1
/
of
9
PayPal, credit cards. Download editable-PDF & invoice in 1 second!
GB/T 4000-2008 English PDF (GBT4000-2008)
GB/T 4000-2008 English PDF (GBT4000-2008)
Regular price
$140.00 USD
Regular price
Sale price
$140.00 USD
Unit price
/
per
Shipping calculated at checkout.
Couldn't load pickup availability
Delivery: 3 seconds. Download true-PDF + Invoice.Newer version: (Replacing this standard) GB/T 4000-2017
Get QUOTATION in 1-minute: Click GB/T 4000-2008
Historical versions: GB/T 4000-2008
Preview True-PDF (Reload/Scroll if blank)
GB/T 4000-2008: Coke -- Determination of reactivity and strength after reaction
GB/T 4000-2008
GB
NATIONAL STANDARD OF THE
PEOPLE’S REPUBLIC OF CHINA
ICS 75.160.10
H 32
Replacing GB/T 4000-1996
Coke - Determination of reactivity and strength
after reaction
ISSUED ON. AUGUST 19, 2008
IMPLEMENTED ON. APRIL 01, 2009
Issued by.
General Administration of Quality Supervision, Inspection
and Quarantine of the People’s Republic of China;
Standardization Administration of the People’s Republic of
China.
Table of Contents
Foreword ... 3
1 Scope ... 4
2 Normative references ... 4
3 Principles ... 4
4 Test instruments, apparatuses and materials ... 4
5 Sampling and sample preparation ... 12
6 Test procedures ... 12
7 Calculation of results ... 15
8 Degree of precision ... 15
Annex A ... 16
Annex B ... 18
Foreword
This Standard replaces GB/T 4000-1996 “Coke - Determination of Reactivity and Strength
after Reaction”.
Compared with GB/T 4000-1996, the main changes of this Standard are as follows.
— Preparation method of coke sample is revised as preparation method that jaw
crushing combines with hand finishing;
— Narrow the particle size control range of coke sample;
— Test apparatuses are improved to facilitate the maintenance.
Annex A and Annex B of this Standard are normative.
This Standard was proposed by China Iron and Steel Industry Association.
This Standard shall be under the jurisdiction of National Steel Standardization Technical
Committee.
Drafting organizations of this Standard. Wuhan Iron and Steel (Group) Corp., China
Metallurgical Information and Standardization Institute AND Shangyu HongXing
Machinery Instrument Manufacturing Co., Ltd.
Main drafters of this Standard. Sun Wei, Xi Wanze, Zhu Mingsan and Zhang Jinying.
The historical versions replaced by this Standard are as follows.
— GB 4000-1983, GB/T 4000-1996.
Coke - Determination of Reactivity and Strength after Reaction
1 Scope
This Standard specifies the principles of coke determination of reactivity and strength after
reaction, test instruments, apparatuses and materials, sampling and sample preparation,
test procedures, calculation of results and degree of precision.
This Standard applies to the determination of reactivity of coke for blast furnace iron
making and strength after reaction; coke for other purposes may refer to this Standard for
implementation.
2 Normative references
The articles contained in the following documents have become part of this document
when they are quoted herein. For the dated documents so quoted, all subsequent
modifications (including all corrections) or revisions made thereafter do not apply to this
Standard. However, the parties who reach an agreement according to this Standard are
encouraged to study whether the latest versions of these documents may be used. For
the undated documents so quoted, the latest versions (including all modification sheets)
apply to this document.
GB/T 1997 Coke - Sampling and preparation of samples
GB/T 2006 Coke for metallurgy - Determination of mechanical strength
3 Principles
Weigh a certain mass of coke sample and place into a reactor; use the percentage of coke
mass loss to express the coke reactivity (CRI), after 2 h of reaction with carbon dioxide at
1100°C±5°C.
After reaction, and after the revolving drum test of type I, use the mass fraction OF coke,
that is greater than 10 mm size, OVER the coke after reaction TO express the coke
strength after reaction (CSR).
4 Test instruments, apparatuses and materials
4.1 Electric furnace
Electric furnace heating wire, silicon carbide and other heating elements that can meet
may be adopted.
4.6 Φ precision temperature control device
Temperature control range is 0 °C~1 600 °C, precision grade is 0.5.
4.7 Round-hole screen
One for Φ10 mm, effective diameter of screen frame is 200 mm.
One for Φ23 mm, effective diameter of screen frame is 300 mm.
One for Φ25 mm and one for Φ3 mm, screen surface is 400 mm×500 mm, made
according to the provisions on round-hole screen in GB/T 2006.
4.8 Drying oven
Workshop capacity is not less than 0.07 m3.
Maximum operating temperature. 300 °C.
4.9 Balance
Maximum capacity is 500 g, sensitivity is 0.5 g.
4.10 Rhodium-platinum thermocouple
Diameter is 0.5 mm, length is 650 mm.
High-alumina thermocouple protection pipe A (Φ7 mmX5 mmX400 mm)
High-alumina dual-hole insulation pipe D (Φ4 mmX1 mmX400 mm)
High-alumina single-hole insulation pipe C (Φ1 mmX0.6 mmX10 mm)
4.11 Board
It is of high temperature resistance alloy steel (GH23 or GH44), thickness of 2 mm~5 mm
and diameter of 79 mm. Drill holes evenly with a uniform diameter of 3 mm and hole
interval is 5 mm.
4.12 High-alumina ball
Diameter is 20 mm.
4.13 Bracket
Bracket is shown in Figure 8, made of material Q235A. Material of three branch pipes is of
1Gr18Ni9Ti.
top of furnace; place into electric furnace; place asbestos board between bracket and
electric furnace lid for thermal insulation. Fill the surrounding of reactor flange with thermal
insulation material to reduce heat dissipation.
6.2.2 When using corundum reactor, load about one half of 200 g±0.5 g of prepared coke
samples; then insert into thermocouple sleeve; load another half of coke; make
thermocouple sleeve to pass the center hole in reactor lid; apply reactor lid. The
surrounding is filled with insulation materials to reduce heat dissipation.
6.3 Insert temperature thermocouple into reactor thermocouple sleeve (protected by
thermocouple high-alumina dual-hole insulation pipe and high-alumina thermocouple
protection pipe).
6.4 Respectively connect reactor intake pipe and vent pipe with gas supply system and
vent pipe. Check gas circuit to ensure tightness.
