1
/
of
12
PayPal, credit cards. Download editable-PDF and invoice in 1 second!
GB 21009-2007 English PDF
GB 21009-2007 English PDF
Regular price
$245.00 USD
Regular price
Sale price
$245.00 USD
Unit price
/
per
Shipping calculated at checkout.
Couldn't load pickup availability
Delivery: 3 seconds. Download true-PDF + Invoice.
Get QUOTATION in 1-minute: Click GB 21009-2007
Historical versions: GB 21009-2007
Preview True-PDF (Reload/Scroll if blank)
GB 21009-2007: Mine blast-hole drills -- Safety requirements
GB 21009-2007
GB
NATIONAL STANDARD OF THE
PEOPLE’S REPUBLIC OF CHINA
ICS 73.100.30
D 92
Mine Blast-Hole Drills – Safety Requirements
ISSUED ON: JULY 19, 2007
IMPLEMENTED ON: JANUARY 1, 2008
Issued by: General Administration of Quality Supervision, Inspection and
Quarantine;
Standardization Administration of the People’s Republic of China.
Table of Contents
Foreword ... 3
1 Scope ... 4
2 Normative References ... 4
3 Terms and Definitions ... 6
4 List of Dangers ... 7
5 Safety Requirements and/or Measures and Judgments ... 8
6 Usage Information ... 18
Mine Blast-Hole Drills – Safety Requirements
1 Scope
This Standard is a restriction on mining blast-hole drills in terms of physical performance and
intended use. The safety requirements specified in this Standard apply to the dangers generated
at all stages of the machine's life cycle.
This Standard applies to rock drills, wire rope impact drills, down-the-hole drills, rotary drills
and rotary drilling rig (hereinafter referred to as drills) used for drilling blast-holes in open-pit
and underground mines and tunnels.
2 Normative References
The provisions in following documents become the provisions of this Standard through
reference in this Standard. For dated references, the subsequent amendments (excluding
corrigendum) or revisions do not apply to this Standard, however, parties who reach an
agreement based on this Standard are encouraged to study if the latest versions of these
documents are applicable. For undated references, the latest edition of the referenced document
applies.
GB 2894 Safety signs (GB 2894-1996, neq ISO 3864)
GB/T 3766 Hydraulic Fluid Power - General Rules Relating to Systems (GB/T 3766-2001,
eqv ISO 4413:1998)
GB 3836.1 Electrical apparatus for explosive gas atmospheres - Part 1: General
requirements (GB 3836.1-2000, eqv IEC 60079-0:1998)
GB 3836.2 Electrical apparatus for explosive gas atmospheres - Part 2: Flameproof
enclosure “d” (GB 3836.2-2000, eqv IEC 60079-1:1990)
GB 3836.3 Electrical apparatus for explosive gas atmospheres - Part 3: Increased safety
“e” (GB 3836.3-2000, eqv IEC 60079-7:1990)
GB 3836.4 Electrical apparatus for explosive gas atmospheres - Part 4: Intrinsic safety “i”
(GB 3836.4-2000, eqv IEC 60079-11:1999)
GB 3836.5 Electrical apparatus for explosive gas atmosphere - Part 5: Pressurized
enclosures “p” (GB 3836.5-2004, IEC 60079-2:2001, MOD)
reconnection will endanger people around, they shall be able to lock.
After the drill cuts off the energy, it shall be able to safely release the energy left or stored in
the circuit so that people around it are not in danger. Some circuits can remain connected to the
energy in order to clamp workpieces, save information, and internal lighting. In this case,
special measures shall be taken to protect the safety of the operator.
5.2 Safety requirements for operating positions
5.2.1 The operation of the drill shall be carried out in a state where the surrounding environment
is not dangerous to personnel. The position and standing space required by the operator shall
meet the requirements of GB/T 8420 and JB/T 3683.
5.2.2 For drill used for underground or tunnel operations, protective measures shall be taken as
needed to prevent the danger caused by splashing objects.
5.2.3 The driving and operating positions of the drill shall have good visibility to ensure that
there is no danger to personnel.
5.2.4 The drill can be equipped with an operator's cab as needed. The operator's cab shall meet
the following requirements:
a) The operator's cab shall be equipped with air conditioning or safe heating and cooling
devices according to the working conditions to ensure that the temperature in the
operator's cab is within the range of 15℃~31℃;
b) An air purification device shall be equipped; and the dust concentration in the air in the
operator's cab shall meet the requirements of 5.13.1 in this Standard;
c) When the drill is operating with the doors and windows closed and the air conditioning
and purification devices turned on, the noise in the operator's cab shall not exceed 85dB
(A), and the noise shall be tested in accordance with the provisions of GB/T 13325;
d) Necessary vibration reduction measures shall be taken, and the weighted root mean square
acceleration correction value at the seat cushion shall not exceed 1.25m/s2. The vibration
test shall be carried out in accordance with the method of GB/T 8419;
e) The direction of the door opening shall enable the operator to quickly leave the operator's
cab in case of danger;
f) The decorative materials in the operator's cab shall meet the fire protection requirements
of 5.12.1 in this Standard;
g) The illumination in the operator's cab shall meet the requirements of 5.11.3 in this
Standard;
h) The glass between the operator's cab and the machine room shall be vibration-resistant
and shall not injure the operator after breaking.
5.3 Control system
5.3.1 The safety part of the drill control system shall meet the requirements of GB/T 16855.1.
5.3.2 The main transmission system of the drill shall be manually started through the starting
device. If the drill has multiple devices for starting, these devices shall be linked to each other
so that one of them can be used to complete the start.
For pneumatically driven drill, a shut-off valve shall be set on the main circuit to connect or
disconnect the power unit and the main machine, and to release the system pressure.
5.3.3 The drill shall have a normal shutdown command device to enable it to stop safely during
operation. The drill shall be equipped with a total stop switch; and each operating position for
operation and driving shall have an emergency stop device to prevent dangers caused by
emergencies.
5.3.4 The interruption of power supply or the re-supply after interruption shall not lead to the
occurrence of danger and shall meet the following requirements:
a) The drill can only be restarted by human command;
b) If the shutdown command has been issued, the drill must be shut down;
c) Equipment parts or tools are not allowed to fall or pop out;
d) Protective devices and protective measures shall be ensured effective.
Power supply failure or hydraulic and pneumatic pressure deviation from the set value is not
allowed to cause dangerous actions and emergency shutdown system failure.
