1
/
of
10
PayPal, credit cards. Download editable-PDF and invoice in 1 second!
JB/T 10505-2016 English PDF (JB/T10505-2016)
JB/T 10505-2016 English PDF (JB/T10505-2016)
Regular price
$260.00 USD
Regular price
Sale price
$260.00 USD
Unit price
/
per
Shipping calculated at checkout.
Couldn't load pickup availability
Delivery: 3 seconds. Download true-PDF + Invoice.
Get QUOTATION in 1-minute: Click JB/T 10505-2016
Historical versions: JB/T 10505-2016
Preview True-PDF (Reload/Scroll if blank)
JB/T 10505-2016: Internal combustion engines - Oil Radiators - Sepcification
JB/T 10505-2016
JB
MACHINERY INDUSTRY STANDARD
OF THE PEOPLE’S REPUBLIC OF CHINA
ICS 27.020
J 95
Record No.: 53624-2016
Replacing JB/T 10505-2005
Internal Combustion Engines – Oil Radiators - Specification
ISSUED ON: JANUARY 15, 2016
IMPLEMENTED ON: JUNE 1, 2016
Issued by: Ministry of Industry and Information Technology of the People’s
Republic of China
Table of Contents
Foreword ... 4
1 Scope ... 6
2 Normative References ... 6
3 Terms and Definitions ... 7
4 Technical Requirements ... 8
4.1 Materials ... 8
4.2 Sealing performance ... 8
4.3 Vibration resistance ... 8
4.4 Pressure alternating cycle resistance ... 8
4.5 Heat shock resistance ... 8
4.6 Static pressure strength ... 8
4.7 External corrosion resistance ... 8
4.8 Comprehensive performance ... 9
4.9 Cleanliness on the oil side ... 9
4.10 Assembly and matching dimensions ... 9
4.11 Manufacturing and appearance ... 9
5 Test Methods ... 10
5.1 Sealing performance ... 10
5.2 Vibration resistance, pressure alternating cycle resistance and heat shock resistance 11
5.3 Static pressure strength ... 11
5.4 External corrosion resistance ... 11
5.5 Comprehensive performance ... 11
5.6 Determination of cleanliness on oil side ... 12
5.7 Determination of the diagonal length of the core ... 12
5.8 Determination of the fin spacing of the heat dissipation fin or the wave crest spacing
of the heat dissipation strip ... 12
5.9 Checking the number of the blocked heat tubes ... 13
6 Inspection Rules ... 13
7 Marking, Packaging, Transportation and Storage ... 13
7.1 Marking ... 13
7.2 Packaging ... 14
7.3 Transportation ... 14
7.4 Storage ... 14
7.5 Others ... 14
Appendix A (Normative) Calculation Method for Main Structural Parameters of
Radiator ... 15
A.1 Radiator’s wind area, F ... 15
A.2 Radiator’s oil passage area, S0 ... 15
A.3 Radiator’s heat exchange area, A ... 16
Appendix B (Informative) Original Record Table of Neutral Salt Spray Test ... 18
Internal Combustion Engines – Oil Radiators – Specification
1 Scope
This Standard specifies the terms and definitions, technical requirements, test methods,
inspection rules, marking, packaging, transportation and storage of oil radiators of internal
combustion engine.
This Standard applies to tube-sheet type, tube-band type, seal type and expansion type oil
radiators (hereinafter referred to as radiators) of internal combustion engine.
2 Normative References
The following documents are essential to the application of this Document. For the dated
documents, only the versions with the dates indicated are applicable to this Document; for the
undated documents, only the latest version (including all the amendments) is applicable to this
Document.
GB/T 2423.17 Environmental testing for electric and electronic products - Part 2: Test
method - Test Ka: Salt mist
GB/T 2828.1 Sampling procedures for inspection by attribute - Part1: Sampling schemes
indexed by acceptance quality limit (AQL) for lot-by-lot inspection
GB/T 3821 Small and medium power internal combustion engines - Cleanliness
measurement
GB 11122-2006 Diesel engine oils
JB/T 6003.3 Internal combustion engines - Oil coolers - Part 3: Test method for heat
transfer capability
JB/T 10408 Internal Combustion Engines - Heat Exchangers - Reliability Test Method
JB/T 11798 Internal Combustion Engines - Heat Exchangers - Wind Tunnel Test
Equipment
to1 – oil inflow temperature, in °C.
4 Technical Requirements
4.1 Materials
The materials that are used for the radiator's heat pipes, main plates and oil chamber shall not
corrode in the oil.
4.2 Sealing performance
4.2.1 During exit-factory test, dry compressed air with a pressure of 800 kPa is passed into the
radiator; and the pressure is maintained for 60 s; in this case, no leakage shall occur.
4.2.2 During type test, dry compressed air with a pressure of 1000 kPa is passed into the radiator;
and the pressure is maintained for 300 s; in this case, no leakage shall occur.
4.3 Vibration resistance
The radiator is filled with clean water and fixed on the vibration test bench according to the
installation method during work. It is vibrated at an acceleration of 40 m/s2 at a frequency of
20 Hz, 30 Hz, 40 Hz, and 50 Hz for 3 h, respectively, for a total of 12 h. The vibration direction
is vertical up and down. After 12 h of vibration, the radiator shall not leak nor the parts have
damage.
4.4 Pressure alternating cycle resistance
Apply an alternating pressure from below 25 kPa to 800 kPa to the inner cavity of the radiator,
with a pressure alternating cycle of 1 s to 6 s. After 3×104 pressure cycles, the radiator shall not
leak, desolder, or permanently deform.
4.5 Heat shock resistance
When the inlet temperature difference of the radiator is 100°C±2°C, after 3×103 hot and cold
alternating cycles, there shall be no leakage nor the parts have damage.
4.6 Static pressure strength
Apply a static pressure of 2.5MPa to the inner cavity of the radiator and maintain the pressure
for 5 min. The radiator shall not leak or permanently deform.
4.7 External corrosion resistance
After 200 h of neutral salt spray corrosion, the radiator shall not have coating peeling. After the
test, it shall meet the requirements of 4.2.2 for sealing performance.
radiator shall comply with the provisions of the product drawings; and its limit deviation is ±2
pieces.
