1
/
of
12
PayPal, credit cards. Download editable-PDF and invoice in 1 second!
JB/T 5000.15-2007 English PDF (JB/T5000.15-2007)
JB/T 5000.15-2007 English PDF (JB/T5000.15-2007)
Regular price
$145.00 USD
Regular price
Sale price
$145.00 USD
Unit price
/
per
Shipping calculated at checkout.
Couldn't load pickup availability
Delivery: 3 seconds. Download true-PDF + Invoice.
Get QUOTATION in 1-minute: Click JB/T 5000.15-2007
Historical versions: JB/T 5000.15-2007
Preview True-PDF (Reload/Scroll if blank)
JB/T 5000.15-2007: Heavy mechanical general techniques and standards. Part 15: Non-destructive inspection of forged steel
JB/T 5000.15-2007
JB
MECHANICAL INDUSTRY STANDARD
OF THE PEOPLE’S REPUBLIC OF CHINA
ICS 25.120.20
H 90
Registration number. 21709-2007
Replacing JB/T 5000.15-1998
Heavy mechanical general techniques and standards -
Part 15. Non-destructive inspection of forged steel
ISSUED ON. AUGUST 28, 2007
IMPLEMENTED ON. FEBRUARY 01, 2008
Issued by. National Development and Reform Commission of PRC
Table of Contents
Foreword ... 4
1 Scope ... 6
2 Normative references ... 6
3 Terms and definitions ... 7
4 General requirements ... 8
4.1 Principles of selection ... 8
4.2 Documentation of testing ... 8
4.3 Testing personnel ... 8
5 Ultrasonic testing and its quality grade ... 9
5.1 Basis of testing ... 9
5.2 Instrument and equipment ... 9
5.3 Probe ... 9
5.4 Coupling agent ... 10
5.5 Test block ... 10
5.6 Test of system’s combined performance ... 10
5.7 Preparation of forgings before testing ... 11
5.8 Testing procedures ... 11
5.9 Record of defects ... 15
5.10 Quality grade ... 15
5.11 Ultrasonic testing report ... 16
6 Magnetic-powder testing and its quality grade ... 17
6.1 Basis of testing ... 17
6.2 Requirements of testing surface ... 17
6.3 Testing period ... 18
6.4 Equipment and magnetic-powder ... 18
6.5 Magnetization method ... 19
6.6 Test piece for sensitivity ... 22
6.7 Magnetic-field’s strength ... 23
6.8 Application of magnetic-powder and magnetic suspension ... 27
6.9 Demagnetization ... 28
6.10 Retesting ... 28
6.11 Classification of magnetic trace ... 28
6.12 Recording limits and acceptance criteria ... 30
6.13 Magnetic-powder test report ... 30
7 Penetration testing and its quality grades ... 31
7.1 Basis of testing ... 31
7.2 Requirements of testing surface ... 31
7.3 Testing materials ... 31
7.4 Control test block ... 32
7.5 Classification and selection of penetration testing methods ... 33
7.6 Operating procedures ... 34
7.7 Classification of liquid-trace ... 38
7.8 Recording limits and acceptance criteria ... 38
7.9 Penetration test report ... 40
Appendix A (Normative) Transverse-wave testing method and quality
acceptance requirements for forging steel ... 41
A.1 Scope of application ... 41
A.2 Probe ... 41
A.3 Test block for verification ... 41
A.4 Adjustment of testing sensitivity ... 43
A.5 Testing operation ... 43
A.6 Recording and evaluation ... 43
Heavy mechanical general techniques and standards -
Part 15. Non-destructive inspection of forged steel
1 Scope
This Part of the JB/T 5000 specifies the ultrasonic, magnetic-powder and
penetration testing methods and quality grades of forged steel.
This Part applies to non-destructive testing of forged steel for heavy machinery.
Non-destructive testing methods as specified in this Part may involve
hazardous materials, operations and equipment, so the non-destructive testing
personnel shall comply with relevant safety and health regulations.
The method, location, quality grade of the non-destructive testing of forgings
shall be indicated in the forging’s drawings, technical documents and technical
conditions of the ordering.
2 Normative references
The provisions in following documents become the provisions of this Part
through reference in this Part of JB/T 5000. For the dated references, the
subsequent amendments (excluding corrections) or revisions do not apply to
this Part; however, parties who reach an agreement based on this Part are
encouraged to study if the latest versions of these documents are applicable.
For undated references, the latest version of the referenced document applies.
GB/T 5097 Indirect assessment method for black light source (GB/T 5097-
1985, eqv 3059.1974)
GB/T 11259 Standard practice for fabrication and control of steel reference
blocks used in ultrasonic inspection (GB/T 11259-1999, eqv ASTM
E428.1992)
JB/T 8290 Magnetic-powder flaw detectors
JB/T 9214 Test methods for evaluating performance of A-mode ultrasonic
flaw detection using pulse echo technique
JB/T 9216 Methods for controlling the quality of liquid penetrant materials
JB/T 10061 Commonly used specification for A-mode ultrasonic flaw
4 General requirements
4.1 Principles of selection
4.1.1 The selection of testing method and quality acceptance level shall be
determined according to the specific use and type of forgings, meet the
requirements of the corresponding technical documents.
4.1.2 For ferromagnetic forgings which requires surface testing, it shall give
priority to the magnetic-powder testing method. If the magnetic-powder test
cannot be used due to structural shape and resource conditions, etc., it selects
the penetration testing.
4.2 Documentation of testing
4.2.1 When forgings are tested in accordance with this Part, if necessary, it may
follow the provisions of this Part to establish a non-destructive testing
procedures which complies with the relevant specifications.
4.2.2 The testing procedures and results shall be correct, complete and signed
and approved by the responsible personnel. The period of storage of test
records, reports, etc. shall not be less than five years. After five years, if the
user needs it, it can be transferred to the user for safekeeping.
4.2.3 In the testing documentation, the corresponding qualification grades and
validity period of the testing items undertaken by the testing personnel shall be
recorded.
4.2.4 The performance of the instruments and equipment used for the testing
shall be periodically calibrated and have calibration records, which can only be
used after passing the calibration.
4.3 Testing personnel
4.3.1 Any person engaged in non-destructive testing shall hold the
corresponding qualification certificate issued by the relevant state department.
4.3.2 Non-destructive testing personnel’s technical grades are divided into high,
medium and primary. Personnel of all technical grades who have obtained
different non-destructive testing methods can only engage in non-destructive
testing corresponding to this grade and bear corresponding technical
responsibilities.
defects.
5.3.4 Probe’s performance test method is as specified in JB/T 10062.
5.4 Coupling agent
5.4.1 The coupling agent shall have good wettability. It may use the oil, glycerin,
paste or water of the full-loss system as a coupling agent. For finished forgings,
it is recommended to use the oil L-AN46 of the full-loss system as the coupling
agent.
5.4.2 Different coupling agents cannot be compared. Therefore, the coupling
agents which are used for the performance test, sensitivity adjustment,
calibration of the testing system must be the same as the coupling agent used
in the testing.
5.5 Test block
5.5.1 The test block shall be made of the same or approximate acoustic
properties as the workpiece being tested. When the material is tested by a
straight probe, there shall be no defects greater than the equivalent diameter of
the Φ2 mm flat-bottom hole.
5.5.2 The reflector for calibration use may be flat-bottom hole and V-shaped
groove. When calibrating, the main sound-beam of the probe shall be aligned
with the reflector, perpendicular to the reflecting surface of the flat-bottom hole,
perpendicular to the axis of the V-shaped groove.
5.5.3 The dimensions of the test block shall be representative of the
characteristics of the workpie...
