1
/
of
4
www.ChineseStandard.us -- Field Test Asia Pte. Ltd.
GB/T 10119-2008 English PDF (GB/T10119-2008)
GB/T 10119-2008 English PDF (GB/T10119-2008)
Regular price
$170.00
Regular price
Sale price
$170.00
Unit price
/
per
Shipping calculated at checkout.
Couldn't load pickup availability
GB/T 10119-2008: Determination of dezincification corrosion resistance of brass
Delivery: 9 seconds. Download (& Email) true-PDF + Invoice.
Get Quotation: Click GB/T 10119-2008 (Self-service in 1-minute)
Historical versions (Master-website): GB/T 10119-2008
Preview True-PDF (Reload/Scroll-down if blank)
GB/T 10119-2008
GB
NATIONAL STANDARD OF THE
PEOPLE’S REPUBLIC OF CHINA
ICS 77.120.99
H 13
Replacing GB/T 10119-1988
Determination of dezincification corrosion resistance
of brass
(ISO 6509:1981, Corrosion of metals and alloys - Determination of
dezincification resistance of brass, MOD)
ISSUED ON: MARCH 31, 2008
IMPLEMENTED ON: SEPTEMBER 01, 2008
Issued by: General Administration of Quality Supervision, Inspection and
Quarantine of PRC;
Standardization Administration of PRC.
Table of Contents
Foreword ... 3
1 Scope ... 5
2 Principle of methods ... 5
3 Reagents and materials ... 5
4 Test instrument and equipment ... 5
5 Specimen preparation and requirements ... 6
6 Test conditions and procedures ... 6
7 Microscopic observation and measurement ... 8
8 Test report ... 9
Appendix A (Informative) Comparison of clause numbers between this standard
and ISO 6509:1981 ... 11
Appendix B (Informative) Technical differences between this standard and ISO
6509:1981, as well as their reasons ... 12
Determination of dezincification corrosion resistance
of brass
1 Scope
This standard specifies the method for determining the dezincification corrosion
resistance of brass materials.
This standard applies to the determination of dezincification corrosion
resistance of brass materials.
2 Principle of methods
Because different brass materials have different dezincification corrosion rates,
the use of copper chloride solution can accelerate the dezincification corrosion
of brass, thereby producing different depths of dezincification layers, the depth
of which is measured by a metallurgical microscope.
3 Reagents and materials
3.1 Copper chloride solution (10 g/L): Dissolve 12.7 g of copper chloride (CuCl2
• 2H2O) in distilled water or deionized water. Dilute it to 1000 mL (prepare it
before use).
3.2 Epoxy resin or other non-conducting materials, which have similar
properties.
3.3 Anhydrous ethanol.
4 Test instrument and equipment
4.1 Test device: Constant temperature water bath or oil bath.
4.2 Metallurgical microscope (with micrometer eyepiece).
4.3 Glass beaker (1000 mL).
4.4 Hair dryer.
4.5 Polishing machine.
4.6 Dryer.
5 Specimen preparation and requirements
5.1 Sampling
5.1.1 Forgings and castings specimens shall be taken at the thinnest and
thickest part of the cross-section, respectively. The specimens of extruded,
drawn or rolled products shall be taken, parallel and perpendicular to the
processing direction.
5.1.2 Take at least 3 parallel specimens each time.
5.1.3 The size of the specimen shall be as close as possible to 10 mm × 10 mm
× 10 mm. The exposed area of the specimen shall be about 100 mm2. If this
requirement is not met, it shall take the largest area.
5.1.4 When sampling, it shall keep the original state of the specimen, to avoid
deformation of the specimen, due to clamping or sawing, OR other changes
that affect the test results.
5.2 Preparation of specimen
5.2.1 It is embedded by epoxy resin or other non-conducting materials (3.2).
5.2.2 The exposed surface of the specimen is ground by metallographic
sandpaper; finally polished by No.500 water sandpaper.
