1
/
of
9
PayPal, credit cards. Download editable-PDF & invoice in 1 second!
GB/T 41295.4-2022 English PDF (GBT41295.4-2022)
GB/T 41295.4-2022 English PDF (GBT41295.4-2022)
Regular price
$170.00 USD
Regular price
Sale price
$170.00 USD
Unit price
/
per
Shipping calculated at checkout.
Couldn't load pickup availability
Delivery: 3 seconds. Download true-PDF + Invoice.
Get QUOTATION in 1-minute: Click GB/T 41295.4-2022
Historical versions: GB/T 41295.4-2022
Preview True-PDF (Reload/Scroll if blank)
GB/T 41295.4-2022: Application guide of functional safety - Part 4: Management and maintenance
GB/T 41295.4-2022
NATIONAL STANDARD OF THE
PEOPLE’S REPUBLIC OF CHINA
ICS 25.040
CCS N 10
Application guide of functional safety - Part 4: Management
and maintenance
ISSUED ON: MARCH 09, 2022
IMPLEMENTED ON: OCTOBER 01, 2022
Issued by: State Administration for Market Regulation;
Standardization Administration of the People’s Republic of China.
Table of Contents
Foreword ... 3
Introduction ... 4
1 Scope ... 5
2 Normative references ... 5
3 Terms and definitions... 5
4 Abbreviations ... 6
5 General ... 6
6 Documentation ... 7
7 Personnel ... 7
8 Change management and configuration management ... 8
9 Safety management of operation and maintenance process ... 8
References ... 15
Application guide of functional safety - Part 4: Management
and maintenance
1 Scope
This document specifies the safety management and maintenance activities for the
functional safety system to achieve the corresponding safety integrity level, including
documentation, personnel, change management, inspection and testing of the
maintenance process.
This document applies to relevant management and maintenance activities from the
installation, commissioning to normal operation of functional safety systems.
2 Normative references
The following documents, in whole or in part, are normatively referenced in this
document and are indispensable for its application. For dated references, only the
version corresponding to that date is applicable to this document; for undated references,
the latest version (including all amendments) is applicable to this document.
GB/T 20438.4-2017, Functional safety of electrical/electronic/programmable
electronic safety-related systems - Part 4: Definitions and abbreviations
3 Terms and definitions
Terms and definitions determined by GB/T 20438.4-2017, and the following ones are
applicable to this document.
3.1
functional safety system
A system that performs safety-related functions, has functional safety-related
characteristics, and satisfies a specific Safety Integrity Level (SIL).
Note: The system here is a generalized concept that includes different levels, such as
safety components, safety equipment or safety control systems. In an actual
industrial process, the functional safety system may be a transmitter, a relay, a
safety programmable controller or a safety instrumented system.
[Source: GB/T 41295.1-2022, 3.6]
3.2
team for functional safety system research and development
The liability subject for the design and development of functional safety systems.
Note: Including functional safety system hardware developers, software developers,
verification testers, safety managers, etc.
[Source: GB/T 41295.2-2022, 3.2]
3.3
team for functional safety system maintenance
The liability subject for the maintenance of functional safety systems.
Note: Including inspection and testing personnel, change management personnel, daily
inspection personnel, and accessories replacement personnel for the functional
safety system.
3.4
offline test
Testing activities carried out when the controlled equipment is in a safe state.
4 Abbreviations
The following abbreviations apply to this document.
HAZOP: Hazard and Operability
HMI: Human Machine Interface
LOPA: Layer Of Protection Analysis
PFDavg: Average Probability of Dangerous Failure on Demand
PFH: Average Frequency of Dangerous Failure Per Hour
SIL: Safety Integrity Level
SRS: Safety Requirement Specification
5 General
5.1 Organizations engaged in the installation, commissioning and formal operation of
functional safety systems need to consider establishing a functional safety management
7.3 Clearly define the scope, responsibilities, required competencies (i.e., training,
technical knowledge, experience and qualifications) and limitations of each person
engaged in safety activities.
7.4 Consideration should be given to regulations and limitations on the competence of
personnel to perform specific functional safety activities, including:
-- All personnel have received functional safety training from professional
institutions and are qualified to be engaged in functional safety activities;
-- The team leader has experience in relevant projects and has an in-depth
understanding of functional safety standards and technologies;
-- All personnel are regular trained to keep abreast of the latest functional safety
standards and technological advances.
7.5 An appropriate communication mechanism should be established between
personnel in different positions.
8 Change management and configuration management
8.1 Appropriate configuration management and change control procedures shall be
ensured.
8.2 Build a configuration item that meets the requirements of a specific project. The
configuration item should cover all software and hardware entities and documents that
may affect the safety integrity level.
8.3 It shall be ensured that the required safety integrity in the event of a change is
continuously met. This includes performing an impact analysis and developing an
appropriate test plan for the change.
8.4 It shall be ensured that an appropriate change approval mechanism exists and that
unauthorized changes are not implemented.
8.5 The configuration management system shall ensure that the configuration status and
version of all configuration items are identified.
8.6 A standardized system should be used to ensure that all items under the
configuration can be individually identified.
9 Safety management of operation and maintenance process
9.1 General
The core goal of functional safety maintenance and management is to ensure that the
SIL capability required by the functional safety system during field operation is not
reduced. The reasons for the reduction of SIL capability may include:
a) Due to improper manual installation and commissioning, the functional safety
system has potential defects from the beginning of operation, and not all the
expected safety functions can be achieved (systematic capabilities are not
satisfied);
b) Failure to perform fault handling, repair and replacement, etc. as required by the
system due to improper maintenance activities;
c) The hardware of the system (including data transmission and soft errors) has a
higher failure rate than expected due to environmental or human factors
(hardware safety integrity is not satisfied);
d) Appropriate inspection tests are not performed during the maintenance process,
including the inspection test cycle being too long or the inspection test content
being insufficient.