Get QUOTATION in 1-minute: Click JB/T 5000.15-2007
Historical versions: JB/T 5000.15-2007
Preview True-PDF (Reload/Scroll if blank)
JB/T 5000.15-2007: Heavy mechanical general techniques and standards. Part 15: Non-destructive inspection of forged steel
JB/T 5000.15-2007
JB
MECHANICAL INDUSTRY STANDARD
OF THE PEOPLE’S REPUBLIC OF CHINA
ICS 25.120.20
H 90
Registration number. 21709-2007
Replacing JB/T 5000.15-1998
Heavy mechanical general techniques and standards -
Part 15. Non-destructive inspection of forged steel
ISSUED ON. AUGUST 28, 2007
IMPLEMENTED ON. FEBRUARY 01, 2008
Issued by. National Development and Reform Commission of PRC
Table of Contents
Foreword ... 4
1 Scope ... 6
2 Normative references ... 6
3 Terms and definitions ... 7
4 General requirements ... 8
4.1 Principles of selection ... 8
4.2 Documentation of testing ... 8
4.3 Testing personnel ... 8
5 Ultrasonic testing and its quality grade ... 9
5.1 Basis of testing ... 9
5.2 Instrument and equipment ... 9
5.3 Probe ... 9
5.4 Coupling agent ... 10
5.5 Test block ... 10
5.6 Test of system’s combined performance ... 10
5.7 Preparation of forgings before testing ... 11
5.8 Testing procedures ... 11
5.9 Record of defects ... 15
5.10 Quality grade ... 15
5.11 Ultrasonic testing report ... 16
6 Magnetic-powder testing and its quality grade ... 17
6.1 Basis of testing ... 17
6.2 Requirements of testing surface ... 17
6.3 Testing period ... 18
6.4 Equipment and magnetic-powder ... 18
6.5 Magnetization method ... 19
6.6 Test piece for sensitivity ... 22
6.7 Magnetic-field’s strength ... 23
6.8 Application of magnetic-powder and magnetic suspension ... 27
6.9 Demagnetization ... 28
6.10 Retesting ... 28
6.11 Classification of magnetic trace ... 28
6.12 Recording limits and acceptance criteria ... 30
6.13 Magnetic-powder test report ... 30
7 Penetration testing and its quality grades ... 31
7.1 Basis of testing ... 31
7.2 Requirements of testing surface ... 31
7.3 Testing materials ... 31
7.4 Control test block ... 32
7.5 Classification and selection of penetration testing methods ... 33
7.6 Operating procedures ... 34
7.7 Classification of liquid-trace ... 38
7.8 Recording limits and acceptance criteria ... 38
7.9 Penetration test report ... 40
Appendix A (Normative) Transverse-wave testing method and quality
acceptance requirements for forging steel ... 41
A.1 Scope of application ... 41
A.2 Probe ... 41
A.3 Test block for verification ... 41
A.4 Adjustment of testing sensitivity ... 43
A.5 Testing operation ... 43
A.6 Recording and evaluation ... 43
Heavy mechanical general techniques and standards -
Part 15. Non-destructive inspection of forged steel
1 Scope
This Part of the JB/T 5000 specifies the ultrasonic, magnetic-powder and
penetration testing methods and quality grades of forged steel.
This Part applies to non-destructive testing of forged steel for heavy machinery.
Non-destructive testing methods as specified in this Part may involve
hazardous materials, operations and equipment, so the non-destructive testing
personnel shall comply with relevant safety and health regulations.
The method, location, quality grade of the non-destructive testing of forgings
shall be indicated in the forging’s drawings, technical documents and technical
conditions of the ordering.
2 Normative references
The provisions in following documents become the provisions of this Part
through reference in this Part of JB/T 5000. For the dated references, the
subsequent amendments (excluding corrections) or revisions do not apply to
this Part; however, parties who reach an agreement based on this Part are
encouraged to study if the latest versions of these documents are applicable.
For undated references, the latest version of the referenced document applies.
GB/T 5097 Indirect assessment method for black light source (GB/T 5097-
1985, eqv 3059.1974)
GB/T 11259 Standard practice for fabrication and control of steel reference
blocks used in ultrasonic inspection (GB/T 11259-1999, eqv ASTM
E428.1992)
JB/T 8290 Magnetic-powder flaw detectors
JB/T 9214 Test methods for evaluating performance of A-mode ultrasonic
flaw detection using pulse echo technique
JB/T 9216 Methods for controlling the quality of liquid penetrant materials
JB/T 10061 Commonly used specification for A-mode ultrasonic flaw
4 General requirements
4.1 Principles of selection
4.1.1 The selection of testing method and quality acceptance level shall be
determined according to the specific use and type of forgings, meet the
requirements of the corresponding technical documents.
4.1.2 For ferromagnetic forgings which requires surface testing, it shall give
priority to the magnetic-powder testing method. If the magnetic-powder test
cannot be used due to structural shape and resource conditions, etc., it selects
the penetration testing.
4.2 Documentation of testing
4.2.1 When forgings are tested in accordance with this Part, if necessary, it may
follow the provisions of this Part to establish a non-destructive testing
procedures which complies with the relevant specifications.
4.2.2 The testing procedures and results shall be correct, complete and signed
and approved by the responsible personnel. The period of storage of test
records, reports, etc. shall not be less than five years. After five years, if the
user needs it, it can be transferred to the user for safekeeping.
4.2.3 In the testing documentation, the corresponding qualification grades and
validity period of the testing items undertaken by the testing personnel shall be
recorded.
4.2.4 The performance of the instruments and equipment used for the testing
shall be periodically calibrated and have calibration records, which can only be
used after passing the calibration.
4.3 Testing personnel
4.3.1 Any person engaged in non-destructive testing shall hold the
corresponding qualification certificate issued by the relevant state department.
4.3.2 Non-destructive testing personnel’s technical grades are divided into high,
medium and primary. Personnel of all technical grades who have obtained
different non-destructive testing methods can only engage in non-destructive
testing corresponding to this grade and bear corresponding technical
responsibilities.
defects.
5.3.4 Probe’s performance test method is as specified in JB/T 10062.
5.4 Coupling agent
5.4.1 The coupling agent shall have good wettability. It may use the oil, glycerin,
paste or water of the full-loss system as a coupling agent. For finished forgings,
it is recommended to use the oil L-AN46 of the full-loss system as the coupling
agent.
5.4.2 Different coupling agents cannot be compared. Therefore, the coupling
agents which are used for the performance test, sensitivity adjustment,
calibration of the testing system must be the same as the coupling agent used
in the testing.
5.5 Test block
5.5.1 The test block shall be made of the same or approximate acoustic
properties as the workpiece being tested. When the material is tested by a
straight probe, there shall be no defects greater than the equivalent diameter of
the Φ2 mm flat-bottom hole.
5.5.2 The reflector for calibration use may be flat-bottom hole and V-shaped
groove. When calibrating, the main sound-beam of the probe shall be aligned
with the reflector, perpendicular to the reflecting surface of the flat-bottom hole,
perpendicular to the axis of the V-shaped groove.
5.5.3 The dimensions of the test block shall be representative of the
characteristics of the workpie...
