1
/
of
7
PayPal, credit cards. Download editable-PDF and invoice in 1 second!
GB 11291.1-2011 English PDF (GB11291.1-2011)
GB 11291.1-2011 English PDF (GB11291.1-2011)
Regular price
$175.00 USD
Regular price
Sale price
$175.00 USD
Unit price
/
per
Shipping calculated at checkout.
Couldn't load pickup availability
Delivery: 3 seconds. Download true-PDF + Invoice.
Get QUOTATION in 1-minute: Click GB 11291.1-2011
Historical versions: GB 11291.1-2011
Preview True-PDF (Reload/Scroll if blank)
GB 11291.1-2011: Robots for industrial environments -- Safety requirements -- Part 1: Robot
GB 11291.1-2011
Robots for industrial environments.Safety requirements.Part 1. Robot
ICS 25.040.30
J28
National Standards of People's Republic of China
Replacing GB 11291-1997
Robots for industrial environments - Safety requirements
Part 1. Robots
Part 1. Robot
(ISO 10218-1.2006, ISO 10218-1/Cor.1.2007, IDT)
Issued on. 2011-05-12
2011-10-01 implementation
Administration of Quality Supervision, Inspection and Quarantine of People's Republic of China
Standardization Administration of China released
Table of Contents
Preface Ⅰ
Introduction Ⅱ
1 Scope 1
2 Normative references 1
3 Terms and definitions
Hazard identification and risk assessment 4 5
5 design requirements and protection measures 6
6 15 use the information
Appendix A (normative) lists 17 major risk
Appendix B (normative) Stop time/distance metric 19
Annex C (informative) 3-position enabling device features 20
Annex D (informative) Optional Features 21
Methods Appendix E (normative) mode of operation mark 22
References 23
Foreword
All technical content in this section is mandatory.
GB 11291 "Robots for industrial environments - Safety requirements" is divided into the following sections.
--- Part 1. Robot;
--- Part 2. Robot systems and integration.
This is Part 1 GB 11291's.
This section drafted in accordance with GB/T 1.1-2009 given rules.
This Part replaces GB 11291-1997 "industrial robot safety norms."
This section of the main changes compared to GB 11291-1997 are as follows.
--- This section updated some files to make them more in line with GB/T 15706-2007 and comply with the requirements of the use of Class C standard check
Testing requirements and corresponding hazards.
--- This section increased (but not limited to) new technical requirements, including those related to security control system performance, the robot stop work
You can enable the device, program verification, wireless teach pendant guidelines, joint control, collaborative robots guidelines, and the latest design safety
specification.
This section identical with the international standard ISO 10218-1.2006 "Safety requirements for industrial environments - Part 1 robot. robot"
(English version) and ISO 10218-1/Cor.1.2007 (revised English edition).
For ease of use, this part of the editorial changes as follows.
--- Uppercase acronym in English formerly reserved to remove ISO foreword;
--- ISO 10218 will be changed to "GB 11291" and "" Robots for industrial environments - Safety requirements '; will the "international standards" and
ISO 10218-1 words "this section" and "GB 11291.1";
--- The Normative documents have been translated into national standards with international standards Renumber national standard number, and the corresponding national
International standards adopted standard version number placed in parentheses after the number of national standards, ease of use and access; unconverted international standards
Approved leave;
--- Deletion of the original text does not meet the standard of written words.
Correspondence between the consistency of the standards of international documents and normative references of the following documents.
--- GB/T 12642-2001 industrial robot performance specifications and test methods (eqvISO 9283.1998);
--- GB 16754-2008 Safety of machinery - Emergency stop design principles (ISO 13850.2006, IDT);
--- GB/T 19876-2005 Safety of machinery and parts of the body close to the speed of the positioning of protective equipment (ISO 13855.
2002, MOD).
This part is proposed by China Machinery Industry Federation.
This part of the automation systems and integration by the National Standardization Technical Committee (SAC/TC159) centralized.
This section is drafted. Beijing Machinery Industry Automation, Beijing University of Aeronautics and Astronautics.
The main drafters of this section. Young book reviews, Yun Chao, Wang Sisi.