6.5 Switch on and adjust electric furnace for heating through precision temperature control
device. Rate of temperature increase is 8 °C/min~16 °C/min. When temperature at the
center of bed of material is up to 400 °C, feed nitrogen at a flow rate of 0.8 L/min to protect
coke and prevent burning.
6.6 When temperature at the center of bed of material reaches 1050 °C, switch on power
plug of carbon dioxide pressure reducing valve with preheating device; preheat the exit of
carbon dioxide gas cylinder to ensure stable outflow of carbon dioxide. When temperature
at the center of bend of material reaches 1100°C, stabilize for 10 min; cut off nitrogen and
replace with carbon dioxide at a flow of 5 L/min; record reaction start time. Temperature of
bend of material shall recover to 1100 °C±5°C within 5 min ~ 10 min after carbon dioxide
feeding starts.
6.7 Stop heating after reaction for 2 h. Cut off gas line of carbon dioxide and replace with
nitrogen; the flow is controlled at 2 L/min.
6.8 Sample cooling
6.8.1 When using high temperature resistance alloy steel reactor, unplug vent pipe and lift
reactor out of electric furnace; place on bracket and continue nitrogen feeding for cooling.
6.8.2 When using corundum reactor, reactor is still placed in furnace; naturally cool to
room temperature.
6.9 Stop nitrogen feeding when coke in reactor cools to 100 °C below. Open upper lid of
reactor and pour out the coke to weigh and record.
6.10 Place all coke after reaction into drum of type I; achieve total revolving of 30 min at a
revolving speed of 20 r/min. Total number of revolutions is 600 r. Take out and apply Φ10
mm round-hole screen; weigh oversize products and record.
6.11 Original data of test are r...
Get QUOTATION in 1-minute: Click GB/T 4000-2008
Historical versions: GB/T 4000-2008
Preview True-PDF (Reload/Scroll if blank)
GB/T 4000-2008: Coke -- Determination of reactivity and strength after reaction
GB/T 4000-2008
GB
NATIONAL STANDARD OF THE
PEOPLE’S REPUBLIC OF CHINA
ICS 75.160.10
H 32
Replacing GB/T 4000-1996
Coke - Determination of reactivity and strength
after reaction
ISSUED ON. AUGUST 19, 2008
IMPLEMENTED ON. APRIL 01, 2009
Issued by.
General Administration of Quality Supervision, Inspection
and Quarantine of the People’s Republic of China;
Standardization Administration of the People’s Republic of
China.
Table of Contents
Foreword ... 3
1 Scope ... 4
2 Normative references ... 4
3 Principles ... 4
4 Test instruments, apparatuses and materials ... 4
5 Sampling and sample preparation ... 12
6 Test procedures ... 12
7 Calculation of results ... 15
8 Degree of precision ... 15
Annex A ... 16
Annex B ... 18
Foreword
This Standard replaces GB/T 4000-1996 “Coke - Determination of Reactivity and Strength
after Reaction”.
Compared with GB/T 4000-1996, the main changes of this Standard are as follows.
— Preparation method of coke sample is revised as preparation method that jaw
crushing combines with hand finishing;
— Narrow the particle size control range of coke sample;
— Test apparatuses are improved to facilitate the maintenance.
Annex A and Annex B of this Standard are normative.
This Standard was proposed by China Iron and Steel Industry Association.
This Standard shall be under the jurisdiction of National Steel Standardization Technical
Committee.
Drafting organizations of this Standard. Wuhan Iron and Steel (Group) Corp., China
Metallurgical Information and Standardization Institute AND Shangyu HongXing
Machinery Instrument Manufacturing Co., Ltd.
Main drafters of this Standard. Sun Wei, Xi Wanze, Zhu Mingsan and Zhang Jinying.
The historical versions replaced by this Standard are as follows.
— GB 4000-1983, GB/T 4000-1996.
Coke - Determination of Reactivity and Strength after Reaction
1 Scope
This Standard specifies the principles of coke determination of reactivity and strength after
reaction, test instruments, apparatuses and materials, sampling and sample preparation,
test procedures, calculation of results and degree of precision.
This Standard applies to the determination of reactivity of coke for blast furnace iron
making and strength after reaction; coke for other purposes may refer to this Standard for
implementation.
2 Normative references
The articles contained in the following documents have become part of this document
when they are quoted herein. For the dated documents so quoted, all subsequent
modifications (including all corrections) or revisions made thereafter do not apply to this
Standard. However, the parties who reach an agreement according to this Standard are
encouraged to study whether the latest versions of these documents may be used. For
the undated documents so quoted, the latest versions (including all modification sheets)
apply to this document.
GB/T 1997 Coke - Sampling and preparation of samples
GB/T 2006 Coke for metallurgy - Determination of mechanical strength
3 Principles
Weigh a certain mass of coke sample and place into a reactor; use the percentage of coke
mass loss to express the coke reactivity (CRI), after 2 h of reaction with carbon dioxide at
1100°C±5°C.
After reaction, and after the revolving drum test of type I, use the mass fraction OF coke,
that is greater than 10 mm size, OVER the coke after reaction TO express the coke
strength after reaction (CSR).
4 Test instruments, apparatuses and materials
4.1 Electric furnace
Electric furnace heating wire, silicon carbide and other heating elements that can meet
may be adopted.
4.6 Φ precision temperature control device
Temperature control range is 0 °C~1 600 °C, precision grade is 0.5.
4.7 Round-hole screen
One for Φ10 mm, effective diameter of screen frame is 200 mm.
One for Φ23 mm, effective diameter of screen frame is 300 mm.
One for Φ25 mm and one for Φ3 mm, screen surface is 400 mm×500 mm, made
according to the provisions on round-hole screen in GB/T 2006.
4.8 Drying oven
Workshop capacity is not less than 0.07 m3.
Maximum operating temperature. 300 °C.
4.9 Balance
Maximum capacity is 500 g, sensitivity is 0.5 g.
4.10 Rhodium-platinum thermocouple
Diameter is 0.5 mm, length is 650 mm.
