1
/
of
12
PayPal, credit cards. Download editable-PDF & invoice in 1 second!
YY/T 0681.4-2021 English PDF (YY/T0681.4-2021)
YY/T 0681.4-2021 English PDF (YY/T0681.4-2021)
Regular price
$215.00 USD
Regular price
Sale price
$215.00 USD
Unit price
/
per
Shipping calculated at checkout.
Couldn't load pickup availability
Delivery: 3 seconds. Download true-PDF + Invoice.
Get Quotation: Click YY/T 0681.4-2021 (Self-service in 1-minute)
Historical versions (Master-website): YY/T 0681.4-2021
Preview True-PDF (Reload/Scroll-down if blank)
YY/T 0681.4-2021: Test methods for sterile medical device package - Part 4: Detecting seal leaks in porous packages by dye penetration
YY/T 0681.4-2021
Test methods for sterile medical device package - Part 4.Detecting seal leaks in porous packages by dye penetration
ICS 11.080.040
C31
People's Republic of China Pharmaceutical Industry Standards
Replace YY/T 0681.4-2010
Sterile medical device packaging test methods
Part 4.Determination of Dyeing Solution Penetration Method
Seal leakage of breathable packaging
Released on 2021-03-09
2022-04-01 implementation
Issued by the National Medical Products Administration
Preface
YY/T 0681 "Test Methods for Packaging of Sterile Medical Devices" will consist of the following parts.
---Part 1.Guide to accelerated aging test;
---Part 2.Sealing strength of soft barrier materials;
---Part 3.Unconstrained packaging resists internal pressure damage;
---Part 4.Dyeing liquid penetration method to determine the seal leakage of breathable packaging;
---Part 5.Internal pressure method to detect gross leaks (bubble method);
---Part 6.Evaluation of the chemical resistance of printing inks and coatings on flexible packaging materials;
---Part 7.Use tape to evaluate the adhesion of ink or coating on flexible packaging materials;
---Part 8.Determination of the weight of the adhesive layer;
---Part 9.Seal burst test of flexible packaging by air pressure inside restraint plate;
---Part 10.Microbial barrier grading test for breathable packaging materials;
---Part 11.Visually inspect the seal integrity of medical packaging;
---Part 12.Anti-rubbing of soft barrier film;
---Part 13.Soft barrier film and composite film resistance to slow puncture;
---Part 14.Test of moisture and dry microbial barrier of breathable packaging materials;
---Part 15.Performance test of transport containers and systems;
---Part 16.Test of Climate Resilience of Packaging System;
---Part 17.Microbial barrier test of aerosol filtration method for breathable packaging materials;
--- Part 18.Non-destructive inspection of packaging leaks by the vacuum attenuation method.
This part is part 4 of YY/T 0681.
This section was drafted in accordance with the rules given in GB/T 1.1-2009.
This part replaces YY/T 0681.4-2010 "Test Methods for Sterile Medical Device Packaging Part 4.Determination of Air Permeability by Dyeing Liquid Penetration Method
Compared with YY/T 0681.4-2010, the main technical changes are as follows.
---Modified the content in the "Scope" (see Chapter 1, Chapter 1 of the.2010 edition);
---Modified the definition of "channel" (see 2.3,.2010 edition 2.3);
--- Deleted the content of data comparability and puncture attention (see 3.4 and 3.6 in the.2010 edition);
---The content of test instruments has been added (see 4.3, 4.4, 4.5);
---Added sampling (see Chapter 7);
---Added edge immersion method and drip method (see 9.2, 9.3);
---Added the precision and bias content of Method B and Method C (see Appendix A);
---Added false positive guidelines (see Appendix B).
Please note that some of the contents of this document may involve patents. The issuing agency of this document is not responsible for identifying these patents.
This part was proposed by the State Drug Administration.
This part is under the jurisdiction of the National Standardization Technical Committee for Medical Infusion Devices (SAC/TC106).
Drafting organizations of this section. Shandong Medical Device Product Quality Inspection Center, Minnesota Mining Manufacturing Medical Equipment (Shanghai) Co., Ltd.
Company, Henan Yadu Industrial Co., Ltd., Shandong Baiduuoan Medical Equipment Co., Ltd., Shandong Kangli Medical Equipment Technology Co., Ltd.
The main drafters of this section. Wang Dongwei, Zheng Yang, Zhang Xianglong, Duan Shuxia, Zhang Jing, Zhang Haijun, Xiong Wei, Liu Zhuang.
This section was first released in December.2010, and this is the first revision.
Sterile medical device packaging test methods
Part 4.Determination of Dyeing Solution Penetration Method
Seal leakage of breathable packaging
1 Scope
This part of YY/T 0681 specifies the test method for determining the leakage of air-permeable packaging by the dye penetration method.
This section applies to the detection of transparent materials and air-permeable materials in the seal of the package greater than or equal to 50μm channel.
This section does not apply to breathable materials that are dyed due to capillary action within 5s, nor does it apply to the contrast between dyeing liquid and opaque materials.
The big situation.
2 Terms and definitions
The following terms and definitions apply to this document.
2.1
Wicking
The liquid moves into the fibrous material.
2.2
Dyepenetrant
A mixed aqueous solution of a coloring agent and a surfactant, designed to be used before capillary action (which masks the existence of defects)
The segment is used to indicate the location of the defect.
2.3
Channel
Any undamaged path across the entire width of the intended sealing area.
3 Significance and application
3.1 Harmful microorganisms or particle contamination may enter the device through leakage. These leaks often occur between the same or different materials
The seal. These leaks may also be caused by holes in the material itself.
3.2 The dye penetration method can only be used to detect independent leaks at the seal of the package, and it is not applicable to the multiple found in the gas-permeable packaging materials.
Small leaks, which require other techniques to detect.
3.3 As far as the specific packaging is concerned, what kind of leakage is considered harmful, there is no consensus yet. However, because this test is used
To detect leakage at the seal, any signs of leakage are usually judged as unqualified.
3.4 The dyeing solution will penetrate into the breathable material over time under capillary action, but this will generally not occur within the longest recommended time (generally not
More than 20s). The dye will not discolor the surface of the material before capillary action occurs. Appendix B describes capillary action and identifying false positives
guide.
4 Instruments
4.1 Tools to destroy packaging materials, such as scissors (9.1 Method A).
4.2 Dyeing solution dispenser, such as a straw or a syringe that can be used to inject dyeing solution (9.1 Method A).
4.3 Container for dyeing liquid (9.2 Method B).
4.4 Scissors or other cutting tools (9.2 Method B).
4.5 Eye dropper or pipette (9.3 Method C).
4.6 A microscope or an optical magnifying glass capable of magnifying 5-20 times.
4.7 The dyeing solution aqueous solution includes, according to the mass fraction.
Capillary agent. TRITONX-100 0.5%
Indicator. toluidine blue 0.05%
Carrier. water 99.45%
Note. The solution is uniform. If precipitation is found, this solution needs to be replaced.
Other colorants or fluorescent agents can also replace toluidine blue, but their precision and bias must be determined through experiments.
Because the capillary agent is viscous, it is best to prepare the solution by weighing a container containing about 10% of the required amount of aqueous solution.
Add the capillary agent to the water, stir or vibrate to mix. After the capillary agent is dispersed, add the rest of the water, and finally add toluidine blue.
5 Security measures
Using hypodermic needles and syringes to inject the dye solution into the package is a common method in this test, which may result in the use of contaminated needles.
It hurts the skin, so it is not recommended. Due to this hazard, it is recommended to use a hose to connect to the syringe through the opening cut with a cutting tool
Pour the staining solution into it.
6 Test sample
The test sample can be a package containing the product, an empty package, or a package with only heat-sealed edges. If it can be proved before the test does not affect the test
The test results can also be used with defective, simulated product packaging or substandard product packaging, but it needs to be recorded before the test.
7 sampling
The number of test samples should meet the test requirements. You need to be very cautious when excluding defective samples, as this may lead to biased results.
Note. Refer to GB/T 2828.1.
8 state adjustment
The packaging should be free of condensation or liquid water from other sources. If there is water in the seal defect, it will affect the detectability of the dyeing solution. If there is
Any indication that the package has been in contact with any liquid should be fully dried at its typical storage temperature before testing.
If state adjustment is required, it is recommended to perform state adjustment in a standard environment with a temperature of (23±2)℃ and a relative humidity of (50±2)%
Section, the state is adjusted for at least 24h before the test.
9 Procedure
9.1 Method A (injection method)
9.1.1 Pour enough dye solution into the package so that the dye solution can form a depth of about 5mm on the longest side of the package. When piercing the bag
When bagging and injecting dyeing solution, special care must be taken not to pierce or damage other surfaces of the package. Next to the virtual sample in the package
It is easier to penetrate. The sample will act as a bulge to separate the two sides of the packaging bag, reducing the risk of accidentally piercing the two sides.
