1
/
の
12
PayPal, credit cards. Download editable-PDF & invoice in 1 second!
YY/T 1106-2008 English PDF (YYT1106-2008)
YY/T 1106-2008 English PDF (YYT1106-2008)
通常価格
$150.00 USD
通常価格
セール価格
$150.00 USD
単価
/
あたり
配送料はチェックアウト時に計算されます。
受取状況を読み込めませんでした
Delivery: 3 seconds. Download true-PDF + Invoice.
Get QUOTATION in 1-minute: Click YY/T 1106-2008
Historical versions: YY/T 1106-2008
Preview True-PDF (Reload/Scroll if blank)
YY/T 1106-2008: Electrically powered operating table
YY/T 1106-2008
YY
PHARMACEUTICAL INDUSTRY STANDARD
OF THE PEOPLE’S REPUBLIC OF CHINA
ICS 11.140
C 46
Replacing YY 91106-1999
Electrically powered operating table
ISSUED ON. APRIL 25, 2008
IMPLEMENTED ON. JUNE 01, 2009
Issued by. China Food and Drug Administration
Table of Contents
Foreword ... 3
1 Scope ... 4
2 Normative references ... 4
3 Classification and basic size ... 4
4 Requirements ... 6
5 Test methods ... 7
6 Inspection rules ... 12
7 Markings, instructions for use, packaging, transport, storage ... 13
Foreword
This standard is a recommended standard.
This standard replaces YY 91106-1999 “Electrically powered operating table”.
The main differences between this standard and YY 91106-1999 “Electrically
powered operating table” are as follows.
- MODIFY the safety requirements to be carried out in accordance with GB
9706.1-2007 “Medical electrical equipment - Part 1. General requirements
for safety”;
- Special requirements for safety shall be implemented in accordance with
YY 0570-2005 “Medical electrical equipment - Part 2-46. Particular
requirements for the safety of operating tables”;
- MODIFY the environmental test requirements to be implemented in
accordance with GB/T 14710-1993 “The environmental requirements and
test methods for medical electrical equipment”;
- DELETE the non-technical contents 4.7, 4.12, 4.13 of the technical
requirements from the original standard;
- UPDATE the outdated reference standards.
This standard was proposed by the Medical Electronic Instruments
Standardization Subcommittee of the National Medical Electrical Apparatus
Standardization Technical Committee.
This standard shall be under the jurisdiction of the Medical Electronic
Instruments Standardization Subcommittee of the National Medical Electrical
Apparatus Standardization Technical Committee.
Drafting organization of this standard. Shanghai Medical Device Testing
Institute.
The main drafters of this standard. Xu Yuemin, Sun Jian.
This standard replaces the standard previously issued as follows.
- ZB C46 006-1989.
- YY 91106-1999.
Electrically powered operating table
1 Scope
This standard specifies the classification, requirements, test methods,
inspection rules and markings, instructions for use, packaging, transport,
storage requirements for electrically powered operating table (hereinafter
referred to as operating table).
This standard applies to electrically powered operating table. This product is
used for general surgery for thoracic and abdominal surgery, ophthalmology,
otolaryngology, gynecology, obstetrics, and urology.
2 Normative references
The provisions in following documents become the provisions of this standard
through reference in this standard. For the dated references, the subsequent
amendments (excluding corrections) or revisions do not apply to this standard;
however, parties who reach an agreement based on this standard are
encouraged to study if the latest versions of these documents are applicable.
For undated references, the latest edition of the referenced document applies.
GB/T 191-2008 Packaging - Pictorial marking for handling of goods
GB 9706.1-2007 Medical electrical equipment - Part 1. General
requirements for safety (IEC 60601-1.1988, IDT)
GB 9969.1-1998 General principles for preparation of instructions for use of
industrial products
GB/T 14710-1993 The environmental requirements and test methods for
medical electrical equipment
YY 0570-2005 Medical electrical equipment - Part 2-46. Particular
requirements for the safety of operating tables (IEC 60601-2-46.1998, IDT)
3 Classification and basic size
3.1 The type of operating table is electrically powered. hydraulic and/or
pneumatic and/or mechanical.
3.2 The basic size of the operating table shall comply with the requirements of
4.8 The special requirements for the safety of the operating table shall comply
with the provisions of YY 0570-2005.
4.9 The environmental test shall be in accordance with the provisions of the
climatic environment test group II and the transport test in GB/T 14710-1993.
4.10 The of operating table shall be flat in appearance, uniform in color, free of
defects such as scratches.
5 Test methods
5.1 Basic parameters. It is measured by the use a universal measuring tool.
The results shall comply with the provisions of 4.1.
5.2 Leakage. The operating table shall be tested in accordance with 5.2.1 ~
5.2.3 at 20 °C ± 5 °C. The results shall comply with the provisions of 4.2.
5.2.1 As shown in Figure 2, raise the table top to the highest position and keep
it horizontally. Align the center of the column on the table top’s hip board, apply
a 100 kg static load. After maintaining the hydraulic pressure for 5 h (or 1 h for
pneumatic system), measure the falling distance.
5.2.2 As shown in Figure 3, lower the table top to a minimum and horizontal
position, hang a 25 kg static load at the middle position of 100 mm from the end
of leg board. After maintaining the hydraulic pressure for 5 h (or 1 h for
pneumatic system), measure the falling distance.
5.2.3 As shown in Figure 4, lower the table top to the lowest position. Upward
fold the back board to form an angle of 125° to the hip board. Hang a 50 kg
static load at the middle of the top of the back board. After maintaining the
hydraulic pressure for 5 h (or 1 h for pneumatic system), measure the falling
distance.
Figure 2 -- Leakage test (5.2.1)
Wood board or
corrugated paper
5.6 The table top and the selected table mat shall be visually inspected through
X-ray (50 kV) or X-ray fluoroscopy (70 kV), it shall be free from shadow and
comply with the requirements of 4.6.
5.7 General requirements for safety shall be tested in accordance with the
method as specified in GB 9706.1, to verify whether it complies with the
requirements.
5.8 Special requirements for safety shall be tested in accordance with the
method as specified in YY 0570, to verify whether it complies with the
requirements.
5.9 Environmental test requirements shall be tested in accordance with the
method as specified in GB/T 14710, to verify whether it complies with the
requirements.
5.10 Make visual observation. The results shall comply with the provisions of
4.10.
6 Inspection rules
6.1 Classification of inspections
The inspection of electrically powered operating table products is divided into
exit-factory inspection and type inspection.
6.2 Exit-factory inspection
6.2.1 The operating table shall be inspected by the quality inspection
department of the manufacturer on a set-by-set basis. Only the qualified
products can be warehoused-in and exit-factory.
6.2.2 The exit-factory inspection items shall be inspected according to the
provisions of Table 2.
6.2.3 Among the inspection items, if there is any unqualified item, the
unqualified item shall be repaired. After the repair, it shall be submitted again
for inspection. Only the qualified products can be warehoused-in and exit-
factory.
Table 2
Inspection items Inspection range Remarks
Performance 4.1, 4.2, 4.3, 4.4, 4.5, 4.10 -
Safety 18 f), 19, 20 in GB 9706.1-2007 -
6.3 Type inspection
g) Product’s standard number.
7.1.2 The wooden box shall have the following markings.
a) The manufacturer’s name and address;
b) The product’s name and model;
c) The product’s production number;
d) The product’...
