1
/
of
6
PayPal, credit cards. Download editable-PDF and invoice in 1 second!
TB/T 1618-2001 English PDF (TBT1618-2001)
TB/T 1618-2001 English PDF (TBT1618-2001)
Regular price
$150.00 USD
Regular price
Sale price
$150.00 USD
Unit price
/
per
Shipping calculated at checkout.
Couldn't load pickup availability
Delivery: 3 seconds. Download true-PDF + Invoice.
Get QUOTATION in 1-minute: Click TB/T 1618-2001
Historical versions: TB/T 1618-2001
Preview True-PDF (Reload/Scroll if blank)
TB/T 1618-2001: Ultrasonic inspection of rolling stock axles
TB/T 1618-2001
TB
RAILWAY INDUSTRY STANDARD
OF THE PEOPLE’S REPUBLIC OF CHINA
eqv ISO 5948.1994
Ultrasonic inspection of rolling stock axles
ISSUED ON. MAY 28, 2001
IMPLEMENTED ON. DECEMBER 01, 2001
Issued by. Ministry of Railways of People’s Republic of China
Table of contents
Foreword ... 3
lSO introduction ... 4
1 Scope ... 5
2 Normative references ... 5
3 Personnel requirements ... 5
4 Instrument, probe and coupling agent ... 6
5 Test block and curves ... 6
6 Preparation of Radial testing distance - amplitude curve ... 6
7 Testing conditions ... 7
8 Axial acoustic transmission testing sensitivity ... 7
9 Axial testing sensitivity ... 7
10 Radial testing sensitivity ... 7
11 Acceptance ... 8
Appendix A (Normative) TS-1 test block ... 11
Appendix B (Normative) TS-1W test block ... 12
Appendix C (Normative) TS-2 test block schematics ... 13
Appendix D (Normative) Axial defect testing distance – amplitude curve ... 14
Appendix E (Normative) Radial defect testing distance - amplitude curve
schematics ... 15
Foreword
The relevant rolling stock axle ultrasonic test method in this Standard is
equivalent to the method specified in ISO 5948-1994 “Railway rolling stock
material-ultrasonic acceptance testing”.
From the date of implementation of this Standard, it shall replace TB 1618-85
“Ultrasonic inspection of rolling stock axles”.
The Appendix A, Appendix B, Appendix C, Appendix D and Appendix E of
standard are normative.
This Standard was proposed by the Ministry of Railways – Qishuyan
Locomotive and Rolling Stock Technology Research Institute.
This Standard shall be under the jurisdiction of the Ministry of Railways –
Qishuyan Locomotive and Rolling Stock Technology Research Institute.
The drafting organizations of this Standard. Ministry of Railways – Qishuyan
Locomotive and Rolling Stock Technology Research Institute, China Academy of
Railway Sciences – Metals and Chemistry Research Institute.
Main drafters of this Standard. Huang Yongwei, Li Lianxiu, Lu Xuanguo, Yao
Rongwen.
This Standard was first-time issued on December 14, 1985.
This Standard was first-time revised in May 2001.
RAILWAY INDUSTRY STANDARD
OF THE PEOPLE’S REPUBLIC OF CHINA
eqv ISO 5948.1994
Ultrasonic inspection of rolling stock axles
1 Scope
This Standard specifies the newly made railway rolling stock axle’s ultrasonic
inspection method AND acceptance specifications.
This Standard applies to the testing of newly made axle material’s overall
performance AND internal defects.
2 Normative references
The provisions in following documents become the provisions of this Standard
through reference in this Standard. At the time of publication of this Standard,
the editions indicated were valid. All standards are subject to revision, however,
parties who use this Standard are encouraged to study if the latest versions of
these documents are applicable.
JB/T 10061-1999 Commonly used specification for A-mode ultrasonic defect
detector using pulse echo technique
JB/T 10062-1999 Testing methods for performance of probes used in
ultrasonic defect testing
GB/T 1804-1992 General tolerances – Tolerances for linear and angular
dimensions without individual tolerance indications
3 Personnel requirements
3.1 The personnel who undertake axle ultrasonic testing must acquire
appropriate basic knowledge, AND be familiar with the provisions of this
Standard.
3.2 The testing personnel must obtain the grade II and above NDT technical
qualification certificate which is issued by the Ministry of Railway – NDT
personnel technical qualification assessment commission.
4 Instrument, probe and coupling agent
4.1 The ultrasonic defect detector shall comply with the requirements of JB/T
10061.
4.2 Ultrasonic probe
4.2.1 Probe type. 2.5P20Z longitudinal wave straight probes.
4.2.2 Main beam deviation. the included angle between the probe’s main beam
AND the probe’s normal shall not be more than 1o.
