1
/
of
12
PayPal, credit cards. Download editable-PDF and invoice in 1 second!
GB/T 4146.3-2011 English PDF (GBT4146.3-2011)
GB/T 4146.3-2011 English PDF (GBT4146.3-2011)
Regular price
$165.00 USD
Regular price
Sale price
$165.00 USD
Unit price
/
per
Shipping calculated at checkout.
Couldn't load pickup availability
Delivery: 3 seconds. Download true-PDF + Invoice.
Get Quotation: Click GB/T 4146.3-2011 (Self-service in 1-minute)
Historical versions (Master-website): GB/T 4146.3-2011
Preview True-PDF (Reload/Scroll-down if blank)
GB/T 4146.3-2011: Textiles - Man-Made Fibers - Part 3: Terms of Inspection
GB/T 4146.3-2011
Textiles - Man-made fibers - Part 3.Terms of inspection
ICS 59.060.20
W50
National Standards of People's Republic of China
Textile chemical fiber
Part 3.Test terminology
2011-06-16 released
2011-12-01 implementation
General Administration of Quality Supervision, Inspection and Quarantine of the People's Republic of China
Issued by China National Standardization Administration
Table of contents
Foreword Ⅰ
1 Scope 1
2 Test term 1
2.1 General chemical fiber inspection terms 1
2.2 Chemical fiber sampling inspection term 1
2.3 Terms for chemical fiber linear density inspection 2
2.4 Chemical fiber length inspection term 2
2.5 Terminology for testing tensile properties of chemical fibers 3
2.6 Chemical fiber crimping/crimping performance test term 6
2.7 Terminology for testing the thermal shrinkage rate of chemical fibers 7
2.8 Terminology for the twist test of chemical fiber filament 7
2.9 Terminology for testing chemical fiber filament network degree 8
2.10 Chemical fiber elastic fiber inspection term 8
2.11 Terminology for quality difference inspection 9
2.12 Visual inspection terms 10
2.13 Terminology for defect inspection 11
2.14 Other fiber inspection terms 12
2.15 Inspection terms for chemical fiber raw materials 14
3 Statistical Test Terms 16
Chinese Index 17
English Correspondence Index 21
Textile chemical fiber
Part 3.Test terminology
1 Scope
This part of GB/T 4146 specifies the inspection terms for textile chemical fibers and their raw materials.
This part is suitable for the exchange of concepts in the production, use, commerce, scientific research, and teaching of chemical fibers.
2 Test term
2.1 General chemical fiber inspection terms
2.1.1
Standard atmosphere
An environment in which relative humidity and temperature are controlled, and textiles are subjected to humidity conditioning and testing under this environmental temperature and humidity.
2.1.2
Relative humidity
Under the same temperature and pressure conditions, the ratio of the actual pressure of water vapor in the atmosphere to the pressure of saturated water vapor, expressed as a percentage.
2.1.3
Pre-conditioning
A treatment in which the sample or specimen is adjusted to a moisture regain lower than the predetermined moisture before the humidity is adjusted in the test standard atmosphere.
2.1.4
Humidity control
A treatment in which the sample or specimen is placed in the test standard atmosphere for a certain period of time to reach the moisture absorption equilibrium.
2.1.5
Humidity balance
The moisture absorption and moisture release of textile fiber reach a balance, and the change of its quality tends to zero.
2.1.6
Gauge length
The distance between the two effective clamping points (lines) that clamp the sample on the test device.
2.1.7
Initial length
Under the specified pretension, the distance between the two effective clamping points (lines) holding the sample on the test device.
2.1.8
Tension
The force that causes the fiber to elongate.
Note. tension is the abbreviation of tensioningforce. In fibers and yarns, tension is usually applied according to the linear density of the fiber.
2.1.9
Pretension
To make the sample straight, the force applied to the sample before the start of the test.
2.2 Terms for chemical fiber sampling and inspection
2.2.1
Rolled wire
In order to facilitate processing, storage and transportation, several lengths of chemical fiber rolls are packed into suitable forms. The package form has "unsupported" (such as
Hank yarn) and "supported" (such as cheese yarn, paper bobbin yarn). Referred to as roll.
2.2.2
According to different purposes, the unit of counting divided by product raw materials, production technology, etc.
2.2.3
Batch sample
Can represent the entire batch of packages (or samples), the sum of packages (or samples) used to extract laboratory samples.
2.2.4
Production batch
The raw and auxiliary fibers, process conditions and product specifications are the same, and are continuously produced within a certain period of time.
2.2.5
Inspection lot
In order to check the quality and stability of the production batch products, products determined periodically or according to production conditions are used.
2.2.6
Laboratory samples
The product unit or part of the fiber taken from the batch sample according to the regulations is used as the source of the test sample.
2.2.7
Sample
The part taken from a laboratory sample for testing.
2.3 Terms for chemical fiber linear density inspection
2.3.1
Linear density
The mass per unit length of fiber or yarn.
2.3.2
Nominal linear density
The linear density mentioned in the sales document (contract, invoice, etc.).
2.3.3
Linear density deviation rate
The percentage of the difference between the measured linear density and the nominal linear density of chemical fiber to the nominal linear density.
2.3.4
Te [x]
A unit that expresses linear density, which is the mass grams per kilometer of fiber. Commonly used unit tex or dtex, 1tex=10dtex.
2.3.5
Number of filaments
The number of monofilaments included in a multifilament formed by a porous spinneret.
2.3.6
Single filament number deviation rate
The percentage of the difference between the number of spinneret holes forming a multifilament and the actual number of single filaments to the number of spinneret holes.
2.4 Chemical fiber length inspection term
2.4.1
Nominal length
The fiber length mentioned in the sales document (contract, invoice, etc.).
2.4.2
Length deviation rate
The percentage of the difference between the measured length of chemical short fibers and the nominal length to the nominal length.
2.4.3
Viscose staple fiber boundary
In the length distribution of viscose staple fiber, the length limit is set for the staple fiber that is not conducive to spinning. When the nominal length is less than 50mm, short
The fiber limit is 20mm; when the nominal length is greater than or equal to 50mm, the short fiber limit is 30mm.
2.4.4
Super long fiber
Cut fibers that are larger than the super-length limit but less than twice the nominal length.
2.4.5
Super long fiber rate
The percentage of super long fiber mass to total fiber mass.
2.4.6
Double length fiber
Missing cut fiber
A cut fiber whose length is twice or more than its nominal length.
2.4.7
Double length fiber content
The ratio of the mass of double-length fiber to the total mass of fiber, expressed in mg/100g.
2.5 Terminology for testing the tensile properties of chemical fibers
2.5.1
Strong
The characteristic of fiber deforming against external forces, expressed in units of force.
2.5.2
Wet strength
Under specified conditions, the strength measured after the sample is soaked.
2.5.3
Breaking strength
Under specified conditions, the maximum force measured when the sample breaks during the tensile test.
2.5.4
Constant elongation strength
The corresponding strength when the sample is stretched to the specified elongation.
2.5.5
Knot breaking strength
The tensile breaking strength of a fiber or yarn with a knot of a predetermined shape clamped between the two clamps of the tensile tester.
2.5.6
Hook breaking strength
The tension of two fibers or yarns that are taken from the same package and hooked together in a prescribed manner, clamped between the two clamps of the tensile tester
Tensile breaking strength.
2.5.7
Single fiber breaking strength
The maximum force measured when a single fiber sample is stretched to break is generally expressed in centinewtons (cN).
2.5.21
Stress relaxation
At a constant temperature, maintaining a given deformation, the stress in the fiber gradually attenuates with time.
2.5.22
strain
Deformation of fibers due to external forces. Usually expressed in the corresponding ratio.
2.5.23
Tensile strain
The strain produced by the fiber under tension is expressed as the ratio of the original length of the specimen.
2.5.24
Force-deformation curve
A graph that characterizes the relationship between force and deformation of a fiber under pressure, shear, tensile or torsion.
2.5.25
stress-strain curve
A graph that characterizes the relationship between stress and strain of a fiber under pressure, shear, tensile or torsion.
2.5.26
Force-elongation curve
Stretch curve
Load elongation curve
A graph characterizing the relationship between force and elongation of the fiber under tensile force (load).
2.5.27
Constant speed extension (CRE) force gauge
A tester that stretches the specimen at a constant speed.
2.5.28
Modulus
Parameters used to characterize fiber deformation characteristics. On the stress-strain curve, the ratio of stress increment to strain increment.
2.5.29
Initial modulus
The slope of the initial straight line on the fiber stress-strain curve.
2.5.30
Young's modulus
On the stress-strain curve of elastic fiber, the ratio of stress increment to strain increment in the elastic region of the fiber.
2.5.31
Secant modulus
Chord modulus
The ratio of the stress difference to the strain difference between two points specified on the stress-strain curve of the fiber.
2.5.32
Elastic Modulus
The ratio of stress to strain in an elastic medium within the proportional limit.