9.1.2 Visually inspect the sealing area through the transparent face of the package. Observe the sealed area through which the dyeing solution flows, and you can directly observe the channel. Correct
For packages sealed on four sides, each side is at most 5s, and the total time is less than or equal to 20s. The long stay of the dyeing solution will cause the sealing area to be
Porous materials are dyed by capillary action, making observation difficult. If necessary, you can use 5~20 times optical magnifier for detailed
Inspection.
9.1.3 The packaging bag must be rotated so that each side is in contact with the dyeing solution. If necessary, you can add dyeing solution to ensure that each side can be
Exposure to staining solution.
9.2 Method B (edge immersion method)
9.2.1 Choose a container of sufficient length to at least contain the longest sealed side of the package to be tested.
9.2.2 Pour enough dye solution into the container so that the dye solution can cover the bottom of the container, with a minimum depth of about 3mm~6mm. Such as
If there is extra material on the outer edge of the sealing of the tested packaging bag, such as the skirt for the opening, some modifications must be made to the packaging. Use a shearer
Cut off the excess material from the skirt along the outer edge of the sealing area at a distance of 3mm, being careful not to cut it into the sealing area. Will be redundant
Cutting off the material will make the dyeing solution close to the sealed area.
9.2.3 Dip one of the sealed edges of the package down into the dyeing solution so that the entire sealed edge of the sealed area is in contact with the dyeing solution for a short time. This
This immersion operation is short, but just enough to completely wet the sealing edge.
9.2.4 Remove the package along the immersion direction and confirm that the entire sealing edge is in contact with the dyeing solution. Observe the stained area of the package from the transparent surface of the package
The penetration of the color liquid in the width direction of the seal. For four-side sealed packages, each side is at most 5s, and the total time is less than or equal to 20s.
9.2.5 If necessary, an optical magnifying glass of 5-20 times can be used for detailed inspection.
9.2.6 Repeat the above edge immersion operation for other sealing edges.
9.3 Method C (drip method)
9.3.1 Pour the staining solution into an open container.
9.3.2 Use your fingers or a paper clip to carefully separate the skirt of the transparent material from the breathable material.
9.3.3 Insert the eye dropper or pipette into the staining solution.
9.3.4 With the transparent surface of the package facing the operator, drip the dyeing liquid along the sealing edge between the transparent material and the breathable material. Indeed
Make sure that the entire edge is soaked in the dyeing solution.
9.3.5 For small packaging bags, slowly rotate the packaging, while continuously dripping the dyeing solution until the sealing edge of the whole package is in contact with the dyeing solution.
touch. If it is inconvenient to operate, you can instill only one side at a time.
9.3.6 Observe the entire width of the dyeing solution in the sealed area of the package. For a four-side sealed package, each side is up to 5s, and the total time is less than
Or equal to 20s.
10 report
The report should contain the following information.
a) Sample information. complete confirmation of test material information, including but not limited to the batch number, source, date, time, and location of the test
And operators;
b) Status adjustment information;
c) Test method. Method A, Method B or Method C;
d) The dyeing solution needs to be identified, if the dyeing solution used is different from that specified in 4.7;
e) Method of inspection results. observation with naked eyes or observation through equipment;
f) Result.
---The signs that the dyeing solution penetrates to the other side of the sealed area through the determined channel should be used as the basis for judging the existence of the leakage point;
---The indication that the dyeing liquid penetrates the breathable material through the capillary action of the surface should not be used as a basis for judging the existence of a leak;
--- Qualitative description or graphical description of the leakage point;
---Other information that deviates from the standard.
Appendix A
(Informative appendix)
Precision and bias of test methods
A.1 Injection method
A.1.1 Test example
From June.1997 to March.1998, three independent laboratories used this method to test the packaging of four manufacturers. use
The method of placing a wire with a diameter of 50 μm in the sealing area artificially creates defects in the sealing area of the package. After the silk thread is drawn out, a
A channel equivalent to the diameter of the wire. Prepare 50 packages for each sample group, of which 25 have defects in silk preparation, and 25 are used as
In ...
Get Quotation: Click YY/T 0681.4-2021 (Self-service in 1-minute)
Historical versions (Master-website): YY/T 0681.4-2021
Preview True-PDF (Reload/Scroll-down if blank)
YY/T 0681.4-2021: Test methods for sterile medical device package - Part 4: Detecting seal leaks in porous packages by dye penetration
YY/T 0681.4-2021
Test methods for sterile medical device package - Part 4.Detecting seal leaks in porous packages by dye penetration
ICS 11.080.040
C31
People's Republic of China Pharmaceutical Industry Standards
Replace YY/T 0681.4-2010
Sterile medical device packaging test methods
Part 4.Determination of Dyeing Solution Penetration Method
Seal leakage of breathable packaging
Released on 2021-03-09
2022-04-01 implementation
Issued by the National Medical Products Administration
Preface
YY/T 0681 "Test Methods for Packaging of Sterile Medical Devices" will consist of the following parts.
---Part 1.Guide to accelerated aging test;
---Part 2.Sealing strength of soft barrier materials;
---Part 3.Unconstrained packaging resists internal pressure damage;
---Part 4.Dyeing liquid penetration method to determine the seal leakage of breathable packaging;
---Part 5.Internal pressure method to detect gross leaks (bubble method);
---Part 6.Evaluation of the chemical resistance of printing inks and coatings on flexible packaging materials;
---Part 7.Use tape to evaluate the adhesion of ink or coating on flexible packaging materials;
---Part 8.Determination of the weight of the adhesive layer;
---Part 9.Seal burst test of flexible packaging by air pressure inside restraint plate;
---Part 10.Microbial barrier grading test for breathable packaging materials;
---Part 11.Visually inspect the seal integrity of medical packaging;
---Part 12.Anti-rubbing of soft barrier film;
---Part 13.Soft barrier film and composite film resistance to slow puncture;
---Part 14.Test of moisture and dry microbial barrier of breathable packaging materials;
---Part 15.Performance test of transport containers and systems;
---Part 16.Test of Climate Resilience of Packaging System;
---Part 17.Microbial barrier test of aerosol filtration method for breathable packaging materials;
--- Part 18.Non-destructive inspection of packaging leaks by the vacuum attenuation method.
This part is part 4 of YY/T 0681.
This section was drafted in accordance with the rules given in GB/T 1.1-2009.
This part replaces YY/T 0681.4-2010 "Test Methods for Sterile Medical Device Packaging Part 4.Determination of Air Permeability by Dyeing Liquid Penetration Method
Compared with YY/T 0681.4-2010, the main technical changes are as follows.
---Modified the content in the "Scope" (see Chapter 1, Chapter 1 of the.2010 edition);
---Modified the definition of "channel" (see 2.3,.2010 edition 2.3);
--- Deleted the content of data comparability and puncture attention (see 3.4 and 3.6 in the.2010 edition);
---The content of test instruments has been added (see 4.3, 4.4, 4.5);
---Added sampling (see Chapter 7);
---Added edge immersion method and drip method (see 9.2, 9.3);
---Added the precision and bias content of Method B and Method C (see Appendix A);
---Added false positive guidelines (see Appendix B).
Please note that some of the contents of this document may involve patents. The issuing agency of this document is not responsible for identifying these patents.
This part was proposed by the State Drug Administration.
This part is under the jurisdiction of the National Standardization Technical Committee for Medical Infusion Devices (SAC/TC106).
Drafting organizations of this section. Shandong Medical Device Product Quality Inspection Center, Minnesota Mining Manufacturing Medical Equipment (Shanghai) Co., Ltd.
Company, Henan Yadu Industrial Co., Ltd., Shandong Baiduuoan Medical Equipment Co., Ltd., Shandong Kangli Medical Equipment Technology Co., Ltd.
The main drafters of this section. Wang Dongwei, Zheng Yang, Zhang Xianglong, Duan Shuxia, Zhang Jing, Zhang Haijun, Xiong Wei, Liu Zhuang.
This section was first released in December.2010, and this is the first revision.
Sterile medical device packaging test methods
Part 4.Determination of Dyeing Solution Penetration Method
Seal leakage of breathable packaging
1 Scope
This part of YY/T 0681 specifies the test method for determining the leakage of air-permeable packaging by the dye penetration method.
This section applies to the detection of transparent materials and air-permeable materials in the seal of the package greater than or equal to 50μm channel.
This section does not apply to breathable materials that are dyed due to capillary action within 5s, nor does it apply to the contrast between dyeing liquid and opaque materials.
The big situation.
2 Terms and definitions
The following terms and definitions apply to this document.
2.1
Wicking
The liquid moves into the fibrous material.
2.2
Dyepenetrant
A mixed aqueous solution of a coloring agent and a surfactant, designed to be used before capillary action (which masks the existence of defects)
The segment is used to indicate the location of the defect.
2.3
Channel
Any undamaged path across the entire width of the intended sealing area.
3 Significance and application
3.1 Harmful microorganisms or particle contamination may enter the device through leakage. These leaks often occur between the same or different materials
The seal. These leaks may also be caused by holes in the material itself.