4.2.3 The sound pressure distribution of the probe sound field shall not have
obvious double peaks.
4.2.4 As for the other performance indicators and test methods of probe, it shall
comply with the requirements of JB/T 10062.
4.3 Coupling agent. engine oil, glycerine or water.
5 Test block and curves
5.1 As for TS-1 test block, see Appendix A.
5.2 As for TS-1W test block, see Appendix B.
5.3 As for TS-2 test block schematics, see Appendix C.
5.4 As for axial defect testing distance - amplitude curve schematics, see
Appendix D.
5.5 As for radial defect testing distance - amplitude curve schematics, see
Appendix E.
6 Preparation of Radial testing distance - amplitude
curve
6.1 Radial testing distance – the amplitude curve is prepared by the testing
personnel based on the testing system used. Before use, it shall calibrate this
curve.
PLACE the straight probe onto the TS-2 test block’s journal; ADJUST the
instrument, to make the echo height of No.1 flat bottom hole equal to 50% of
the full vertical scale; COMPENSATE the coupling difference between the test
block and real axle; GAIN another 4 dB, which is the testing sensitivity.
10.2 Wheel seat
PLACE the straight probe onto the TS-2 test block’s wheel seat; ADJUST the
instrument, to make the echo height of No.4 flat bottom hole equal to 50% of
the full vertical scale; COMPENSATE the coupling difference between the test
block and real axle; GAIN another 4 dB, which is the testing sensitivity.
10.3 Axle body
PLACE the straight probe onto the TS-2 test block’s axle body; ADJUST the
instrument, to make the echo height of No.7 flat bottom hole equal to 50% of
the full vertical scale; COMPENSATE the coupling difference between the test
block and real axle; GAIN another 4 dB, which is the testing sensitivity.
10.4 Bottom echo attenuation
PLACE the straight probe onto the TS-2 test block’s axle body; MAKE the echo
height of the axle body bottom at No.10 taper hole equal to 50% of the full
vertical scale; COMPENSATE the coupling difference between the test block
and real axle, which is the testing sensitivity by bottom echo height attenuation
method.
11 Acceptance
11.1 Axial acoustic transmission
11.1.1 Acceptance region. within the axle end face center to 1/2R area, AND
the region boundary is based on the probe center.
11.1.2 Within the acceptance region, if the bottom echo height equals to or
higher than the reference wave height, it is deemed as qualified.
11.1.3 Within the acceptance region, if the bottom echo height is lower than the
reference wave height, the total area does not exceed 1/16 of the acceptance
region, AND the amplitude decrease is not less than 1/2 of the reference wave
height, it is also deemed as qualified.
11.1.4 If it fails to meet the requirements of Clause 11.1.2 and 11.1.3, it is
deemed as disqualified.
Get QUOTATION in 1-minute: Click TB/T 1618-2001
Historical versions: TB/T 1618-2001
Preview True-PDF (Reload/Scroll if blank)
TB/T 1618-2001: Ultrasonic inspection of rolling stock axles
TB/T 1618-2001
TB
RAILWAY INDUSTRY STANDARD
OF THE PEOPLE’S REPUBLIC OF CHINA
eqv ISO 5948.1994
Ultrasonic inspection of rolling stock axles
ISSUED ON. MAY 28, 2001
IMPLEMENTED ON. DECEMBER 01, 2001
Issued by. Ministry of Railways of People’s Republic of China
Table of contents
Foreword ... 3
lSO introduction ... 4
1 Scope ... 5
2 Normative references ... 5
3 Personnel requirements ... 5
4 Instrument, probe and coupling agent ... 6
5 Test block and curves ... 6
6 Preparation of Radial testing distance - amplitude curve ... 6
7 Testing conditions ... 7
8 Axial acoustic transmission testing sensitivity ... 7
9 Axial testing sensitivity ... 7
10 Radial testing sensitivity ... 7
11 Acceptance ... 8
Appendix A (Normative) TS-1 test block ... 11
Appendix B (Normative) TS-1W test block ... 12
Appendix C (Normative) TS-2 test block schematics ... 13
Appendix D (Normative) Axial defect testing distance – amplitude curve ... 14
Appendix E (Normative) Radial defect testing distance - amplitude curve
schematics ... 15
Foreword
The relevant rolling stock axle ultrasonic test method in this Standard is
equivalent to the method specified in ISO 5948-1994 “Railway rolling stock
material-ultrasonic acceptance testing”.
From the date of implementation of this Standard, it shall replace TB 1618-85
“Ultrasonic inspection of rolling stock axles”.
The Appendix A, Appendix B, Appendix C, Appendix D and Appendix E of
standard are normative.
This Standard was proposed by the Ministry of Railways – Qishuyan
Locomotive and Rolling Stock Technology Research Institute.
