1
/
su
12
PayPal, credit cards. Download editable-PDF and invoice in 1 second!
TB/T 2817-1997 English PDF (TBT2817-1997)
TB/T 2817-1997 English PDF (TBT2817-1997)
Prezzo di listino
$165.00 USD
Prezzo di listino
Prezzo scontato
$165.00 USD
Prezzo unitario
/
per
Spese di spedizione calcolate al check-out.
Impossibile caricare la disponibilità di ritiro
Delivery: 3 seconds. Download true-PDF + Invoice.
Get QUOTATION in 1-minute: Click TB/T 2817-1997
Historical versions: TB/T 2817-1997
Preview True-PDF (Reload/Scroll if blank)
TB/T 2817-1997: Technical specification for solid rolled steel wheel for rolling stock
TB/T 2817-1997
TB
RAILWAY INDUSTRY STANDARD
OF THE PEOPLE’S REPUBLIC OF CHINA
Technical Specification for
Solid Rolled Steel Wheel for Rolling Stock
ISSUED ON. JULY 10, 1997
IMPLEMENTED ON. JANUARY 1, 1998
Issued by. Ministry of Railways of the People's Republic of China
Table of Contents
Forward ... 3
1 Scope ... 4
2 Normative References ... 4
3 Type Size of Wheel ... 5
4 Technical Requirements ... 7
5 Test Methods ... 15
6 Inspection Rules ... 19
7 Package, marking, and Quality Certificate ... 20
8 Warranty ... 22
Appendix A (Standard’s Appendix) Shot Peening Strengthening of Wheel
... 24
Forward
This Standard was prepared on the basis of equivalently adopting UIC812-3 Technical
Specification for the Supply of Non-Alloy Steel Solid Rolled Steel Wheel for
Railway Locomotive; some provisions of national and other standards are
supplemented for adapting the national situation.
This Standard was proposed by the Ministry of Railway Science and Technology
Development Department.
This Standard shall be under the jurisdiction of Standards and Metrology Research
Institute of the Ministry of Railway.
Drafting organizations of this Standard. Standards and Metrology Research Institute
of the Ministry of Railway, Metals and Chemistry Research Institute, China Academy
of Railway, and Sifang Rolling Stock Research Institute of the Ministry of Railway.
Chief drafting staffs of this Standard. Han Ying, Zhang Yingzhi, Zheng Weisheng, Liu
Xinming, and Zhang Bin.
Technical Specification for
Solid Rolled Steel Wheel for Rolling Stock
1 Scope
This Standard specifies the type size and geometric tolerance, technical requirements,
test methods, inspection rules, package, marking and quality certificate and etc. of
solid rolled steel wheel (hereinafter refers to wheel) for quasi rail vehicle.
This Standard is applicable to the manufacturing, ordering, and testing of solid rolled
steel wheel for rolling stock with passenger train speed ≤160km/h, and freight train
speed ≤120km/h.
2 Normative References
The following normative documents contain provisions which, through reference in this
Standard, constitute provisions of this Standard. At the time of publication, the editions
indicated were valid. All the standards will be revised and all parties who reach an
agreement according to this Standard are encouraged to study whether the latest
editions of the following standards are applicable.
GB 222-84 Method of Sampling Steel for Determination of Chemical Composition
and Permissible Variations for Product Analysis
GB 223 Methods for Chemical Analysis of Iron, Steel and Alloy
GB 226-91 Test Method for Macrostructure and Defect of Steel by Etching
GB 228-87 Method of Tensile Tests for Metal
GB/T 229-1994 Metallic Materials-Charpy Notch (U-Shaped Notch) Impact Test
GB 231-84 Test Method for Brinell Hardness of Metal
GB 8601-88 Solid Rolled Steel Wheel for Railway
GB 10561-89 Microscopic Testing Method for the Non - Metallic Inclusions in Steel
TB 1967-87 Wheel Profile for Locomotive and Car
ZBY 230-84 Commonly Used Specification for A-Mode Ultrasonic Flaw Detector
4.1.3 Allowable tolerances (%) of chemical composition analysis and melting
analysis of finished wheel are shown as follows.
C. -0.02 or +0.03 P. +0.005
Si. -0.02 or +0.03 S. +0.005
Mn. -0.04 or +0.05
4.2 Wheel manufacture
4.2.1 Steel making
Wheel steel shall be manufactured by excellent-quality killed steel molten in electric
furnace, open hearth, or revolving furnace; if it is agreed by the buyer and seller, other
melting method can also be adopted, and go through the refining treatment outside of
the furnace, the hydrogen content in the molten steel is ≤3.5ppm. Steel ingots must be
casted from the bottom. After stripping, the steel ingots must conduct fully slow-cooling
in the slow-cooling pit. When it undertakes vacuum degassing treatment, it can realize
stack-cooling directly.
4.2.2 Wheel thermoforming
Wheel shall be manufactured by the steel ingots with head-cutting, and the head-
cutting amount shall be sufficient to eliminate the harmful part that may influence the
wheel quality on two sides of the steel ingots, all surfaces of the steel ingots must not
have any defects that may influence the rolling quality.
During the thermoforming heating period, the over-burning and over-heating of wheel
steel billet shall be avoided, thermoforming heating temperature shall not exceed
1250Ԩ, and the thermal machining final temperature shall be controlled within the
range of 850Ԩ~1000Ԩ.
After the thermoforming of wheel manufactured by steel that doesn’t carry out vacuum
degassing treatment, measures to eliminate white spots must be taken, such as
isothermal, slow cooling, and etc..
4.2.3 Wheel’s identification marking during the manufacturing process
All steel ingots, steel billets, cutting bars, and wheels must be marked clearly on each
process, so that each wheel can be identified before delivery. If such mark is different
from the final mark of the finished wheel, then such mark shall be as shallow as
possible, even leaves no trace on the finished wheel.
4.2.4 Wheel heat treatment
Wheel rim shall be carried out quenched and tempered treatment, water shall be
prevented to enter into the spoke during the quenching period.
No more than Grade-2 general looseness, center looseness, segregation, and non-
metallic inclusion are allowed to exist.
4.5 Non-metallic inclusion
In the three specimens of rim, the grade of each inclusion shall conform to the following
requirements. Class B (alumina inclusion) shall be no more than Grade 1; Class A
(sulphide inclusion), Class C (silicate inclusion), and Class D (globular oxide) shall be
no more than Grade 3 respectively.
4.6 Ultrasonic flaw detection
All wheels, after the heat treatment and mechanical machining, shall be carried out
ultrasonic flaw detection one by one.
To detect the internal discontinuity of all wheels’ rims, adopt the following specified
equipment to conduct ultrasonic flaw detection as per the following procedures.
4.6.1 Flaw detection equipment shall conform to the provisions of ZB Y 230-84, and
its frequency band shall meet the requirements of flaw detection method.
4.6.2 Probe operating frequency. 2.25~5MHz.
4.6.3 Probe structure and dimension shall be applicable to all testing methods.
4.6.4 Ultrasonic flaw detector shall be equipped with defect automatic alarm system.
4.6.5 Proper couplant shall be used between the testing surface and the probe,
however, the impermissible corrosion shall not be generated on the rim. The same
couplant shall be used for the adjusting instrument, calibrating instrument, and in the
testing period.