5.2.3 Use water to wash the ground specimen. Use absolute ethanol to wipe it.
Use hair dryer (4.4) to blow it dry. If the corrosion test cannot be performed in
time, it shall be stored in a desiccator (4.6).
6 Test conditions and procedures
6.1 Test conditions
6.1.1 Temperature of test solution: 75 °C ± 2 °C.
6.1.2 Volume of test solution: mL of copper chloride solution (3.1) is
required, for every 100 mm2 of the actual exposed area of the specimen.
6.1.3 Test time: 24 h continuously.
6.1.4 Only parallel specimens of the same alloy material can be placed in each
test beaker (4.3).
GB/T 10119-2008
GB
NATIONAL STANDARD OF THE
PEOPLE’S REPUBLIC OF CHINA
ICS 77.120.99
H 13
Replacing GB/T 10119-1988
Determination of dezincification corrosion resistance
of brass
(ISO 6509:1981, Corrosion of metals and alloys - Determination of
dezincification resistance of brass, MOD)
ISSUED ON: MARCH 31, 2008
IMPLEMENTED ON: SEPTEMBER 01, 2008
Issued by: General Administration of Quality Supervision, Inspection and
Quarantine of PRC;
Standardization Administration of PRC.
Table of Contents
Foreword ... 3
1 Scope ... 5
2 Principle of methods ... 5
3 Reagents and materials ... 5
4 Test instrument and equipment ... 5
5 Specimen preparation and requirements ... 6
6 Test conditions and procedures ... 6
7 Microscopic observation and measurement ... 8
8 Test report ... 9
Appendix A (Informative) Comparison of clause numbers between this standard
and ISO 6509:1981 ... 11
Appendix B (Informative) Technical differences between this standard and ISO
6509:1981, as well as their reasons ... 12
Determination of dezincification corrosion resistance
of brass
1 Scope
This standard specifies the method for determining the dezincification corrosion
resistance of brass materials.
This standard applies to the determination of dezincification corrosion
resistance of brass materials.
2 Principle of methods
Because different brass materials have different dezincification corrosion rates,
the use of copper chloride solution can accelerate the dezincification corrosion
of brass, thereby producing different depths of dezincification layers, the depth
of which is measured by a metallurgical microscope.
3 Reagents and materials
3.1 Copper chloride solution (10 g/L): Dissolve 12.7 g of copper chloride (CuCl2
• 2H2O) in distilled water or deionized water. Dilute it to 1000 mL (prepare it
before use).
3.2 Epoxy resin or other non-conducting materials, which have similar
properties.
3.3 Anhydrous ethanol.
4 Test instrument and equipment
4.1 Test device: Constant temperature water bath or oil bath.
4.2 Metallurgical microscope (with micrometer eyepiece).
4.3 Glass beaker (1000 mL).
4.4 Hair dryer.
4.5 Polishing machine.
4.6 Dryer.
5 Specimen preparation and requirements
5.1 Sampling
5.1.1 Forgings and castings specimens shall be taken at the thinnest and
thickest part of the cross-section, respectively. The specimens of extruded,
drawn or rolled products shall be taken, parallel and perpendicular to the
processing direction.
5.1.2 Take at least 3 parallel specimens each time.
5.1.3 The size of the specimen shall be as close as possible to 10 mm × 10 mm
× 10 mm. The exposed area of the specimen shall be about 100 mm2. If this
requirement is not met, it shall take the largest area.
5.1.4 When sampling, it shall keep the original state of the specimen, to avoid
deformation of the specimen, due to clamping or sawing, OR other changes
that affect the test results.
5.2 Preparation of specimen
5.2.1 It is embedded by epoxy resin or other non-conducting materials (3.2).
5.2.2 The exposed surface of the specimen is ground by metallographic
sandpaper; finally polished by No.500 water sandpaper.
5.2.3 Use water to wash the ground specimen. Use absolute ethanol to wipe it.
Use hair dryer (4.4) to blow it dry. If the corrosion test cannot be performed in
time, it shall be stored in a desiccator (4.6).