4.11.3 The limit deviation of the fin spacing of the tube-fin radiator fins is ±0.2 mm; and the
two fins shall not be pressed together. The limit deviation of the wave crest spacing of the heat
dissipation strip of the tube-strip radiator is ±0.5mm.
4.11.4 The fins (strips) on the two sides of the radiator shall not be curled, fallen over, or have
broken edges; the difference between them shall not exceed 1 mm.
4.11.5 There shall be no floating solid residue inside the radiator.
4.11.6 There shall be no obvious solder accumulation on all welds of the radiator.
4.11.7 The anti-corrosion layer on the external surface of the radiator shall be uniform and
beautiful, and there shall be no coating peeling.
4.11.8 The number of blocked heat tubes of the radiator shall not exceed 1% of the total number
of heat tubes.
5 Test Methods
5.1 Sealing performance
5.1.1 The sealing test can be carried out on the wet or dry sealing test bench. When the
conclusions obtained by the two methods are inconsistent, the conclusions obtained on the wet
sealing test bench shall prevail.
5.1.2 The exit-factory test shall be carried out in the following manner:
a) On a wet sealing test bench, the radiator submerged in the water tank is fed with 800 kPa
dry compressed air as specified in 4.2.1 and maintained for 60 s. No more than 3 bubbles
shall appear at the same position;
b) On a dry sealing test bench, the radiator is fed with 800 kPa dry compressed air as
specified in 4.2.1 and maintained for 60 s. The air leakage shall be less than 12 mL
(standard state).
5.1.3 The type test shall be carried out according to the following manner:
a) On a wet sealing test bench, the radiator submerged in the water tank is fed with 1000
kPa dry compressed air as specified in 4.2.2 and maintained for 300 s. No more than 8
bubbles shall appear at the same position;
b) On a dry sealing test bench, the radiator is fed with 1000 kPa dry compressed air as
specified in 4.2.2, and maintained for 300 s. The air leakage s...
Get QUOTATION in 1-minute: Click JB/T 10505-2016
Historical versions: JB/T 10505-2016
Preview True-PDF (Reload/Scroll if blank)
JB/T 10505-2016: Internal combustion engines - Oil Radiators - Sepcification
JB/T 10505-2016
JB
MACHINERY INDUSTRY STANDARD
OF THE PEOPLE’S REPUBLIC OF CHINA
ICS 27.020
J 95
Record No.: 53624-2016
Replacing JB/T 10505-2005
Internal Combustion Engines – Oil Radiators - Specification
ISSUED ON: JANUARY 15, 2016
IMPLEMENTED ON: JUNE 1, 2016
Issued by: Ministry of Industry and Information Technology of the People’s
Republic of China
Table of Contents
Foreword ... 4
1 Scope ... 6
2 Normative References ... 6
3 Terms and Definitions ... 7
4 Technical Requirements ... 8
4.1 Materials ... 8
4.2 Sealing performance ... 8
4.3 Vibration resistance ... 8
4.4 Pressure alternating cycle resistance ... 8
4.5 Heat shock resistance ... 8
4.6 Static pressure strength ... 8
4.7 External corrosion resistance ... 8
4.8 Comprehensive performance ... 9
4.9 Cleanliness on the oil side ... 9
4.10 Assembly and matching dimensions ... 9
4.11 Manufacturing and appearance ... 9
5 Test Methods ... 10
5.1 Sealing performance ... 10
5.2 Vibration resistance, pressure alternating cycle resistance and heat shock resistance 11
5.3 Static pressure strength ... 11
5.4 External corrosion resistance ... 11
5.5 Comprehensive performance ... 11
5.6 Determination of cleanliness on oil side ... 12
5.7 Determination of the diagonal length of the core ... 12
5.8 Determination of the fin spacing of the heat dissipation fin or the wave crest spacing
of the heat dissipation strip ... 12
5.9 Checking the number of the blocked heat tubes ... 13
6 Inspection Rules ... 13
7 Marking, Packaging, Transportation and Storage ... 13
7.1 Marking ... 13
7.2 Packaging ... 14
7.3 Transportation ... 14
7.4 Storage ... 14
7.5 Others ... 14
Appendix A (Normative) Calculation Method for Main Structural Parameters of
Radiator ... 15
A.1 Radiator’s wind area, F ... 15
A.2 Radiator’s oil passage area, S0 ... 15
A.3 Radiator’s heat exchange area, A ... 16
Appendix B (Informative) Original Record Table of Neutral Salt Spray Test ... 18
Internal Combustion Engines – Oil Radiators – Specification
1 Scope
This Standard specifies the terms and definitions, technical requirements, test methods,
inspection rules, marking, packaging, transportation and storage of oil radiators of internal
combustion engine.
This Standard applies to tube-sheet type, tube-band type, seal type and expansion type oil
radiators (hereinafter referred to as radiators) of internal combustion engine.
2 Normative References
The following documents are essential to the application of this Document. For the dated
documents, only the versions with the dates indicated are applicable to this Document; for the
undated documents, only the latest version (including all the amendments) is applicable to this
Document.
GB/T 2423.17 Environmental testing for electric and electronic products - Part 2: Test
method - Test Ka: Salt mist
GB/T 2828.1 Sampling procedures for inspection by attribute - Part1: Sampling schemes
indexed by acceptance quality limit (AQL) for lot-by-lot inspection
GB/T 3821 Small and medium power internal combustion engines - Cleanliness
measurement
GB 11122-2006 Diesel engine oils
JB/T 6003.3 Internal combustion engines - Oil coolers - Part 3: Test method for heat
transfer capability
JB/T 10408 Internal Combustion Engines - Heat Exchangers - Reliability Test Method
JB/T 11798 Internal Combustion Engines - Heat Exchangers - Wind Tunnel Test
Equipment
to1 – oil inflow temperature, in °C.
4 Technical Requirements
4.1 Materials
The materials that are used for the radiator's heat pipes, main plates and oil chamber shall not
corrode in the oil.
4.2 Sealing performance
4.2.1 During exit-factory test, dry compressed air with a pressure of 800 kPa is passed into the
radiator; and the pressure is maintained for 60 s; in this case, no leakage shall occur.