4.6.6 One wheel or one segment of rim, which has artificial simulation defect shall be
used as comparison test block to calibrate the instrument. Instrument sensitivity shall
be adjusted to make the artificial defects specified in Clause 4.6.7, Clause 4.6.8, and
Clause 4.6.9 generate 1/2 full magnitude of the reflected echo.
4.6.7 During the axial test period, the artificial defect shall be placed at half thickness
of rim, the diameter perpendicular to rim side face is about 3.2mm, and the depth of
flat-bottom hole is about 25~38mm (see Figure 2).
formal table for future checking.
4.7.3 Lighting illumination shall be checked once a week, the test results shall be
recorded in the specified table for future checking.
Get QUOTATION in 1-minute: Click TB/T 2817-1997
Historical versions: TB/T 2817-1997
Preview True-PDF (Reload/Scroll if blank)
TB/T 2817-1997: Technical specification for solid rolled steel wheel for rolling stock
TB/T 2817-1997
TB
RAILWAY INDUSTRY STANDARD
OF THE PEOPLE’S REPUBLIC OF CHINA
Technical Specification for
Solid Rolled Steel Wheel for Rolling Stock
ISSUED ON. JULY 10, 1997
IMPLEMENTED ON. JANUARY 1, 1998
Issued by. Ministry of Railways of the People's Republic of China
Table of Contents
Forward ... 3
1 Scope ... 4
2 Normative References ... 4
3 Type Size of Wheel ... 5
4 Technical Requirements ... 7
5 Test Methods ... 15
6 Inspection Rules ... 19
7 Package, marking, and Quality Certificate ... 20
8 Warranty ... 22
Appendix A (Standard’s Appendix) Shot Peening Strengthening of Wheel
... 24
Forward
This Standard was prepared on the basis of equivalently adopting UIC812-3 Technical
Specification for the Supply of Non-Alloy Steel Solid Rolled Steel Wheel for
Railway Locomotive; some provisions of national and other standards are
supplemented for adapting the national situation.
This Standard was proposed by the Ministry of Railway Science and Technology
Development Department.
This Standard shall be under the jurisdiction of Standards and Metrology Research
Institute of the Ministry of Railway.
Drafting organizations of this Standard. Standards and Metrology Research Institute
of the Ministry of Railway, Metals and Chemistry Research Institute, China Academy
of Railway, and Sifang Rolling Stock Research Institute of the Ministry of Railway.
Chief drafting staffs of this Standard. Han Ying, Zhang Yingzhi, Zheng Weisheng, Liu
Xinming, and Zhang Bin.
Technical Specification for
Solid Rolled Steel Wheel for Rolling Stock
1 Scope
This Standard specifies the type size and geometric tolerance, technical requirements,
test methods, inspection rules, package, marking and quality certificate and etc. of
solid rolled steel wheel (hereinafter refers to wheel) for quasi rail vehicle.
This Standard is applicable to the manufacturing, ordering, and testing of solid rolled
steel wheel for rolling stock with passenger train speed ≤160km/h, and freight train
speed ≤120km/h.
2 Normative References
The following normative documents contain provisions which, through reference in this
Standard, constitute provisions of this Standard. At the time of publication, the editions
indicated were valid. All the standards will be revised and all parties who reach an
agreement according to this Standard are encouraged to study whether the latest
editions of the following standards are applicable.
GB 222-84 Method of Sampling Steel for Determination of Chemical Composition
and Permissible Variations for Product Analysis
GB 223 Methods for Chemical Analysis of Iron, Steel and Alloy
GB 226-91 Test Method for Macrostructure and Defect of Steel by Etching
GB 228-87 Method of Tensile Tests for Metal
GB/T 229-1994 Metallic Materials-Charpy Notch (U-Shaped Notch) Impact Test
GB 231-84 Test Method for Brinell Hardness of Metal
GB 8601-88 Solid Rolled Steel Wheel for Railway
GB 10561-89 Microscopic Testing Method for the Non - Metallic Inclusions in Steel
TB 1967-87 Wheel Profile for Locomotive and Car
ZBY 230-84 Commonly Used Specification for A-Mode Ultrasonic Flaw Detector
4.1.3 Allowable tolerances (%) of chemical composition analysis and melting
analysis of finished wheel are shown as follows.
C. -0.02 or +0.03 P. +0.005
Si. -0.02 or +0.03 S. +0.005
Mn. -0.04 or +0.05
4.2 Wheel manufacture
4.2.1 Steel making
Wheel steel shall be manufactured by excellent-quality killed steel molten in electric
furnace, open hearth, or revolving furnace; if it is agreed by the buyer and seller, other
melting method can also be adopted, and go through the refining treatment outside of
the furnace, the hydrogen content in the molten steel is ≤3.5ppm. Steel ingots must be
casted from the bottom. After stripping, the steel ingots must conduct fully slow-cooling
in the slow-cooling pit. When it undertakes vacuum degassing treatment, it can realize
stack-cooling directly.
4.2.2 Wheel thermoforming
Wheel shall be manufactured by the steel ingots with head-cutting, and the head-
cutting amount shall be sufficient to eliminate the harmful part that may influence the
wheel quality on two sides of the steel ingots, all surfaces of the steel ingots must not
have any defects that may influence the rolling quality.
During the thermoforming heating period, the over-burning and over-heating of wheel
steel billet shall be avoided, thermoforming heating temperature shall not exceed
1250Ԩ, and the thermal machining final temperature shall be controlled within the
range of 850Ԩ~1000Ԩ.
After the thermoforming of wheel manufactured by steel that doesn’t carry out vacuum
degassing treatment, measures to eliminate white spots must be taken, such as
isothermal, slow cooling, and etc..
4.2.3 Wheel’s identification marking during the manufacturing process
All steel ingots, steel billets, cutting bars, and wheels must be marked clearly on each
process, so that each wheel can be identified before delivery. If such mark is different
from the final mark of the finished wheel, then such mark shall be as shallow as
possible, even leaves no trace on the finished wheel.
4.2.4 Wheel heat treatment
Wheel rim shall be carried out quenched and tempered treatment, water shall be
prevented to enter into the spoke during the quenching period.
No more than Grade-2 general looseness, center looseness, segregation, and non-
metallic inclusion are allowed to exist.
4.5 Non-metallic inclusion
In the three specimens of rim, the grade of each inclusion shall conform to the following
requirements. Class B (alumina inclusion) shall be no more than Grade 1; Class A
(sulphide inclusion), Class C (silicate inclusion), and Class D (globular oxide) shall be
no more than Grade 3 respectively.
4.6 Ultrasonic flaw detection
All wheels, after the heat treatment and mechanical machining, shall be carried out
ultrasonic flaw detection one by one.
To detect the internal discontinuity of all wheels’ rims, adopt the following specified
equipment to conduct ultrasonic flaw detection as per the following procedures.
4.6.1 Flaw detection equipment shall conform to the provisions of ZB Y 230-84, and
its frequency band shall meet the requirements of flaw detection method.
4.6.2 Probe operating frequency. 2.25~5MHz.
4.6.3 Probe structure and dimension shall be applicable to all testing methods.
4.6.4 Ultrasonic flaw detector shall be equipped with defect automatic alarm system.
4.6.5 Proper couplant shall be used between the testing surface and the probe,
however, the impermissible corrosion shall not be generated on the rim. The same
couplant shall be used for the adjusting instrument, calibrating instrument, and in the
testing period.