This Standard shall be under the jurisdiction of the Ministry of Railways –
Qishuyan Locomotive and Rolling Stock Technology Research Institute.
The drafting organizations of this Standard. Ministry of Railways – Qishuyan
Locomotive and Rolling Stock Technology Research Institute, China Academy of
Railway Sciences – Metals and Chemistry Research Institute.
Main drafters of this Standard. Huang Yongwei, Li Lianxiu, Lu Xuanguo, Yao
Rongwen.
This Standard was first-time issued on December 14, 1985.
This Standard was first-time revised in May 2001.
RAILWAY INDUSTRY STANDARD
OF THE PEOPLE’S REPUBLIC OF CHINA
eqv ISO 5948.1994
Ultrasonic inspection of rolling stock axles
1 Scope
This Standard specifies the newly made railway rolling stock axle’s ultrasonic
inspection method AND acceptance specifications.
This Standard applies to the testing of newly made axle material’s overall
performance AND internal defects.
2 Normative references
The provisions in following documents become the provisions of this Standard
through reference in this Standard. At the time of publication of this Standard,
the editions indicated were valid. All standards are subject to revision, however,
parties who use this Standard are encouraged to study if the latest versions of
these documents are applicable.
JB/T 10061-1999 Commonly used specification for A-mode ultrasonic defect
detector using pulse echo technique
JB/T 10062-1999 Testing methods for performance of probes used in
ultrasonic defect testing
GB/T 1804-1992 General tolerances – Tolerances for linear and angular
dimensions without individual tolerance indications
3 Personnel requirements
3.1 The personnel who undertake axle ultrasonic testing must acquire
appropriate basic knowledge, AND be familiar with the provisions of this
Standard.
3.2 The testing personnel must obtain the grade II and above NDT technical
qualification certificate which is issued by the Ministry of Railway – NDT
personnel technical qualification assessment commission.
4 Instrument, probe and coupling agent
4.1 The ultrasonic defect detector shall comply with the requirements of JB/T
10061.
4.2 Ultrasonic probe
4.2.1 Probe type. 2.5P20Z longitudinal wave straight probes.
4.2.2 Main beam deviation. the included angle between the probe’s main beam
AND the probe’s normal shall not be more than 1o.
4.2.3 The sound pressure distribution of the probe sound field shall not have
obvious double peaks.
4.2.4 As for the other performance indicators and test methods of probe, it shall
comply with the requirements of JB/T 10062.
4.3 Coupling agent. engine oil, glycerine or water.
5 Test block and curves
5.1 As for TS-1 test block, see Appendix A.
5.2 As for TS-1W test block, see Appendix B.
5.3 As for TS-2 test block schematics, see Appendix C.
5.4 As for axial defect testing distance - amplitude curve schematics, see
Appendix D.
5.5 As for radial defect testing distance - amplitude curve schematics, see
Appendix E.
6 Preparation of Radial testing distance - amplitude
curve
6.1 Radial testing distance – the amplitude curve is prepared by the testing
personnel based on the testing system used. Before use, it shall calibrate this
curve.
PLACE the straight probe onto the TS-2 test block’s journal; ADJUST the
instrument, to make the echo height of No.1 flat bottom hole equal to 50% of
the full vertical scale; COMPENSATE the coupling difference between the test
block and real axle; GAIN another 4 dB, which is the testing sensitivity.
10.2 Wheel seat
PLACE the straight probe onto the TS-2 test block’s wheel seat; ADJUST the
instrument, to make the echo height of No.4 flat bottom hole equal to 50% of
the full vertical scale; COMPENSATE the coupling difference between the test
block and real axle; GAIN another 4 dB, which is the testing sensitivity.
10.3 Axle body
PLACE the straight probe onto the TS-2 test block’s axle body; ADJUST the
instrument, to make the echo height of No.7 flat bottom hole equal to 50% of
the full vertical scale; COMPENSATE the coupling difference between the test
block and real axle; GAIN another 4 dB, which is the testing sensitivity.
10.4 Bottom echo attenuation
PLACE the straight probe onto the TS-2 test block’s axle body; MAKE the echo
height of the axle body bottom at No.10 taper hole equal to 50% of the full
vertical scale; COMPENSATE the coupling difference between the test block
and real axle, which is the testing sensitivity by bottom echo height attenuation
method.
11 Acceptance
11.1 Axial acoustic transmission
11.1.1 Acceptance region. within the axle end face center to 1/2R area, AND
the region boundary is based on the probe center.
11.1.2 Within the acceptance region, if the bottom echo height equals to or
higher than the reference wave height, it is deemed as qualified.
11.1.3 Within the acceptance region, if the bottom echo height is lower than the
reference wave height, the total area does not exceed 1/16 of the acceptance
region, AND the amplitude decrease is not less than 1/2 of the reference wave
height, it is also deemed as qualified.