6 Test conditions and procedures
6.1 Test conditions
6.1.1 Temperature of test solution: 75 °C ± 2 °C.
6.1.2 Volume of test solution: mL of copper chloride solution (3.1) is
required, for every 100 mm2 of the actual exposed area of the specimen.
6.1.3 Test time: 24 h continuously.
6.1.4 Only parallel specimens of the same alloy material can be placed in each
test beaker (4.3).
Delivery: 9 seconds. Download (& Email) true-PDF + Invoice.
Get Quotation: Click GB/T 10119-2008 (Self-service in 1-minute)
Historical versions (Master-website): GB/T 10119-2008
Preview True-PDF (Reload/Scroll-down if blank)
GB/T 10119-2008
GB
NATIONAL STANDARD OF THE
PEOPLE’S REPUBLIC OF CHINA
ICS 77.120.99
H 13
Replacing GB/T 10119-1988
Determination of dezincification corrosion resistance
of brass
(ISO 6509:1981, Corrosion of metals and alloys - Determination of
dezincification resistance of brass, MOD)
ISSUED ON: MARCH 31, 2008
IMPLEMENTED ON: SEPTEMBER 01, 2008
Issued by: General Administration of Quality Supervision, Inspection and
Quarantine of PRC;
Standardization Administration of PRC.
Table of Contents
Foreword ... 3
1 Scope ... 5
2 Principle of methods ... 5
3 Reagents and materials ... 5
4 Test instrument and equipment ... 5
5 Specimen preparation and requirements ... 6
6 Test conditions and procedures ... 6
7 Microscopic observation and measurement ... 8
8 Test report ... 9
Appendix A (Informative) Comparison of clause numbers between this standard
and ISO 6509:1981 ... 11
Appendix B (Informative) Technical differences between this standard and ISO
6509:1981, as well as their reasons ... 12
Determination of dezincification corrosion resistance
of brass
1 Scope
This standard specifies the method for determining the dezincification corrosion
resistance of brass materials.
This standard applies to the determination of dezincification corrosion
resistance of brass materials.
2 Principle of methods
Because different brass materials have different dezincification corrosion rates,
the use of copper chloride solution can accelerate the dezincification corrosion
of brass, thereby producing different depths of dezincification layers, the depth
of which is measured by a metallurgical microscope.
3 Reagents and materials
3.1 Copper chloride solution (10 g/L): Dissolve 12.7 g of copper chloride (CuCl2
• 2H2O) in distilled water or deionized water. Dilute it to 1000 mL (prepare it
before use).
3.2 Epoxy resin or other non-conducting materials, which have similar
properties.
3.3 Anhydrous ethanol.
4 Test instrument and equipment
4.1 Test device: Constant temperature water bath or oil bath.
4.2 Metallurgical microscope (with micrometer eyepiece).
4.3 Glass beaker (1000 mL).
4.4 Hair dryer.
4.5 Polishing machine.
4.6 Dryer.
5 Specimen preparation and requirements
5.1 Sampling
5.1.1 Forgings and castings specimens shall be taken at the thinnest and
thickest part of the cross-section, respectively. The specimens of extruded,
drawn or rolled products shall be taken, parallel and perpendicular to the
processing direction.
5.1.2 Take at least 3 parallel specimens each time.
5.1.3 The size of the specimen shall be as close as possible to 10 mm × 10 mm
× 10 mm. The exposed area of the specimen shall be about 100 mm2. If this
requirement is not met, it shall take the largest area.
5.1.4 When sampling, it shall keep the original state of the specimen, to avoid
deformation of the specimen, due to clamping or sawing, OR other changes
that affect the test results.
5.2 Preparation of specimen
5.2.1 It is embedded by epoxy resin or other non-conducting materials (3.2).
5.2.2 The exposed surface of the specimen is ground by metallographic
sandpaper; finally polished by No.500 water sandpaper.
5.2.3 Use water to wash the ground specimen. Use absolute ethanol to wipe it.
Use hair dryer (4.4) to blow it dry. If the corrosion test cannot be performed in
time, it shall be stored in a desiccator (4.6).