2.5.33
Secant modulus
The special case of chord modulus is the ratio of the difference in stress to the difference in strain between the zero point and any point on the stress-strain curve.
2.5.34
Tangent modulus
The ratio of the stress change to the strain change derived from the tangent line at any point on the stress-strain curve.
2.5.35
Wet modulus
The modulus measured when the fiber is completely wet.
2.5.36
tensile strength
The strength per unit cross-sectional area of the sample is expressed in megapascals (MPa).
2.6 Chemical fiber crimp/crimp performance test terminology
2.6.1
curly
The wavy state of the fiber.
2.6.2
Curl number
The number of crimps within a certain length of fiber.
2.6.3
Curl rate
The percentage of the difference between fiber straight length and crimp length to its straight length under specified tension.
2.6.4
Curl recovery rate
The percentage of the difference between the straightened length of the crimped fiber and the recovered length after straightening to the straightened length.
2.6.5
Crimp elasticity
The percentage of the difference between the straightened length of the crimped fiber and the recovered length after straightening to the difference between the straightened length and the crimped length.
2.6.6
Crimp shrinkage
After the deformed yarn has been crimped, the difference between the straightened length and the length when the stretched
The ratio of the length after straight.
2.6.7
Crimp stability
The textured yarn appears after crimping, and the ratio of crimp shrinkage after heavier load and before heavier load.
2.6.8
Curl modulus
After the deformed yarn is crimped, the difference between the straightened length measured under the specified load and the elastic length in the elastic range and the straightened length
The ratio of degrees.
2.6.9
Curling
Re-emerge potential curls.
2.6.10
Curled display medium
Can make the tested textured yarn form temporarily crimped and permanently deformed substances, such as dry hot air, water vapor, hot water, etc.
2.8.6
S-twist
The inclination direction of the monofilament in the multifilament is consistent with the middle of the letter "S", which is called "S" twist.
2.8.7
Z twist
The inclination direction of the monofilament in the multifilament is consistent with the middle of the letter "Z", which is called "Z" twist.
2.8.8
Twisting resilience
The tendency of the twisted filament yarn to return to its shape before twisting.
2.8.9
Residual torque
The torsional stress in the textured filament yarn remains. When one end of the yarn is fixed and the other end is free, it is expressed by the number of revolutions per unit length.
2.8.10
Residual twist
After heat setting, the twists remaining on the thread.
2.9 Terminology for testing chemical fiber filament network degree
2.9.1
Network degree
Degree of engagement
The number of network points in the unit length of the thread, expressed in units per meter (pieces/m).
2.9.2
Network distance
The distance between two adjacent interweaving points.
2.9.3
Network stability
Network fastness
A measure of the stability (fastness) of the network points.
2.9.4
Relief
The minimum load value that can meet the requirements of network fastness set when measuring the network degree. Expressed in centinewtons (cN).
2.10 Chemical fiber elastic fiber inspection terminology
2.10.1
Stretch recovery cycle
In the tensile test of elastic fibers, the sample is stretched to the selected length at the specified initial length and tensile speed without interruption, and the cycle
After elongation, it is a repeated process of returning to the original length.
2.10.2
elasticity
After the force that causes the fiber to deform is removed, the fiber tends to immediately return to its original size and state performance.
2.10.3
Elastic deformation
Deformation that the fiber can recover after removing the external force.
2.10.4
Sudden elastic deformation
The deformation that the fiber recovers instantly after the external force is removed, that is, the recoverable deformation that is basically independent of time.
2.10.5
Slow elastic deformation
After removing the external force, the fiber recovers its deformation after a certain period of time.
2.10.6
Elastic elongation
After the fiber is stretched and stretched to a certain extent, it can be stretched back by stress relaxation and creep.
2.10.7
Elastic recovery rate
After the elastic fiber is s...
Get Quotation: Click GB/T 4146.3-2011 (Self-service in 1-minute)
Historical versions (Master-website): GB/T 4146.3-2011
Preview True-PDF (Reload/Scroll-down if blank)
GB/T 4146.3-2011: Textiles - Man-Made Fibers - Part 3: Terms of Inspection
GB/T 4146.3-2011
Textiles - Man-made fibers - Part 3.Terms of inspection
ICS 59.060.20
W50
National Standards of People's Republic of China
Textile chemical fiber
Part 3.Test terminology
2011-06-16 released
2011-12-01 implementation
General Administration of Quality Supervision, Inspection and Quarantine of the People's Republic of China
Issued by China National Standardization Administration
Table of contents
Foreword Ⅰ
1 Scope 1
2 Test term 1
2.1 General chemical fiber inspection terms 1
2.2 Chemical fiber sampling inspection term 1
2.3 Terms for chemical fiber linear density inspection 2
2.4 Chemical fiber length inspection term 2
2.5 Terminology for testing tensile properties of chemical fibers 3
2.6 Chemical fiber crimping/crimping performance test term 6
2.7 Terminology for testing the thermal shrinkage rate of chemical fibers 7
2.8 Terminology for the twist test of chemical fiber filament 7
2.9 Terminology for testing chemical fiber filament network degree 8
2.10 Chemical fiber elastic fiber inspection term 8
2.11 Terminology for quality difference inspection 9
2.12 Visual inspection terms 10
2.13 Terminology for defect inspection 11
2.14 Other fiber inspection terms 12
2.15 Inspection terms for chemical fiber raw materials 14
3 Statistical Test Terms 16
Chinese Index 17
English Correspondence Index 21
Textile chemical fiber
Part 3.Test terminology
1 Scope
This part of GB/T 4146 specifies the inspection terms for textile chemical fibers and their raw materials.
This part is suitable for the exchange of concepts in the production, use, commerce, scientific research, and teaching of chemical fibers.
2 Test term
2.1 General chemical fiber inspection terms
2.1.1
Standard atmosphere
An environment in which relative humidity and temperature are controlled, and textiles are subjected to humidity conditioning and testing under this environmental temperature and humidity.
2.1.2
Relative humidity
Under the same temperature and pressure conditions, the ratio of the actual pressure of water vapor in the atmosphere to the pressure of saturated water vapor, expressed as a percentage.
2.1.3
Pre-conditioning
A treatment in which the sample or specimen is adjusted to a moisture regain lower than the predetermined moisture before the humidity is adjusted in the test standard atmosphere.
2.1.4
Humidity control
A treatment in which the sample or specimen is placed in the test standard atmosphere for a certain period of time to reach the moisture absorption equilibrium.
2.1.5
Humidity balance
The moisture absorption and moisture release of textile fiber reach a balance, and the change of its quality tends to zero.
2.1.6
Gauge length
The distance between the two effective clamping points (lines) that clamp the sample on the test device.
2.1.7
Initial length
Under the specified pretension, the distance between the two effective clamping points (lines) holding the sample on the test device.
2.1.8
Tension
The force that causes the fiber to elongate.
Note. tension is the abbreviation of tensioningforce. In fibers and yarns, tension is usually applied according to the linear density of the fiber.
2.1.9
Pretension
To make the sample straight, the force applied to the sample before the start of the test.
2.2 Terms for chemical fiber sampling and inspection
2.2.1
Rolled wire
In order to facilitate processing, storage and transportation, several lengths of chemical fiber rolls are packed into suitable forms. The package form has "unsupported" (such as
Hank yarn) and "supported" (such as cheese yarn, paper bobbin yarn). Referred to as roll.
2.2.2
According to different purposes, the unit of counting divided by product raw materials, production technology, etc.
2.2.3
Batch sample
Can represent the entire batch of packages (or samples), the sum of packages (or samples) used to extract laboratory samples.
2.2.4
Production batch
The raw and auxiliary fibers, process conditions and product specifications are the same, and are continuously produced within a certain period of time.
2.2.5
Inspection lot
In order to check the quality and stability of the production batch products, products determined periodically or according to production conditions are used.
2.2.6
Laboratory samples
The product unit or part of the fiber taken from the batch sample according to the regulations is used as the source of the test sample.
2.2.7
Sample
The part taken from a laboratory sample for testing.
2.3 Terms for chemical fiber linear density inspection
2.3.1
Linear density
The mass per unit length of fiber or yarn.
2.3.2
Nominal linear density
The linear density mentioned in the sales document (contract, invoice, etc.).
2.3.3
Linear density deviation rate
The percentage of the difference between the measured linear density and the nominal linear density of chemical fiber to the nominal linear density.
2.3.4
Te [x]
A unit that expresses linear density, which is the mass grams per kilometer of fiber. Commonly used unit tex or dtex, 1tex=10dtex.
2.3.5
Number of filaments
The number of monofilaments included in a multifilament formed by a porous spinneret.
2.3.6
Single filament number deviation rate
The percentage of the difference between the number of spinneret holes forming a multifilament and the actual number of single filaments to the number of spinneret holes.