3.2 The dye penetration method can only be used to detect independent leaks at the seal of the package, and it is not applicable to the multiple found in the gas-permeable packaging materials.
Small leaks, which require other techniques to detect.
3.3 As far as the specific packaging is concerned, what kind of leakage is considered harmful, there is no consensus yet. However, because this test is used
To detect leakage at the seal, any signs of leakage are usually judged as unqualified.
3.4 The dyeing solution will penetrate into the breathable material over time under capillary action, but this will generally not occur within the longest recommended time (generally not
More than 20s). The dye will not discolor the surface of the material before capillary action occurs. Appendix B describes capillary action and identifying false positives
guide.
4 Instruments
4.1 Tools to destroy packaging materials, such as scissors (9.1 Method A).
4.2 Dyeing solution dispenser, such as a straw or a syringe that can be used to inject dyeing solution (9.1 Method A).
4.3 Container for dyeing liquid (9.2 Method B).
4.4 Scissors or other cutting tools (9.2 Method B).
4.5 Eye dropper or pipette (9.3 Method C).
4.6 A microscope or an optical magnifying glass capable of magnifying 5-20 times.
4.7 The dyeing solution aqueous solution includes, according to the mass fraction.
Capillary agent. TRITONX-100 0.5%
Indicator. toluidine blue 0.05%
Carrier. water 99.45%
Note. The solution is uniform. If precipitation is found, this solution needs to be replaced.
Other colorants or fluorescent agents can also replace toluidine blue, but their precision and bias must be determined through experiments.
Because the capillary agent is viscous, it is best to prepare the solution by weighing a container containing about 10% of the required amount of aqueous solution.
Add the capillary agent to the water, stir or vibrate to mix. After the capillary agent is dispersed, add the rest of the water, and finally add toluidine blue.
5 Security measures
Using hypodermic needles and syringes to inject the dye solution into the package is a common method in this test, which may result in the use of contaminated needles.
It hurts the skin, so it is not recommended. Due to this hazard, it is recommended to use a hose to connect to the syringe through the opening cut with a cutting tool
Pour the staining solution into it.
6 Test sample
The test sample can be a package containing the product, an empty package, or a package with only heat-sealed edges. If it can be proved before the test does not affect the test
The test results can also be used with defective, simulated product packaging or substandard product packaging, but it needs to be recorded before the test.
7 sampling
The number of test samples should meet the test requirements. You need to be very cautious when excluding defective samples, as this may lead to biased results.
Note. Refer to GB/T 2828.1.
8 state adjustment
The packaging should be free of condensation or liquid water from other sources. If there is water in the seal defect, it will affect the detectability of the dyeing solution. If there is
Any indication that the package has been in contact with any liquid should be fully dried at its typical storage temperature before testing.
If state adjustment is required, it is recommended to perform state adjustment in a standard environment with a temperature of (23±2)℃ and a relative humidity of (50±2)%
Section, the state is adjusted for at least 24h before the test.
9 Procedure
9.1 Method A (injection method)
9.1.1 Pour enough dye solution into the package so that the dye solution can form a depth of about 5mm on the longest side of the package. When piercing the bag
When bagging and injecting dyeing solution, special care must be taken not to pierce or damage other surfaces of the package. Next to the virtual sample in the package
It is easier to penetrate. The sample will act as a bulge to separate the two sides of the packaging bag, reducing the risk of accidentally piercing the two sides.
9.1.2 Visually inspect the sealing area through the transparent face of the package. Observe the sealed area through which the dyeing solution flows, and you can directly observe the channel. Correct
For packages sealed on four sides, each side is at most 5s, and the total time is less than or equal to 20s. The long stay of the dyeing solution will cause the sealing area to be
Porous materials are dyed by capillary action, making observation difficult. If necessary, you can use 5~20 times optical magnifier for detailed
Inspection.
9.1.3 The packaging bag must be rotated so that each side is in contact with the dyeing solution. If necessary, you can add dyeing solution to ensure that each side can be
Exposure to staining solution.
9.2 Method B (edge immersion method)
9.2.1 Choose a container of sufficient length to at least contain the longest sealed side of the package to be tested.
9.2.2 Pour enough dye solution into the container so that the dye solution can cover the bottom of the container, with a minimum depth of about 3mm~6mm. Such as
If there is extra material on the outer edge of the sealing of the tested packaging bag, such as the skirt for the opening, some modifications must be made to the packaging. Use a shearer
Cut off the excess material from the skirt along the outer edge of the sealing area at a distance of 3mm, being careful not to cut it into the sealing area. Will be redundant
Cutting off the material will make the dyeing solution close to the sealed area.
9.2.3 Dip one of the sealed edges of the package down into the dyeing solution so that the entire sealed edge of the sealed area is in contact with the dyeing solution for a short time. This
This immersion operation is short, but just enough to completely wet the sealing edge.
9.2.4 Remove the package along the immersion direction and confirm that the entire sealing edge is in contact with the dyeing solution. Observe the stained area of the package from the transparent surface of the package
The penetration of the color liquid in the width direction of the seal. For four-side sealed packages, each side is at most 5s, and the total time is less than or equal to 20s.
9.2.5 If necessary, an optical magnifying glass of 5-20 times can be used for detailed inspection.
9.2.6 Repeat the above edge immersion operation for other sealing edges.
9.3 Method C (drip method)
9.3.1 Pour the staining solution into an open container.
9.3.2 Use your fingers or a paper clip to carefully separate the skirt of the transparent material from the breathable material.
9.3.3 Insert the eye dropper or pipette into the staining solution.
9.3.4 With the transparent surface of the package facing the operator, drip the dyeing liquid along the sealing edge between the transparent material and the breathable material. Indeed
Make sure that the entire edge is soaked in the dyeing solution.
9.3.5 For small packaging bags, slowly rotate the packaging, while continuously dripping the dyeing solution until the sealing edge of the whole package is in contact with the dyeing solution.
touch. If it is inconvenient to operate, you can instill only one side at a time.
9.3.6 Observe the entire width of the dyeing solution in the sealed area of the package. For a four-side sealed package, each side is up to 5s, and the total time is less than
Or equal to 20s.
10 report
The report should contain the following information.
a) Sample information. complete confirmation of test material information, including but not limited to the batch number, source, date, time, and location of the test
And operators;
b) Status adjustment information;
c) Test method. Method A, Method B or Method C;
d) The dyeing solution needs to be identified, if the dyeing solution used is different from that specified in 4.7;
e) Method of inspection results. observation with naked eyes or observation through equipment;
f) Result.
---The signs that the dyeing solution penetrates to the other side of the sealed area through the determined channel should be used as the basis for judging the existence of the leakage point;
---The indication that the dyeing liquid penetrates the breathable material through the capillary action of the surface should not be used as a basis for judging the existence of a leak;
--- Qualitative description or graphical description of the leakage point;
---Other information that deviates from the standard.
Appendix A
(Informative appendix)
Precision and bias of test methods
A.1 Injection method
A.1.1 Test example
From June.1997 to March.1998, three independent laboratories used this method to test the packaging of four manufacturers. use
The method of placing a wire with a diameter of 50 μm in the sealing area artificially creates defects in the sealing area of the package. After the silk thread is drawn out, a
A channel equivalent to the diameter of the wire. Prepare 50 packages for each sample group, of which 25 have defects in silk preparation, and 25 are used as
In ...