The contents of a) and b) need to be ensured using appropriate functional safety
management and pre-operational acceptance testing. To avoid the occurrence of c) and
d), the contents of 9.2 ~ 9.4 need to be considered.
9.2 Online safety analysis of operation process
9.2.1 Consider carrying out on-site failure analysis and online safety management of
functional safety systems during maintenance.
9.2.2 During the operation of the functional safety system, the on-site operation and
maintenance personnel need to record the failures of the functional safety system.
9.2.3 Special recording tools should be used for automatic fault statistics. The automatic
recording tool can realize the automatic acquisition, aggregation, classification and
display of the failure information of each component of the functional safety system
through the...
Get QUOTATION in 1-minute: Click GB/T 41295.4-2022
Historical versions: GB/T 41295.4-2022
Preview True-PDF (Reload/Scroll if blank)
GB/T 41295.4-2022: Application guide of functional safety - Part 4: Management and maintenance
GB/T 41295.4-2022
NATIONAL STANDARD OF THE
PEOPLE’S REPUBLIC OF CHINA
ICS 25.040
CCS N 10
Application guide of functional safety - Part 4: Management
and maintenance
ISSUED ON: MARCH 09, 2022
IMPLEMENTED ON: OCTOBER 01, 2022
Issued by: State Administration for Market Regulation;
Standardization Administration of the People’s Republic of China.
Table of Contents
Foreword ... 3
Introduction ... 4
1 Scope ... 5
2 Normative references ... 5
3 Terms and definitions... 5
4 Abbreviations ... 6
5 General ... 6
6 Documentation ... 7
7 Personnel ... 7
8 Change management and configuration management ... 8
9 Safety management of operation and maintenance process ... 8
References ... 15
Application guide of functional safety - Part 4: Management
and maintenance
1 Scope
This document specifies the safety management and maintenance activities for the
functional safety system to achieve the corresponding safety integrity level, including
documentation, personnel, change management, inspection and testing of the
maintenance process.
This document applies to relevant management and maintenance activities from the
installation, commissioning to normal operation of functional safety systems.
2 Normative references
The following documents, in whole or in part, are normatively referenced in this
document and are indispensable for its application. For dated references, only the
version corresponding to that date is applicable to this document; for undated references,
the latest version (including all amendments) is applicable to this document.
GB/T 20438.4-2017, Functional safety of electrical/electronic/programmable
electronic safety-related systems - Part 4: Definitions and abbreviations
3 Terms and definitions
Terms and definitions determined by GB/T 20438.4-2017, and the following ones are
applicable to this document.
3.1
functional safety system
A system that performs safety-related functions, has functional safety-related
characteristics, and satisfies a specific Safety Integrity Level (SIL).
Note: The system here is a generalized concept that includes different levels, such as
safety components, safety equipment or safety control systems. In an actual
industrial process, the functional safety system may be a transmitter, a relay, a
safety programmable controller or a safety instrumented system.
[Source: GB/T 41295.1-2022, 3.6]
3.2
team for functional safety system research and development
The liability subject for the design and development of functional safety systems.
Note: Including functional safety system hardware developers, software developers,
verification testers, safety managers, etc.
[Source: GB/T 41295.2-2022, 3.2]
3.3
team for functional safety system maintenance
The liability subject for the maintenance of functional safety systems.
Note: Including inspection and testing personnel, change management personnel, daily
inspection personnel, and accessories replacement personnel for the functional
safety system.
3.4
offline test
Testing activities carried out when the controlled equipment is in a safe state.
4 Abbreviations
The following abbreviations apply to this document.
HAZOP: Hazard and Operability
HMI: Human Machine Interface
LOPA: Layer Of Protection Analysis
PFDavg: Average Probability of Dangerous Failure on Demand
PFH: Average Frequency of Dangerous Failure Per Hour
SIL: Safety Integrity Level
SRS: Safety Requirement Specification
5 General
5.1 Organizations engaged in the installation, commissioning and formal operation of
functional safety systems need to consider establishing a functional safety management
7.3 Clearly define the scope, responsibilities, required competencies (i.e., training,
technical knowledge, experience and qualifications) and limitations of each person
engaged in safety activities.
7.4 Consideration should be given to regulations and limitations on the competence of
personnel to perform specific functional safety activities, including:
-- All personnel have received functional safety training from professional
institutions and are qualified to be engaged in functional safety activities;
-- The team leader has experience in relevant projects and has an in-depth
understanding of functional safety standards and technologies;
-- All personnel are regular trained to keep abreast of the latest functional safety
standards and technological advances.
7.5 An appropriate communication mechanism should be established between
personnel in different positions.
8 Change management and configuration management
8.1 Appropriate configuration management and change control procedures shall be
ensured.
8.2 Build a configuration item that meets the requirements of a specific project. The
configuration item should cover all software and hardware entities and documents that
may affect the safety integrity level.
8.3 It shall be ensured that the required safety integrity in the event of a change is
continuously met. This includes performing an impact analysis and developing an
appropriate test plan for the change.
8.4 It shall be ensured that an appropriate change approval mechanism exists and that
unauthorized changes are not implemented.
8.5 The configuration management system shall ensure that the configuration status and
version of all configuration items are identified.
8.6 A standardized system should be used to ensure that all items under the
configuration can be individually identified.
9 Safety management of operation and maintenance process
9.1 General
The core goal of functional safety maintenance and management is to ensure that the
SIL capability required by the functional safety system during field operation is not
reduced. The reasons for the reduction of SIL capability may include:
a) Due to improper manual installation and commissioning, the functional safety
system has potential defects from the beginning of operation, and not all the
expected safety functions can be achieved (systematic capabilities are not
satisfied);
b) Failure to perform fault handling, repair and replacement, etc. as required by the
system due to improper maintenance activities;
c) The hardware of the system (including data transmission and soft errors) has a
higher failure rate than expected due to environmental or human factors
(hardware safety integrity is not satisfied);
d) Appropriate inspection tests are not performed during the maintenance process,
including the inspection test cycle being too long or the inspection test content
being insufficient.