2.4 Chemical fiber length inspection term
2.4.1
Nominal length
The fiber length mentioned in the sales document (contract, invoice, etc.).
2.4.2
Length deviation rate
The percentage of the difference between the measured length of chemical short fibers and the nominal length to the nominal length.
2.4.3
Viscose staple fiber boundary
In the length distribution of viscose staple fiber, the length limit is set for the staple fiber that is not conducive to spinning. When the nominal length is less than 50mm, short
The fiber limit is 20mm; when the nominal length is greater than or equal to 50mm, the short fiber limit is 30mm.
2.4.4
Super long fiber
Cut fibers that are larger than the super-length limit but less than twice the nominal length.
2.4.5
Super long fiber rate
The percentage of super long fiber mass to total fiber mass.
2.4.6
Double length fiber
Missing cut fiber
A cut fiber whose length is twice or more than its nominal length.
2.4.7
Double length fiber content
The ratio of the mass of double-length fiber to the total mass of fiber, expressed in mg/100g.
2.5 Terminology for testing the tensile properties of chemical fibers
2.5.1
Strong
The characteristic of fiber deforming against external forces, expressed in units of force.
2.5.2
Wet strength
Under specified conditions, the strength measured after the sample is soaked.
2.5.3
Breaking strength
Under specified conditions, the maximum force measured when the sample breaks during the tensile test.
2.5.4
Constant elongation strength
The corresponding strength when the sample is stretched to the specified elongation.
2.5.5
Knot breaking strength
The tensile breaking strength of a fiber or yarn with a knot of a predetermined shape clamped between the two clamps of the tensile tester.
2.5.6
Hook breaking strength
The tension of two fibers or yarns that are taken from the same package and hooked together in a prescribed manner, clamped between the two clamps of the tensile tester
Tensile breaking strength.
2.5.7
Single fiber breaking strength
The maximum force measured when a single fiber sample is stretched to break is generally expressed in centinewtons (cN).
2.5.21
Stress relaxation
At a constant temperature, maintaining a given deformation, the stress in the fiber gradually attenuates with time.
2.5.22
strain
Deformation of fibers due to external forces. Usually expressed in the corresponding ratio.
2.5.23
Tensile strain
The strain produced by the fiber under tension is expressed as the ratio of the original length of the specimen.
2.5.24
Force-deformation curve
A graph that characterizes the relationship between force and deformation of a fiber under pressure, shear, tensile or torsion.
2.5.25
stress-strain curve
A graph that characterizes the relationship between stress and strain of a fiber under pressure, shear, tensile or torsion.
2.5.26
Force-elongation curve
Stretch curve
Load elongation curve
A graph characterizing the relationship between force and elongation of the fiber under tensile force (load).
2.5.27
Constant speed extension (CRE) force gauge
A tester that stretches the specimen at a constant speed.
2.5.28
Modulus
Parameters used to characterize fiber deformation characteristics. On the stress-strain curve, the ratio of stress increment to strain increment.
2.5.29
Initial modulus
The slope of the initial straight line on the fiber stress-strain curve.
2.5.30
Young's modulus
On the stress-strain curve of elastic fiber, the ratio of stress increment to strain increment in the elastic region of the fiber.
2.5.31
Secant modulus
Chord modulus
The ratio of the stress difference to the strain difference between two points specified on the stress-strain curve of the fiber.
2.5.32
Elastic Modulus
The ratio of stress to strain in an elastic medium within the proportional limit.
2.5.33
Secant modulus
The special case of chord modulus is the ratio of the difference in stress to the difference in strain between the zero point and any point on the stress-strain curve.
2.5.34
Tangent modulus
The ratio of the stress change to the strain change derived from the tangent line at any point on the stress-strain curve.
2.5.35
Wet modulus
The modulus measured when the fiber is completely wet.
2.5.36
tensile strength
The strength per unit cross-sectional area of the sample is expressed in megapascals (MPa).
2.6 Chemical fiber crimp/crimp performance test terminology
2.6.1
curly
The wavy state of the fiber.
2.6.2
Curl number
The number of crimps within a certain length of fiber.
2.6.3
Curl rate
The percentage of the difference between fiber straight length and crimp length to its straight length under specified tension.
2.6.4
Curl recovery rate
The percentage of the difference between the straightened length of the crimped fiber and the recovered length after straightening to the straightened length.
2.6.5
Crimp elasticity
The percentage of the difference between the straightened length of the crimped fiber and the recovered length after straightening to the difference between the straightened length and the crimped length.
2.6.6
Crimp shrinkage
After the deformed yarn has been crimped, the difference between the straightened length and the length when the stretched
The ratio of the length after straight.
2.6.7
Crimp stability
The textured yarn appears after crimping, and the ratio of crimp shrinkage after heavier load and before heavier load.
2.6.8
Curl modulus
After the deformed yarn is crimped, the difference between the straightened length measured under the specified load and the elastic length in the elastic range and the straightened length
The ratio of degrees.
2.6.9
Curling
Re-emerge potential curls.
2.6.10
Curled display medium
Can make the tested textured yarn form temporarily crimped and permanently deformed substances, such as dry hot air, water vapor, hot water, etc.
2.8.6
S-twist
The inclination direction of the monofilament in the multifilament is consistent with the middle of the letter "S", which is called "S" twist.
2.8.7
Z twist
The inclination direction of the monofilament in the multifilament is consistent with the middle of the letter "Z", which is called "Z" twist.
2.8.8
Twisting resilience
The tendency of the twisted filament yarn to return to its shape before twisting.
2.8.9
Residual torque
The torsional stress in the textured filament yarn remains. When one end of the yarn is fixed and the other end is free, it is expressed by the number of revolutions per unit length.
2.8.10
Residual twist
After heat setting, the twists remaining on the thread.
2.9 Terminology for testing chemical fiber filament network degree
2.9.1
Network degree
Degree of engagement
The number of network points in the unit length of the thread, expressed in units per meter (pieces/m).
2.9.2
Network distance
The distance between two adjacent interweaving points.
2.9.3
Network stability
Network fastness
A measure of the stability (fastness) of the network points.
2.9.4
Relief
The minimum load value that can meet the requirements of network fastness set when measuring the network degree. Expressed in centinewtons (cN).
2.10 Chemical fiber elastic fiber inspection terminology
2.10.1
Stretch recovery cycle
In the tensile test of elastic fibers, the sample is stretched to the selected length at the specified initial length and tensile speed without interruption, and the cycle
After elongation, it is a repeated process of returning to the original length.
2.10.2
elasticity
After the force that causes the fiber to deform is removed, the fiber tends to immediately return to its original size and state performance.
2.10.3
Elastic deformation
Deformation that the fiber can recover after removing the external force.
2.10.4
Sudden elastic deformation
The deformation that the fiber recovers instantly after the external force is removed, that is, the recoverable deformation that is basically independent of time.
2.10.5
Slow elastic deformation
After removing the external force, the fiber recovers its deformation after a certain period of time.
2.10.6
Elastic elongation
After the fiber is stretched and stretched to a certain extent, it can be stretched back by stress relaxation and creep.
2.10.7
Elastic recovery rate
After the elastic fiber is s...