Share
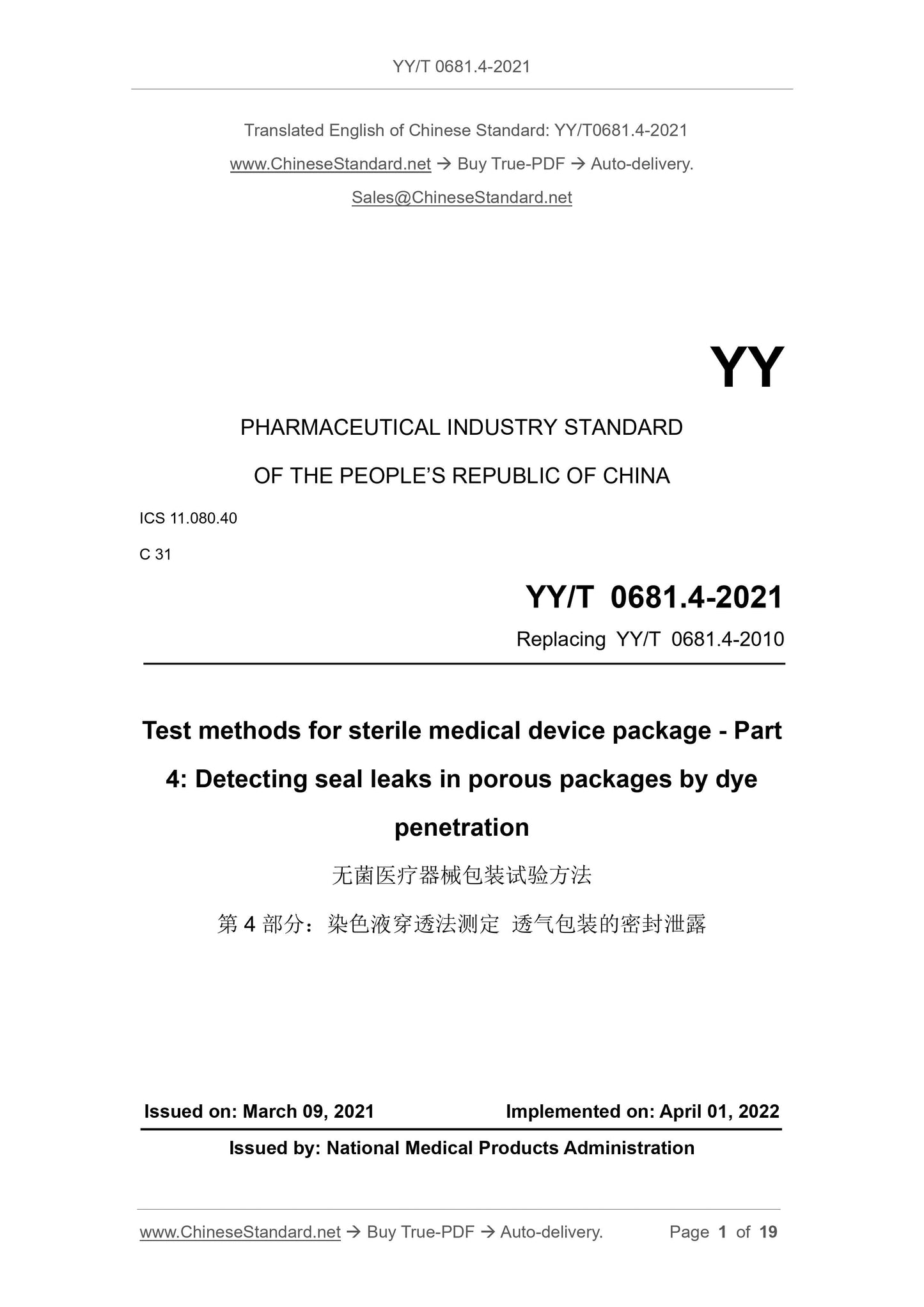
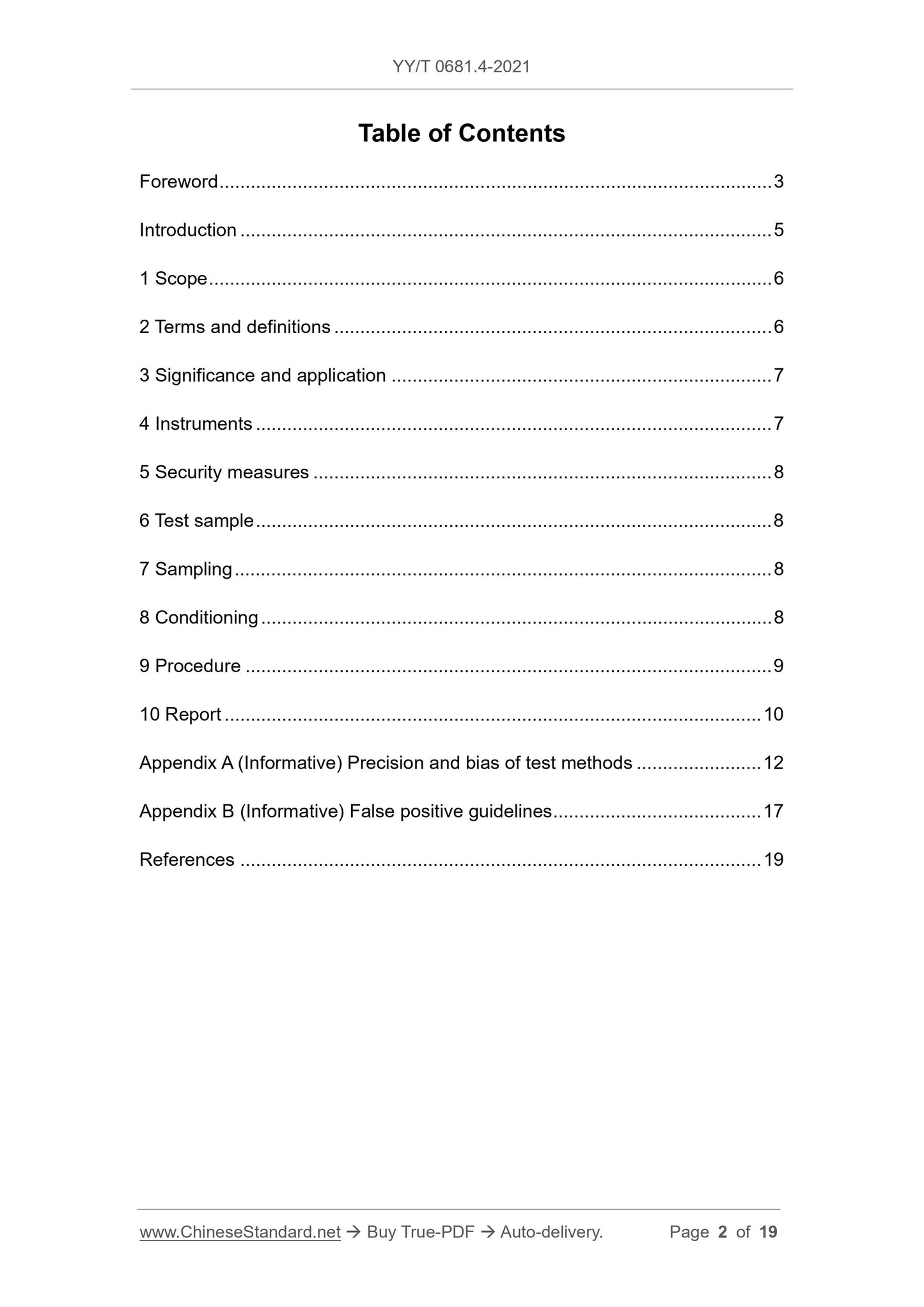