This part of the standard replaces the previous editions are.
--- GB 11291-1997.
introduction
GB 11291 is based on the recognition of industrial robots and industrial robot systems can lead to specific risks basis.
GB 11291 is GB/T 15706.1-2007 standard Class C said.
Note the machine, the level of risk, hazard and incident involved have been described in the context of GB 11291.
Class C and Class A standard Class B standard or standards are different. For Class C in accordance with the standard design and manufacture of machinery, Class C standard terms
Precedence over other standard terms.
Related dangerous robot has been widely recognized. However, the use of different sources of danger robot system is often different, so the type of risk
The automation process is directly related to the number and complexity of the robot installation. Depending on the type of robot use, purpose of use of the robot,
Risks associated with the robot installation, programming, operation and maintenance of different ways, leading to the danger of these are different.
Note 1. Not all danger described in GB 11291 are applicable to each robot. Similarly, the level of risk of a particular dangerous situations in different machine
It is the world may differ. Thus, the provisions in GB 11291 safety requirements and/or protective measures for different robots may vary
With, then it can carry out a risk assessment to determine what protective measures.
In recognition of industrial robots for different purposes have different hazardous properties, GB 11291 is divided into two parts; Part 1 provides
Security assurances guidance recommends that when designing and manufacturing the robot. Since the industrial robot application security by a particular robotic system integration
Influence in the design and application, Part 2 will provide the robot integration, installation, functional testing, programming, operation, maintenance and repair of the people engaged in
Members of security guidelines.
Note 2. Since the industrial environment, noise is generally considered to be a hazard, in line with the provisions of 3.18 robot can not be considered the final product. The accord
3.20 robot system is defined taking into account noise hazard machine. Thus, in Section 2 GB 11291 of the regulations at the noise hazard
Management measures.
Robots for industrial environments - Safety requirements
Part 1. Robots
1 Scope
GB 11291 of the provisions of this part of the industrial robot (defined in Chapter 3) of the basic security design, protection measures and the use of information
The requirements and guidelines. Describe industrial robots basic hazard related, and proposes to eliminate or substantially reduce the risk of these requirements.
Noise as a potential hazard in this section do not relate, but are included in Section 2 GB 11291's.
GB 11291 This part is suitable for industrial robots. Although the "Robots for industrial environments - Safety requirements" established safety principles can
Other types of robots can be used, but this does not apply to non-industrial robots. Examples of non-industrial robot including (but not limited to
In). Underwater, military and space robots, robot remote control assistive devices, prosthetics and other physically handicapped persons, micro-robots (displacement range
Wai < 1mm), surgery or rehabilitation robots, and service and consumer robots.
Note 1. The industrial robot system integration and installation requirements are contained in Part 2.
Note 2. The special applications (welding, laser cutting, machining, etc.) may produce additional hazards in these dangerous design of the robot may need to be c...
Get QUOTATION in 1-minute: Click GB 11291.1-2011
Historical versions: GB 11291.1-2011
Preview True-PDF (Reload/Scroll if blank)
GB 11291.1-2011: Robots for industrial environments -- Safety requirements -- Part 1: Robot
GB 11291.1-2011
Robots for industrial environments.Safety requirements.Part 1. Robot
ICS 25.040.30
J28
National Standards of People's Republic of China
Replacing GB 11291-1997
Robots for industrial environments - Safety requirements
Part 1. Robots
Part 1. Robot
(ISO 10218-1.2006, ISO 10218-1/Cor.1.2007, IDT)
Issued on. 2011-05-12
2011-10-01 implementation
Administration of Quality Supervision, Inspection and Quarantine of People's Republic of China
Standardization Administration of China released
Table of Contents
Preface Ⅰ
Introduction Ⅱ
1 Scope 1
2 Normative references 1
3 Terms and definitions
Hazard identification and risk assessment 4 5
5 design requirements and protection measures 6
6 15 use the information
Appendix A (normative) lists 17 major risk
Appendix B (normative) Stop time/distance metric 19
Annex C (informative) 3-position enabling device features 20
Annex D (informative) Optional Features 21
Methods Appendix E (normative) mode of operation mark 22
References 23
Foreword
All technical content in this section is mandatory.