5.3.5 Failure of the control circuit or logical failure of the control circuit is not allowed to cause
danger.
5.4 Control device
5.4.1 The operation of the control device shall be safe, flexible and comfortable; and its design
configuration and marking shall meet the requirements of GB/T 15706.2.
The main control device shall be arranged in the comfortable area of operation, and the auxiliary
control device can be arranged in the reach of operation or other positions outside the danger
zone.
If the drill has multiple operating positions, a selection switch shall be configured so that the
operator can purposefully select a favorable operating position.
5.4.2 The drill shall have corresponding emergency stop and safety devices; and the emergency
5.6.5 When the drill is operating, traveling and stopping on a slope exceeding the maximum
allowable slope, a traction winch shall be equipped to prevent the drill from slipping on the
slope.
5.7 Protection of moving parts
5.7.1 The design, manufacture and installation of the moving parts of the drill shall avoid the
dangers described in GB/T ...
Get QUOTATION in 1-minute: Click GB 21009-2007
Historical versions: GB 21009-2007
Preview True-PDF (Reload/Scroll if blank)
GB 21009-2007: Mine blast-hole drills -- Safety requirements
GB 21009-2007
GB
NATIONAL STANDARD OF THE
PEOPLE’S REPUBLIC OF CHINA
ICS 73.100.30
D 92
Mine Blast-Hole Drills – Safety Requirements
ISSUED ON: JULY 19, 2007
IMPLEMENTED ON: JANUARY 1, 2008
Issued by: General Administration of Quality Supervision, Inspection and
Quarantine;
Standardization Administration of the People’s Republic of China.
Table of Contents
Foreword ... 3
1 Scope ... 4
2 Normative References ... 4
3 Terms and Definitions ... 6
4 List of Dangers ... 7
5 Safety Requirements and/or Measures and Judgments ... 8
6 Usage Information ... 18
Mine Blast-Hole Drills – Safety Requirements
1 Scope
This Standard is a restriction on mining blast-hole drills in terms of physical performance and
intended use. The safety requirements specified in this Standard apply to the dangers generated
at all stages of the machine's life cycle.
This Standard applies to rock drills, wire rope impact drills, down-the-hole drills, rotary drills
and rotary drilling rig (hereinafter referred to as drills) used for drilling blast-holes in open-pit
and underground mines and tunnels.
2 Normative References
The provisions in following documents become the provisions of this Standard through
reference in this Standard. For dated references, the subsequent amendments (excluding
corrigendum) or revisions do not apply to this Standard, however, parties who reach an
agreement based on this Standard are encouraged to study if the latest versions of these
documents are applicable. For undated references, the latest edition of the referenced document
applies.
GB 2894 Safety signs (GB 2894-1996, neq ISO 3864)
GB/T 3766 Hydraulic Fluid Power - General Rules Relating to Systems (GB/T 3766-2001,
eqv ISO 4413:1998)
GB 3836.1 Electrical apparatus for explosive gas atmospheres - Part 1: General
requirements (GB 3836.1-2000, eqv IEC 60079-0:1998)
GB 3836.2 Electrical apparatus for explosive gas atmospheres - Part 2: Flameproof
enclosure “d” (GB 3836.2-2000, eqv IEC 60079-1:1990)
GB 3836.3 Electrical apparatus for explosive gas atmospheres - Part 3: Increased safety
“e” (GB 3836.3-2000, eqv IEC 60079-7:1990)
GB 3836.4 Electrical apparatus for explosive gas atmospheres - Part 4: Intrinsic safety “i”
(GB 3836.4-2000, eqv IEC 60079-11:1999)
GB 3836.5 Electrical apparatus for explosive gas atmosphere - Part 5: Pressurized
enclosures “p” (GB 3836.5-2004, IEC 60079-2:2001, MOD)
reconnection will endanger people around, they shall be able to lock.
After the drill cuts off the energy, it shall be able to safely release the energy left or stored in
the circuit so that people around it are not in danger. Some circuits can remain connected to the
energy in order to clamp workpieces, save information, and internal lighting. In this case,
special measures shall be taken to protect the safety of the operator.
5.2 Safety requirements for operating positions
5.2.1 The operation of the drill shall be carried out in a state where the surrounding environment
is not dangerous to personnel. The position and standing space required by the operator shall
meet the requirements of GB/T 8420 and JB/T 3683.
5.2.2 For drill used for underground or tunnel operations, protective measures shall be taken as
needed to prevent the danger caused by splashing objects.
5.2.3 The driving and operating positions of the drill shall have good visibility to ensure that
there is no danger to personnel.
5.2.4 The drill can be equipped with an operator's cab as needed. The operator's cab shall meet
the following requirements:
a) The operator's cab shall be equipped with air conditioning or safe heating and cooling
devices according to the working conditions to ensure that the temperature in the
operator's cab is within the range of 15℃~31℃;
b) An air purification device shall be equipped; and the dust concentration in the air in the
operator's cab shall meet the requirements of 5.13.1 in this Standard;
c) When the drill is operating with the doors and windows closed and the air conditioning
and purification devices turned on, the noise in the operator's cab shall not exceed 85dB
(A), and the noise shall be tested in accordance with the provisions of GB/T 13325;
d) Necessary vibration reduction measures shall be taken, and the weighted root mean square
acceleration correction value at the seat cushion shall not exceed 1.25m/s2. The vibration
test shall be carried out in accordance with the method of GB/T 8419;
e) The direction of the door opening shall enable the operator to quickly leave the operator's
cab in case of danger;
f) The decorative materials in the operator's cab shall meet the fire protection requirements
of 5.12.1 in this Standard;
g) The illumination in the operator's cab shall meet the requirements of 5.11.3 in this
Standard;
h) The glass between the operator's cab and the machine room shall be vibration-resistant
and shall not injure the operator after breaking.
5.3 Control system
5.3.1 The safety part of the drill control system shall meet the requirements of GB/T 16855.1.
5.3.2 The main transmission system of the drill shall be manually started through the starting
device. If the drill has multiple devices for starting, these devices shall be linked to each other
so that one of them can be used to complete the start.
For pneumatically driven drill, a shut-off valve shall be set on the main circuit to connect or
disconnect the power unit and the main machine, and to release the system pressure.
5.3.3 The drill shall have a normal shutdown command device to enable it to stop safely during
operation. The drill shall be equipped with a total stop switch; and each operating position for
operation and driving shall have an emergency stop device to prevent dangers caused by
emergencies.