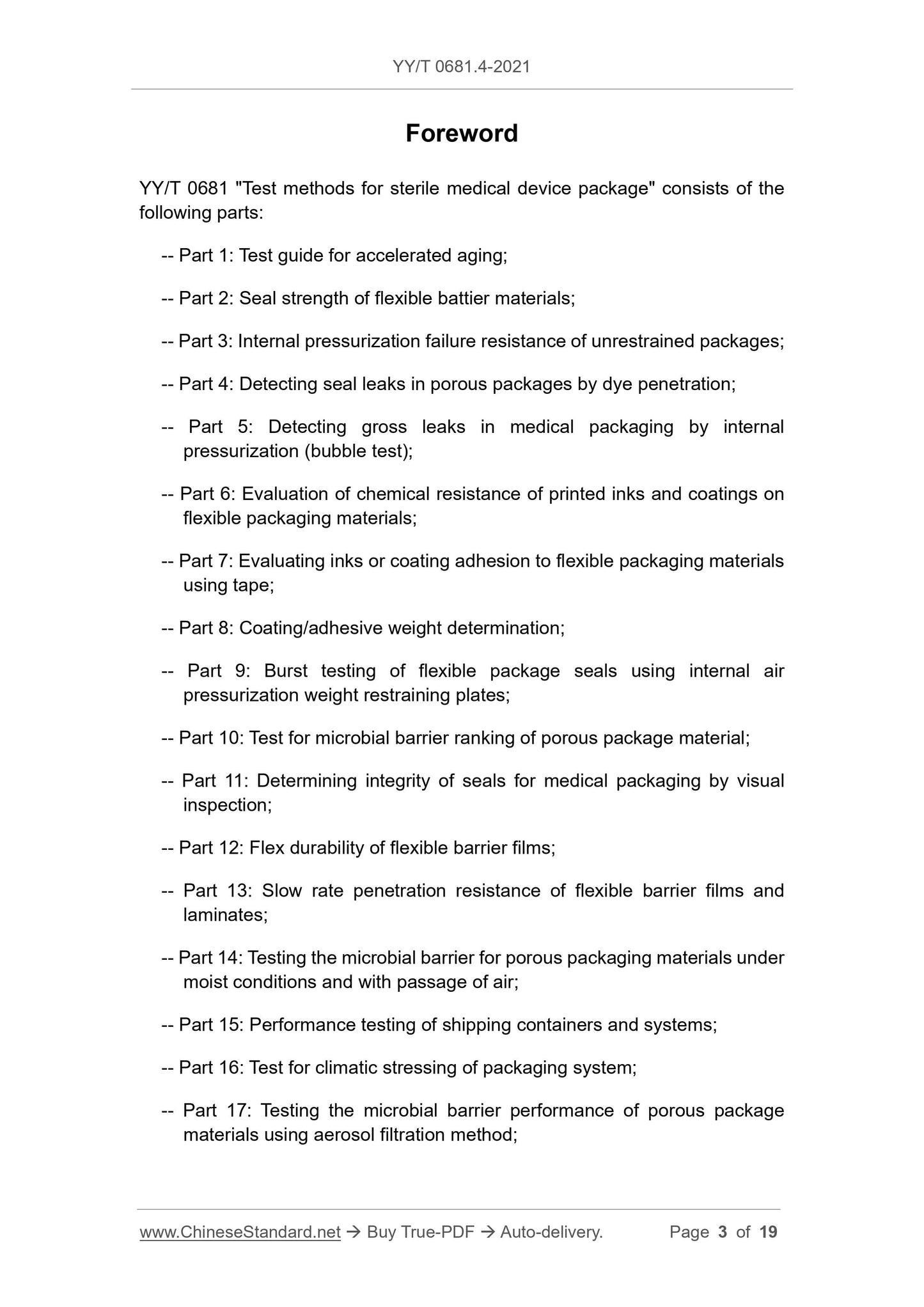
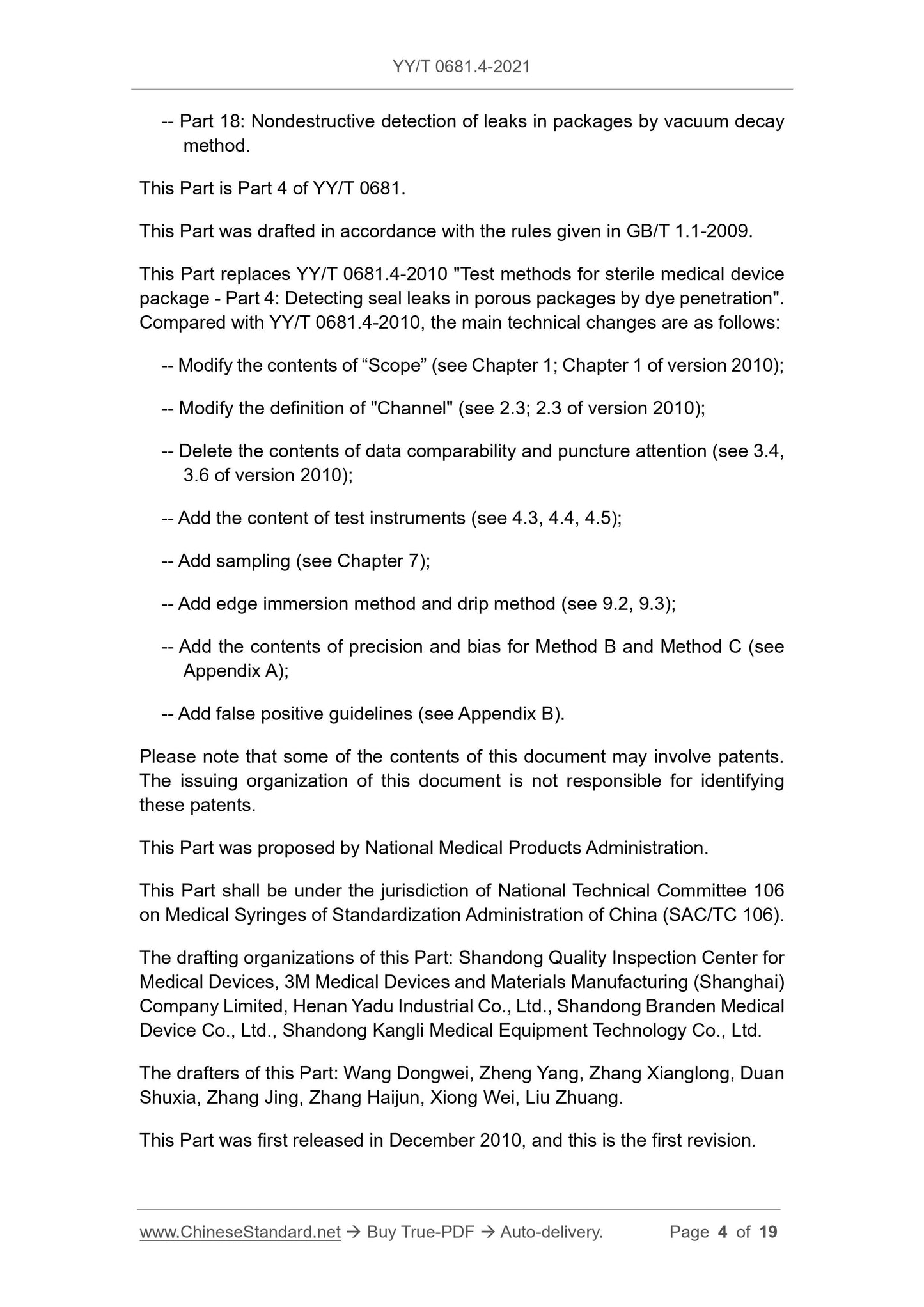
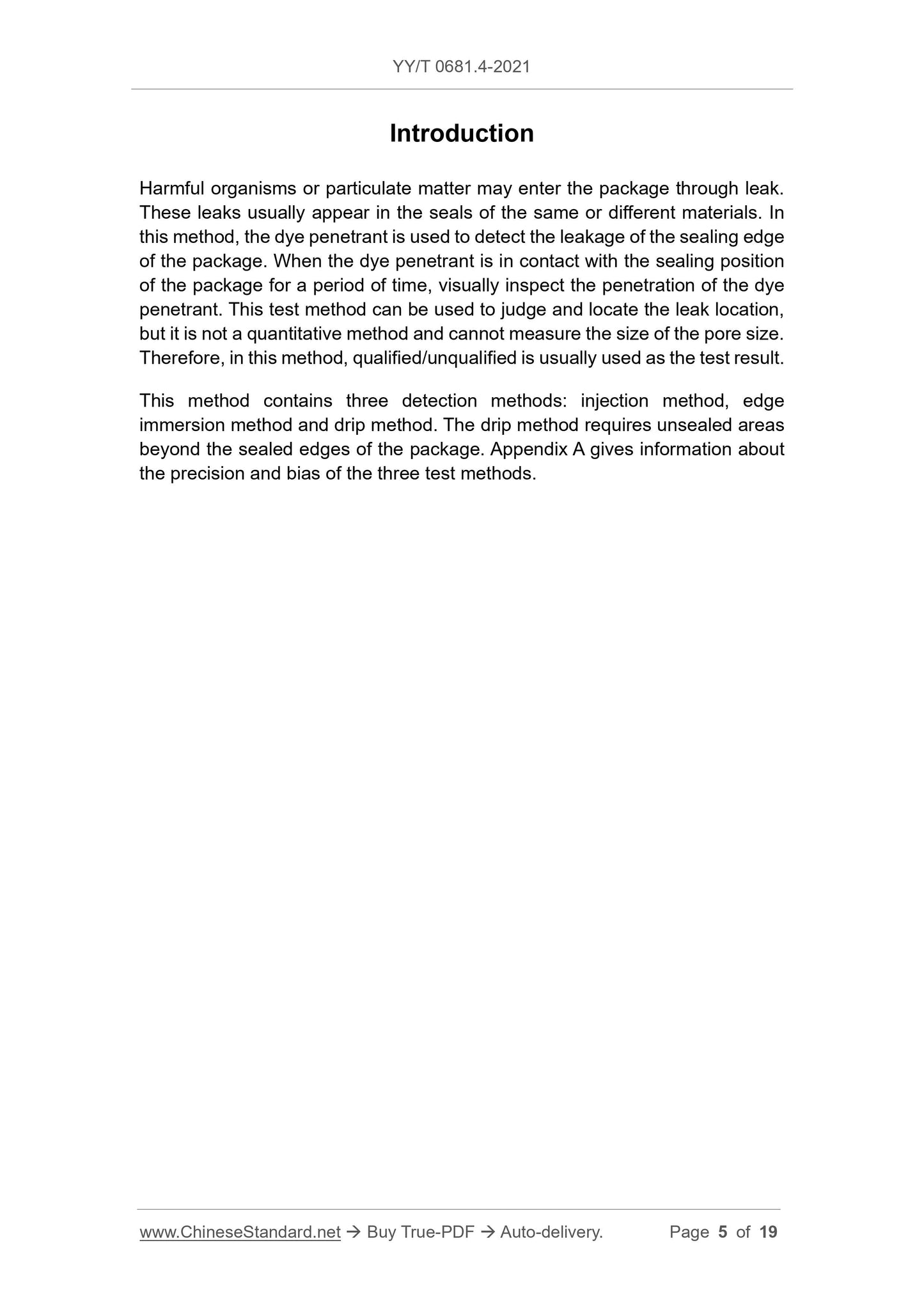
