1
/
of
9
PayPal, credit cards. Download editable-PDF and invoice in 1 second!
CB/T 4197-2011 English PDF (CB/T4197-2011)
CB/T 4197-2011 English PDF (CB/T4197-2011)
Regular price
$220.00 USD
Regular price
Sale price
$220.00 USD
Unit price
/
per
Shipping calculated at checkout.
Couldn't load pickup availability
Delivery: 3 seconds. Download true-PDF + Invoice.
Get QUOTATION in 1-minute: Click CB/T 4197-2011
Historical versions: CB/T 4197-2011
Preview True-PDF (Reload/Scroll if blank)
CB/T 4197-2011: The technical specifications of turbochargers used for marine diesel engines
CB/T 4197-2011
MARINE INDUSTRY STANDARD OF
THE PEOPLE’S REPUBLIC OF CHINA
ICS 47.020.20
U 44
Filing No.: 32906-2011
The technical specifications of turbochargers used for
marine diesel engines
ISSUED ON: JUNE 15, 2011
IMPLEMENTED ON: OCTOBER 01, 2011
Issued by: Ministry of Industry and Information Technology of PRC
Table of Contents
Foreword ... 3
1 Scope ... 4
2 Normative references ... 4
3 Technical requirements ... 4
4 Tests ... 8
5 Inspection rules ... 15
6 Marking, packaging, transportation, storage ... 17
Appendix A (Normative) Measurement items and compressor and turbine performance
curves ... 20
The technical specifications of turbochargers used for
marine diesel engines
1 Scope
This standard specifies the technical requirements, test, inspection rules, marking,
packaging, transportation, storage of turbochargers used for marine diesel engines.
This standard applies to the design, manufacture, acceptance of turbochargers
(hereinafter referred to as "turbochargers"), which is matched with marine diesel
engines, used as main propulsion or power generation auxiliary engines of ship.
2 Normative references
The following documents are essential to the application of this document. For the dated
documents, only the versions with the dates indicated are applicable to this document;
for the undated documents, only the latest version (including all the amendments) is
applicable to this standard.
GB 727 Turbocharger nomenclature and code
GB/T 1147 Reciprocating internal combustion engines - General technical
specifications
GB/T 9239.1-2006 Mechanical vibration - Balance quality requirements for rotors
in a constant (rigid) state - Part 1: Specification and verification of balance
tolerances
CB/T 3253 Technical conditions for marine diesel engine
3 Technical requirements
3.1 Nomenclature and designation
The nomenclature and designation of the turbocharger shall comply with the provisions
of GB 727.
3.2 Classification
The turbocharger is divided into the following, according to turbine type:
the turbocharger, the air temperature and pressure at the outlet of the compressor, the
temperature and pressure of the exhaust gas at the inlet of the turbine.
3.5.4 The casing design of the turbocharger shall ensure that it has sufficient
containment, to ensure that any part of the rotor will fly away without penetrating the
casing, when the turbocharger is abnormal.
3.5.5 The main rotating parts and rotor assembly of the turbocharger, such as the air
guide wheel, the compressor impeller, the main shaft with blades, shall be subjected to
a dynamic balance test. The balance accuracy shall reach the balance quality grade G2.5
of GB/T 9239.1-2006.
3.5.6 The air guide wheel and compressor impeller of the turbocharger shall be
subjected to an overspeed test. The overspeed speed shall not be lower than 110% of
the maximum speed of the turbocharger.
3.5.7 The turbocharger shall be provided with an air intake muffler filter. The air intake
muffler filter shall have the functions of filtering dust and impurities AND reducing
intake noise.
3.5.8 For the turbocharger, whose lubricating oil is supplied by the lubricating oil
system of the diesel engine, when the lubricating oil's filtration accuracy of the diesel
engine cannot meet the requirements of the turbocharger, it shall provide a lubricating
oil filter, which matches the bearing system, in front of the lubricating oil inlet of the
turbocharger; meanwhile it shall be provided with low pressure and high temperature
alarming device. The lubricating oil pressure shall be in the range of 150 kPa ~ 600 kPa.
The inlet temperature of lubricating oil is generally not lower than 40 °C; the outlet
temperature is not higher than 120 °C.
3.5.9 For a turbocharger, which has a water-cooled casing, the inlet temperature of the
cooling water shall not be lower than 30 °C; the outlet temperature shall not be higher
than 90 °C; the temperature difference between the inlet and outlet of the cooling water
in the same casing shall not exceed 12 °C. The cooling water's flow and pressure shall
meet the requirements for the temperature difference, between the cooling water inlet
and outlet.
3.5.10 The working conditions of pitch and heel of the turbocharger shall meet the
relevant provisions in GB/T 1147 and CB/T 3253.
3.5.11 The same type of parts of the same type of turbocharger shall have complete
interchangeability.
3.5.12 The turbocharger shall be equipped with a rotor locking device.
3.6 Performance
3.6.1 Aerodynamic performance
The total efficiency of the turbocharger, flow rate, compressor's pressure ratio,
compressor efficiency, turbine efficiency shall reach the design indicators. Under the
specified pressure ratio, the maximum deviation of the speed shall not exceed ±2%; the
maximum deviation of the flow shall not exceed ±3%.
3.6.2 Reliability
The turbocharger, that is normally used according to the maintenance and operation
instructions, shall be able to operate safely and stably, under its calibrated maximum
allowable speed and maximum allowable temperature (referring to the exhaust gas
temperature at turbine inlet). This calibration value corresponds to the 110% load
condition of the matched diesel engine AND has a certain margin.
