1
/
of
8
PayPal, credit cards. Download editable-PDF and invoice in 1 second!
CQC 11-462298-2018 English PDF (CQC11-462298-2018)
CQC 11-462298-2018 English PDF (CQC11-462298-2018)
Regular price
$305.00 USD
Regular price
Sale price
$305.00 USD
Unit price
/
per
Shipping calculated at checkout.
Couldn't load pickup availability
Delivery: 3 seconds. Download true-PDF + Invoice.
Get QUOTATION in 1-minute: Click CQC 11-462298-2018
Historical versions: CQC 11-462298-2018
Preview True-PDF (Reload/Scroll if blank)
CQC 11-462298-2018: Safety Certification Rules for plug, socket-outlet and couplers for industrial purposes
CQC11-462298-2018
CQC
PRODUCT SAFETY CERTIFICATION RULES
Safety Certification Rules for plug, socket-outlet and
couplers for industrial purposes
ISSUED ON: MAY 18, 2018
IMPLEMENTED ON: MAY 18, 2018
Issued by: China Quality Certification Centre
Table of Contents
Introduction ... 3
1. Scope of application ... 4
2. Certification mode ... 4
3. Application for certification ... 4
4. Product type test ... 5
5. Initial factory inspection ... 7
6. Evaluation, approval and time limit of certification results ... 9
7. Post-certification supervision ... 9
8. Certification certificate ... 11
9. Use of certification mark ... 13
10. Charge ... 13
11. Certification responsibilities ... 13
12. Technical disputes and appeals ... 13
Product description of plugs, socket-outlets and couplers for industrial purposes ... 14
1. Scope of application
This Rules applies to plugs and socket-outlets, cable couplers and appliance couplers
intended primarily for industrial use, for indoor or outdoor use, with a rated working
voltage not exceeding 1000V d.c. or a.c. and 500Hz a.c. and a rated current not
exceeding 800A.
This Rules applies to electrical accessories with a rated current not exceeding 32A in
series I and a rated current not exceeding 30A in series II, and with screwless terminals
or insulation piercing terminals.
Socket-outlets or appliance inlets installed in or fixed to electrical equipment are
covered by this Rules. This Rules also applies to electrical accessories intended for use
in extra-low voltage installations.
This Rules does not apply to electrical accessories that are primarily intended for home
use or similar general purposes.
2. Certification mode
The mode for safety certification of plugs, socket-outlets and couplers for industrial use
are Product type test + Initial factory inspection + Post-certification supervision.
The basic steps of certification include:
a) Application for certification
b) Type test
c) Initial factory inspection
d) Evaluation and approval of certification results
e) Post-certification supervision.
3. Application for certification
3.1 Division of certification units
Apply for certification according to the certification unit, which is generally divided as
follows:
a) Application units shall be divided according to product type, current, structure,
rewirable and non-rewirable, etc.
b) In principle, the same type of electrical accessories with basically the same
structure, the same function, and the same main material category (such as
metal, thermoplastic and thermosetting) can be taken as a certification unit.
Products from different manufacturers are considered as different certification units,
and products from different production factories are considered as different certification
units. Type tests of products of the same specifications and models can be carried out
on samples from one factory.
3.2 Materials submitted for certification application
3.2.1 Application materials
a. Formal application form
b. Factory inspection questionnaire (when first applying)
c. Product description (CQC11-462298.01-2011)
3.2.2 Proof materials
a. Registration certificate of the applicant, manufacturer, or production factory,
such as business license, organization code
b. If the applicant is a seller or importer, a copy of the relevant contract between
the seller and the manufacturer, or between the importer and the manufacturer
must also be submitted.
c. Agent's power of attorney (if any)
d. Other required documents
4. Product type test
4.1 Samples
4.1.1 Sample sending principles and sample quantity
If there is only one model in the application unit, the samples of this model shall be
submitted. When applying for certification with a series of products as the same
application unit, representative samples shall be selected for type testing. If necessary,
the covered samples shall be submitted for supplementary difference testing. The
applicant shall submit samples to the testing agency entrusted by CQC as required. The
number of samples is as follows:
15 sets of samples for the main inspection model (including 3 sets of spare samples)
and 3 sets of samples for each covered model.
4.1.2 Sample and data handling
After the test is completed and the test report is issued, the relevant information will be
kept by the testing agency and the samples will be disposed of in accordance with
relevant CQC regulations.
4.2 Type test
4.2.1 Based on standards
GB/T 11918.1-2014 Plugs, socket-outlets and couplers for industrial purposes - Part 1:
General requirements
GB/T 11918.2-2014 Plugs, socket-outlets and couplers for industrial purposes - Part 2:
Dimensional compatibility and interchangeability requirements for pin and contact-
tube accessories
GB/T 11918.4-2014 Plugs, socket-outlets and couplers for industrial purposes - Part 4:
Switched socket-outlets and connectors with or without interlock
4.2.2 Type test requirements
Product inspection items are all applicable items specified in the standards mentioned
in 4.2.1.
4.2.3 Determination
Type tests shall comply with product standards. If any one item does not meet the
standard requirements, the product of the certification unit is deemed to be non-
compliant with the certification requirements. If part of the type test items are
unqualified, the applicant is allowed to make rectification; the rectification shall be
completed within the time limit specified by the certification body (counted from the
date of the notification of type test non-conformity). If the rectification is not completed
on time, the applicant is deemed to have given up the application; the applicant may
also take the initiative to terminate the application.