11.1.4 If it fails to meet the requirements of Clause 11.1.2 and 11.1.3, it is
deemed as disqualified.
Share
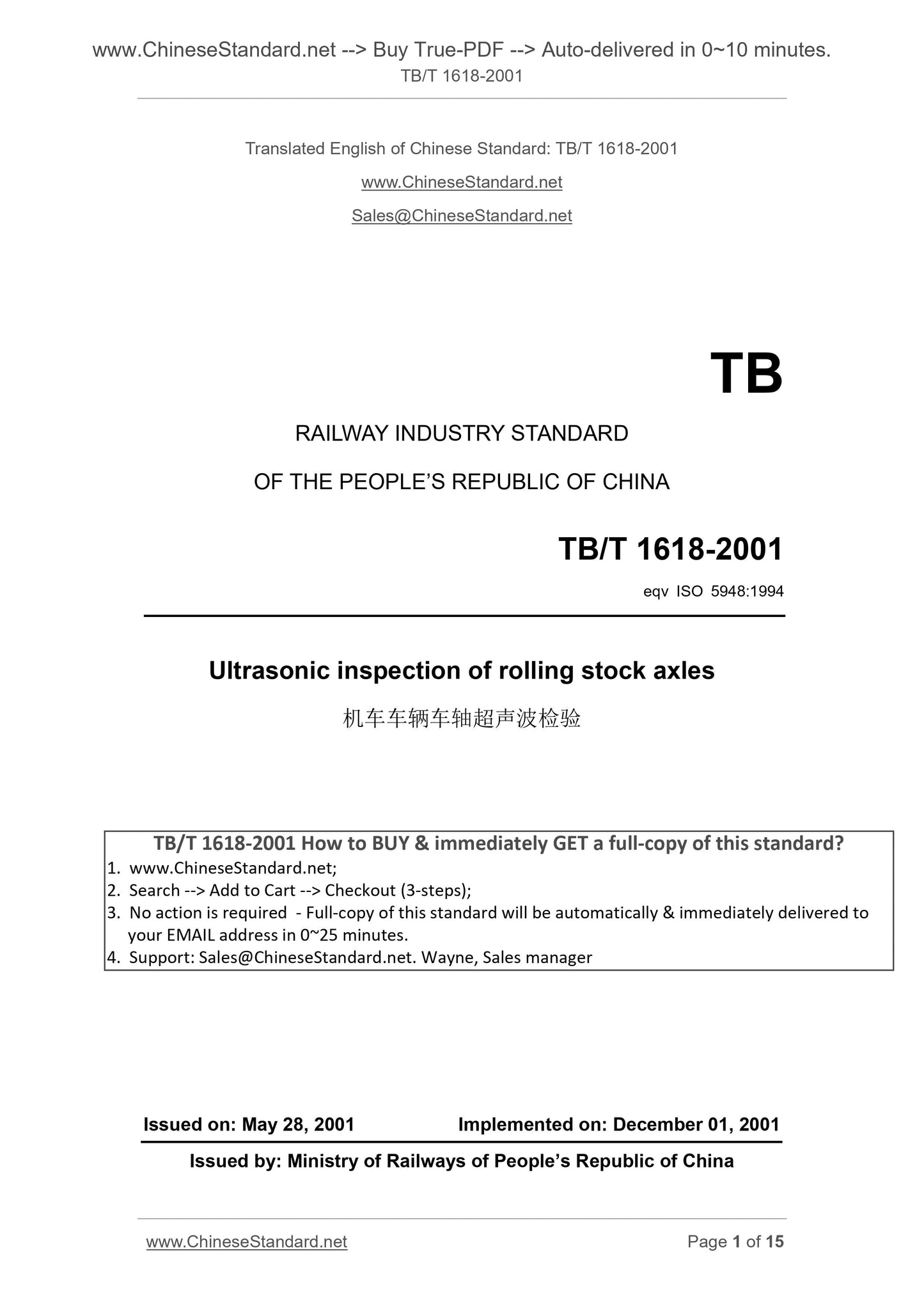