Share
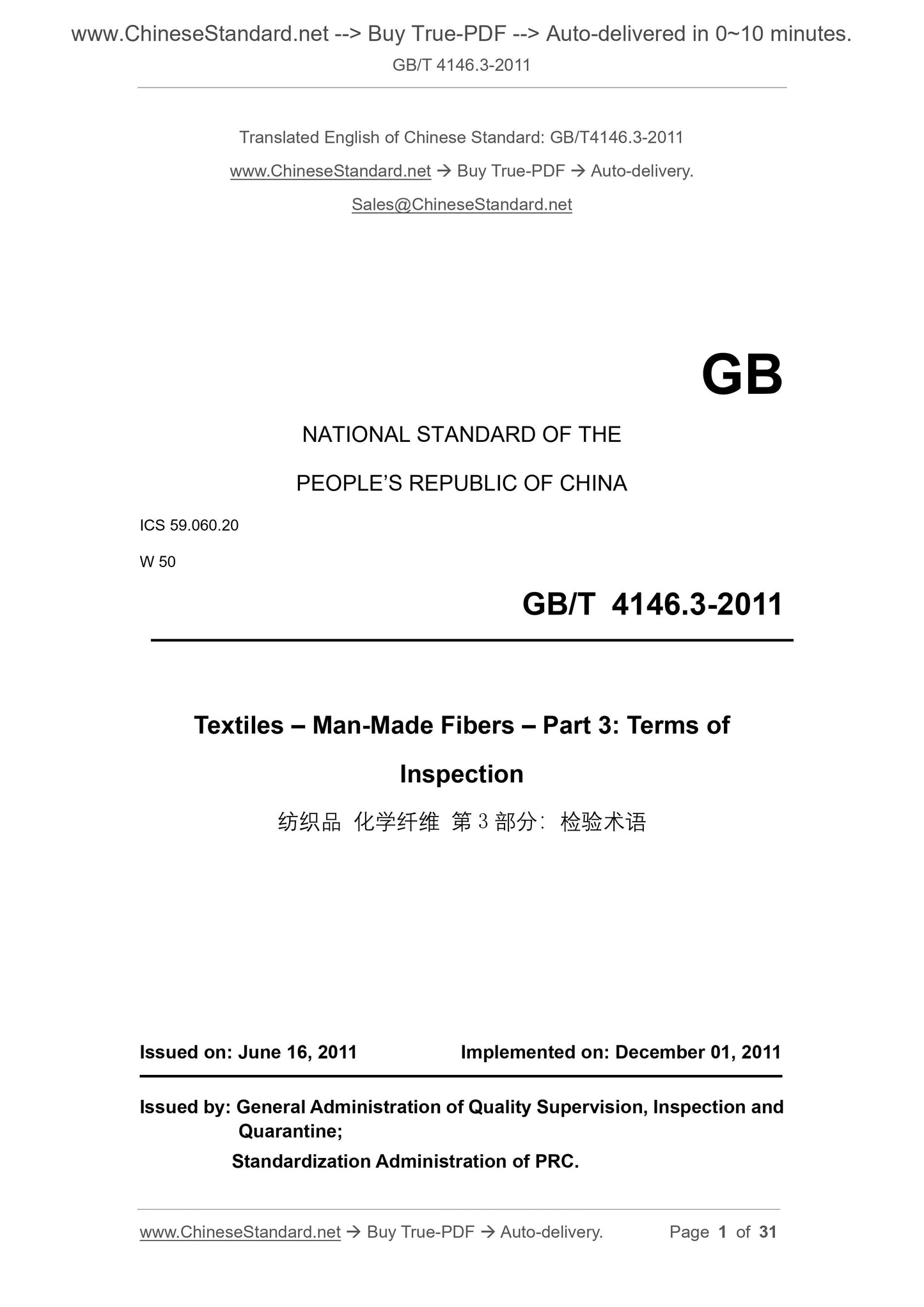
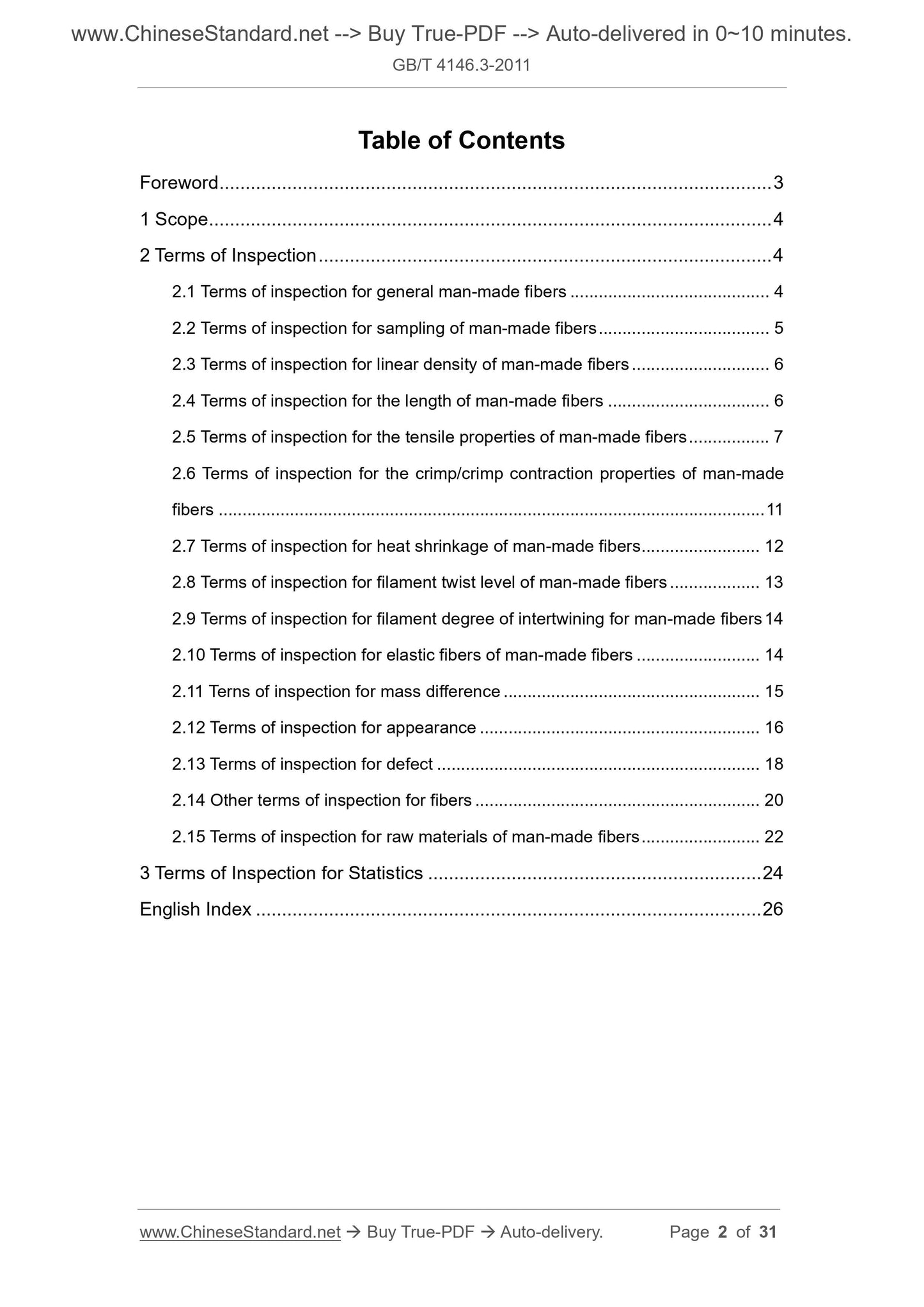
