1
/
of
11
PayPal, credit cards. Download editable-PDF & invoice in 1 second!
YY/T 1702-2020 English PDF (YYT1702-2020)
YY/T 1702-2020 English PDF (YYT1702-2020)
Regular price
$260.00 USD
Regular price
Sale price
$260.00 USD
Unit price
/
per
Shipping calculated at checkout.
Couldn't load pickup availability
Delivery: 3 seconds. Download true-PDF + Invoice.
Get Quotation: Click YY/T 1702-2020 (Self-service in 1-minute)
Historical versions (Master-website): YY/T 1702-2020
Preview True-PDF (Reload/Scroll-down if blank)
YY/T 1702-2020: Dentistry - Additive Manufacturing - Selective Laser Melting Metallic Materials for Fixed and Removable Restorations and Appliances
YY/T 1702-2020
Dentistry--Additive manufacturing--Selective laser melting metallic materials for fixed and removable restorations and appliances
ICS 11.060.10
C33
People's Republic of China Pharmaceutical Industry Standard
Dental Additive Manufacturing Oral Fixation and Movement
Laser selective melting of metal materials for repair
2020-02-21 released
2021-01-01 implementation
Issued by the State Drug Administration
Dental Additive Manufacturing Oral Fixation and Movement
Laser selective melting of metal materials for repair
1 Scope
This standard covers additive manufacturing of metal materials for dental fixation and movable restoration, including those used for porcelain or not for porcelain, or both.
Additive manufacturing metal materials are classified and specified performance requirements and test methods. It also stipulates the accompanying documents and usage instructions for the product packaging.
Requirements for clearing, marking and labeling.
This standard applies to cobalt-chromium alloy, pure titanium and titanium alloy metal powders for laser selective melting of additive manufacturing processes.
2 Normative references
The following documents are indispensable for the application of this document. For dated reference documents, only the dated version applies to this document.
For undated references, the latest version (including all amendments) applies to this document.
GB/T 1479.1-2011 Determination of bulk density of metal powder Part 1.Funnel method
GB/T 1482-2010 Standard funnel method for determination of metal powder fluidity (Hall flow meter)
GB/T 3851-2015 Determination of transverse fracture strength of cemented carbide
GB/T 4340.1-2009 Vickers hardness test of metallic materials Part 1.Test method
GB/T 5162-2006 Determination of Tap Density of Metal Powder
GB/T 5314-2011 Powder sampling method for powder metallurgy
GB/T 10610-2009 Product Geometric Technical Specification (GPS) Surface structure profile method. Rules and methods for evaluating surface structure
GB/T 13298-2015 Metal Microstructure Inspection Method
GB/T 18876.1-2002 Application of automatic image analysis to determine the metallographic structure,
Standard test method for inclusion content and grade. Part 1.Image analysis and stereology determination of inclusion or second phase structure content in steel and other metals
GB/T 19077-2016 Particle size distribution laser diffraction method
GB/T 19660 Industrial automation system and integrated machine tool numerical control coordinate system and motion naming
GB/T 35351-2017 Additive Manufacturing Terminology
YY/T 0466.1-2016 Medical devices used for labeling, marking and providing information symbols for medical devices. Part 1.General requirements
YY 0621.1-2016 Dentistry compatibility test Part 1.Metal-ceramic system
ISO 1942.2009 Dental Terminology
ISO 22674.2016 Metallic materials for fixed and movable restorations in dentistry
3 Terms and definitions
The following terms and definitions defined in ISO 1942.2009, ISO 22674-2016 and GB/T 35351-2017 apply to this
file.
3.1
Laser selective melting
Using a high-energy laser beam, scan the pre-coated metal powder according to the predetermined scanning path, melt it completely, and then cool it down
A technique of forming after solidification.
3.2
Forming origin
The origin defined by the device manufacturer.
[GB/T 35351-2017, definition 2.3.18]
3.3
x axis
The coordinate axis in the device coordinate system that is parallel to the front and perpendicular to the y-axis and z-axis.
Note 1.Unless otherwise specified by the equipment manufacturer, usually refers to the x-axis of the equipment.
Note 2.Except as specified by the equipment manufacturer, the positive x-axis direction is the direction from left to right when viewed from the front of the equipment and facing the origin of the forming space.
Note 3.Usually the x-axis is in the horizontal position.
[GB/T 35351-2017, definition 2.3.20]
3.4
y-axis
The axis perpendicular to the x-axis and z-axis in the device coordinate system.
Note 1.Unless otherwise specified by the equipment manufacturer, it usually refers to the y-axis of the equipment.
Note 2.Except as specified by the equipment manufacturer, the definition of the positive direction of the y-axis follows the right-hand rule of the coordinate system in GB/T 19660, usually when the positive z-axis is upward, at this time
From the front of the device, the direction from the front to the back of the device is the positive direction of the y-axis; when the positive z-axis
The direction from back to front is the positive direction of the y-axis.
Note 3.Usually the y-axis is in a horizontal position.
[GB/T 35351-2017, definition 2.3.21]
3.5
z axis
The coordinate axis perpendicular to the x-axis and y-axis (the plane composed of) in the device coordinate system.
Note 1.Unless otherwise specified by the equipment manufacturer, it usually refers to the z-axis of the equipment.
Note 2.Except as specified by the equipment manufacturer, the definition of the positive z-axis direction follows the right-hand rule of the coordinate system in GB/T 19660.For the use of planes and materials layer by layer
In the process of adding, the normal direction of the layer is the positive direction of the z-axis; for the process of using planes and materials layer by layer, the positive direction of the z-axis is from the first layer to the direction of the subsequent layers.
Note 3.When materials are superimposed from different directions [for example, in a directional energy deposition system], the z-axis can be determined according to GB/T 19660 rotation or rolling.
[GB/T 35351-2017, definition 2.3.22]
3.6
Powder sphericity (roundness) roundness
On the observation surface, the ratio of the actual cross-sectional area of the particle to the area corresponding to the longest diameter of the particle.
Sphericity (roundness) is an index that measures the similarity between particles and circles. The sphericity (roundness) varies from 0 to 1.The sphericity (roundness) value of a perfect circle is 1.
[ASTMF1877-2016, definition 11.3.5]
3.7
D10
The particle size when the cumulative volume distribution in the particle size distribution curve reaches 10%.
3.8
D90
The particle size corresponding to the cumulative volume distribution of 90% in the particle size distribution curve.
4 categories
This standard adopts the classification in ISO 22674-2016, and divides metal materials into 6 types based on mechanical properties.
Examples of the intended use of these 6 types of metal materials are as follows.
---0 type. used for single-tooth fixed restorations with low stress, such as small veneer single-sided inlays and veneer crowns;
---1 type. used for single-tooth fixed restorations with low stress, such as veneer or non-veneer single-sided inlays, veneer crowns;
- Type-2.used for single-tooth fixed restorations, such as crowns or inlays (the number of surfaces is not limited);
---3 type. used for multi-unit fixed restorations, such as bridges;
---4 type. used for prostheses with thin parts that bear extremely high stress, such as removable partial dentures, snap rings, thin crowns, and large spans
Or the superstructure of fixed restorations, rods, attachments and implants with small cross-sections;
---5 type. used for restorations that require high hardness and strength, such as thin removable partial dentures, parts with small cross-sections, and snap rings.
5 requirements
5.1 Metal powder
5.1.1 Chemical composition
According to 8.1.1 test, it should meet the requirements of 5.1 in ISO 22674-2016.
5.1.2 Harmful ingredients
According to 8.1.1 test, it should meet the requirements of 5.2 in ISO 22674-2016.
5.1.3 Powder appearance
According to the test in 8.1.2, the powder is uniform and there is no visible impurities.
5.1.4 Sphericity
According to 8.1.3 test, the sphericity should not be lower than the manufacturer's claimed value.
5.1.5 Powder size and distribution
According to 8.1.4 test, D10≥12μm, D90≤65μm.
5.1.6 Powder flowability
According to the test in 8.1.5, cobalt-chromium alloy powder. not more than 40s/50g; titanium and titanium alloy powder. not more than 50s/50g.