5.3.4 The interruption of power supply or the re-supply after interruption shall not lead to the
occurrence of danger and shall meet the following requirements:
a) The drill can only be restarted by human command;
b) If the shutdown command has been issued, the drill must be shut down;
c) Equipment parts or tools are not allowed to fall or pop out;
d) Protective devices and protective measures shall be ensured effective.
Power supply failure or hydraulic and pneumatic pressure deviation from the set value is not
allowed to cause dangerous actions and emergency shutdown system failure.
5.3.5 Failure of the control circuit or logical failure of the control circuit is not allowed to cause
danger.
5.4 Control device
5.4.1 The operation of the control device shall be safe, flexible and comfortable; and its design
configuration and marking shall meet the requirements of GB/T 15706.2.
The main control device shall be arranged in the comfortable area of operation, and the auxiliary
control device can be arranged in the reach of operation or other positions outside the danger
zone.
If the drill has multiple operating positions, a selection switch shall be configured so that the
operator can purposefully select a favorable operating position.
5.4.2 The drill shall have corresponding emergency stop and safety devices; and the emergency
5.6.5 When the drill is operating, traveling and stopping on a slope exceeding the maximum
allowable slope, a traction winch shall be equipped to prevent the drill from slipping on the
slope.
5.7 Protection of moving parts
5.7.1 The design, manufacture and installation of the moving parts of the drill shall avoid the
dangers described in GB/T ...
Share
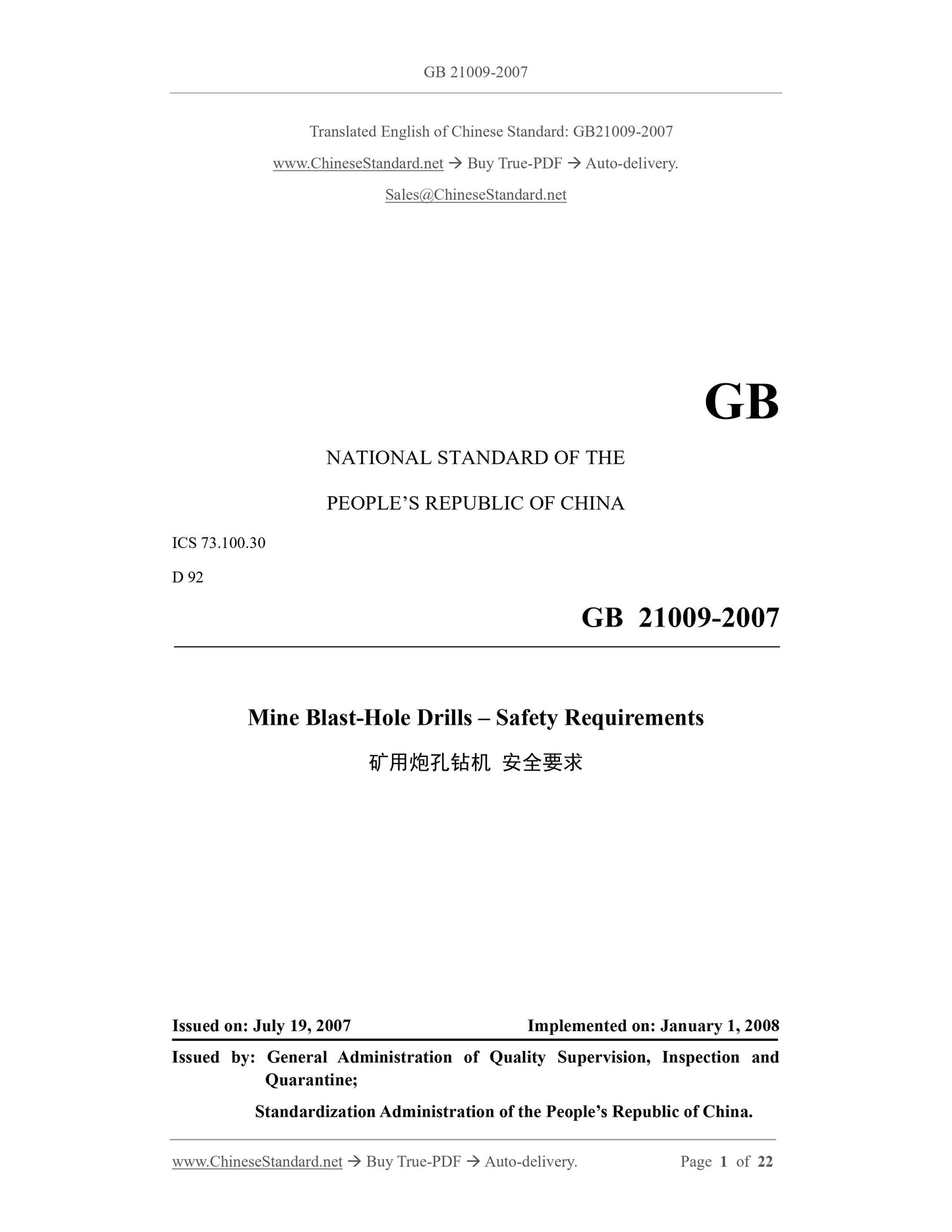