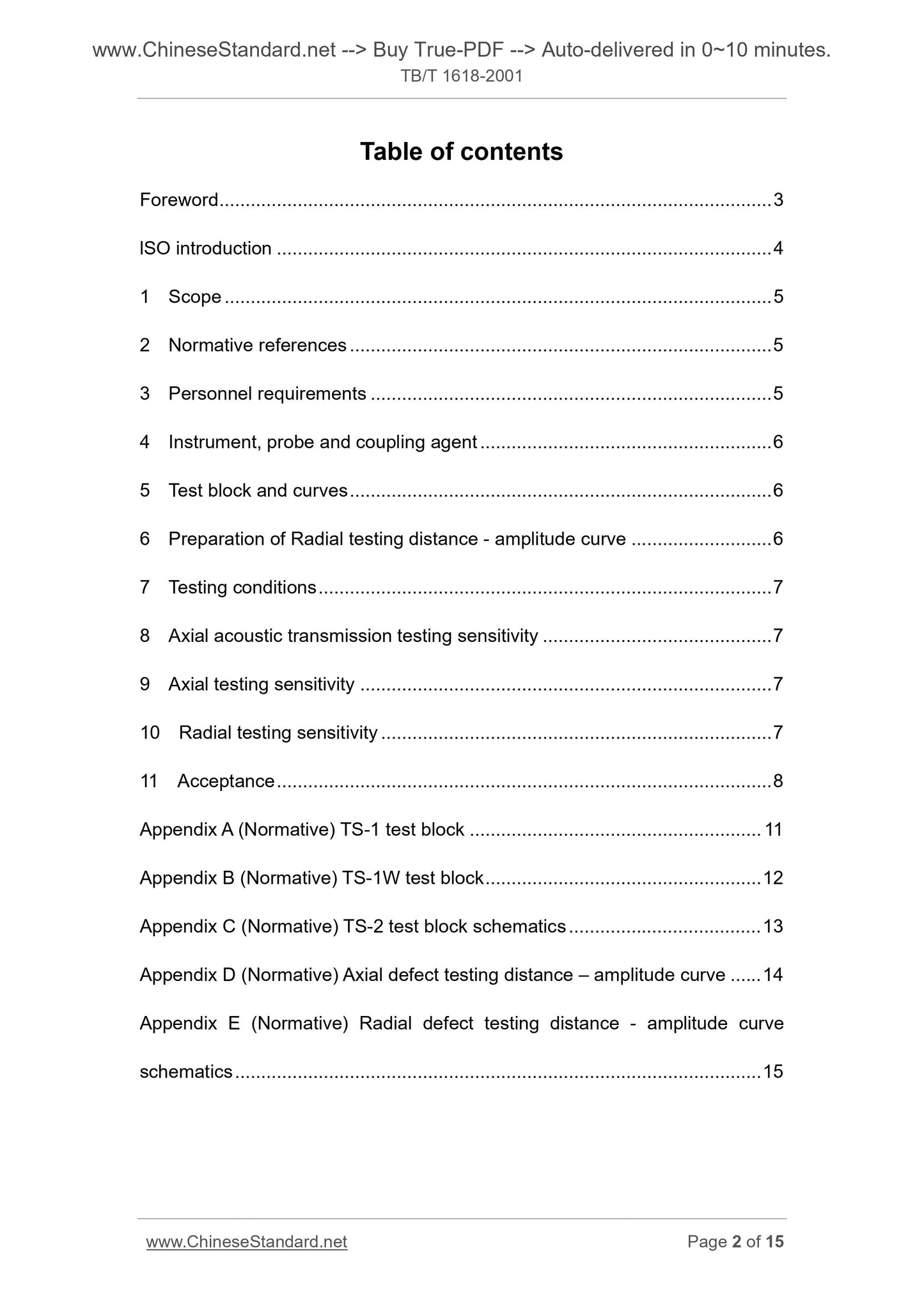
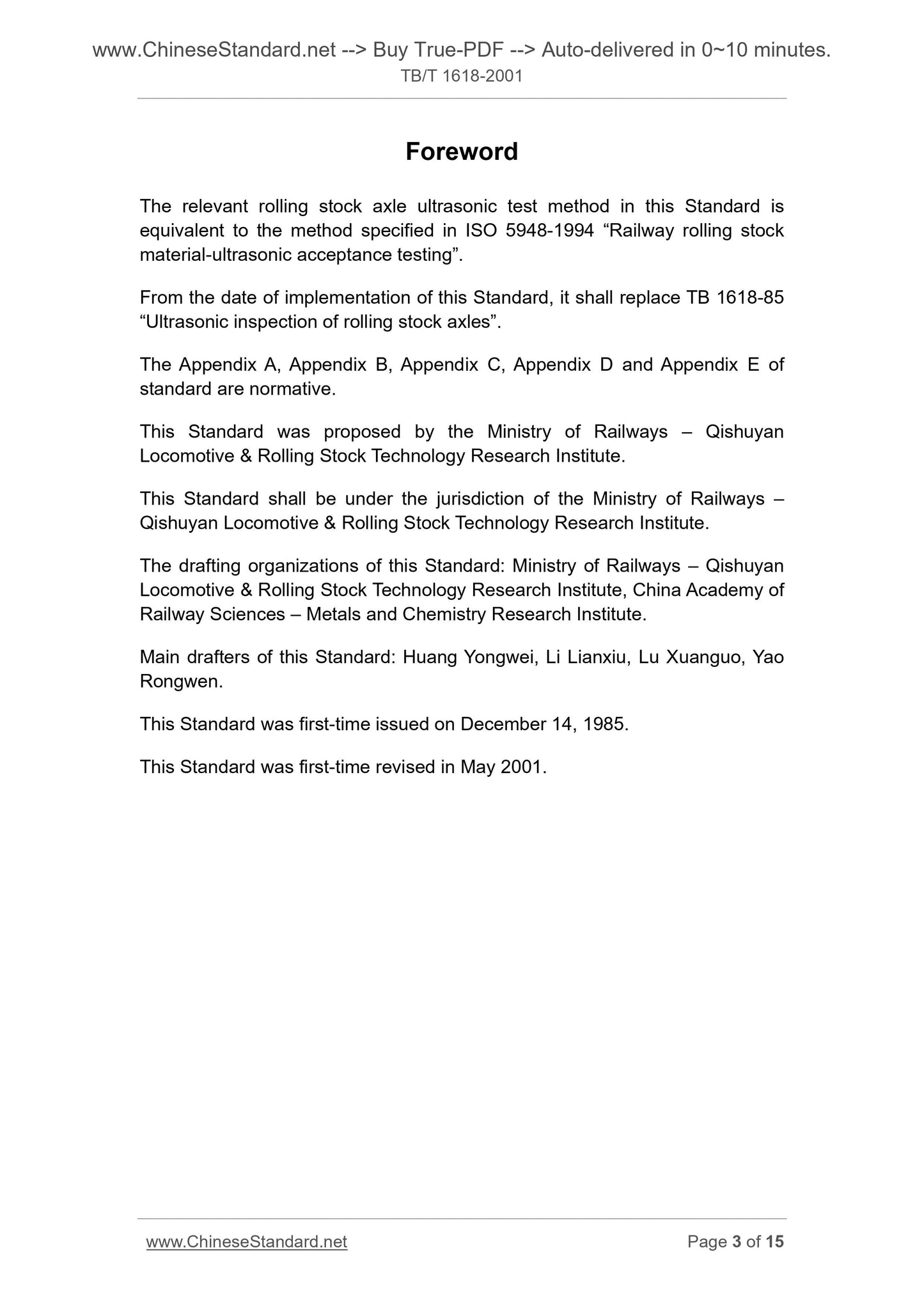