Get QUOTATION in 1-minute: Click YY/T 1106-2008
Historical versions: YY/T 1106-2008
Preview True-PDF (Reload/Scroll if blank)
YY/T 1106-2008: Electrically powered operating table
YY/T 1106-2008
YY
PHARMACEUTICAL INDUSTRY STANDARD
OF THE PEOPLE’S REPUBLIC OF CHINA
ICS 11.140
C 46
Replacing YY 91106-1999
Electrically powered operating table
ISSUED ON. APRIL 25, 2008
IMPLEMENTED ON. JUNE 01, 2009
Issued by. China Food and Drug Administration
Table of Contents
Foreword ... 3
1 Scope ... 4
2 Normative references ... 4
3 Classification and basic size ... 4
4 Requirements ... 6
5 Test methods ... 7
6 Inspection rules ... 12
7 Markings, instructions for use, packaging, transport, storage ... 13
Foreword
This standard is a recommended standard.
This standard replaces YY 91106-1999 “Electrically powered operating table”.
The main differences between this standard and YY 91106-1999 “Electrically
powered operating table” are as follows.
- MODIFY the safety requirements to be carried out in accordance with GB
9706.1-2007 “Medical electrical equipment - Part 1. General requirements
for safety”;
- Special requirements for safety shall be implemented in accordance with
YY 0570-2005 “Medical electrical equipment - Part 2-46. Particular
requirements for the safety of operating tables”;
- MODIFY the environmental test requirements to be implemented in
accordance with GB/T 14710-1993 “The environmental requirements and
test methods for medical electrical equipment”;
- DELETE the non-technical contents 4.7, 4.12, 4.13 of the technical
requirements from the original standard;
- UPDATE the outdated reference standards.
This standard was proposed by the Medical Electronic Instruments
Standardization Subcommittee of the National Medical Electrical Apparatus
Standardization Technical Committee.
This standard shall be under the jurisdiction of the Medical Electronic
Instruments Standardization Subcommittee of the National Medical Electrical
Apparatus Standardization Technical Committee.
Drafting organization of this standard. Shanghai Medical Device Testing
Institute.
The main drafters of this standard. Xu Yuemin, Sun Jian.
This standard replaces the standard previously issued as follows.
- ZB C46 006-1989.
- YY 91106-1999.
Electrically powered operating table
1 Scope
This standard specifies the classification, requirements, test methods,
inspection rules and markings, instructions for use, packaging, transport,
storage requirements for electrically powered operating table (hereinafter
referred to as operating table).
This standard applies to electrically powered operating table. This product is
used for general surgery for thoracic and abdominal surgery, ophthalmology,
otolaryngology, gynecology, obstetrics, and urology.
2 Normative references
The provisions in following documents become the provisions of this standard
through reference in this standard. For the dated references, the subsequent
amendments (excluding corrections) or revisions do not apply to this standard;
however, parties who reach an agreement based on this standard are
encouraged to study if the latest versions of these documents are applicable.
For undated references, the latest edition of the referenced document applies.
GB/T 191-2008 Packaging - Pictorial marking for handling of goods
GB 9706.1-2007 Medical electrical equipment - Part 1. General
requirements for safety (IEC 60601-1.1988, IDT)
GB 9969.1-1998 General principles for preparation of instructions for use of
industrial products
GB/T 14710-1993 The environmental requirements and test methods for
medical electrical equipment
YY 0570-2005 Medical electrical equipment - Part 2-46. Particular
requirements for the safety of operating tables (IEC 60601-2-46.1998, IDT)
3 Classification and basic size
3.1 The type of operating table is electrically powered. hydraulic and/or
pneumatic and/or mechanical.
3.2 The basic size of the operating table shall comply with the requirements of
4.8 The special requirements for the safety of the operating table shall comply
with the provisions of YY 0570-2005.
4.9 The environmental test shall be in accordance with the provisions of the
climatic environment test group II and the transport test in GB/T 14710-1993.
4.10 The of operating table shall be flat in appearance, uniform in color, free of
defects such as scratches.
5 Test methods
5.1 Basic parameters. It is measured by the use a universal measuring tool.
The results shall comply with the provisions of 4.1.
5.2 Leakage. The operating table shall be tested in accordance with 5.2.1 ~
5.2.3 at 20 °C ± 5 °C. The results shall comply with the provisions of 4.2.
5.2.1 As shown in Figure 2, raise the table top to the highest position and keep
it horizontally. Align the center of the column on the table top’s hip board, apply
a 100 kg static load. After maintaining the hydraulic pressure for 5 h (or 1 h for
pneumatic system), measure the falling distance.
5.2.2 As shown in Figure 3, lower the table top to a minimum and horizontal
position, hang a 25 kg static load at the middle position of 100 mm from the end
of leg board. After maintaining the hydraulic pressure for 5 h (or 1 h for
pneumatic system), measure the falling distance.
5.2.3 As shown in Figure 4, lower the table top to the lowest position. Upward
fold the back board to form an angle of 125° to the hip board. Hang a 50 kg
static load at the middle of the top of the back board. After maintaining the
hydraulic pressure for 5 h (or 1 h for pneumatic system), measure the falling
distance.
Figure 2 -- Leakage test (5.2.1)
Wood board or
corrugated paper
5.6 The table top and the selected table mat shall be visually inspected through
X-ray (50 kV) or X-ray fluoroscopy (70 kV), it shall be free from shadow and
comply with the requirements of 4.6.
5.7 General requirements for safety shall be tested in accordance with the
method as specified in GB 9706.1, to verify whether it complies with the
requirements.
5.8 Special requirements for safety shall be tested in accordance with the
method as specified in YY 0570, to verify whether it complies with the
requirements.
5.9 Environmental test requirements shall be tested in accordance with the
method as specified in GB/T 14710, to verify whether it complies with the
requirements.
5.10 Make visual observation. The results shall comply with the provisions of
4.10.
6 Inspection rules
6.1 Classification of inspections
The inspection of electrically powered operating table products is divided into
exit-factory inspection and type inspection.
6.2 Exit-factory inspection
6.2.1 The operating table shall be inspected by the quality inspection
department of the manufacturer on a set-by-set basis. Only the qualified
products can be warehoused-in and exit-factory.
6.2.2 The exit-factory inspection items shall be inspected according to the
provisions of Table 2.
6.2.3 Among the inspection items, if there is any unqualified item, the
unqualified item shall be repaired. After the repair, it shall be submitted again
for inspection. Only the qualified products can be warehoused-in and exit-
factory.
Table 2
Inspection items Inspection range Remarks
Performance 4.1, 4.2, 4.3, 4.4, 4.5, 4.10 -
Safety 18 f), 19, 20 in GB 9706.1-2007 -
6.3 Type inspection
g) Product’s standard number.
7.1.2 The wooden box shall have the following markings.
a) The manufacturer’s name and address;
b) The product’s name and model;
c) The product’s production number;
d) The product’...