4.6.6 One wheel or one segment of rim, which has artificial simulation defect shall be
used as comparison test block to calibrate the instrument. Instrument sensitivity shall
be adjusted to make the artificial defects specified in Clause 4.6.7, Clause 4.6.8, and
Clause 4.6.9 generate 1/2 full magnitude of the reflected echo.
4.6.7 During the axial test period, the artificial defect shall be placed at half thickness
of rim, the diameter perpendicular to rim side face is about 3.2mm, and the depth of
flat-bottom hole is about 25~38mm (see Figure 2).
formal table for future checking.
4.7.3 Lighting illumination shall be checked once a week, the test results shall be
recorded in the specified table for future checking.
Share
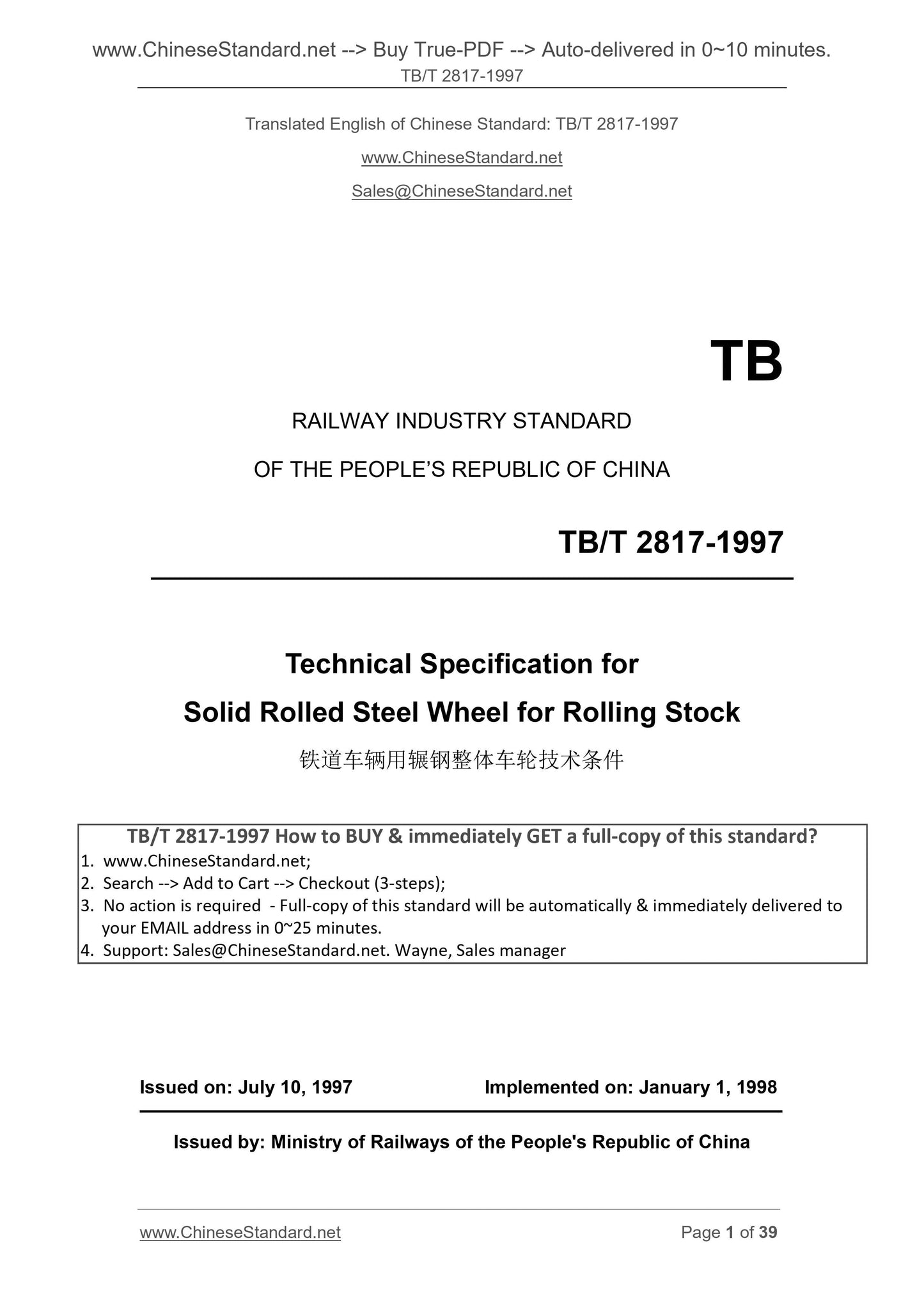