High-alumina thermocouple protection pipe A (Φ7 mmX5 mmX400 mm)
High-alumina dual-hole insulation pipe D (Φ4 mmX1 mmX400 mm)
High-alumina single-hole insulation pipe C (Φ1 mmX0.6 mmX10 mm)
4.11 Board
It is of high temperature resistance alloy steel (GH23 or GH44), thickness of 2 mm~5 mm
and diameter of 79 mm. Drill holes evenly with a uniform diameter of 3 mm and hole
interval is 5 mm.
4.12 High-alumina ball
Diameter is 20 mm.
4.13 Bracket
Bracket is shown in Figure 8, made of material Q235A. Material of three branch pipes is of
1Gr18Ni9Ti.
top of furnace; place into electric furnace; place asbestos board between bracket and
electric furnace lid for thermal insulation. Fill the surrounding of reactor flange with thermal
insulation material to reduce heat dissipation.
6.2.2 When using corundum reactor, load about one half of 200 g±0.5 g of prepared coke
samples; then insert into thermocouple sleeve; load another half of coke; make
thermocouple sleeve to pass the center hole in reactor lid; apply reactor lid. The
surrounding is filled with insulation materials to reduce heat dissipation.
6.3 Insert temperature thermocouple into reactor thermocouple sleeve (protected by