4.2.2 During type test, dry compressed air with a pressure of 1000 kPa is passed into the radiator;
and the pressure is maintained for 300 s; in this case, no leakage shall occur.
4.3 Vibration resistance
The radiator is filled with clean water and fixed on the vibration test bench according to the
installation method during work. It is vibrated at an acceleration of 40 m/s2 at a frequency of
20 Hz, 30 Hz, 40 Hz, and 50 Hz for 3 h, respectively, for a total of 12 h. The vibration direction
is vertical up and down. After 12 h of vibration, the radiator shall not leak nor the parts have
damage.
4.4 Pressure alternating cycle resistance
Apply an alternating pressure from below 25 kPa to 800 kPa to the inner cavity of the radiator,
with a pressure alternating cycle of 1 s to 6 s. After 3×104 pressure cycles, the radiator shall not
leak, desolder, or permanently deform.
4.5 Heat shock resistance
When the inlet temperature difference of the radiator is 100°C±2°C, after 3×103 hot and cold
alternating cycles, there shall be no leakage nor the parts have damage.
4.6 Static pressure strength
Apply a static pressure of 2.5MPa to the inner cavity of the radiator and maintain the pressure
for 5 min. The radiator shall not leak or permanently deform.
4.7 External corrosion resistance
After 200 h of neutral salt spray corrosion, the radiator shall not have coating peeling. After the
test, it shall meet the requirements of 4.2.2 for sealing performance.
radiator shall comply with the provisions of the product drawings; and its limit deviation is ±2
pieces.
4.11.3 The limit deviation of the fin spacing of the tube-fin radiator fins is ±0.2 mm; and the
two fins shall not be pressed together. The limit deviation of the wave crest spacing of the heat
dissipation strip of the tube-strip radiator is ±0.5mm.
4.11.4 The fins (strips) on the two sides of the radiator shall not be curled, fallen over, or have
broken edges; the difference between them shall not exceed 1 mm.