3.7 Leaks
The cooling water cavity and oil cavity of the turbocharger shall be subjected to a
hydraulic test. The test pressure shall be 500 kPa or 1.5 times the working pressure
(whichever is greater), which lasts for 5 minutes. There shall be no leakage. When the
turbocharger is running, there shall be no water leakage, oil leakage, air leakage in the
casing and each seal.
3.8 Environmental adaptability
The design, test, parameter calculation of the turbocharger are based on the following
standard environmental conditions:
a) Ambient temperature t0 = 25 °C;
b) Atmospheric pressure p0 = 100 kPa;
c) Relative humidity Φ0 = 60%.
3.9 Vibration
When the turbocharger is running stably at each speed, the maximum allowable
vibration velocity of the axial-flow turbocharger is 4 mm/s. When the radial-flow and
mixed-flow turbochargers use a water-cooled casing, the allowable maximum vibration
velocity is 6 mm/s. When using a non-water-cooled casing, the maximum allowable
vibration velocity value is 4 mm/s.
3.10 Noise
During the platform test, the average value of the noise of the turbocharger (tested with
a muffler filter, sound pressure level) shall meet the requirements of Table 1.
The turbine performance test shall be carried out, on the turbine performance test bench.
When the conditions are not available, the turbocharger can also be operated in the self-
circulating condition, on the turbocharger test bench. Based on the measured parameters,
use the thermodynamic method to calculate the turbine performance parameters directly.
The specific measurement items are as shown in A.1 in Appendix A. After the test, the
expansion ratio-turbine efficiency curve and the expansion ratio-flow capacity curve
shall be made, according to the calculation results, as shown in A.3 in Appendix A.
The results of the turbine performance test shall meet the requirements of 3.6.1.
4.1.2.2.3 Performance test of the whole machine
The performance test of the whole machine is carried out on the turbocharger whole
machine test bench. During the test, the turbocharger runs to a specified pressure ratio,
in a self-...
Get QUOTATION in 1-minute: Click CB/T 4197-2011
Historical versions: CB/T 4197-2011
Preview True-PDF (Reload/Scroll if blank)
CB/T 4197-2011: The technical specifications of turbochargers used for marine diesel engines
CB/T 4197-2011
MARINE INDUSTRY STANDARD OF
THE PEOPLE’S REPUBLIC OF CHINA
ICS 47.020.20
U 44
Filing No.: 32906-2011
The technical specifications of turbochargers used for
marine diesel engines
ISSUED ON: JUNE 15, 2011
IMPLEMENTED ON: OCTOBER 01, 2011
Issued by: Ministry of Industry and Information Technology of PRC
Table of Contents
Foreword ... 3
1 Scope ... 4
2 Normative references ... 4
3 Technical requirements ... 4
4 Tests ... 8
5 Inspection rules ... 15
6 Marking, packaging, transportation, storage ... 17
Appendix A (Normative) Measurement items and compressor and turbine performance
curves ... 20
The technical specifications of turbochargers used for
marine diesel engines
1 Scope
This standard specifies the technical requirements, test, inspection rules, marking,
packaging, transportation, storage of turbochargers used for marine diesel engines.
This standard applies to the design, manufacture, acceptance of turbochargers
(hereinafter referred to as "turbochargers"), which is matched with marine diesel
engines, used as main propulsion or power generation auxiliary engines of ship.
2 Normative references
The following documents are essential to the application of this document. For the dated
documents, only the versions with the dates indicated are applicable to this document;
for the undated documents, only the latest version (including all the amendments) is
applicable to this standard.
GB 727 Turbocharger nomenclature and code
GB/T 1147 Reciprocating internal combustion engines - General technical
specifications
GB/T 9239.1-2006 Mechanical vibration - Balance quality requirements for rotors
in a constant (rigid) state - Part 1: Specification and verification of balance
tolerances
CB/T 3253 Technical conditions for marine diesel engine
3 Technical requirements
3.1 Nomenclature and designation
The nomenclature and designation of the turbocharger shall comply with the provisions
of GB 727.
3.2 Classification
The turbocharger is divided into the following, according to turbine type:
the turbocharger, the air temperature and pressure at the outlet of the compressor, the
temperature and pressure of the exhaust gas at the inlet of the turbine.
3.5.4 The casing design of the turbocharger shall ensure that it has sufficient
containment, to ensure that any part of the rotor will fly away without penetrating the
casing, when the turbocharger is abnormal.
3.5.5 The main rotating parts and rotor assembly of the turbocharger, such as the air
guide wheel, the compressor impeller, the main shaft with blades, shall be subjected to
a dynamic balance test. The balance accuracy shall reach the balance quality grade G2.5
of GB/T 9239.1-2006.
3.5.6 The air guide wheel and compressor impeller of the turbocharger shall be
subjected to an overspeed test. The overspeed speed shall not be lower than 110% of
the maximum speed of the turbocharger.
3.5.7 The turbocharger shall be provided with an air intake muffler filter. The air intake
muffler filter shall have the functions of filtering dust and impurities AND reducing
intake noise.
3.5.8 For the turbocharger, whose lubricating oil is supplied by the lubricating oil
system of the diesel engine, when the lubricating oil's filtration accuracy of the diesel
engine cannot meet the requirements of the turbocharger, it shall provide a lubricating
oil filter, which matches the bearing system, in front of the lubricating oil inlet of the
turbocharger; meanwhile it shall be provided with low pressure and high temperature
alarming device. The lubricating oil pressure shall be in the range of 150 kPa ~ 600 kPa.
The inlet temperature of lubricating oil is generally not lower than 40 °C; the outlet
temperature is not higher than 120 °C.
3.5.9 For a turbocharger, which has a water-cooled casing, the inlet temperature of the
cooling water shall not be lower than 30 °C; the outlet temperature shall not be higher
than 90 °C; the temperature difference between the inlet and outlet of the cooling water
in the same casing shall not exceed 12 °C. The cooling water's flow and pressure shall
meet the requirements for the temperature difference, between the cooling water inlet
and outlet.
