1
/
de
12
PayPal, credit cards. Download editable-PDF & invoice in 1 second!
YY/T 0681.5-2010 English PDF (YYT0681.5-2010)
YY/T 0681.5-2010 English PDF (YYT0681.5-2010)
Prix habituel
$185.00 USD
Prix habituel
Prix promotionnel
$185.00 USD
Prix unitaire
/
par
Frais d'expédition calculés à l'étape de paiement.
Impossible de charger la disponibilité du service de retrait
Delivery: 3 seconds. Download true-PDF + Invoice.
Get QUOTATION in 1-minute: Click YY/T 0681.5-2010
Historical versions: YY/T 0681.5-2010
Preview True-PDF (Reload/Scroll if blank)
YY/T 0681.5-2010: Test methods for sterile medical device package. Part 5: Detecting gross leaks in medical packaging by internal pressurization (bubble test)
YY/T 0681.5-2010
YY
PHARMACEUTICAL INDUSTRY STANDARD
OF THE PEOPLE’S REPUBLIC OF CHINA
ICS 11.080.40
C 31
Test methods for sterile medical device package - Part 5:
Detecting gross leaks in medical packaging by internal
pressurization (bubble test)
ISSUED ON: DECEMBER 27, 2010
IMPLEMENTED ON: JUNE 01, 2012
Issued by: China Food and Drug Administration
Table of Contents
Foreword ... 3
1 Scope ... 4
2 Normative references ... 4
3 Terms and definitions ... 4
4 Summary of test method ... 4
5 Meaning and application ... 5
6 Instruments ... 5
7 Sampling ... 6
8 State adjustment ... 6
9 Procedure ... 6
10 Report ... 8
Annex A (normative) Determination of test pressure ... 9
Annex B (informative) Precision and bias ... 12
Test methods for sterile medical device package - Part 5:
Detecting gross leaks in medical packaging by internal
pressurization (bubble test)
1 Scope
This Part of YY/T 0681 covers the inspection of gross leaks in medical packaging. The
sensitivity of the method has a detection probability of 81% for pore sizes above 250
μm (see Annex B). This test method can be used for pallet and multi-bag packaging.
This test method evaluates sensitivity only for spunbond polyolefin or non-breathable
packaging. The sensitivity of other packages with gas permeable materials is not
evaluated.
This method is a destructive test. In the test, it is necessary to inject air into the package
to form internal pressure.
2 Normative references
The following referenced documents are indispensable for the application of this
document. For dated references, only the edition cited applies. For undated references,
the latest edition of the referenced document (including any amendments) applies.
GB/T 2918, Plastics - Standard atmospheres for conditioning and testing
3 Terms and definitions
For the purposes of this document, the following terms and definitions apply.
3.1 breathing point pressure
The pressure at which gas begins to pass through a porous material2.
4 Summary of test method
4.1 The package is inflated underwater to a pre-determined pressure. Then observe a
2 All breathable materials are permeable to air. Whether a continuous flow of bubbles is emitted at a given internal
air pressure depends on the material pore size. Bubble flow identified at internal pressures below the breathing
point pressure can indicate a defect in the package.
continuous stream of bubbles showing a broken package.
4.2 The sensitivity of this test method depends on the differential pressure and the
method of pressurization. Determination of the test pressure for each packaging
material and size is key to obtaining reproducible results (see Annex A for procedures
for determining the test pressure). Improper pressurization of the packaging will
significantly reduce the sensitivity of the test method. Increasing the differential
pressure will increase the test sensitivity. But inflating to too high a pressure can cause
the seal to crack or air bubbles to be ejected from the breathable material to be confused
with defective air bubbles. This could lead to erroneous conclusions about the existence
of defects. A pressure limiting valve can be used in the line with pressure monitoring
device (this helps to stabilize the test pressure). It helps prevent excessive pressure on
the package (see Figure 1).
4.3 Two different test methods are given for breathable and non-breathable materials.
The main difference between the two methods (as described in Annex A) is that the
soak-through times are given for breathable materials.
5 Meaning and application
5.1 This internal pressurization test method provides a test method for detecting gross
leaks on a package that would render it non-sterile. Gross leaks on the packaging will
not guarantee product sterility. This internal pressure test method provides a practical
way to check for gross leaks on packaging.
5.2 This test method is useful for the inspection of unusual packaging materials and
pack sizes in a laboratory environment.
5.3 This test method can be applied to very large or long packages. Such packages are
not suitable for use with any other testing apparatus for testing package integrity.
5.4 This test method may be used as a means of evaluating package integrity. Since
heat-sealed packaging is designed to provide a contamination-free and sterile
environment for the product, packaging integrity is critical to consumer safety.
6 Instruments
6.1 Pressure-applying system (as shown in Figure 1): it has a pressure monitoring
instrument and a pressure limiting valve, which can provide an air pressure of 0~5 kPa.
6.2 Package piercer (such as a small slotted screwdriver or other suitable device): so
that the air source and pressure monitoring device can be inserted.
6.3 Water container: suitable for submerging the test sample for about 2.5 cm.
sample. The perforation shall be located in the center of the package as much as possible.
The hole size shall be able to allow insertion of the air source and pressure monitor and
minimize air leakage. If necessary, seal the insertion site with tape and a rubber pad as
an occluder at the perforation site.
9.1.2 Insert the air source and pressure monitor into the test sample. Submerge the
package approximately 2.5 cm under water. Apply air to the package.
NOTE 2: Using a limiter that keeps the package at the proper depth will facilitate testing.
9.1.3 Adjust gas and pressure limiting valves if necessary. Slowly inflate the package
to a pressure greater than or equal to the minimum test pressure determined in
accordance with Annex A. If necessary, adjust the pressure limiting valve and pressure
regulator to maintain constant pressure.
9.1.4 Inspect air bubble flow in areas showing damage (channels in seals, pinholes,
ruptures, tears, etc.) throughout the package. The inspection time depends on the size
of the package.
9.1.5 Remove the package from water. Mark all observed damaged areas.
9.2 Test method B -- Procedure for breathable packaging
9.2.1 If necessary, apply a barrier to the sample according to A.1.2.4.
9.2.2 Use a perforator (such as a small slotted screwdriver or other suitable device) to
punch a hole in the package, so as to insert the air source and pressure monitor into the
sample. The perforation shall be located in the center of the package as much as possible.
The hole size shall be able to allow insertion of the air source and pressure monitor and
minimize air leakage. If necessary, seal the insertion site with tape and a rubber pad as
an occluder at the perforation site.
9.2.3 Insert the air source and pressure monitor into the package. Submerge the package
about 2.5 cm under water and keep it for at least 5 s. Apply air to the package.
NOTE 3: Using a limiter will help keep the entire package at the proper depth.
9.2.4 Adjust gas and pressure limiting valves if necessary. Slowly inflate the package
to a pressure greater than or equal to the minimum test pressure determined in
accordance with Annex A. If necessary, adjust the pressure limiting valve and pressure
regulator to maintain constant pressure.