Share
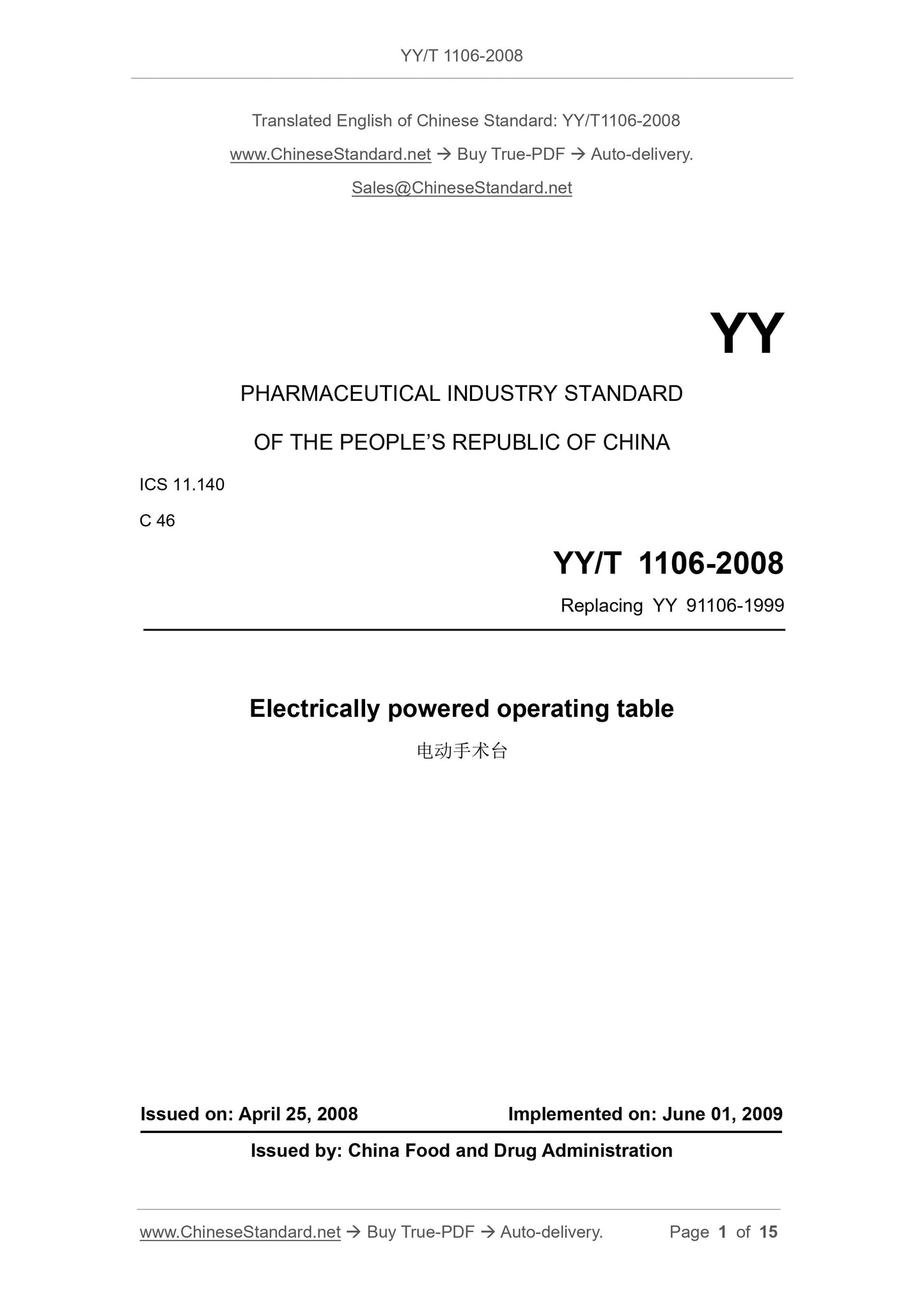
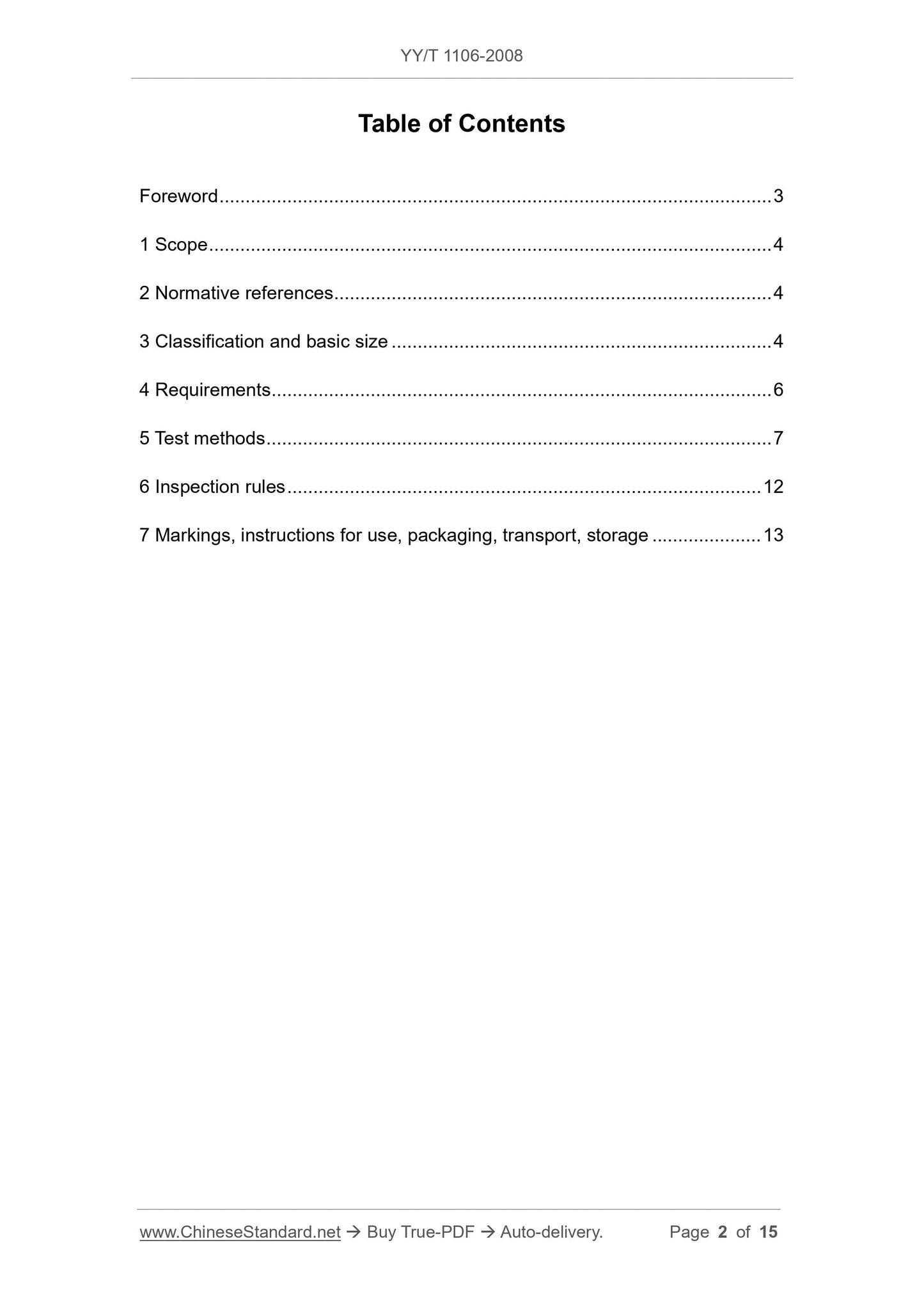