4.2.4 Type test time limit and test report
The testing agency designated by CQC will test the samples and issue a test report in
the prescribed format. The sample testing time is generally 35 working days from the
receipt of the samples and the testing fee; the time for the enterprise to make
rectifications and re-tests due to unqualified test items is not included.
After the certification is approved, the testing agency is responsible for sending a test
report to the applicant.
7.1.1 Supervision-inspection time
In general, annual supervision shall be arranged within 12 months after the initial
factory inspection, and the interval between each annual supervision-inspection shall
not exceed 12 months. The certification body may adjust the timing of supervision-
inspection on an annual basis according to the actual situation of product production.
The number of supervision-inspection man-days is shown in Table 2. The supervision
frequency may be increased if any of the following situations occurs:
1) The certified product has serious quality problems or the user has made a
serious complaint and it is verified that the certificate holder is responsible;
2) When CQC has sufficient reasons to question the conformity of the certified
product with the certification basis standards;
3) When there is sufficient information to indicate that changes in the producer
or production factory's organization, production conditions, quality
management system, etc. may affect product conformity or consistency.
7.1.2 Contents of supervision-inspection
The post-certification supervision-inspection method adopts the Supervision-inspection
of the factory's product qual...
Get QUOTATION in 1-minute: Click CQC 11-462298-2018
Historical versions: CQC 11-462298-2018
Preview True-PDF (Reload/Scroll if blank)
CQC 11-462298-2018: Safety Certification Rules for plug, socket-outlet and couplers for industrial purposes
CQC11-462298-2018
CQC
PRODUCT SAFETY CERTIFICATION RULES
Safety Certification Rules for plug, socket-outlet and
couplers for industrial purposes
ISSUED ON: MAY 18, 2018
IMPLEMENTED ON: MAY 18, 2018
Issued by: China Quality Certification Centre
Table of Contents
Introduction ... 3
1. Scope of application ... 4
2. Certification mode ... 4
3. Application for certification ... 4
4. Product type test ... 5
5. Initial factory inspection ... 7
6. Evaluation, approval and time limit of certification results ... 9
7. Post-certification supervision ... 9
8. Certification certificate ... 11
9. Use of certification mark ... 13
10. Charge ... 13
11. Certification responsibilities ... 13
12. Technical disputes and appeals ... 13
Product description of plugs, socket-outlets and couplers for industrial purposes ... 14
1. Scope of application
This Rules applies to plugs and socket-outlets, cable couplers and appliance couplers
intended primarily for industrial use, for indoor or outdoor use, with a rated working
voltage not exceeding 1000V d.c. or a.c. and 500Hz a.c. and a rated current not
exceeding 800A.
This Rules applies to electrical accessories with a rated current not exceeding 32A in
series I and a rated current not exceeding 30A in series II, and with screwless terminals
or insulation piercing terminals.
Socket-outlets or appliance inlets installed in or fixed to electrical equipment are
covered by this Rules. This Rules also applies to electrical accessories intended for use
in extra-low voltage installations.
This Rules does not apply to electrical accessories that are primarily intended for home
use or similar general purposes.
2. Certification mode
The mode for safety certification of plugs, socket-outlets and couplers for industrial use
are Product type test + Initial factory inspection + Post-certification supervision.
The basic steps of certification include:
a) Application for certification
b) Type test
c) Initial factory inspection
d) Evaluation and approval of certification results
e) Post-certification supervision.
3. Application for certification
3.1 Division of certification units
Apply for certification according to the certification unit, which is generally divided as
follows:
a) Application units shall be divided according to product type, current, structure,
rewirable and non-rewirable, etc.
b) In principle, the same type of electrical accessories with basically the same
structure, the same function, and the same main material category (such as
metal, thermoplastic and thermosetting) can be taken as a certification unit.
Products from different manufacturers are considered as different certification units,
and products from different production factories are considered as different certification
units. Type tests of products of the same specifications and models can be carried out
on samples from one factory.
3.2 Materials submitted for certification application
3.2.1 Application materials
a. Formal application form
b. Factory inspection questionnaire (when first applying)
c. Product description (CQC11-462298.01-2011)
3.2.2 Proof materials
a. Registration certificate of the applicant, manufacturer, or production factory,
such as business license, organization code
b. If the applicant is a seller or importer, a copy of the relevant contract between
the seller and the manufacturer, or between the importer and the manufacturer
must also be submitted.
c. Agent's power of attorney (if any)
d. Other required documents
4. Product type test
4.1 Samples
4.1.1 Sample sending principles and sample quantity
If there is only one model in the application unit, the samples of this model shall be
submitted. When applying for certification with a series of products as the same
application unit, representative samples shall be selected for type testing. If necessary,
the covered samples shall be submitted for supplementary difference testing. The
applicant shall submit samples to the testing agency entrusted by CQC as required. The
number of samples is as follows:
15 sets of samples for the main inspection model (including 3 sets of spare samples)
and 3 sets of samples for each covered model.
4.1.2 Sample and data handling
After the test is completed and the test report is issued, the relevant information will be
kept by the testing agency and the samples will be disposed of in accordance with
relevant CQC regulations.