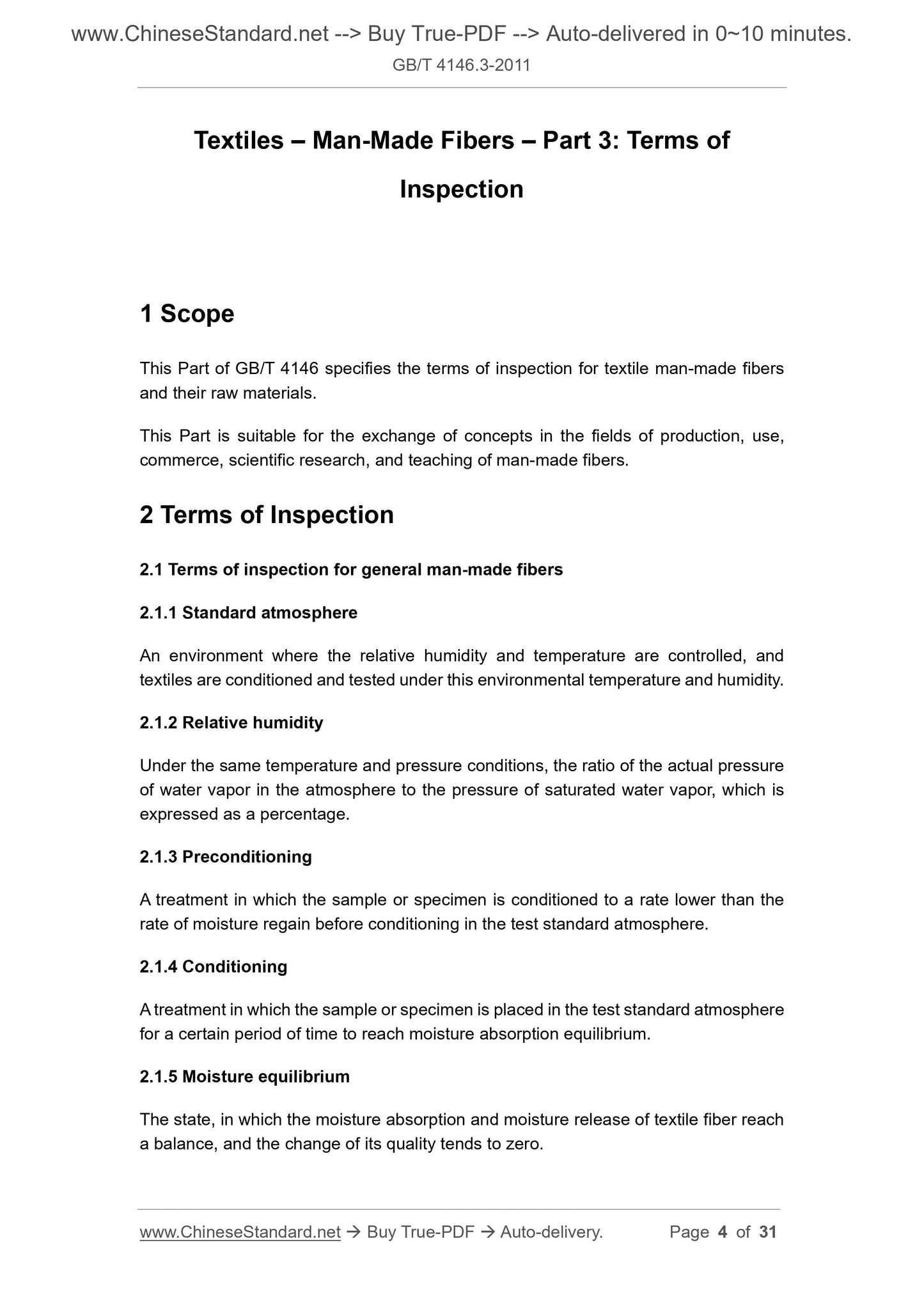
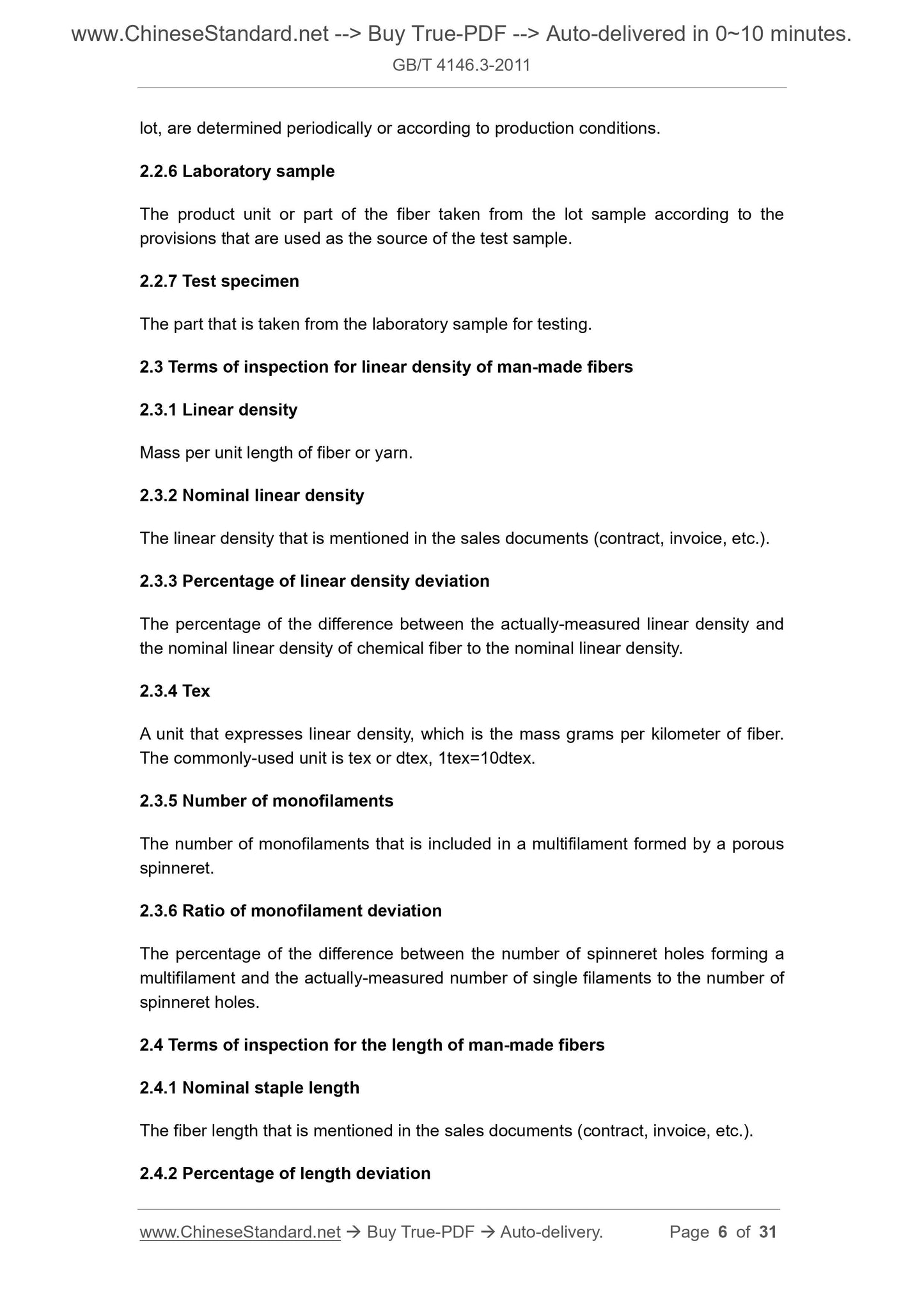
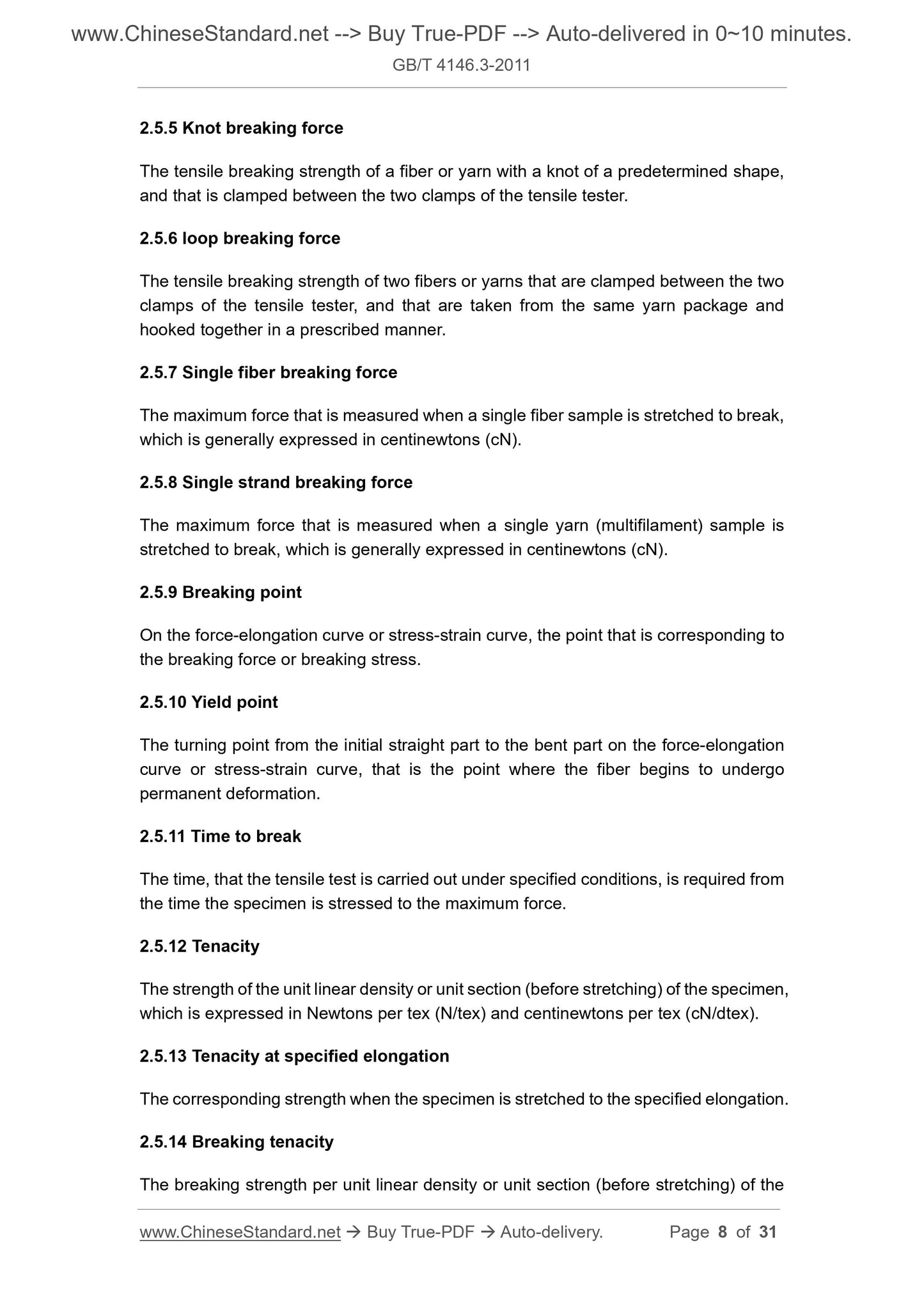