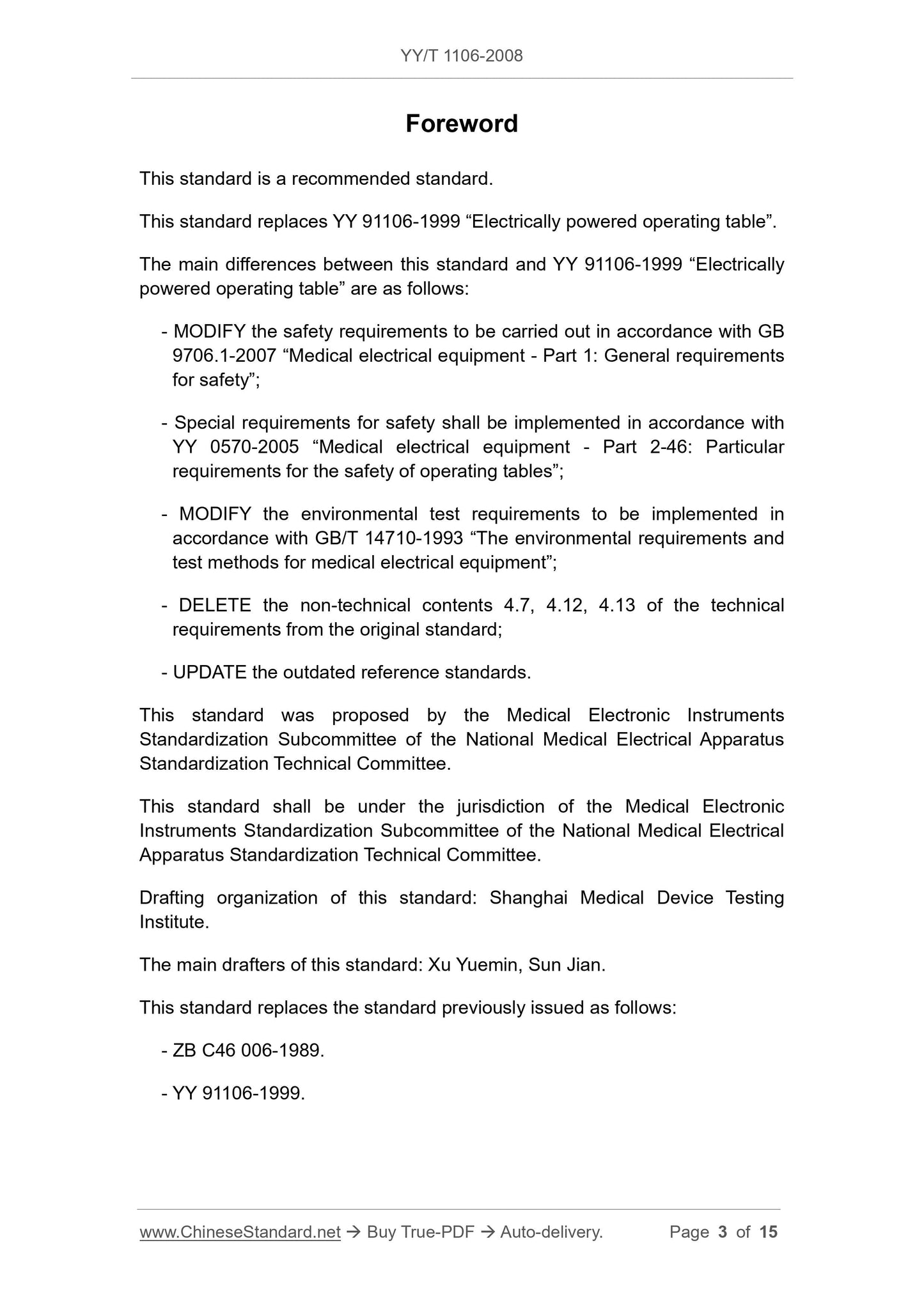
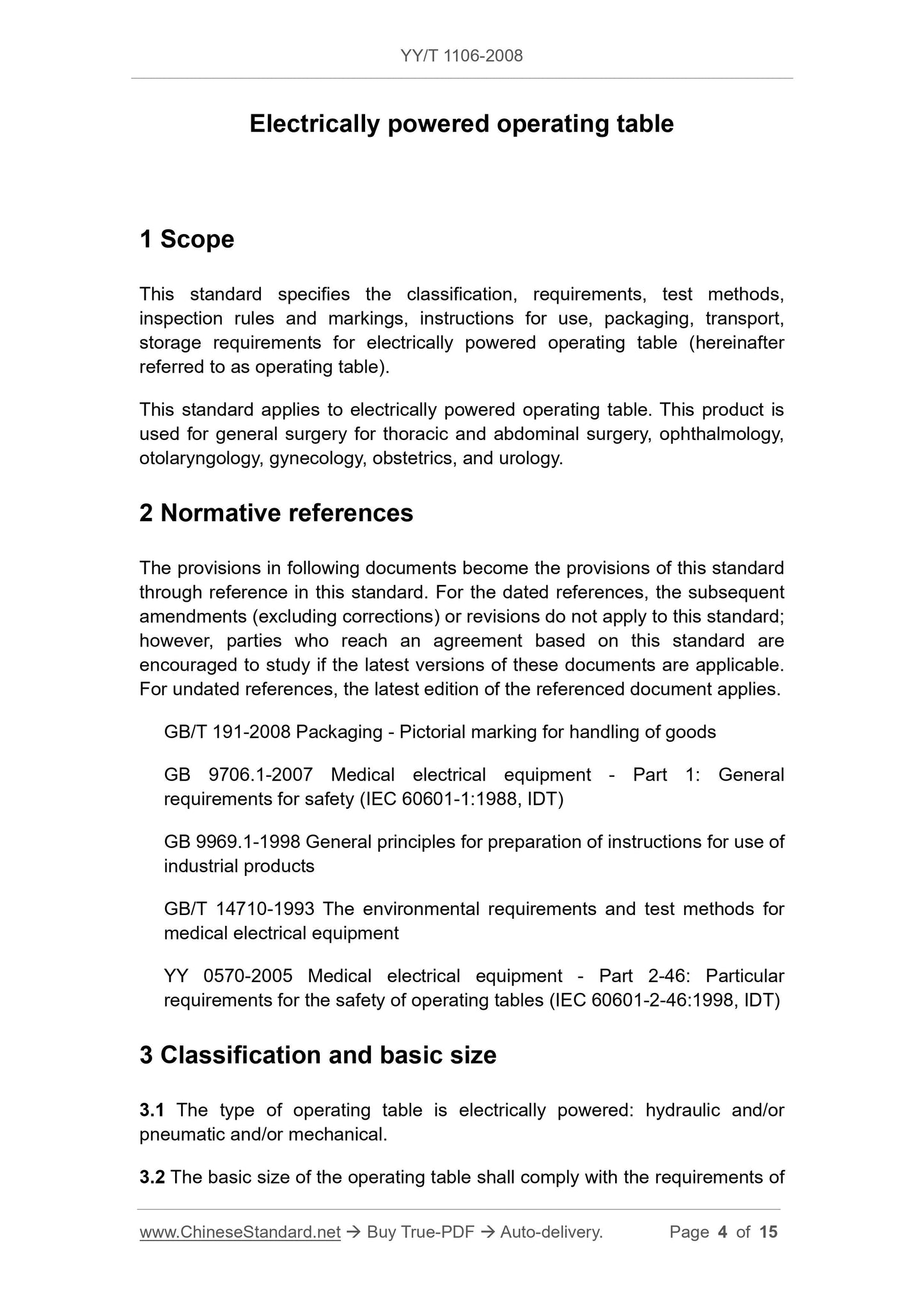