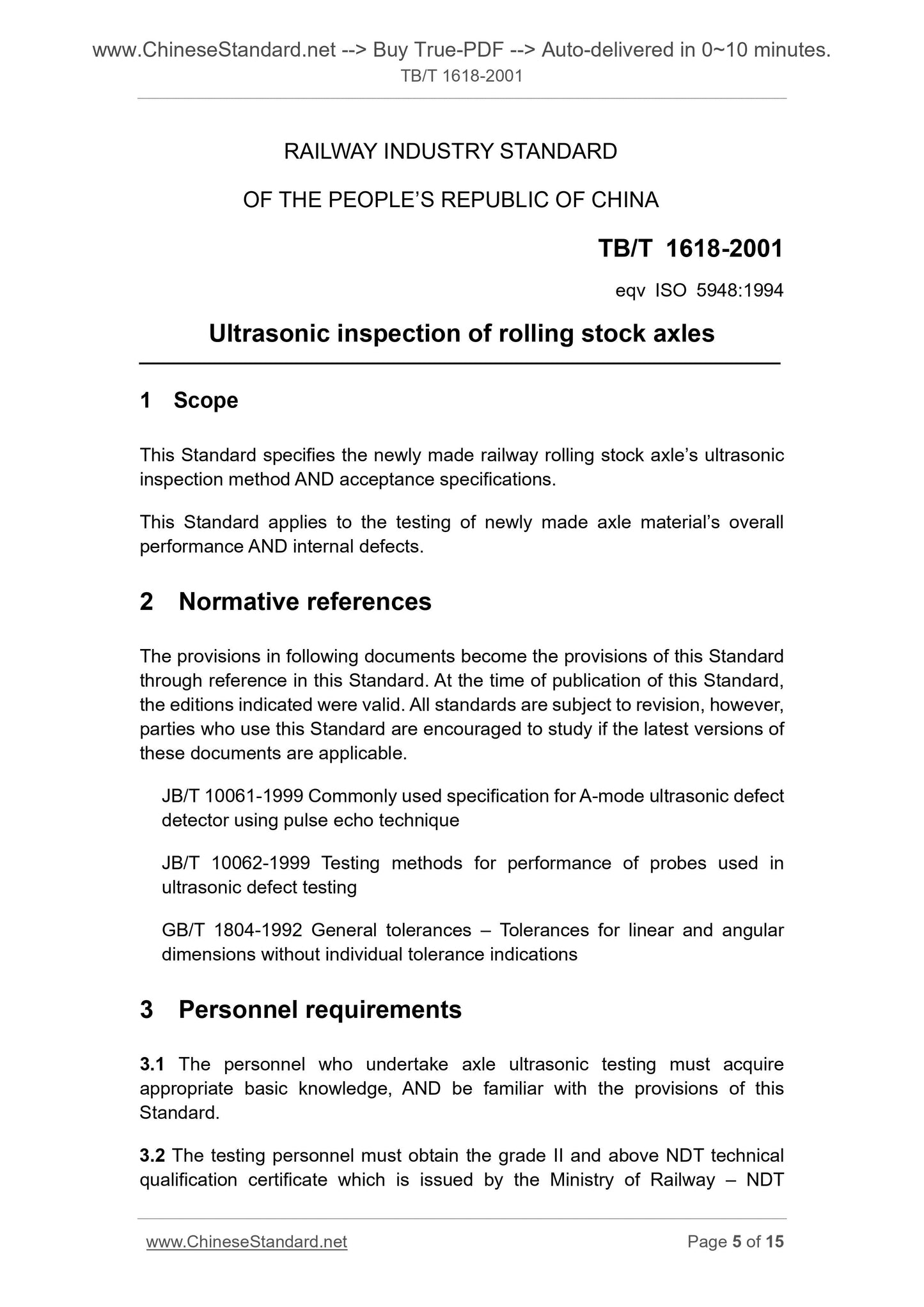
