1
/
of
12
PayPal, credit cards. Download editable-PDF & invoice in 1 second!
YY/T 1106-2008 English PDF (YY/T1106-2008)
YY/T 1106-2008 English PDF (YY/T1106-2008)
Regular price
$150.00 USD
Regular price
Sale price
$150.00 USD
Unit price
/
per
Shipping calculated at checkout.
Couldn't load pickup availability
Delivery: 3 seconds. Download true-PDF + Invoice.
Get Quotation: Click YY/T 1106-2008 (Self-service in 1-minute)
Historical versions (Master-website): YY/T 1106-2008
Preview True-PDF (Reload/Scroll-down if blank)
YY/T 1106-2008: Electrically powered operating table
YY/T 1106-2008
Electrically powered operating table
ICS 11.140
C46
People's Republic of China Pharmaceutical Industry Standard
YY/T 1106-2008
Replacing YY 91106-1999
Electric operating table
Released on.2008-04-25
2009-06-01 implementation
State Food and Drug Administration released
Foreword
This standard is a recommended standard.
This standard replaces YY 91106-1999 "Electric Operating Table".
The main differences between this standard and YY 91106-1999 "Electric Operating Table" are as follows.
--- Safety requirements are modified to be implemented in accordance with GB 9706.1-2007 "Medical Electrical Equipment Part 1. General Requirements for Safety";
---Special requirements for safety shall be implemented in accordance with YY 0570-2005 "Medical Electrical Equipment Part 2. Special Requirements for Safety of Operating Tables";
---Environmental test requirements are modified to be carried out in accordance with GB/T 14710-1993 "Environmental Test Requirements and Test Methods for Medical Electrical Equipment";
--- Removed the non-technical content of the technical requirements of the original standard 4.7, 4.12, 4.13;
--- Updated outdated reference standards.
This standard was proposed by the National Medical Electrical Apparatus Standardization Technical Committee for the standardization of medical electronic instruments.
This standard is under the jurisdiction of the Technical Committee for Standardization of Medical Electronic Instruments of the National Medical Electrical Equipment Standardization Technical Committee.
This standard was drafted. Shanghai Medical Device Testing Institute.
The main drafters of this standard. Xu Yuemin, Sun Jian.
The historical version of the standard replaced by this standard is as follows.
---ZBC46006-1989.
---YY 91106-1999.
YY/T 1106-2008
Electric operating table
1 range
This standard specifies the classification, requirements, test methods, inspection rules and signs, and the use of electric operating tables (hereinafter referred to as operating tables).
Requirements for writing, packaging, transportation and storage.
This standard applies to electric operating tables. This product is used for general surgery for thoracic and abdominal surgery, ophthalmology, otolaryngology, obstetrics and gynecology, and urology.
2 Normative references
The terms in the following documents become the terms of this standard by reference to this standard. All dated references, followed by all
Modifications (not including errata content) or revisions do not apply to this standard, however, parties to agreements based on this standard are encouraged to study
Is it possible to use the latest version of these files? For undated references, the latest edition applies to this standard.
GB/T 191-2008 packaging storage and transportation icon
GB 9706.1-2007 Medical electrical equipment - Part 1. General requirements for safety (IEC 60601-1.1988, IDT)
GB 9969.1-1998 General instructions for the use of industrial products
GB/T 14710-1993 Environmental requirements and test methods for medical electrical equipment
Medical electrical equipment - Part 2. Safety requirements for operating tables (IEC 60601-2-46.1998, IDT)
3 classification and basic size
3.1 The type of operating table is electric. hydraulic and/or pneumatic and/or mechanical.
3.2 The basic dimensions of the operating table shall comply with the requirements of Figure 1.
3.3 The table top rises 100mm in a horizontal position, and the basic parameters of the single action shall comply with the requirements of Table 1.
YY/T 1106-2008
1---head plate;
2---backboard;
3---waist plate (if applicable);
4---hip plate;
5---leg plate;
6---foot board (if applicable).
Figure 1 Basic size
Note 1. The minimum and maximum height of the countertop does not include the thickness of the table mat.
Note 2. The table lift stroke S ≥.200mm.
Table 1 Basic parameters
Basic parameters of the action item
Stage tilting and backward tilting range
Forward tilt ≥20°
Back tilt ≥15°
Table top left and right tilt angle range
Left tilt ≥15°
Right tilt ≥15°
Basic parameters of the action item
Headboard folding angle range
Upfold ≥30°
Fold down ≥90°, or detachable
Leg plate fold angle range ≥90°, or detachable
Folding angle range on the back plate ≥75°
Waist plate height range ≥ 80mm (if applicable)
4 requirements
4.1 Basic parameters The basic parameters of the operating table shall comply with the provisions of 3.3.
4.2 Leakage operating table hydraulic and/or pneumatic system should be free of leakage. The operating table top is tested according to the method specified in 5.2, and the hydraulic pressure lasts for 5 hours.
(The air pressure system lasted for 1 hour), and the operating table lowered distance was no more than 8mm.
4.3 Movement stability The various movements of the operating table should be stable and must not cause jitter.
YY/T 1106-2008
4.4 When the table top swing is under no load, when the table top is at the highest position, it should be kept horizontal, remove the head plate, the arm plate, the foot plate (if applicable) and all the matching
After the kit, the following requirements should be met.
a) the amount of longitudinal oscillation should be no more than 15mm;
b) the amount of lateral swing should be no more than 10mm;
c) The horizontal lateral swing should be no more than 18mm.
4.5 Head plate, armrest plate, leg plate (if applicable), foot plate (if applicable) and all accessory parts should be convenient to handle and lock should be reliable.
4.6 Countertops and table mats should be made of X-ray permeable materials for fluoroscopy (if applicable).
4.7 The general safety requirements for the operating table shall comply with the provisions of GB 9706.1-2007.
4.8 The special requirements for the safety of the operating table shall comply with the provisions of YY 0570-2005.
4.9 The environmental test shall be in accordance with the provisions of the climatic environment test group II and the transport test in GB/T 14710-1993.
4.10 The operating table should be flat, uniform in color, free of defects such as scratches and scratches.
5 Test methods
5.1 The basic parameters are measured with a universal measuring tool and the results shall comply with the provisions of 4.1.
5.2 Leakage operating table shall be tested according to 5.2.1~5.2.3 under the condition of 20 °C ± 5 °C, and the results shall comply with the provisions of 4.2.
5.2.1 As shown in Figure 2, raise the table top to the highest position and keep it level. Align the center of the column on the platform hip plate and add 100kg static.
After the load and hydraulic pressure were passed for 5 hours (1 hour after the air pressure system), the falling distance was measured.
5.2.2 As shown in Figure 3, the table top is reduced to a minimum position and placed horizontally at a distance of 100 mm from the end of the leg plate.
After 5 h (pressure system for 1 h), the distance of the drop was measured.
5.2.3 As shown in Figure 4, the table top is lowered to the lowest position, the angle between the fold plate and the hip plate on the back plate is 125°, and the 50kg static load is hung in the middle of the top of the back plate.
After the load, the hydraulic pressure is measured for 5 h (the air pressure system is 1 h), and the falling distance is measured.
Figure 2 Leakage test (5.2.1)
YY/T 1106-2008
Figure 3 Leakage test (5.2.2)
Figure 4 Leak test (5.2.3)
5.3 Operational stability When the operating table is changed, the operating table is touched by hand and the result should meet the requirements of 4.3.
5.4 Table swing amount
5.4.1 The amount of longitudinal swing is as shown in Figure 5, with a downward force of 98N at the top of the backplane of the longitudinal centerline of the table, and then in the distance between the swing rod holders.
The measurement is made at 1 m from the heart, and the value of the wobble is read from the measurement scale, which is the amount of back tilting of the table. At the end of the leg of the longitudinal centerline of the countertop
The end is applied with a downward force of 98N, and then measured at a distance of 1 m from the center of the pendulum mount. The wobble value is read from the measuring scale, that is, the table is tilted forward.
The amount of swing (see Figure 6). The absolute sum of the amount of backward and forward tilting shall comply with the provisions of 4.4.1.
YY/T 1106-2008
1---dynamometer;
2---forced chuck;
3---swing bar;
4---scale;
5---pendulum mount.
Figure 5 Longitudinal swing amount (backward tilt)
1--- pendulum rod holder;
2---swing bar;
3---forced chuck;
4---dynamometer;
5---scale.
Figure 6 Longitudinal swing amount (forward tilt)
YY/T 1106-2008
5.4.2 The amount of lateral swing is as shown in Figure 7. On the horizontal centerline of the mesa, the left and right are added and the force is 98N, and then in the longitudinal direction.
The measurement is made at a height of 0.5 m, and the absolute value of the upper and lower swings is read from the measuring scale, which shall comply with the provisions of 4.4.2.
1---dynamometer;
2---pendulum mount;
3---swing bar;
4---scale.