Share
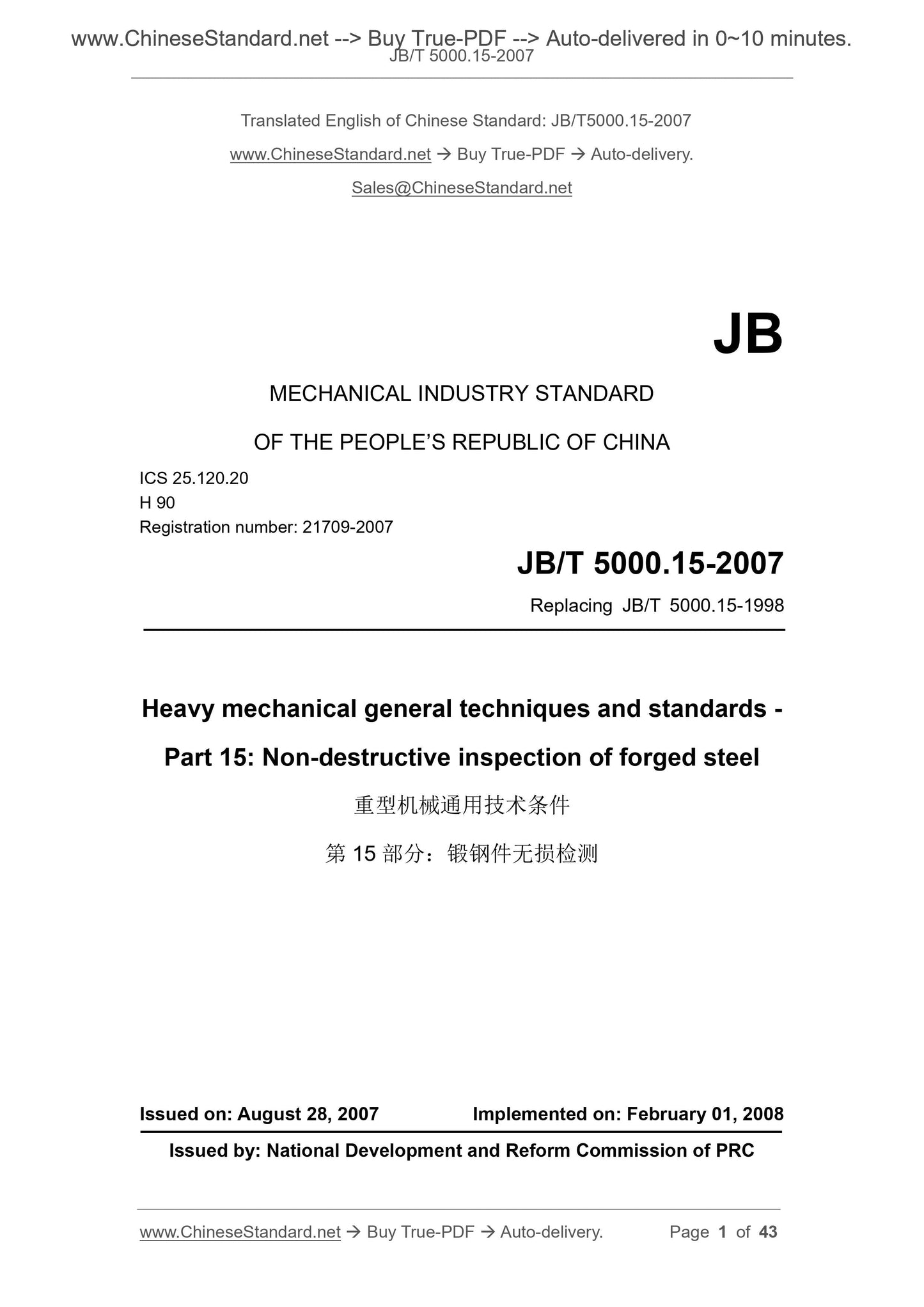
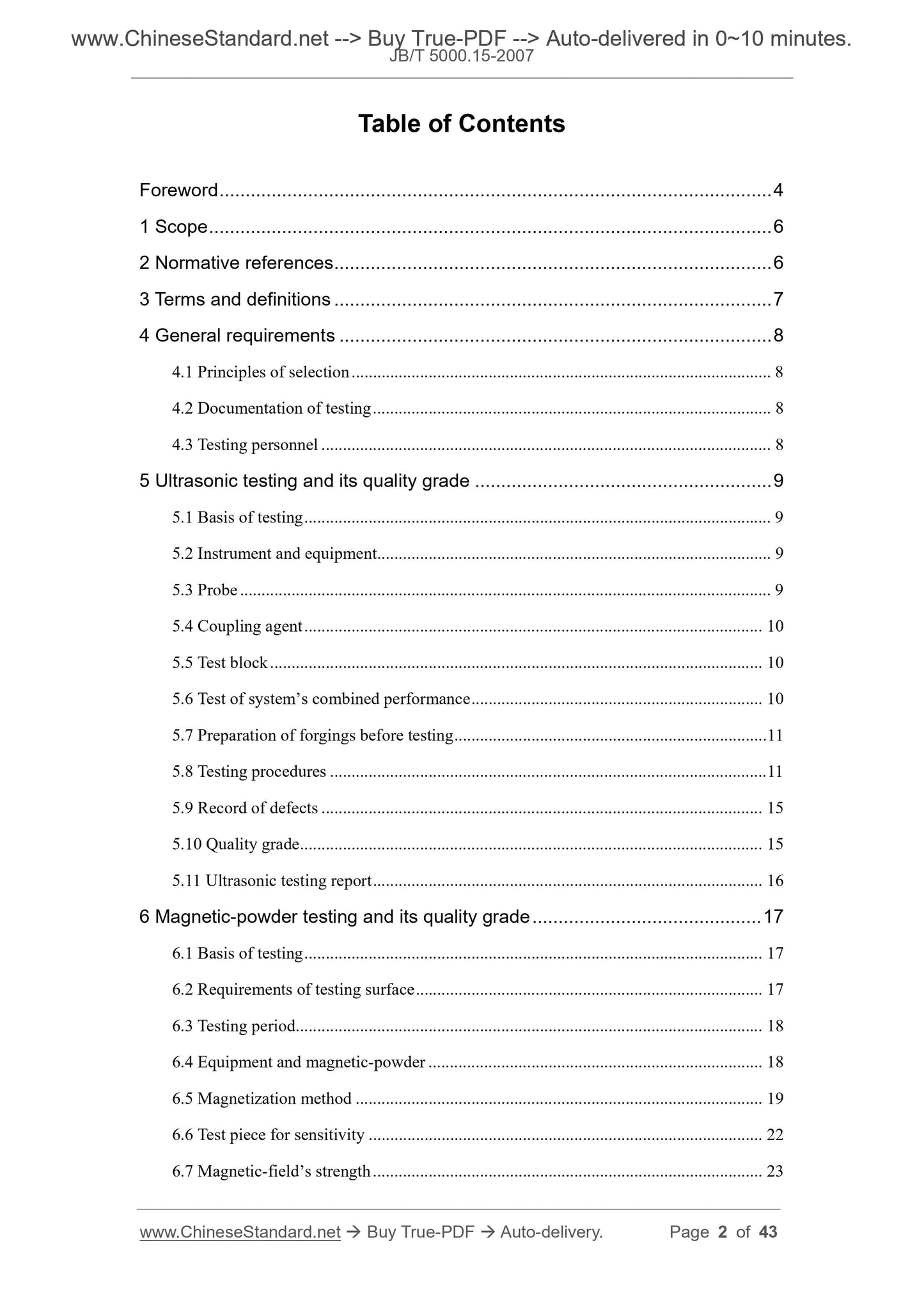