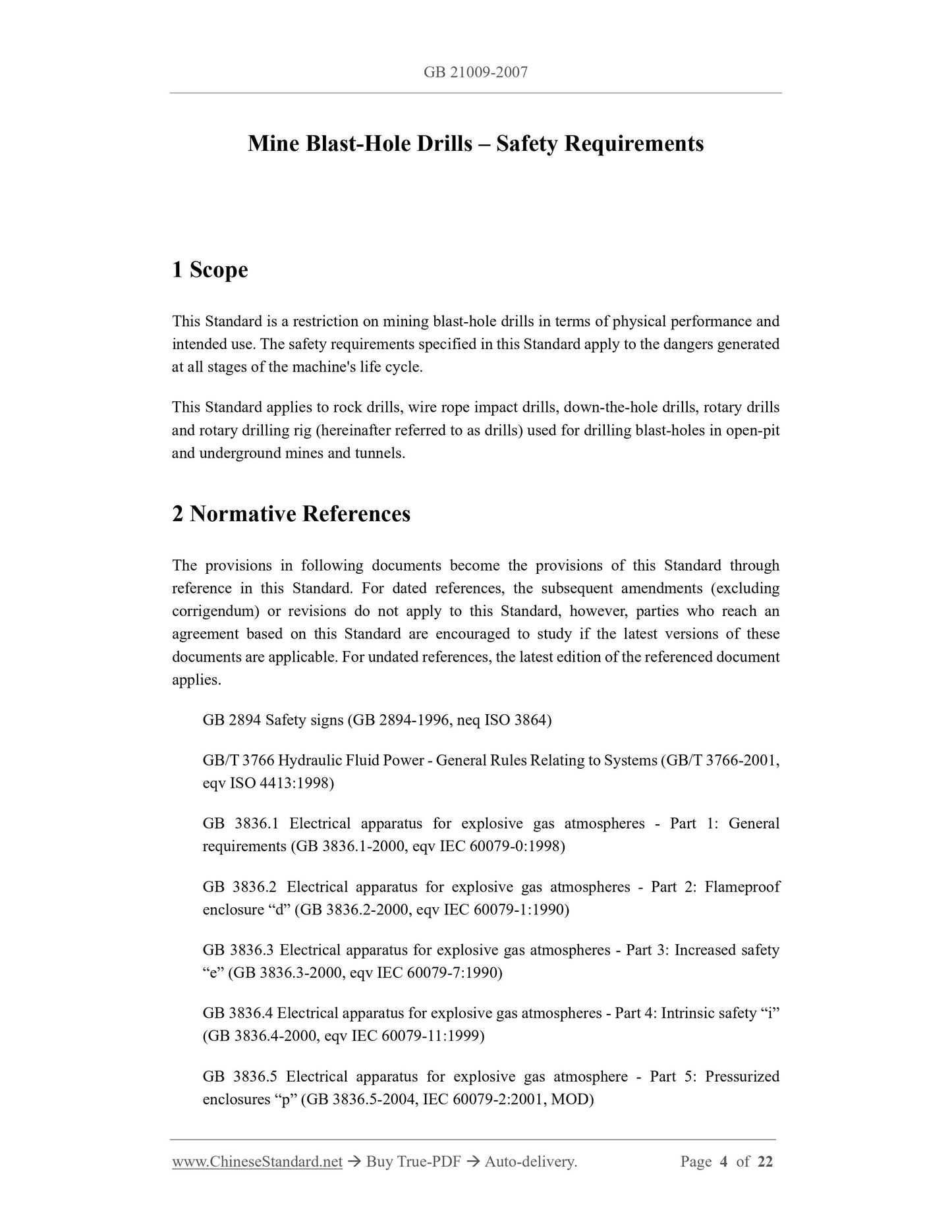
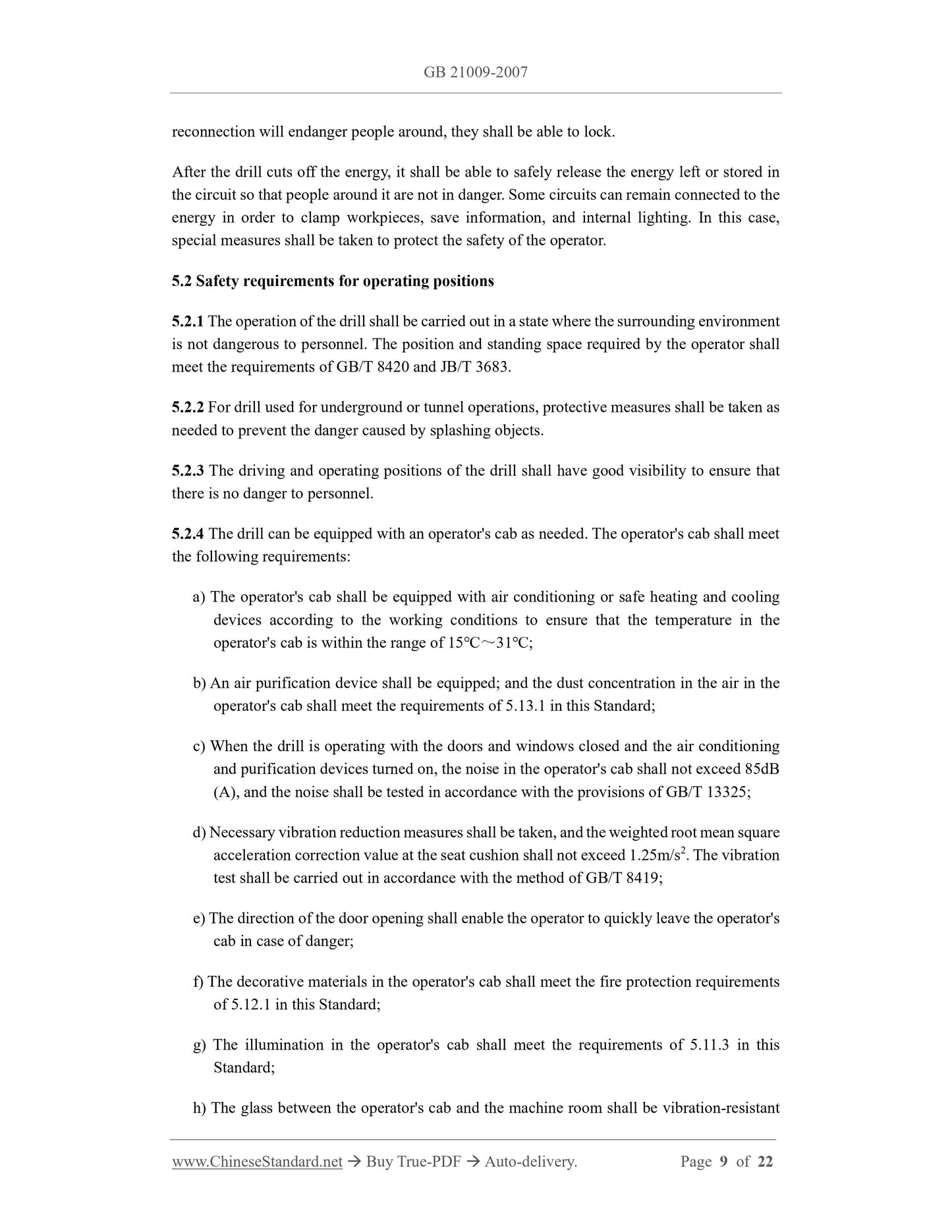
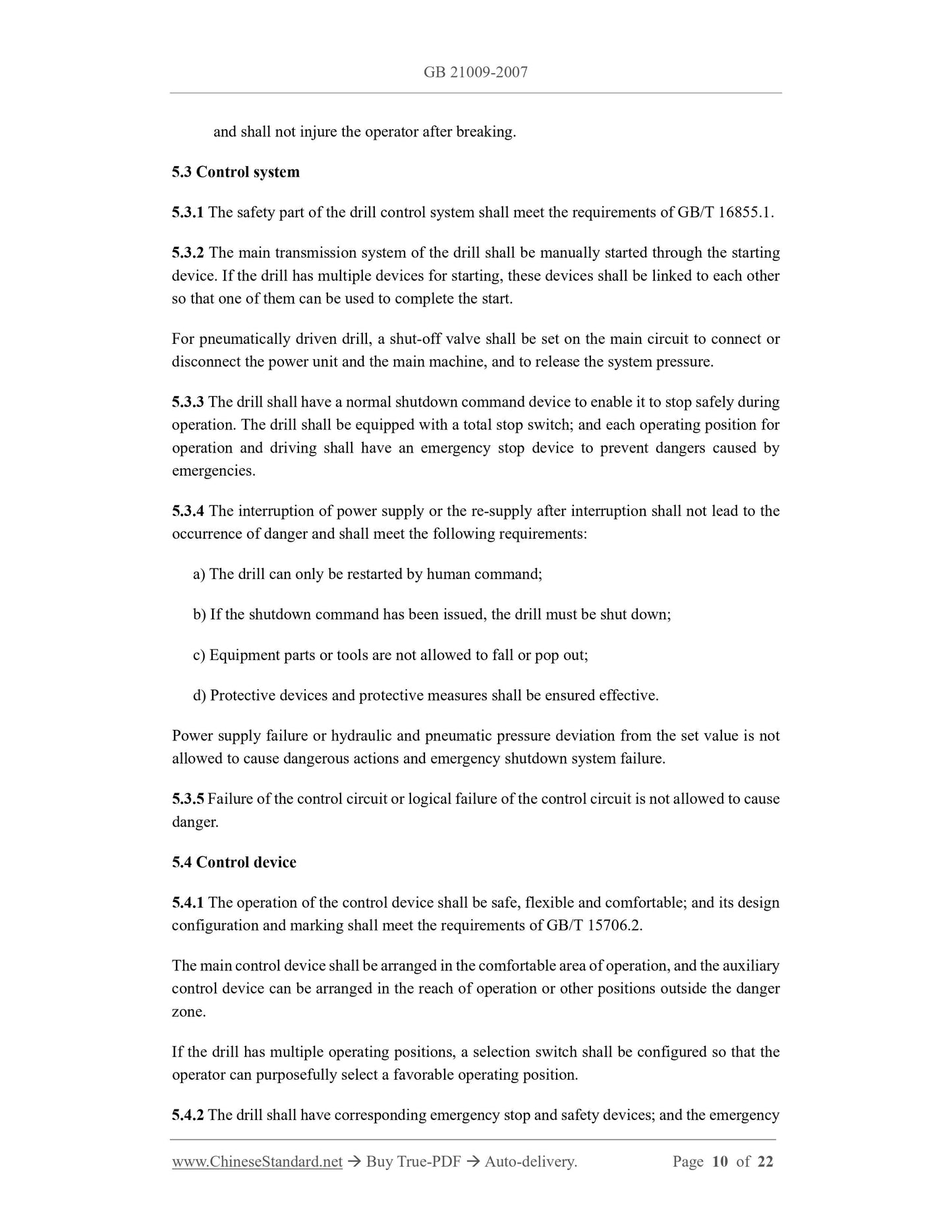
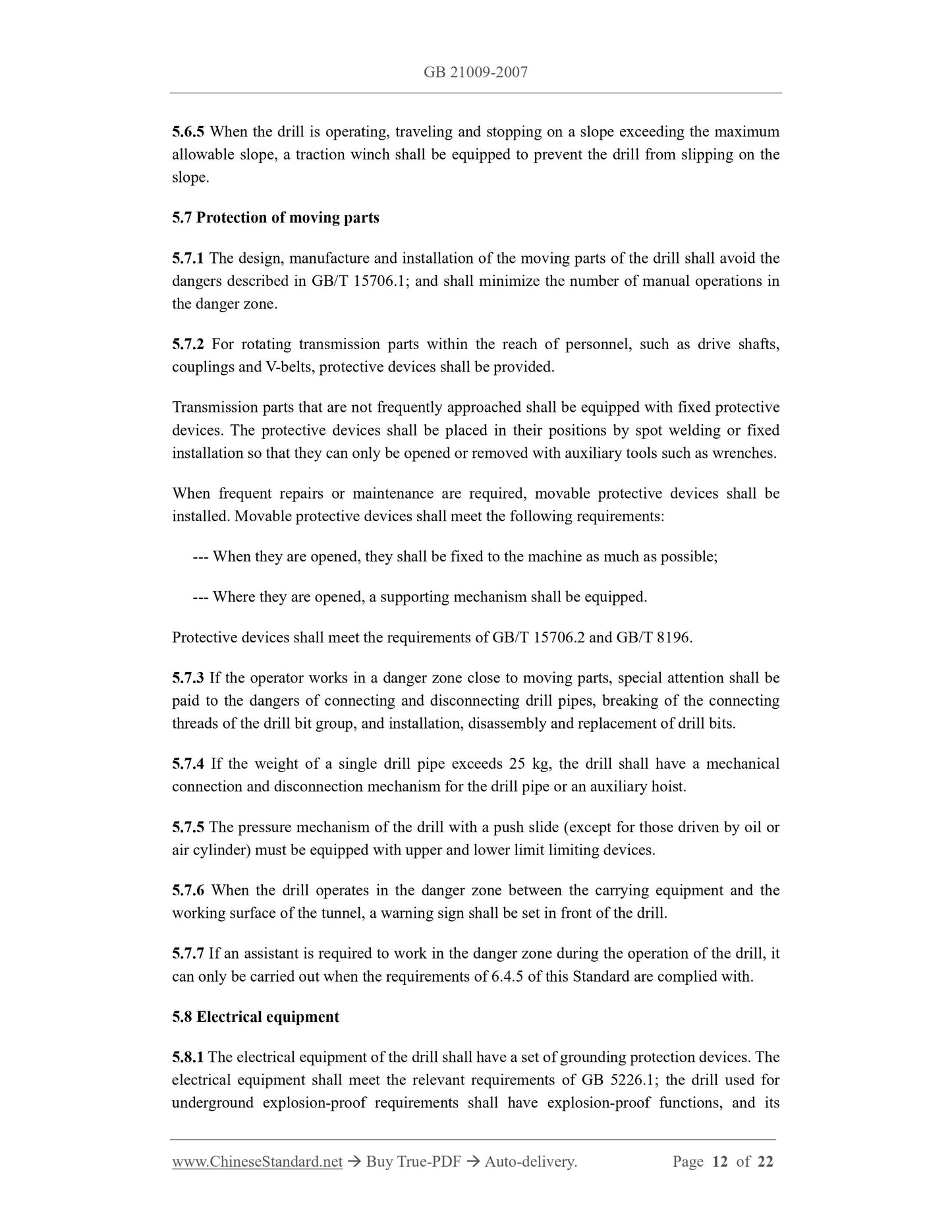
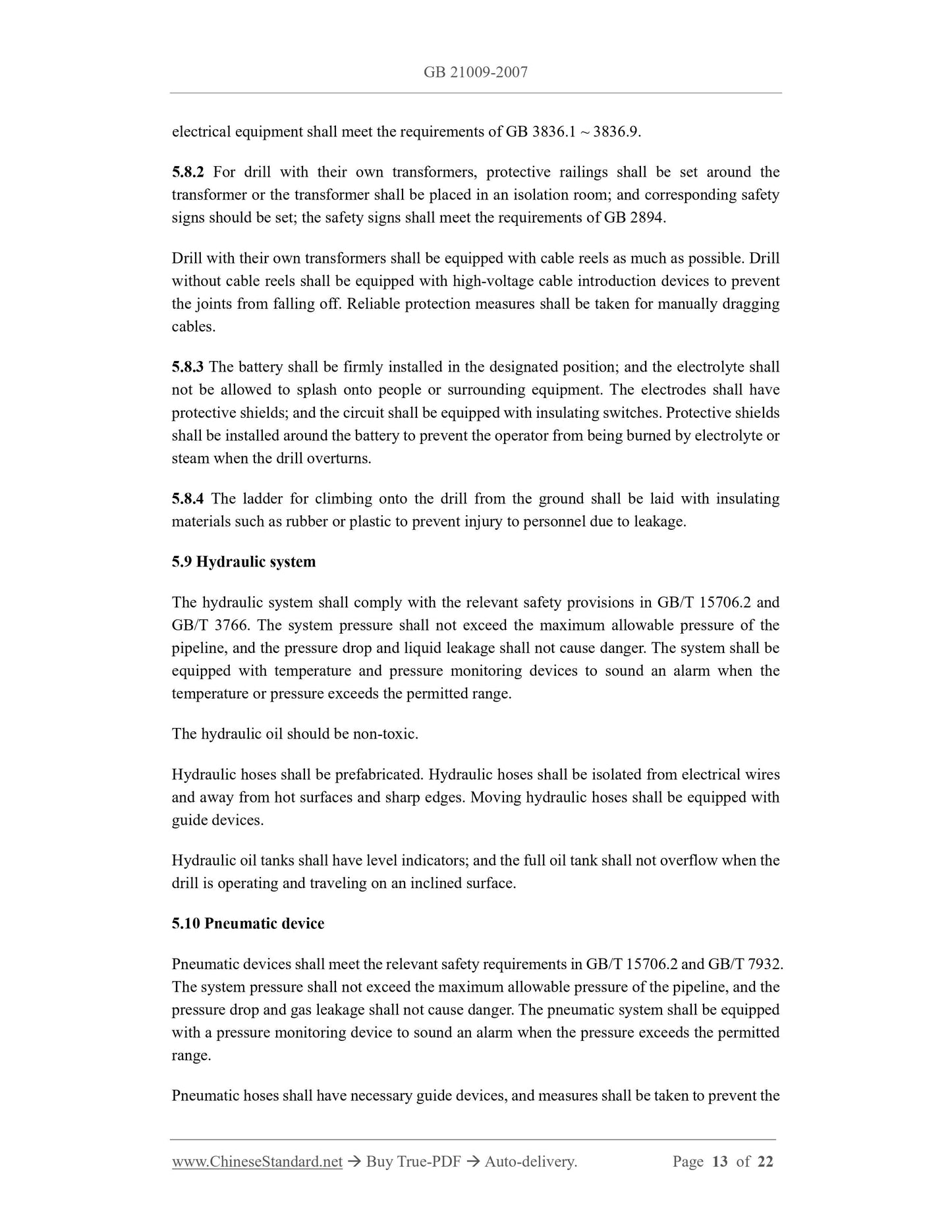
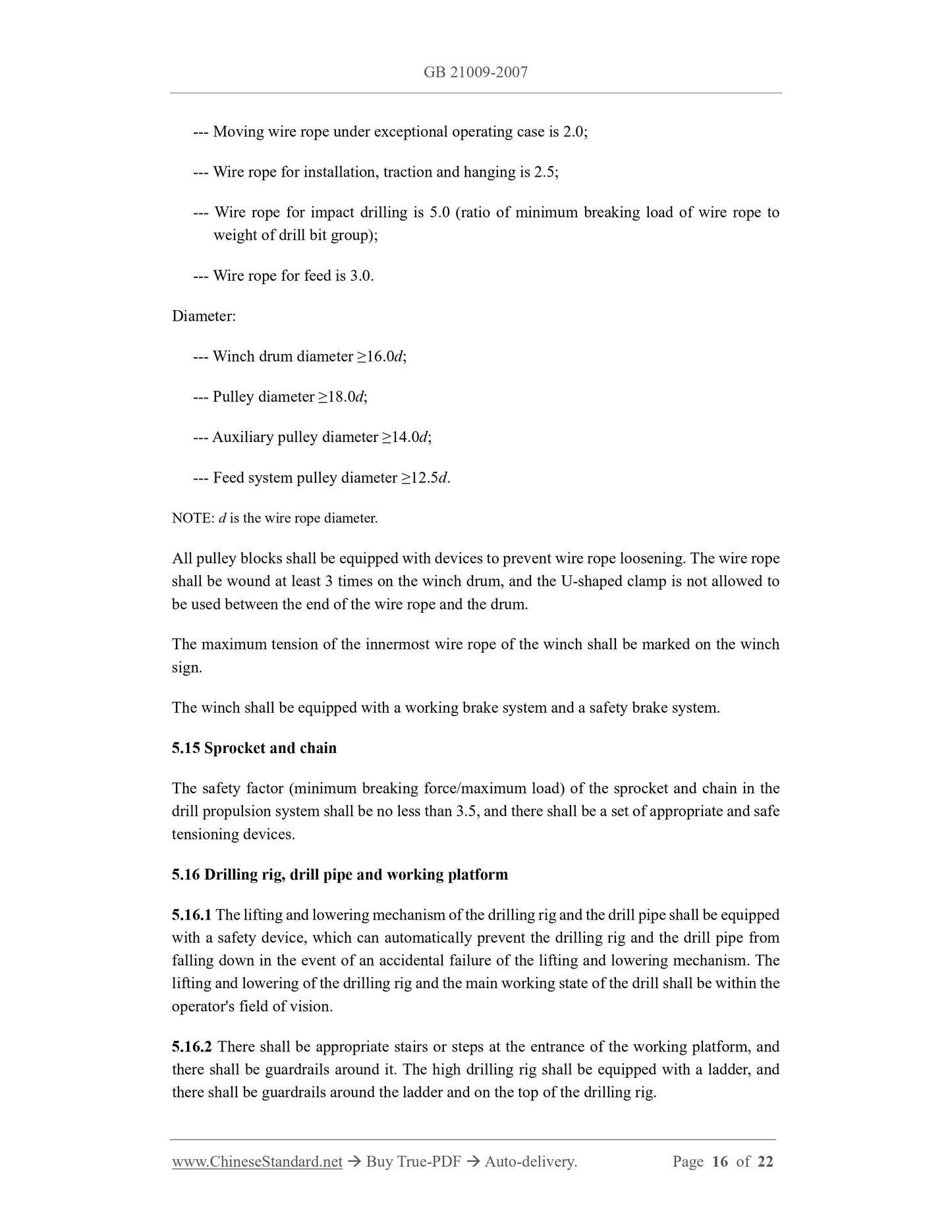

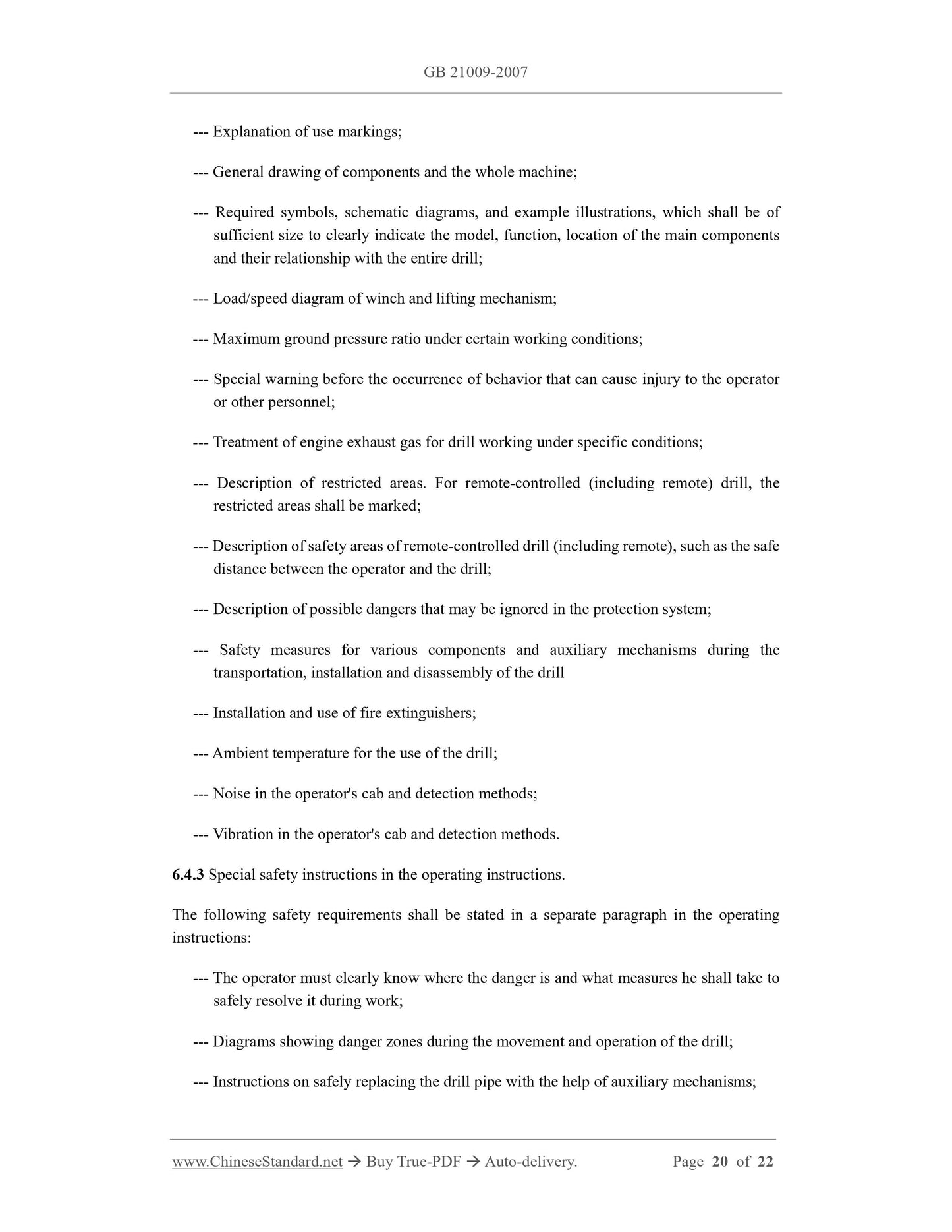
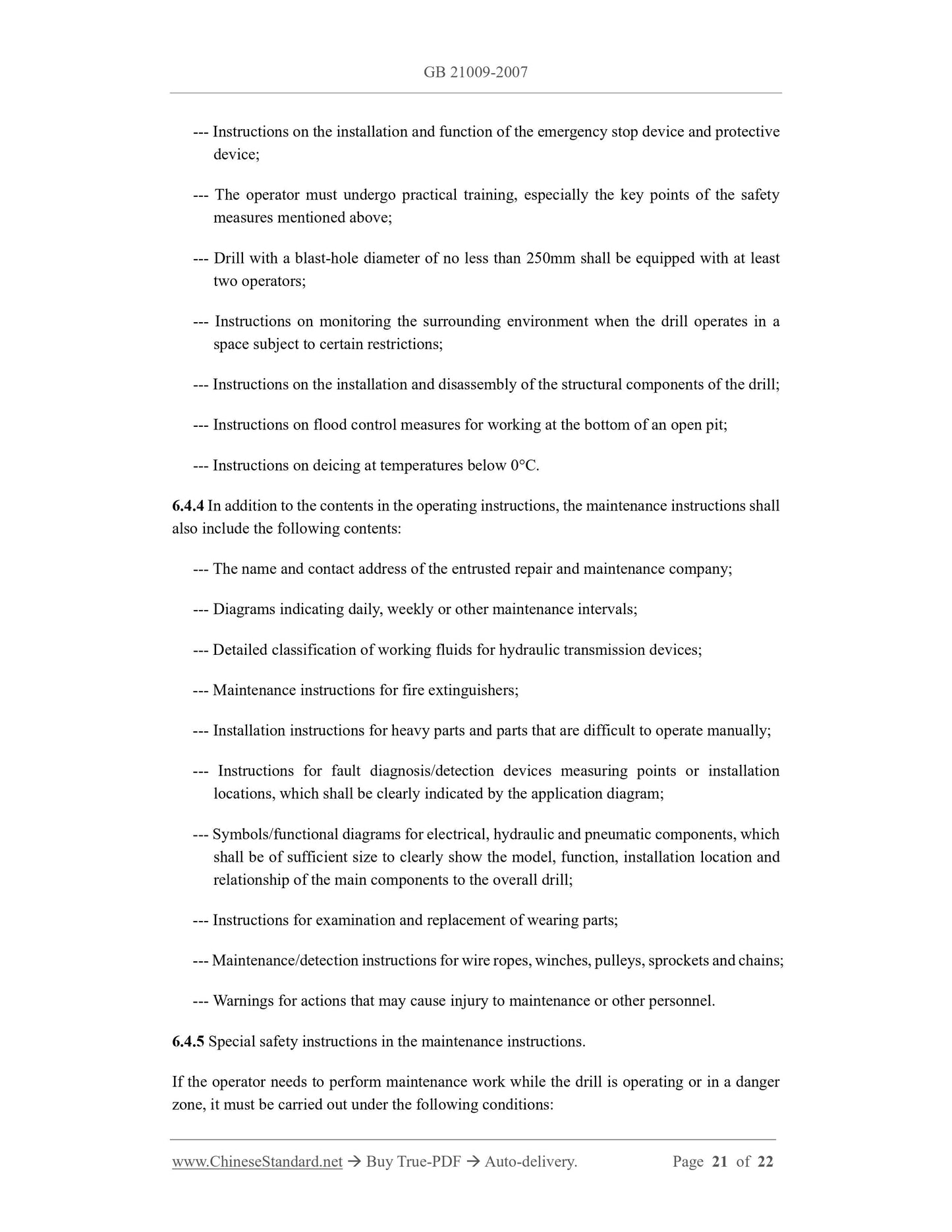
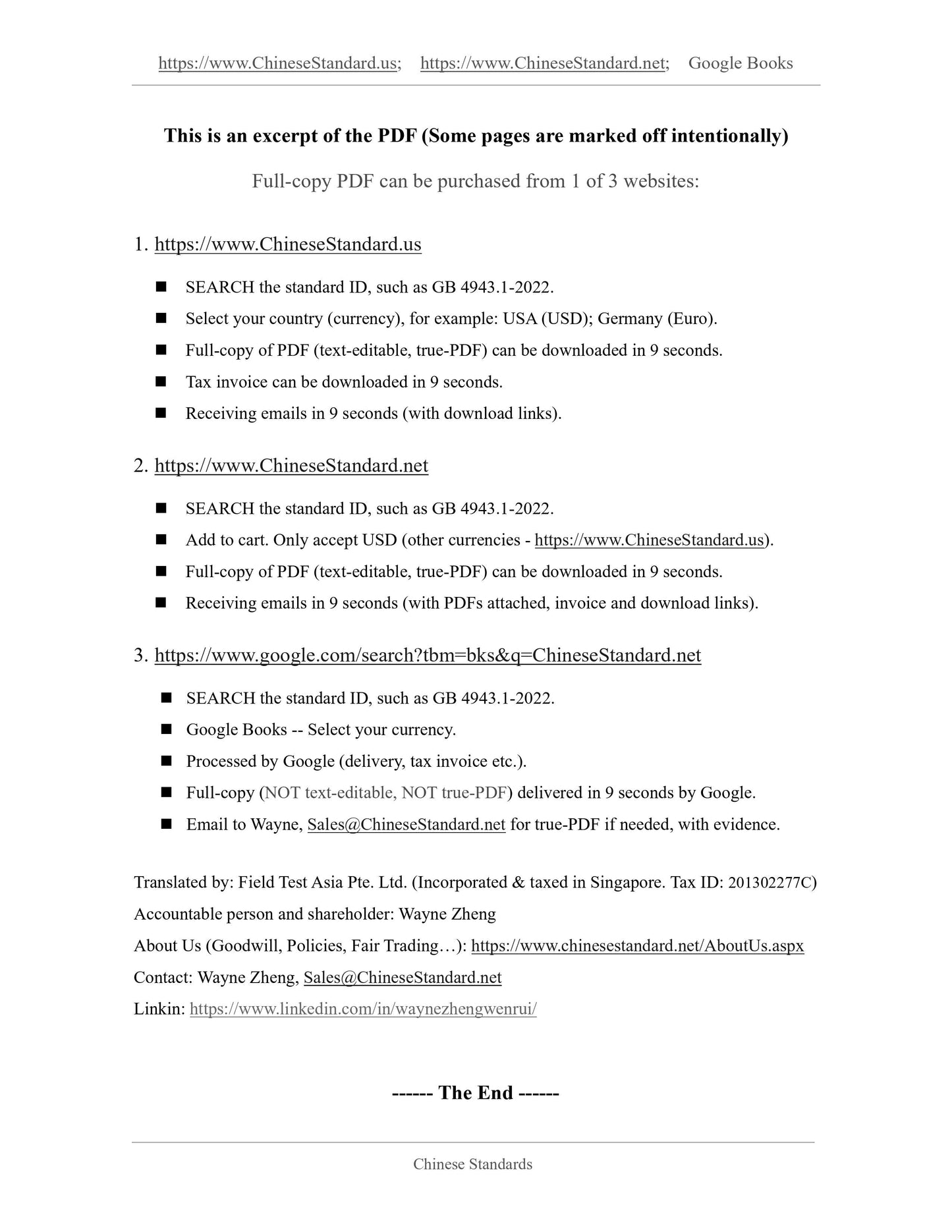