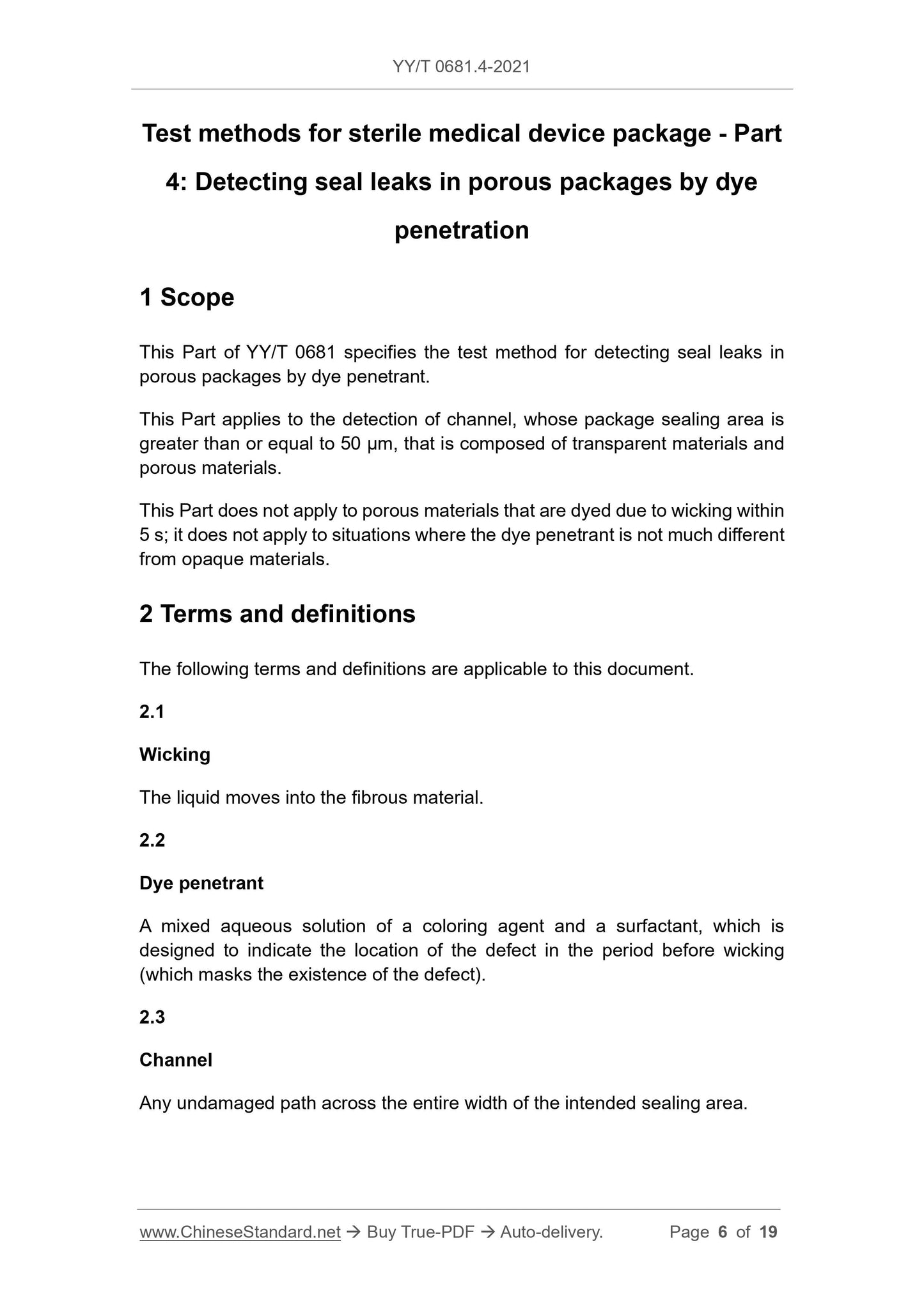
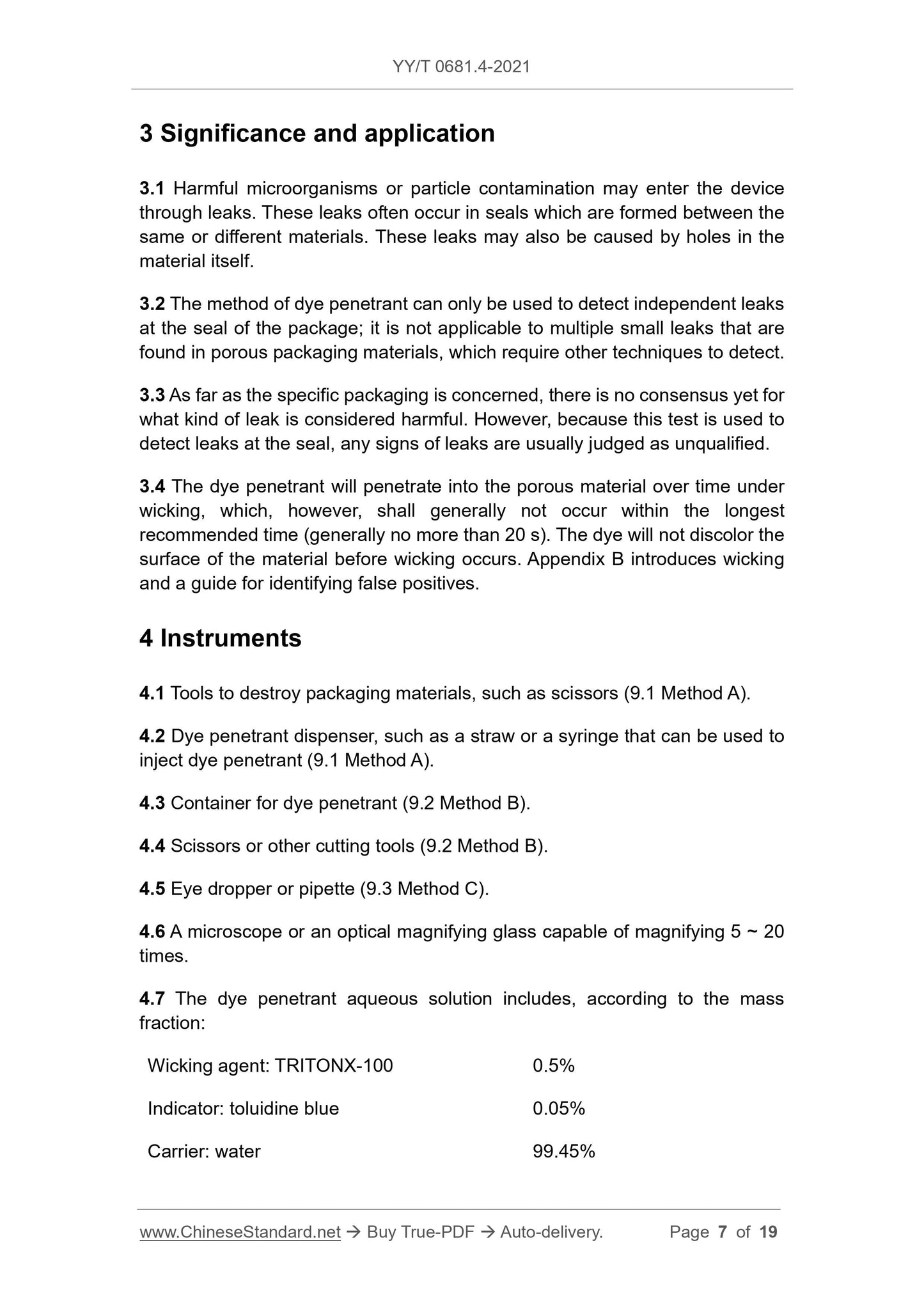