thermocouple high-alumina dual-hole insulation pipe and high-alumina thermocouple
protection pipe).
6.4 Respectively connect reactor intake pipe and vent pipe with gas supply system and
vent pipe. Check gas circuit to ensure tightness.
6.5 Switch on and adjust electric furnace for heating through precision temperature control
device. Rate of temperature increase is 8 °C/min~16 °C/min. When temperature at the
center of bed of material is up to 400 °C, feed nitrogen at a flow rate of 0.8 L/min to protect
coke and prevent burning.
6.6 When temperature at the center of bed of material reaches 1050 °C, switch on power
plug of carbon dioxide pressure reducing valve with preheating device; preheat the exit of
carbon dioxide gas cylinder to ensure stable outflow of carbon dioxide. When temperature
at the center of bend of material reaches 1100°C, stabilize for 10 min; cut off nitrogen and
replace with carbon dioxide at a flow of 5 L/min; record reaction start time. Temperature of
bend of material shall recover to 1100 °C±5°C within 5 min ~ 10 min after carbon dioxide
feeding starts.
6.7 Stop heating after reaction for 2 h. Cut off gas line of carbon dioxide and replace with
nitrogen; the flow is controlled at 2 L/min.
6.8 Sample cooling
6.8.1 When using high temperature resistance alloy steel reactor, unplug vent pipe and lift
reactor out of electric furnace; place on bracket and continue nitrogen feeding for cooling.
6.8.2 When using corundum reactor, reactor is still placed in furnace; naturally cool to
room temperature.
6.9 Stop nitrogen feeding when coke in reactor cools to 100 °C below. Open upper lid of
reactor and pour out the coke to weigh and record.
6.10 Place all coke after reaction into drum of type I; achieve total revolving of 30 min at a