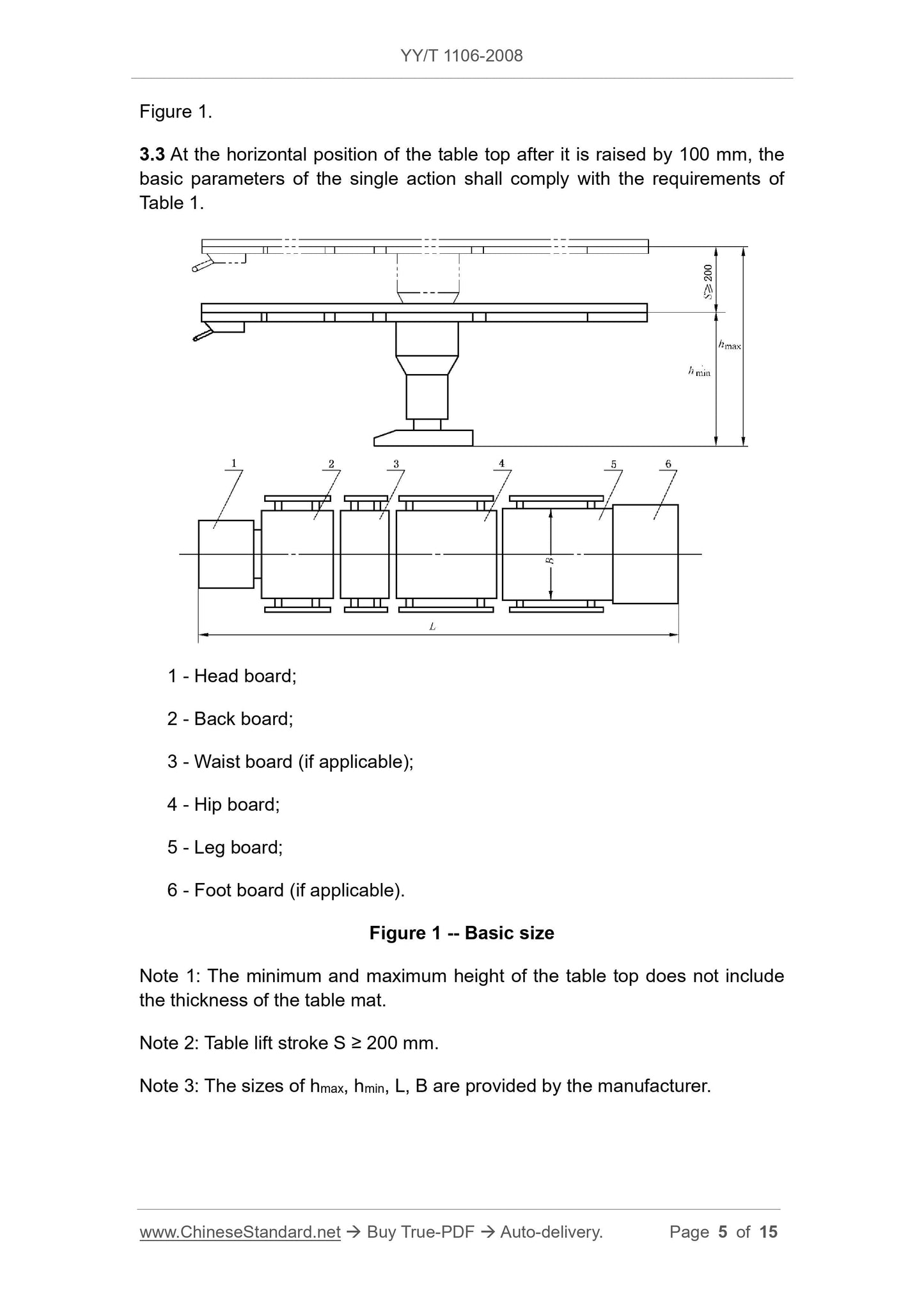
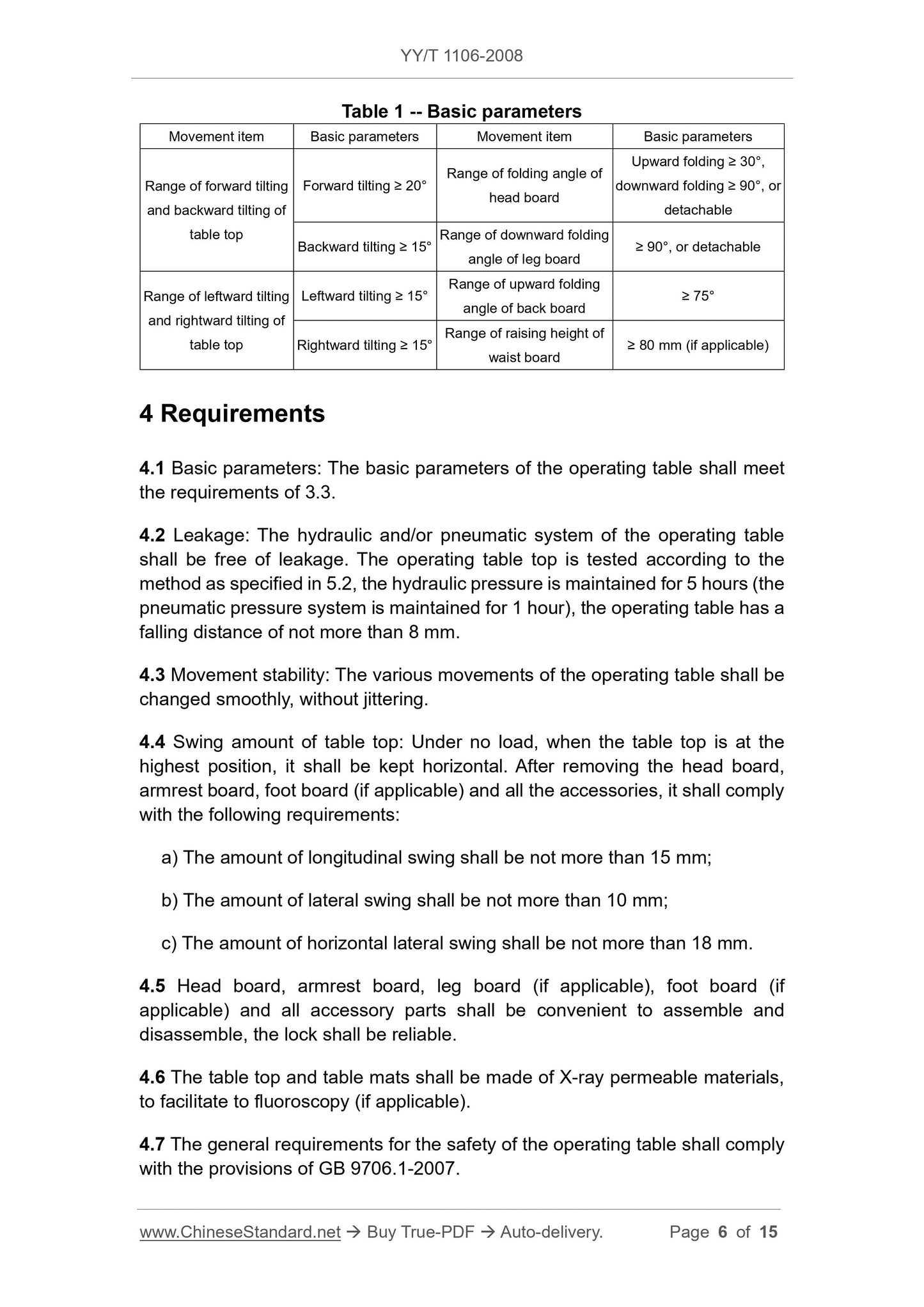