4.2 Type test
4.2.1 Based on standards
GB/T 11918.1-2014 Plugs, socket-outlets and couplers for industrial purposes - Part 1:
General requirements
GB/T 11918.2-2014 Plugs, socket-outlets and couplers for industrial purposes - Part 2:
Dimensional compatibility and interchangeability requirements for pin and contact-
tube accessories
GB/T 11918.4-2014 Plugs, socket-outlets and couplers for industrial purposes - Part 4:
Switched socket-outlets and connectors with or without interlock
4.2.2 Type test requirements
Product inspection items are all applicable items specified in the standards mentioned
in 4.2.1.
4.2.3 Determination
Type tests shall comply with product standards. If any one item does not meet the
standard requirements, the product of the certification unit is deemed to be non-
compliant with the certification requirements. If part of the type test items are
unqualified, the applicant is allowed to make rectification; the rectification shall be
completed within the time limit specified by the certification body (counted from the
date of the notification of type test non-conformity). If the rectification is not completed
on time, the applicant is deemed to have given up the application; the applicant may
also take the initiative to terminate the application.
4.2.4 Type test time limit and test report
The testing agency designated by CQC will test the samples and issue a test report in
the prescribed format. The sample testing time is generally 35 working days from the
receipt of the samples and the testing fee; the time for the enterprise to make
rectifications and re-tests due to unqualified test items is not included.