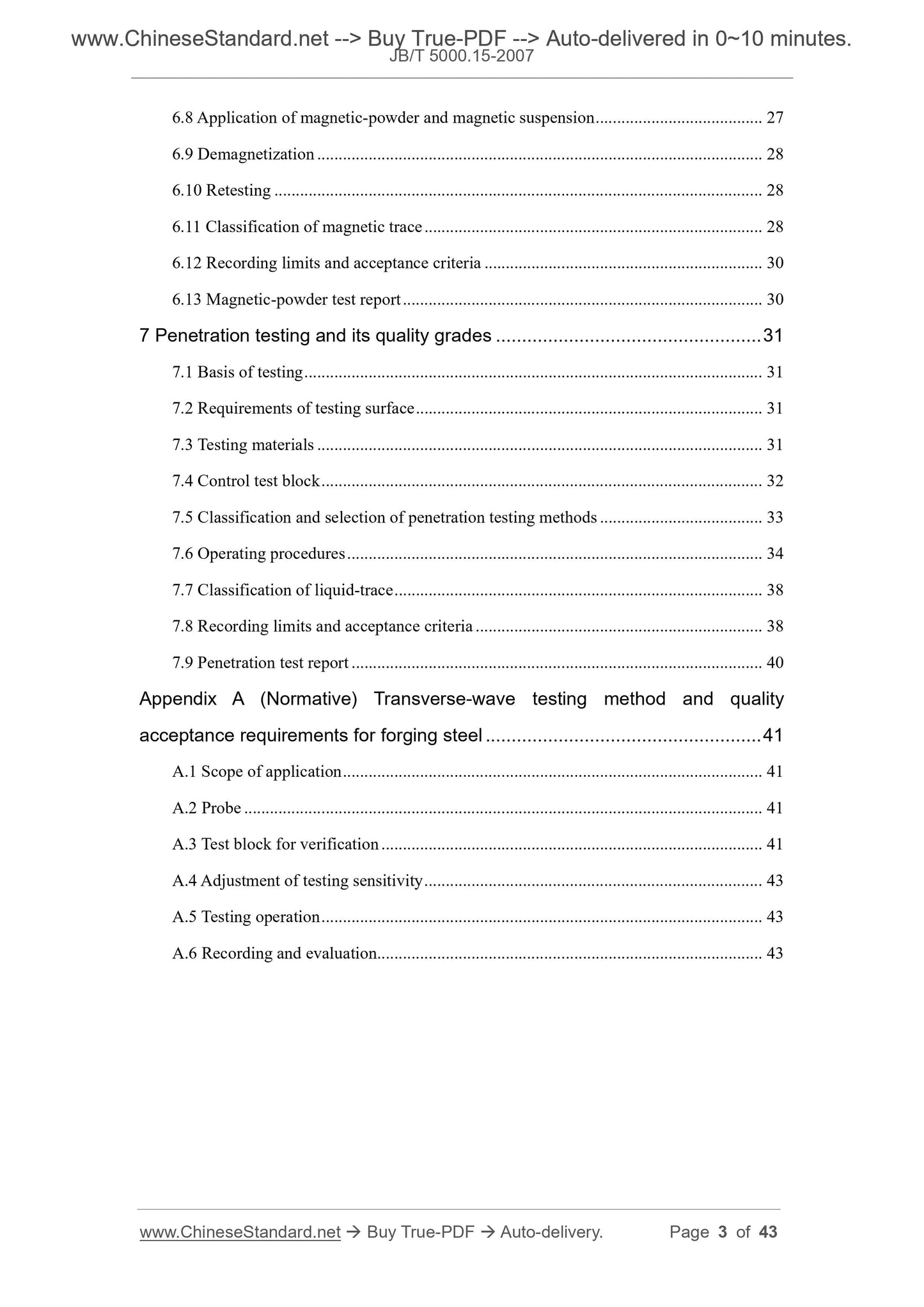
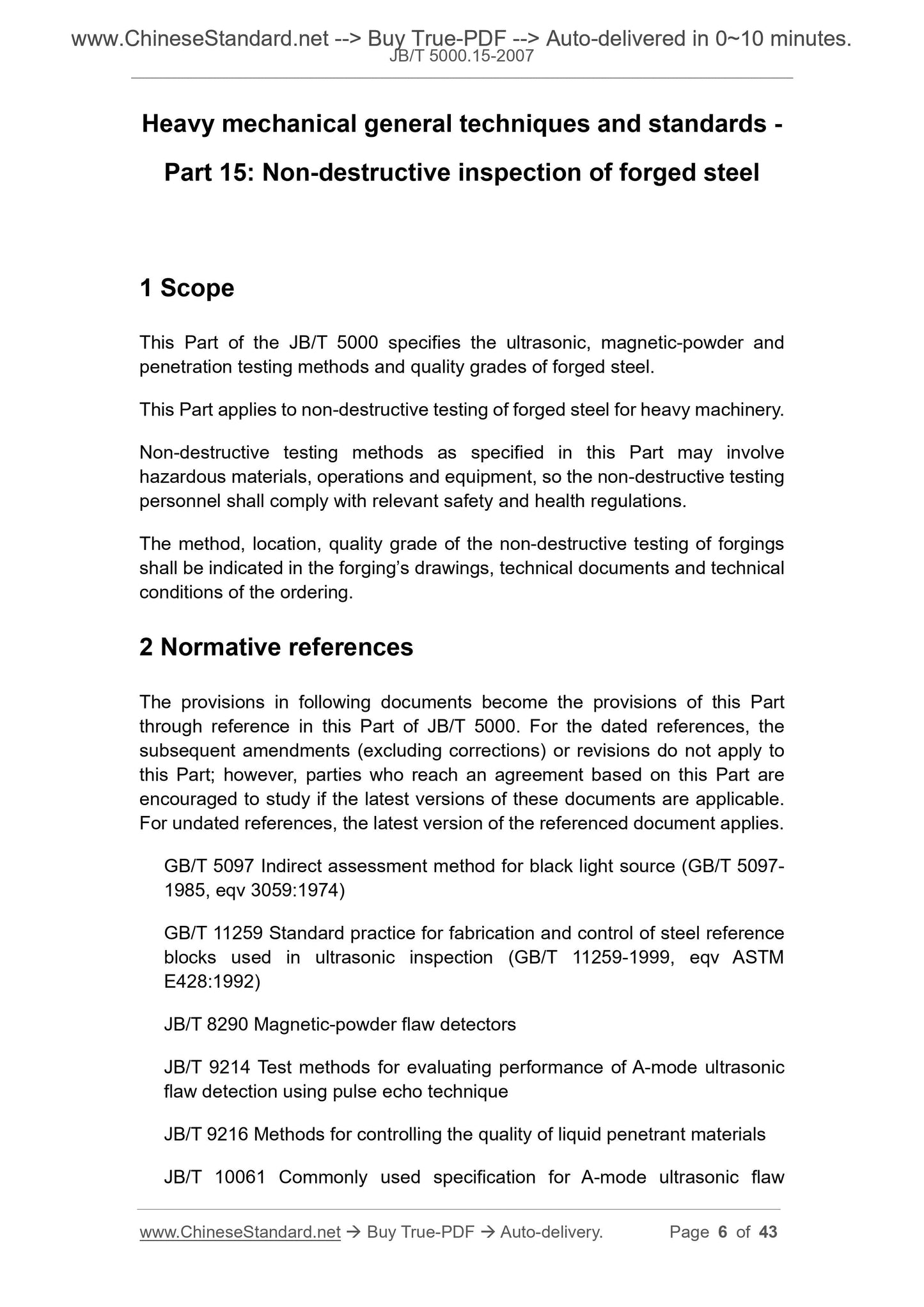