6 Test conditions and procedures
6.1 Test conditions
6.1.1 Temperature of test solution: 75 °C ± 2 °C.
6.1.2 Volume of test solution: mL of copper chloride solution (3.1) is
required, for every 100 mm2 of the actual exposed area of the specimen.
6.1.3 Test time: 24 h continuously.
6.1.4 Only parallel specimens of the same alloy material can be placed in each
test beaker (4.3).
GB/T 10119-2008
GB
NATIONAL STANDARD OF THE
PEOPLE’S REPUBLIC OF CHINA
ICS 77.120.99
H 13
Replacing GB/T 10119-1988
Determination of dezincification corrosion resistance
of brass
(ISO 6509:1981, Corrosion of metals and alloys - Determination of
dezincification resistance of brass, MOD)
ISSUED ON: MARCH 31, 2008
IMPLEMENTED ON: SEPTEMBER 01, 2008
Issued by: General Administration of Quality Supervision, Inspection and
Quarantine of PRC;
Standardization Administration of PRC.
Table of Contents
Foreword ... 3
1 Scope ... 5
2 Principle of methods ... 5
3 Reagents and materials ... 5
4 Test instrument and equipment ... 5
5 Specimen preparation and requirements ... 6
6 Test conditions and procedures ... 6
7 Microscopic observation and measurement ... 8
8 Test report ... 9
Appendix A (Informative) Comparison of clause numbers between this standard
and ISO 6509:1981 ... 11
Appendix B (Informative) Technical differences between this standard and ISO
6509:1981, as well as their reasons ... 12
Determination of dezincification corrosion resistance
of brass
1 Scope
This standard specifies the method for determining the dezincification corrosion
resistance of brass materials.
This standard applies to the determination of dezincification corrosion
resistance of brass materials.
2 Principle of methods
Because different brass materials have different dezincification corrosion rates,
the use of copper chloride solution can accelerate the dezincification corrosion
of brass, thereby producing different depths of dezincification layers, the depth
of which is measured by a metallurgical microscope.
3 Reagents and materials
3.1 Copper chloride solution (10 g/L): Dissolve 12.7 g of copper chloride (CuCl2
• 2H2O) in distilled water or deionized water. Dilute it to 1000 mL (prepare it
before use).
3.2 Epoxy resin or other non-conducting materials, which have similar
properties.
3.3 Anhydrous ethanol.
4 Test instrument and equipment
4.1 Test device: Constant temperature water bath or oil bath.
4.2 Metallurgical microscope (with micrometer eyepiece).
4.3 Glass beaker (1000 mL).
4.4 Hair dryer.
4.5 Polishing machine.
4.6 Dryer.
5 Specimen preparation and requirements
5.1 Sampling
5.1.1 Forgings and castings specimens shall be taken at the thinnest and
thickest part of the cross-section, respectively. The specimens of extruded,
drawn or rolled products shall be taken, parallel and perpendicular to the
processing direction.
5.1.2 Take at least 3 parallel specimens each time.
5.1.3 The size of the specimen shall be as close as possible to 10 mm × 10 mm
× 10 mm. The exposed area of the specimen shall be about 100 mm2. If this
requirement is not met, it shall take the largest area.
5.1.4 When sampling, it shall keep the original state of the specimen, to avoid
deformation of the specimen, due to clamping or sawing, OR other changes
that affect the test results.
5.2 Preparation of specimen
5.2.1 It is embedded by epoxy resin or other non-conducting materials (3.2).
5.2.2 The exposed surface of the specimen is ground by metallographic
sandpaper; finally polished by No.500 water sandpaper.
5.2.3 Use water to wash the ground specimen. Use absolute ethanol to wipe it.
Use hair dryer (4.4) to blow it dry. If the corrosion test cannot be performed in
time, it shall be stored in a desiccator (4.6).