Figure 7 Horizontal swing amount
YY/T 1106-2008
5.4.3 Horizontal lateral swinging amount As shown in Figure 8, add 98N horizontal and horizontal force to the top of the longitudinal centerline backplane of the mesa, and then
The measurement is made 1m away from the horizontal center line, the swing value is read from the measuring scale, and the absolute value of the left and right swing amounts in the horizontal direction should be
Meet the requirements of 4.4.3.
1---dynamometer;
2---forced chuck;
3--- pendulum rod holder;
4---swing bar;
5---scale.
Figure 8 Horizontal lateral swing
5.5 Verification by actual operation, the results should meet the requirements of 4.5.
5.6 The table top and the selected table mat shall be visually inspected without X-ray (50kV) or X-ray fluoroscopy (70kV).
The provisions of 4.6.
5.7 General requirements for safety The test shall be carried out in accordance with the method specified in GB 9706.1 to verify compliance with the requirements.
5.8 Special requirements for safety shall be tested in accordance with the method specified in YY 0570 to verify compliance with the requirements.
5.9 Environmental test requirements Test according to the method specified in GB/T 14710 to check whether it meets the requirements.
5.10 Observed by eyesight, the results should be in accordance with 4.10.
6 Inspection rules
6.1 Inspection classification
The inspection of electric operating table products is divided into factory inspection and type inspection.
6.2 Factory inspection
6.2.1 The operating table shall be inspected by the quality inspection department of the manufacturer on a case-by-case basis.
6.2.2 The factory inspection items shall be inspected according to the provisions of Table 2.
6.2.3 In the case of inspection, if there is any unqualified item, the unqualified item shall be refurbished. Resubmit the test after repair, check the joint
The grid can be stored in the warehouse and shipped out.
YY/T 1106-2008
Table 2
Inspection item inspection scope remarks
Performance 4.1, 4.2, 4.3, 4.4, 4.5, 4.10 -
Safety 18 s, 19, 20 in GB 9706.1-2007 -
6.3 Type inspection
6.3.1 Type inspection shall be carried out in one of the following cases.
a) when the product is registered and re-registered;
b) when there is a significant change in structure, process or material;
c) when it is put into production at intervals of more than one year;
d) When the national quality supervision agency proposes the type inspection requirements.
6.3.2 Sampling plan. Random sampling in the qualified batch of factory inspection, the number of samples is not less than one.
6.3.3 Type inspection items. All the terms required in this standard.
6.3.4 Judgment rules and re-examination rules. The products shall be qualified according to the requirements of the type inspection items before they can be qualified for this type inspection.
If there is a non-conformity in the inspection, the modification is allowed, and after the re-test is passed, the type inspection is passed; if the re-test fails, the judgment is
Type inspection failed.
These rules apply to registration inspection, permit inspection and safety certification inspection. The national supervision and inspection shall be carried out in accordance with relevant regulations.
7 signs, instructions for use, packaging, transportation, storage
7.1 mark
7.1.1 Each operating table shall have the following markings in a suitably prominent position.
a) the manufacturer's name (or trademark) and the site;
b) product name and model number;
c) product production number;
d) the date of manufacture of the product;
e) safety classification;
f) power supply voltage, frequency, input power;
g) Product standard number.
7.1.2 The following signs shall be on the wooden box.
a) manufacturer's name and site;
b) product name and model number;
c) product production number;
d) the date of manufacture of the product;
e) product registration number;
f) product standard number;
g) net weight and gross weight;
h) volume (length, width, height);
i) “Fragile items”, “upward”, “fear of rain” and transportation and storage marks shall be in accordance with the relevant provisions of GB/T 191.
7.2 User's Guide
Instructions for use shall comply with the requirements of 6.8 of GB 9969.1, GB 9706.1-2007 and relevant regulations of medical devices.
7.3 Packaging
Each operating table together with the accessory box should be packed in a wooden packing box with instructions for use, inspection certificate and packing list.
One copy and should meet the following packing requirements.
YY/T 1106-2008
a) The wooden box should have moisture-proof and rain-proof devices to ensure that the product is not damaged by nature, and the bottom of the box should have sliding wood.
b) The operating table must be firmly positioned in the box, and a soft padding of appropriate thickn...
Get Quotation: Click YY/T 1106-2008 (Self-service in 1-minute)
Historical versions (Master-website): YY/T 1106-2008
Preview True-PDF (Reload/Scroll-down if blank)
YY/T 1106-2008: Electrically powered operating table
YY/T 1106-2008
Electrically powered operating table
ICS 11.140
C46
People's Republic of China Pharmaceutical Industry Standard
YY/T 1106-2008
Replacing YY 91106-1999
Electric operating table
Released on.2008-04-25
2009-06-01 implementation
State Food and Drug Administration released
Foreword
This standard is a recommended standard.
This standard replaces YY 91106-1999 "Electric Operating Table".
The main differences between this standard and YY 91106-1999 "Electric Operating Table" are as follows.
--- Safety requirements are modified to be implemented in accordance with GB 9706.1-2007 "Medical Electrical Equipment Part 1. General Requirements for Safety";
---Special requirements for safety shall be implemented in accordance with YY 0570-2005 "Medical Electrical Equipment Part 2. Special Requirements for Safety of Operating Tables";
---Environmental test requirements are modified to be carried out in accordance with GB/T 14710-1993 "Environmental Test Requirements and Test Methods for Medical Electrical Equipment";
--- Removed the non-technical content of the technical requirements of the original standard 4.7, 4.12, 4.13;
--- Updated outdated reference standards.
This standard was proposed by the National Medical Electrical Apparatus Standardization Technical Committee for the standardization of medical electronic instruments.
This standard is under the jurisdiction of the Technical Committee for Standardization of Medical Electronic Instruments of the National Medical Electrical Equipment Standardization Technical Committee.
This standard was drafted. Shanghai Medical Device Testing Institute.
The main drafters of this standard. Xu Yuemin, Sun Jian.
The historical version of the standard replaced by this standard is as follows.
---ZBC46006-1989.
---YY 91106-1999.
YY/T 1106-2008
Electric operating table
1 range
This standard specifies the classification, requirements, test methods, inspection rules and signs, and the use of electric operating tables (hereinafter referred to as operating tables).
Requirements for writing, packaging, transportation and storage.
This standard applies to electric operating tables. This product is used for general surgery for thoracic and abdominal surgery, ophthalmology, otolaryngology, obstetrics and gynecology, and urology.
2 Normative references
The terms in the following documents become the terms of this standard by reference to this standard. All dated references, followed by all
Modifications (not including errata content) or revisions do not apply to this standard, however, parties to agreements based on this standard are encouraged to study
Is it possible to use the latest version of these files? For undated references, the latest edition applies to this standard.
GB/T 191-2008 packaging storage and transportation icon
GB 9706.1-2007 Medical electrical equipment - Part 1. General requirements for safety (IEC 60601-1.1988, IDT)
GB 9969.1-1998 General instructions for the use of industrial products
GB/T 14710-1993 Environmental requirements and test methods for medical electrical equipment
Medical electrical equipment - Part 2. Safety requirements for operating tables (IEC 60601-2-46.1998, IDT)
3 classification and basic size
3.1 The type of operating table is electric. hydraulic and/or pneumatic and/or mechanical.
3.2 The basic dimensions of the operating table shall comply with the requirements of Figure 1.
3.3 The table top rises 100mm in a horizontal position, and the basic parameters of the single action shall comply with the requirements of Table 1.
YY/T 1106-2008
1---head plate;
2---backboard;
3---waist plate (if applicable);
4---hip plate;
5---leg plate;
6---foot board (if applicable).
Figure 1 Basic size
Note 1. The minimum and maximum height of the countertop does not include the thickness of the table mat.
Note 2. The table lift stroke S ≥.200mm.
Table 1 Basic parameters
Basic parameters of the action item
Stage tilting and backward tilting range
Forward tilt ≥20°
Back tilt ≥15°
Table top left and right tilt angle range
Left tilt ≥15°
Right tilt ≥15°
Basic parameters of the action item
Headboard folding angle range
Upfold ≥30°
Fold down ≥90°, or detachable
Leg plate fold angle range ≥90°, or detachable
Folding angle range on the back plate ≥75°
Waist plate height range ≥ 80mm (if applicable)
4 requirements
4.1 Basic parameters The basic parameters of the operating table shall comply with the provisions of 3.3.
4.2 Leakage operating table hydraulic and/or pneumatic system should be free of leakage. The operating table top is tested according to the method specified in 5.2, and the hydraulic pressure lasts for 5 hours.
(The air pressure system lasted for 1 hour), and the operating table lowered distance was no more than 8mm.
4.3 Movement stability The various movements of the operating table should be stable and must not cause jitter.
YY/T 1106-2008
4.4 When the table top swing is under no load, when the table top is at the highest position, it should be kept horizontal, remove the head plate, the arm plate, the foot plate (if applicable) and all the matching
After the kit, the following requirements should be met.
a) the amount of longitudinal oscillation should be no more than 15mm;
b) the amount of lateral swing should be no more than 10mm;
c) The horizontal lateral swing should be no more than 18mm.