9.2.5 Inspect air bubble flow in areas showing damage (channels in seals, pinholes,
ruptures, tears, etc.) throughout the package. The inspection time depends on the size
of the package.
9.2.6 Remove the package from water. Mark all observed damaged areas.
Annex A
(normative)
Determination of test pressu...
Get QUOTATION in 1-minute: Click YY/T 0681.5-2010
Historical versions: YY/T 0681.5-2010
Preview True-PDF (Reload/Scroll if blank)
YY/T 0681.5-2010: Test methods for sterile medical device package. Part 5: Detecting gross leaks in medical packaging by internal pressurization (bubble test)
YY/T 0681.5-2010
YY
PHARMACEUTICAL INDUSTRY STANDARD
OF THE PEOPLE’S REPUBLIC OF CHINA
ICS 11.080.40
C 31
Test methods for sterile medical device package - Part 5:
Detecting gross leaks in medical packaging by internal
pressurization (bubble test)
ISSUED ON: DECEMBER 27, 2010
IMPLEMENTED ON: JUNE 01, 2012
Issued by: China Food and Drug Administration
Table of Contents
Foreword ... 3
1 Scope ... 4
2 Normative references ... 4
3 Terms and definitions ... 4
4 Summary of test method ... 4
5 Meaning and application ... 5
6 Instruments ... 5
7 Sampling ... 6
8 State adjustment ... 6
9 Procedure ... 6
10 Report ... 8
Annex A (normative) Determination of test pressure ... 9
Annex B (informative) Precision and bias ... 12
Test methods for sterile medical device package - Part 5:
Detecting gross leaks in medical packaging by internal
pressurization (bubble test)
1 Scope
This Part of YY/T 0681 covers the inspection of gross leaks in medical packaging. The
sensitivity of the method has a detection probability of 81% for pore sizes above 250
μm (see Annex B). This test method can be used for pallet and multi-bag packaging.
This test method evaluates sensitivity only for spunbond polyolefin or non-breathable
packaging. The sensitivity of other packages with gas permeable materials is not
evaluated.
This method is a destructive test. In the test, it is necessary to inject air into the package
to form internal pressure.
2 Normative references
The following referenced documents are indispensable for the application of this
document. For dated references, only the edition cited applies. For undated references,
the latest edition of the referenced document (including any amendments) applies.
GB/T 2918, Plastics - Standard atmospheres for conditioning and testing
3 Terms and definitions
For the purposes of this document, the following terms and definitions apply.
3.1 breathing point pressure
The pressure at which gas begins to pass through a porous material2.
4 Summary of test method
4.1 The package is inflated underwater to a pre-determined pressure. Then observe a
2 All breathable materials are permeable to air. Whether a continuous flow of bubbles is emitted at a given internal
air pressure depends on the material pore size. Bubble flow identified at internal pressures below the breathing
point pressure can indicate a defect in the package.
continuous stream of bubbles showing a broken package.
4.2 The sensitivity of this test method depends on the differential pressure and the
method of pressurization. Determination of the test pressure for each packaging
material and size is key to obtaining reproducible results (see Annex A for procedures
for determining the test pressure). Improper pressurization of the packaging will
significantly reduce the sensitivity of the test method. Increasing the differential
pressure will increase the test sensitivity. But inflating to too high a pressure can cause
the seal to crack or air bubbles to be ejected from the breathable material to be confused
with defective air bubbles. This could lead to erroneous conclusions about the existence
of defects. A pressure limiting valve can be used in the line with pressure monitoring
device (this helps to stabilize the test pressure). It helps prevent excessive pressure on
the package (see Figure 1).
4.3 Two different test methods are given for breathable and non-breathable materials.
The main difference between the two methods (as described in Annex A) is that the
soak-through times are given for breathable materials.
5 Meaning and application
5.1 This internal pressurization test method provides a test method for detecting gross
leaks on a package that would render it non-sterile. Gross leaks on the packaging will
not guarantee product sterility. This internal pressure test method provides a practical
way to check for gross leaks on packaging.
5.2 This test method is useful for the inspection of unusual packaging materials and
pack sizes in a laboratory environment.
5.3 This test method can be applied to very large or long packages. Such packages are
not suitable for use with any other testing apparatus for testing package integrity.
5.4 This test method may be used as a means of evaluating package integrity. Since
heat-sealed packaging is designed to provide a contamination-free and sterile
environment for the product, packaging integrity is critical to consumer safety.
6 Instruments
6.1 Pressure-applying system (as shown in Figure 1): it has a pressure monitoring
instrument and a pressure limiting valve, which can provide an air pressure of 0~5 kPa.
6.2 Package piercer (such as a small slotted screwdriver or other suitable device): so
that the air source and pressure monitoring device can be inserted.
6.3 Water container: suitable for submerging the test sample for about 2.5 cm.
sample. The perforation shall be located in the center of the package as much as possible.
The hole size shall be able to allow insertion of the air source and pressure monitor and
minimize air leakage. If necessary, seal the insertion site with tape and a rubber pad as
an occluder at the perforation site.
9.1.2 Insert the air source and pressure monitor into the test sample. Submerge the
package approximately 2.5 cm under water. Apply air to the package.
NOTE 2: Using a limiter that keeps the package at the proper depth will facilitate testing.
9.1.3 Adjust gas and pressure limiting valves if necessary. Slowly inflate the package
to a pressure greater than or equal to the minimum test pressure determined in
accordance with Annex A. If necessary, adjust the pressure limiting valve and pressure
regulator to maintain constant pressure.
9.1.4 Inspect air bubble flow in areas showing damage (channels in seals, pinholes,
ruptures, tears, etc.) throughout the package. The inspection time depends on the size
of the package.
9.1.5 Remove the package from water. Mark all observed damaged areas.
9.2 Test method B -- Procedure for breathable packaging
9.2.1 If necessary, apply a barrier to the sample according to A.1.2.4.
9.2.2 Use a perforator (such as a small slotted screwdriver or other suitable device) to
punch a hole in the package, so as to insert the air source and pressure monitor into the
sample. The perforation shall be located in the center of the package as much as possible.
The hole size shall be able to allow insertion of the air source and pressure monitor and
minimize air leakage. If necessary, seal the insertion site with tape and a rubber pad as
an occluder at the perforation site.
9.2.3 Insert the air source and pressure monitor into the package. Submerge the package
about 2.5 cm under water and keep it for at least 5 s. Apply air to the package.
NOTE 3: Using a limiter will help keep the entire package at the proper depth.
9.2.4 Adjust gas and pressure limiting valves if necessary. Slowly inflate the package
to a pressure greater than or equal to the minimum test pressure determined in
accordance with Annex A. If necessary, adjust the pressure limiting valve and pressure
regulator to maintain constant pressure.