5.1.7 Bulk density of powder
Test according to 8.1.6, cobalt-chromium alloy powder. not less than 4.0g/cm3; titanium and titanium alloy powder. not less than 2.2g/cm3.
5.1.8 Tap density of powder
According to 8.1.7 test, cobalt-chromium alloy powder. not less than 4.5g/cm3; titanium and titanium alloy powder. not less than 2.5g/cm3.
5.2.6 Density
According to 8.2.6 test, it should meet the requirements of 5.6 in ISO 22674-2016.
5.2.7 Corrosion resistance
According to 8.2.7 test, it should meet the requirements of 5.7 in ISO 22674-2016.
5.2.8 Anti-darkness
If the manufacturer declares that the material has anti-dark properties, the test according to 8.2.8 shall meet the requirements of 5.8 in ISO 22674-2016.
5.2.9 Linear expansion coefficient
This requirement only applies to metal materials for metal-ceramic restorations. The test according to 8.2.9 should meet the requirements of 5.10 in ISO 22674-2016.
Claim.
5.2.10 The performance of the metal-ceramic system-peeling/initiating crack strength
This requirement is only applicable to metal materials for metal-ceramic restorations. According to 8.2.10, the test should meet the requirements of 4.2 in YY 0621.1-2016.
Claim.
5.2.11 Biocompatibility
See introduction.
6 sampling
The powder sampling by the manufacturer should comply with GB/T 5314-2011.
The sample size should be able to meet the requirements of 7.3 preparation of samples, and the samples taken should be of the same batch. In addition, packaging information, instructions for use, labels
Identification and labeling meet the requirements of Chapter 9 and Chapter 10.
7 Sample preparation
7.1 Overview
Prepare all samples in accordance with the documentation attached to the product packaging (see 9.1) and the manufacturer's instructions (see 9.2).
The effect of printing direction on performance should be fully considered, tensile performance, bending performance, corrosion resistance, dullness resistance, linear expansion coefficient and metal-ceramic
The performance of the system should prepare two sets of samples, that is, the long axis of the sample is parallel to the printing growth direction (z-axis direction) and the long axis of the sample is perpendicular to the printing growth
Direction (x-axis or y-axis direction). The performance of the two sets of specimens in the two printing directions should meet the requirements of the corresponding clauses.
Replace all samples with visible defects.
The sample preparer should provide relevant information and main printing parameters of the printing equipment used (including at least. laser power, scanning speed, printing room
Distance, spot diameter and powder layer thickness).
The relevant information and main printing parameters of the printing equipment provided by the manufacturer should be confirmed, and the performance of the printed product should meet the requirements of this standard.
All requirements. If you change the printing equipment and main printing parameters, the printed product performance should be reconfirmed according to 5.2.
7.2 Heat treatment
7.2.1 Metal materials recommended for heat treatment in the manufacturer's instructions
If the manufacturer recommends heat treatment [9.2c)], the heat treatment should be carried out in accordance with the heat treatment conditions specified in the manufacturer’s instruction manual
7.3.3 Mechanical properties
7.3.3.1 Tensile performance
Prepare samples in accordance with ISO 22674-2016 in 7.3, 7.4 and 7.5.2.The long axis of the sample is parallel to the printing growth direction
(z-axis direction) and the long axis of the sample are perpendicular to the printing growth direction (x-axis or y-axis direction) to prepare 2 sets of samples (6 samples per set). Sample
Perform heat treatment in accordance with 7.2.1.
7.3.3.2 Bending performance
Prepare (25±2)mm×(2.0±0.1)mm×(2.0±0.1)mm specimens according to the manufacturer’s instructions, and take the long axis of the specimen parallel to
The printing growth direction (z-axis direction) and the long axis of the sample are perpendicular to the printing growth direction (x-axis or y-axis direction) to prepare 6 samples each. Sample press
Perform heat treatment according to 7.2.1.
7.3.4 Corrosion resistance
Perform sample preparation in accordance with ISO 22674-2016 in 7.7.The long axis of the sample is parallel to the printing growth direction (z axis direction)
Prepare two samples each with the long axis of the sample perpendicular to the printing growth direction (x-axis or y-axis direction). The samples are heat treated in accordance with 7.2.1.
7.3.5 Anti-darkness
Perform sample preparation in accordance with ISO 22674-2016 in 7.8.The long axis of the sample is parallel to the printing growth direction (z axis direction)
Prepare two samples each with the long axis of the sample perpendicular to the printing growth direction (x-axis or y-axis direction). The samples are heat treated in accordance with 7.2.1.
7.3.6 Linear thermal expansion
Perform sample preparation in accordance with ISO 22674-2016, 7.9.The long axis of the sample is parallel to the printing growth direction (z axis direction)
Prepare two samples each with the long axis of the sample perpendicular to the printing growth direction (x-axis or y-axis direction). The samples are heat treated in accordance with 7.2.1.
7.3.7 Performance of the metal-ceramic system---peel/crack initiation strength
Prepare samples in accordance with the provisions of 6.4.2 in YY 0621.1-2016.The long axis of the sample is parallel to the printing growth direction (z-axis
6 specimens were prepared in each direction) and the long axis of the specimen was perpendicular to the printing growth direction (x-axis or y-axis direction). The samples are heat treated in accordance with 7.2.1.
8 Test method
8.1 Metal powder
8.1.1 Chemical composition and harmful ingredients
According to ISO 22674-2016 in 8.2 test, it should meet the requirements of 5.1.1 and 5.1.2.
8.1...
Get Quotation: Click YY/T 1702-2020 (Self-service in 1-minute)
Historical versions (Master-website): YY/T 1702-2020
Preview True-PDF (Reload/Scroll-down if blank)
YY/T 1702-2020: Dentistry - Additive Manufacturing - Selective Laser Melting Metallic Materials for Fixed and Removable Restorations and Appliances
YY/T 1702-2020
Dentistry--Additive manufacturing--Selective laser melting metallic materials for fixed and removable restorations and appliances
ICS 11.060.10
C33
People's Republic of China Pharmaceutical Industry Standard
Dental Additive Manufacturing Oral Fixation and Movement
Laser selective melting of metal materials for repair
2020-02-21 released
2021-01-01 implementation
Issued by the State Drug Administration
Dental Additive Manufacturing Oral Fixation and Movement
Laser selective melting of metal materials for repair
1 Scope
This standard covers additive manufacturing of metal materials for dental fixation and movable restoration, including those used for porcelain or not for porcelain, or both.
Additive manufacturing metal materials are classified and specified performance requirements and test methods. It also stipulates the accompanying documents and usage instructions for the product packaging.
Requirements for clearing, marking and labeling.
This standard applies to cobalt-chromium alloy, pure titanium and titanium alloy metal powders for laser selective melting of additive manufacturing processes.
2 Normative references
The following documents are indispensable for the application of this document. For dated reference documents, only the dated version applies to this document.
For undated references, the latest version (including all amendments) applies to this document.
GB/T 1479.1-2011 Determination of bulk density of metal powder Part 1.Funnel method
GB/T 1482-2010 Standard funnel method for determination of metal powder fluidity (Hall flow meter)
GB/T 3851-2015 Determination of transverse fracture strength of cemented carbide
GB/T 4340.1-2009 Vickers hardness test of metallic materials Part 1.Test method
GB/T 5162-2006 Determination of Tap Density of Metal Powder
GB/T 5314-2011 Powder sampling method for powder metallurgy
GB/T 10610-2009 Product Geometric Technical Specification (GPS) Surface structure profile method. Rules and methods for evaluating surface structure
GB/T 13298-2015 Metal Microstructure Inspection Method
GB/T 18876.1-2002 Application of automatic image analysis to determine the metallographic structure,
Standard test method for inclusion content and grade. Part 1.Image analysis and stereology determination of inclusion or second phase structure content in steel and other metals
GB/T 19077-2016 Particle size distribution laser diffraction method
GB/T 19660 Industrial automation system and integrated machine tool numerical control coordinate system and motion naming
GB/T 35351-2017 Additive Manufacturing Terminology
YY/T 0466.1-2016 Medical devices used for labeling, marking and providing information symbols for medical devices. Part 1.General requirements
YY 0621.1-2016 Dentistry compatibility test Part 1.Metal-ceramic system
ISO 1942.2009 Dental Terminology
ISO 22674.2016 Metallic materials for fixed and movable restorations in dentistry
3 Terms and definitions
The following terms and definitions defined in ISO 1942.2009, ISO 22674-2016 and GB/T 35351-2017 apply to this
file.