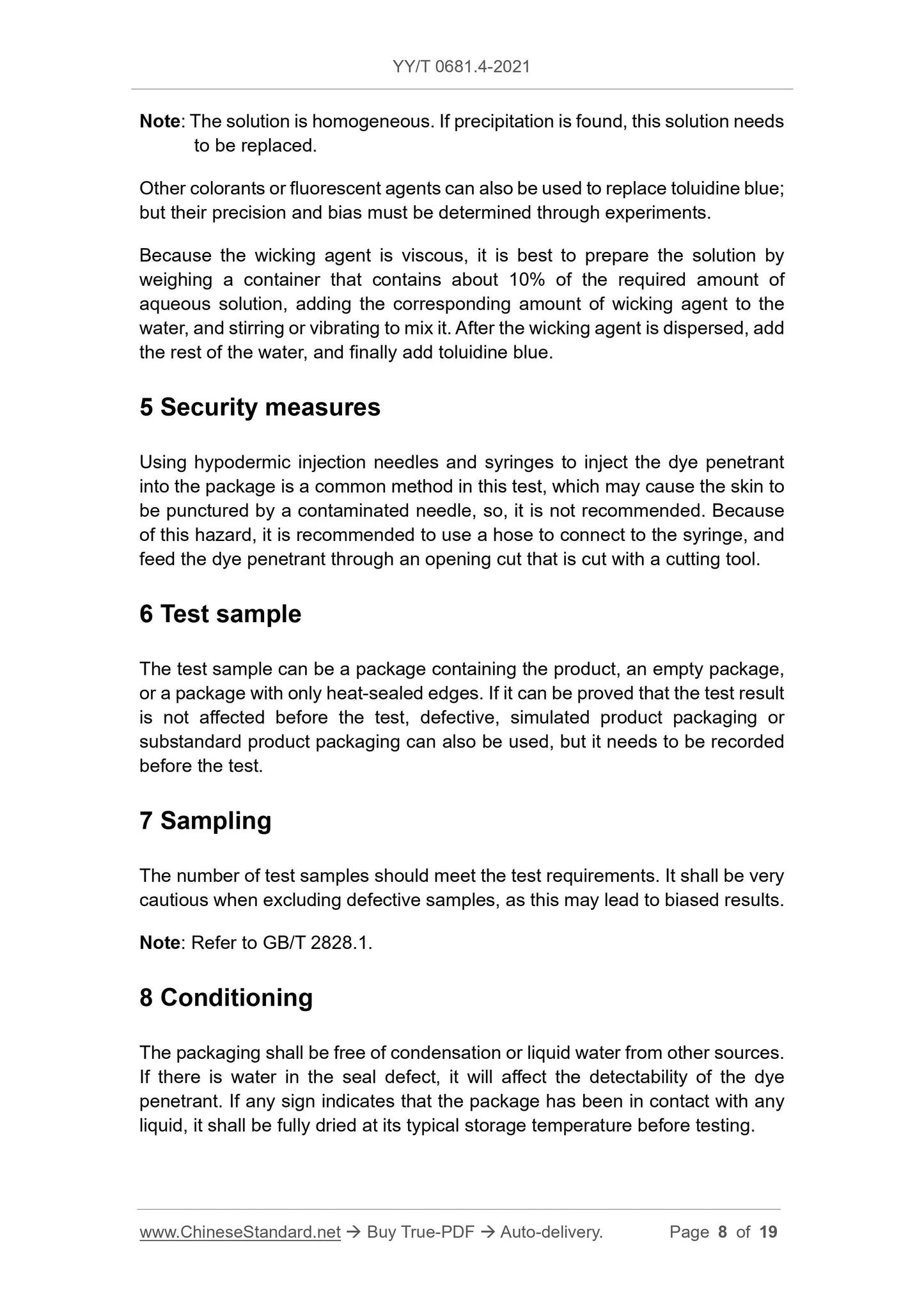
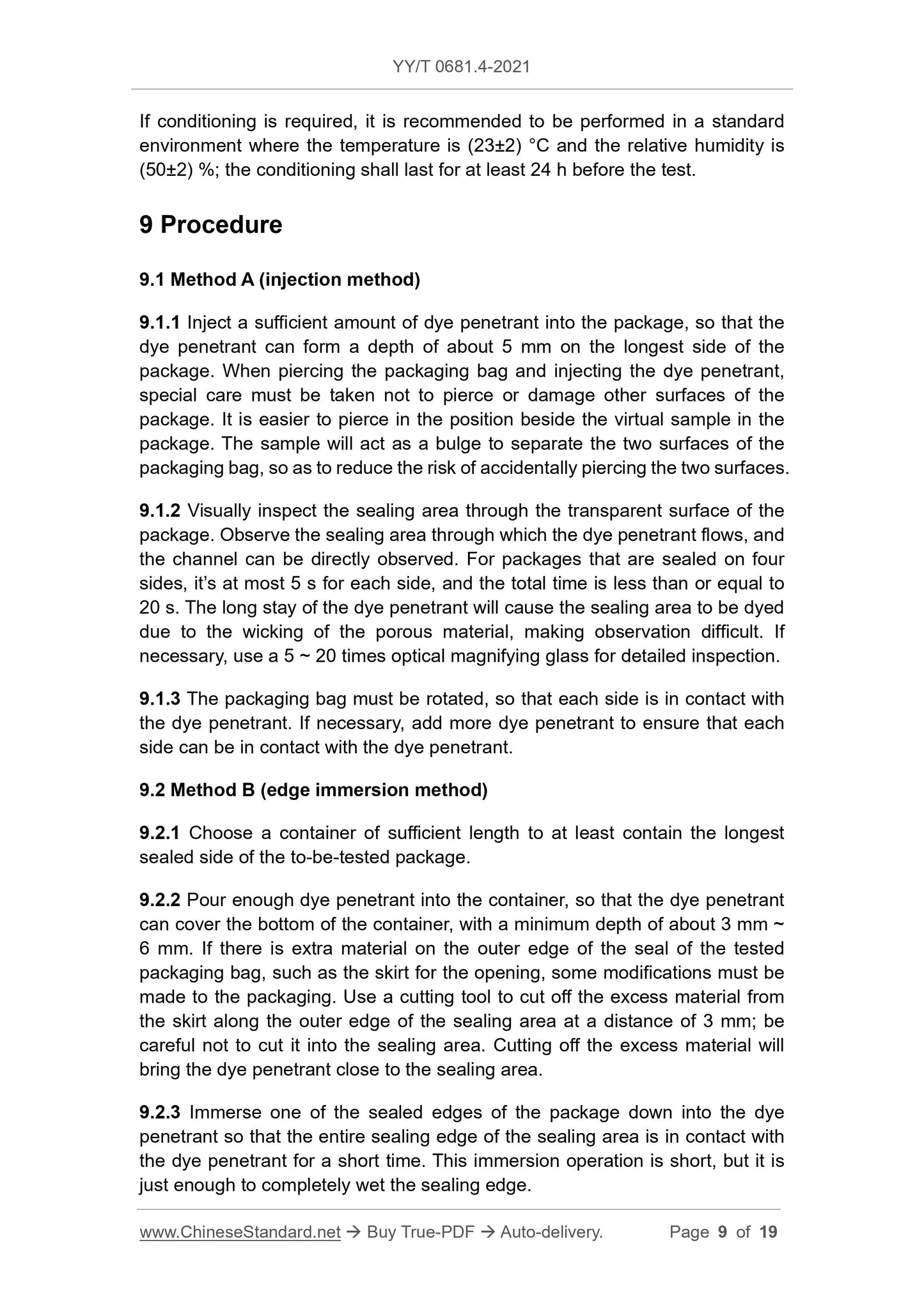
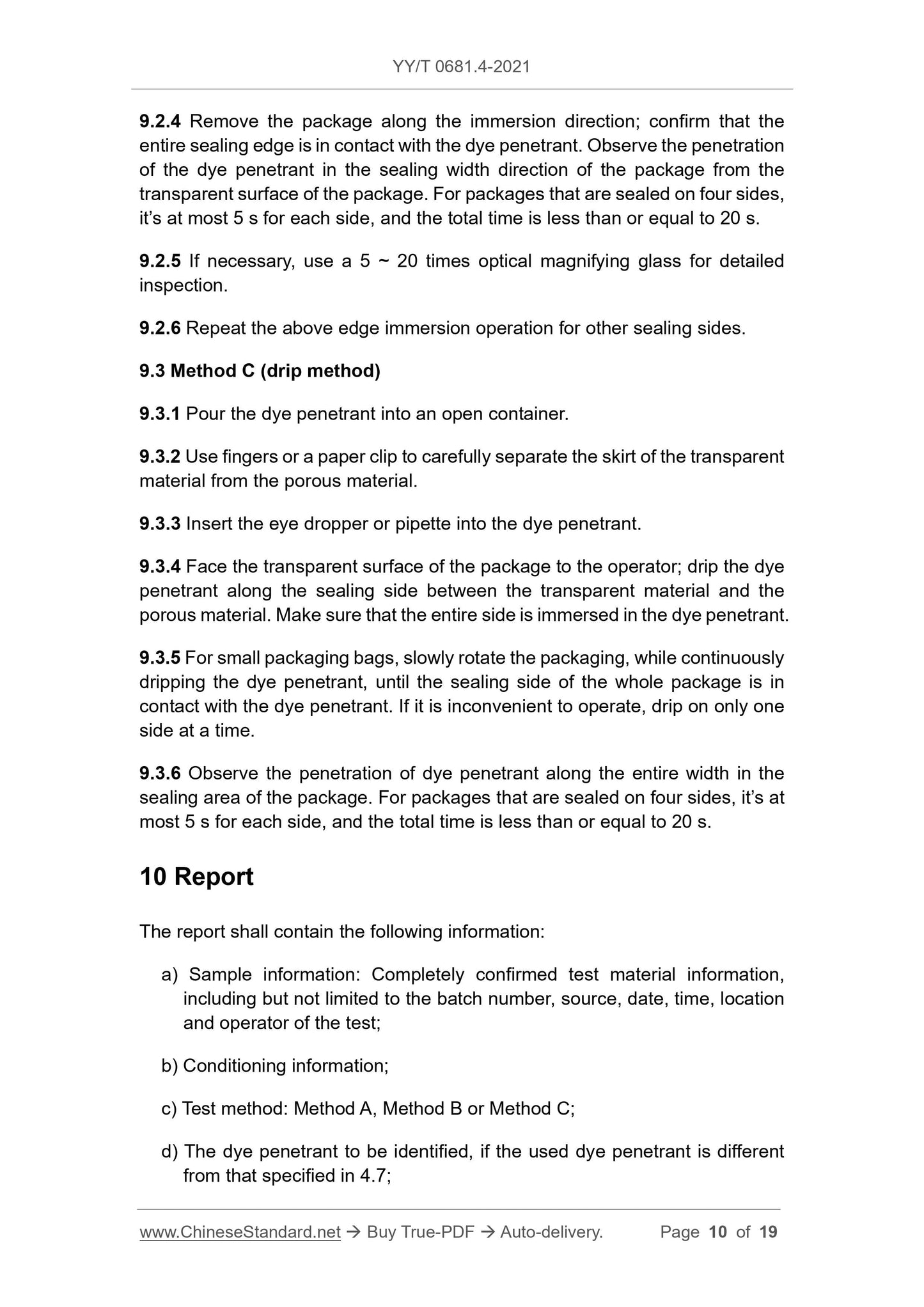