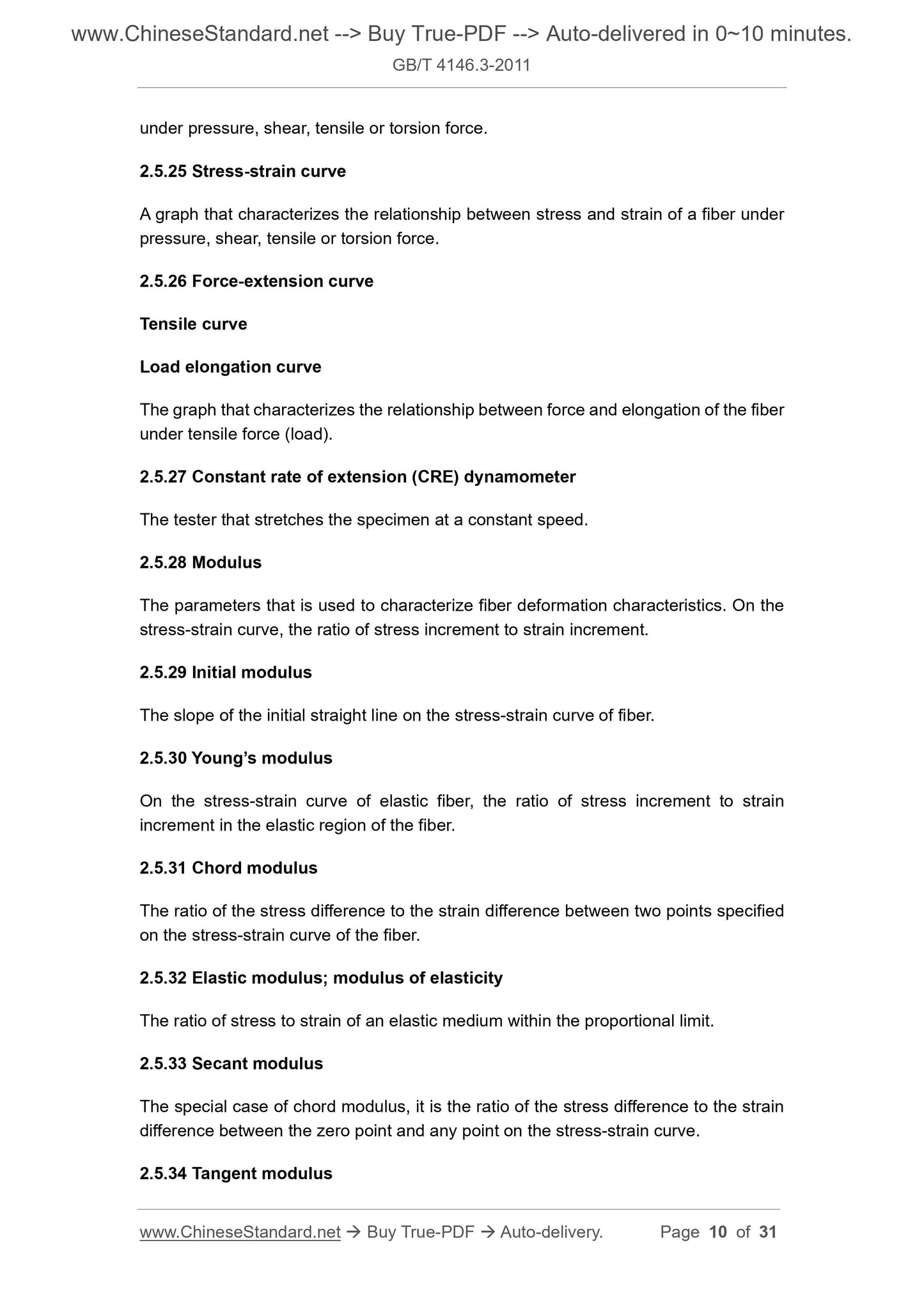
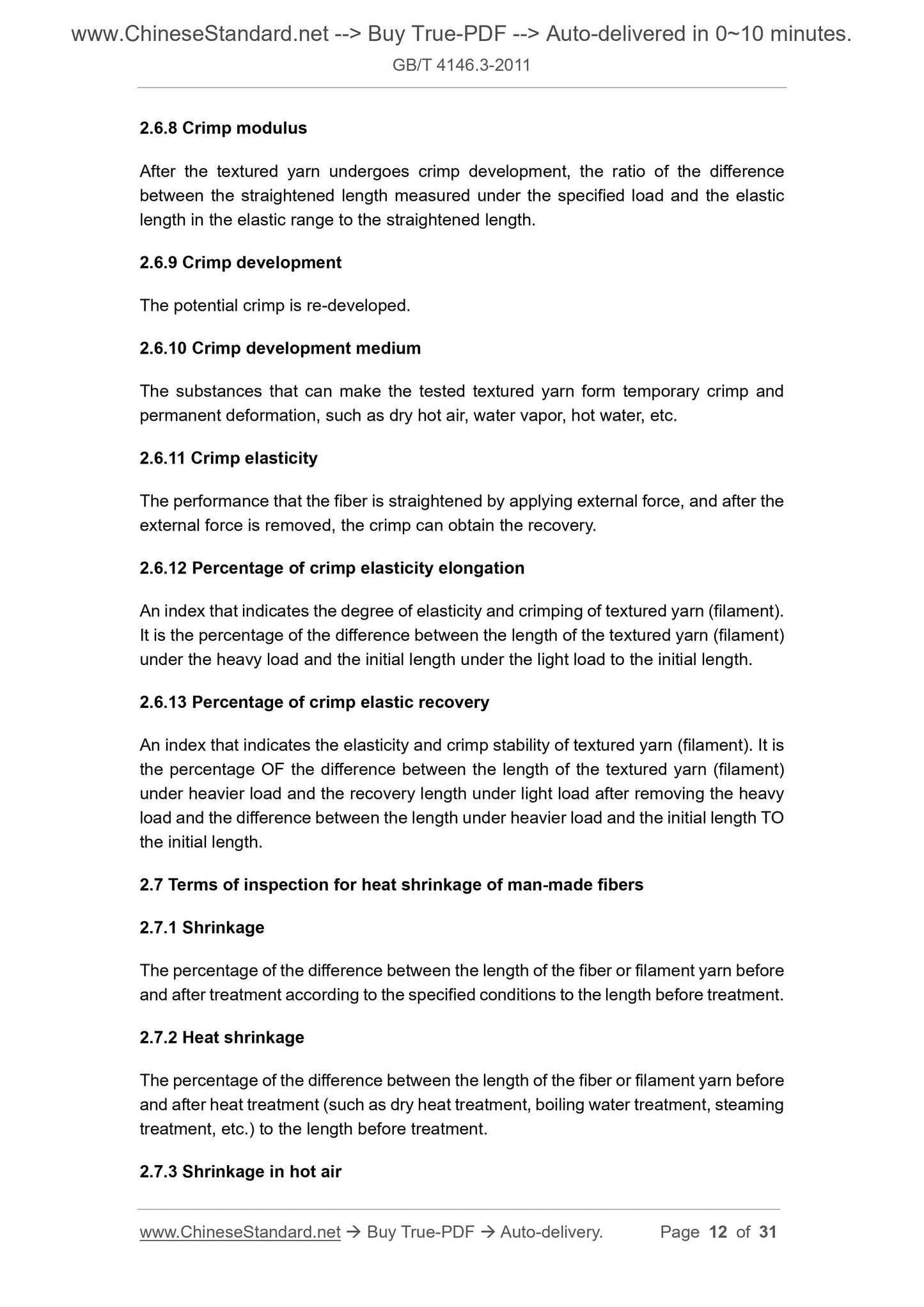