3.1
Laser selective melting
Using a high-energy laser beam, scan the pre-coated metal powder according to the predetermined scanning path, melt it completely, and then cool it down
A technique of forming after solidification.
3.2
Forming origin
The origin defined by the device manufacturer.
[GB/T 35351-2017, definition 2.3.18]
3.3
x axis
The coordinate axis in the device coordinate system that is parallel to the front and perpendicular to the y-axis and z-axis.
Note 1.Unless otherwise specified by the equipment manufacturer, usually refers to the x-axis of the equipment.
Note 2.Except as specified by the equipment manufacturer, the positive x-axis direction is the direction from left to right when viewed from the front of the equipment and facing the origin of the forming space.
Note 3.Usually the x-axis is in the horizontal position.
[GB/T 35351-2017, definition 2.3.20]
3.4
y-axis
The axis perpendicular to the x-axis and z-axis in the device coordinate system.
Note 1.Unless otherwise specified by the equipment manufacturer, it usually refers to the y-axis of the equipment.
Note 2.Except as specified by the equipment manufacturer, the definition of the positive direction of the y-axis follows the right-hand rule of the coordinate system in GB/T 19660, usually when the positive z-axis is upward, at this time
From the front of the device, the direction from the front to the back of the device is the positive direction of the y-axis; when the positive z-axis
The direction from back to front is the positive direction of the y-axis.
Note 3.Usually the y-axis is in a horizontal position.
[GB/T 35351-2017, definition 2.3.21]
3.5
z axis
The coordinate axis perpendicular to the x-axis and y-axis (the plane composed of) in the device coordinate system.
Note 1.Unless otherwise specified by the equipment manufacturer, it usually refers to the z-axis of the equipment.
Note 2.Except as specified by the equipment manufacturer, the definition of the positive z-axis direction follows the right-hand rule of the coordinate system in GB/T 19660.For the use of planes and materials layer by layer
In the process of adding, the normal direction of the layer is the positive direction of the z-axis; for the process of using planes and materials layer by layer, the positive direction of the z-axis is from the first layer to the direction of the subsequent layers.
Note 3.When materials are superimposed from different directions [for example, in a directional energy deposition system], the z-axis can be determined according to GB/T 19660 rotation or rolling.
[GB/T 35351-2017, definition 2.3.22]
3.6
Powder sphericity (roundness) roundness
On the observation surface, the ratio of the actual cross-sectional area of the particle to the area corresponding to the longest diameter of the particle.
Sphericity (roundness) is an index that measures the similarity between particles and circles. The sphericity (roundness) varies from 0 to 1.The sphericity (roundness) value of a perfect circle is 1.
[ASTMF1877-2016, definition 11.3.5]
3.7
D10
The particle size when the cumulative volume distribution in the particle size distribution curve reaches 10%.
3.8
D90
The particle size corresponding to the cumulative volume distribution of 90% in the particle size distribution curve.
4 categories
This standard adopts the classification in ISO 22674-2016, and divides metal materials into 6 types based on mechanical properties.
Examples of the intended use of these 6 types of metal materials are as follows.
---0 type. used for single-tooth fixed restorations with low stress, such as small veneer single-sided inlays and veneer crowns;
---1 type. used for single-tooth fixed restorations with low stress, such as veneer or non-veneer single-sided inlays, veneer crowns;
- Type-2.used for single-tooth fixed restorations, such as crowns or inlays (the number of surfaces is not limited);
---3 type. used for multi-unit fixed restorations, such as bridges;
---4 type. used for prostheses with thin parts that bear extremely high stress, such as removable partial dentures, snap rings, thin crowns, and large spans
Or the superstructure of fixed restorations, rods, attachments and implants with small cross-sections;
---5 type. used for restorations that require high hardness and strength, such as thin removable partial dentures, parts with small cross-sections, and snap rings.
5 requirements
5.1 Metal powder
5.1.1 Chemical composition
According to 8.1.1 test, it should meet the requirements of 5.1 in ISO 22674-2016.
5.1.2 Harmful ingredients
According to 8.1.1 test, it should meet the requirements of 5.2 in ISO 22674-2016.
5.1.3 Powder appearance
According to the test in 8.1.2, the powder is uniform and there is no visible impurities.
5.1.4 Sphericity
According to 8.1.3 test, the sphericity should not be lower than the manufacturer's claimed value.
5.1.5 Powder size and distribution
According to 8.1.4 test, D10≥12μm, D90≤65μm.
5.1.6 Powder flowability
According to the test in 8.1.5, cobalt-chromium alloy powder. not more than 40s/50g; titanium and titanium alloy powder. not more than 50s/50g.
5.1.7 Bulk density of powder
Test according to 8.1.6, cobalt-chromium alloy powder. not less than 4.0g/cm3; titanium and titanium alloy powder. not less than 2.2g/cm3.
5.1.8 Tap density of powder
According to 8.1.7 test, cobalt-chromium alloy powder. not less than 4.5g/cm3; titanium and titanium alloy powder. not less than 2.5g/cm3.
5.2.6 Density
According to 8.2.6 test, it should meet the requirements of 5.6 in ISO 22674-2016.
5.2.7 Corrosion resistance
According to 8.2.7 test, it should meet the requirements of 5.7 in ISO 22674-2016.
5.2.8 Anti-darkness
If the manufacturer declares that the material has anti-dark properties, the test according to 8.2.8 shall meet the requirements of 5.8 in ISO 22674-2016.
5.2.9 Linear expansion coefficient
This requirement only applies to metal materials for metal-ceramic restorations. The test according to 8.2.9 should meet the requirements of 5.10 in ISO 22674-2016.
Claim.
5.2.10 The performance of the metal-ceramic system-peeling/initiating crack strength
This requirement is only applicable to metal materials for metal-ceramic restorations. According to 8.2.10, the test should meet the requirements of 4.2 in YY 0621.1-2016.
Claim.
5.2.11 Biocompatibility
See introduction.
6 sampling
The powder sampling by the manufacturer should comply with GB/T 5314-2011.
The sample size should be able to meet the requirements of 7.3 preparation of samples, and the samples taken should be of the same batch. In addition, packaging information, instructions for use, labels
Identification and labeling meet the requirements of Chapter 9 and Chapter 10.
7 Sample preparation
7.1 Overview
Prepare all samples in accordance with the documentation attached to the product packaging (see 9.1) and the manufacturer's instructions (see 9.2).
The effect of printing direction on performance should be fully considered, tensile performance, bending performance, corrosion resistance, dullness resistance, linear expansion coefficient and metal-ceramic
The performance of the system should prepare two sets of samples, that is, the long axis of the sample is parallel to the printing growth direction (z-axis direction) and the long axis of the sample is perpendicular to the printing growth
Direction (x-axis or y-axis direction). The performance of the two sets of specimens in the two printing directions should meet the requirements of the corresponding clauses.
Replace all samples with visible defects.
The sample preparer should provide relevant information and main printing parameters of the printing equipment used (including at least. laser power, scanning speed, printing room
Distance, spot diameter and powder layer thickness).
The relevant information and main printing parameters of the printing equipment provided by the manufacturer should be confirmed, and the performance of the printed product should meet the requirements of this standard.
All requirements. If you change the printing equipment and main printing parameters, the printed product performance should be reconfirmed according to 5.2.
7.2 Heat treatment
7.2.1 Metal materials recommended for heat treatment in the manufacturer's instructions
If the manufacturer recommends heat treatment [9.2c)], the heat treatment should be carried out in accordance with the heat treatment conditions specified in the manufacturer’s instruction manual
7.3.3 Mechanical properties
7.3.3.1 Tensile performance
Prepare samples in accordance with ISO 22674-2016 in 7.3, 7.4 and 7.5.2.The long axis of the sample is parallel to the printing growth direction
(z-axis direction) and the long axis of the sample are perpendicular to the printing growth direction (x-axis or y-axis direction) to prepare 2 sets of samples (6 samples per set). Sample
Perform heat treatment in accordance with 7.2.1.