The contents of a) and b) need to be ensured using appropriate functional safety
management and pre-operational acceptance testing. To avoid the occurrence of c) and
d), the contents of 9.2 ~ 9.4 need to be considered.
9.2 Online safety analysis of operation process
9.2.1 Consider carrying out on-site failure analysis and online safety management of
functional safety systems during maintenance.
9.2.2 During the operation of the functional safety system, the on-site operation and
maintenance personnel need to record the failures of the functional safety system.
9.2.3 Special recording tools should be used for automatic fault statistics. The automatic
recording tool can realize the automatic acquisition, aggregation, classification and
display of the failure information of each component of the functional safety system
through the...
Share
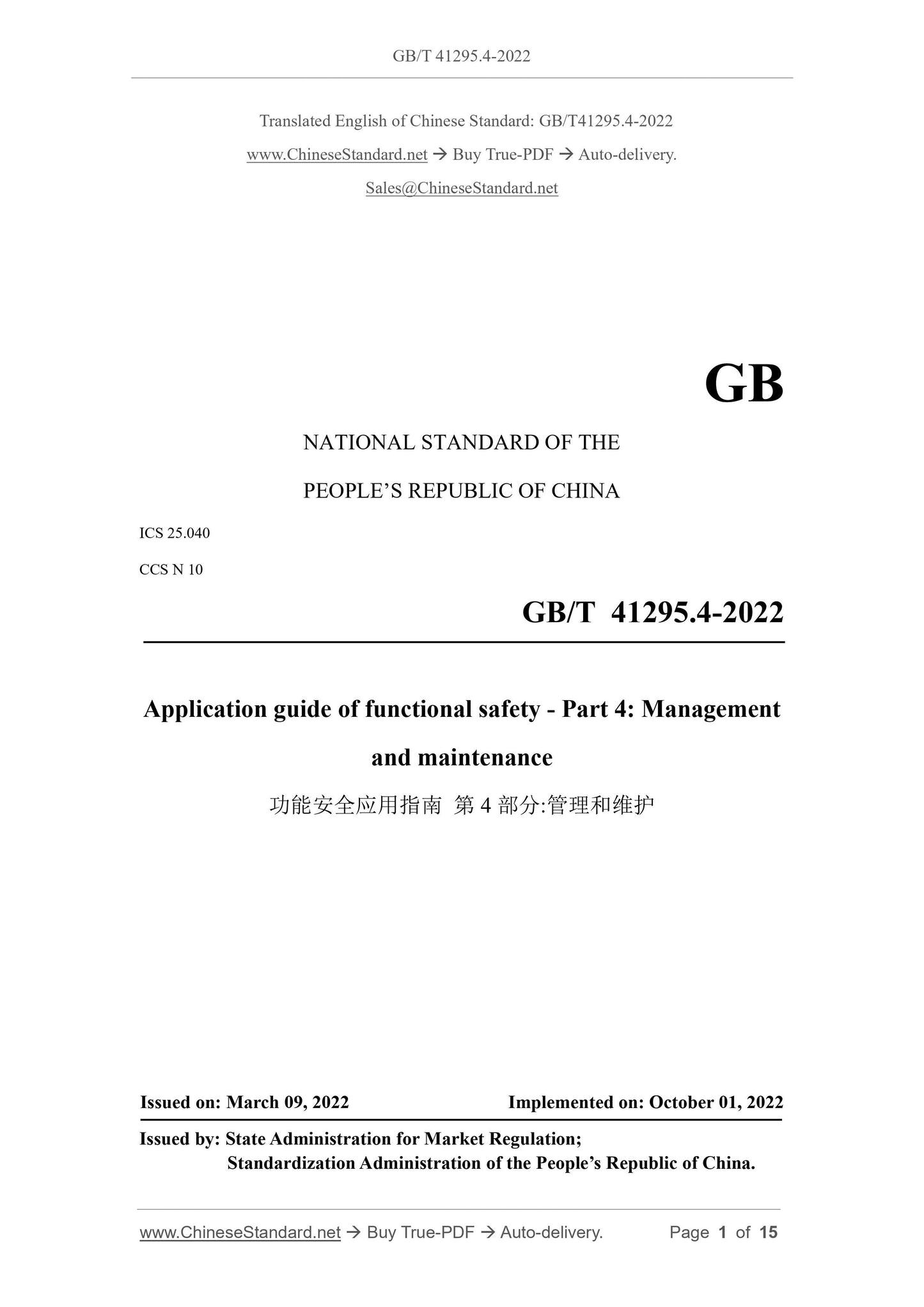
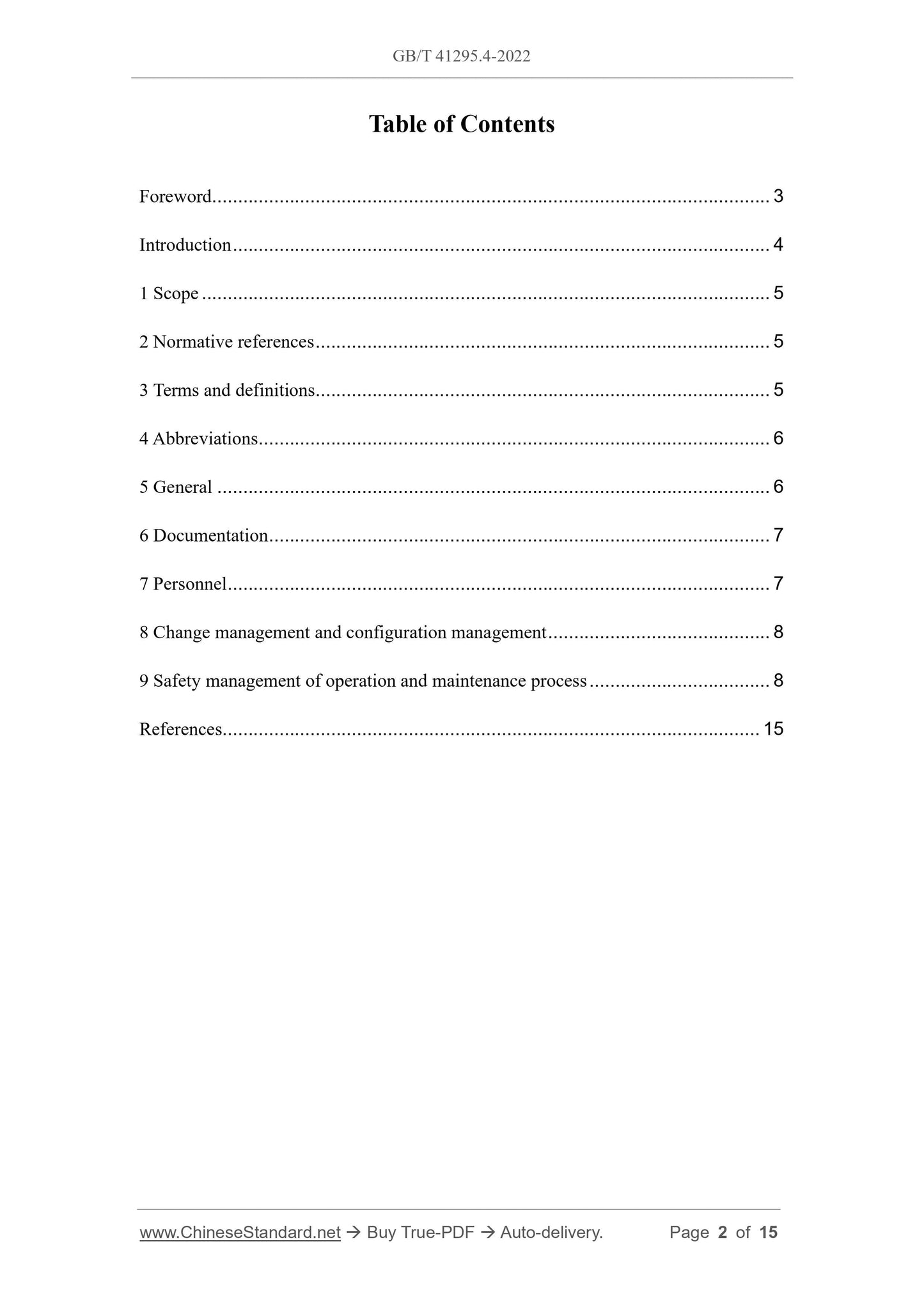
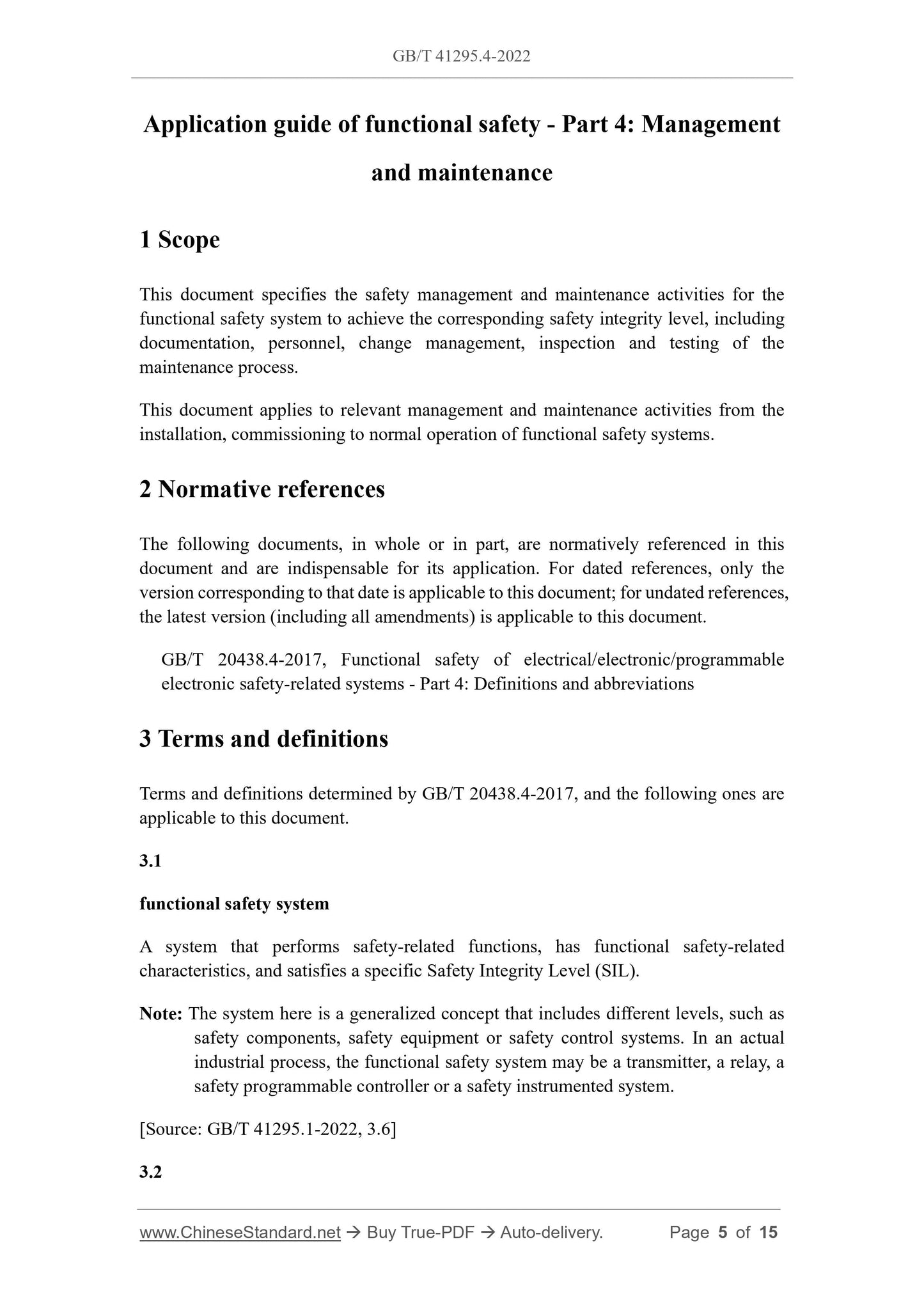
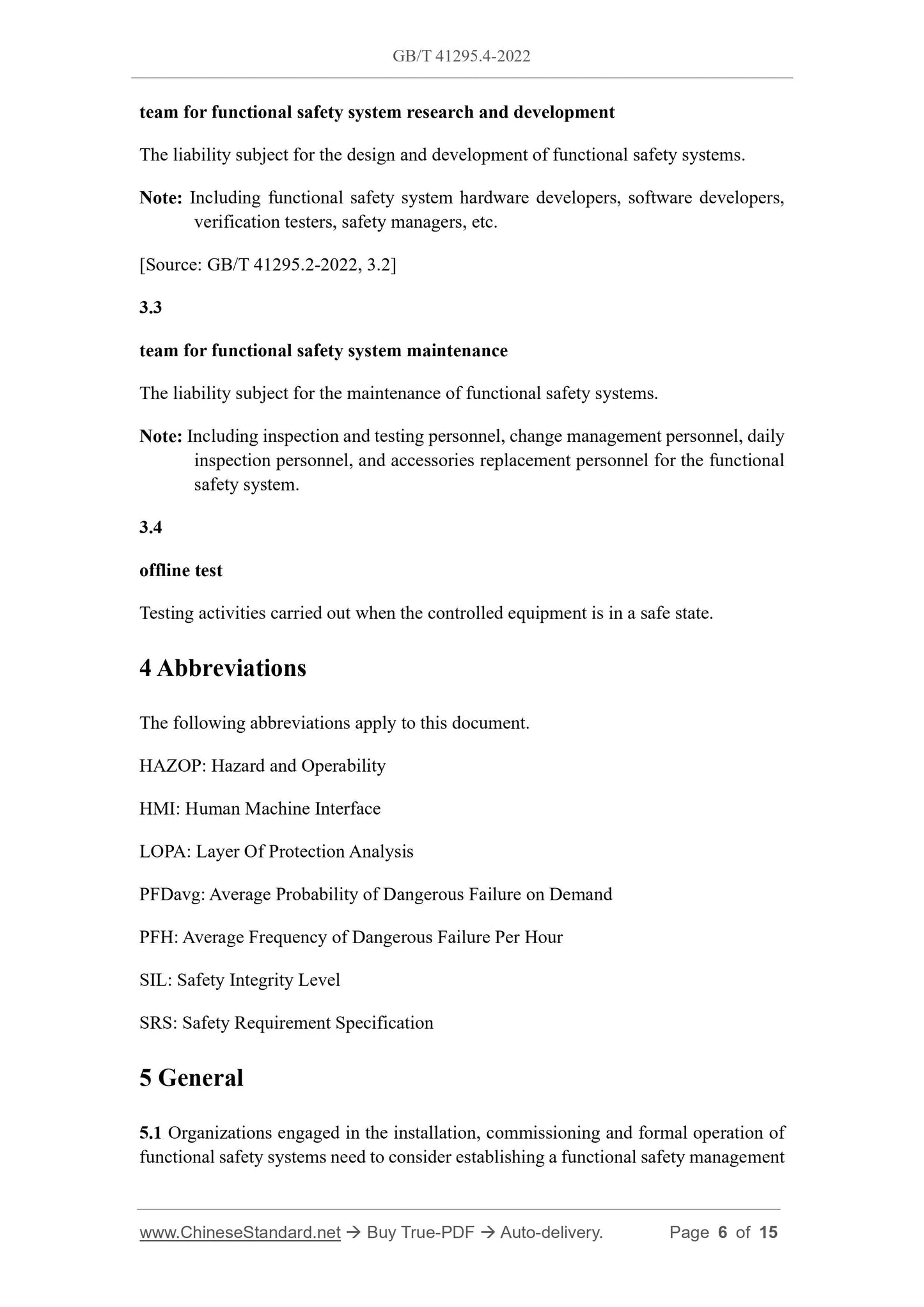