6 Test conditions and procedures
6.1 Test conditions
6.1.1 Temperature of test solution: 75 °C ± 2 °C.
6.1.2 Volume of test solution: mL of copper chloride solution (3.1) is
required, for every 100 mm2 of the actual exposed area of the specimen.
6.1.3 Test time: 24 h continuously.
6.1.4 Only parallel specimens of the same alloy material can be placed in each
test beaker (4.3).
Share
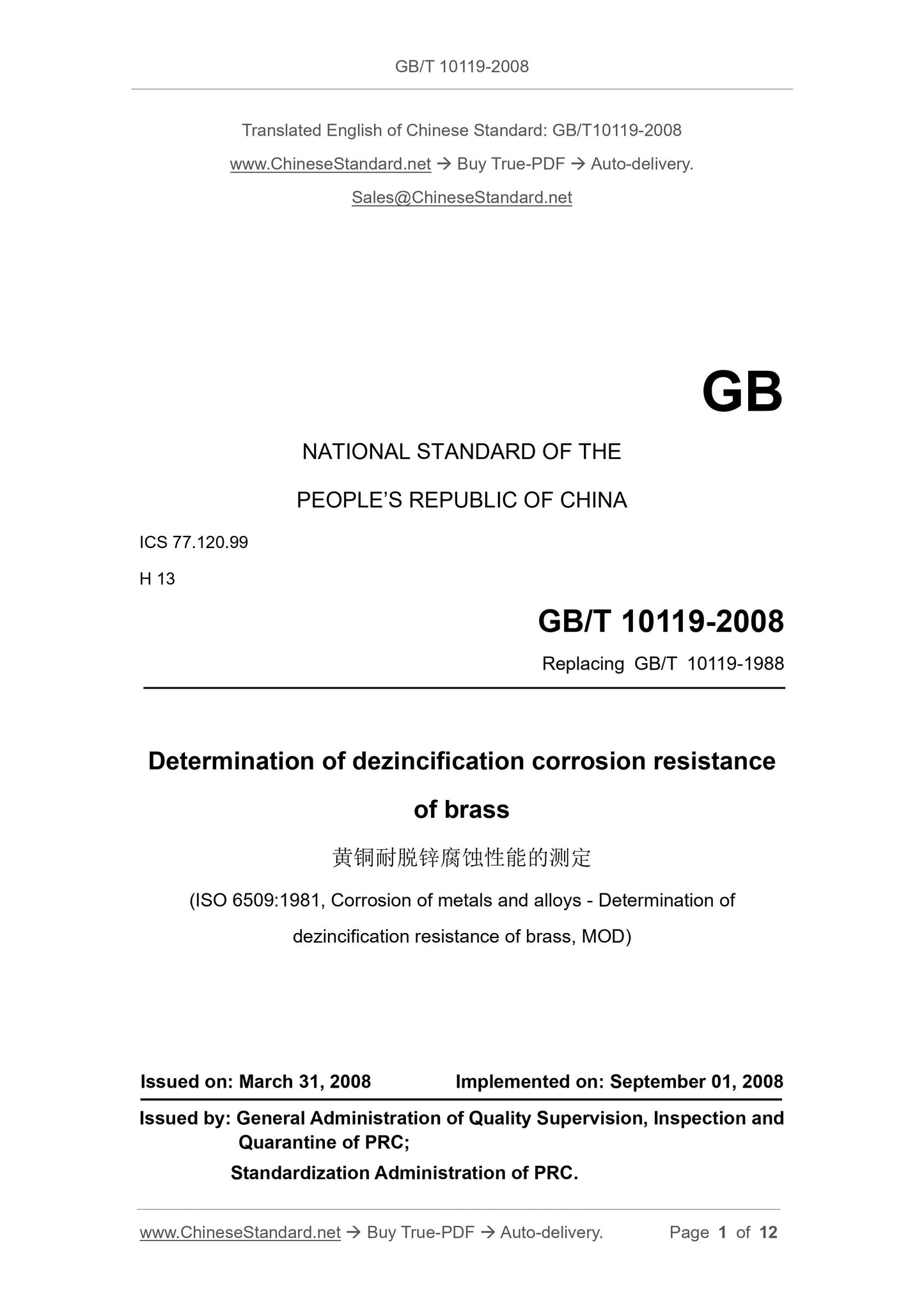