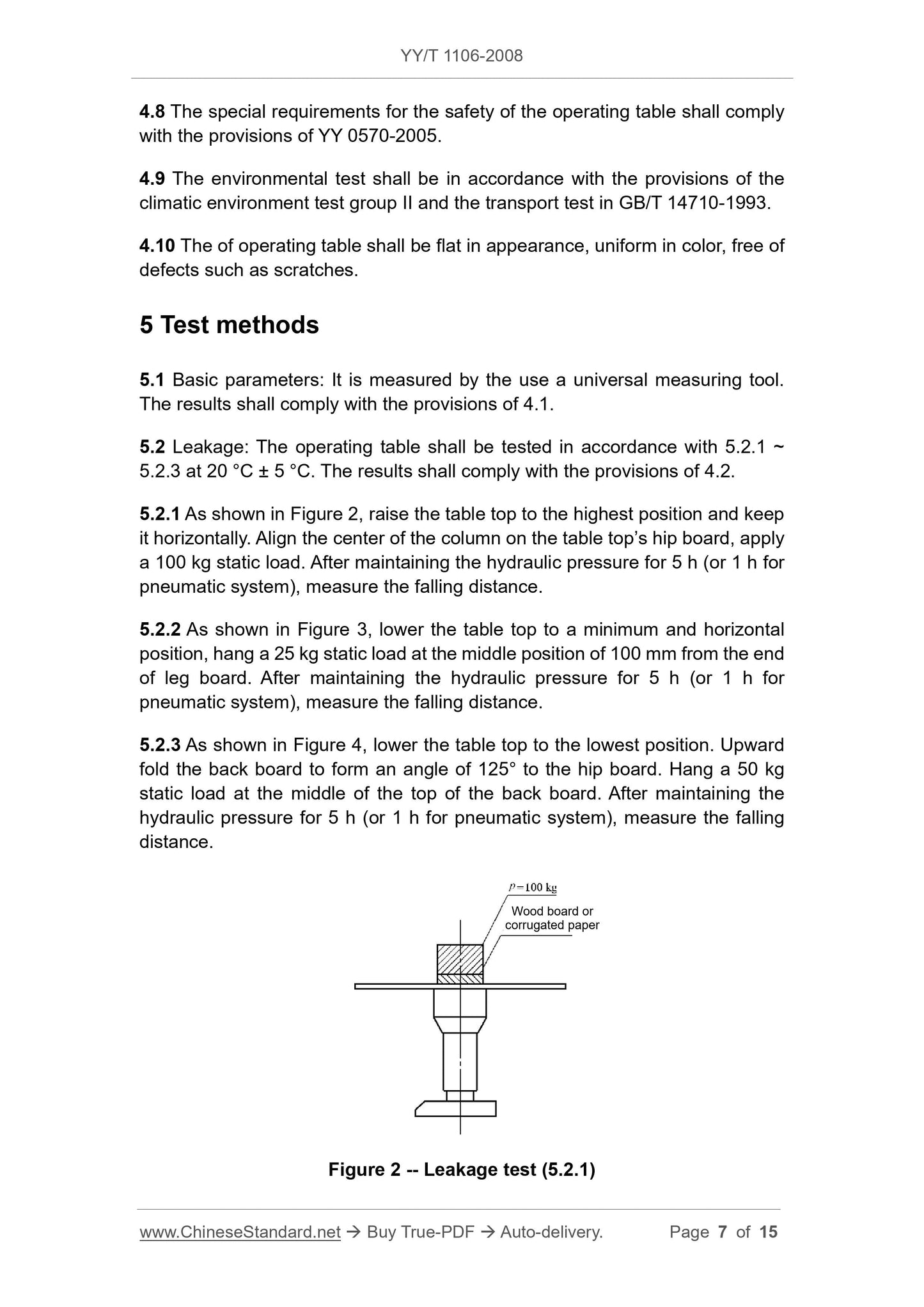
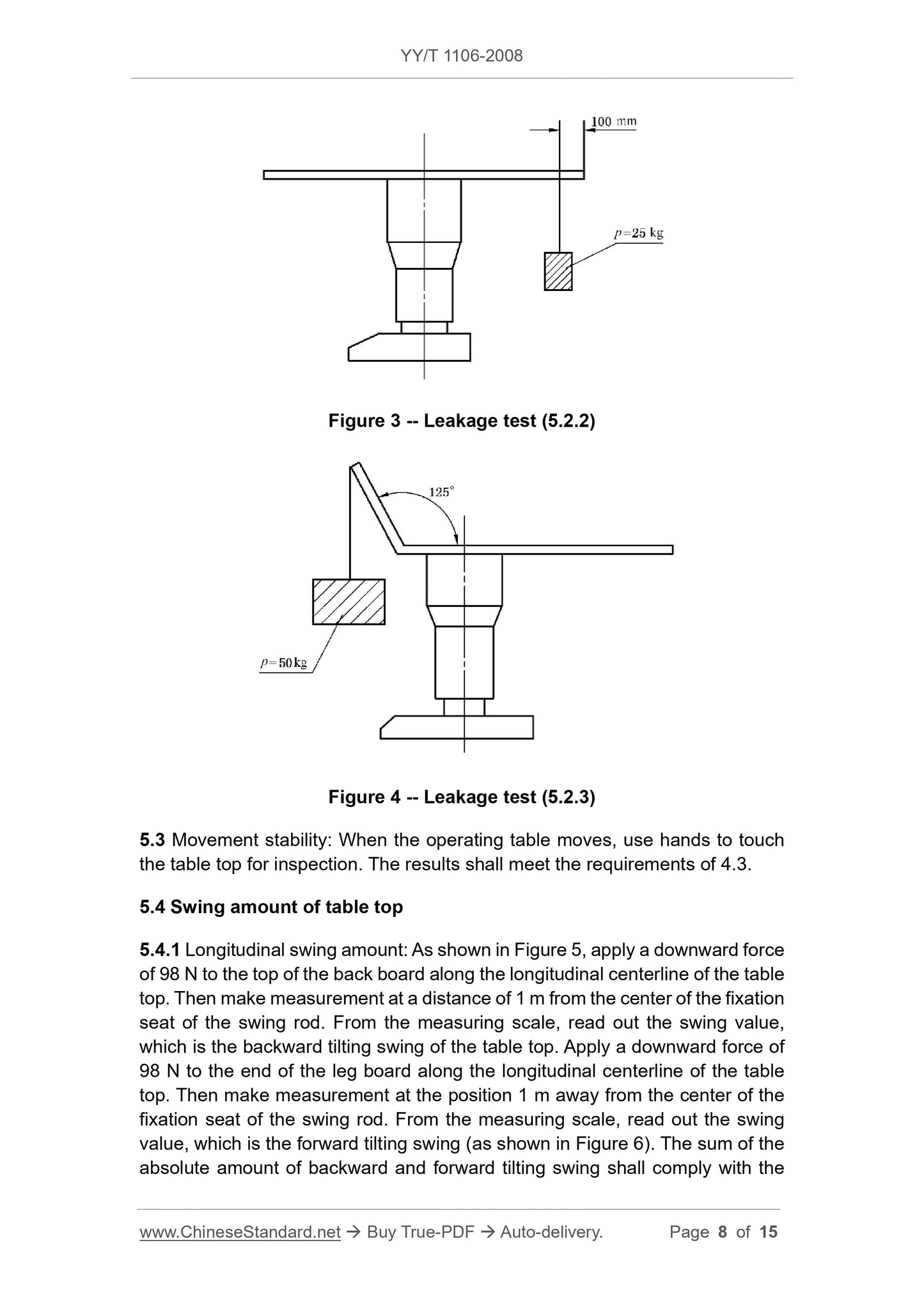