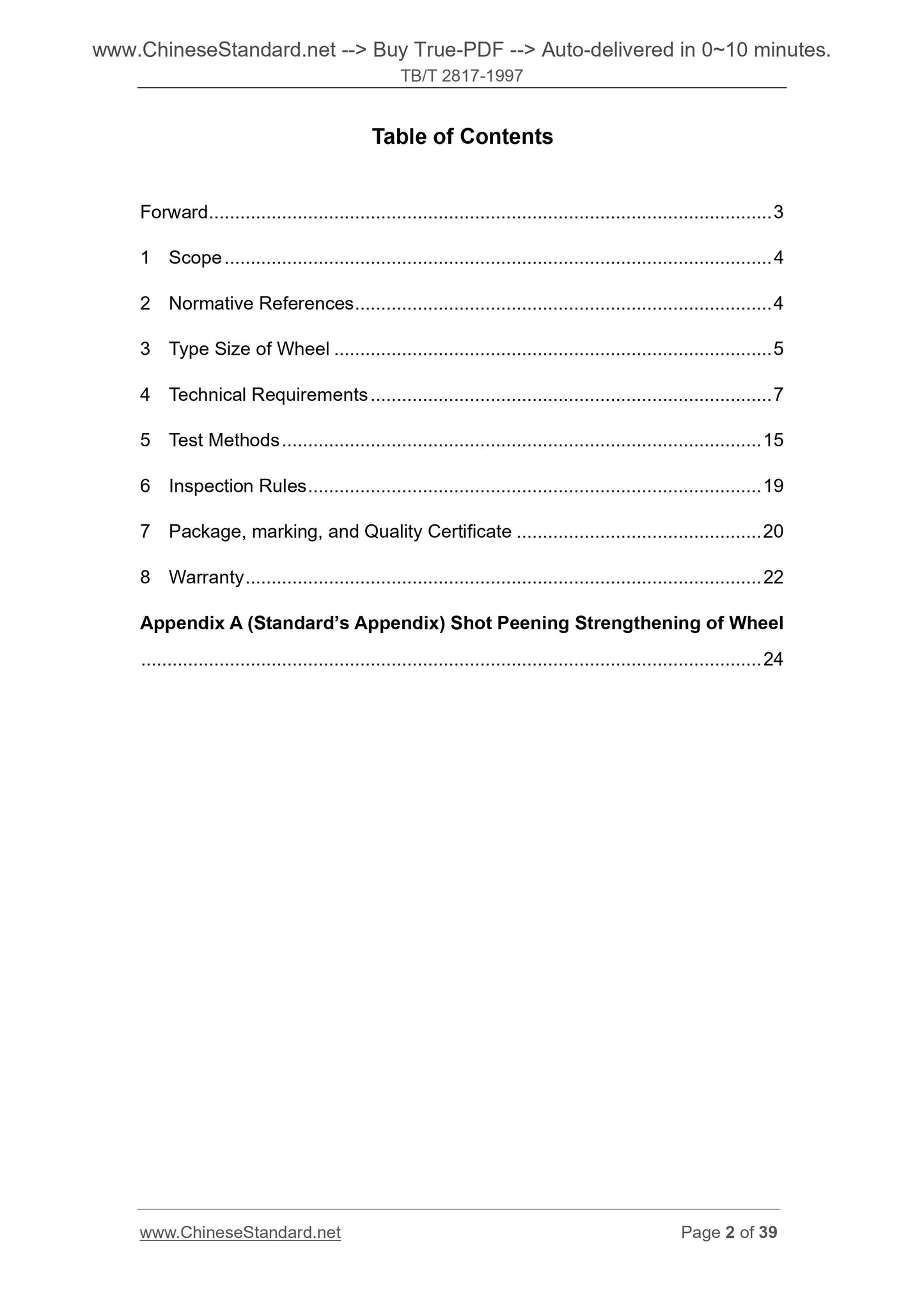
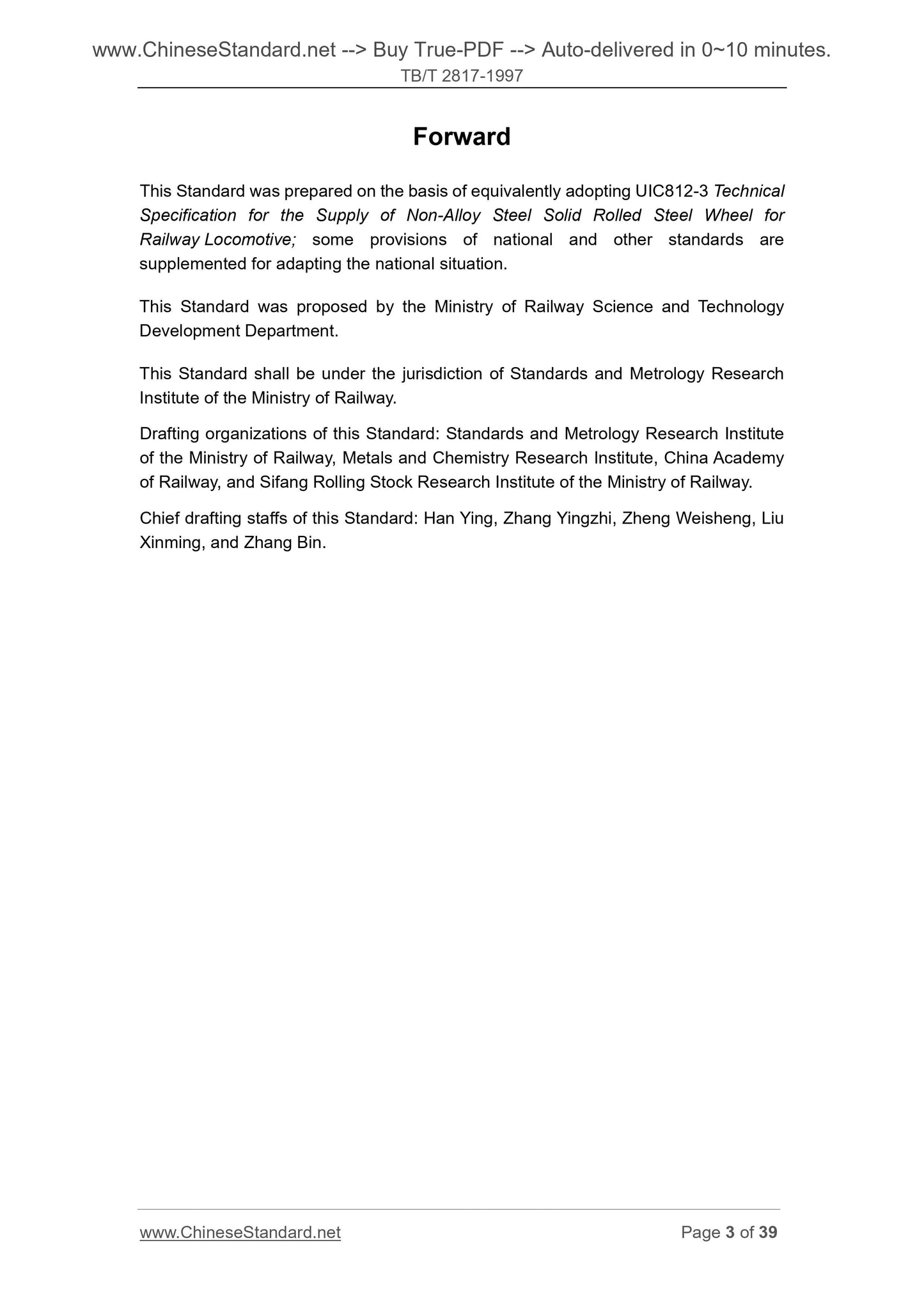
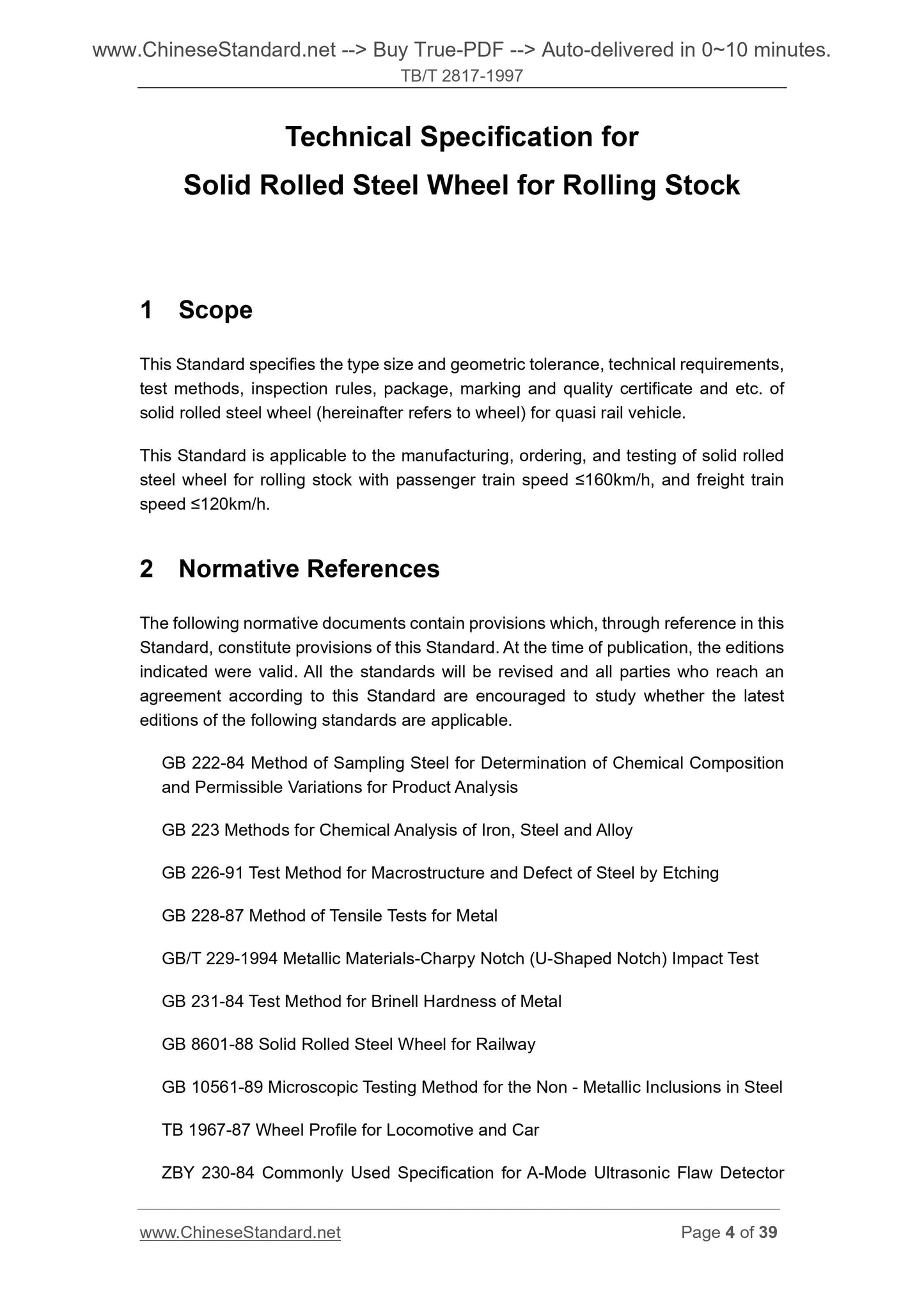
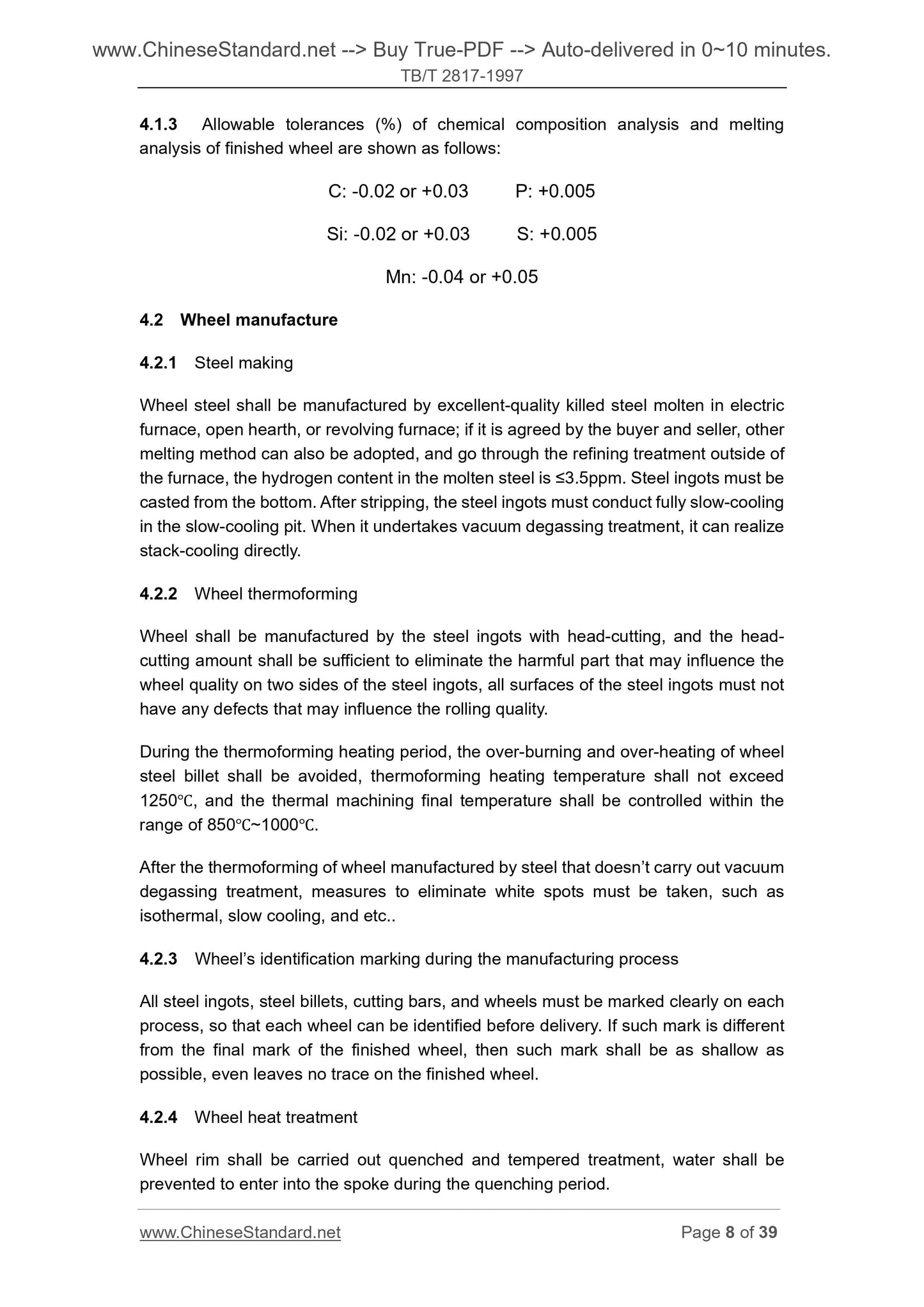
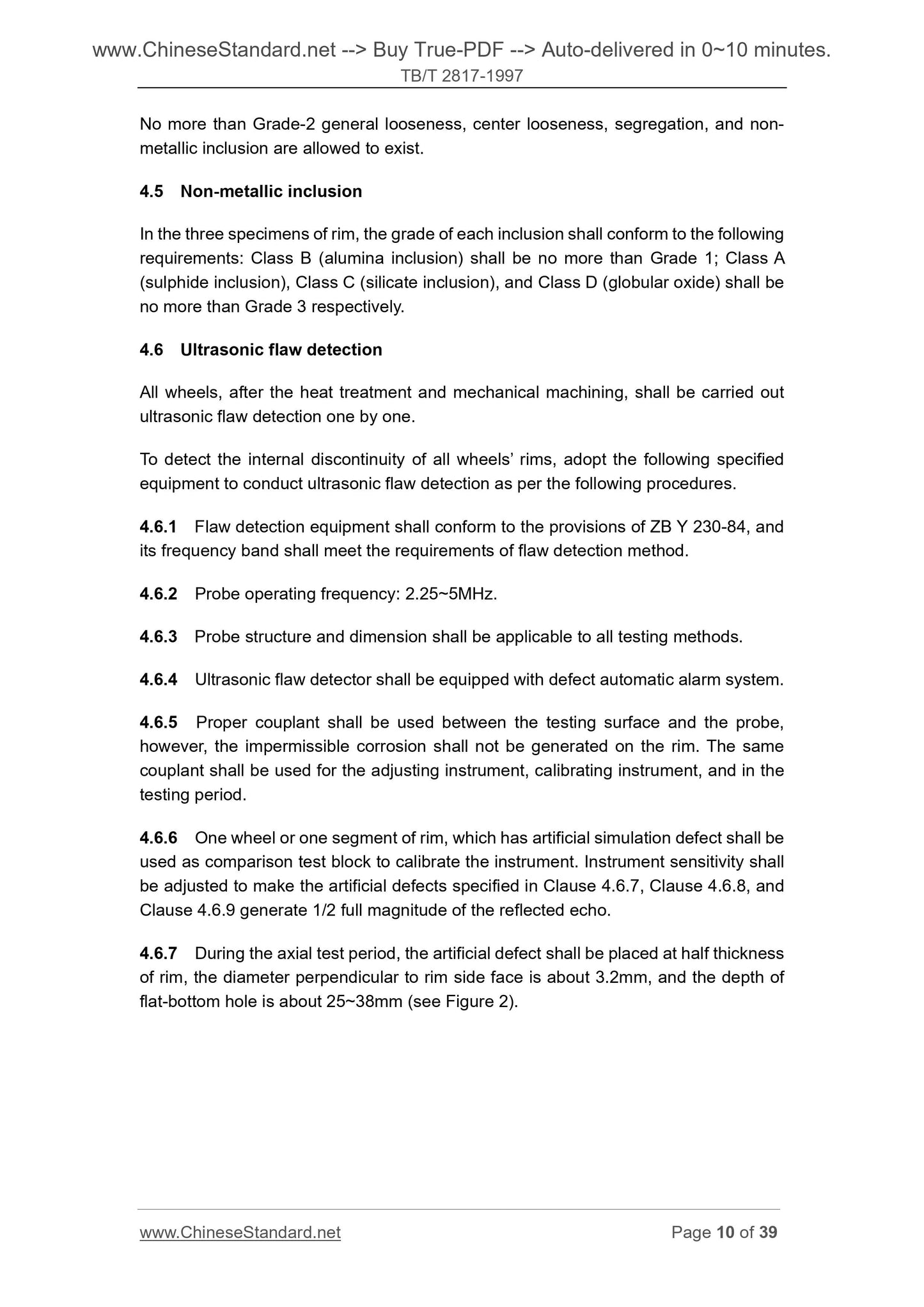