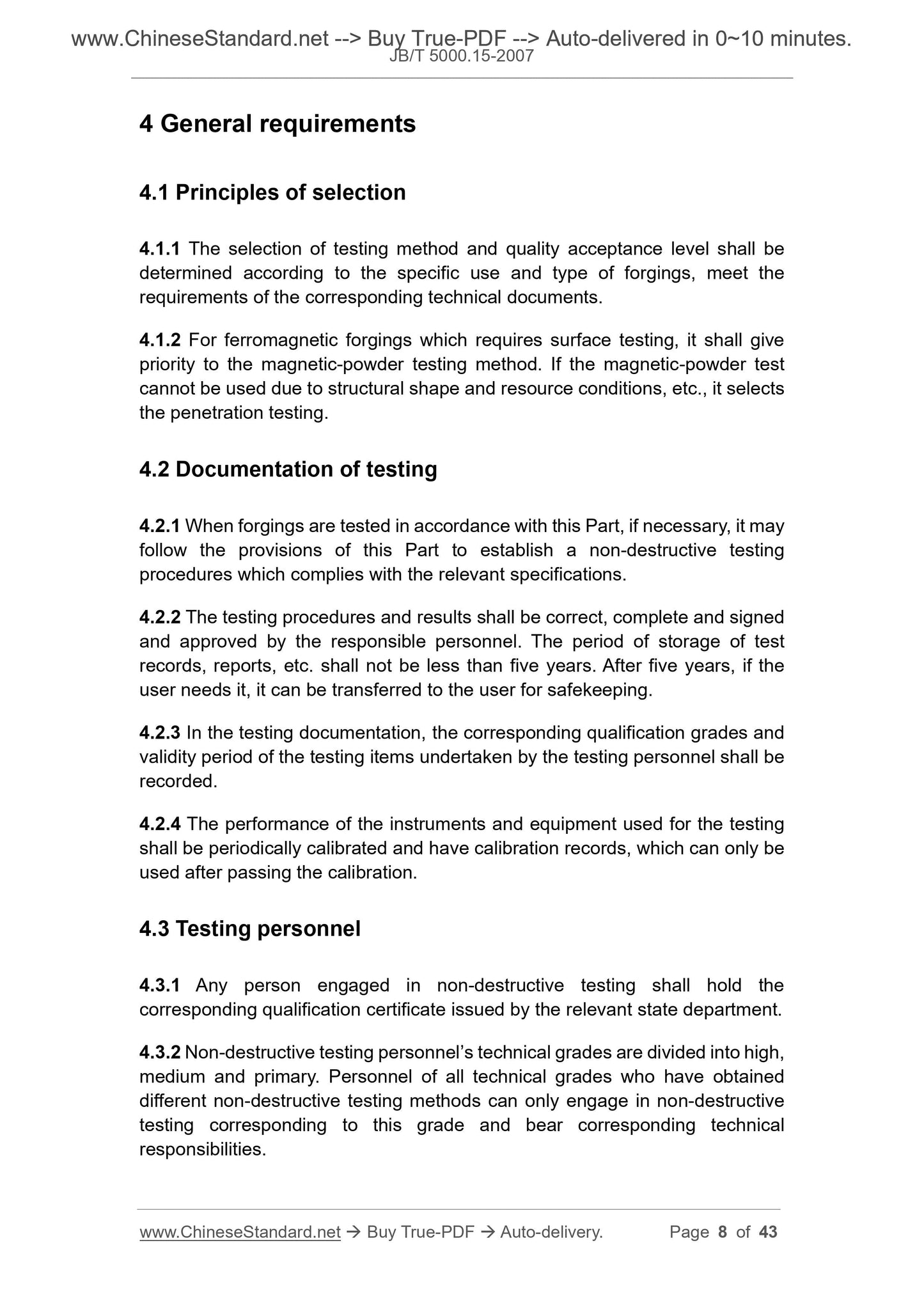
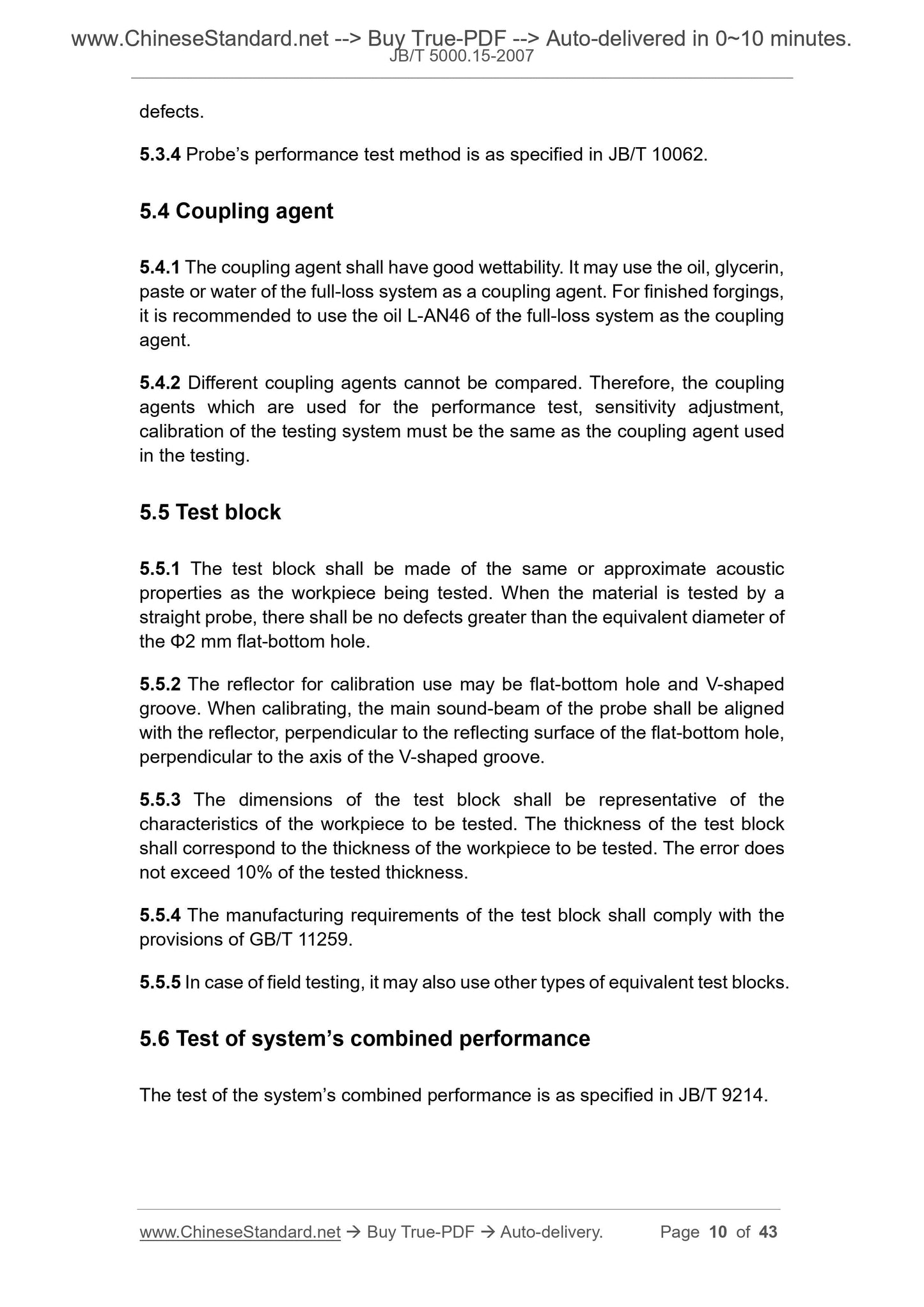