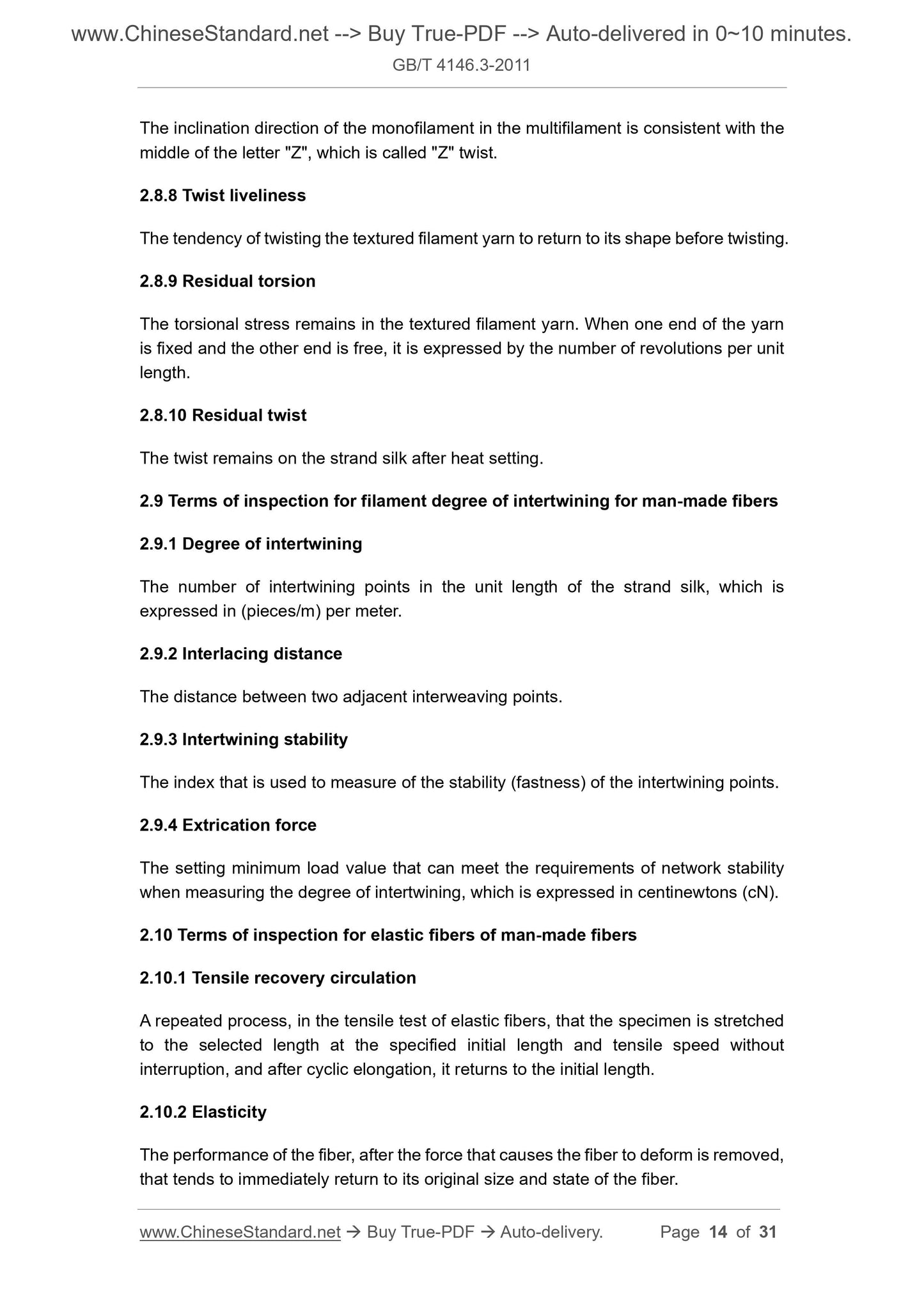
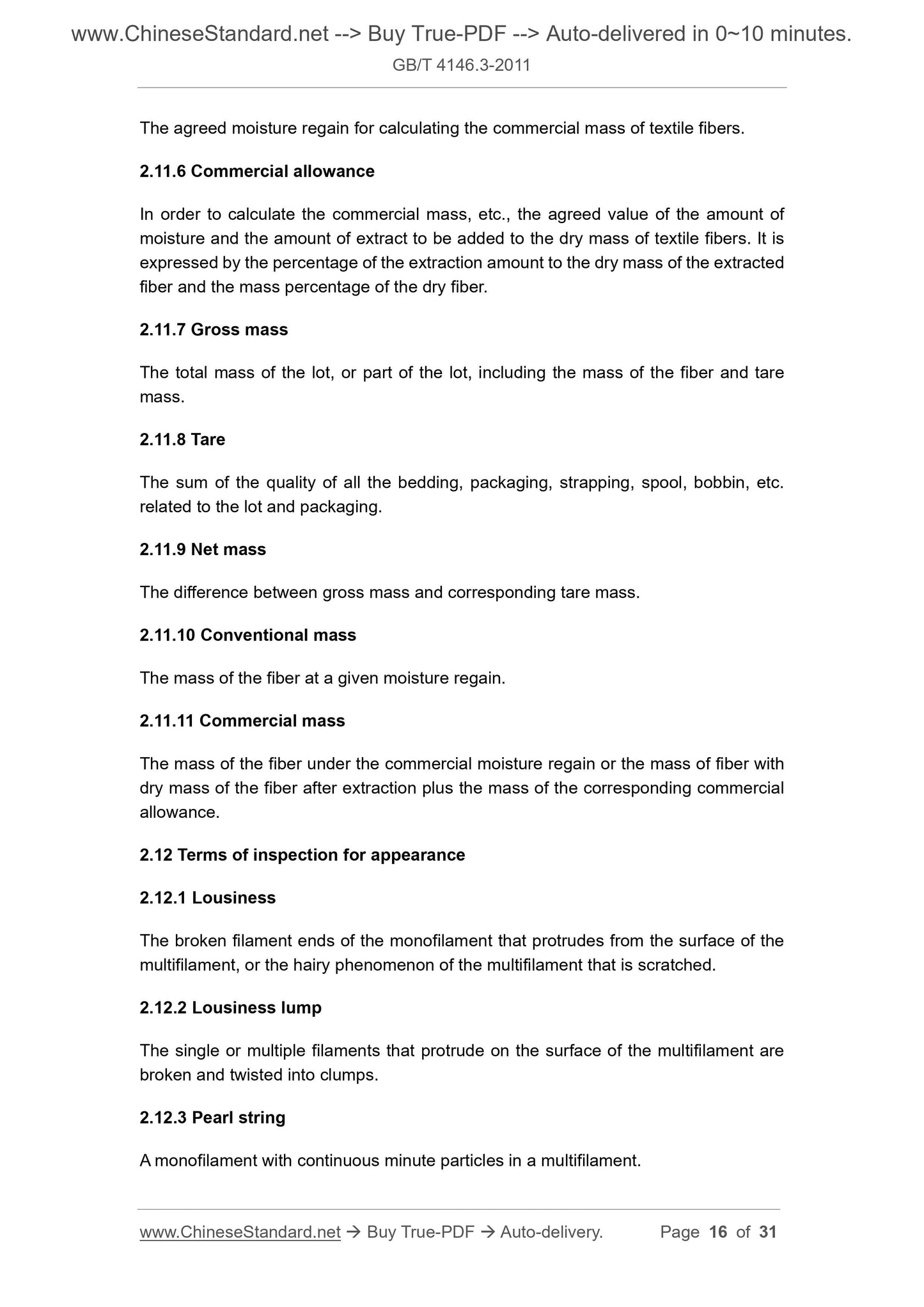
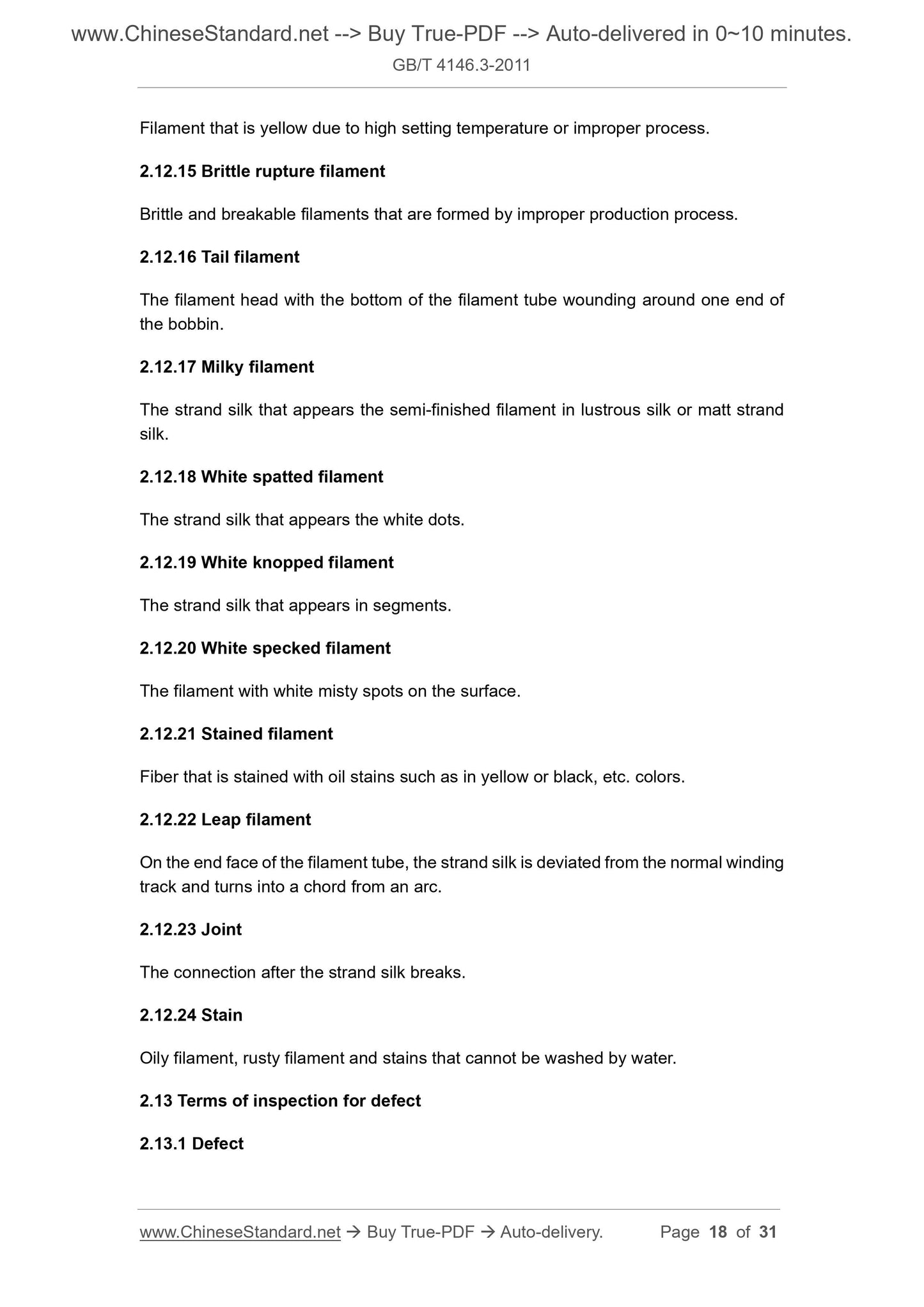