7.3.3.2 Bending performance
Prepare (25±2)mm×(2.0±0.1)mm×(2.0±0.1)mm specimens according to the manufacturer’s instructions, and take the long axis of the specimen parallel to
The printing growth direction (z-axis direction) and the long axis of the sample are perpendicular to the printing growth direction (x-axis or y-axis direction) to prepare 6 samples each. Sample press
Perform heat treatment according to 7.2.1.
7.3.4 Corrosion resistance
Perform sample preparation in accordance with ISO 22674-2016 in 7.7.The long axis of the sample is parallel to the printing growth direction (z axis direction)
Prepare two samples each with the long axis of the sample perpendicular to the printing growth direction (x-axis or y-axis direction). The samples are heat treated in accordance with 7.2.1.
7.3.5 Anti-darkness
Perform sample preparation in accordance with ISO 22674-2016 in 7.8.The long axis of the sample is parallel to the printing growth direction (z axis direction)
Prepare two samples each with the long axis of the sample perpendicular to the printing growth direction (x-axis or y-axis direction). The samples are heat treated in accordance with 7.2.1.
7.3.6 Linear thermal expansion
Perform sample preparation in accordance with ISO 22674-2016, 7.9.The long axis of the sample is parallel to the printing growth direction (z axis direction)
Prepare two samples each with the long axis of the sample perpendicular to the printing growth direction (x-axis or y-axis direction). The samples are heat treated in accordance with 7.2.1.