9.2.5 Inspect air bubble flow in areas showing damage (channels in seals, pinholes,
ruptures, tears, etc.) throughout the package. The inspection time depends on the size
of the package.
9.2.6 Remove the package from water. Mark all observed damaged areas.
Annex A
(normative)
Determination of test pressu...
Share
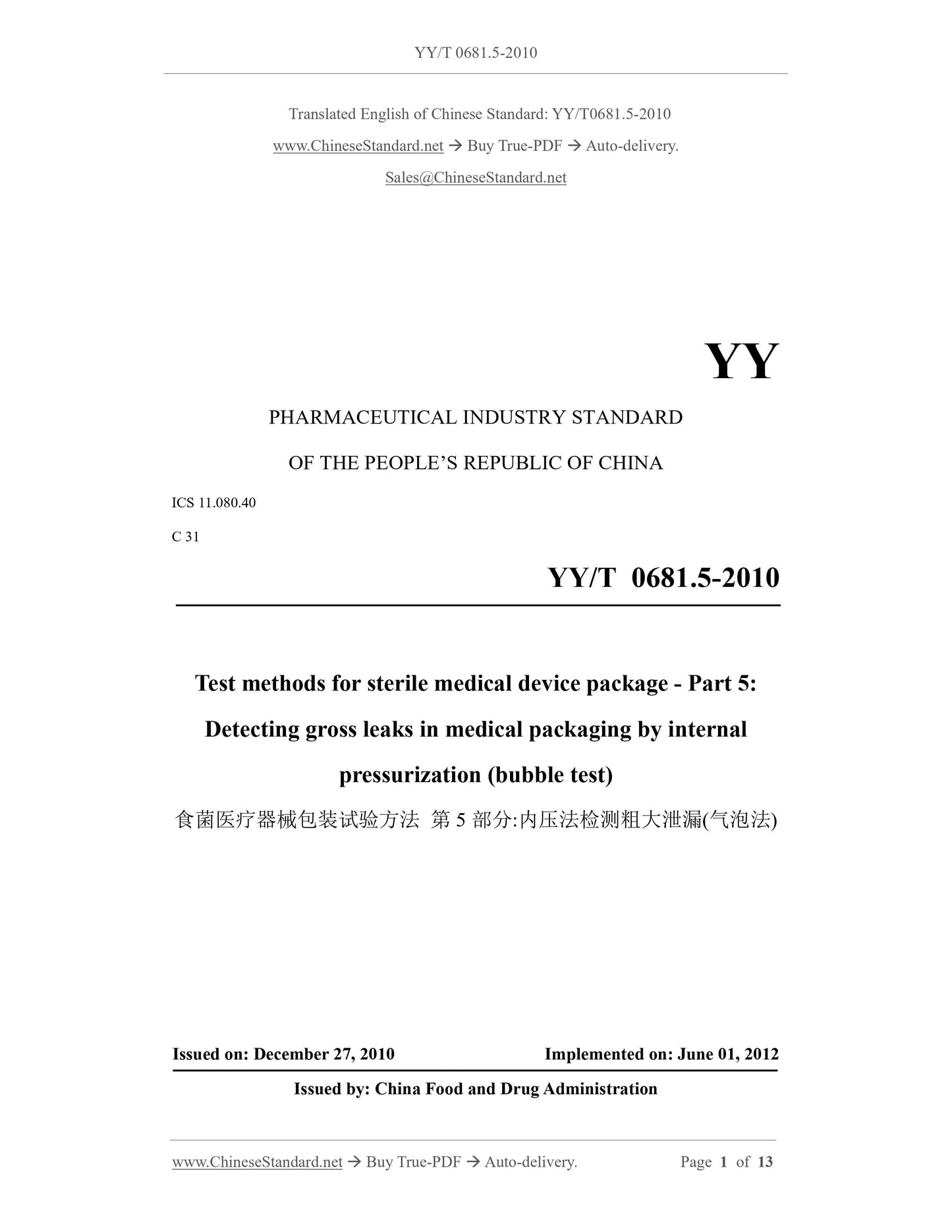

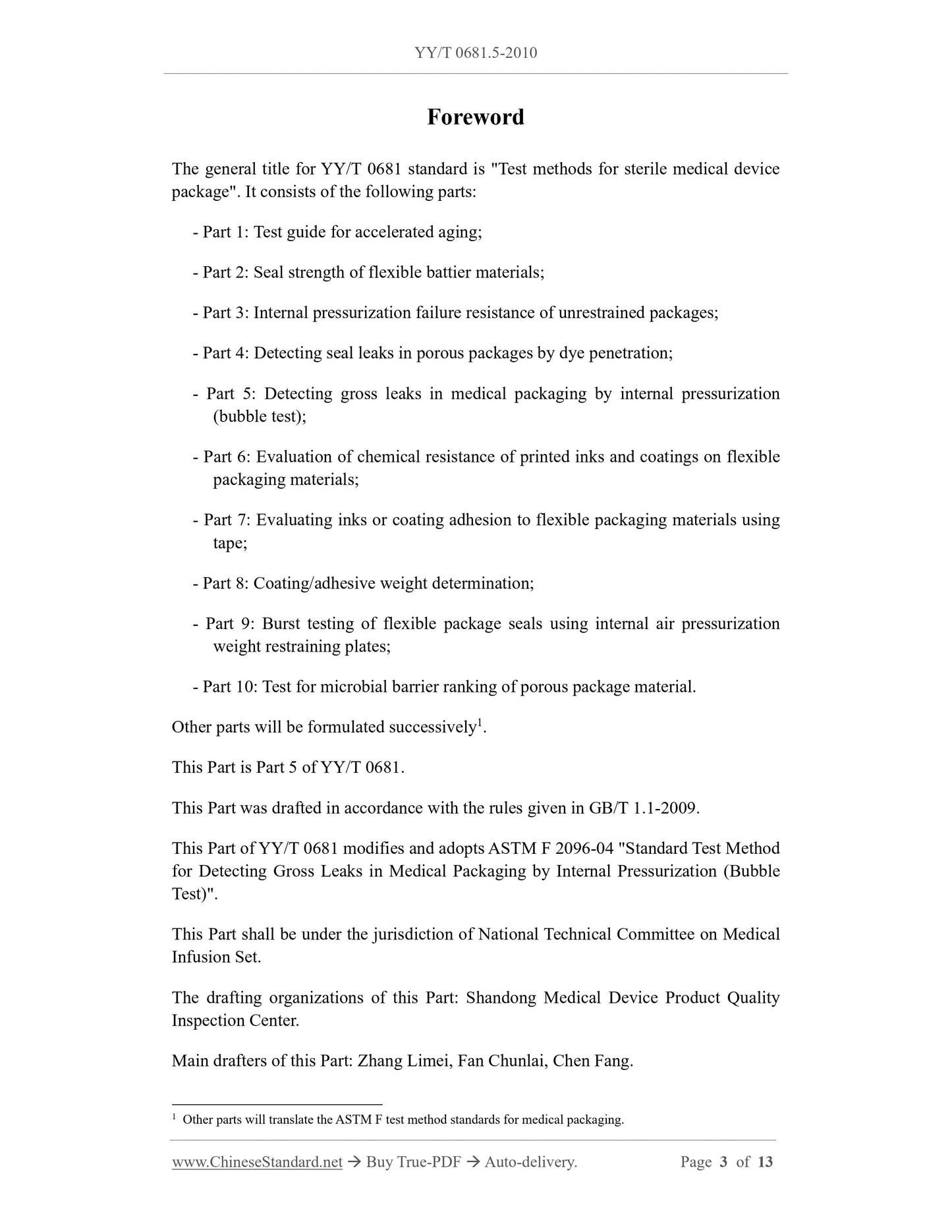