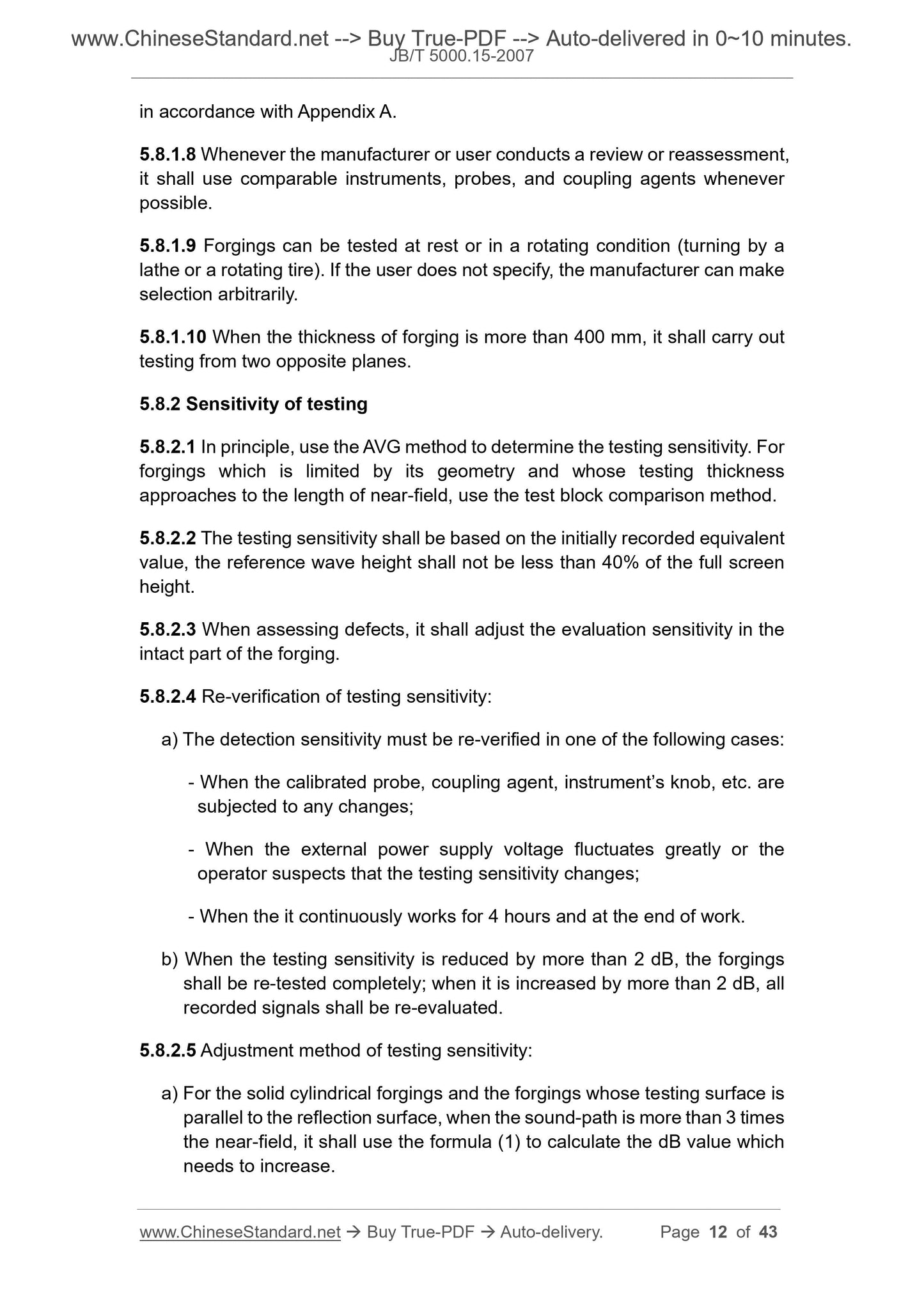
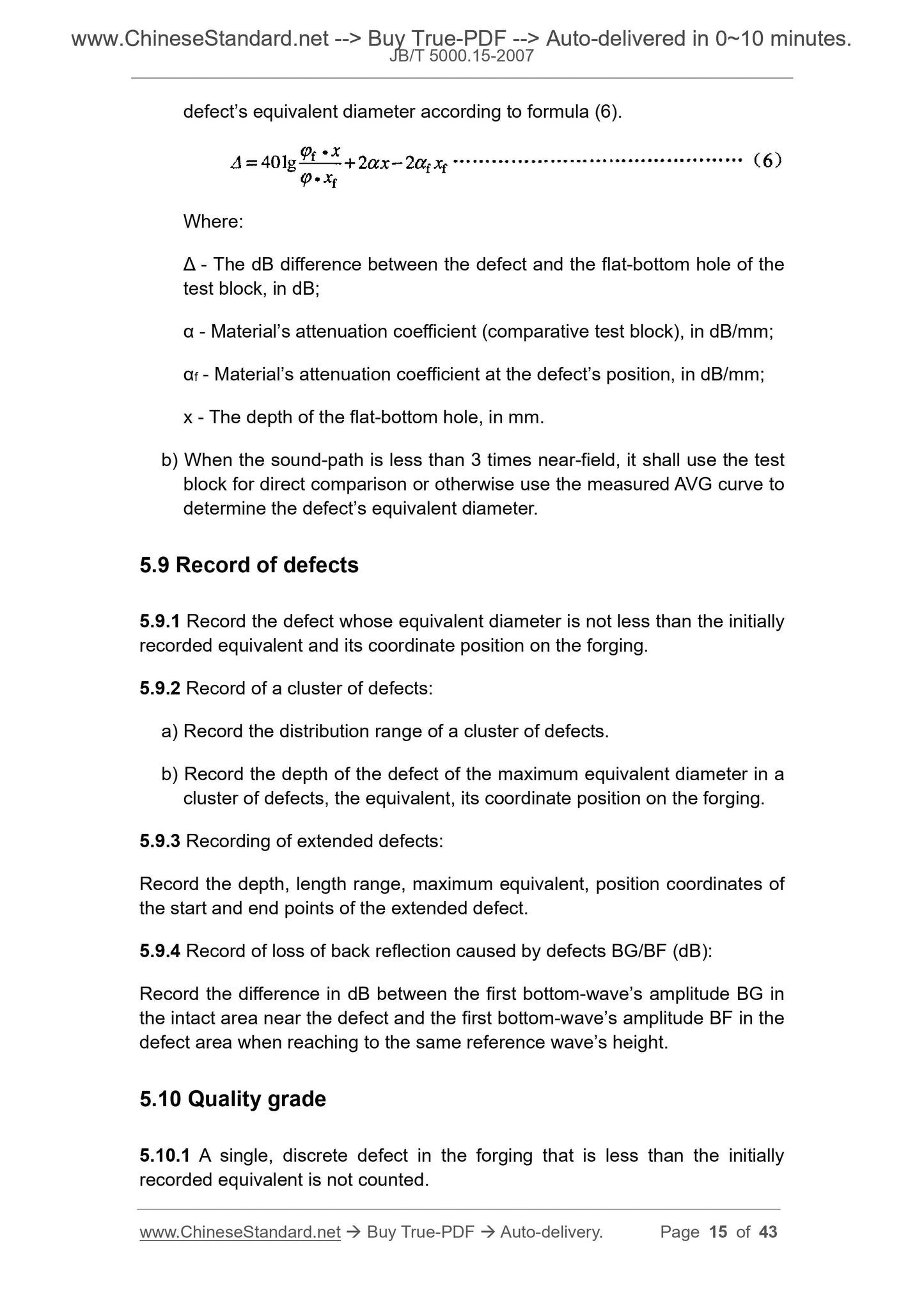