GB 11291 "Robots for industrial environments - Safety requirements" is divided into the following sections.
--- Part 1. Robot;
--- Part 2. Robot systems and integration.
This is Part 1 GB 11291's.
This section drafted in accordance with GB/T 1.1-2009 given rules.
This Part replaces GB 11291-1997 "industrial robot safety norms."
This section of the main changes compared to GB 11291-1997 are as follows.
--- This section updated some files to make them more in line with GB/T 15706-2007 and comply with the requirements of the use of Class C standard check
Testing requirements and corresponding hazards.
--- This section increased (but not limited to) new technical requirements, including those related to security control system performance, the robot stop work
You can enable the device, program verification, wireless teach pendant guidelines, joint control, collaborative robots guidelines, and the latest design safety
specification.
This section identical with the international standard ISO 10218-1.2006 "Safety requirements for industrial environments - Part 1 robot. robot"
(English version) and ISO 10218-1/Cor.1.2007 (revised English edition).
For ease of use, this part of the editorial changes as follows.
--- Uppercase acronym in English formerly reserved to remove ISO foreword;
--- ISO 10218 will be changed to "GB 11291" and "" Robots for industrial environments - Safety requirements '; will the "international standards" and
ISO 10218-1 words "this section" and "GB 11291.1";
--- The Normative documents have been translated into national standards with international standards Renumber national standard number, and the corresponding national
International standards adopted standard version number placed in parentheses after the number of national standards, ease of use and access; unconverted international standards
Approved leave;
--- Deletion of the original text does not meet the standard of written words.
Correspondence between the consistency of the standards of international documents and normative references of the following documents.
--- GB/T 12642-2001 industrial robot performance specifications and test methods (eqvISO 9283.1998);
--- GB 16754-2008 Safety of machinery - Emergency stop design principles (ISO 13850.2006, IDT);
--- GB/T 19876-2005 Safety of machinery and parts of the body close to the speed of the positioning of protective equipment (ISO 13855.
2002, MOD).
This part is proposed by China Machinery Industry Federation.
This part of the automation systems and integration by the National Standardization Technical Committee (SAC/TC159) centralized.
This section is drafted. Beijing Machinery Industry Automation, Beijing University of Aeronautics and Astronautics.
The main drafters of this section. Young book reviews, Yun Chao, Wang Sisi.
This part of the standard replaces the previous editions are.
--- GB 11291-1997.
introduction
GB 11291 is based on the recognition of industrial robots and industrial robot systems can lead to specific risks basis.
GB 11291 is GB/T 15706.1-2007 standard Class C said.
Note the machine, the level of risk, hazard and incident involved have been described in the context of GB 11291.
Class C and Class A standard Class B standard or standards are different. For Class C in accordance with the standard design and manufacture of machinery, Class C standard terms
Precedence over other standard terms.
Related dangerous robot has been widely recognized. However, the use of different sources of danger robot system is often different, so the type of risk
The automation process is directly related to the number and complexity of the robot installation. Depending on the type of robot use, purpose of use of the robot,
Risks associated with the robot installation, programming, operation and maintenance of different ways, leading to the danger of these are different.
Note 1. Not all danger described in GB 11291 are applicable to each robot. Similarly, the level of risk of a particular dangerous situations in different machine
It is the world may differ. Thus, the provisions in GB 11291 safety requirements and/or protective measures for different robots may vary
With, then it can carry out a risk assessment to determine what protective measures.
In recognition of industrial robots for different purposes have different hazardous properties, GB 11291 is divided into two parts; Part 1 provides
Security assurances guidance recommends that when designing and manufacturing the robot. Since the industrial robot application security by a particular robotic system integration
Influence in the design and application, Part 2 will provide the robot integration, installation, functional testing, programming, operation, maintenance and repair of the people engaged in
Members of security guidelines.
Note 2. Since the industrial environment, noise is generally considered to be a hazard, in line with the provisions of 3.18 robot can not be considered the final product. The accord
3.20 robot system is defined taking into account noise hazard machine. Thus, in Section 2 GB 11291 of the regulations at the noise hazard
Management measures.