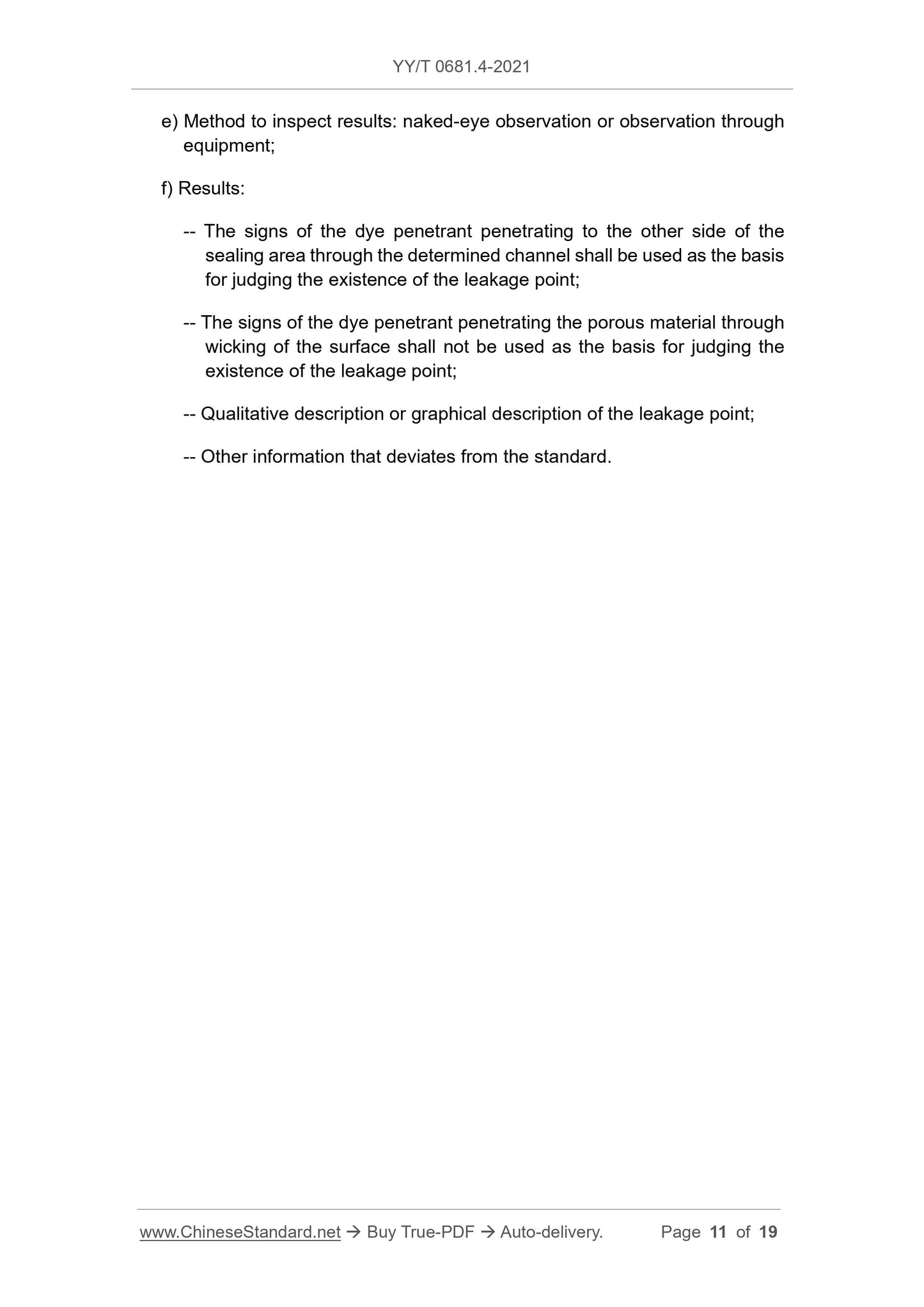
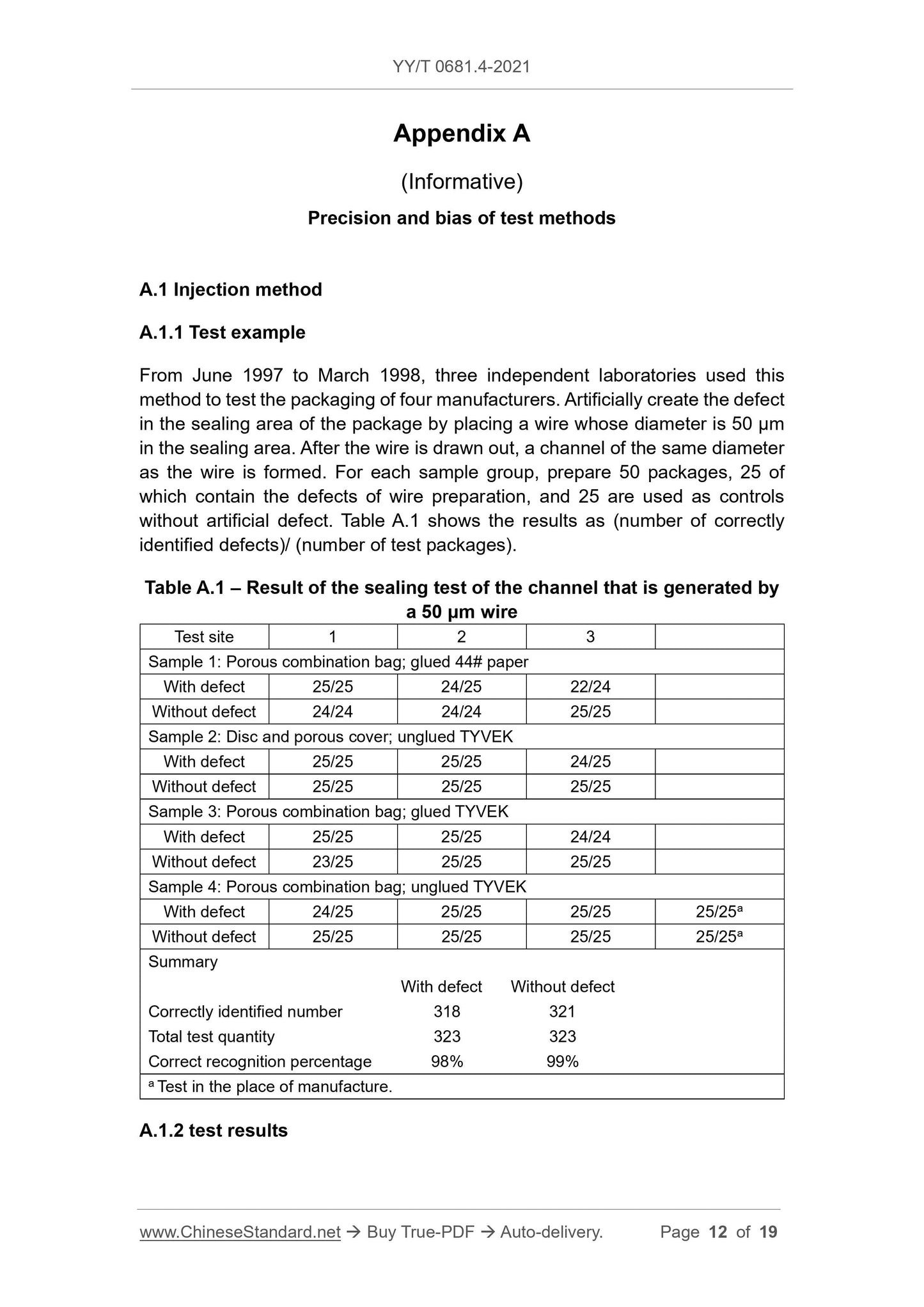