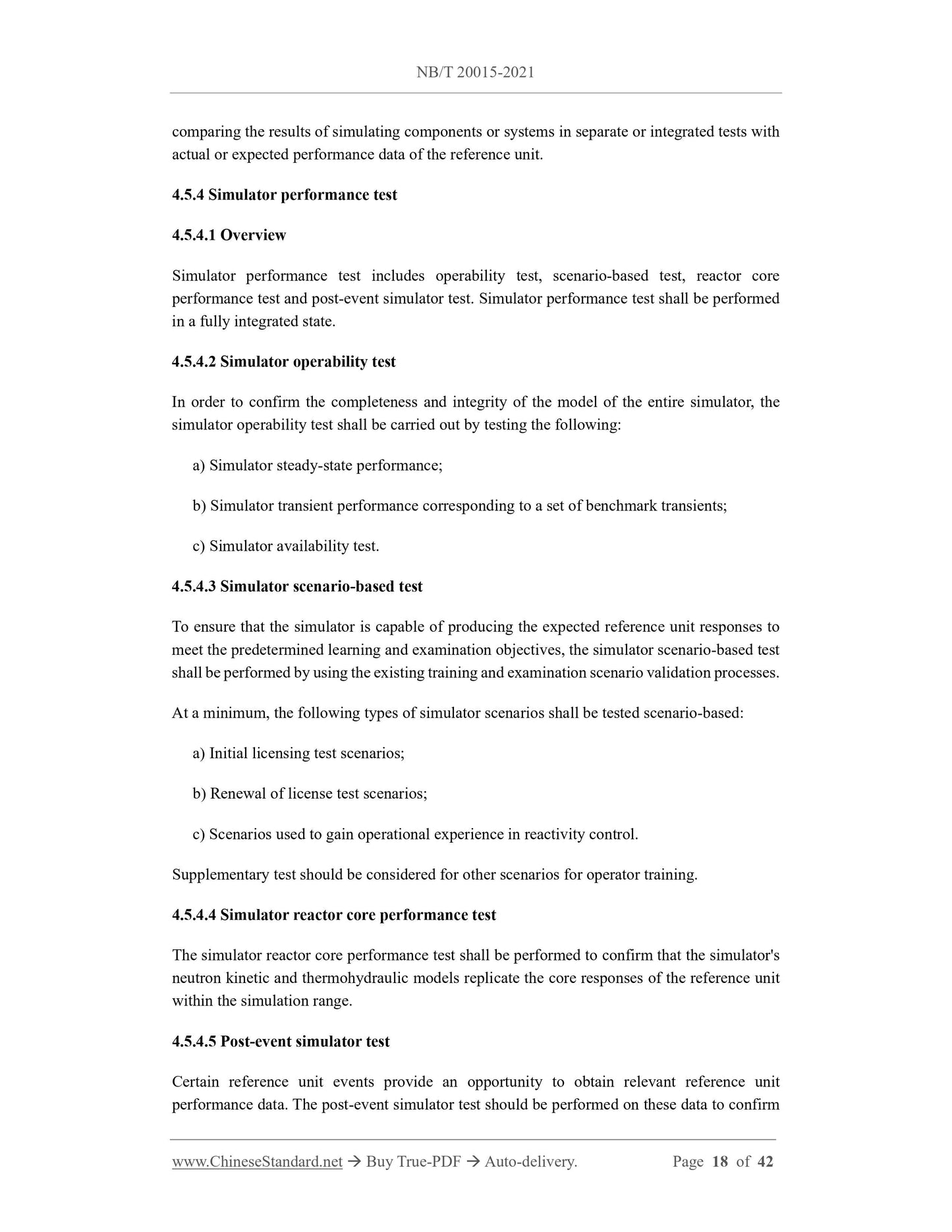