4.5 Head plate, armrest plate, leg plate (if applicable), foot plate (if applicable) and all accessory parts should be convenient to handle and lock should be reliable.
4.6 Countertops and table mats should be made of X-ray permeable materials for fluoroscopy (if applicable).
4.7 The general safety requirements for the operating table shall comply with the provisions of GB 9706.1-2007.
4.8 The special requirements for the safety of the operating table shall comply with the provisions of YY 0570-2005.
4.9 The environmental test shall be in accordance with the provisions of the climatic environment test group II and the transport test in GB/T 14710-1993.
4.10 The operating table should be flat, uniform in color, free of defects such as scratches and scratches.
5 Test methods
5.1 The basic parameters are measured with a universal measuring tool and the results shall comply with the provisions of 4.1.
5.2 Leakage operating table shall be tested according to 5.2.1~5.2.3 under the condition of 20 °C ± 5 °C, and the results shall comply with the provisions of 4.2.
5.2.1 As shown in Figure 2, raise the table top to the highest position and keep it level. Align the center of the column on the platform hip plate and add 100kg static.
After the load and hydraulic pressure were passed for 5 hours (1 hour after the air pressure system), the falling distance was measured.
5.2.2 As shown in Figure 3, the table top is reduced to a minimum position and placed horizontally at a distance of 100 mm from the end of the leg plate.
After 5 h (pressure system for 1 h), the distance of the drop was measured.
5.2.3 As shown in Figure 4, the table top is lowered to the lowest position, the angle between the fold plate and the hip plate on the back plate is 125°, and the 50kg static load is hung in the middle of the top of the back plate.
After the load, the hydraulic pressure is measured for 5 h (the air pressure system is 1 h), and the falling distance is measured.
Figure 2 Leakage test (5.2.1)
YY/T 1106-2008
Figure 3 Leakage test (5.2.2)
Figure 4 Leak test (5.2.3)
5.3 Operational stability When the operating table is changed, the operating table is touched by hand and the result should meet the requirements of 4.3.
5.4 Table swing amount
5.4.1 The amount of longitudinal swing is as shown in Figure 5, with a downward force of 98N at the top of the backplane of the longitudinal centerline of the table, and then in the distance between the swing rod holders.
The measurement is made at 1 m from the heart, and the value of the wobble is read from the measurement scale, which is the amount of back tilting of the table. At the end of the leg of the longitudinal centerline of the countertop
The end is applied with a downward force of 98N, and then measured at a distance of 1 m from the center of the pendulum mount. The wobble value is read from the measuring scale, that is, the table is tilted forward.
The amount of swing (see Figure 6). The absolute sum of the amount of backward and forward tilting shall comply with the provisions of 4.4.1.
YY/T 1106-2008
1---dynamometer;
2---forced chuck;
3---swing bar;
4---scale;
5---pendulum mount.
Figure 5 Longitudinal swing amount (backward tilt)
1--- pendulum rod holder;
2---swing bar;
3---forced chuck;
4---dynamometer;
5---scale.
Figure 6 Longitudinal swing amount (forward tilt)
YY/T 1106-2008
5.4.2 The amount of lateral swing is as shown in Figure 7. On the horizontal centerline of the mesa, the left and right are added and the force is 98N, and then in the longitudinal direction.
The measurement is made at a height of 0.5 m, and the absolute value of the upper and lower swings is read from the measuring scale, which shall comply with the provisions of 4.4.2.
1---dynamometer;
2---pendulum mount;
3---swing bar;
4---scale.
Figure 7 Horizontal swing amount
YY/T 1106-2008
5.4.3 Horizontal lateral swinging amount As shown in Figure 8, add 98N horizontal and horizontal force to the top of the longitudinal centerline backplane of the mesa, and then
The measurement is made 1m away from the horizontal center line, the swing value is read from the measuring scale, and the absolute value of the left and right swing amounts in the horizontal direction should be
Meet the requirements of 4.4.3.
1---dynamometer;
2---forced chuck;
3--- pendulum rod holder;
4---swing bar;
5---scale.
Figure 8 Horizontal lateral swing
5.5 Verification by actual operation, the results should meet the requirements of 4.5.
5.6 The table top and the selected table mat shall be visually inspected without X-ray (50kV) or X-ray fluoroscopy (70kV).
The provisions of 4.6.
5.7 General requirements for safety The test shall be carried out in accordance with the method specified in GB 9706.1 to verify compliance with the requirements.
5.8 Special requirements for safety shall be tested in accordance with the method specified in YY 0570 to verify compliance with the requirements.
5.9 Environmental test requirements Test according to the method specified in GB/T 14710 to check whether it meets the requirements.
5.10 Observed by eyesight, the results should be in accordance with 4.10.
6 Inspection rules
6.1 Inspection classification
The inspection of electric operating table products is divided into factory inspection and type inspection.
6.2 Factory inspection
6.2.1 The operating table shall be inspected by the quality inspection department of the manufacturer on a case-by-case basis.
6.2.2 The factory inspection items shall be inspected according to the provisions of Table 2.
6.2.3 In the case of inspection, if there is any unqualified item, the unqualified item shall be refurbished. Resubmit the test after repair, check the joint
The grid can be stored in the warehouse and shipped out.
YY/T 1106-2008
Table 2
Inspection item inspection scope remarks
Performance 4.1, 4.2, 4.3, 4.4, 4.5, 4.10 -
Safety 18 s, 19, 20 in GB 9706.1-2007 -
6.3 Type inspection
6.3.1 Type inspection shall be carried out in one of the following cases.
a) when the product is registered and re-registered;
b) when there is a significant change in structure, process or material;
c) when it is put into production at intervals of more than one year;
d) When the national quality supervision agency proposes the type inspection requirements.
6.3.2 Sampling plan. Random sampling in the qualified batch of factory inspection, the number of samples is not less than one.
6.3.3 Type inspection items. All the terms required in this standard.
6.3.4 Judgment rules and re-examination rules. The products shall be qualified according to the requirements of the type inspection items before they can be qualified for this type inspection.
If there is a non-conformity in the inspection, the modification is allowed, and after the re-test is passed, the type inspection is passed; if the re-test fails, the judgment is
Type inspection failed.
These rules apply to registration inspection, permit inspection and safety certification inspection. The national supervision and inspection shall be carried out in accordance with relevant regulations.
7 signs, instructions for use, packaging, transportation, storage
7.1 mark
7.1.1 Each operating table shall have the following markings in a suitably prominent position.
a) the manufacturer's name (or trademark) and the site;
b) product name and model number;
c) product production number;
d) the date of manufacture of the product;
e) safety classification;
f) power supply voltage, frequency, input power;
g) Product standard number.
7.1.2 The following signs shall be on the wooden box.
a) manufacturer's name and site;
b) product name and model number;
c) product production number;
d) the date of manufacture of the product;
e) product registration number;
f) product standard number;
g) net weight and gross weight;
h) volume (length, width, height);
i) “Fragile items”, “upward”, “fear of rain” and transportation and storage marks shall be in accordance with the relevant provisions of GB/T 191.
7.2 User's Guide
Instructions for use shall comply with the requirements of 6.8 of GB 9969.1, GB 9706.1-2007 and relevant regulations of medical devices.
7.3 Packaging
Each operating table together with the accessory box should be packed in a wooden packing box with instructions for use, inspection certificate and packing list.
One copy and should meet the following packing requirements.
YY/T 1106-2008
a) The wooden box should have moisture-proof and rain-proof devices to ensure that the product is not damaged by nature, and the bottom of the box should have sliding wood.
b) The operating table must be firmly positioned in the box, and a soft padding of appropriate thickn...