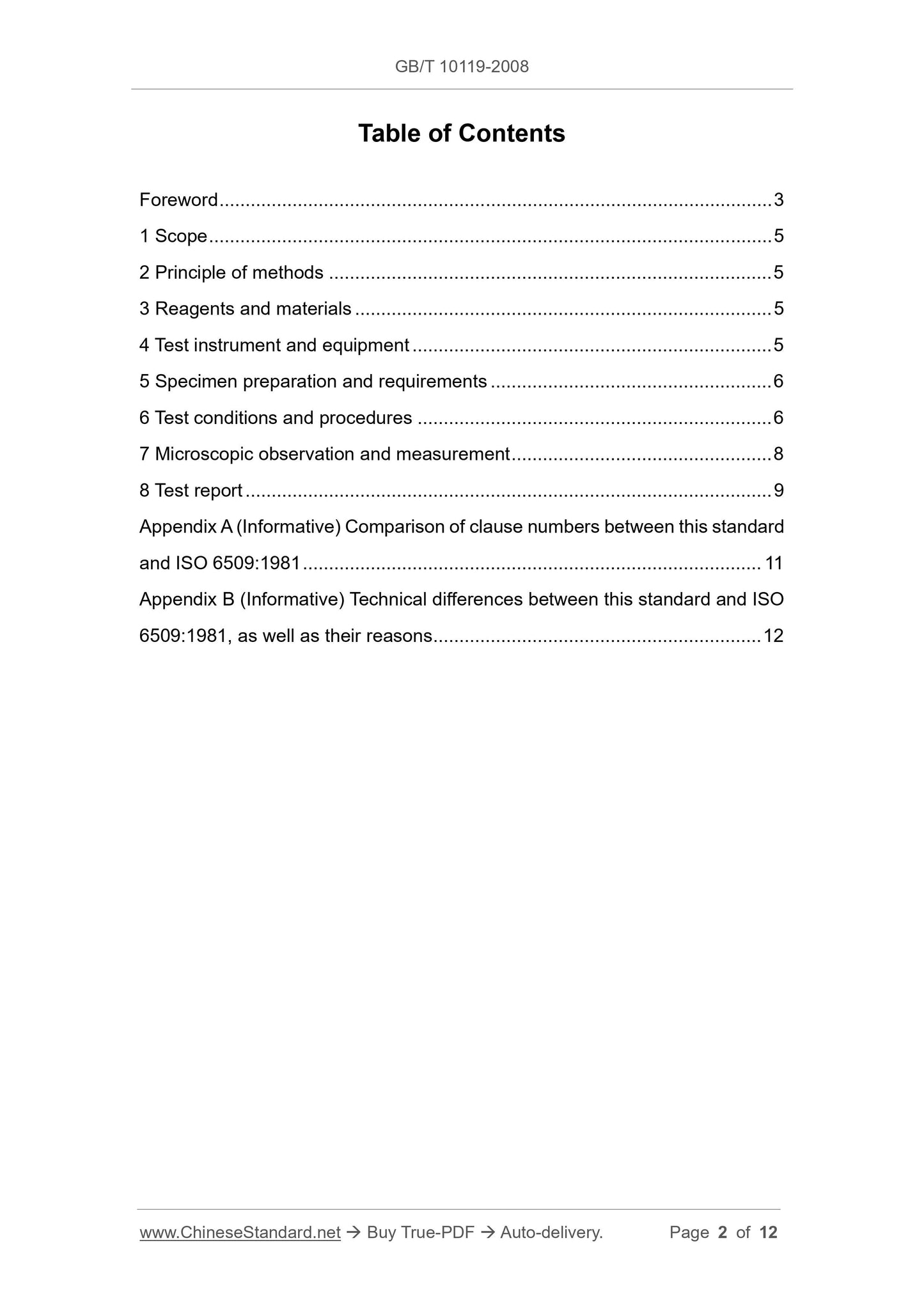
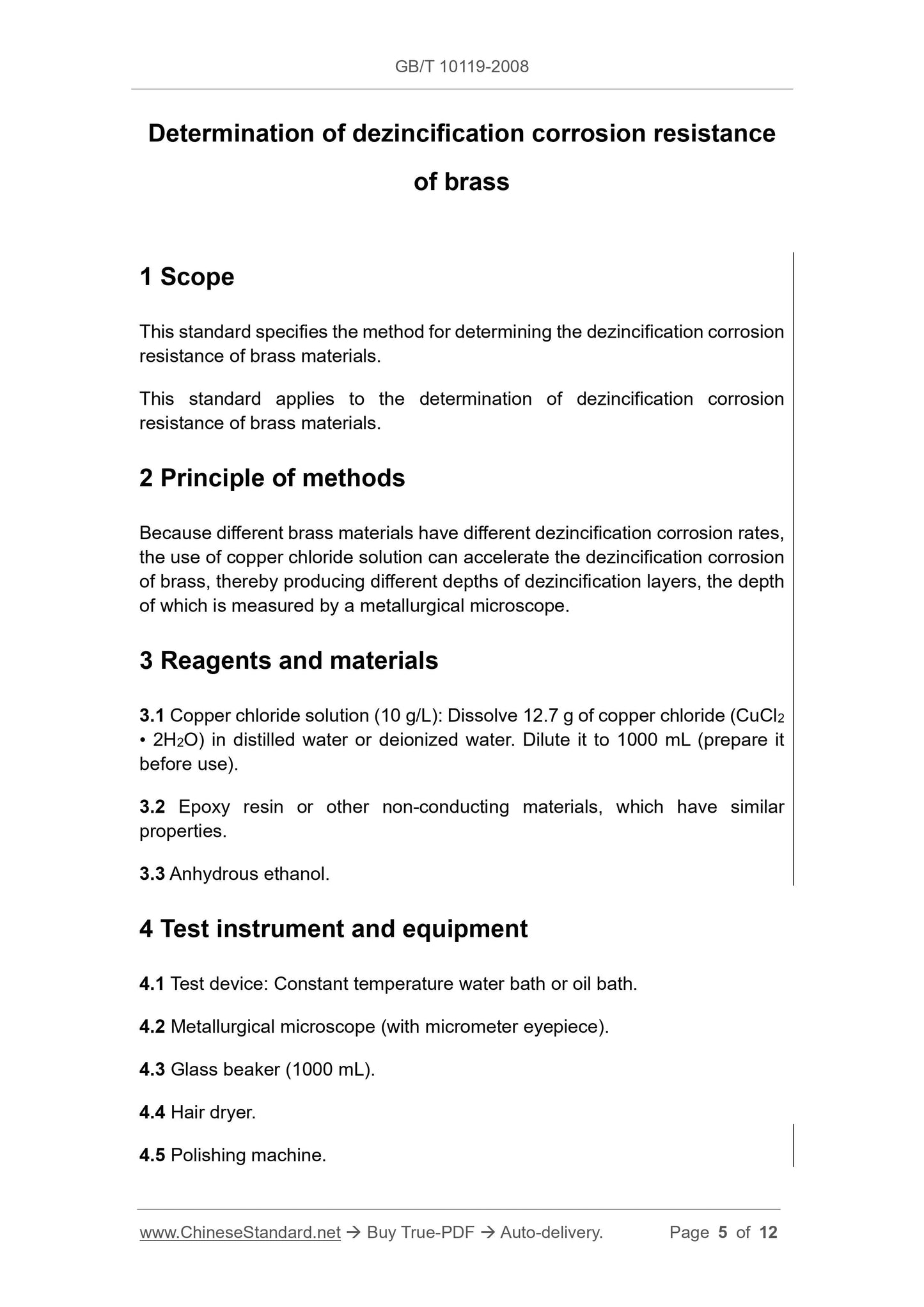
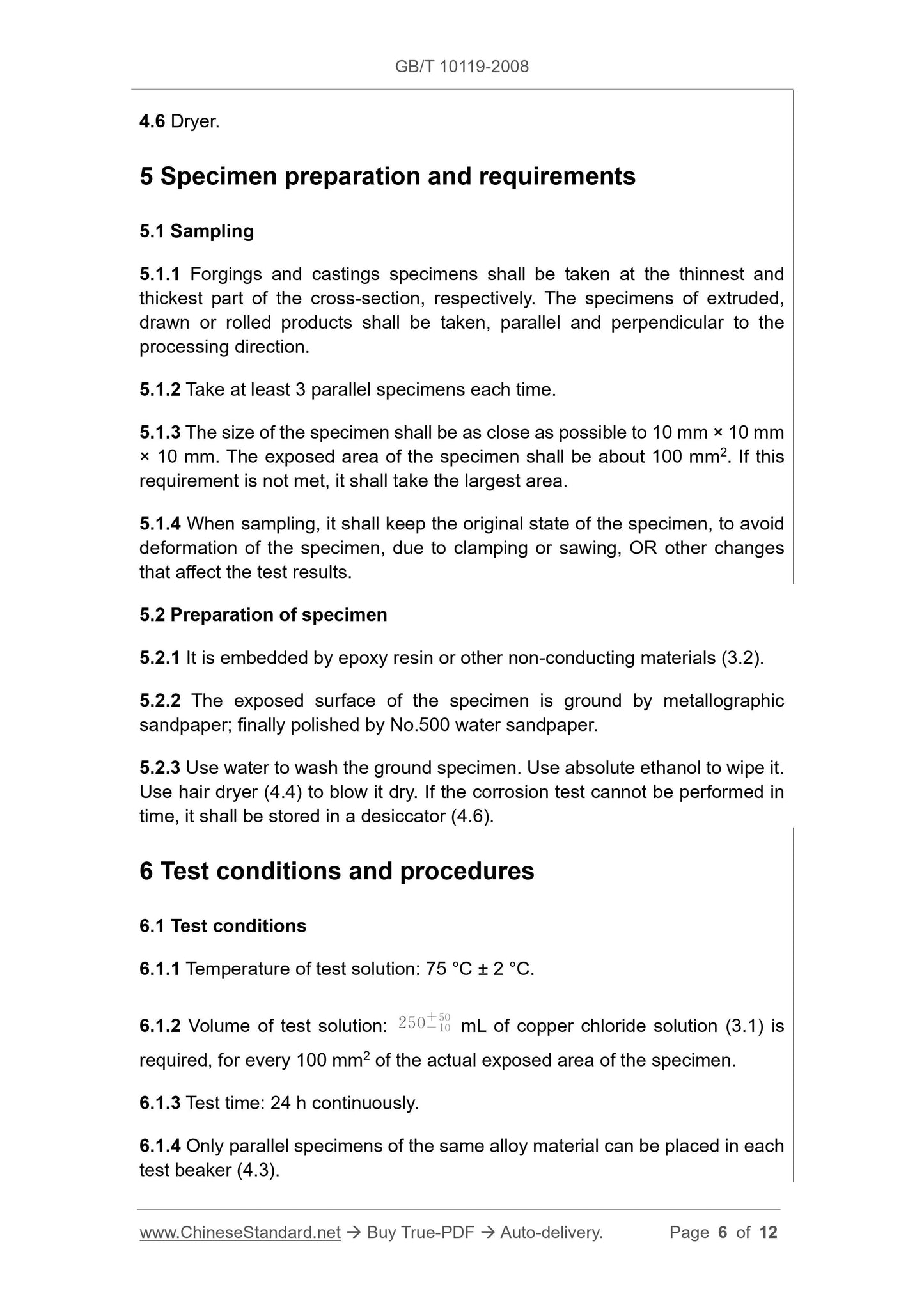