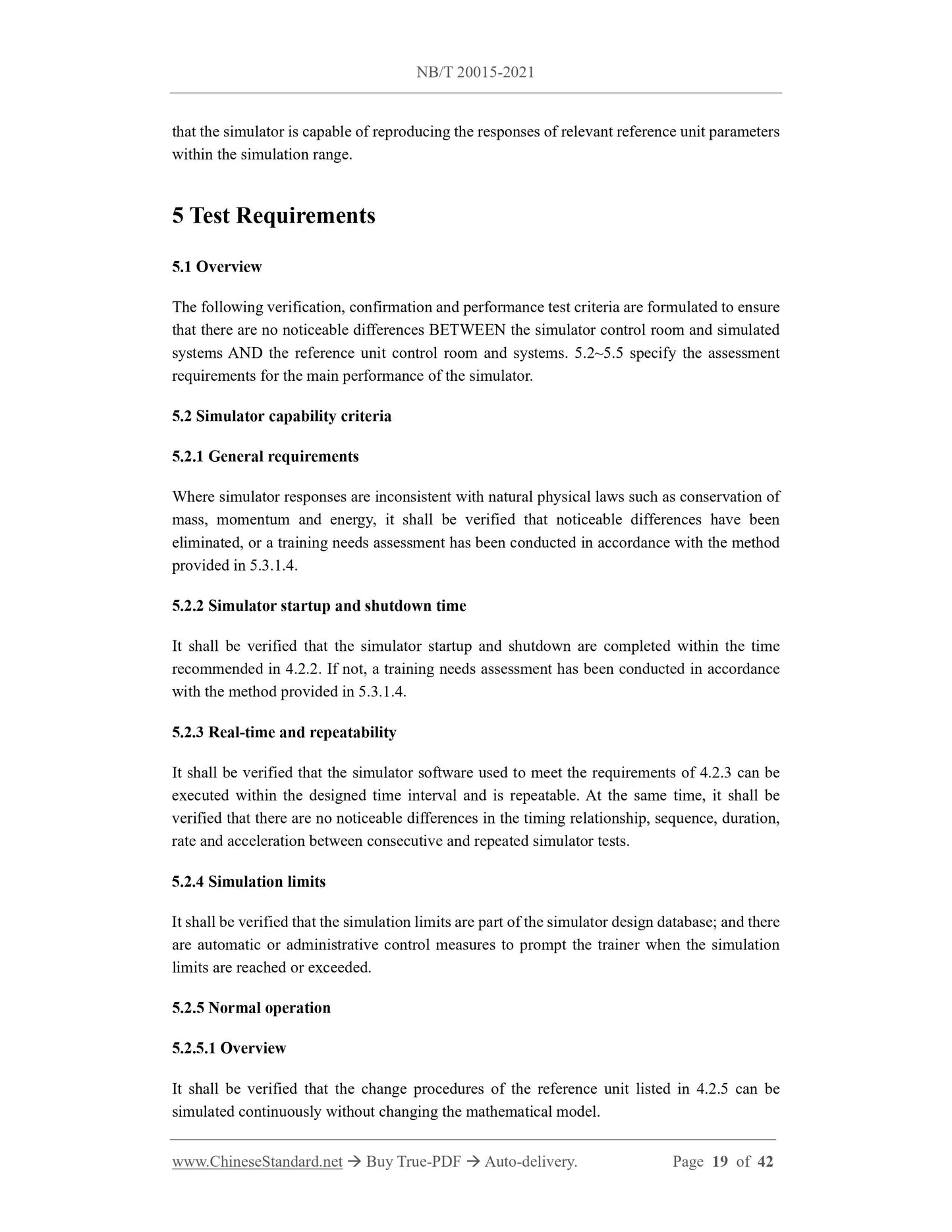
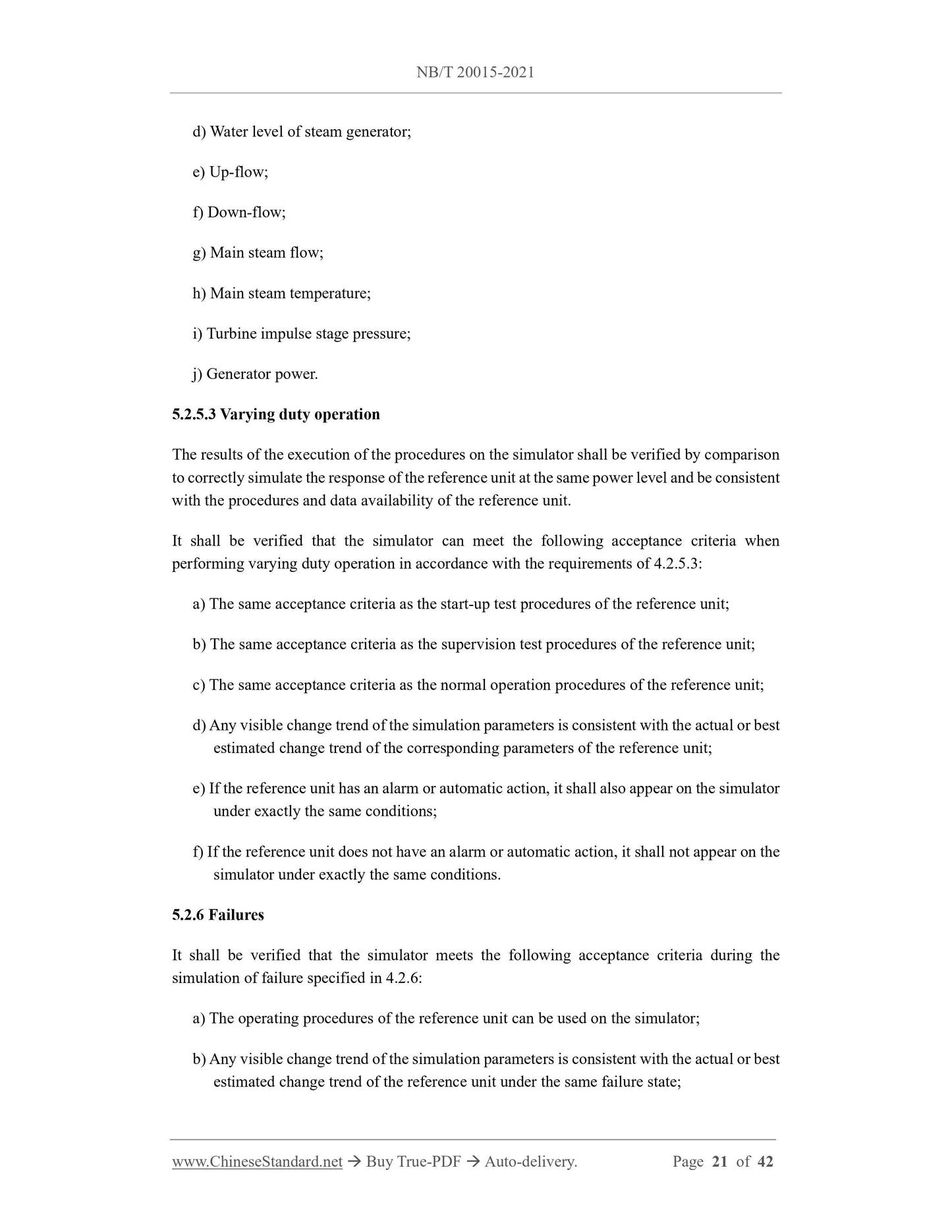