Share
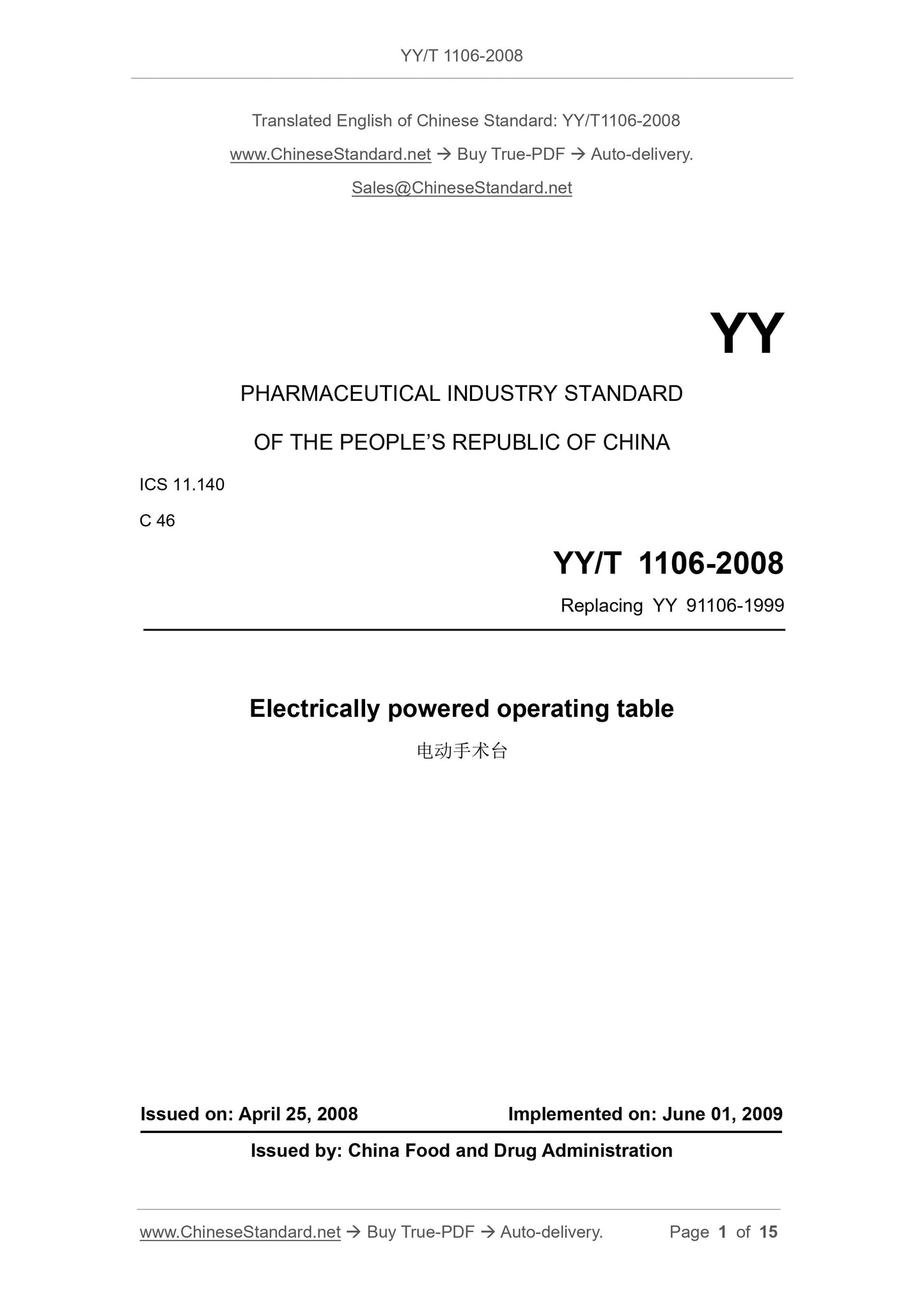
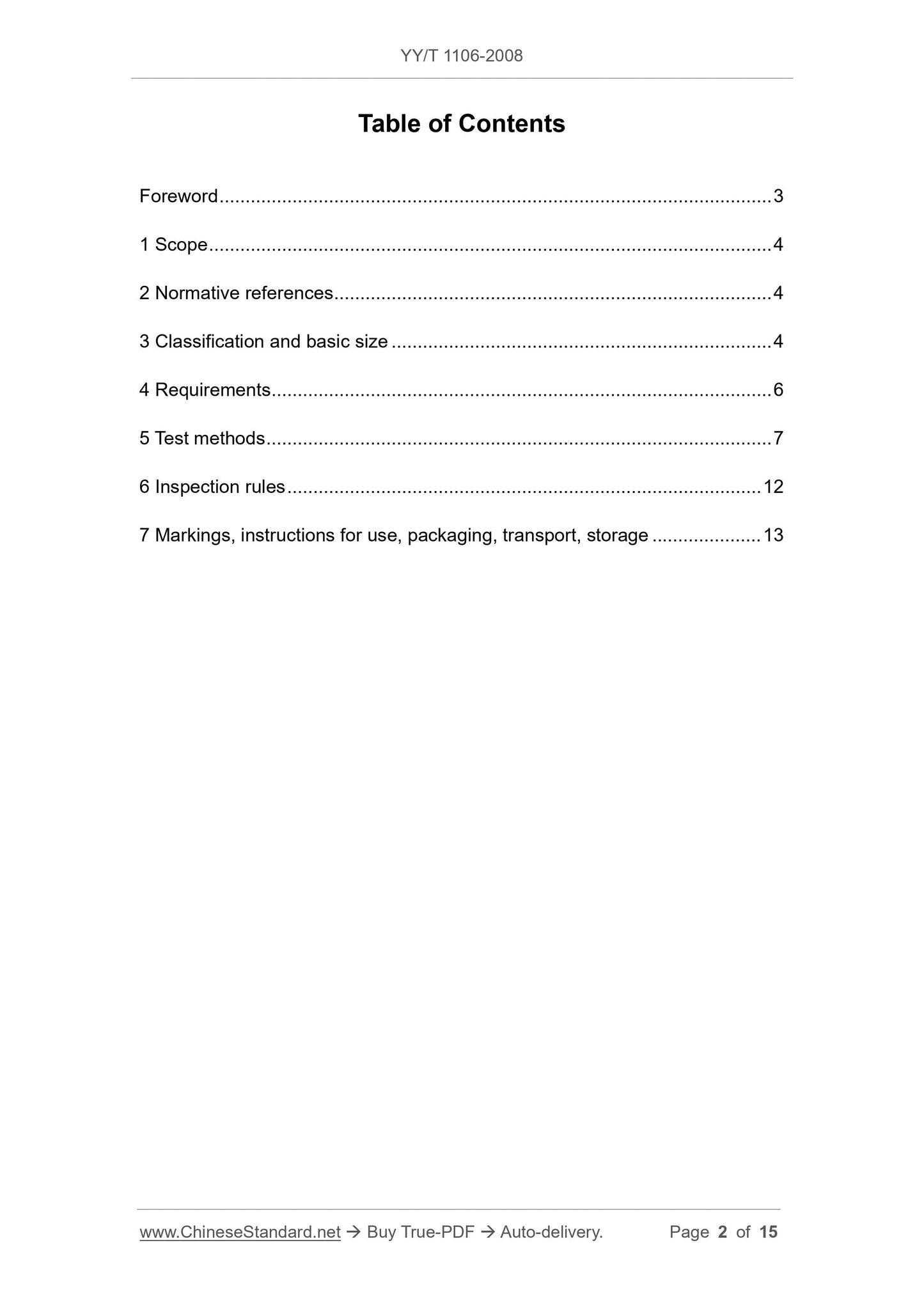