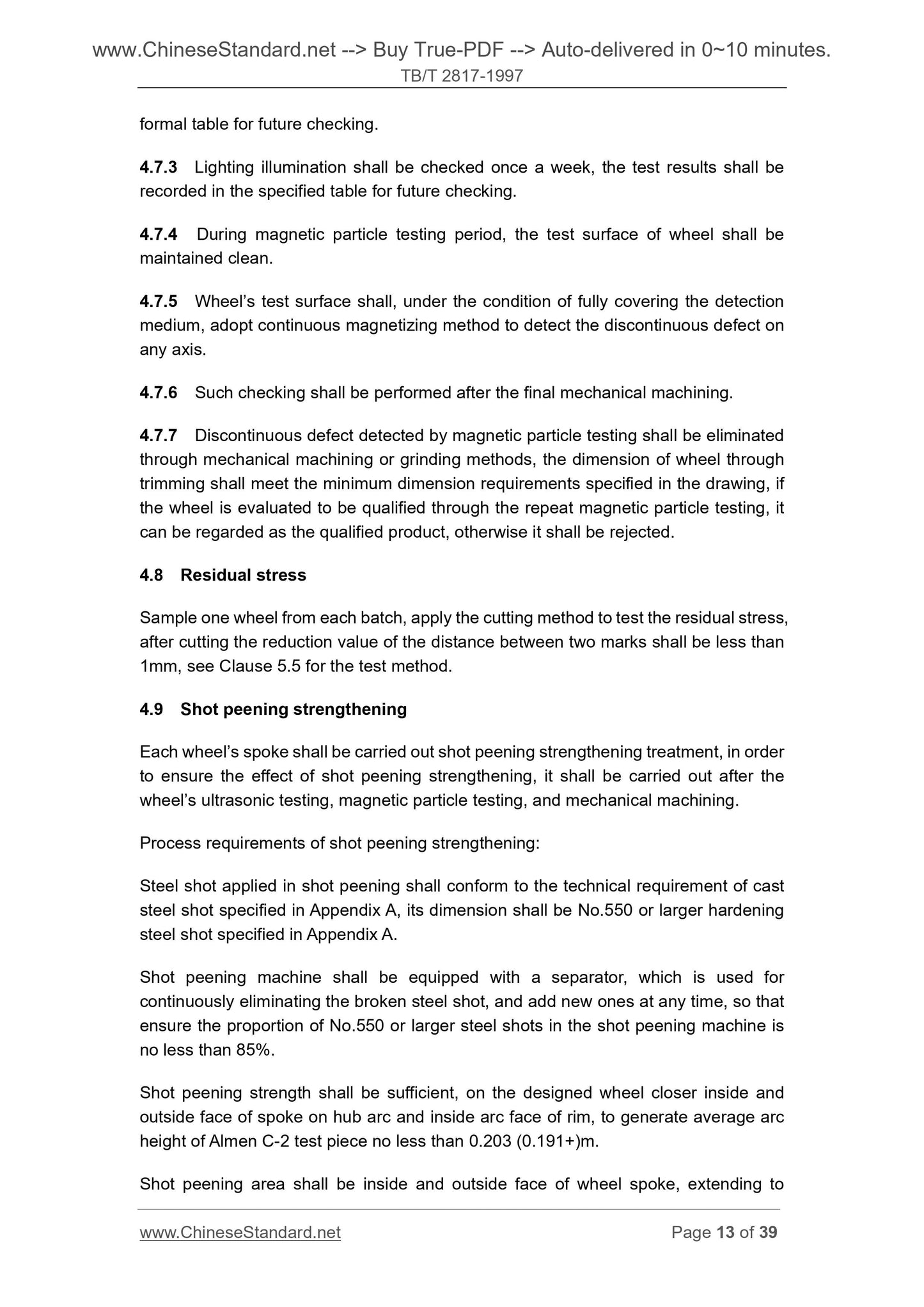
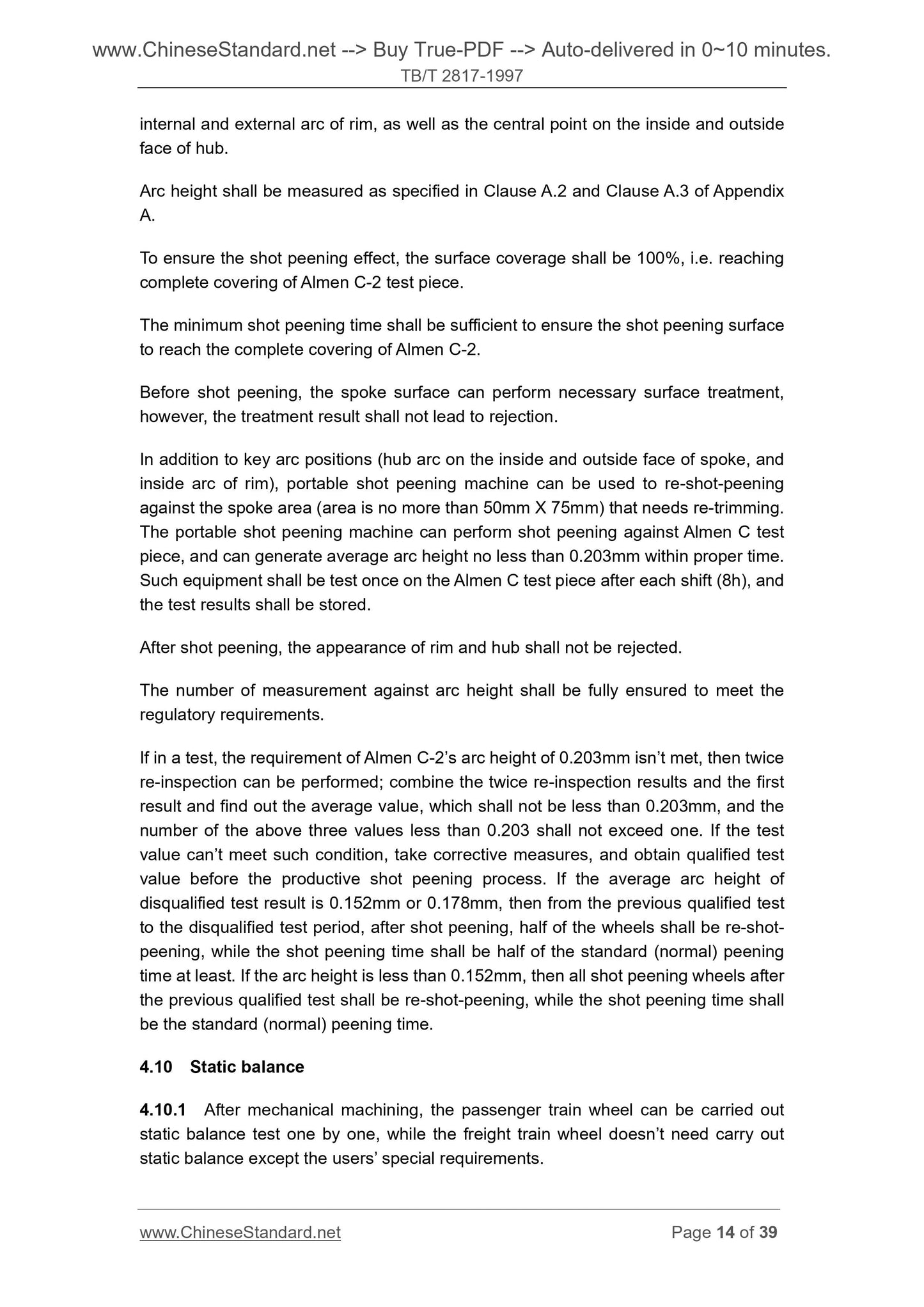

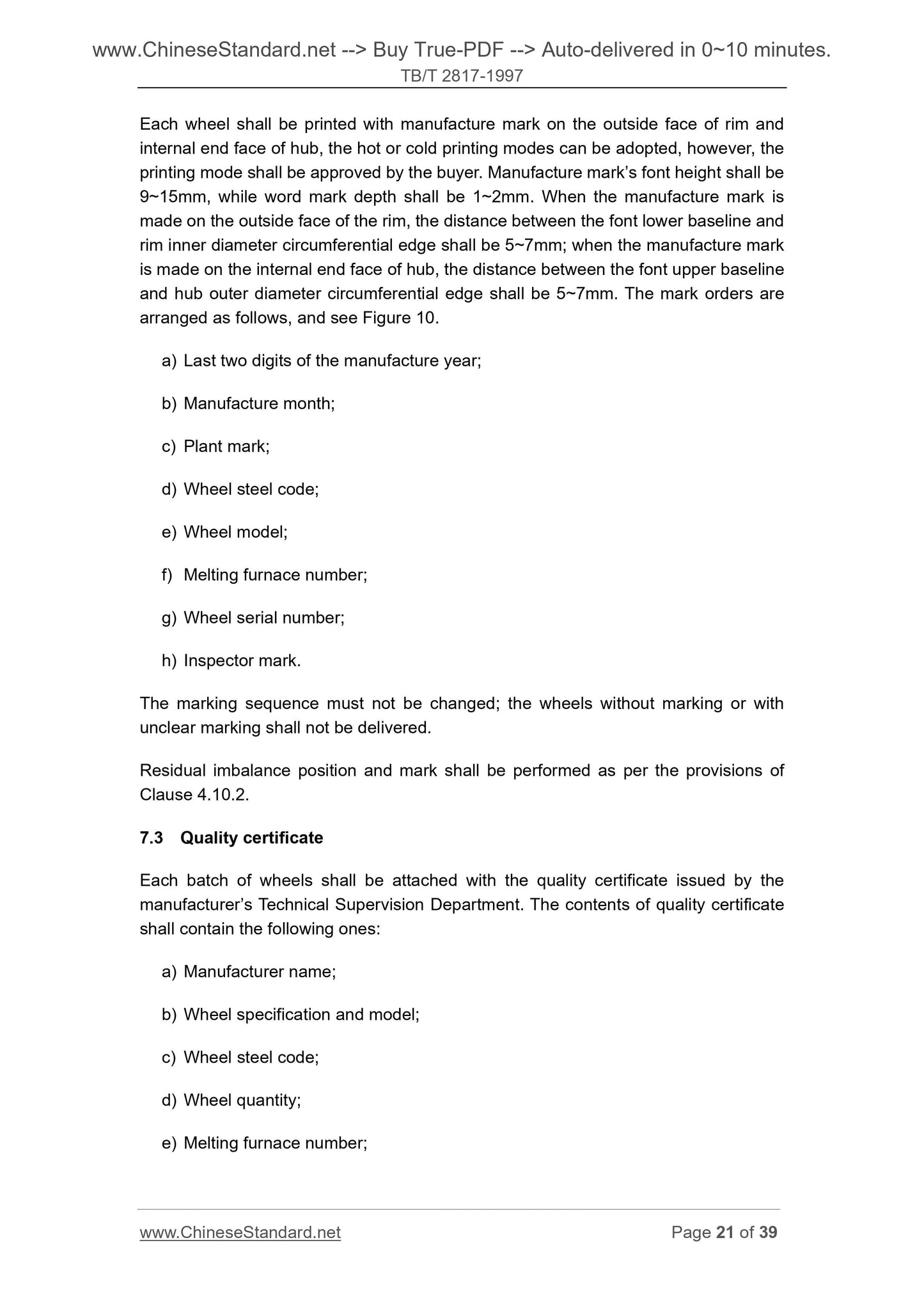
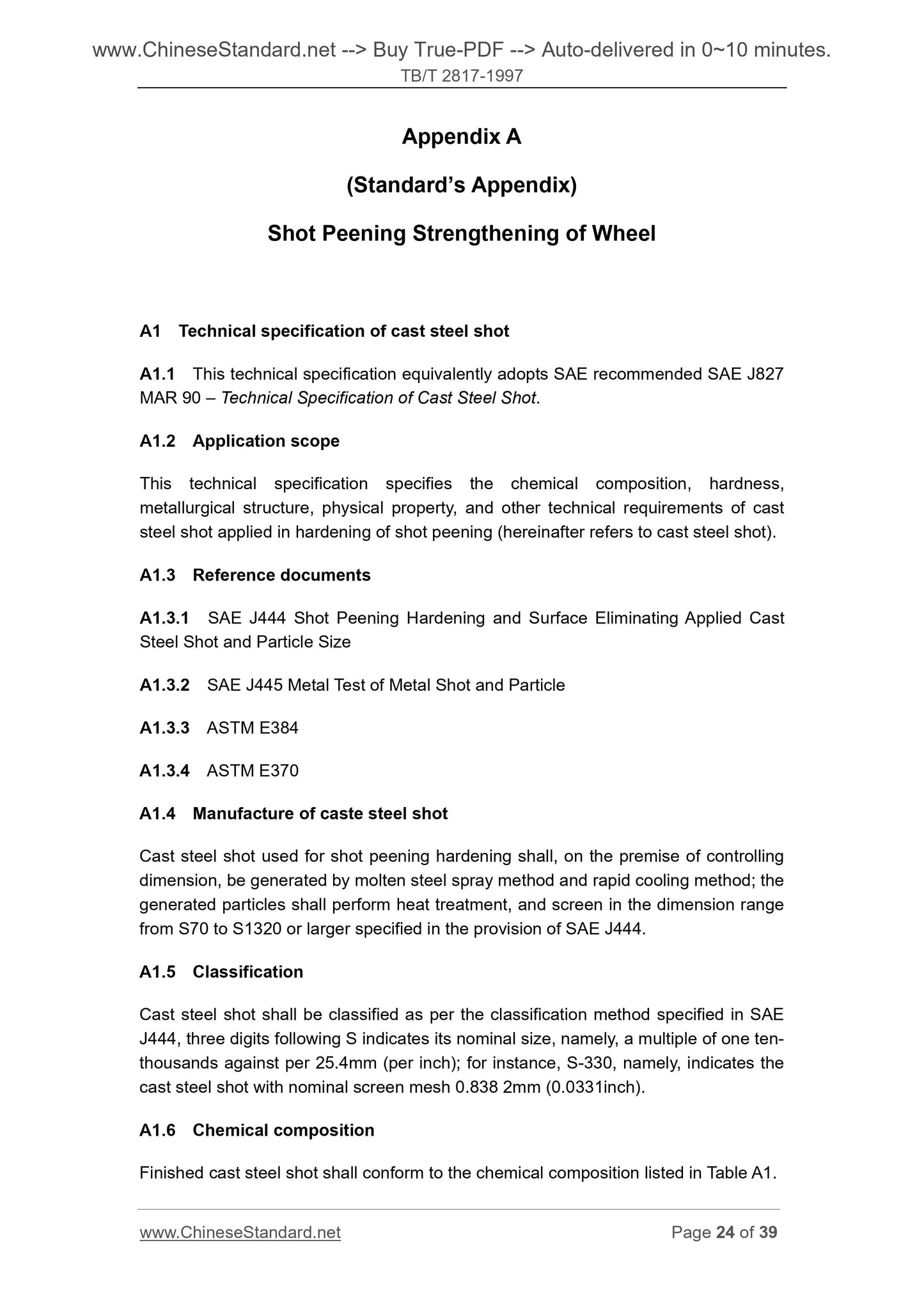
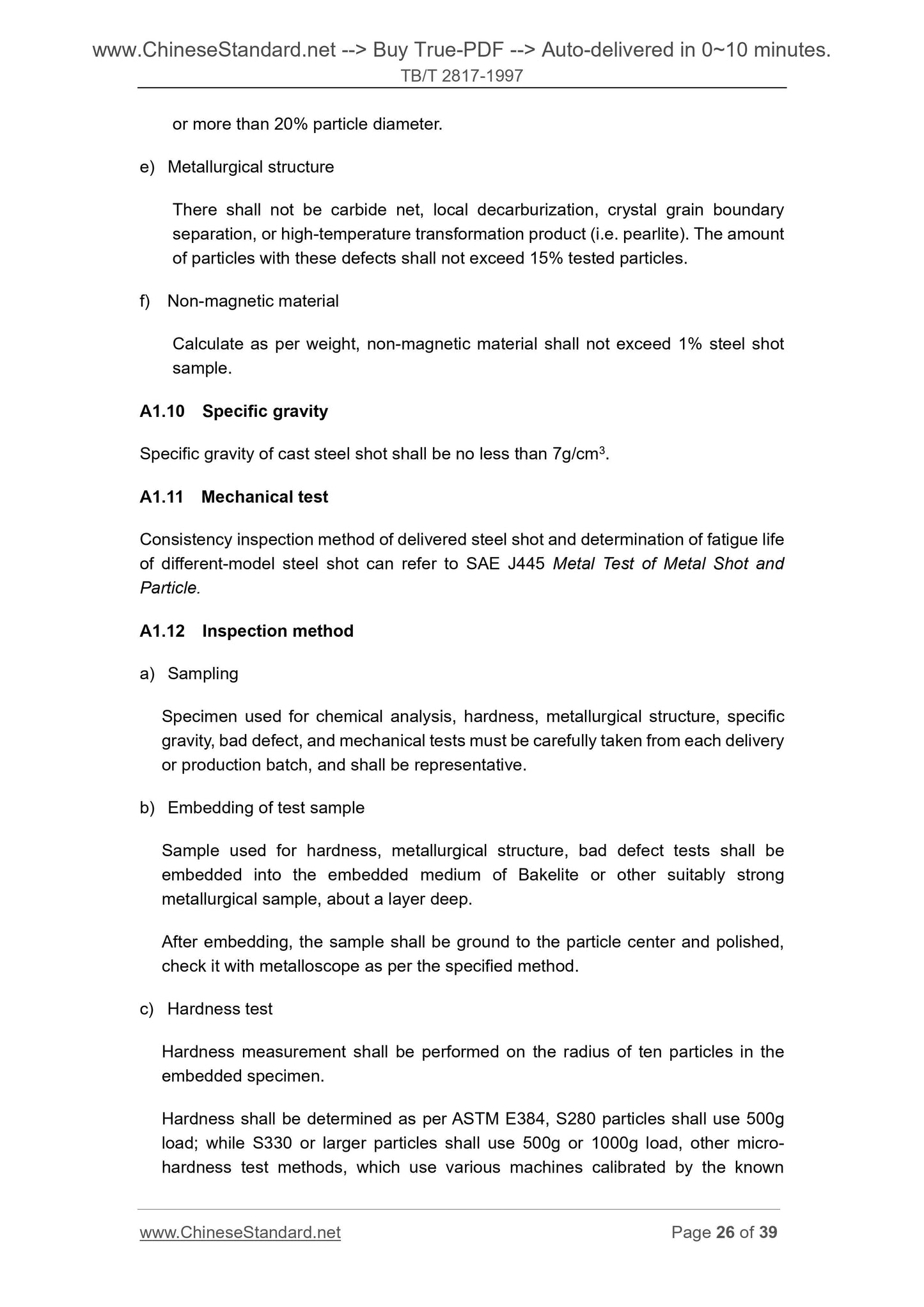