4.11.5 There shall be no floating solid residue inside the radiator.
4.11.6 There shall be no obvious solder accumulation on all welds of the radiator.
4.11.7 The anti-corrosion layer on the external surface of the radiator shall be uniform and
beautiful, and there shall be no coating peeling.
4.11.8 The number of blocked heat tubes of the radiator shall not exceed 1% of the total number
of heat tubes.
5 Test Methods
5.1 Sealing performance
5.1.1 The sealing test can be carried out on the wet or dry sealing test bench. When the
conclusions obtained by the two methods are inconsistent, the conclusions obtained on the wet
sealing test bench shall prevail.
5.1.2 The exit-factory test shall be carried out in the following manner:
a) On a wet sealing test bench, the radiator submerged in the water tank is fed with 800 kPa
dry compressed air as specified in 4.2.1 and maintained for 60 s. No more than 3 bubbles
shall appear at the same position;
b) On a dry sealing test bench, the radiator is fed with 800 kPa dry compressed air as
specified in 4.2.1 and maintained for 60 s. The air leakage shall be less than 12 mL
(standard state).
5.1.3 The type test shall be carried out according to the following manner:
a) On a wet sealing test bench, the radiator submerged in the water tank is fed with 1000
kPa dry compressed air as specified in 4.2.2 and maintained for 300 s. No more than 8
bubbles shall appear at the same position;
b) On a dry sealing test bench, the radiator is fed with 1000 kPa dry compressed air as
specified in 4.2.2, and maintained for 300 s. The air leakage s...
Share
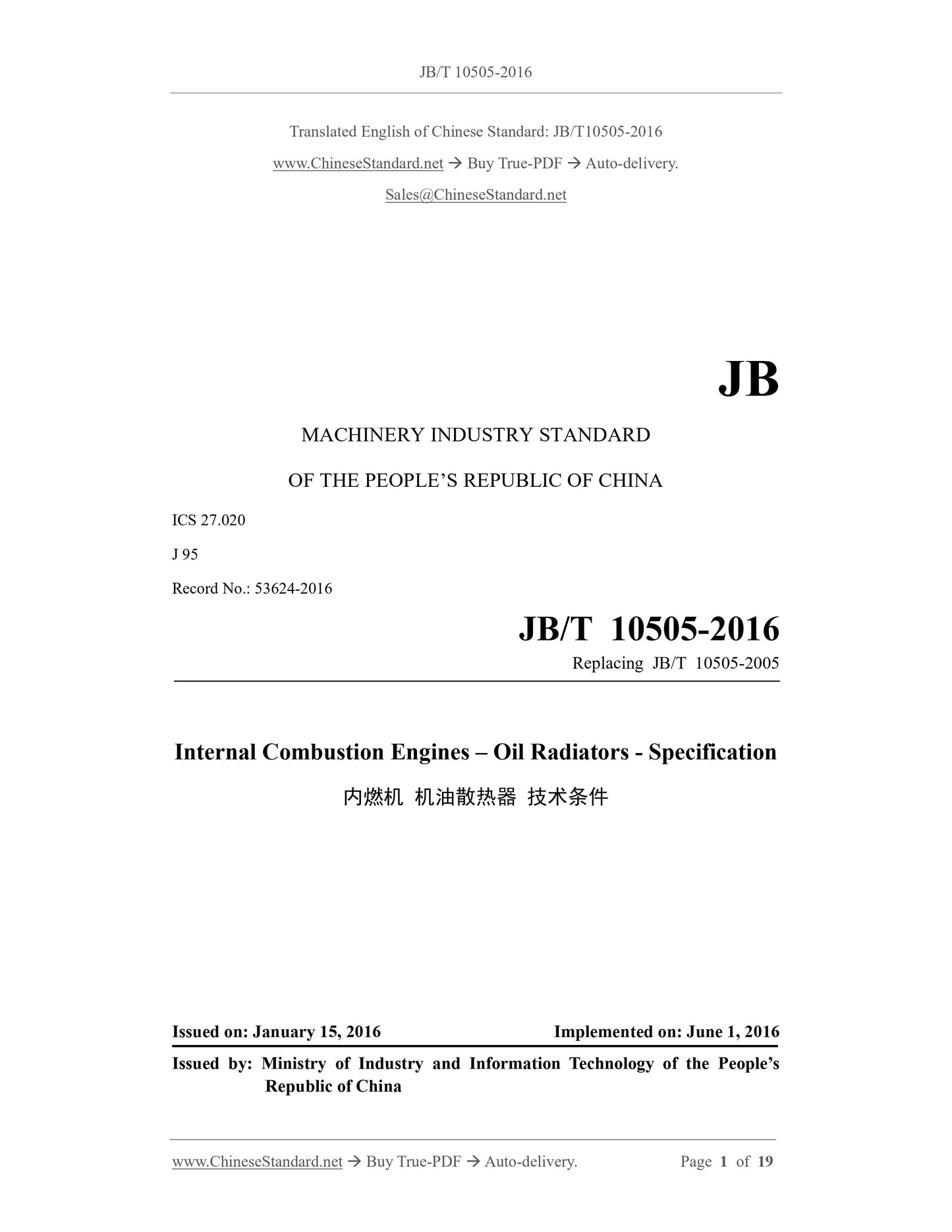
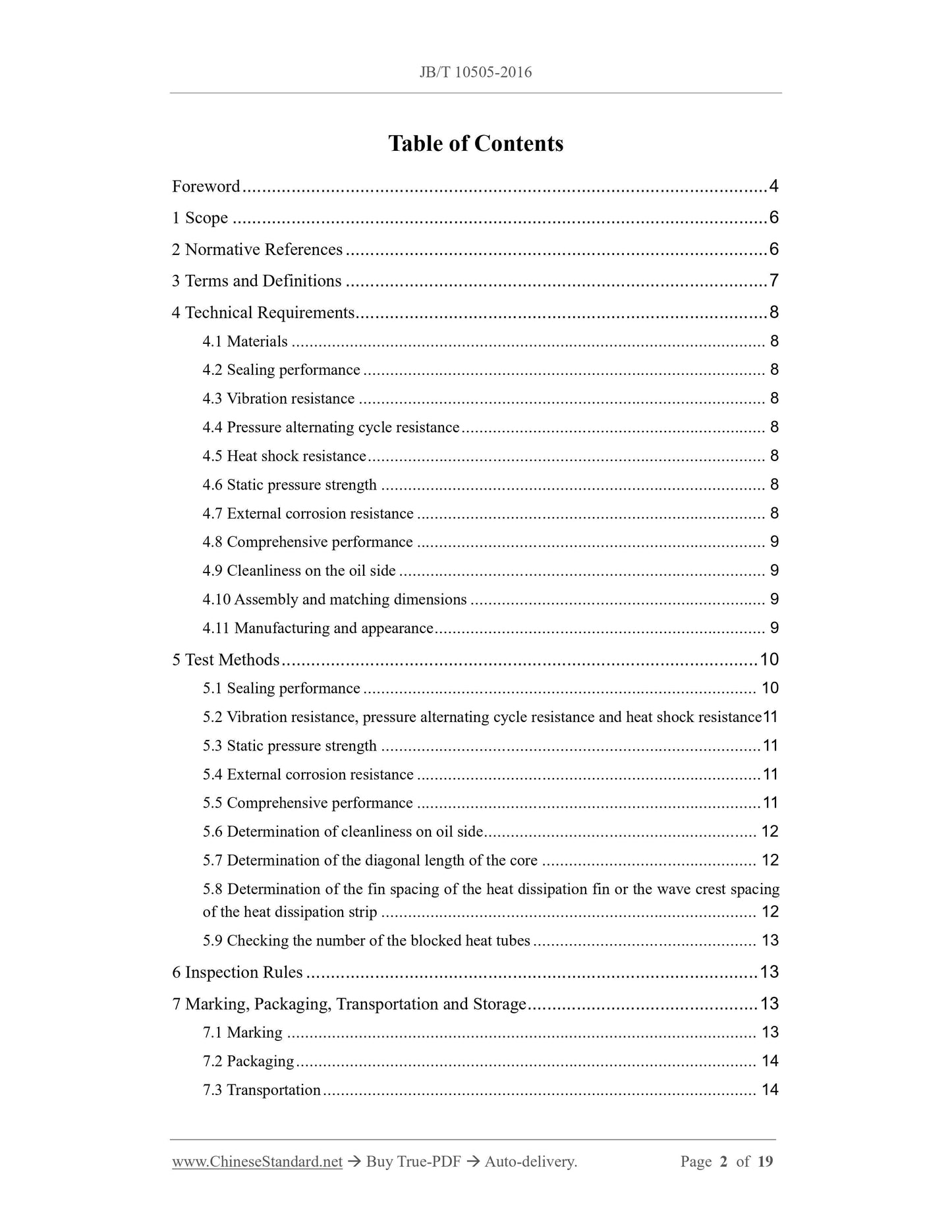
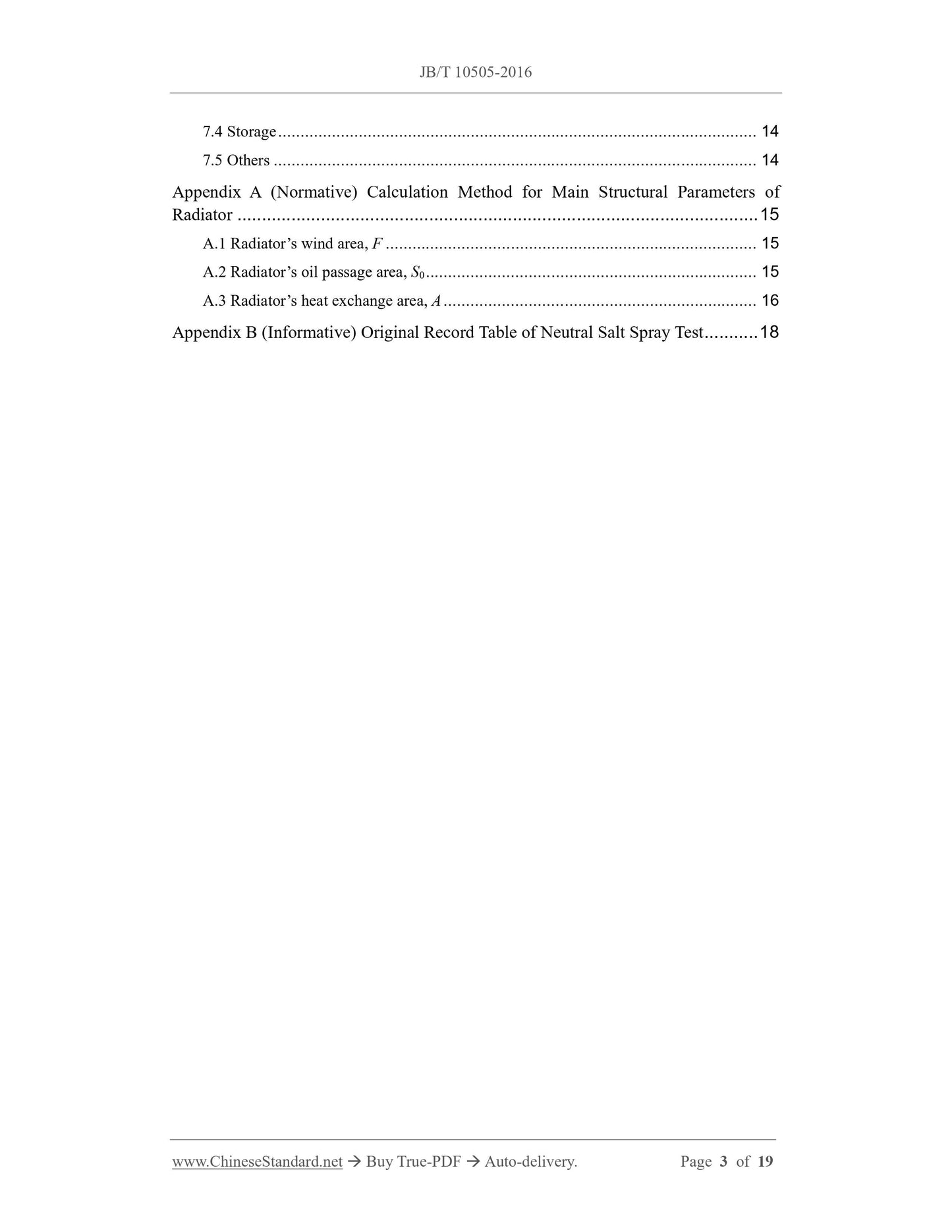
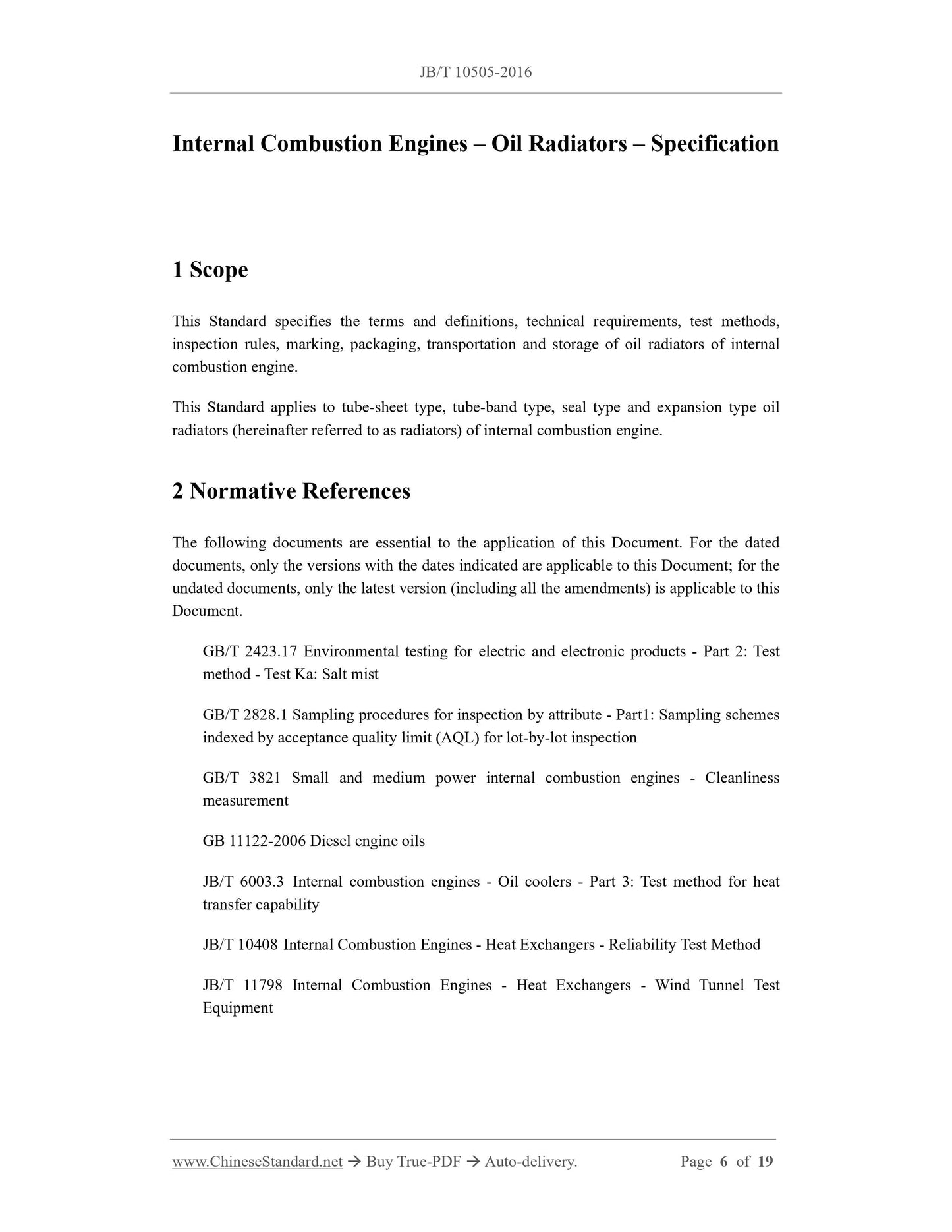
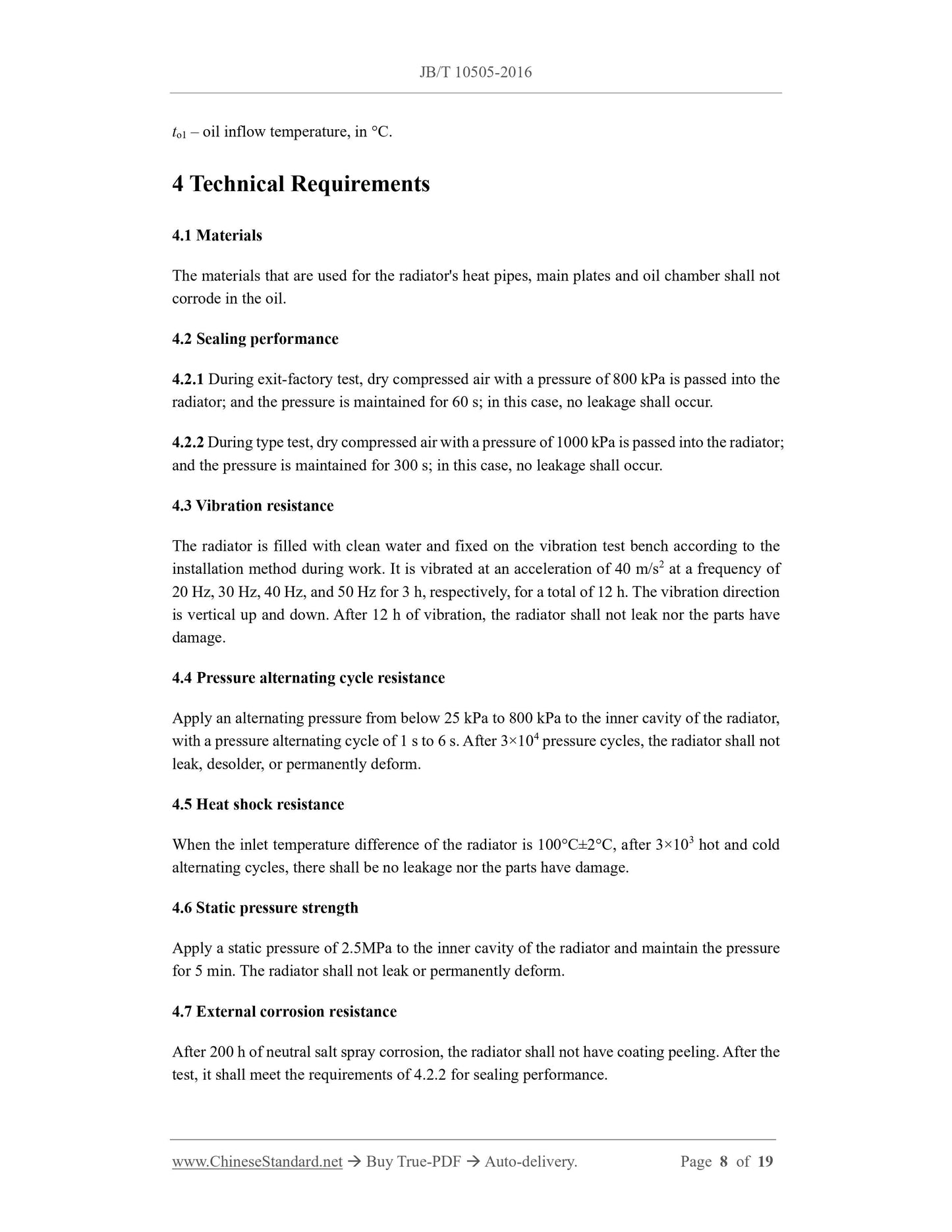
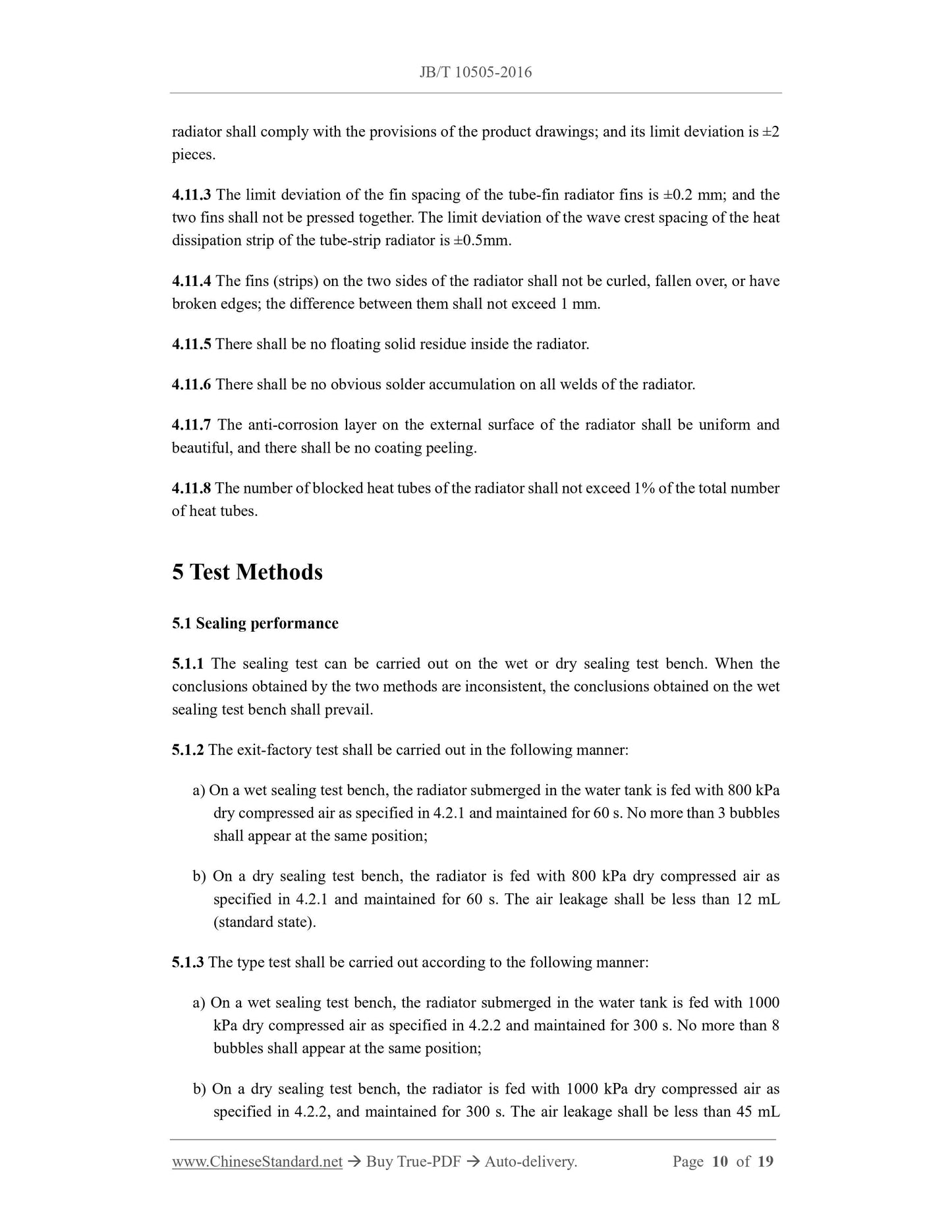
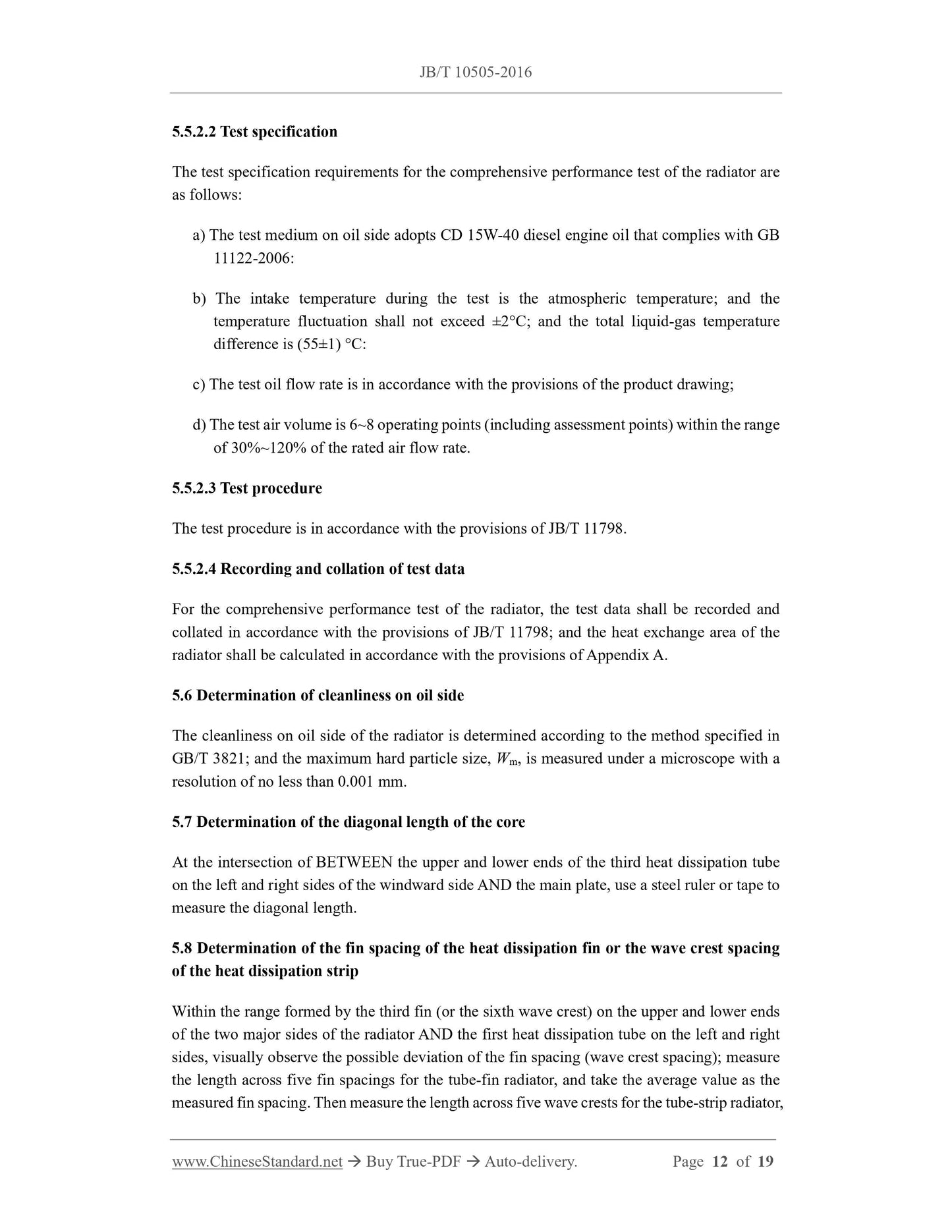
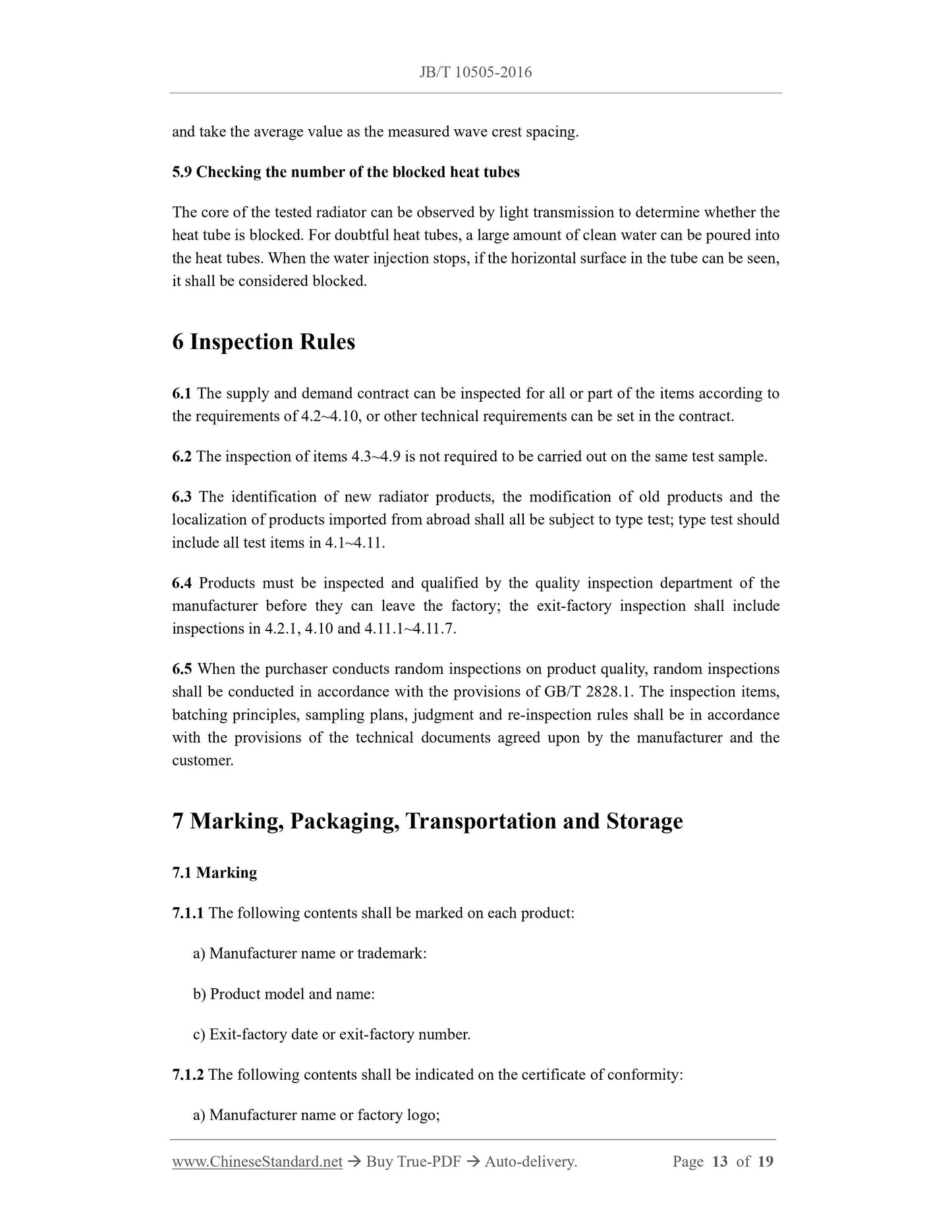

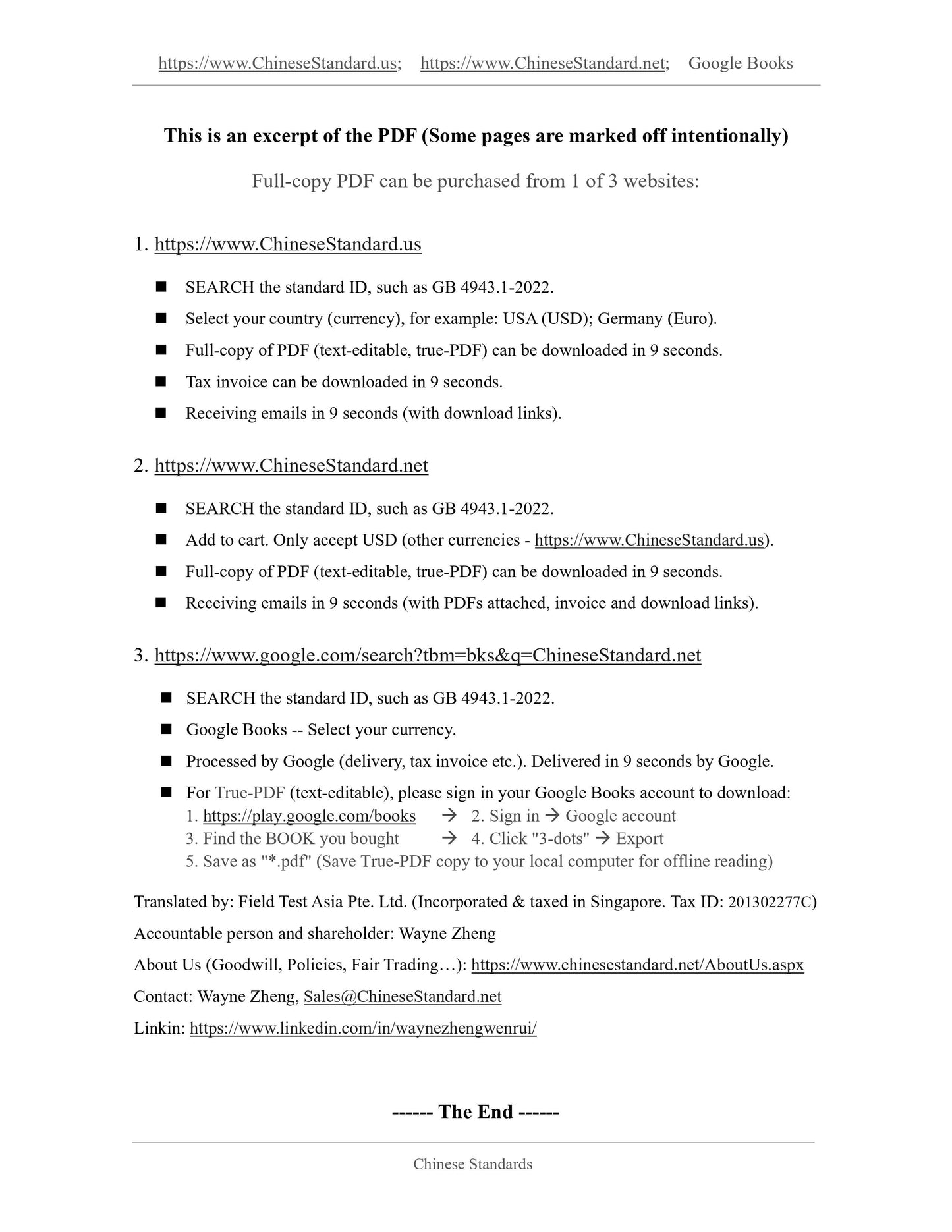