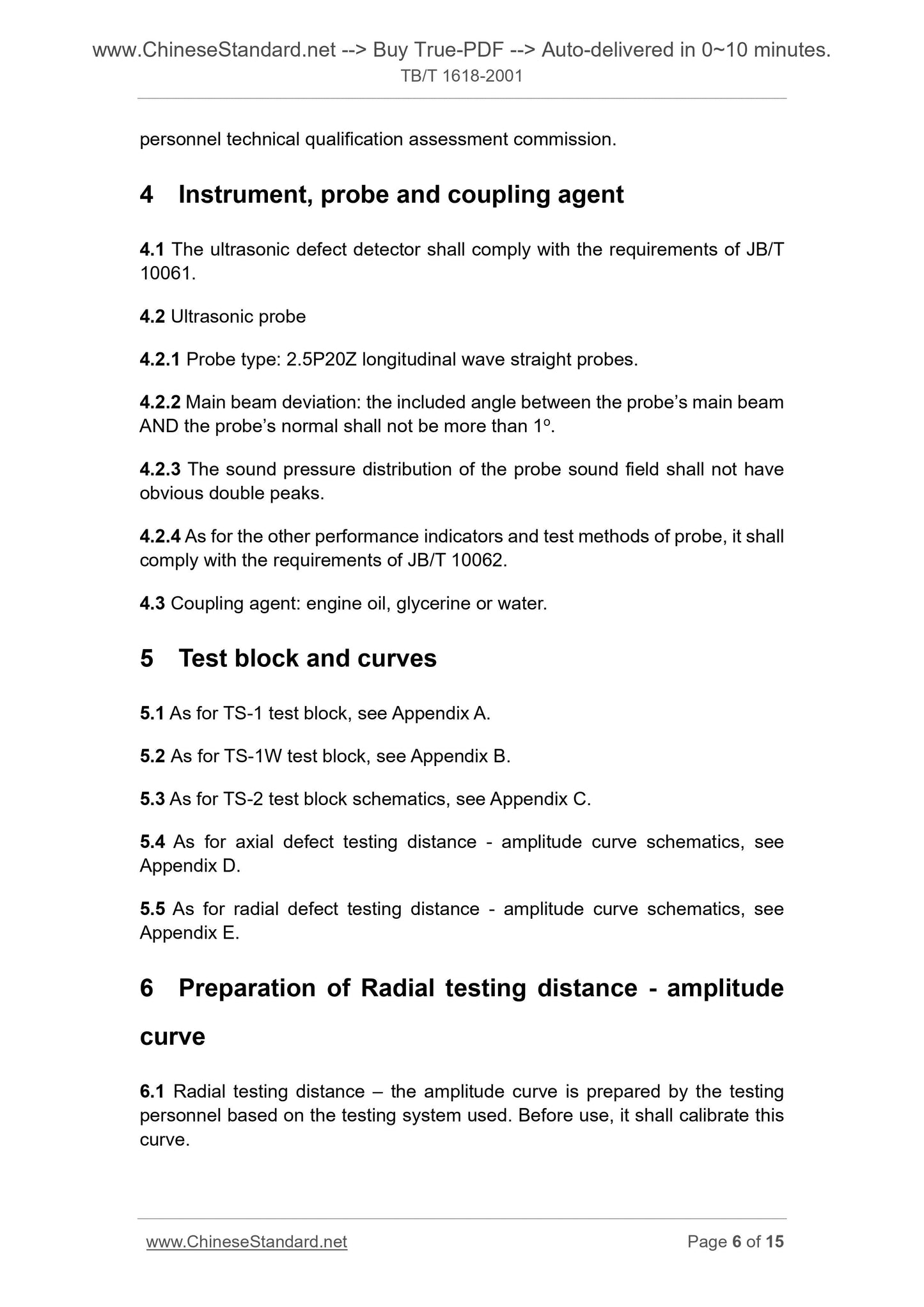
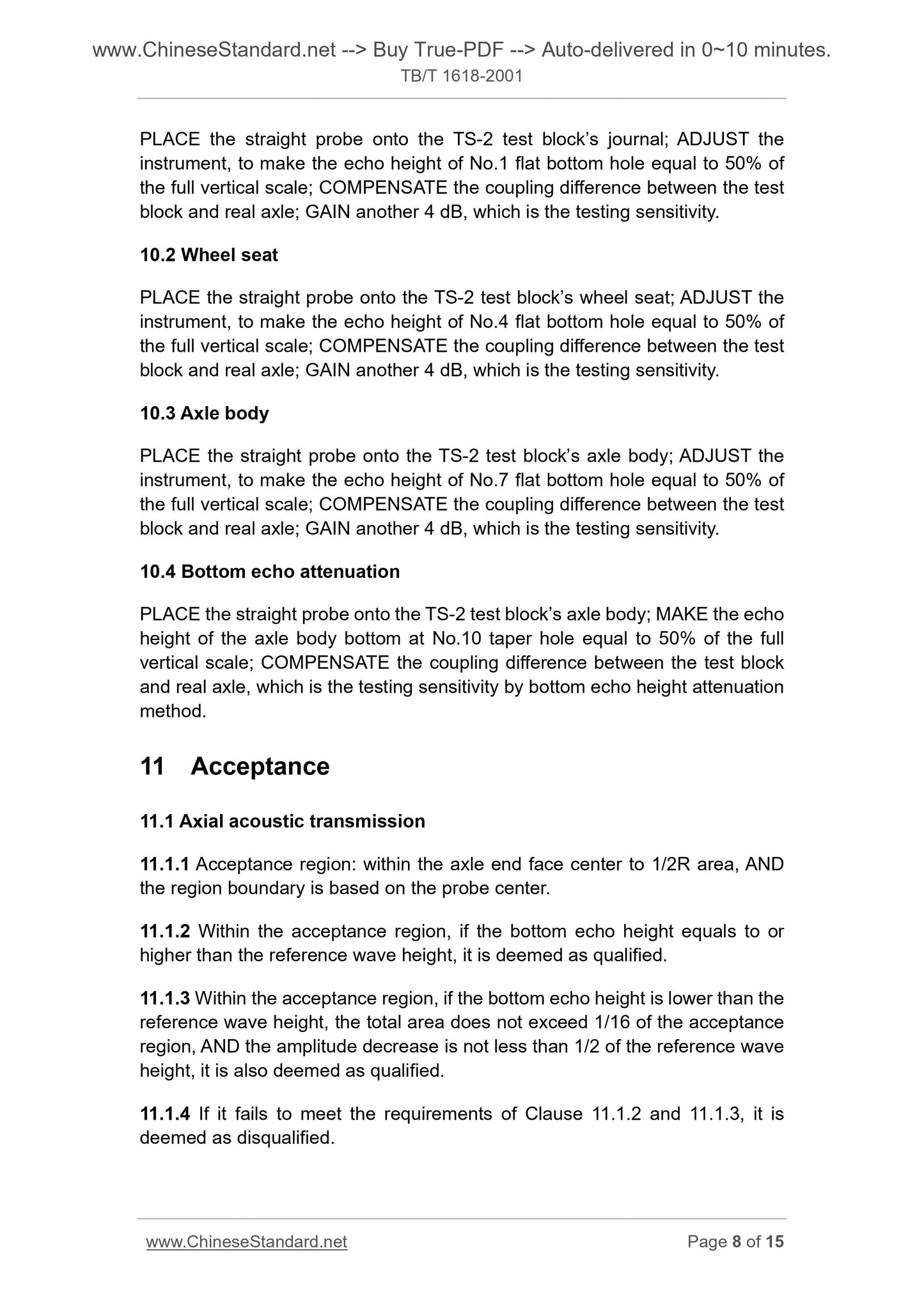