3.5.10 The working conditions of pitch and heel of the turbocharger shall meet the
relevant provisions in GB/T 1147 and CB/T 3253.
3.5.11 The same type of parts of the same type of turbocharger shall have complete
interchangeability.
3.5.12 The turbocharger shall be equipped with a rotor locking device.
3.6 Performance
3.6.1 Aerodynamic performance
The total efficiency of the turbocharger, flow rate, compressor's pressure ratio,
compressor efficiency, turbine efficiency shall reach the design indicators. Under the
specified pressure ratio, the maximum deviation of the speed shall not exceed ±2%; the
maximum deviation of the flow shall not exceed ±3%.
3.6.2 Reliability
The turbocharger, that is normally used according to the maintenance and operation
instructions, shall be able to operate safely and stably, under its calibrated maximum
allowable speed and maximum allowable temperature (referring to the exhaust gas
temperature at turbine inlet). This calibration value corresponds to the 110% load
condition of the matched diesel engine AND has a certain margin.
3.7 Leaks
The cooling water cavity and oil cavity of the turbocharger shall be subjected to a
hydraulic test. The test pressure shall be 500 kPa or 1.5 times the working pressure
(whichever is greater), which lasts for 5 minutes. There shall be no leakage. When the
turbocharger is running, there shall be no water leakage, oil leakage, air leakage in the
casing and each seal.
3.8 Environmental adaptability
The design, test, parameter calculation of the turbocharger are based on the following
standard environmental conditions:
a) Ambient temperature t0 = 25 °C;
b) Atmospheric pressure p0 = 100 kPa;
c) Relative humidity Φ0 = 60%.
3.9 Vibration
When the turbocharger is running stably at each speed, the maximum allowable