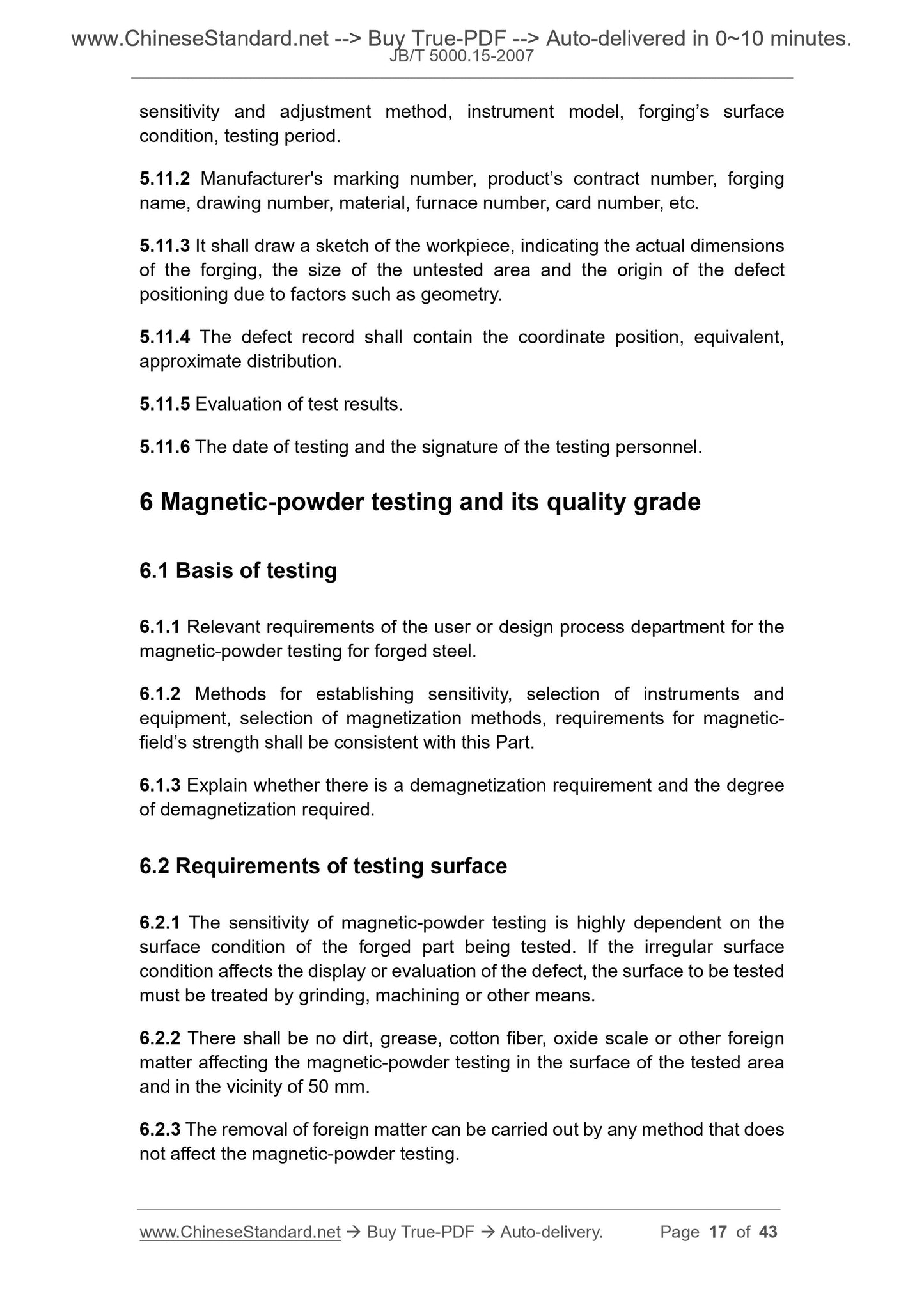
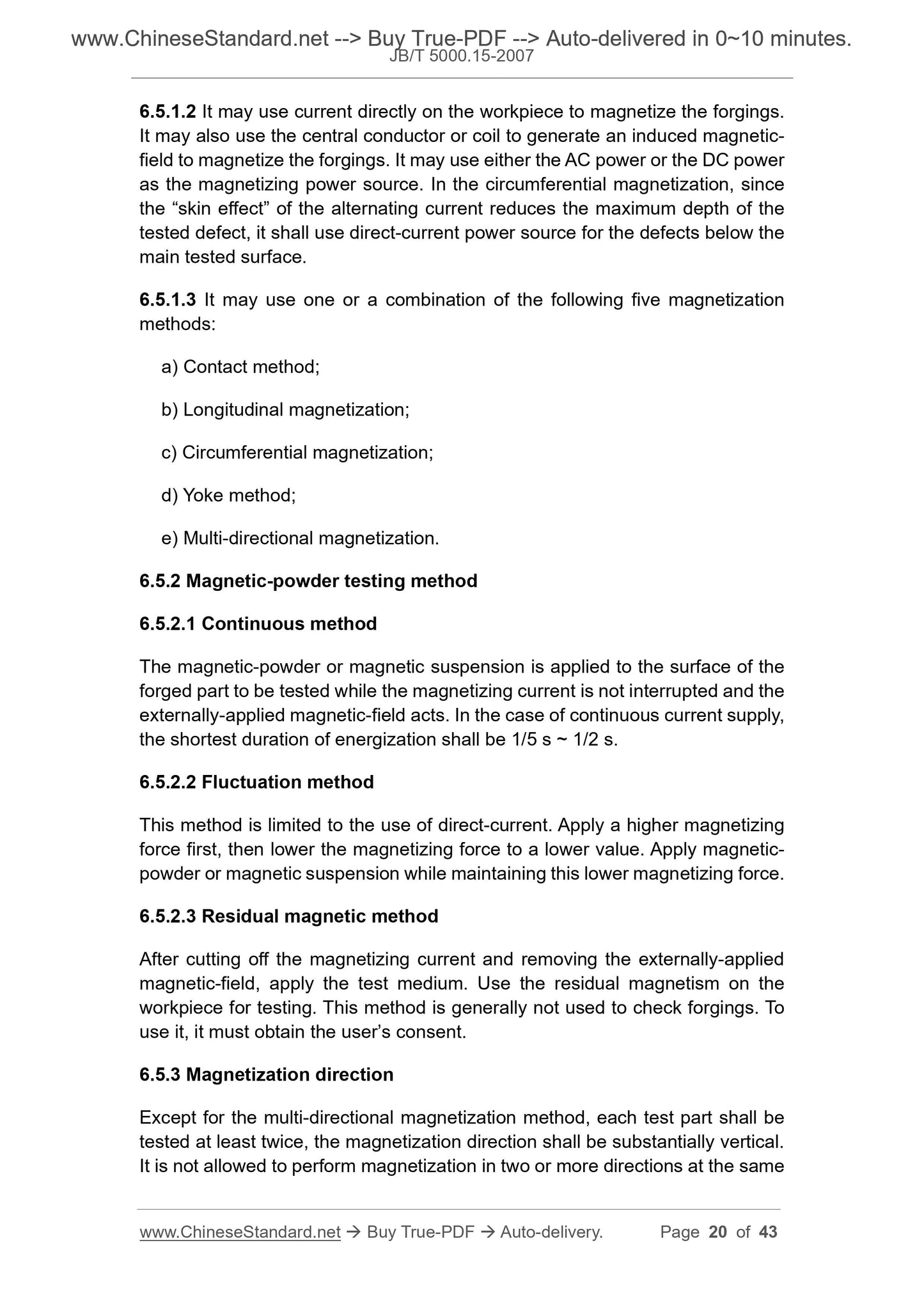