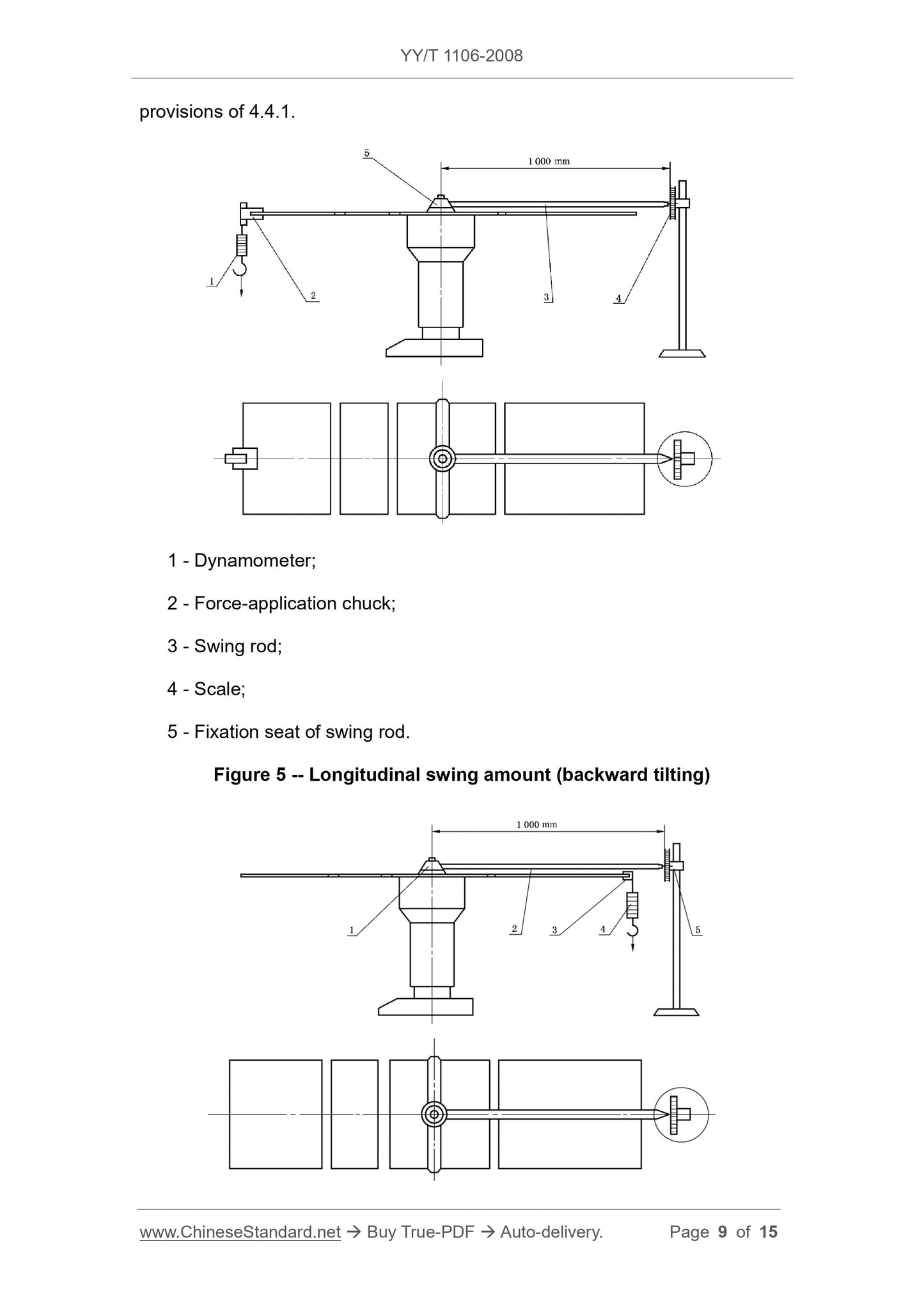
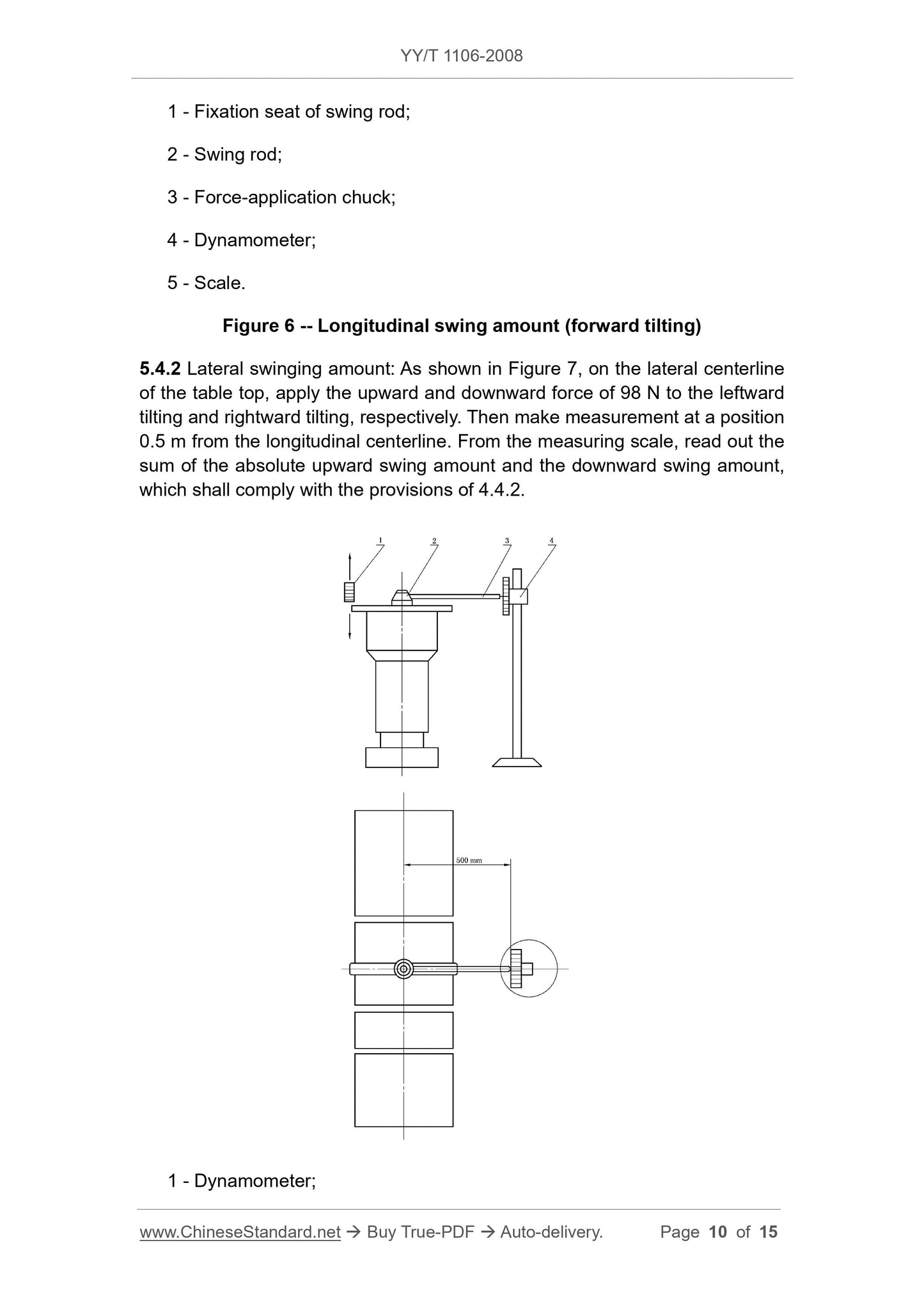