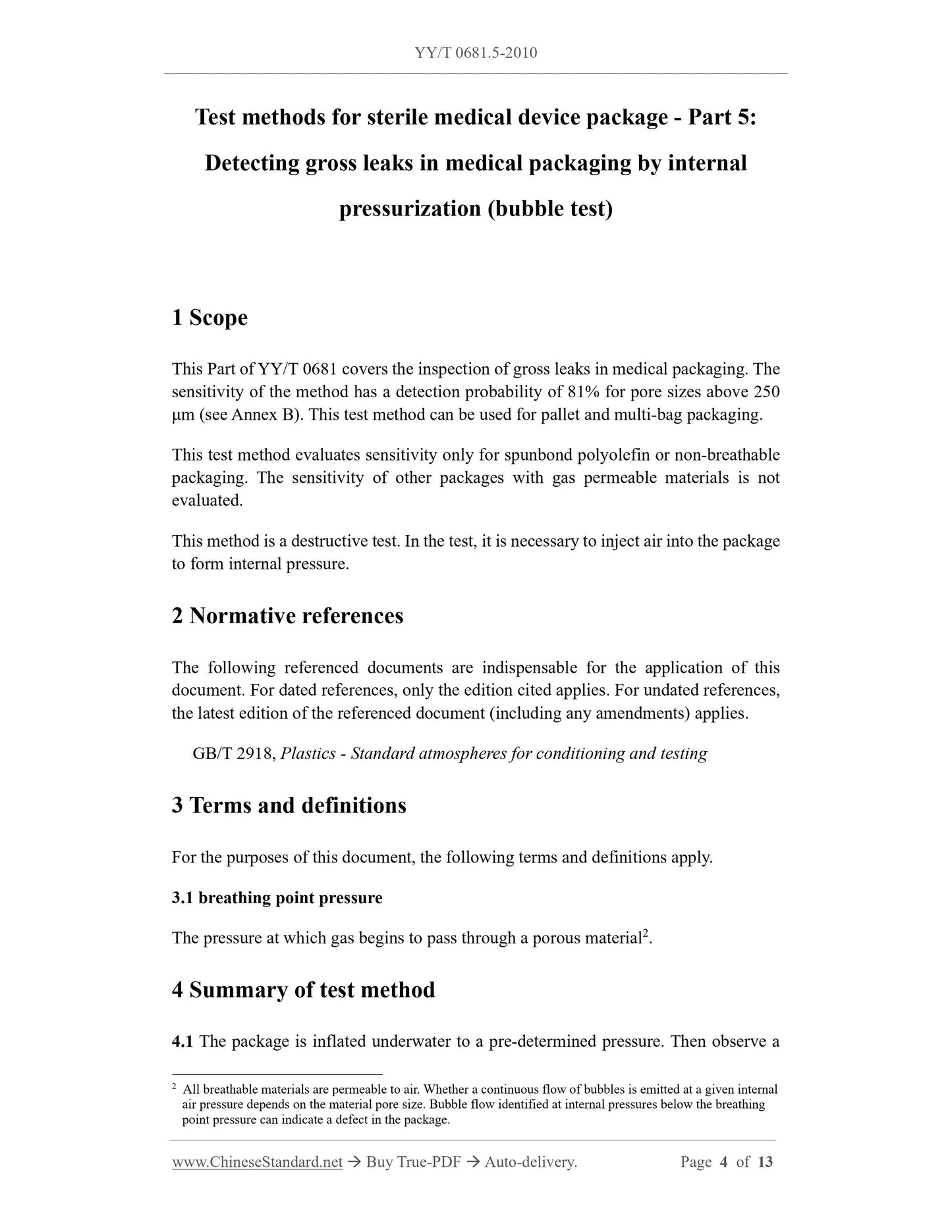
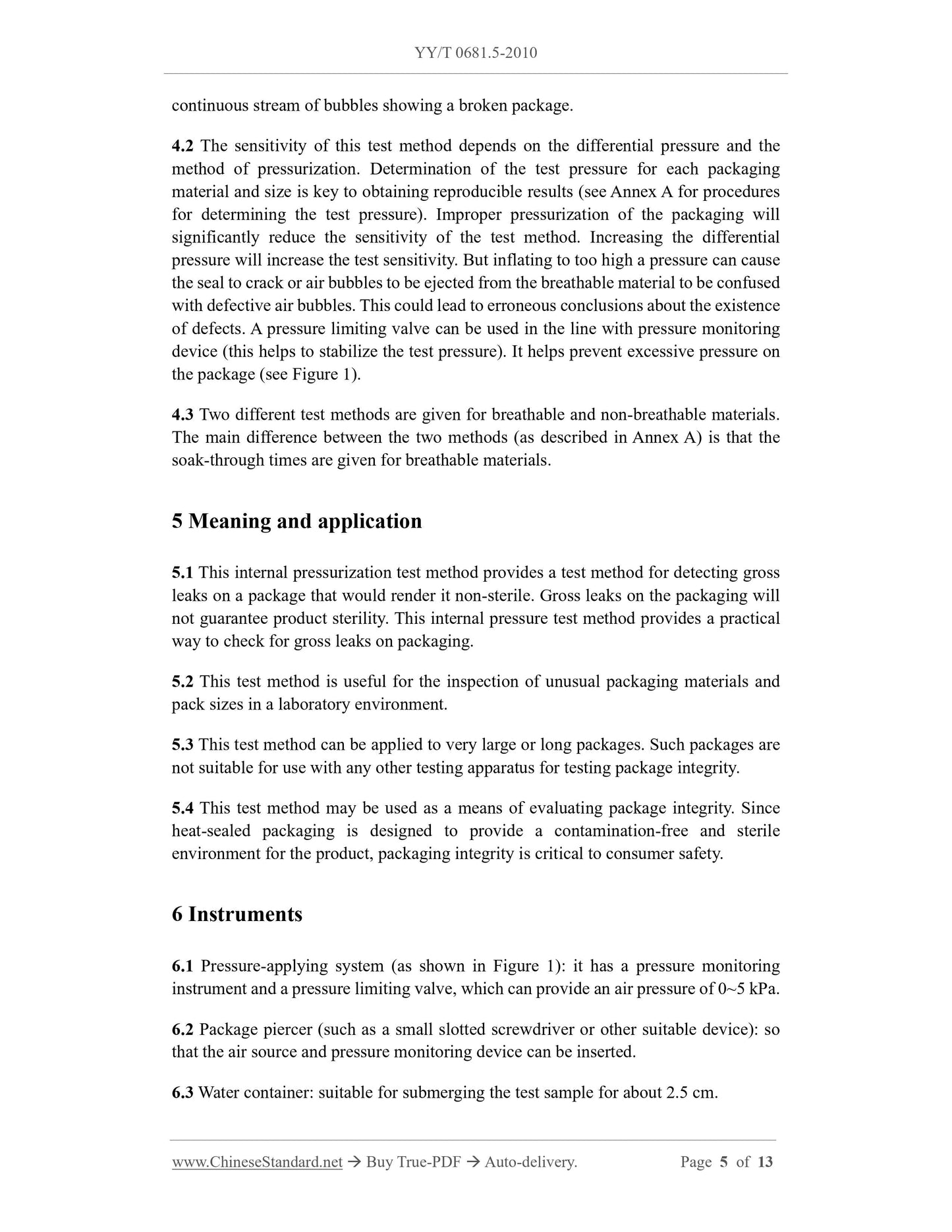
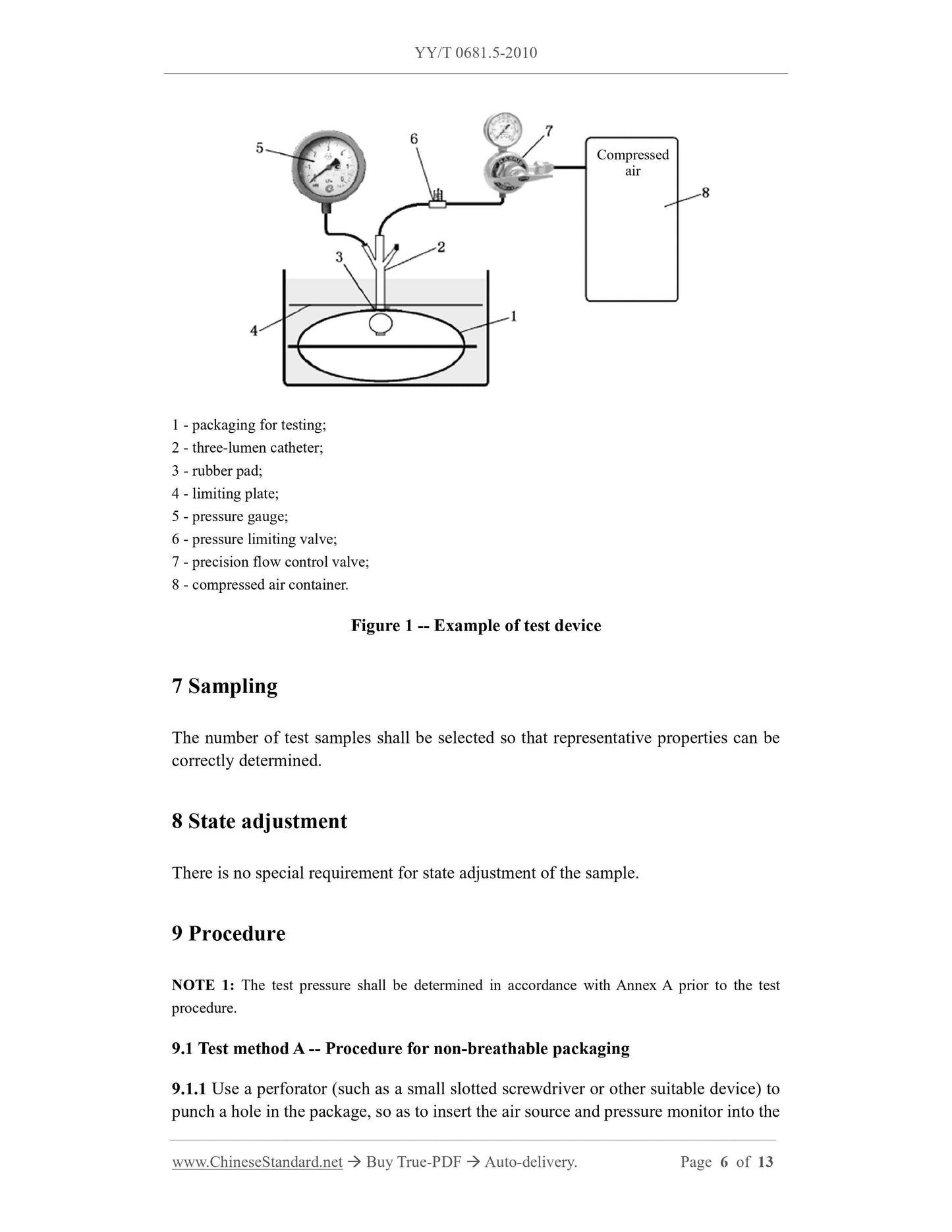