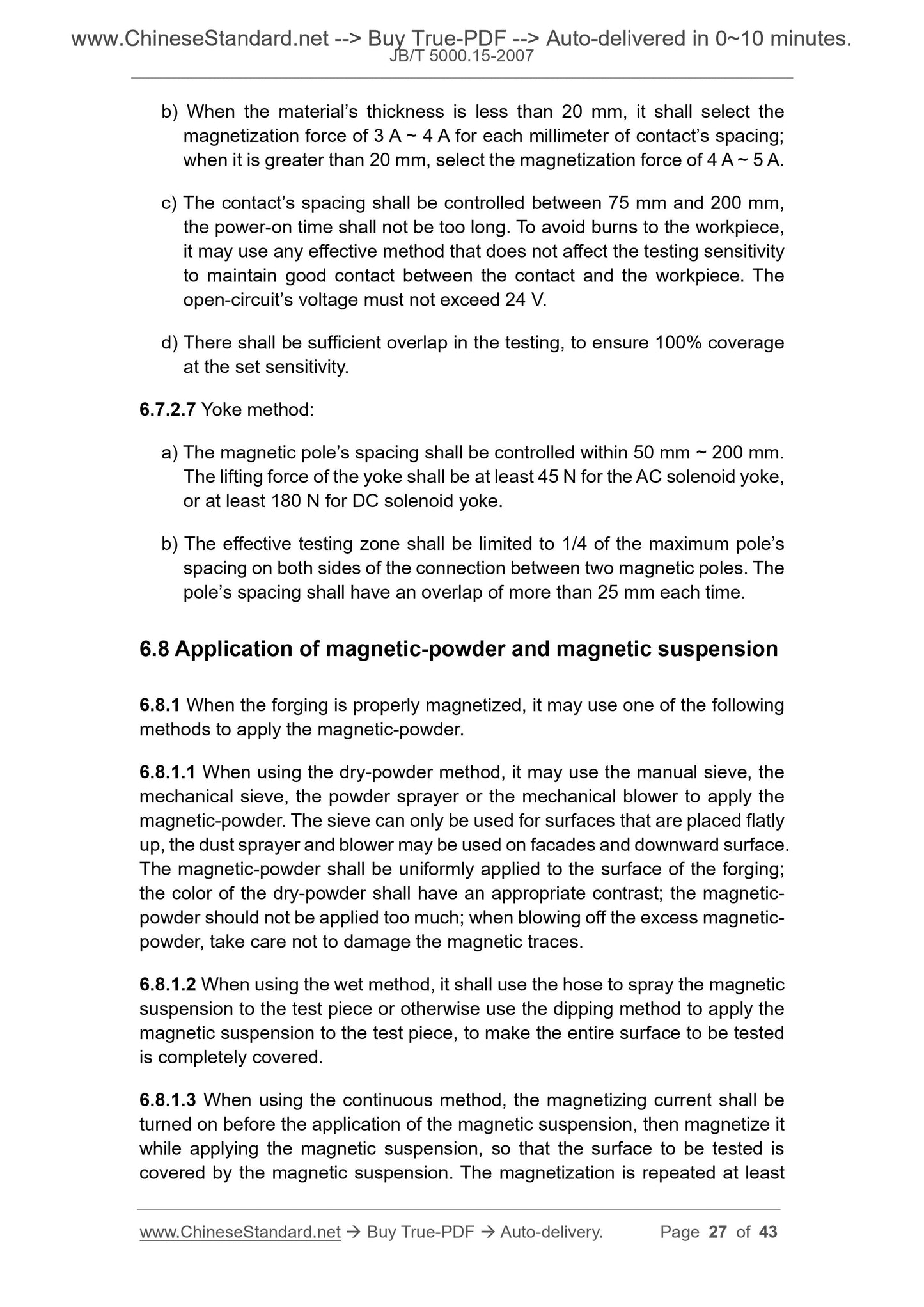
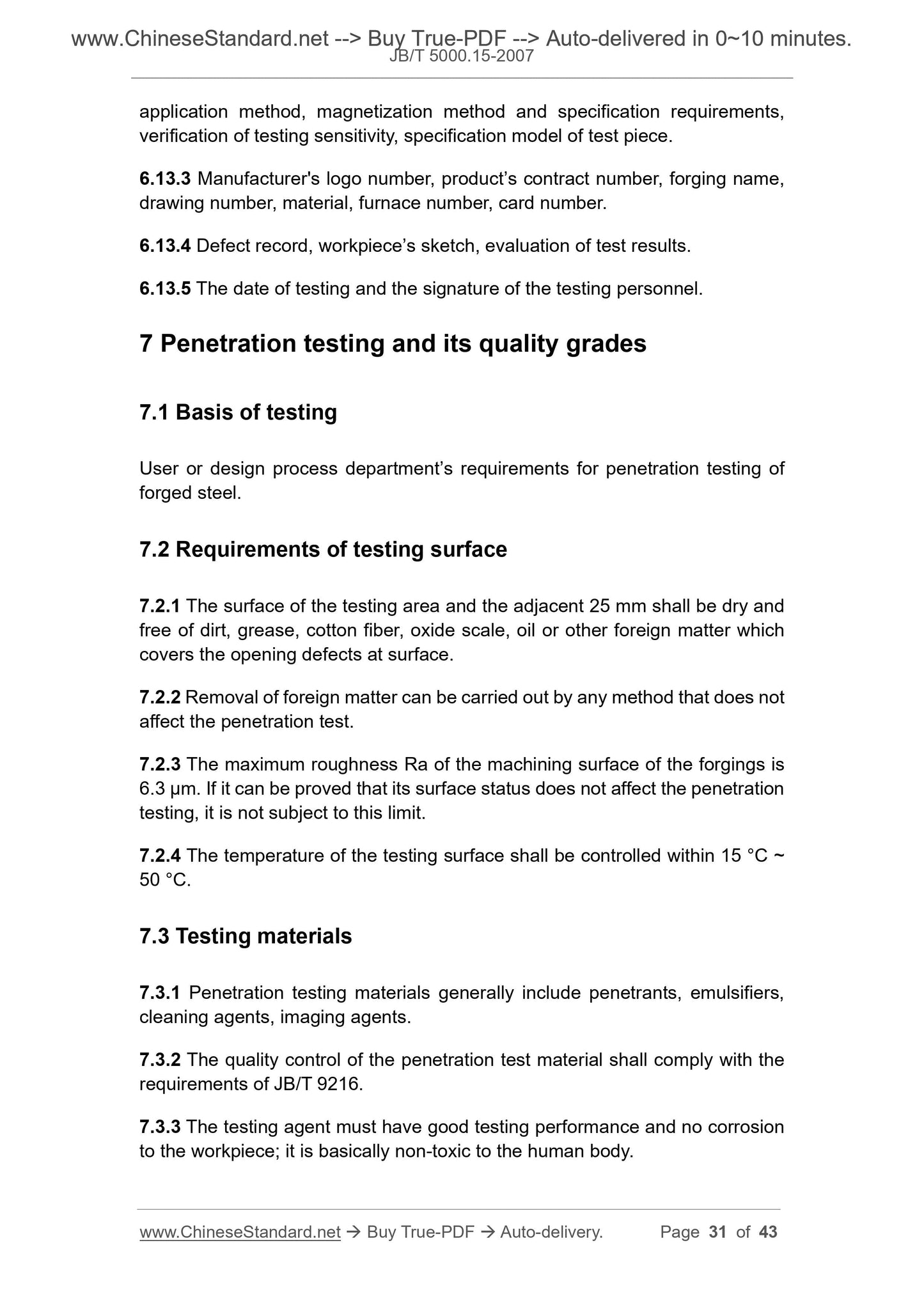