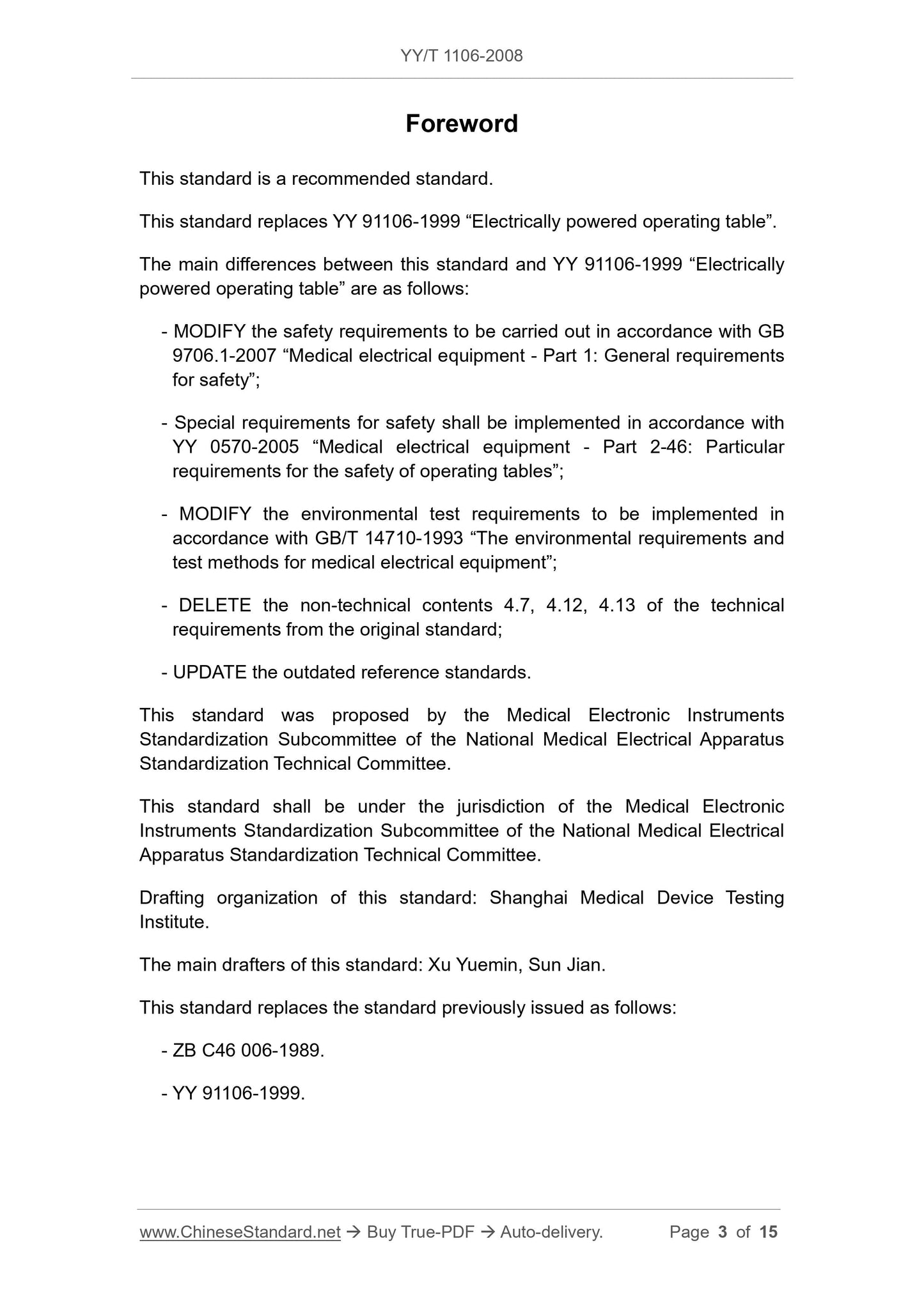
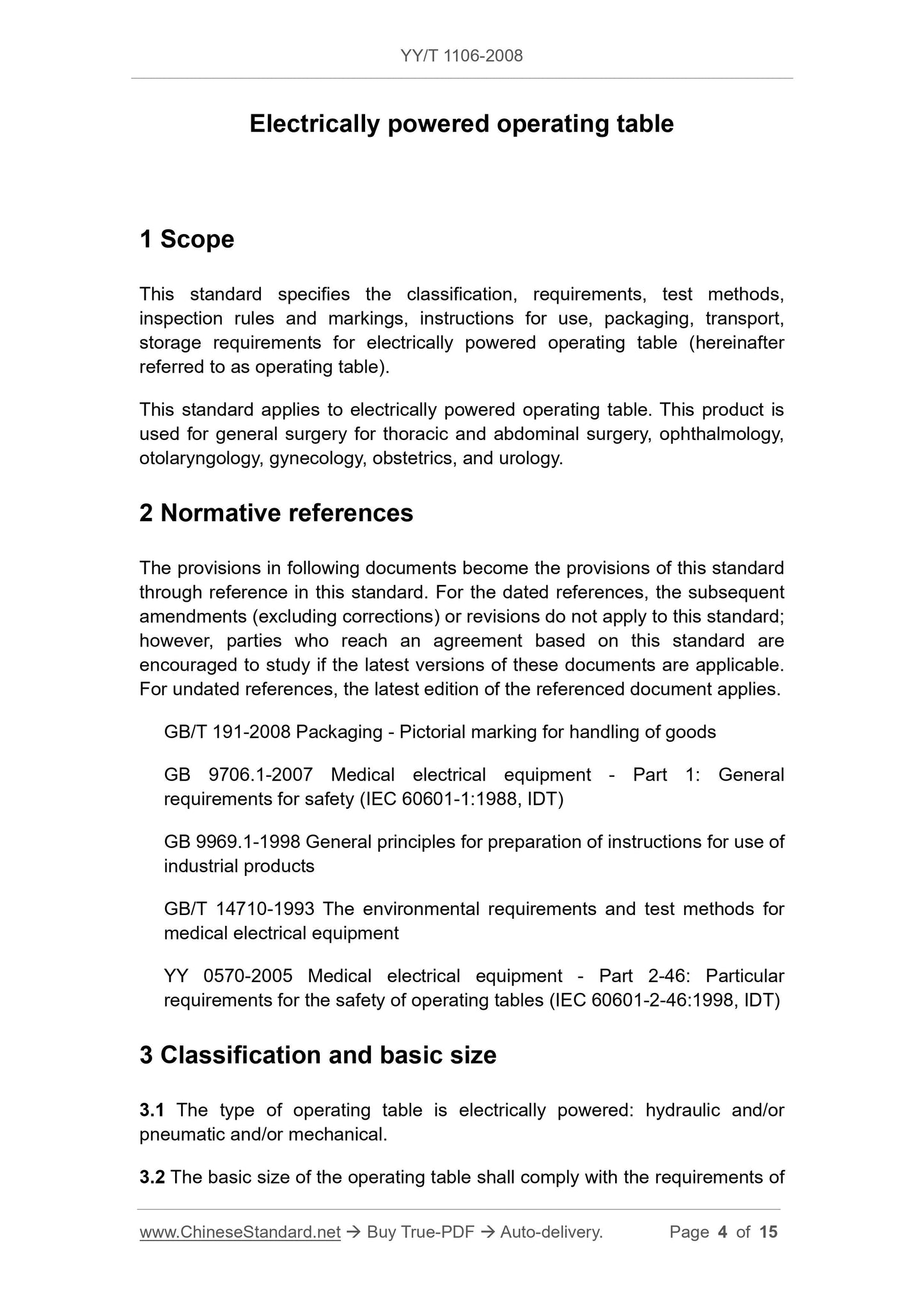
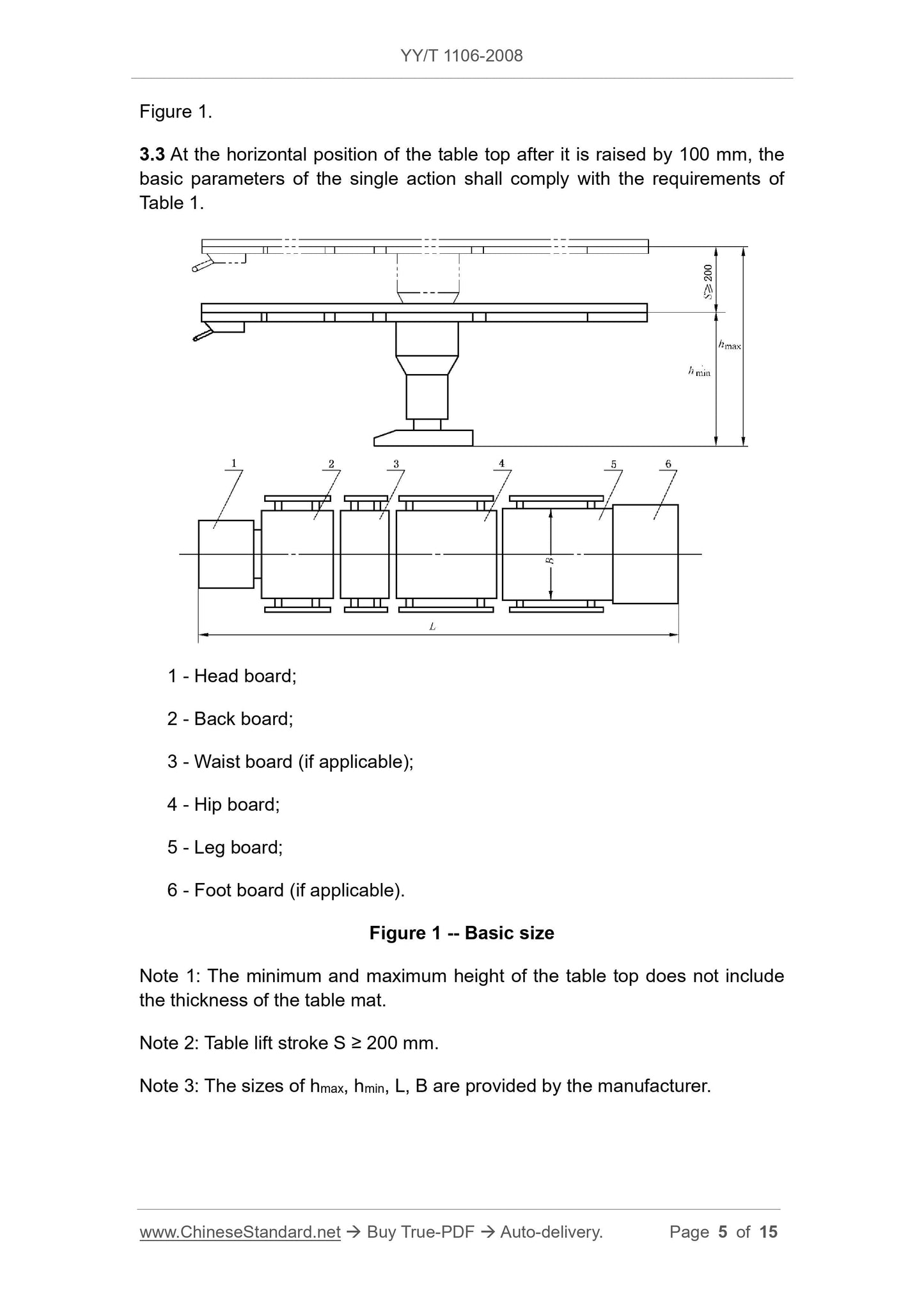