Robots for industrial environments - Safety requirements
Part 1. Robots
1 Scope
GB 11291 of the provisions of this part of the industrial robot (defined in Chapter 3) of the basic security design, protection measures and the use of information
The requirements and guidelines. Describe industrial robots basic hazard related, and proposes to eliminate or substantially reduce the risk of these requirements.
Noise as a potential hazard in this section do not relate, but are included in Section 2 GB 11291's.
GB 11291 This part is suitable for industrial robots. Although the "Robots for industrial environments - Safety requirements" established safety principles can
Other types of robots can be used, but this does not apply to non-industrial robots. Examples of non-industrial robot including (but not limited to
In). Underwater, military and space robots, robot remote control assistive devices, prosthetics and other physically handicapped persons, micro-robots (displacement range
Wai < 1mm), surgery or rehabilitation robots, and service and consumer robots.
Note 1. The industrial robot system integration and installation requirements are contained in Part 2.
Note 2. The special applications (welding, laser cutting, machining, etc.) may produce additional hazards in these dangerous design of the robot may need to be c...
Share
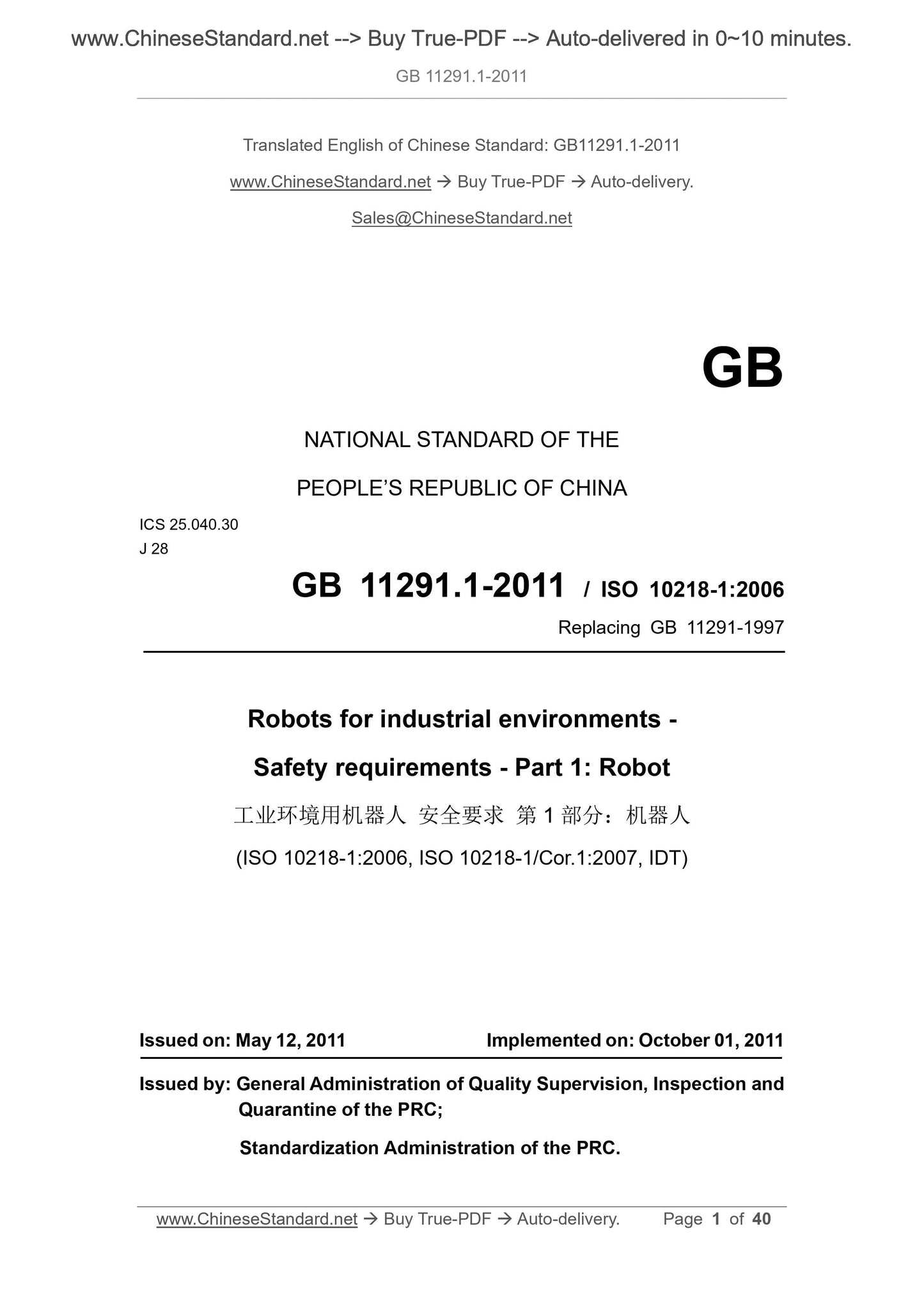

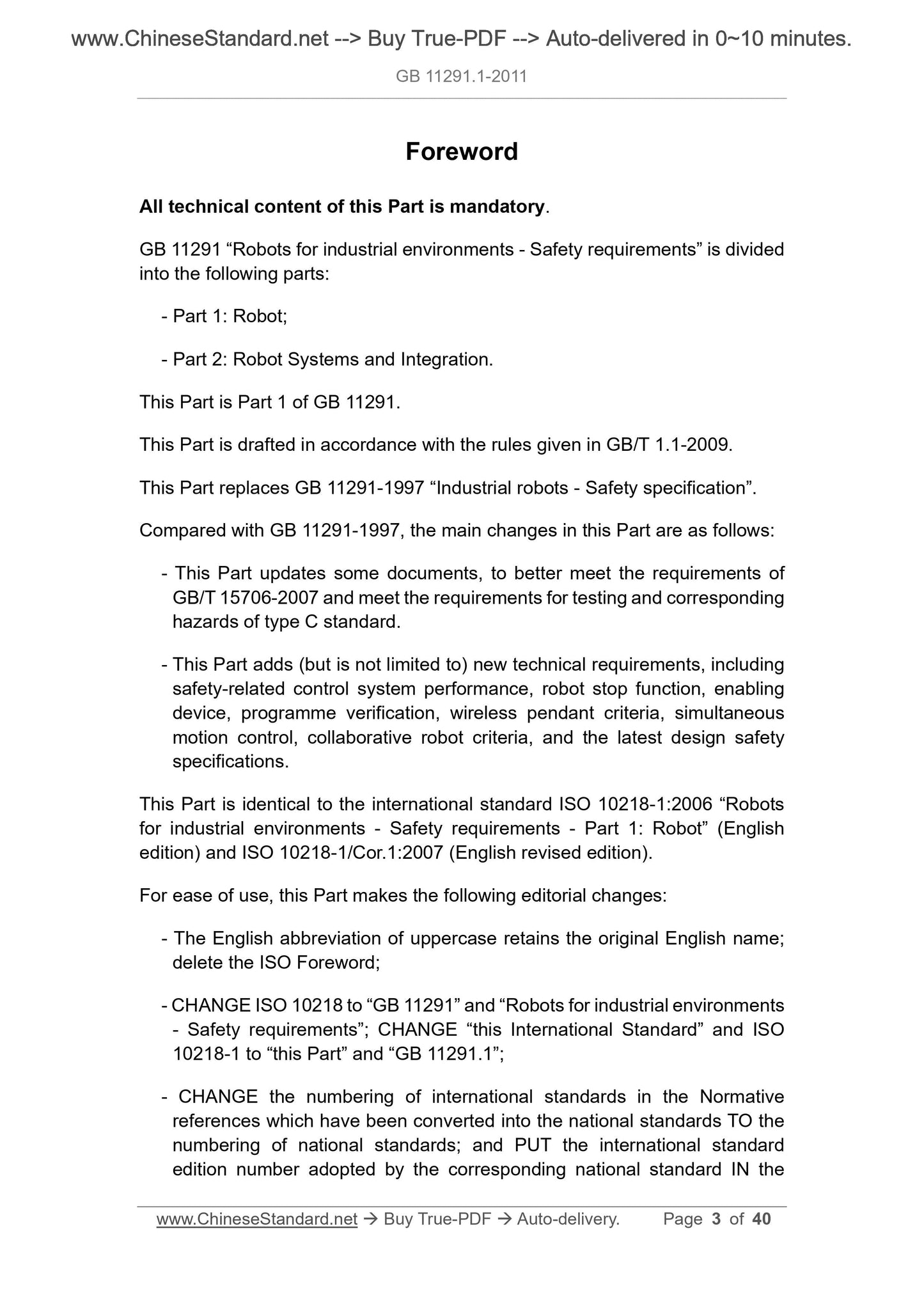

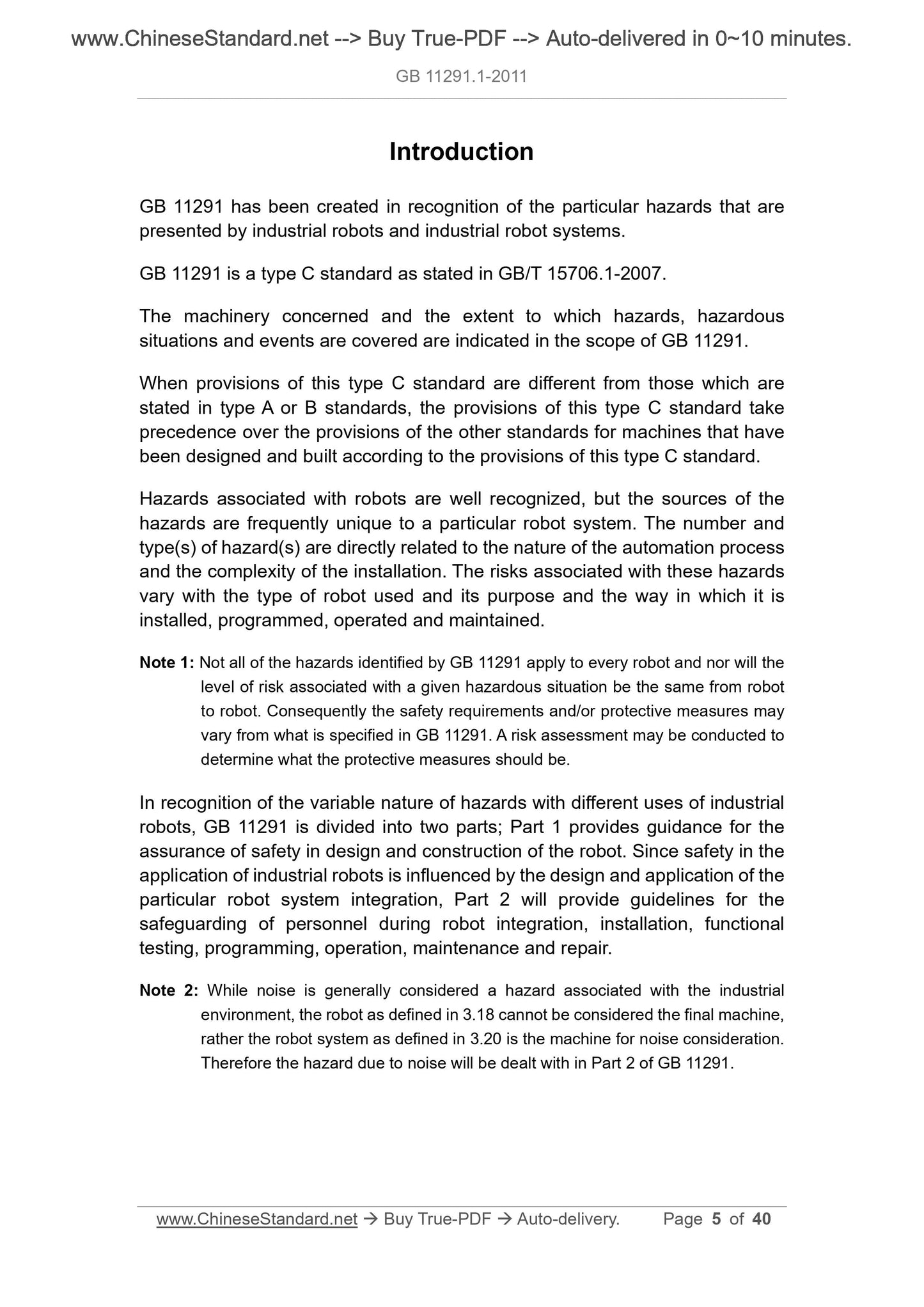
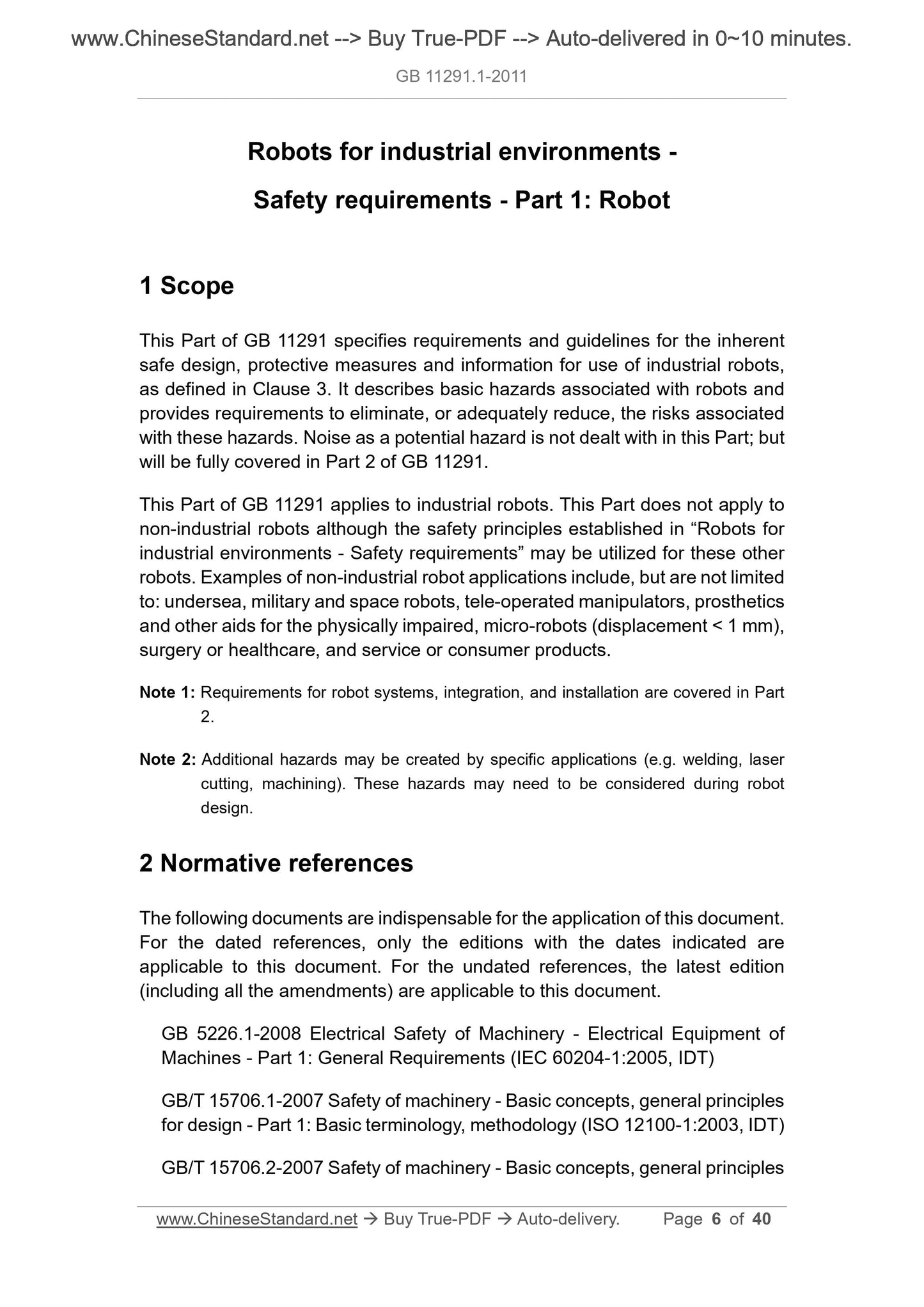
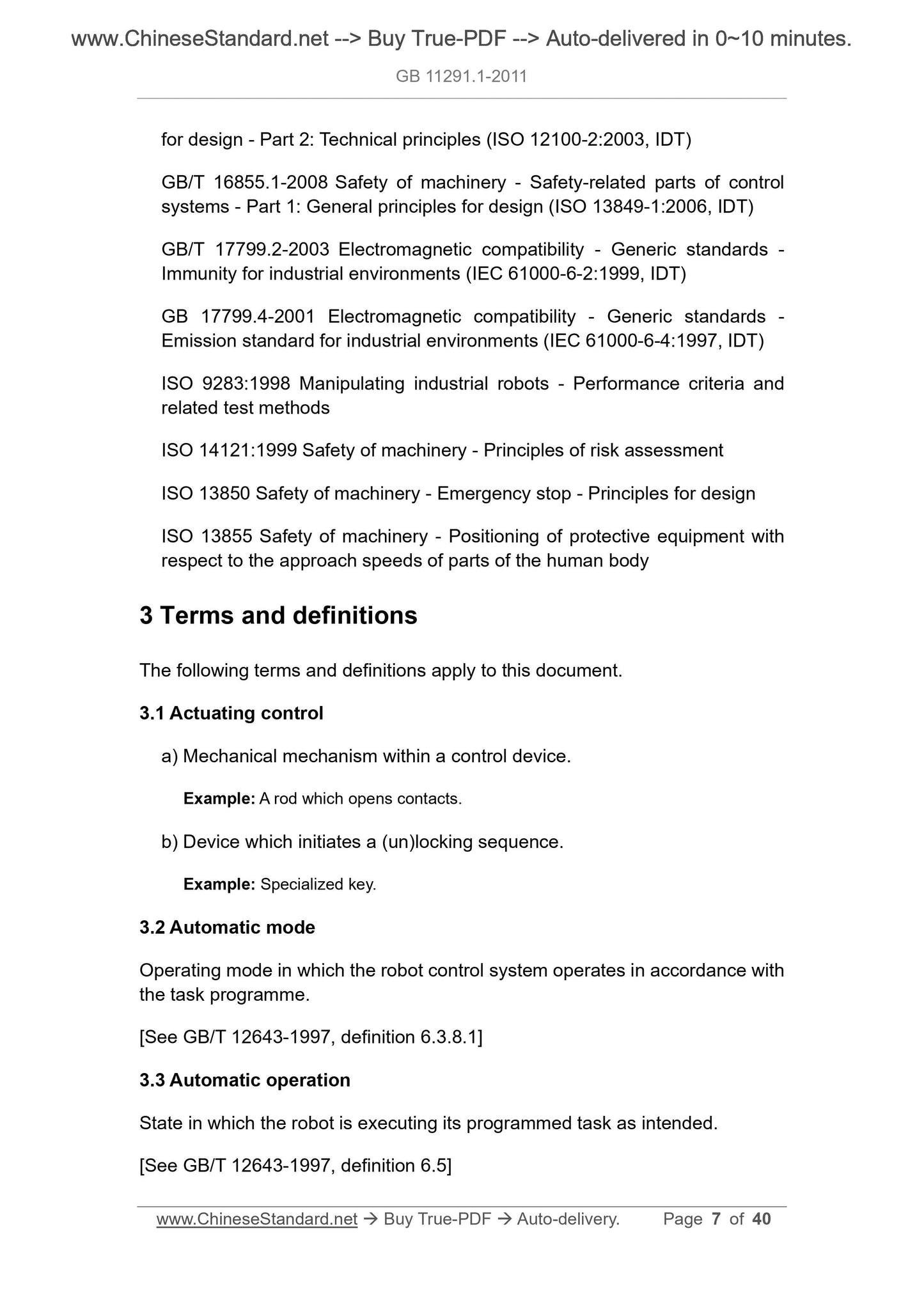