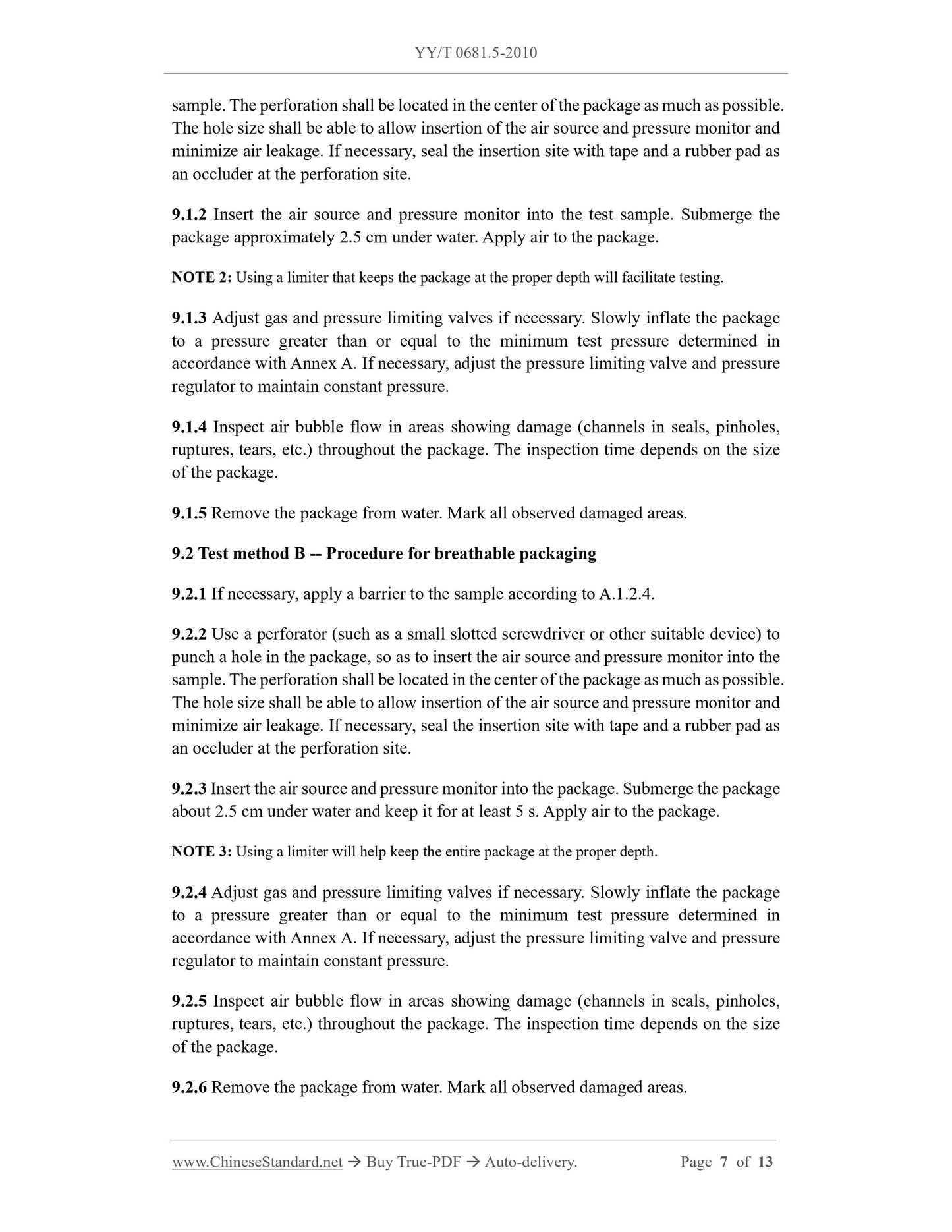
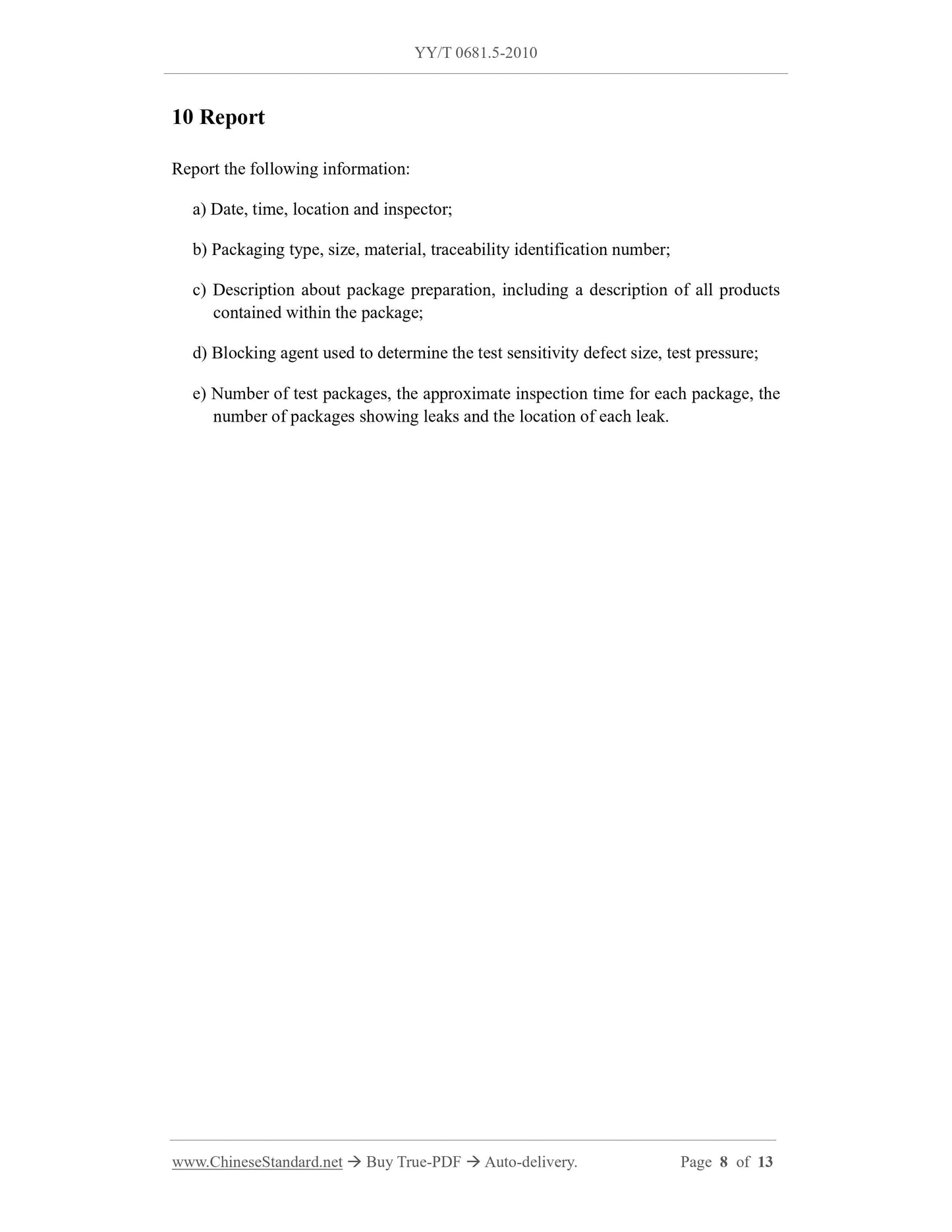
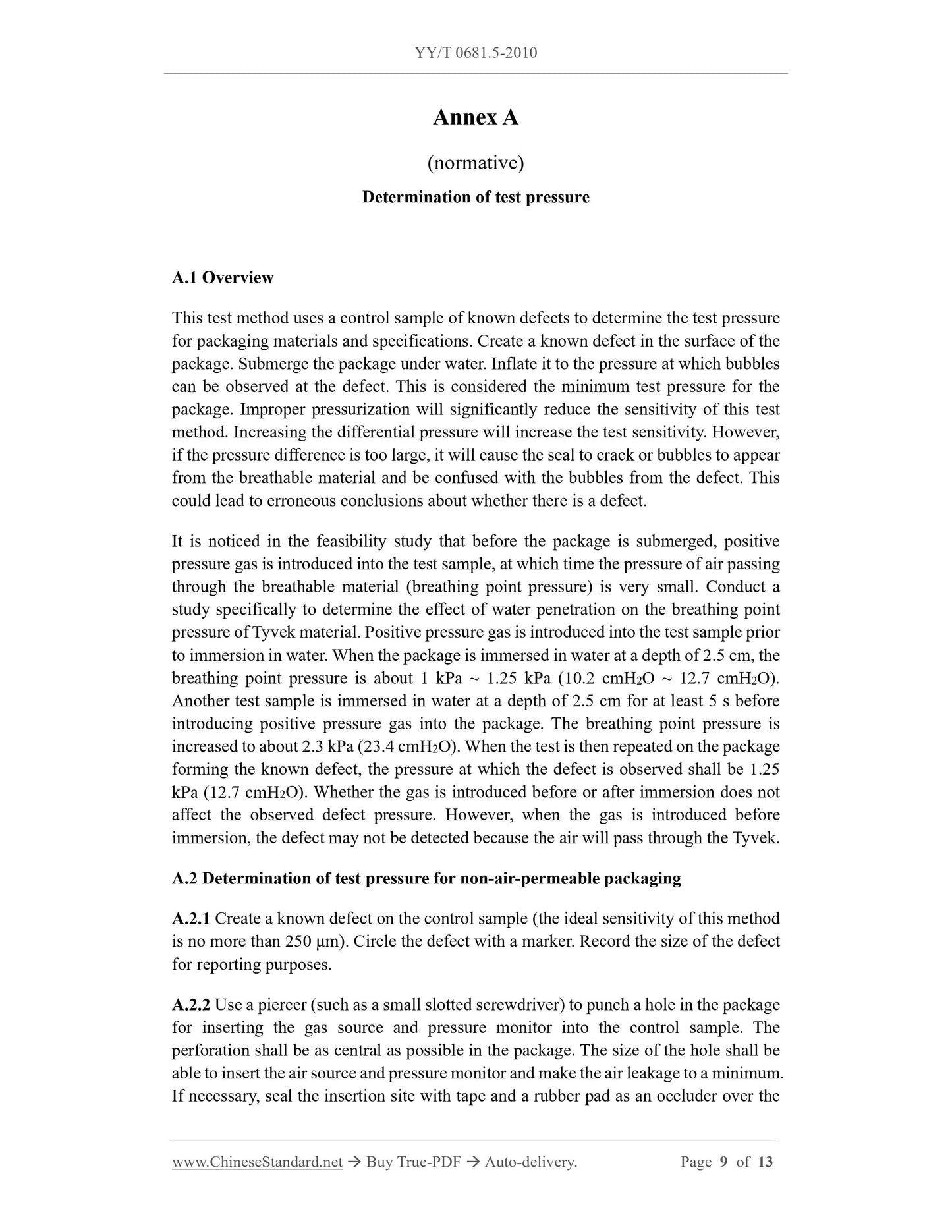