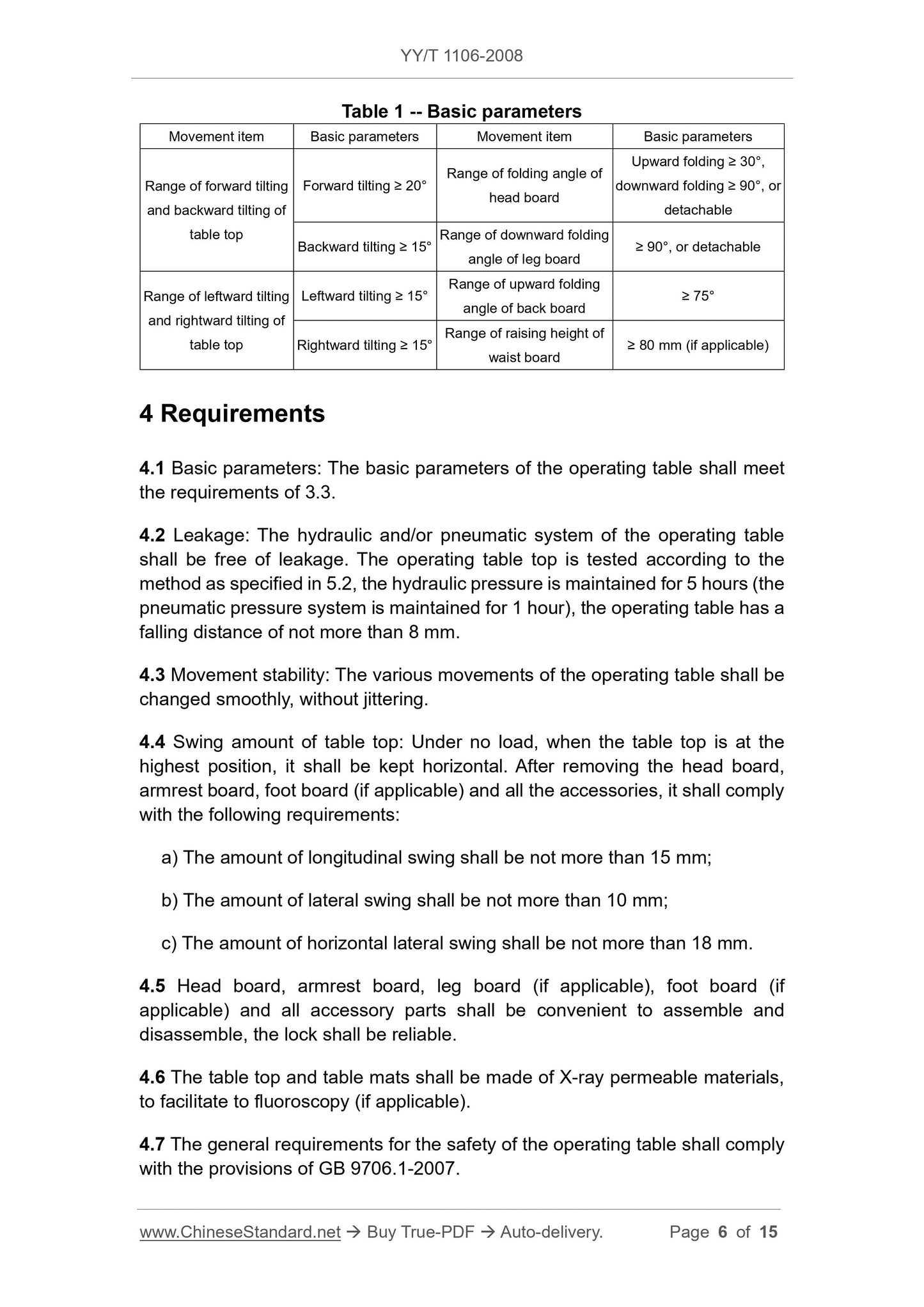
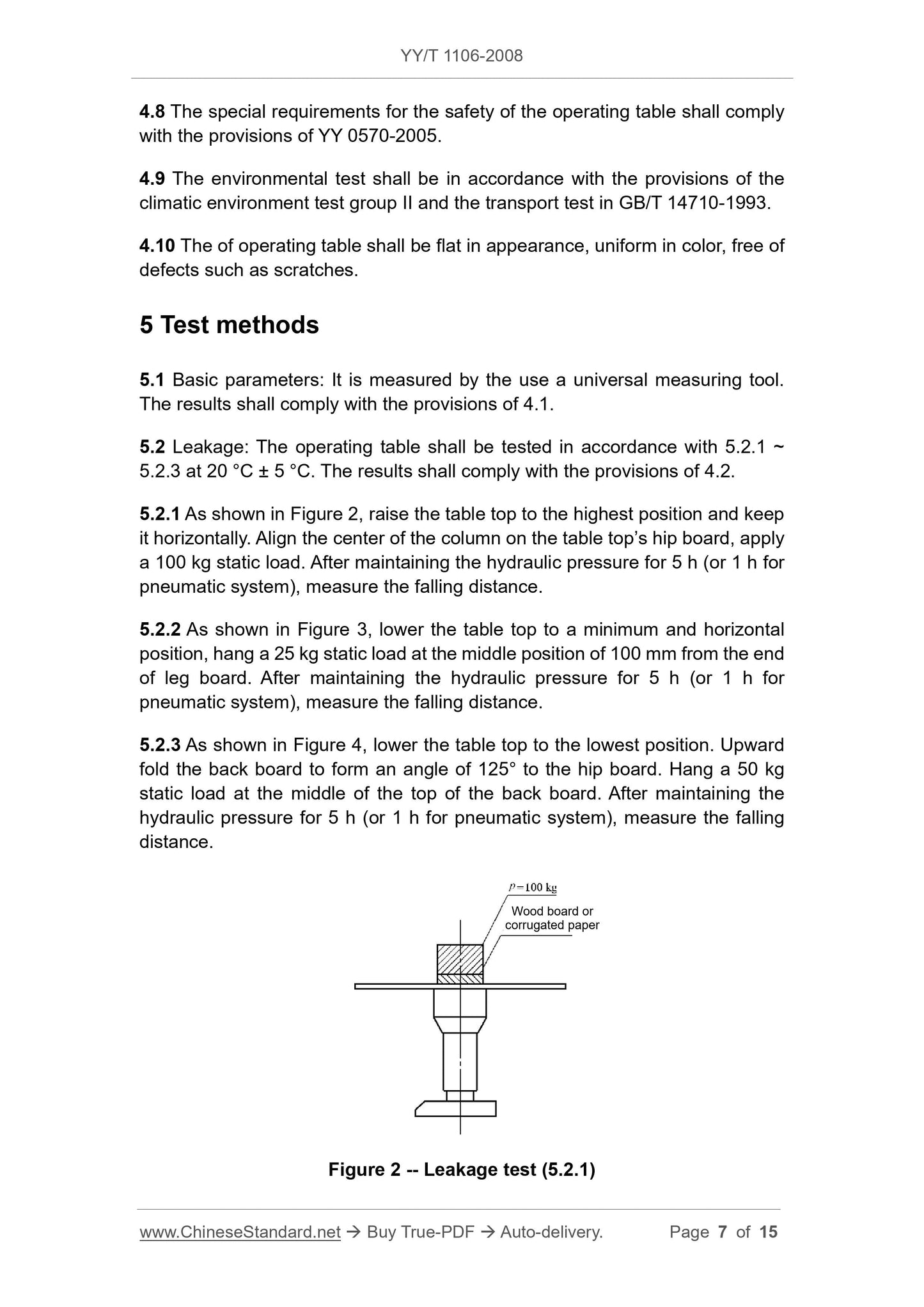