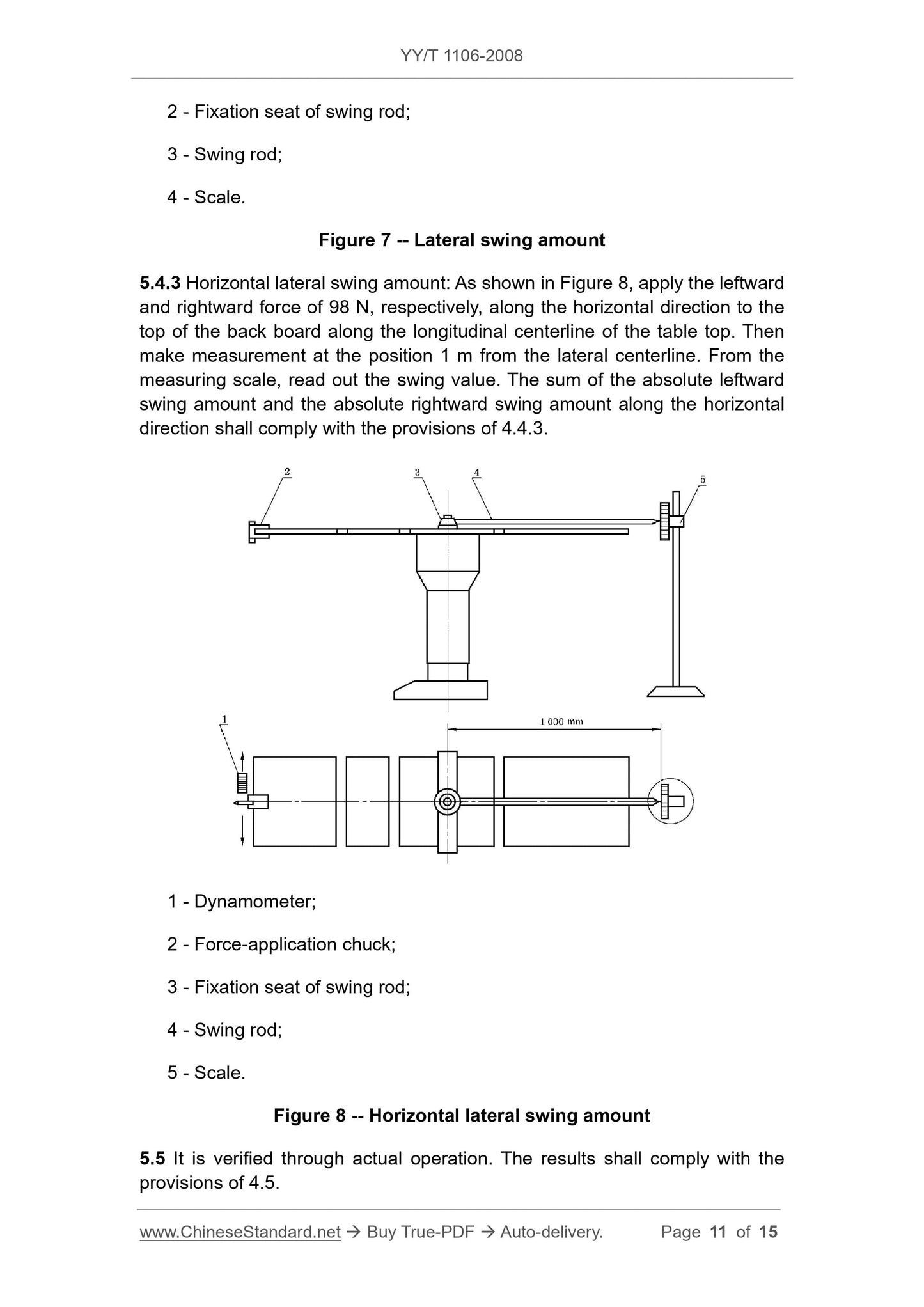
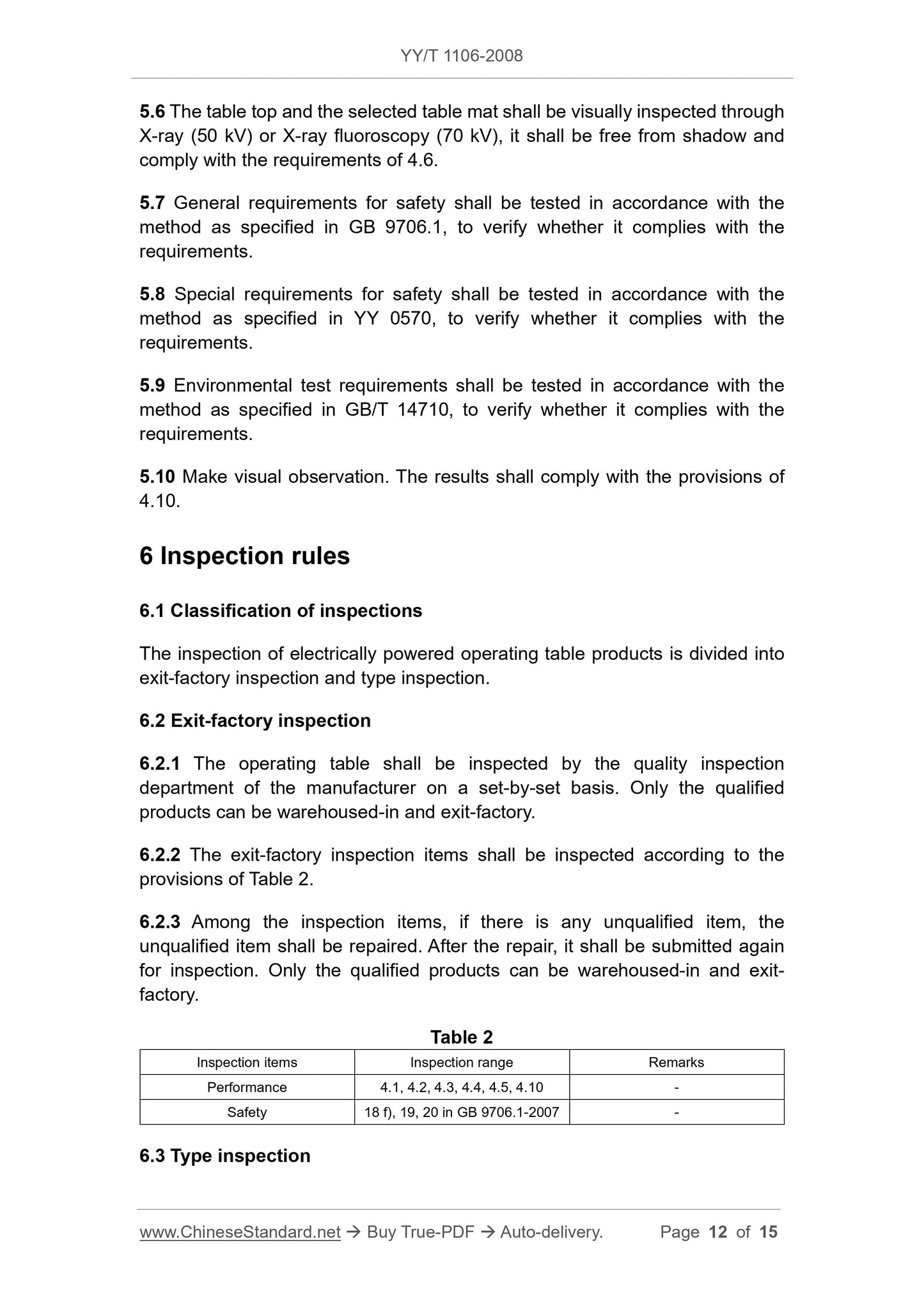