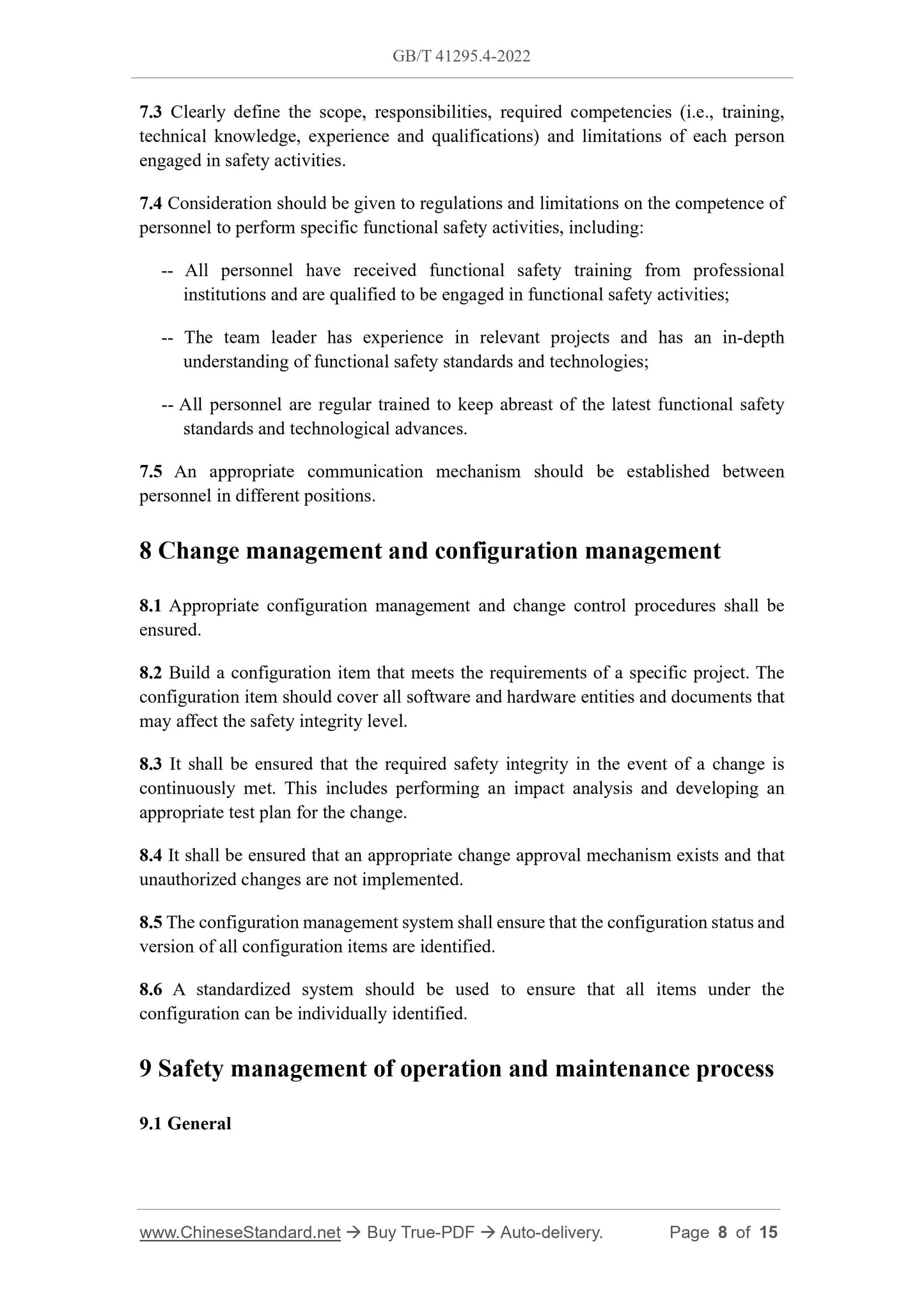
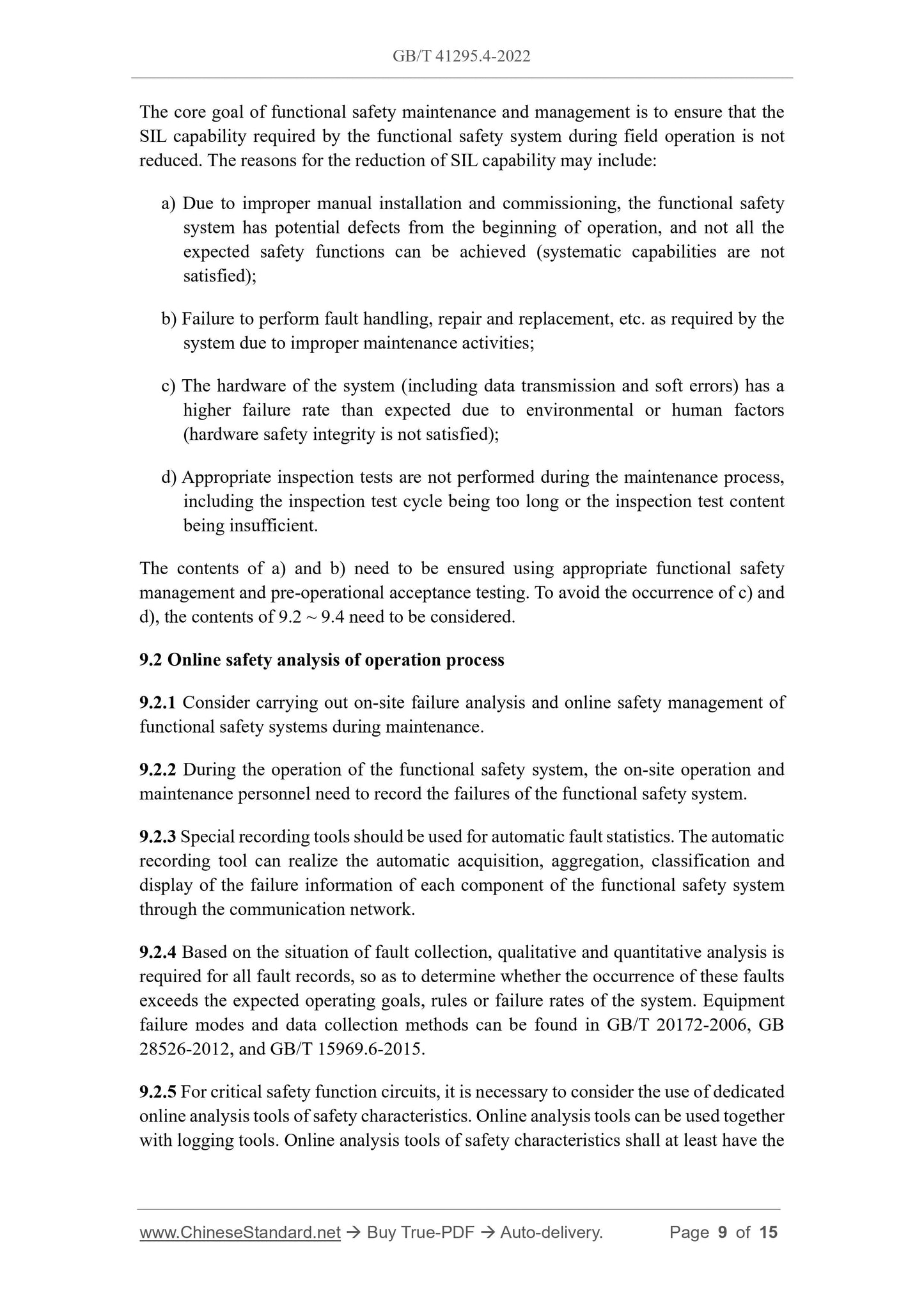
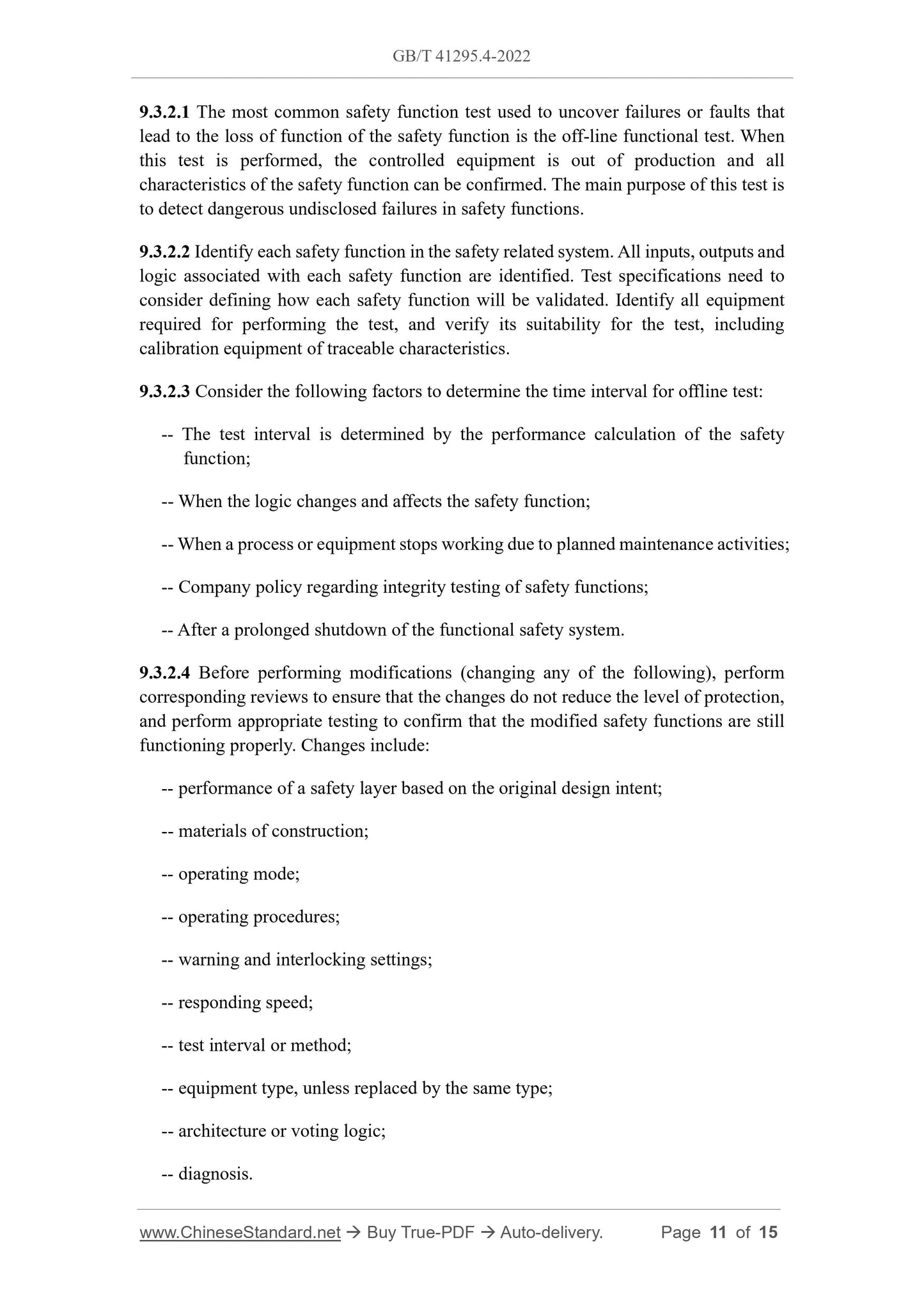
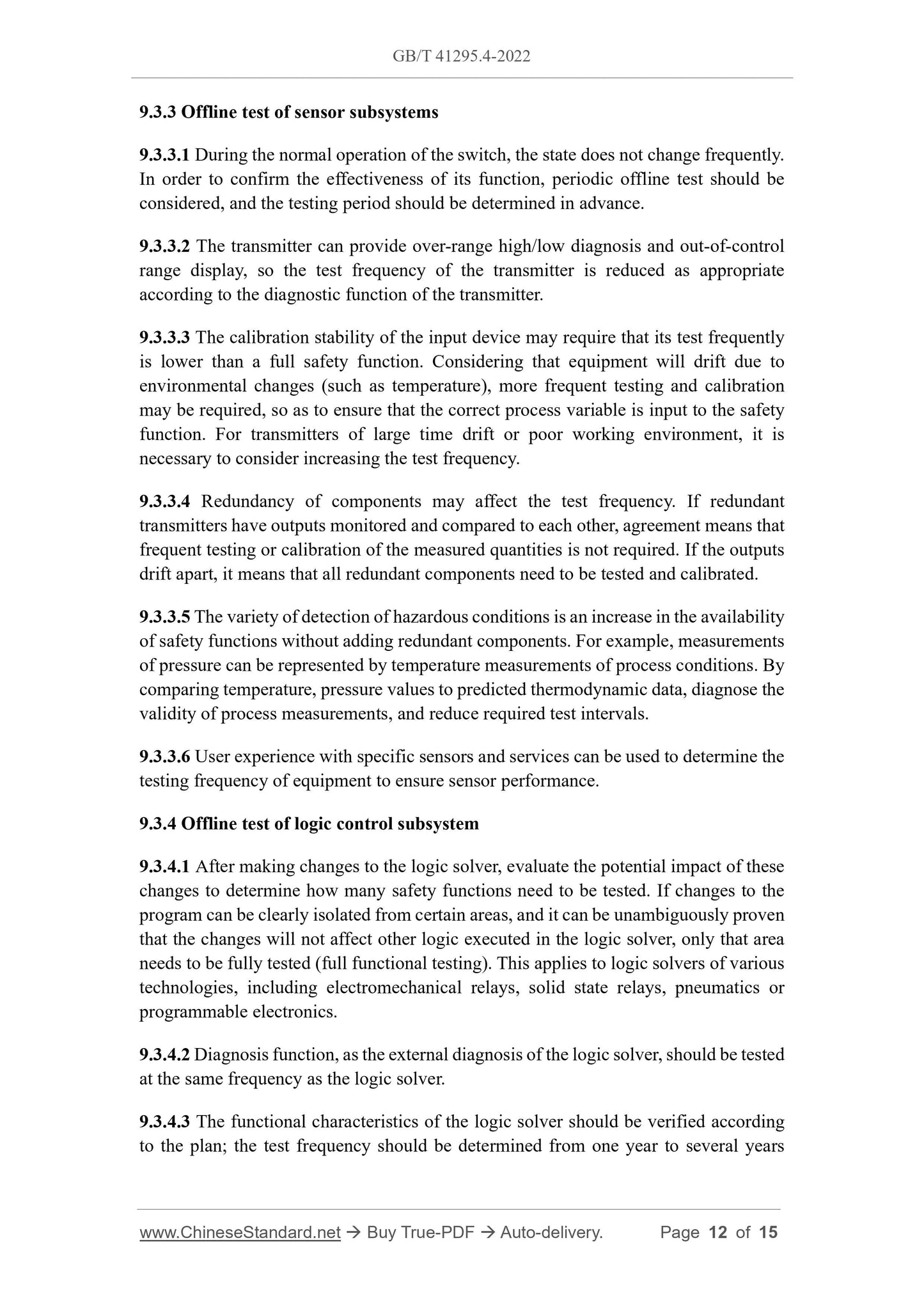
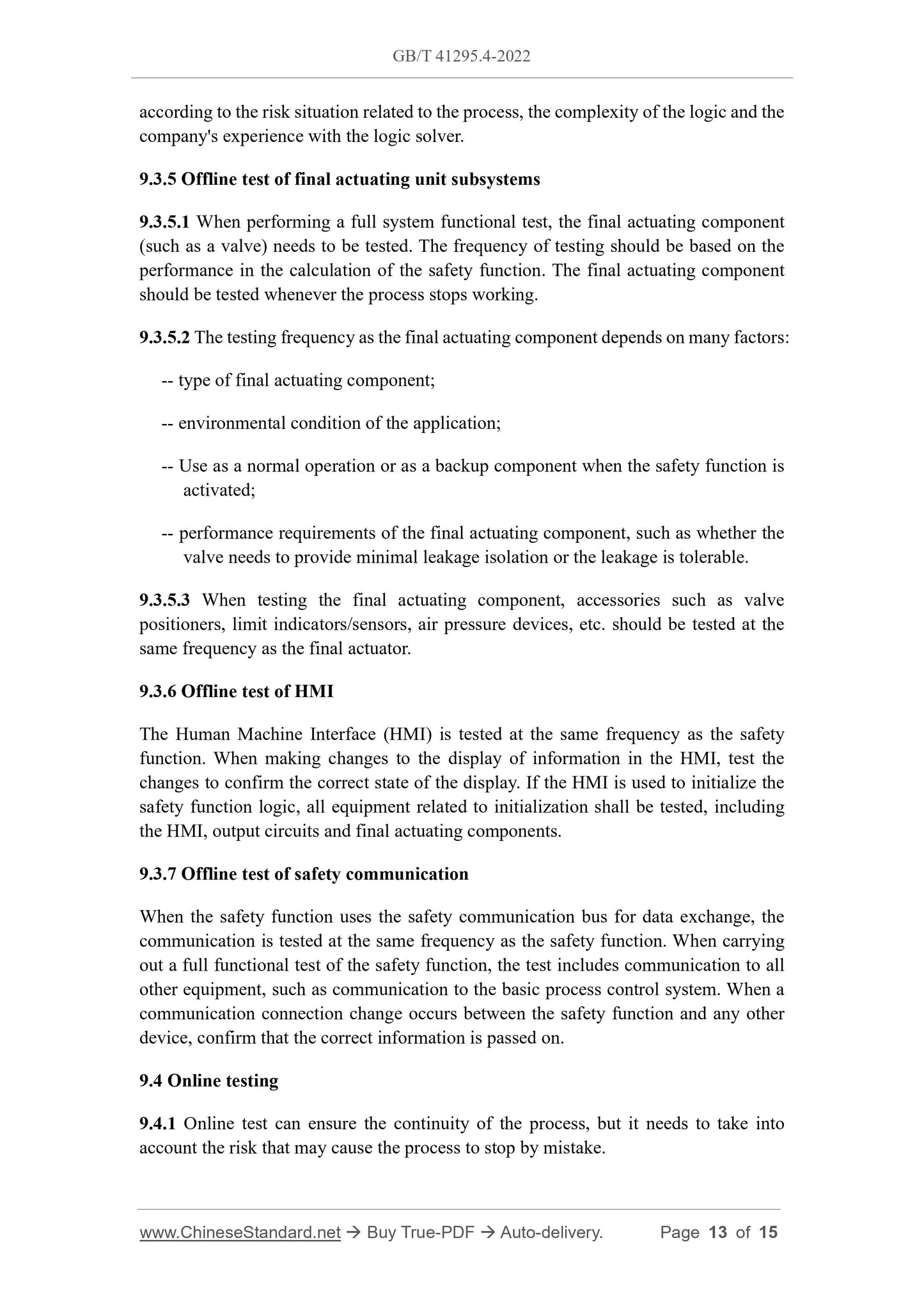