After the certification is approved, the testing agency is responsible for sending a test
report to the applicant.
7.1.1 Supervision-inspection time
In general, annual supervision shall be arranged within 12 months after the initial
factory inspection, and the interval between each annual supervision-inspection shall
not exceed 12 months. The certification body may adjust the timing of supervision-
inspection on an annual basis according to the actual situation of product production.
The number of supervision-inspection man-days is shown in Table 2. The supervision
frequency may be increased if any of the following situations occurs:
1) The certified product has serious quality problems or the user has made a
serious complaint and it is verified that the certificate holder is responsible;
2) When CQC has sufficient reasons to question the conformity of the certified
product with the certification basis standards;
3) When there is sufficient information to indicate that changes in the producer
or production factory's organization, production conditions, quality
management system, etc. may affect product conformity or consistency.
7.1.2 Contents of supervision-inspection
The post-certification supervision-inspection method adopts the Supervision-inspection
of the factory's product qual...
Share
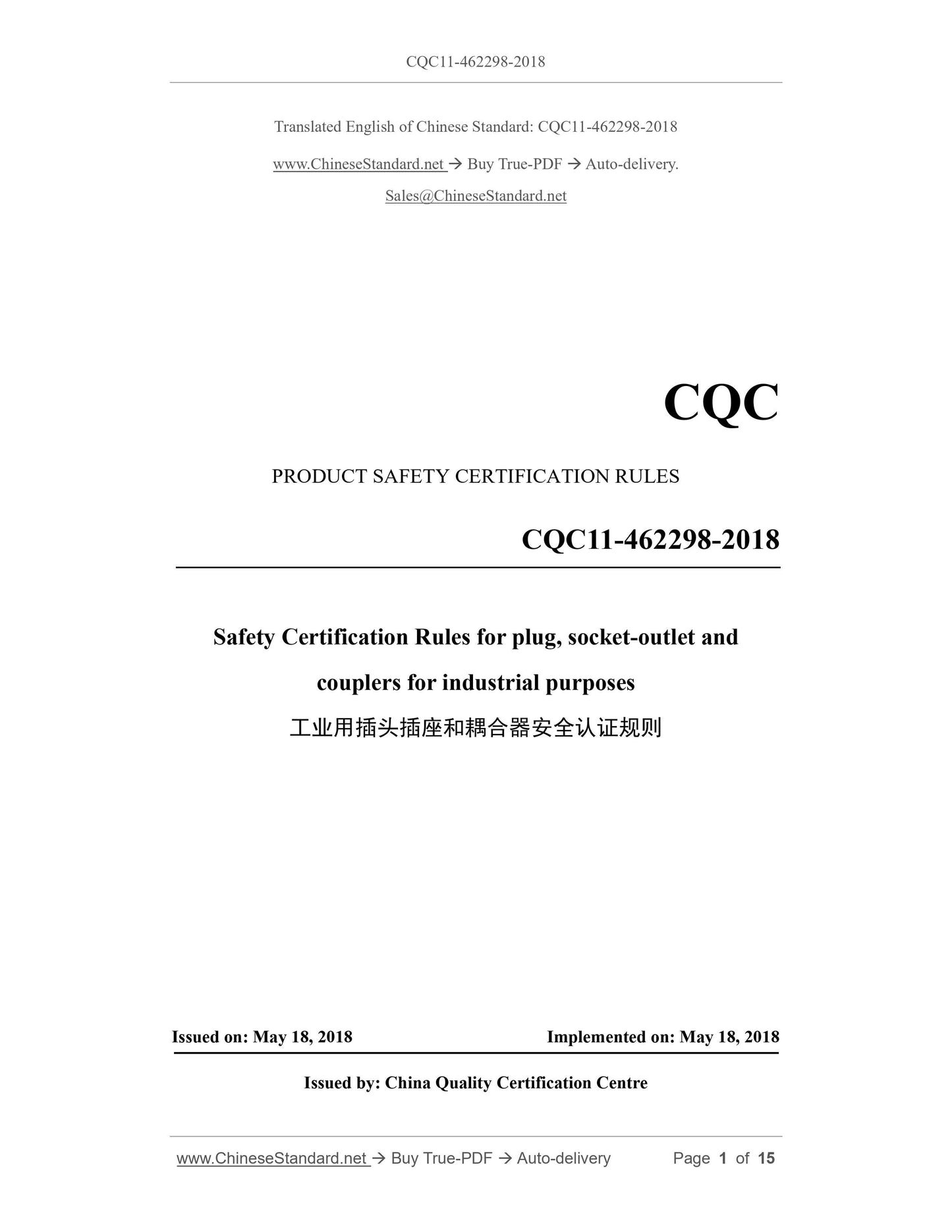
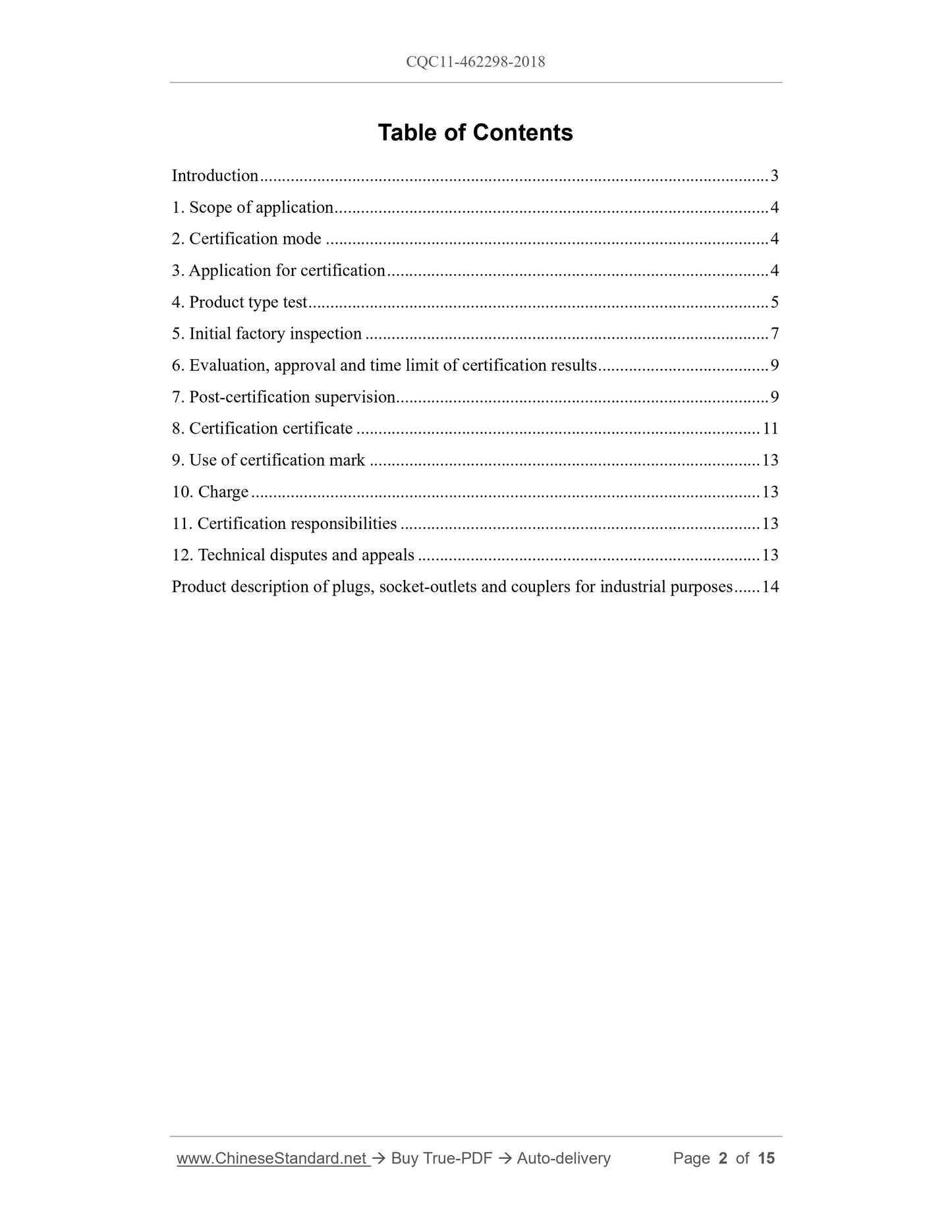
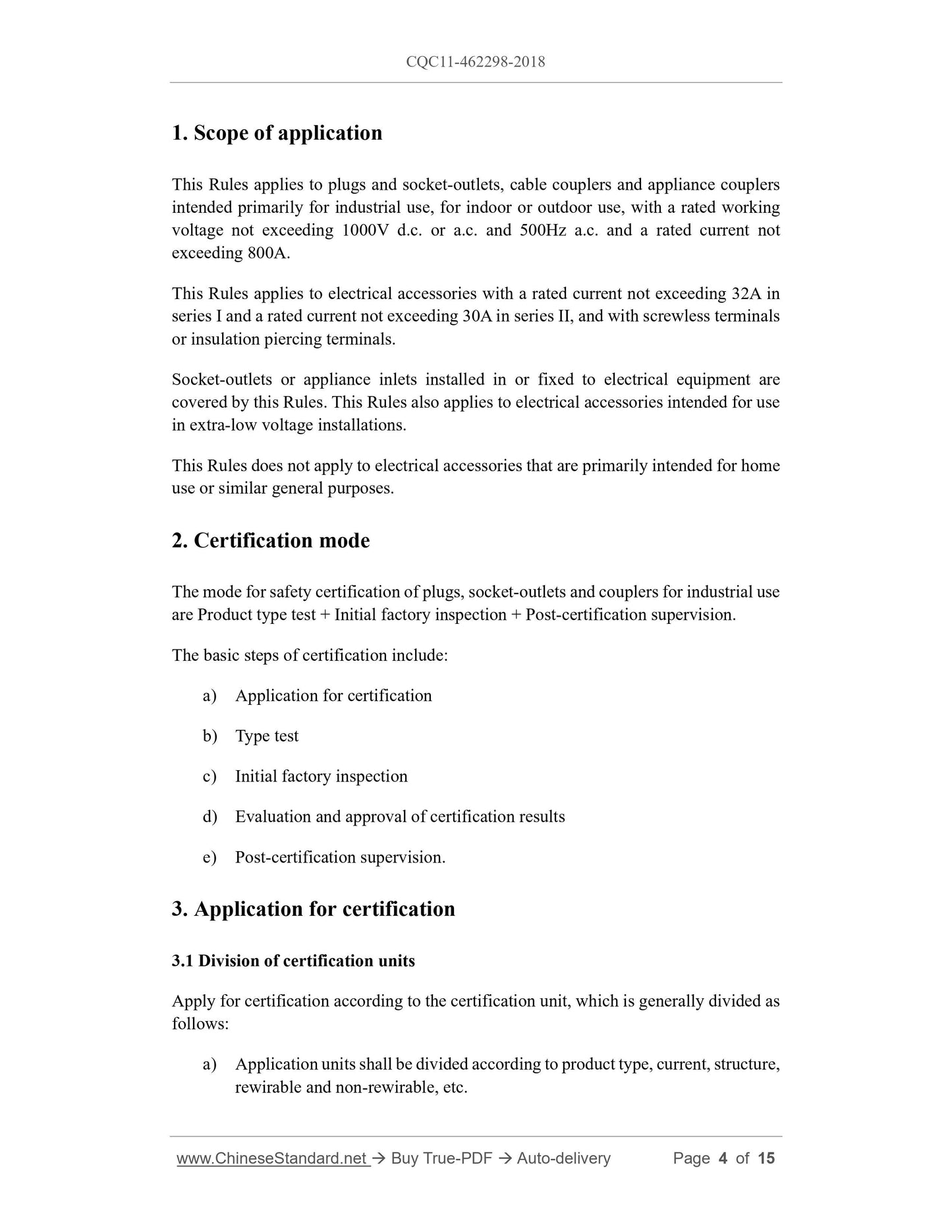
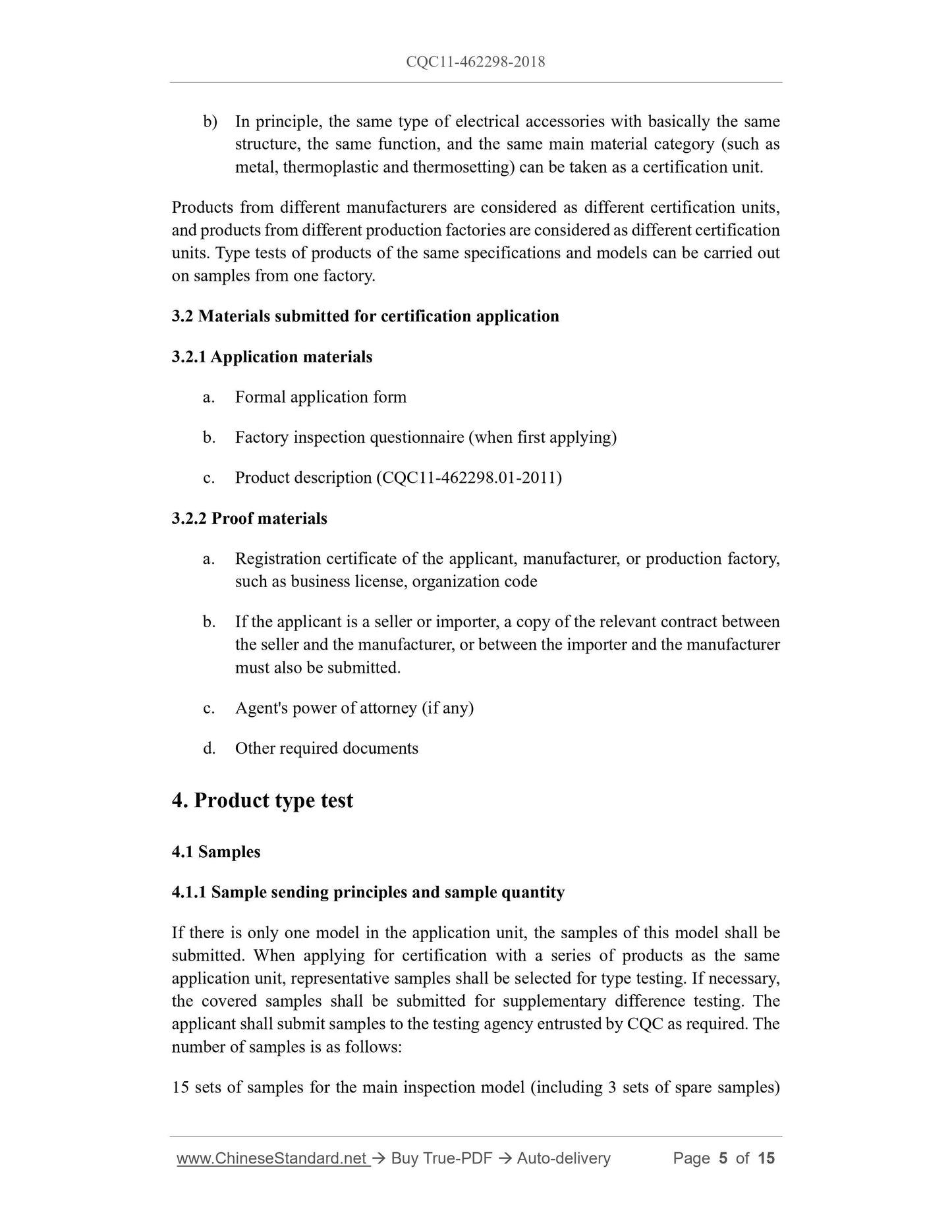
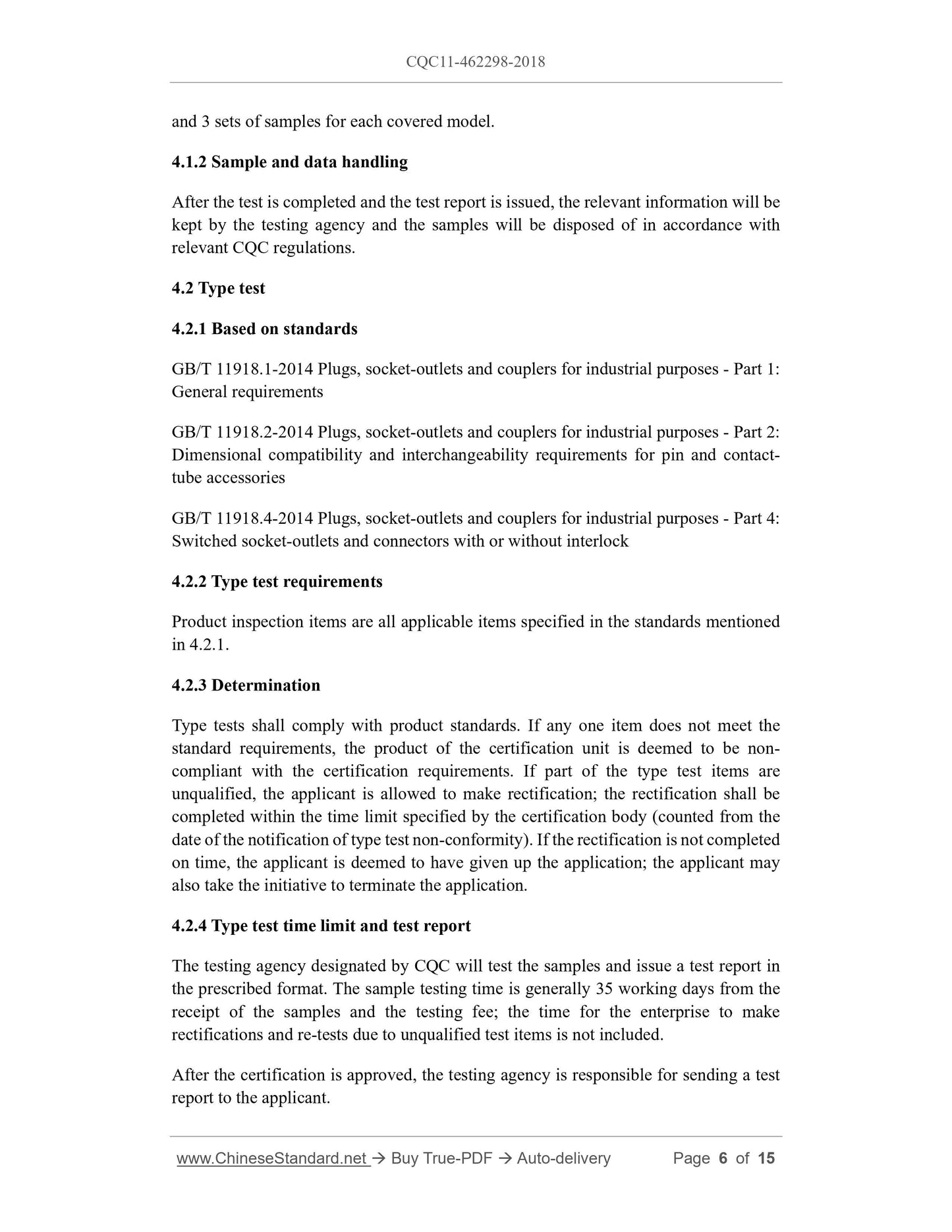
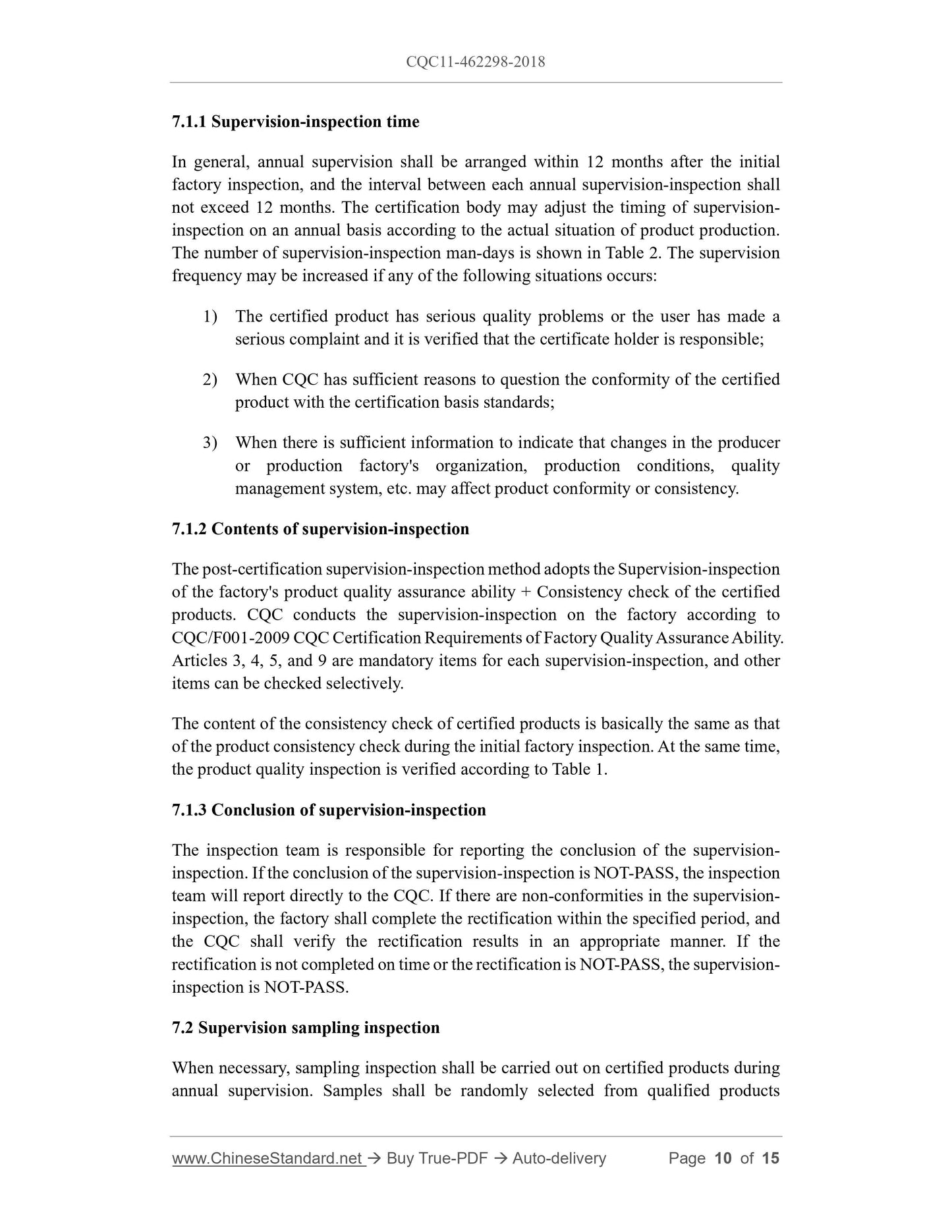
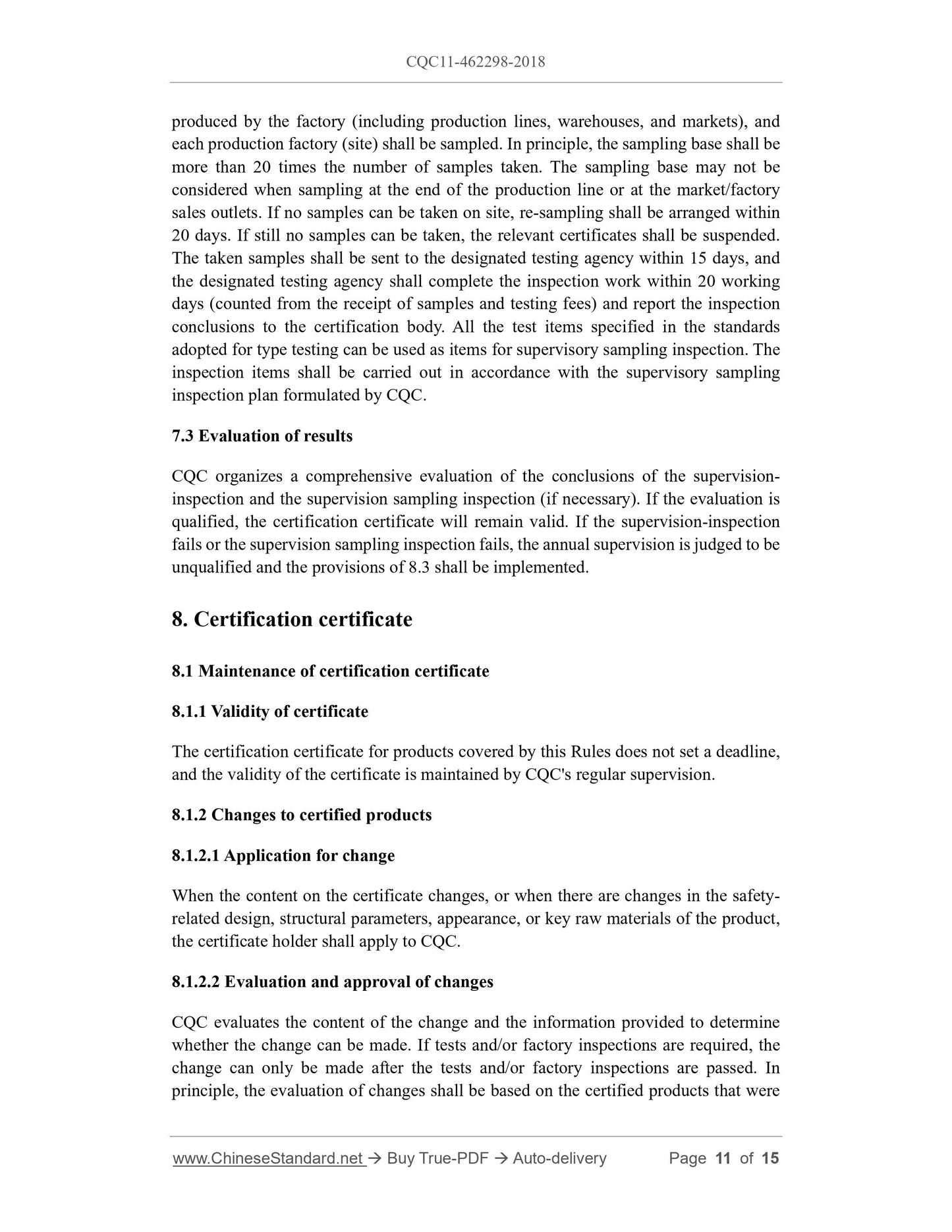
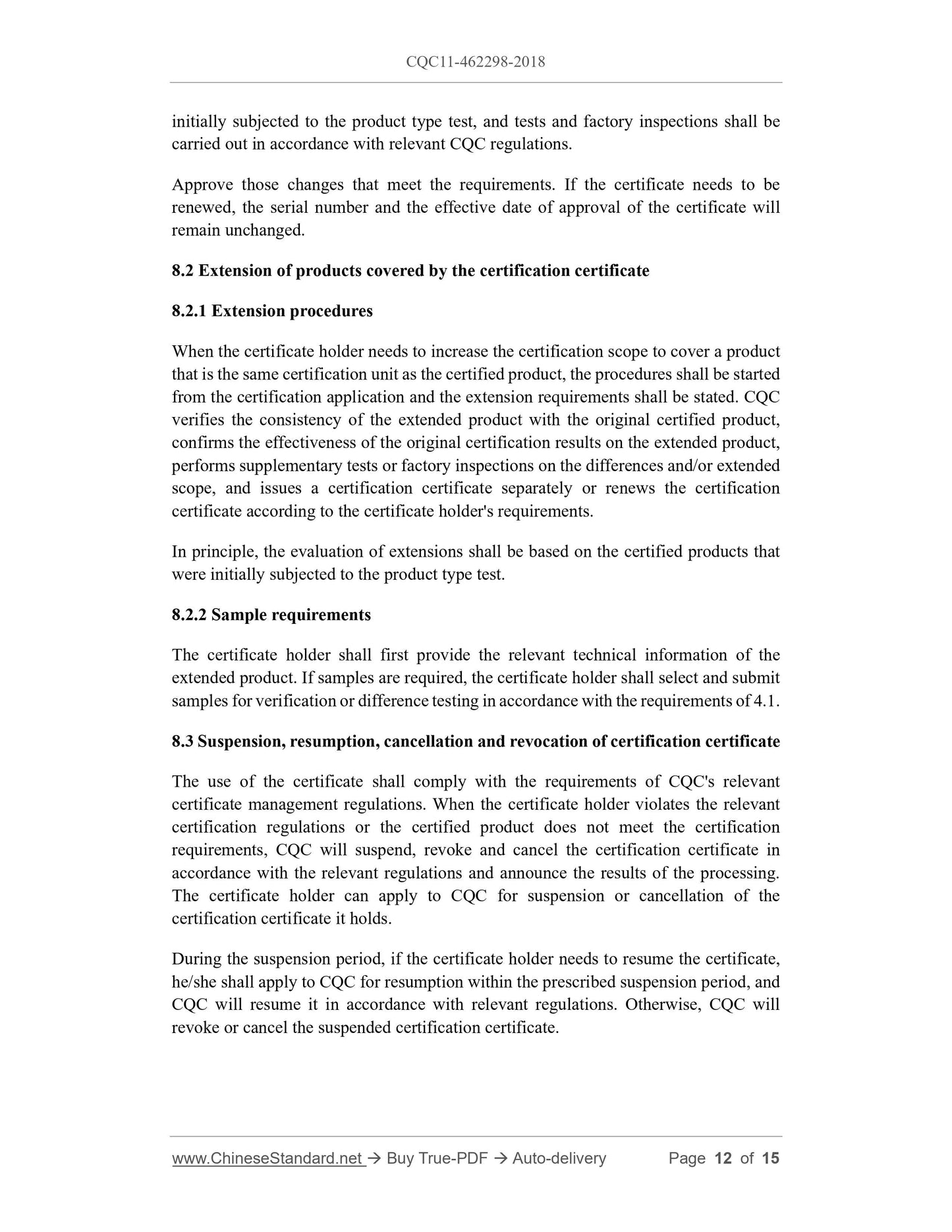