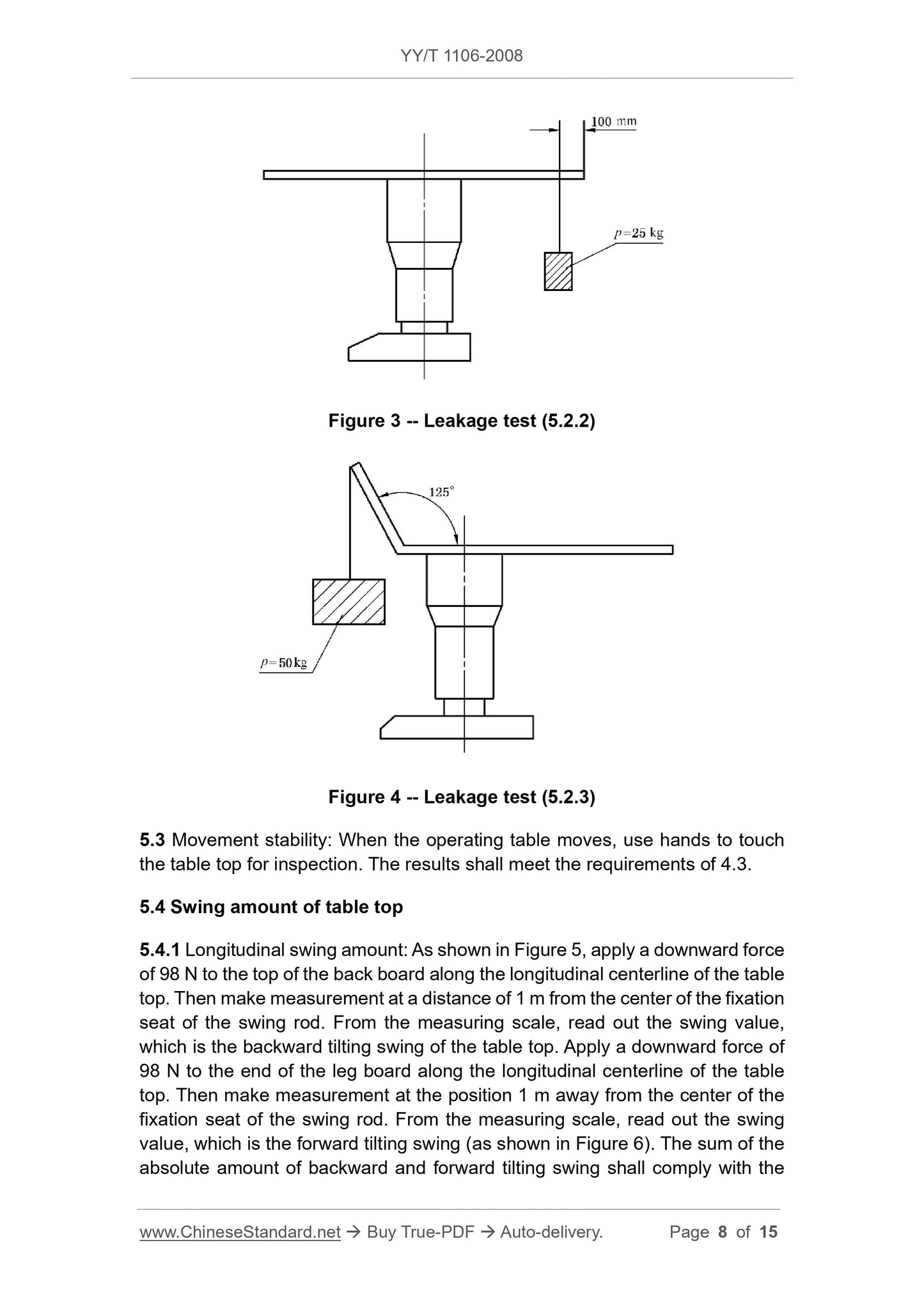
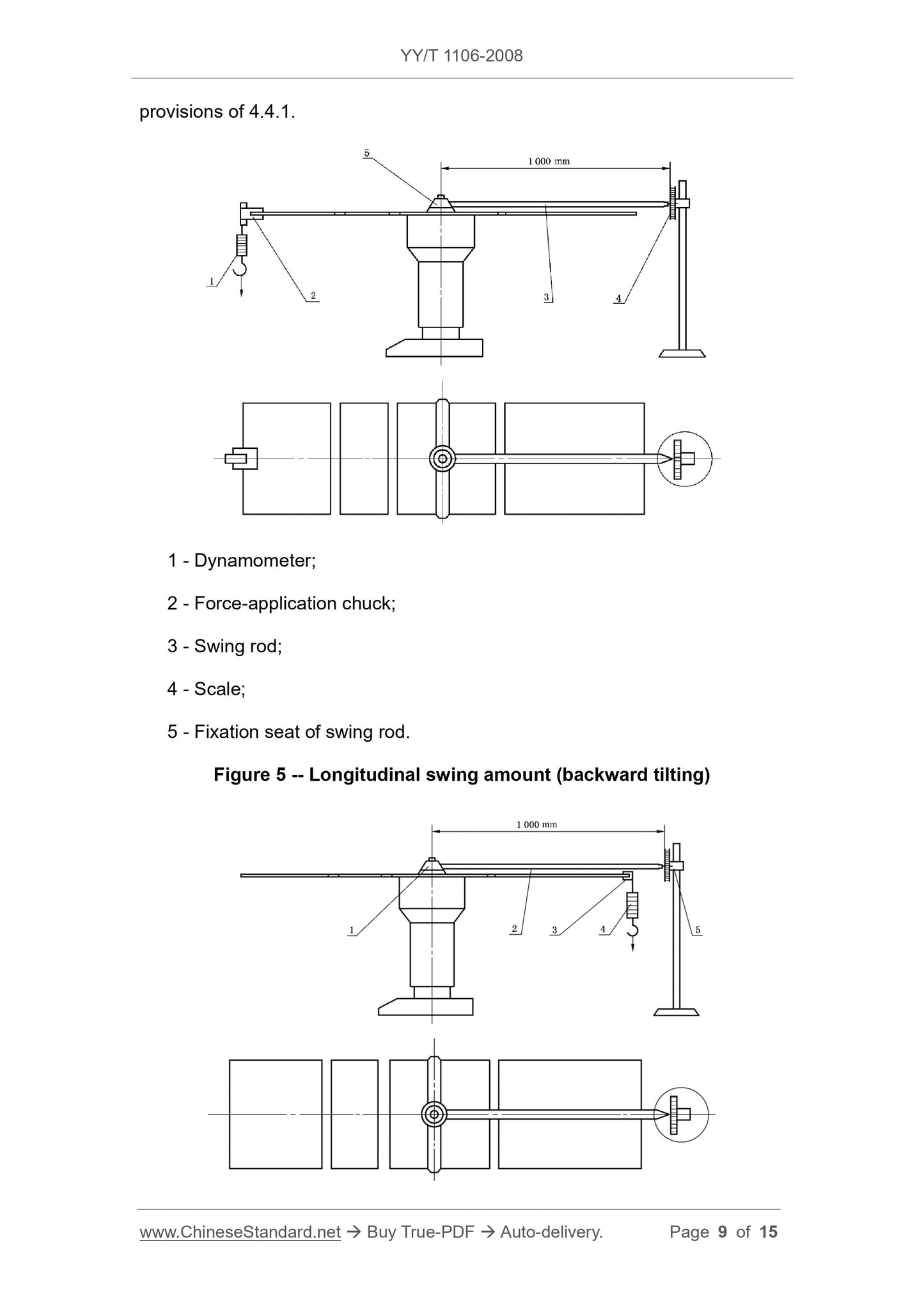
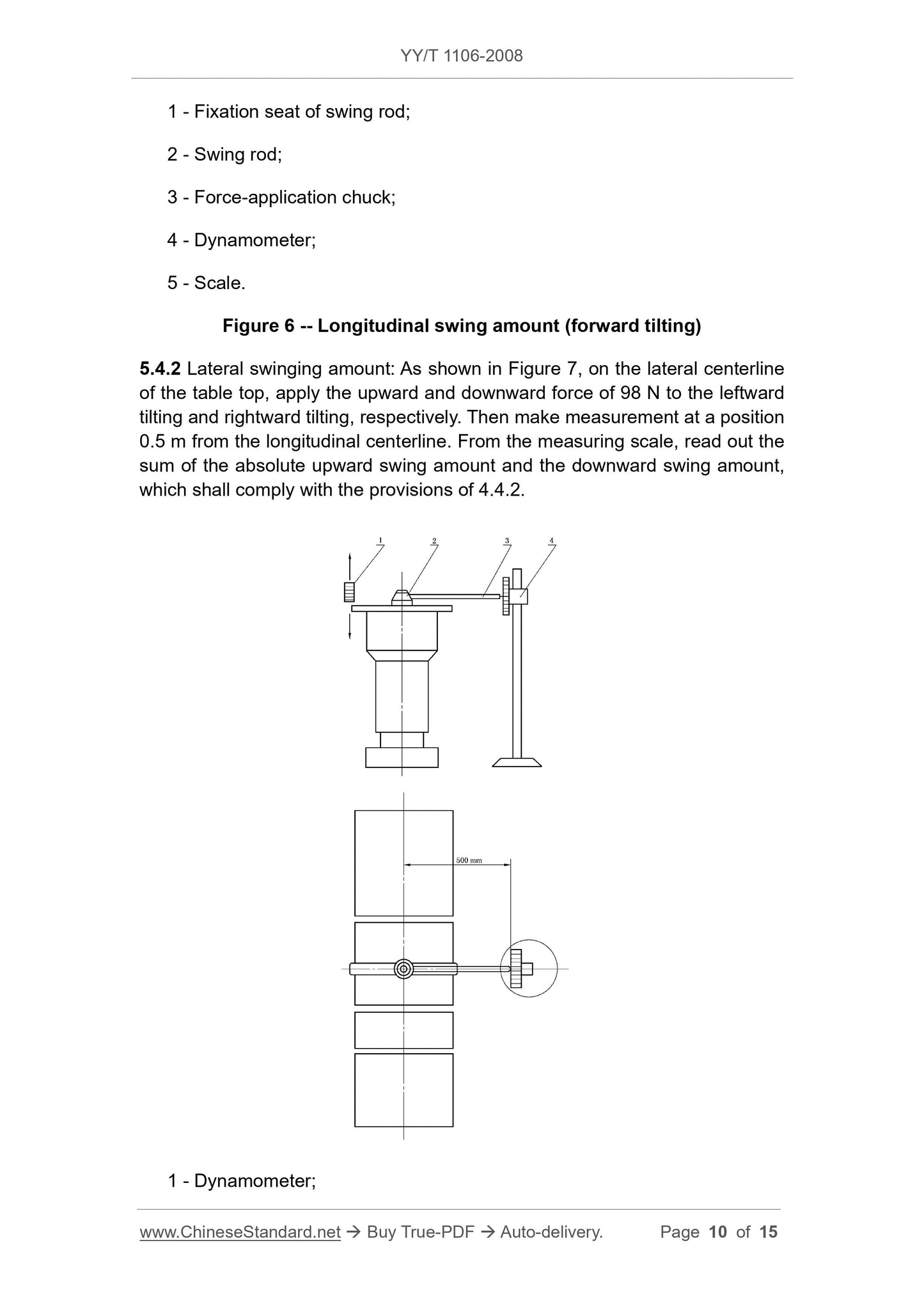