revolving speed of 20 r/min. Total number of revolutions is 600 r. Take out and apply Φ10
mm round-hole screen; weigh oversize products and record.
6.11 Original data of test are r...
Share
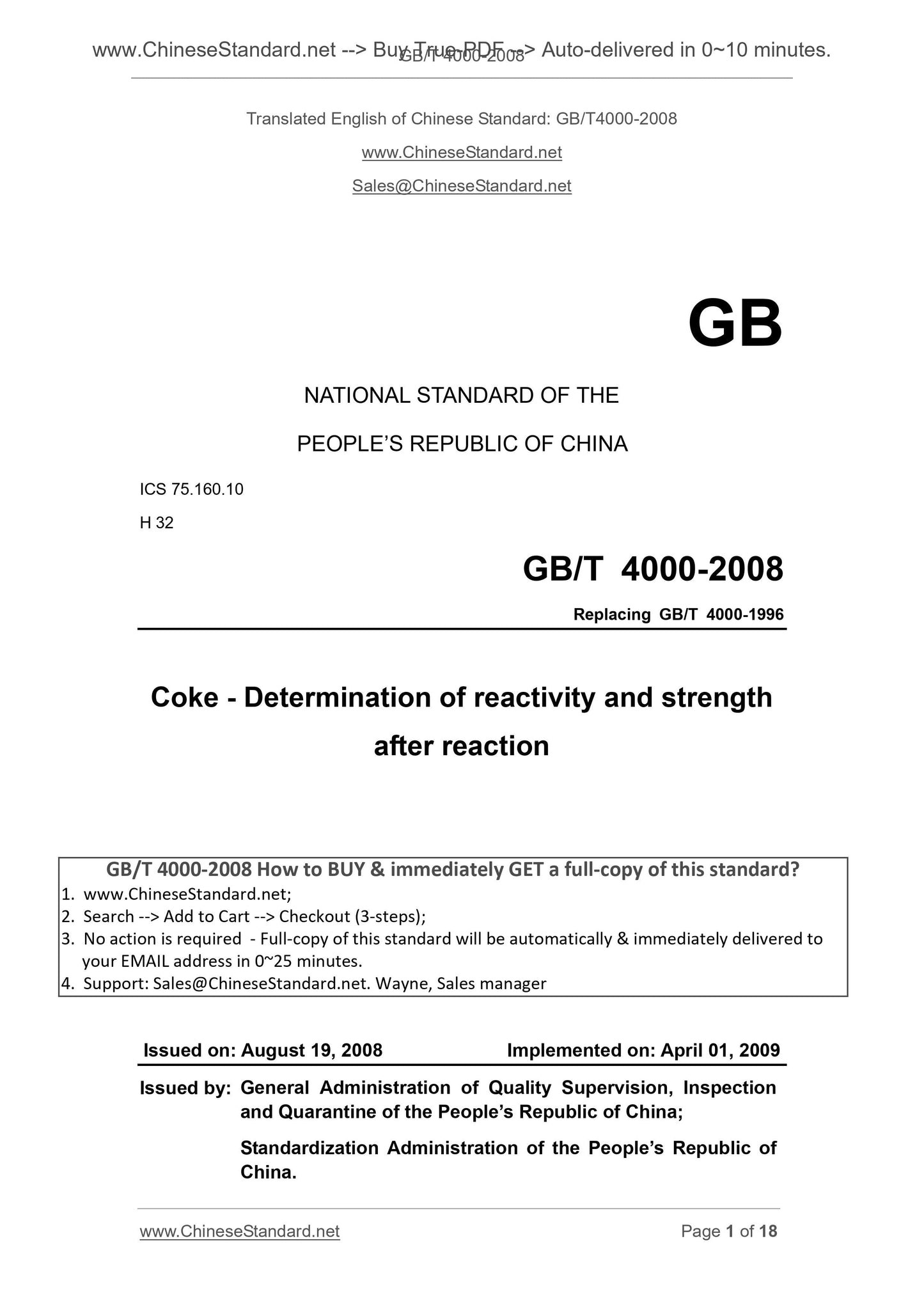
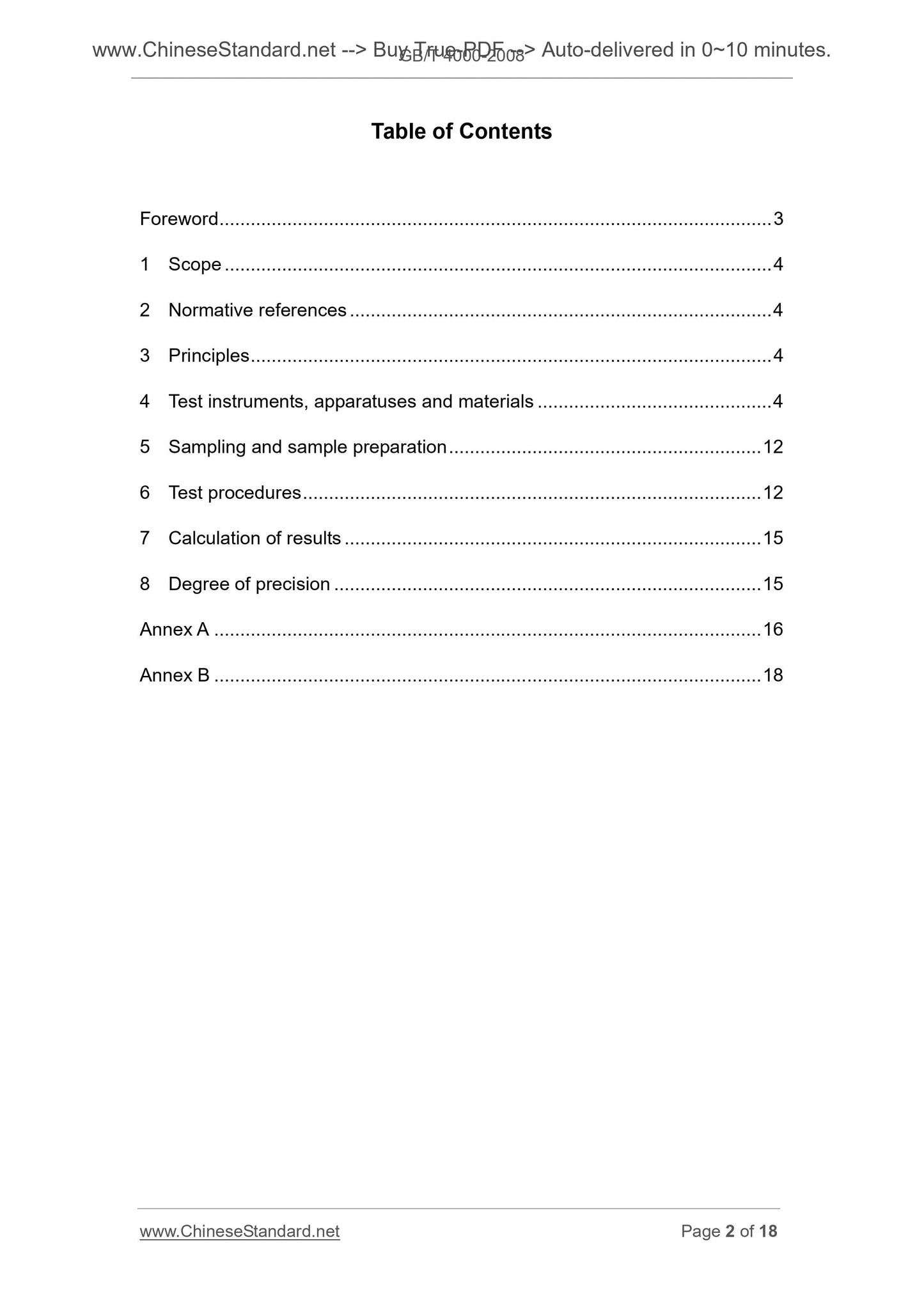
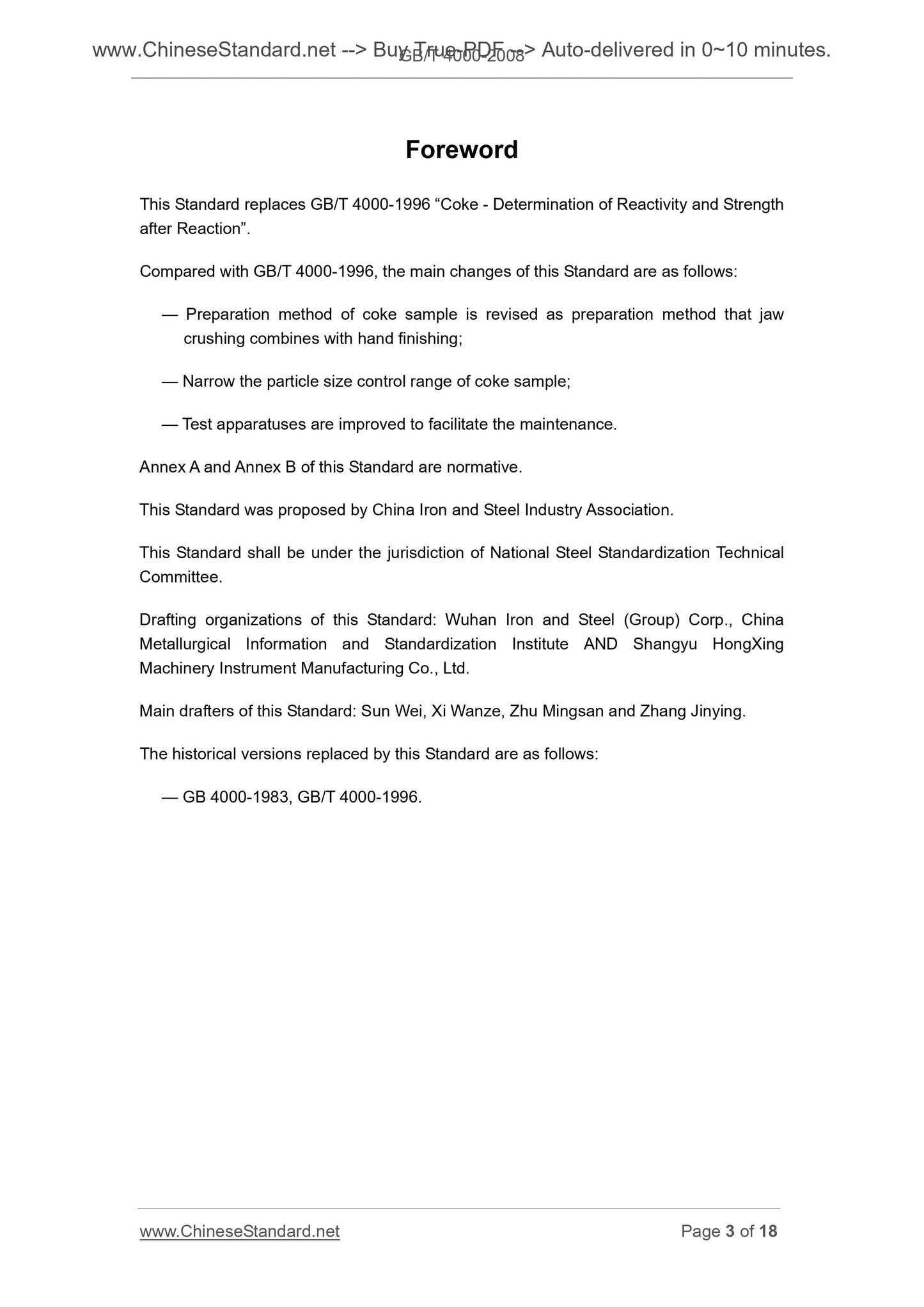
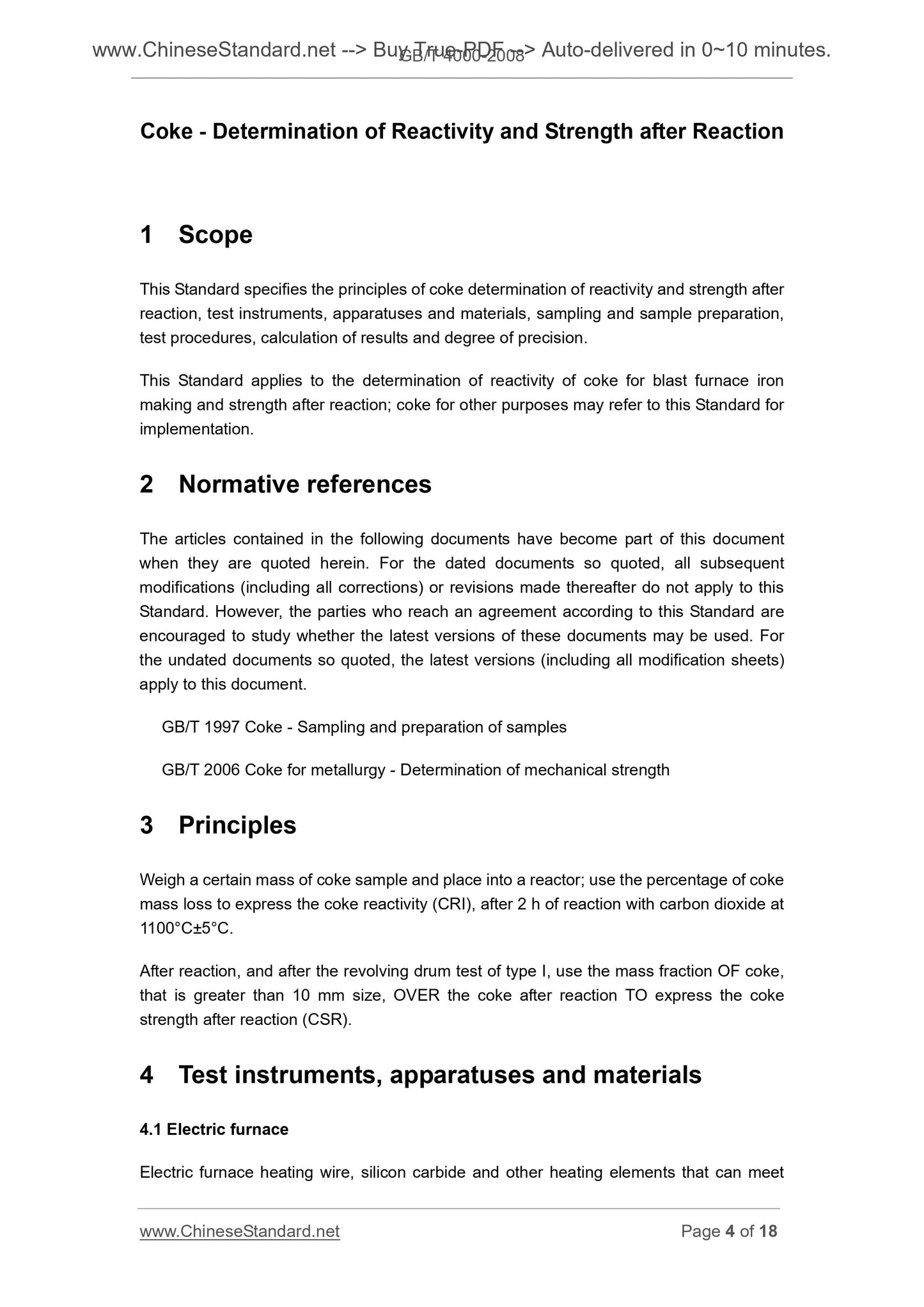
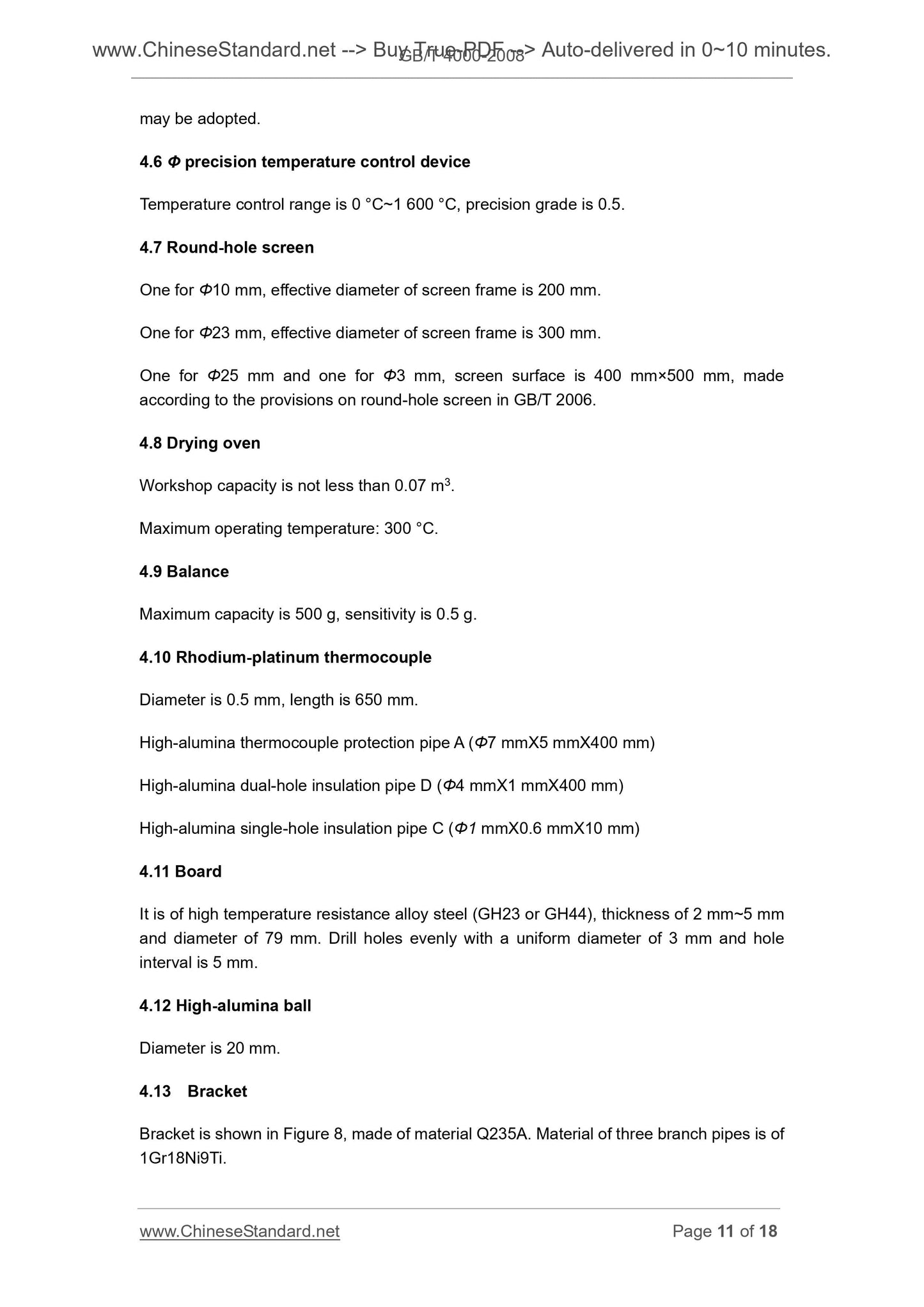
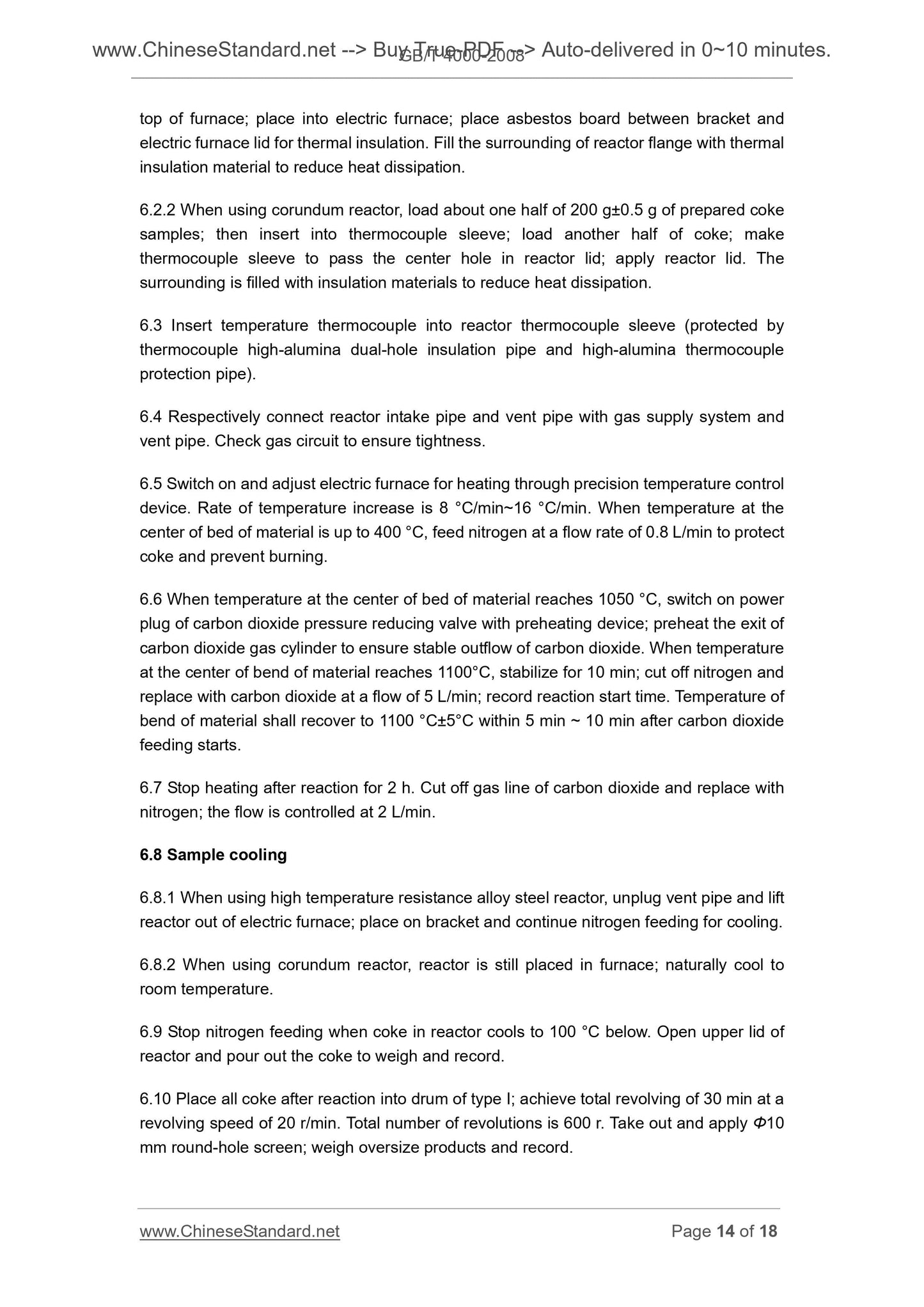
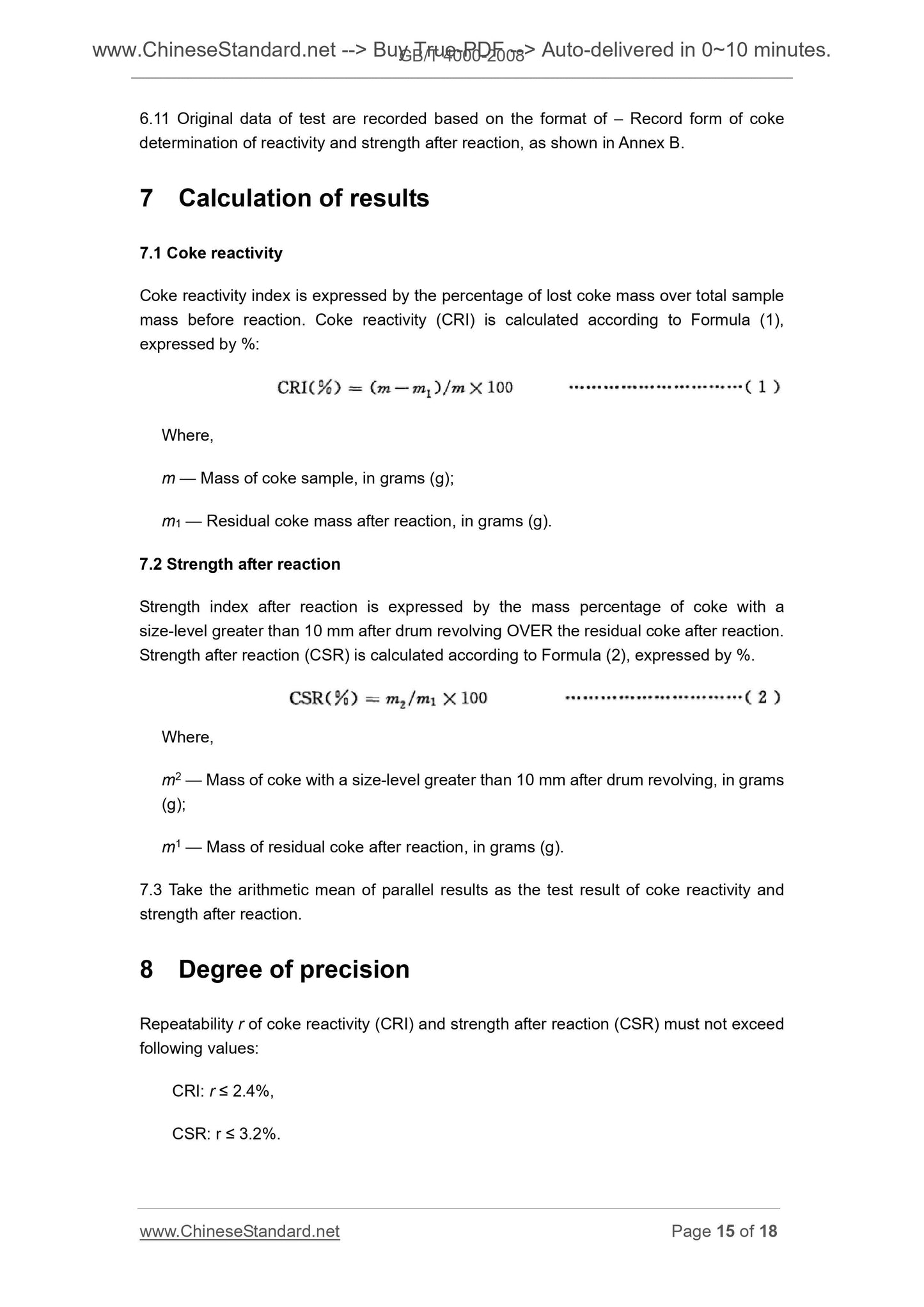
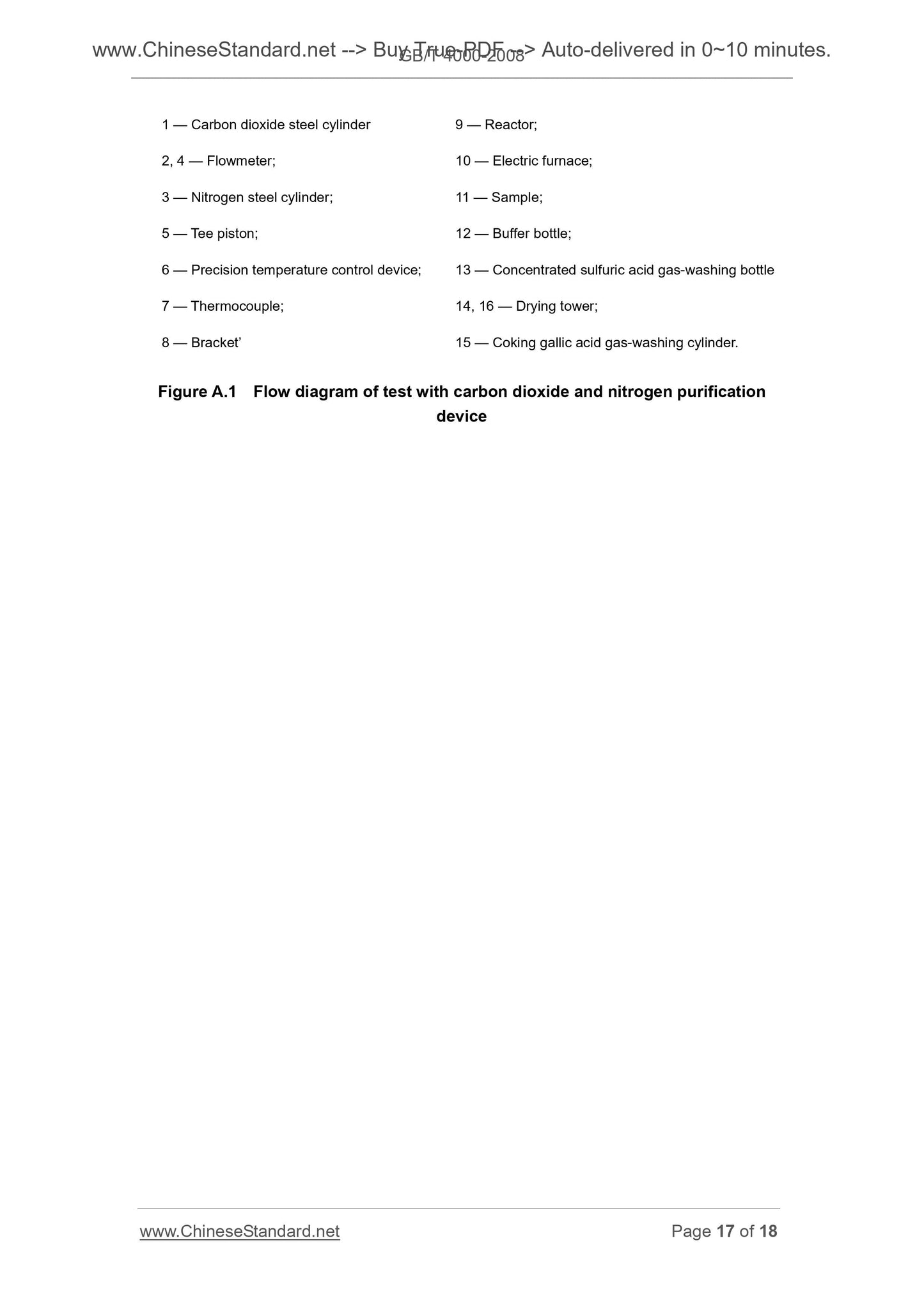
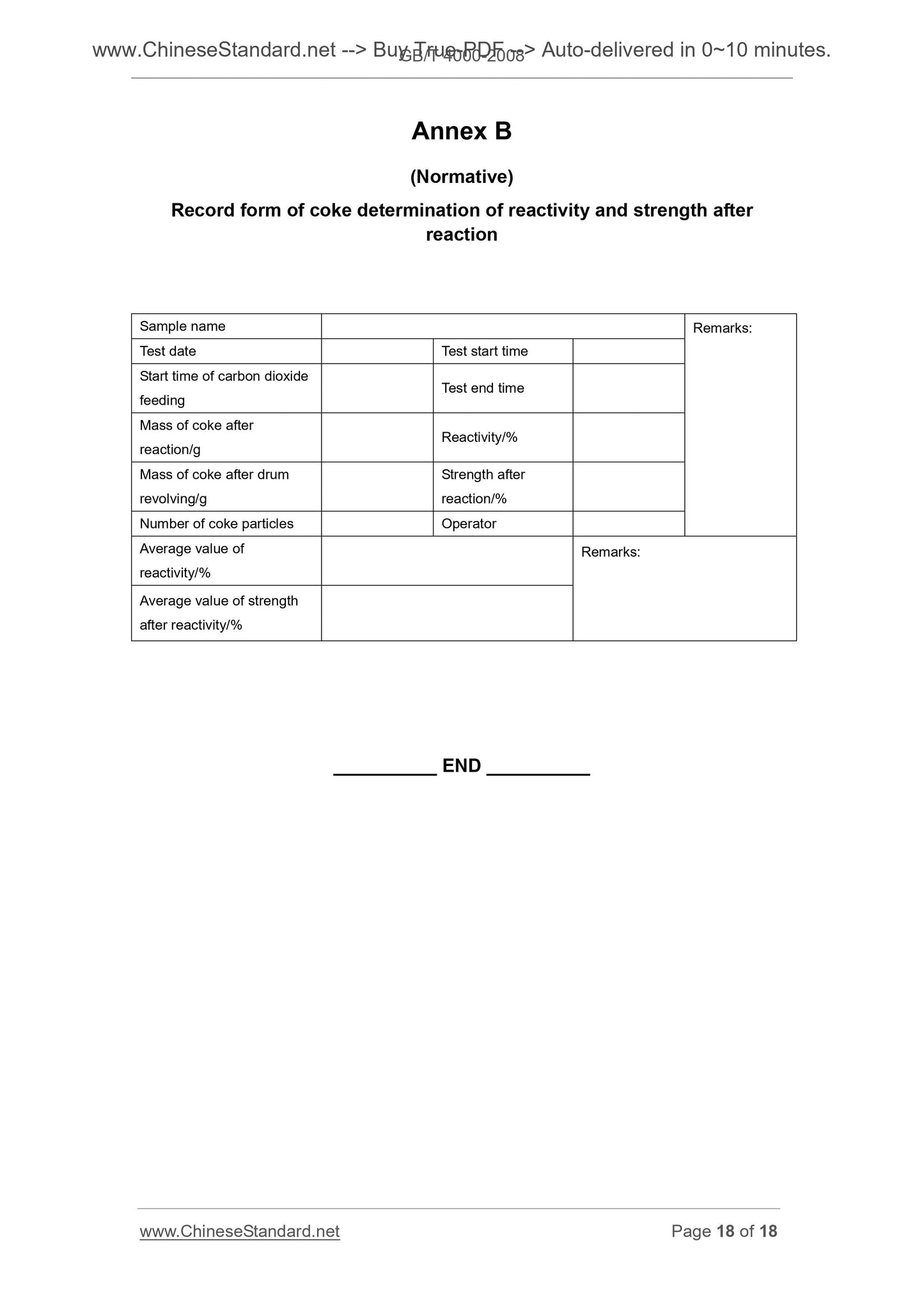