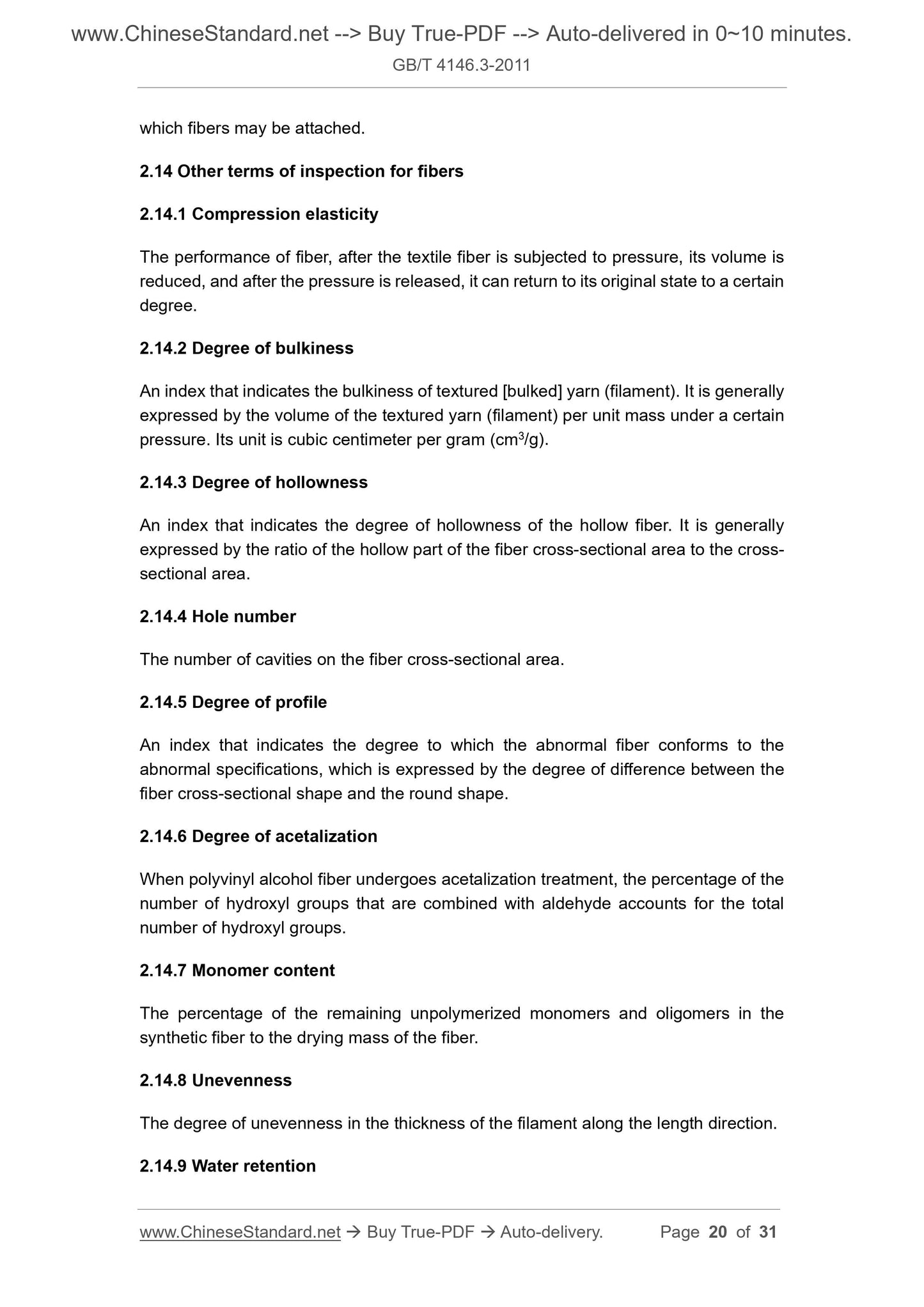
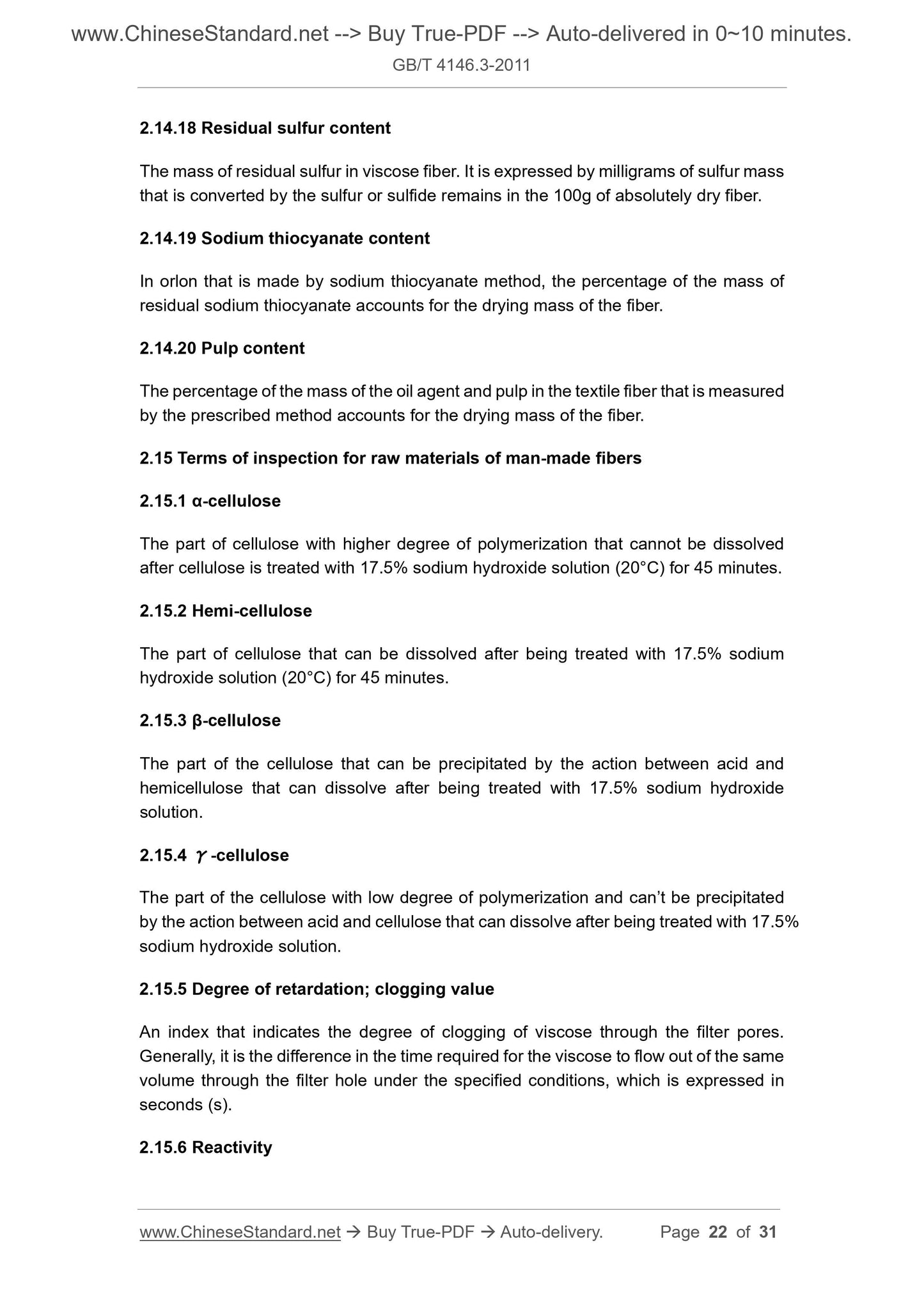