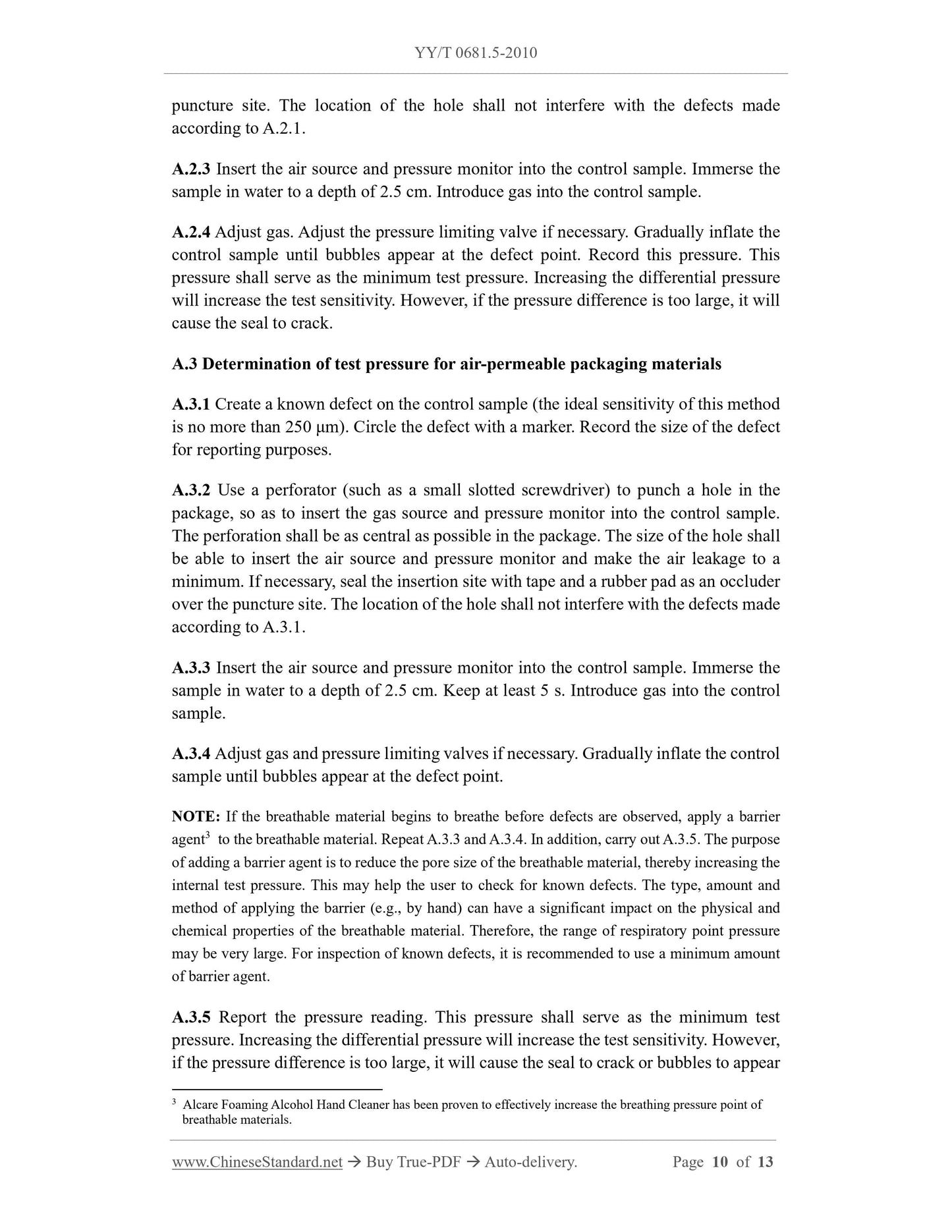
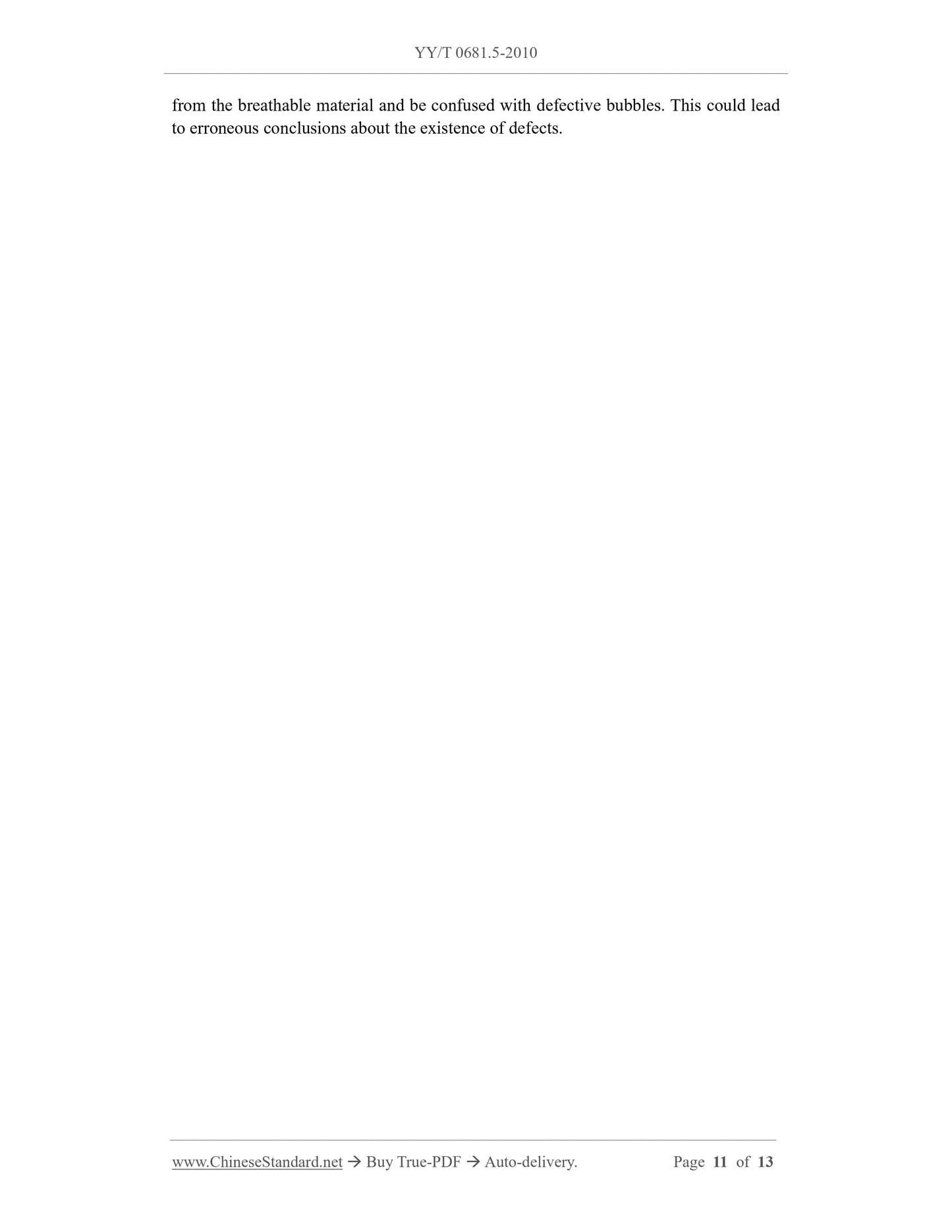
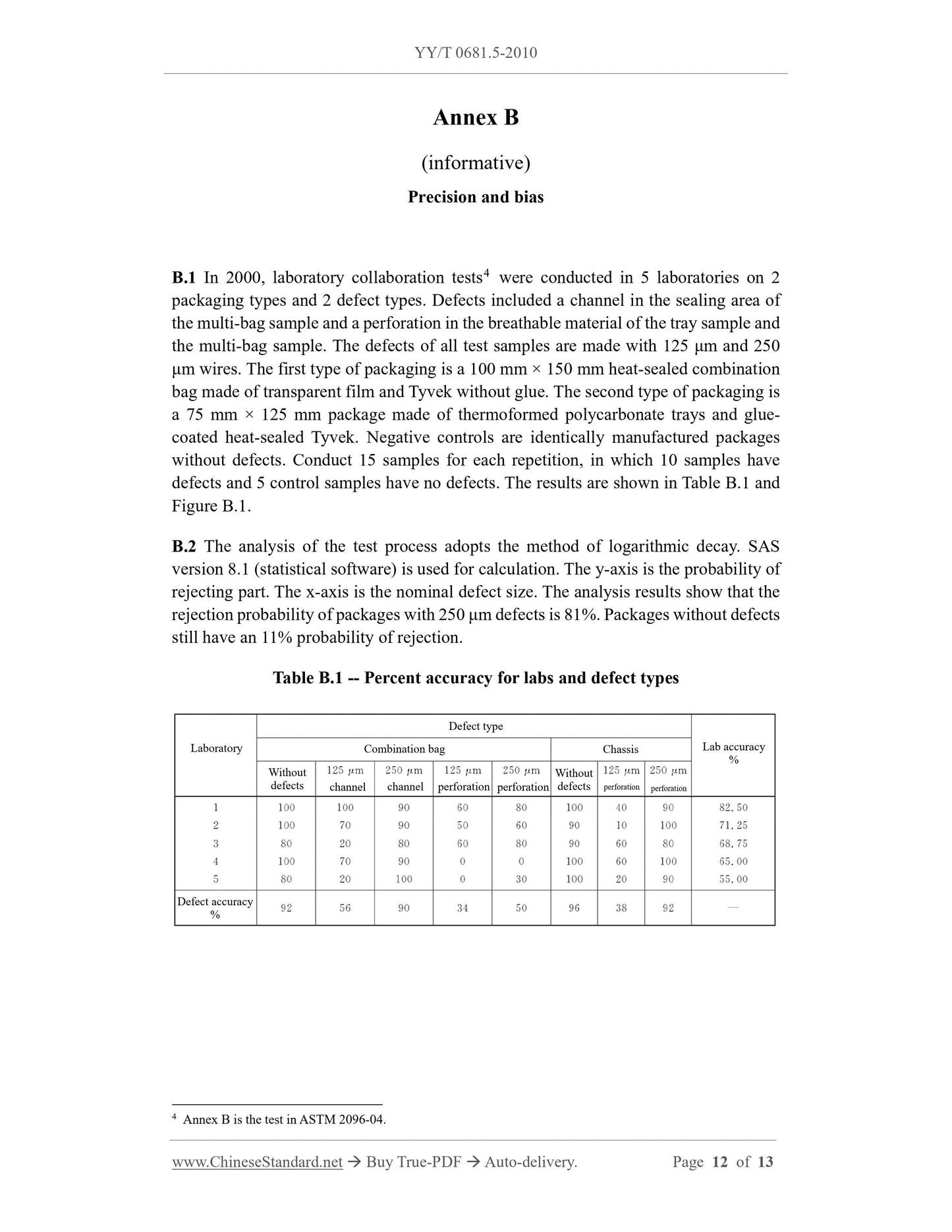