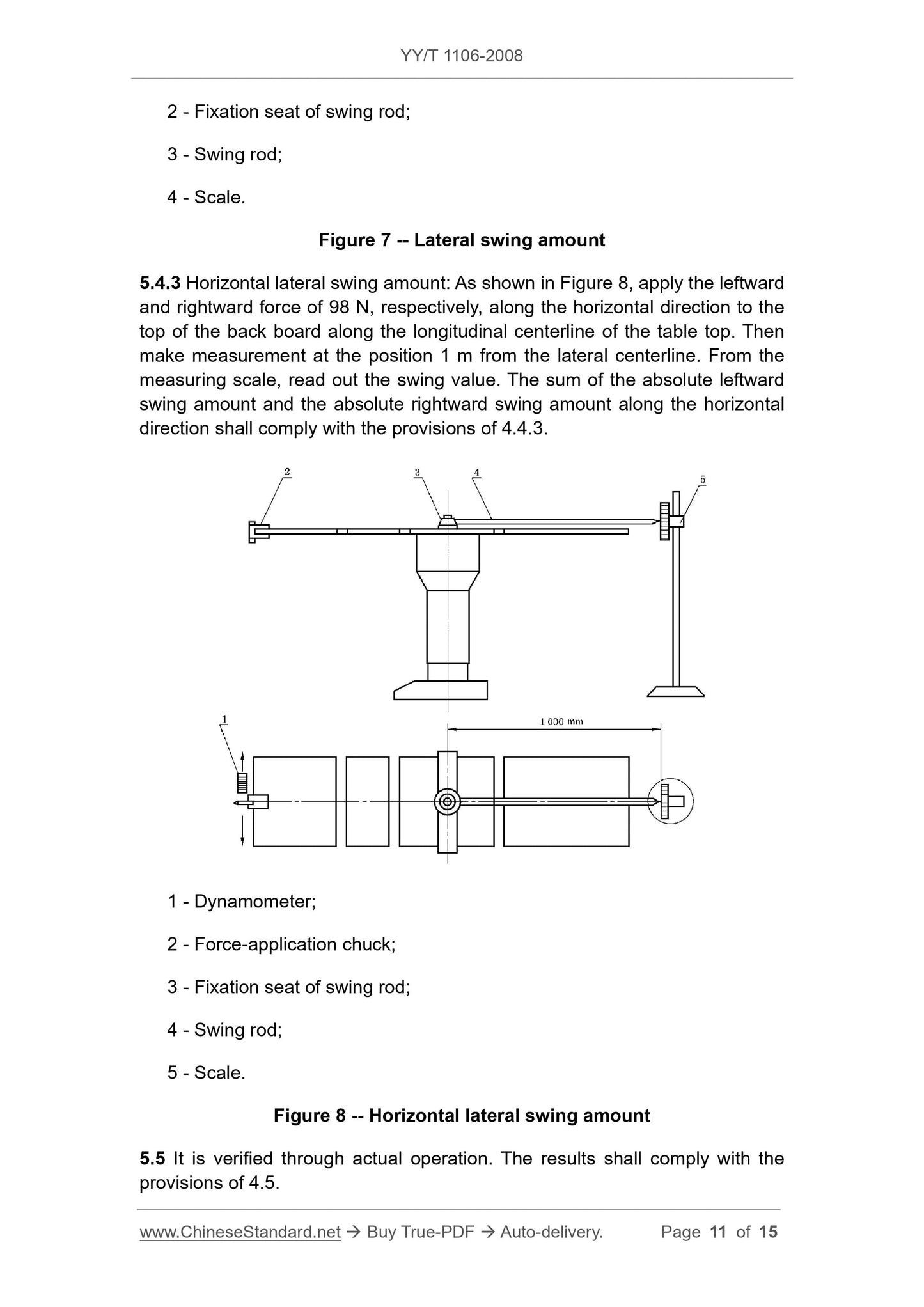
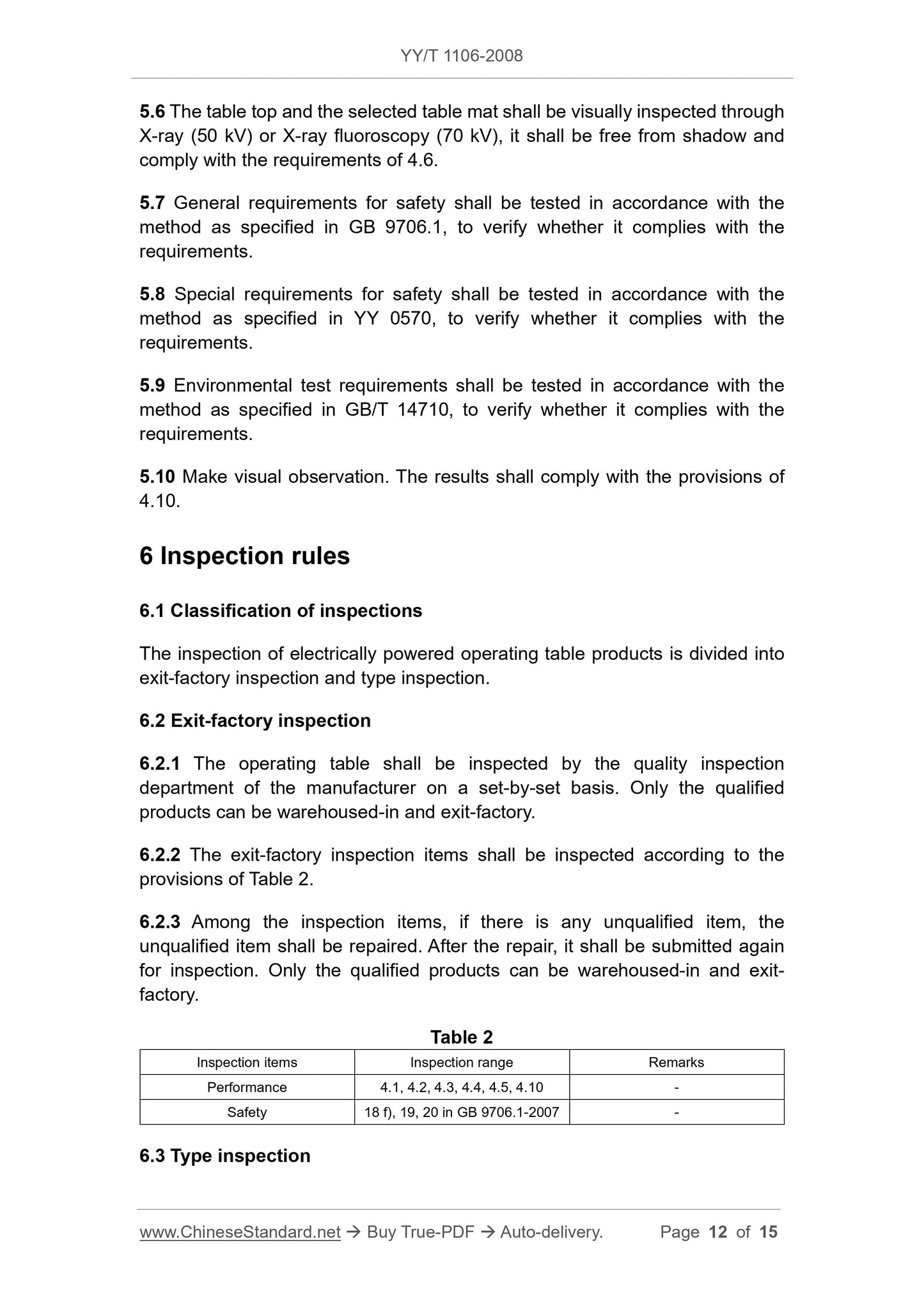