vibration velocity of the axial-flow turbocharger is 4 mm/s. When the radial-flow and
mixed-flow turbochargers use a water-cooled casing, the allowable maximum vibration
velocity is 6 mm/s. When using a non-water-cooled casing, the maximum allowable
vibration velocity value is 4 mm/s.
3.10 Noise
During the platform test, the average value of the noise of the turbocharger (tested with
a muffler filter, sound pressure level) shall meet the requirements of Table 1.
The turbine performance test shall be carried out, on the turbine performance test bench.
When the conditions are not available, the turbocharger can also be operated in the self-
circulating condition, on the turbocharger test bench. Based on the measured parameters,
use the thermodynamic method to calculate the turbine performance parameters directly.
The specific measurement items are as shown in A.1 in Appendix A. After the test, the
expansion ratio-turbine efficiency curve and the expansion ratio-flow capacity curve
shall be made, according to the calculation results, as shown in A.3 in Appendix A.
The results of the turbine performance test shall meet the requirements of 3.6.1.
4.1.2.2.3 Performance test of the whole machine
The performance test of the whole machine is carried out on the turbocharger whole
machine test bench. During the test, the turbocharger runs to a specified pressure ratio,
in a self-...
Share
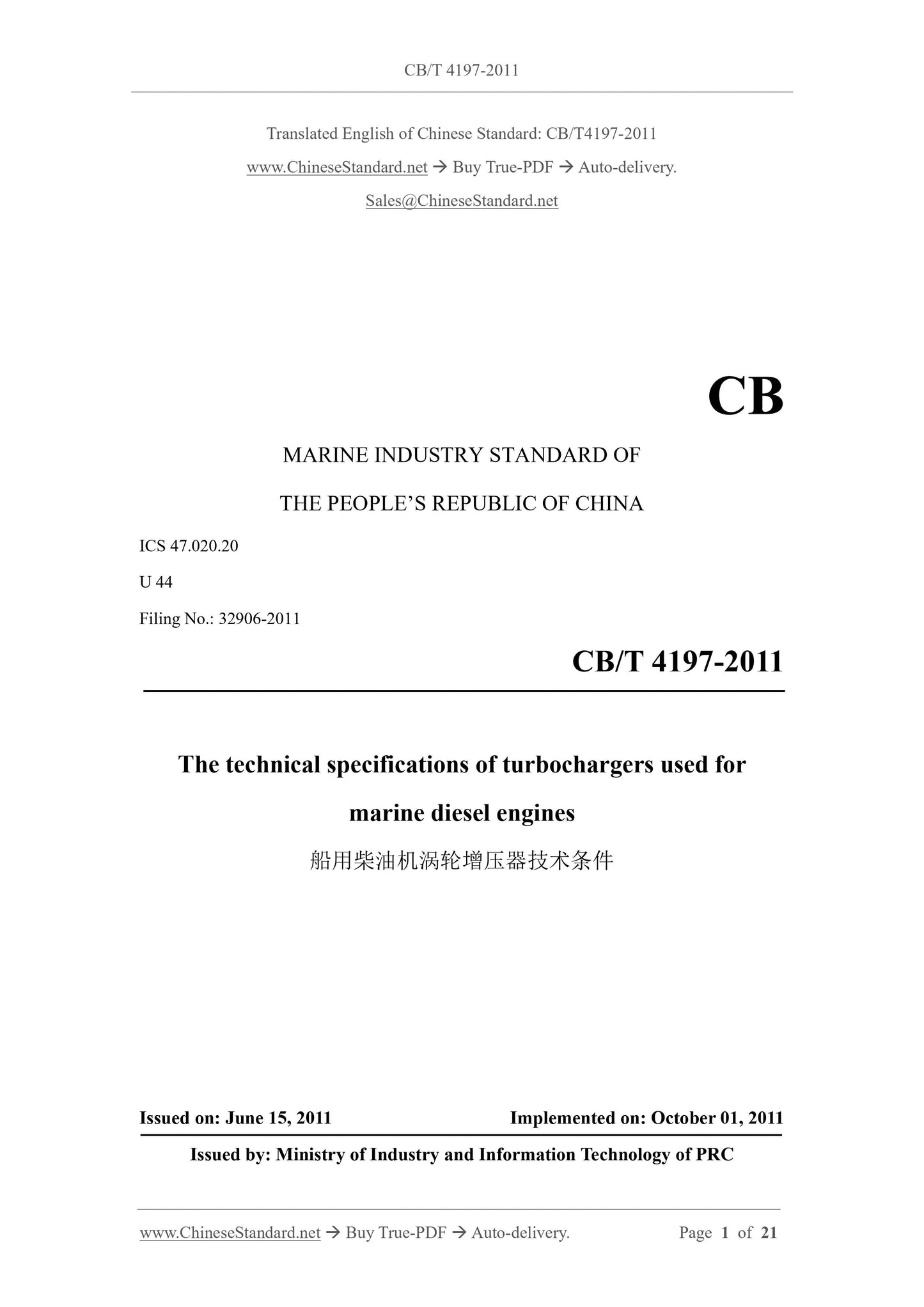
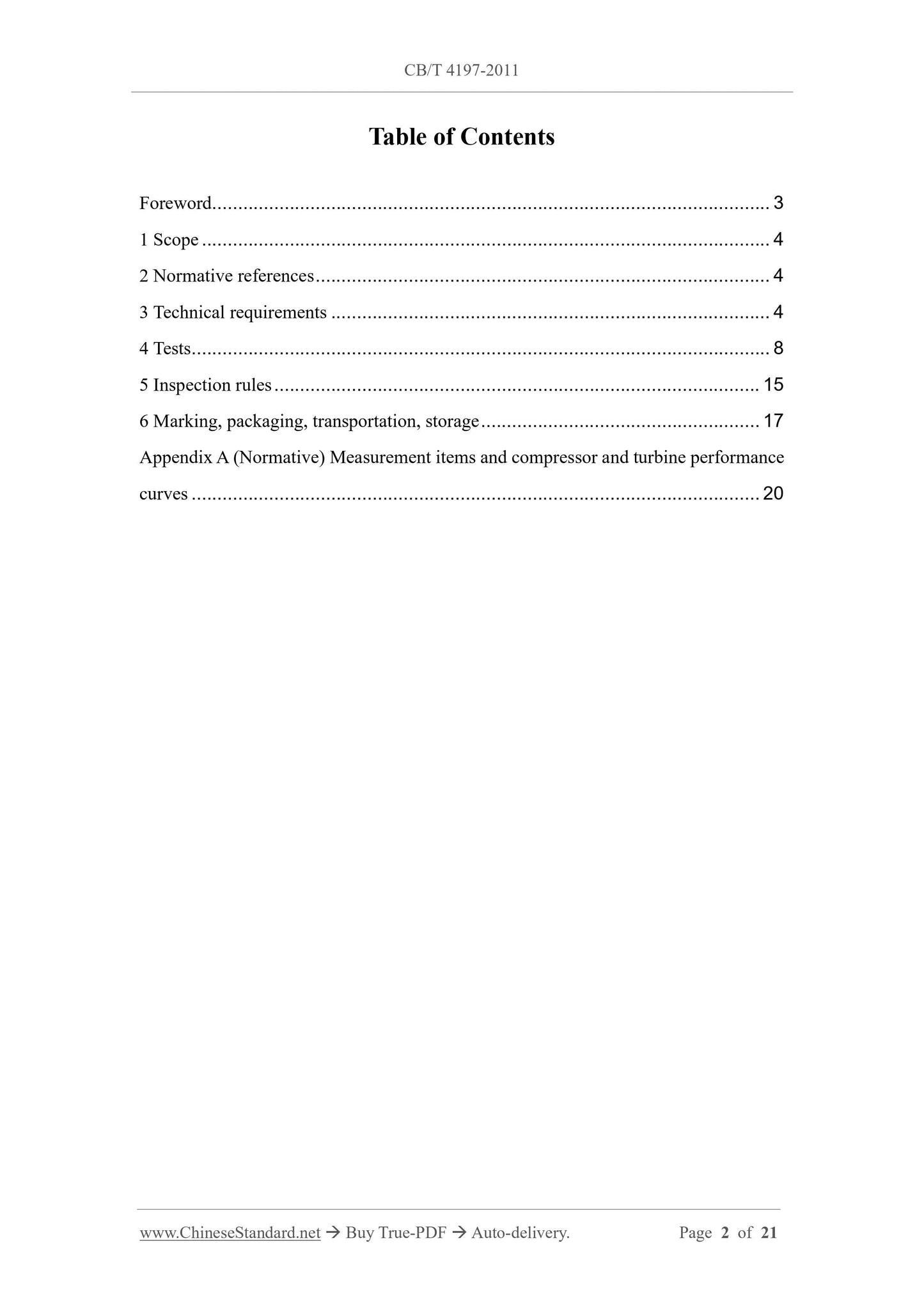

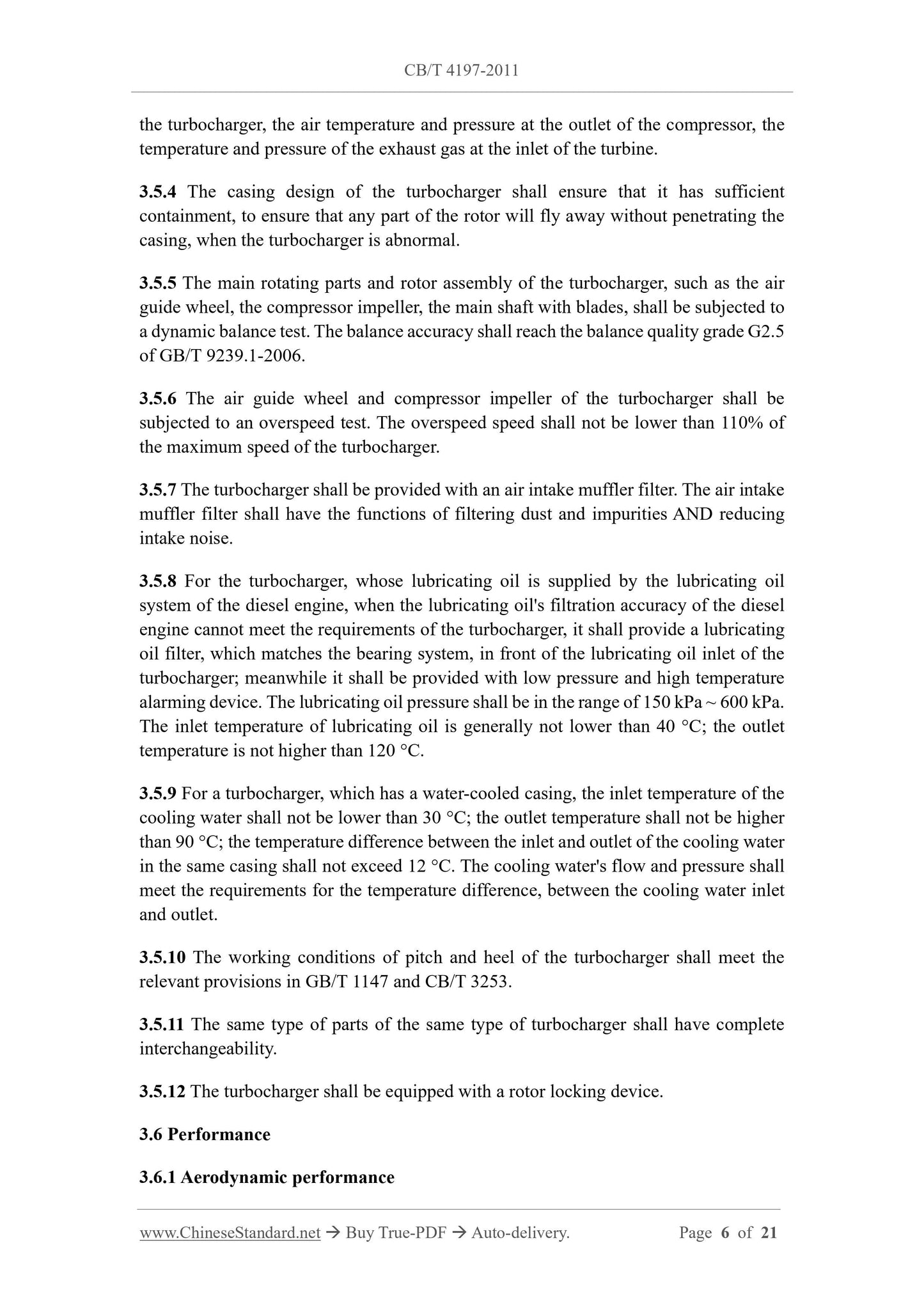
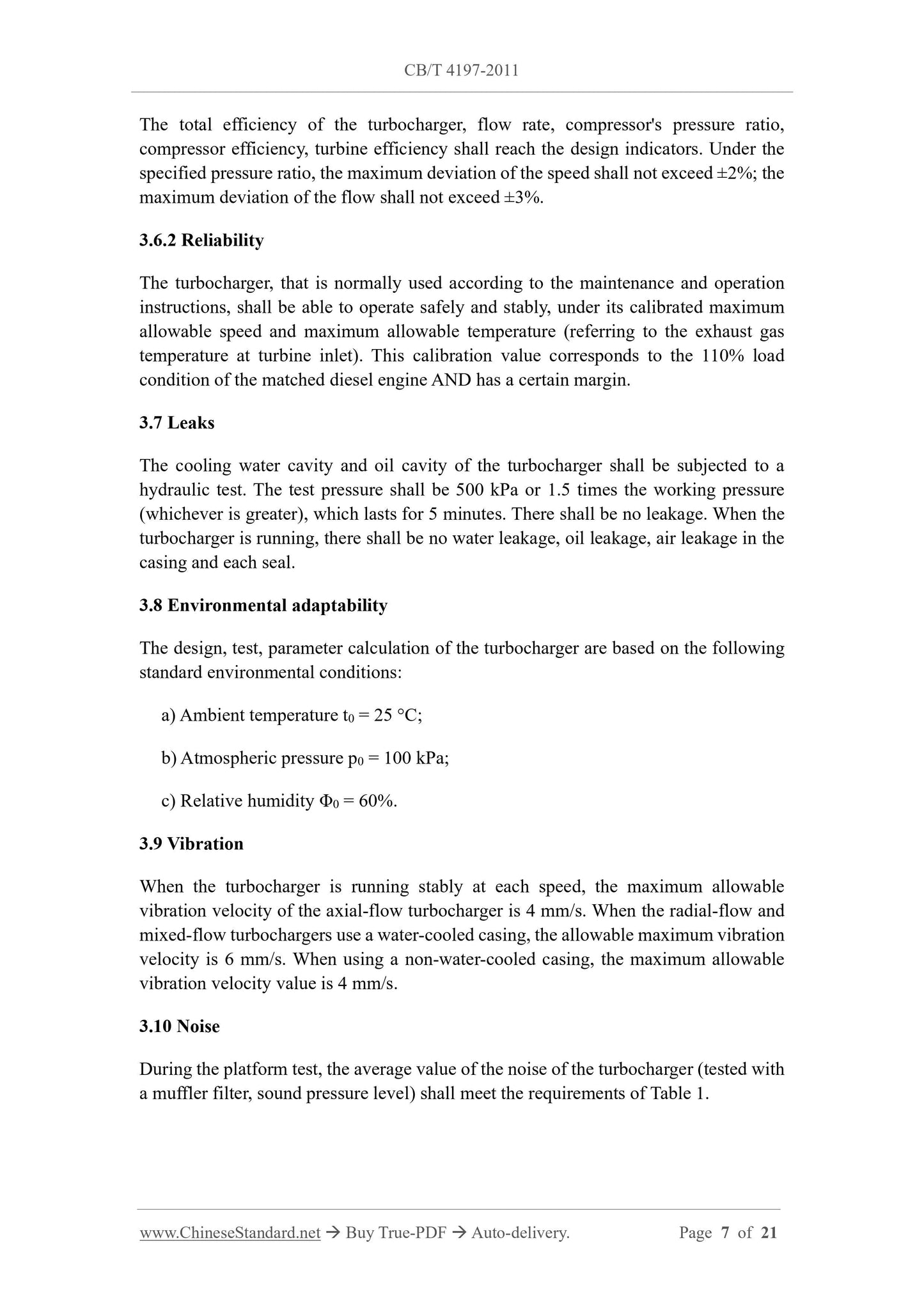
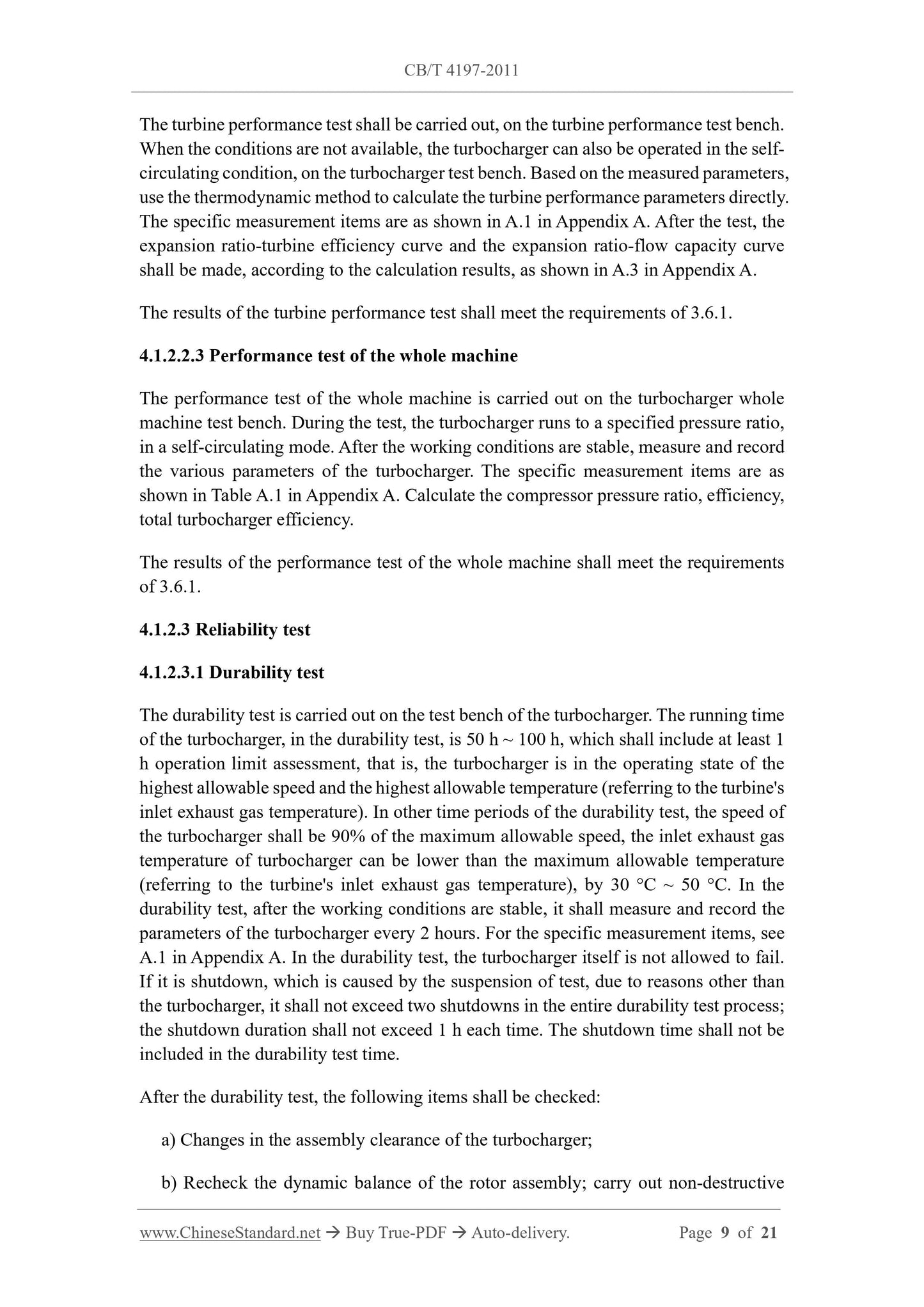
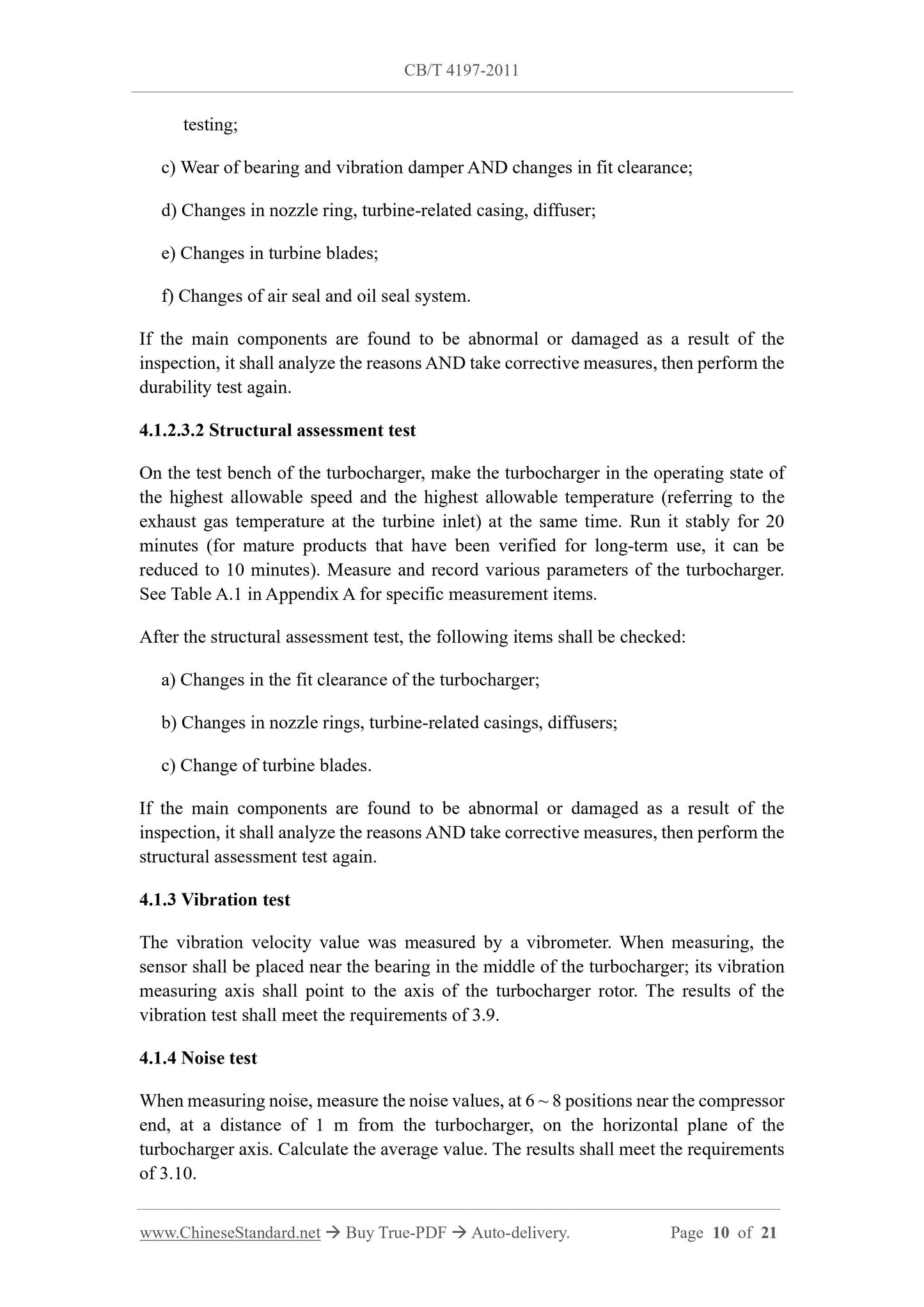
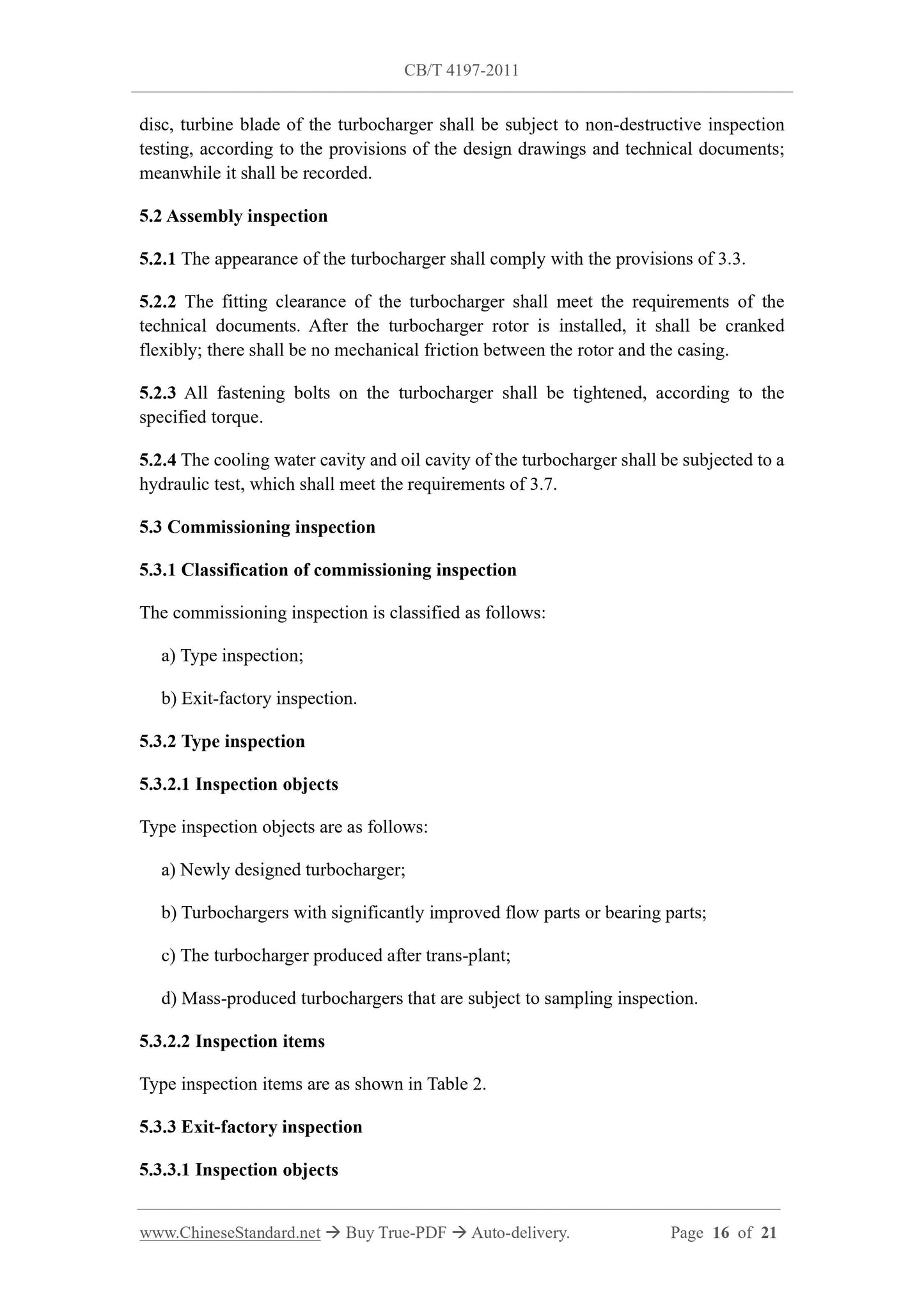
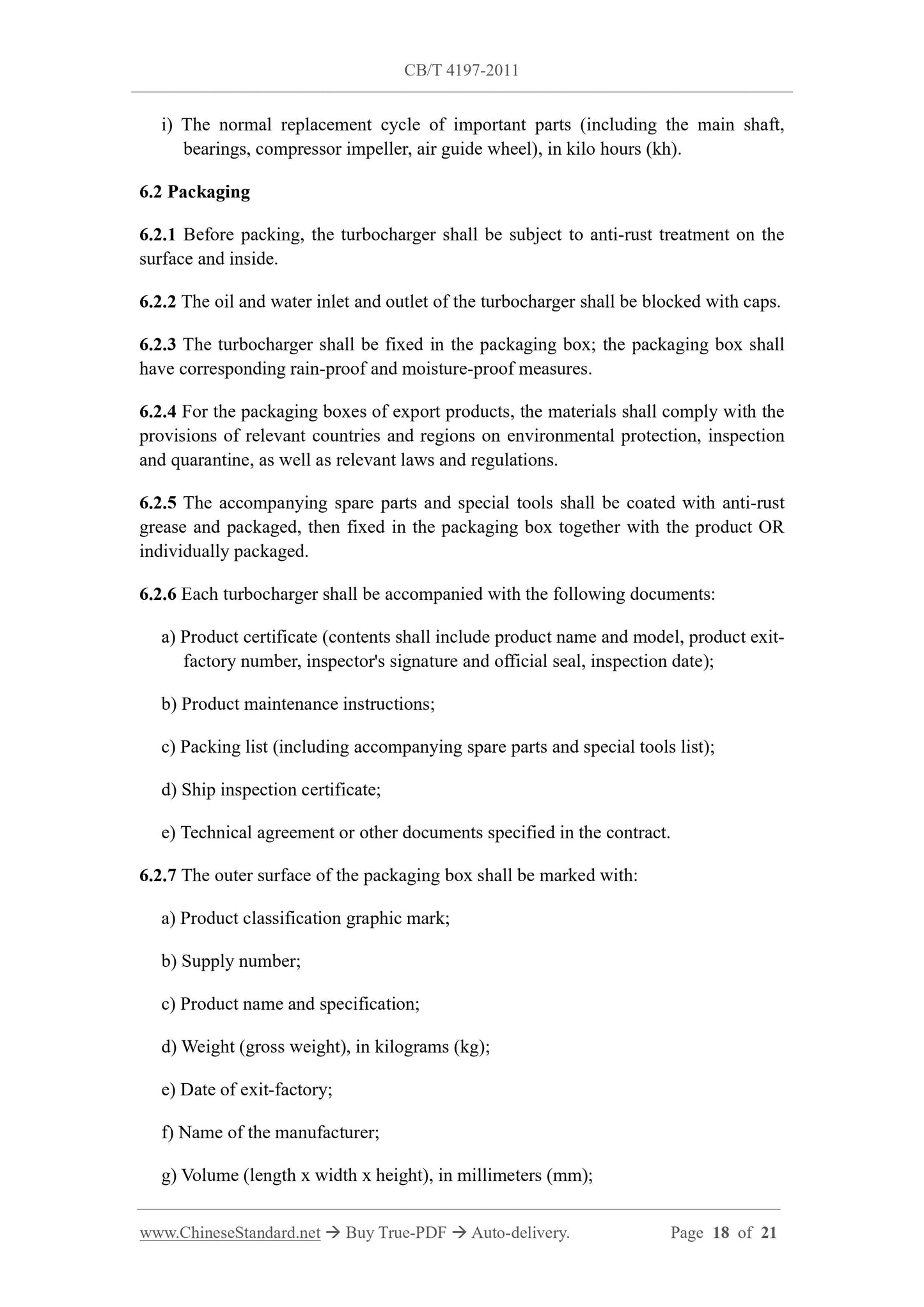