7.3.7 Performance of the metal-ceramic system---peel/crack initiation strength
Prepare samples in accordance with the provisions of 6.4.2 in YY 0621.1-2016.The long axis of the sample is parallel to the printing growth direction (z-axis
6 specimens were prepared in each direction) and the long axis of the specimen was perpendicular to the printing growth direction (x-axis or y-axis direction). The samples are heat treated in accordance with 7.2.1.
8 Test method
8.1 Metal powder
8.1.1 Chemical composition and harmful ingredients
According to ISO 22674-2016 in 8.2 test, it should meet the requirements of 5.1.1 and 5.1.2.
8.1...
Share
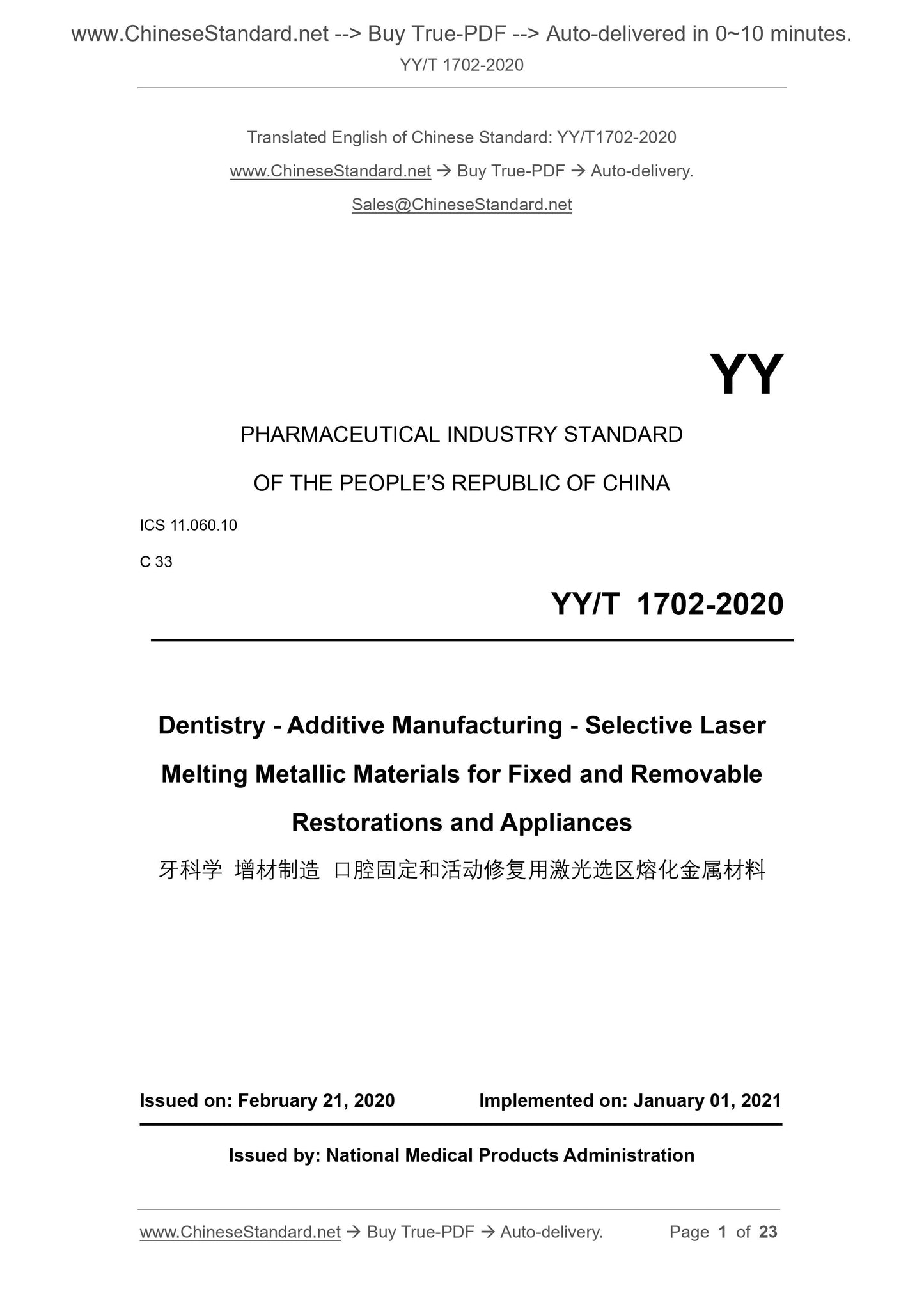
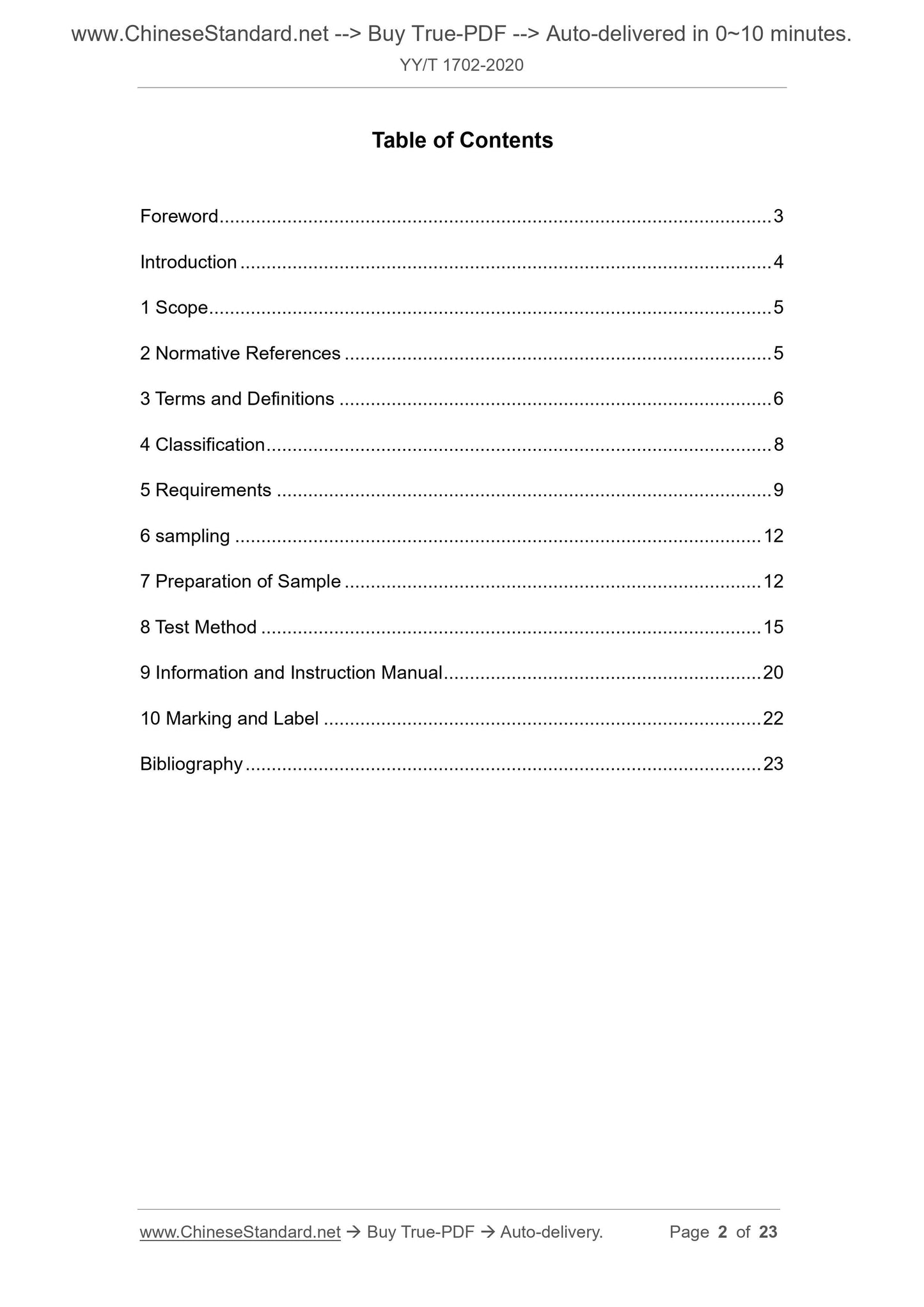
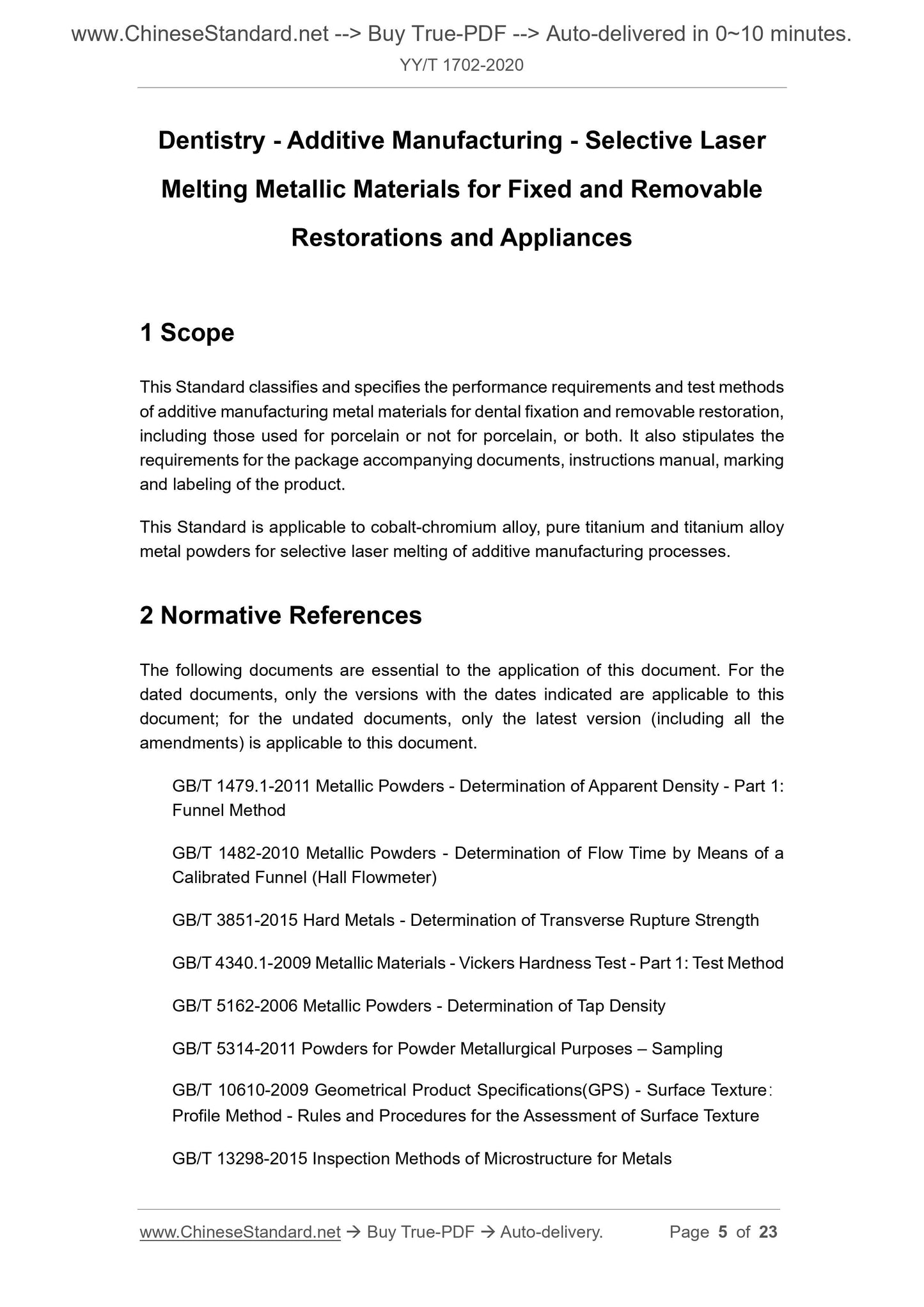
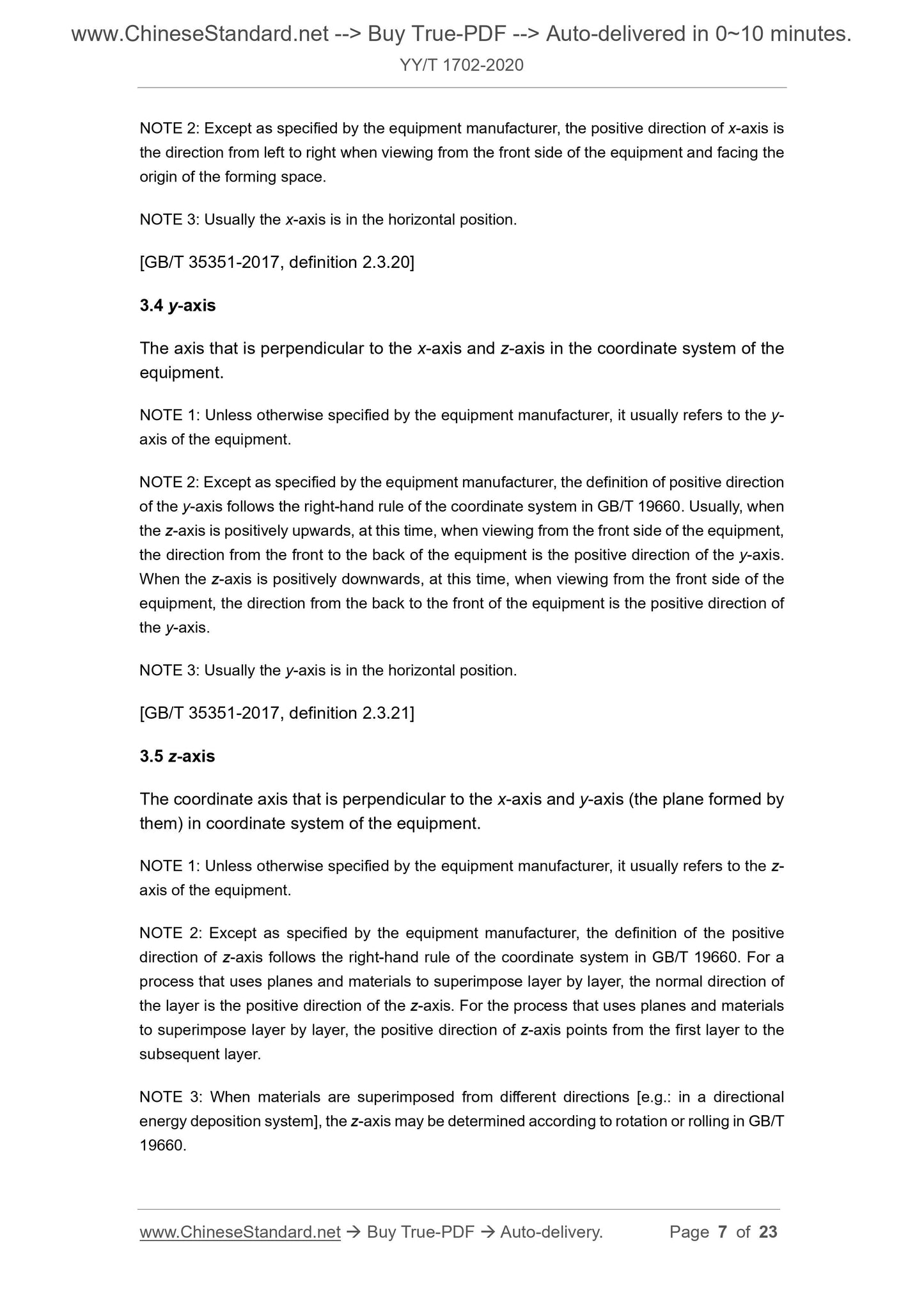
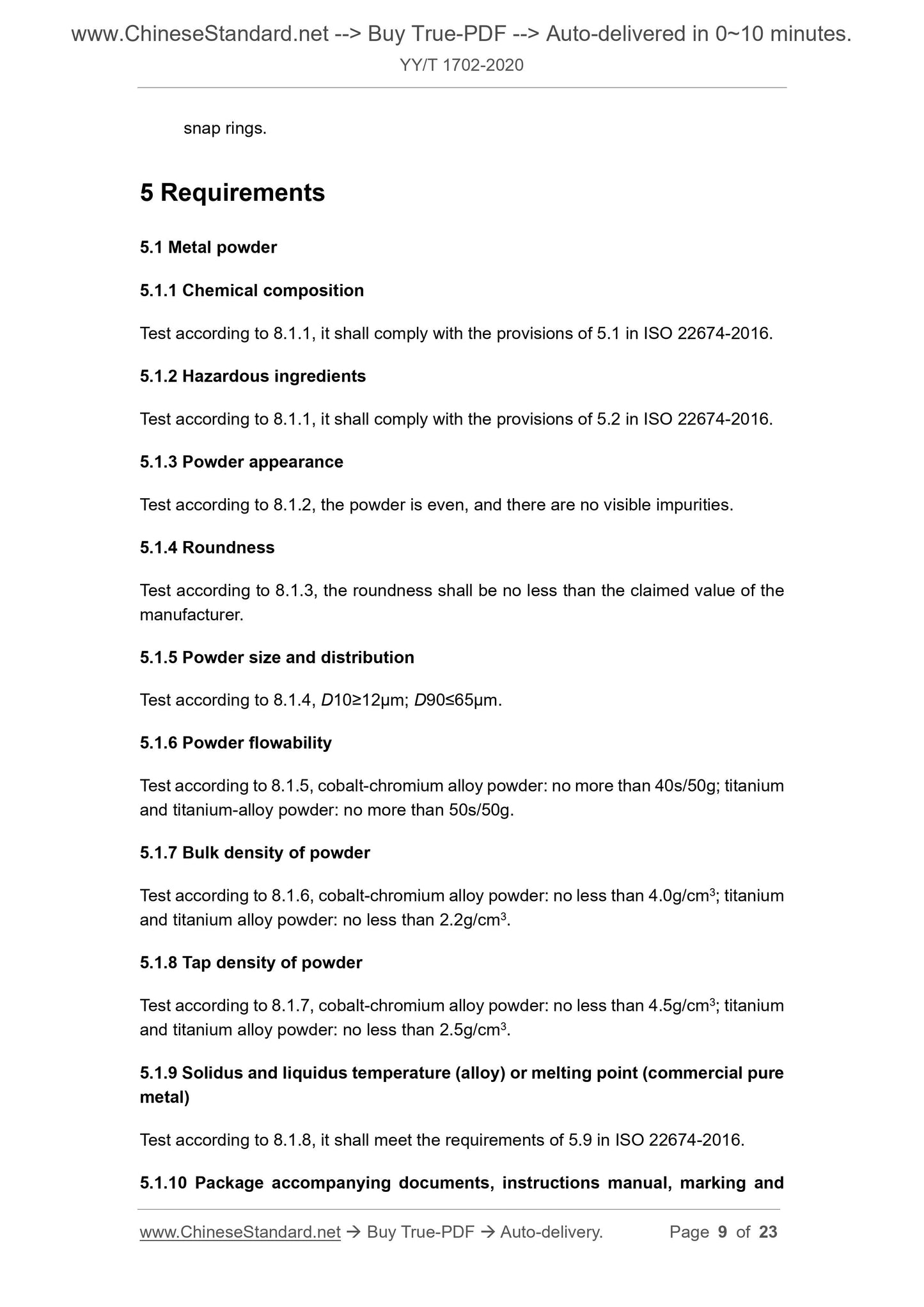
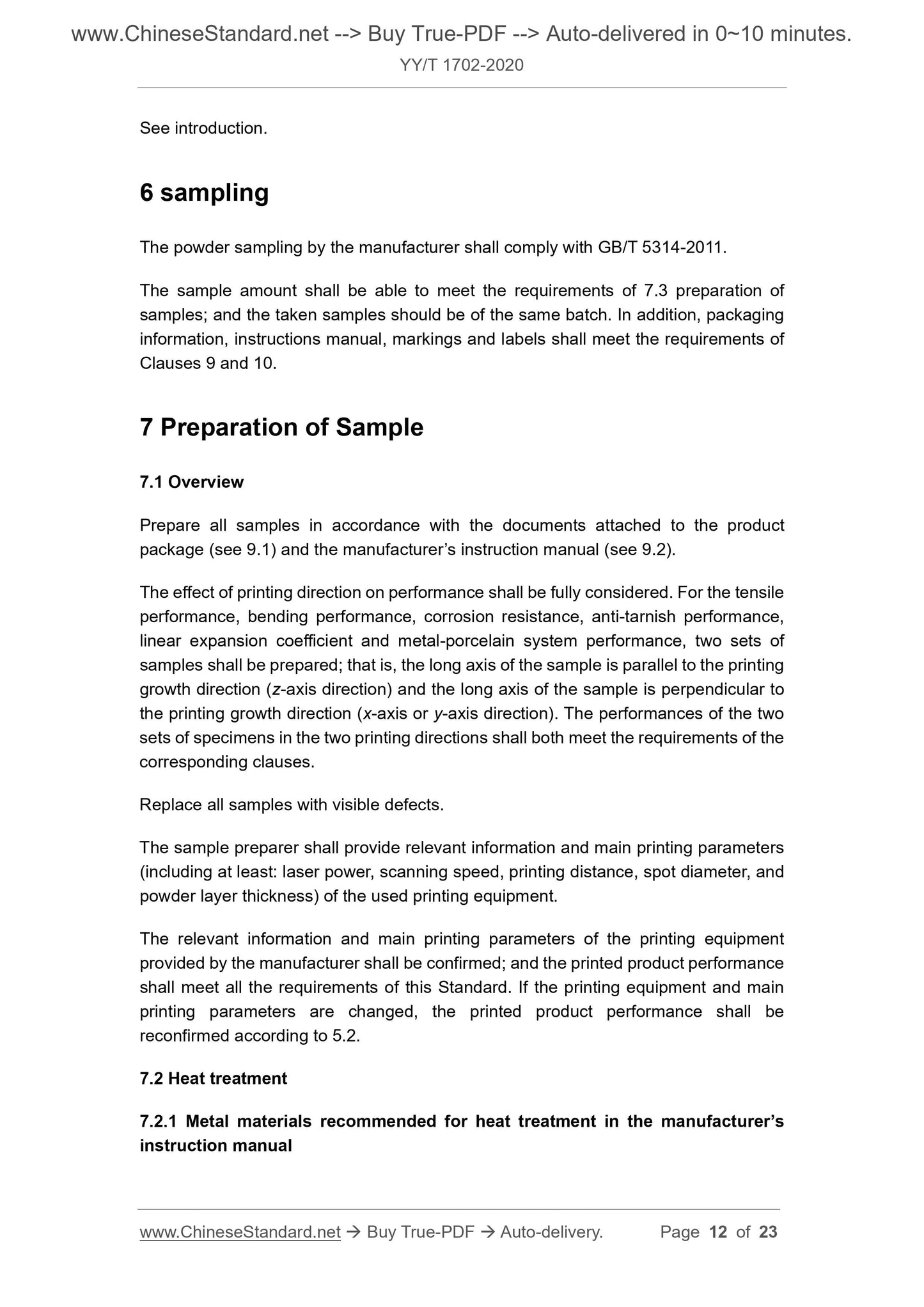
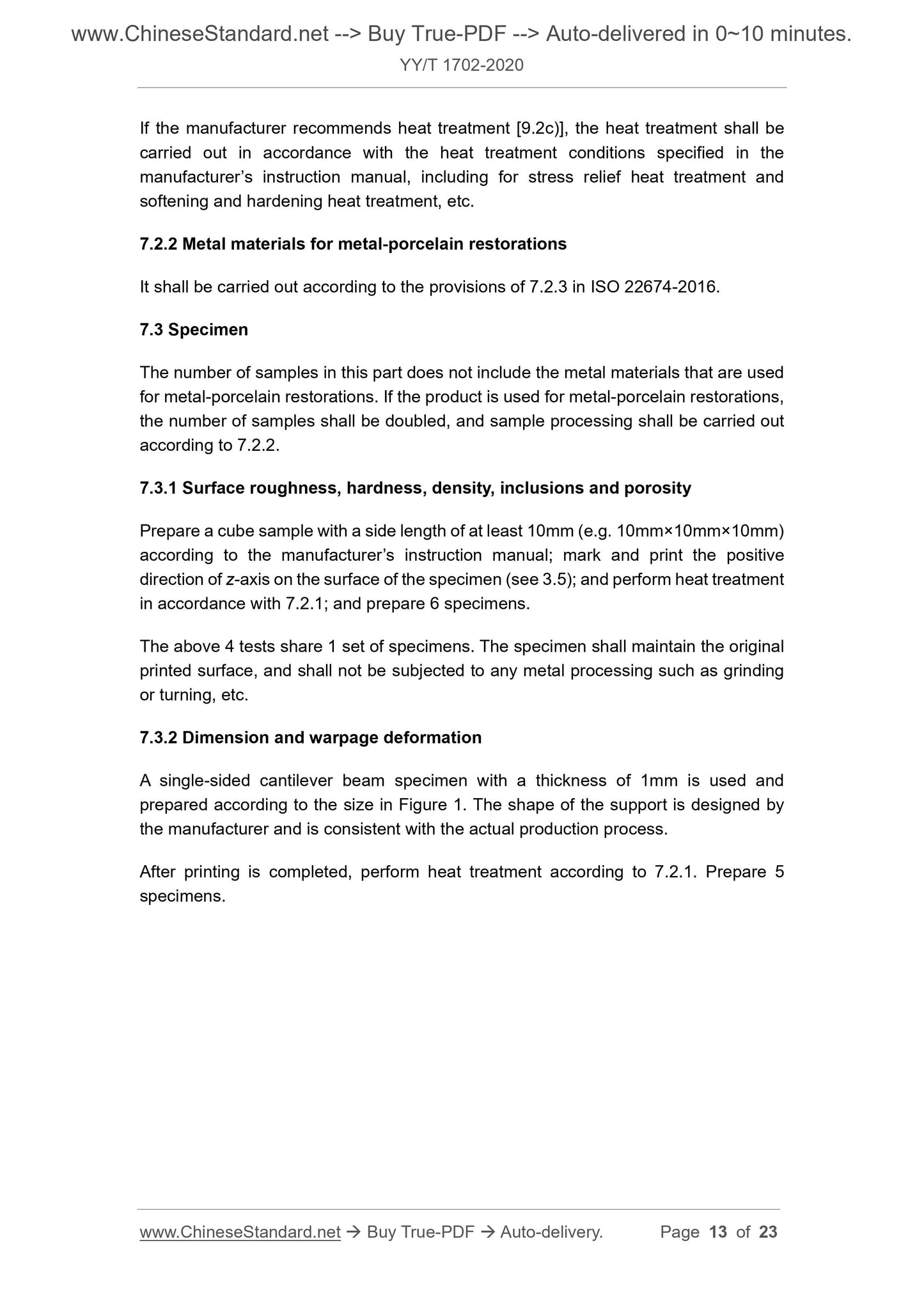
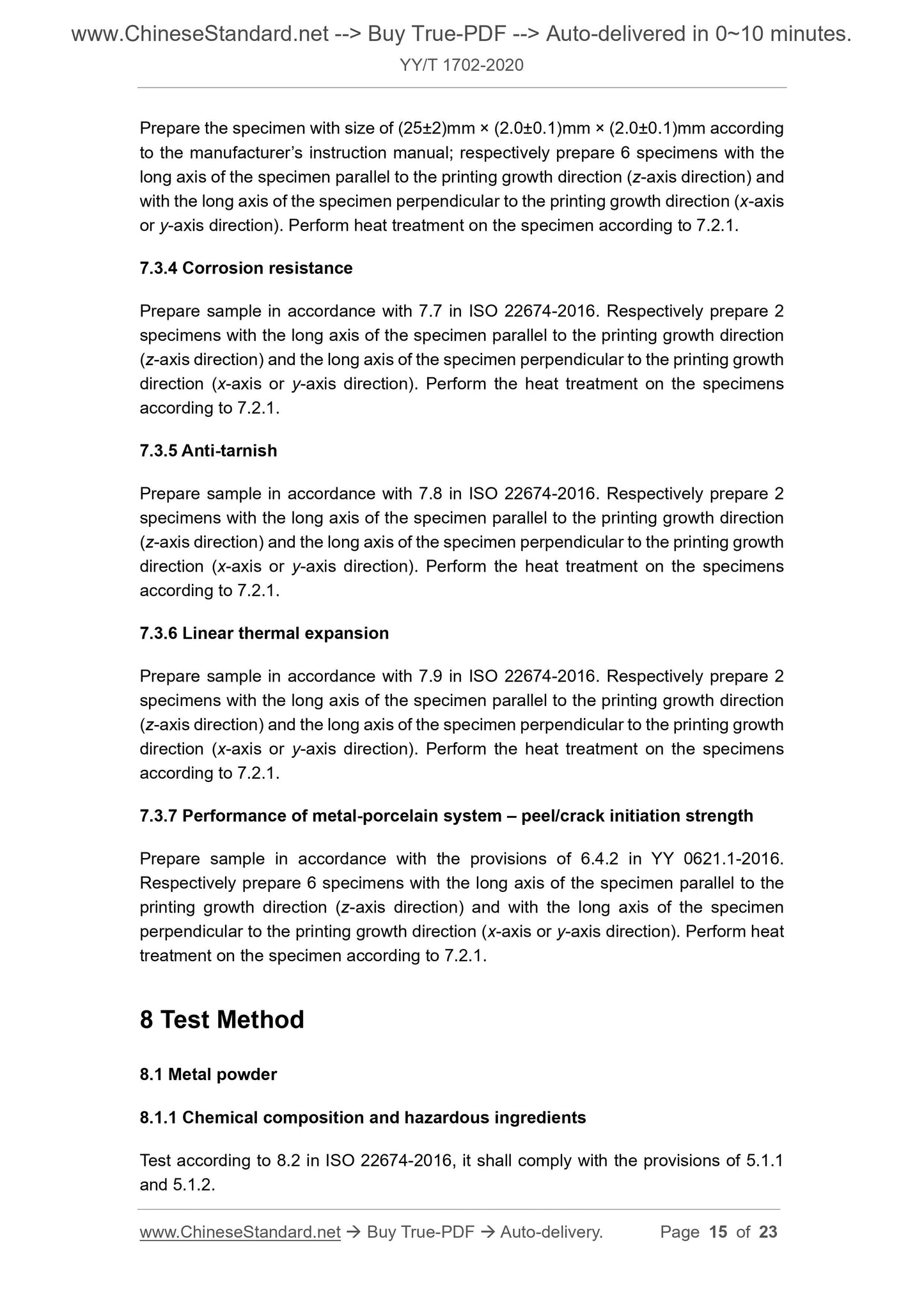
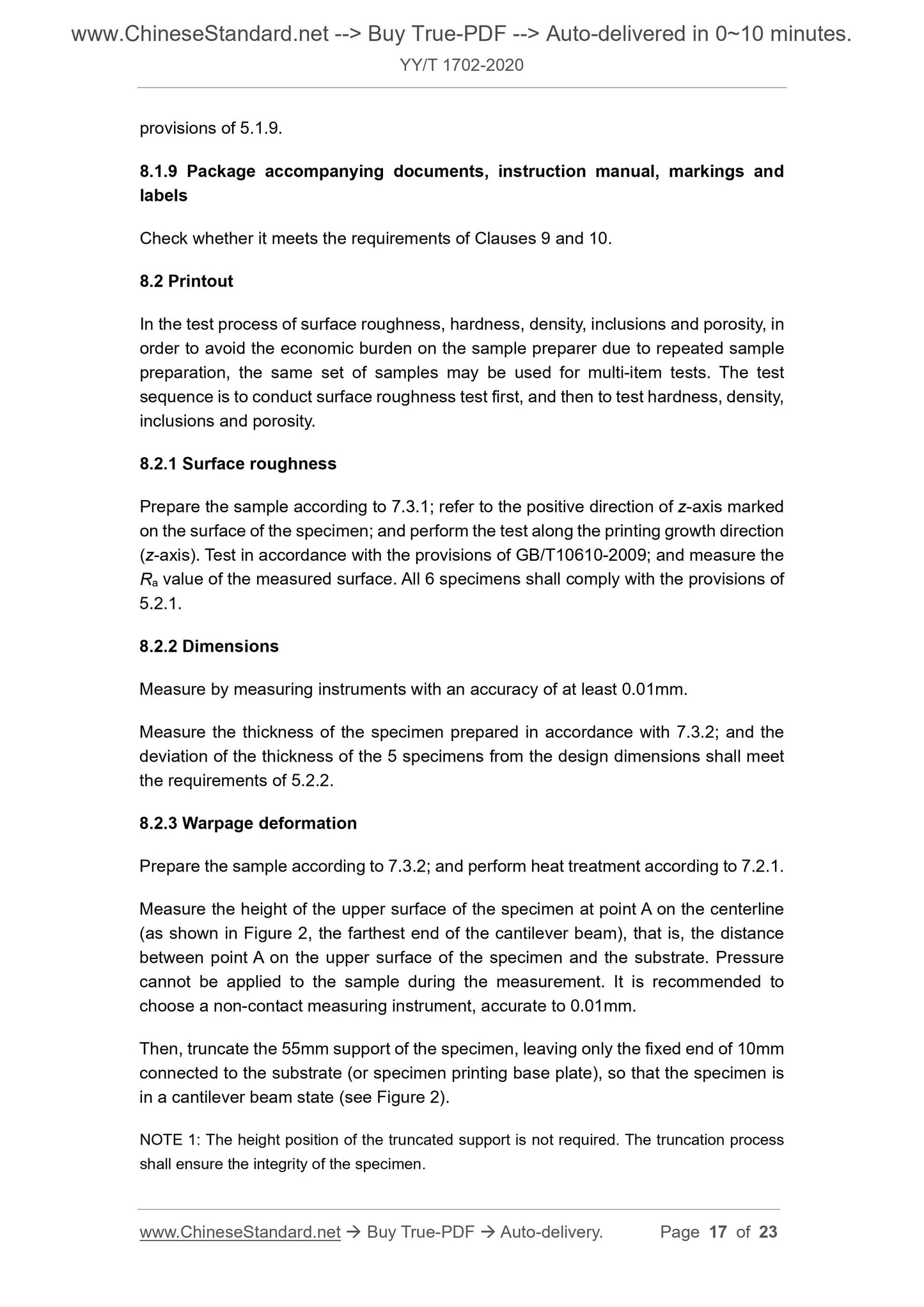
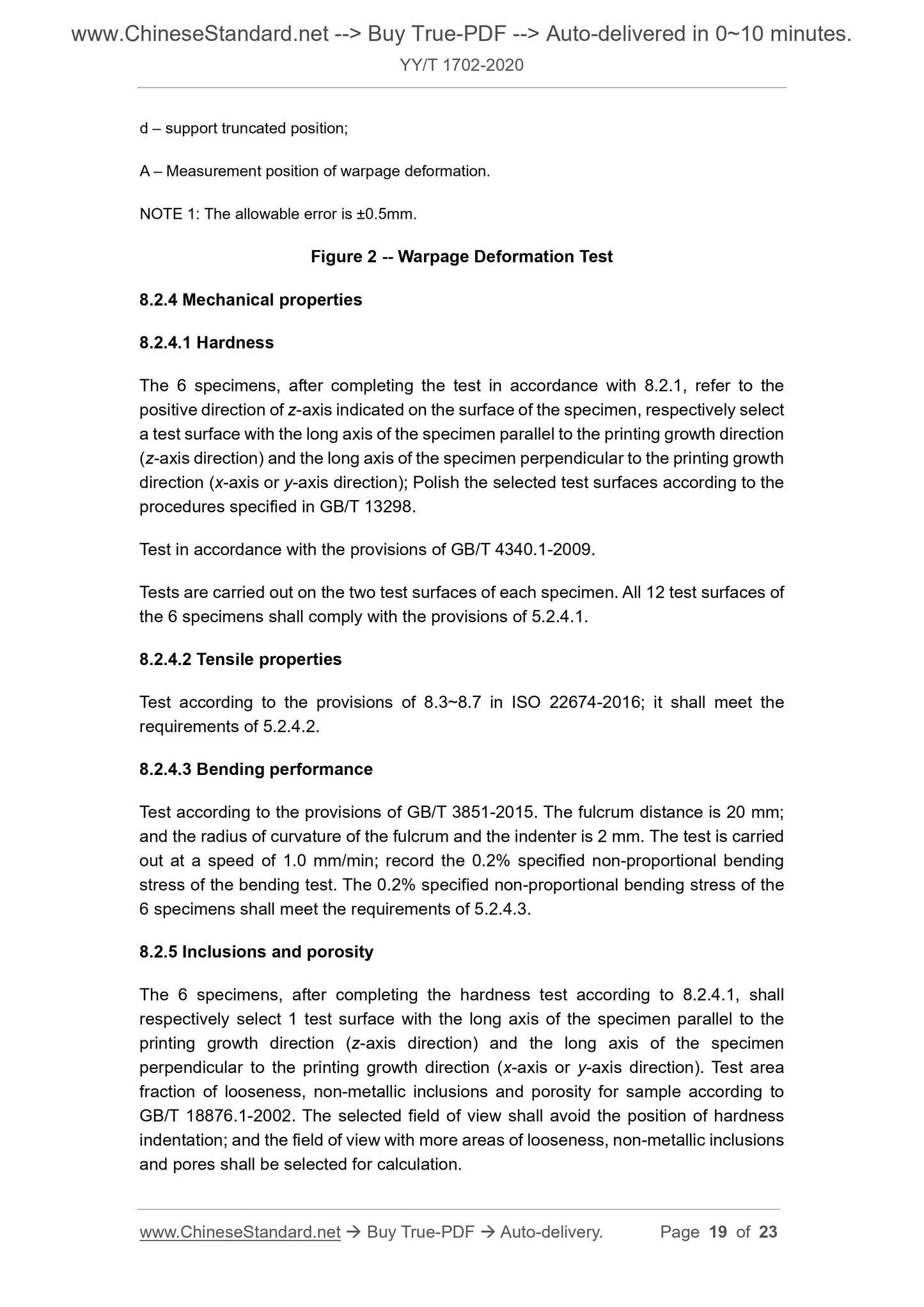
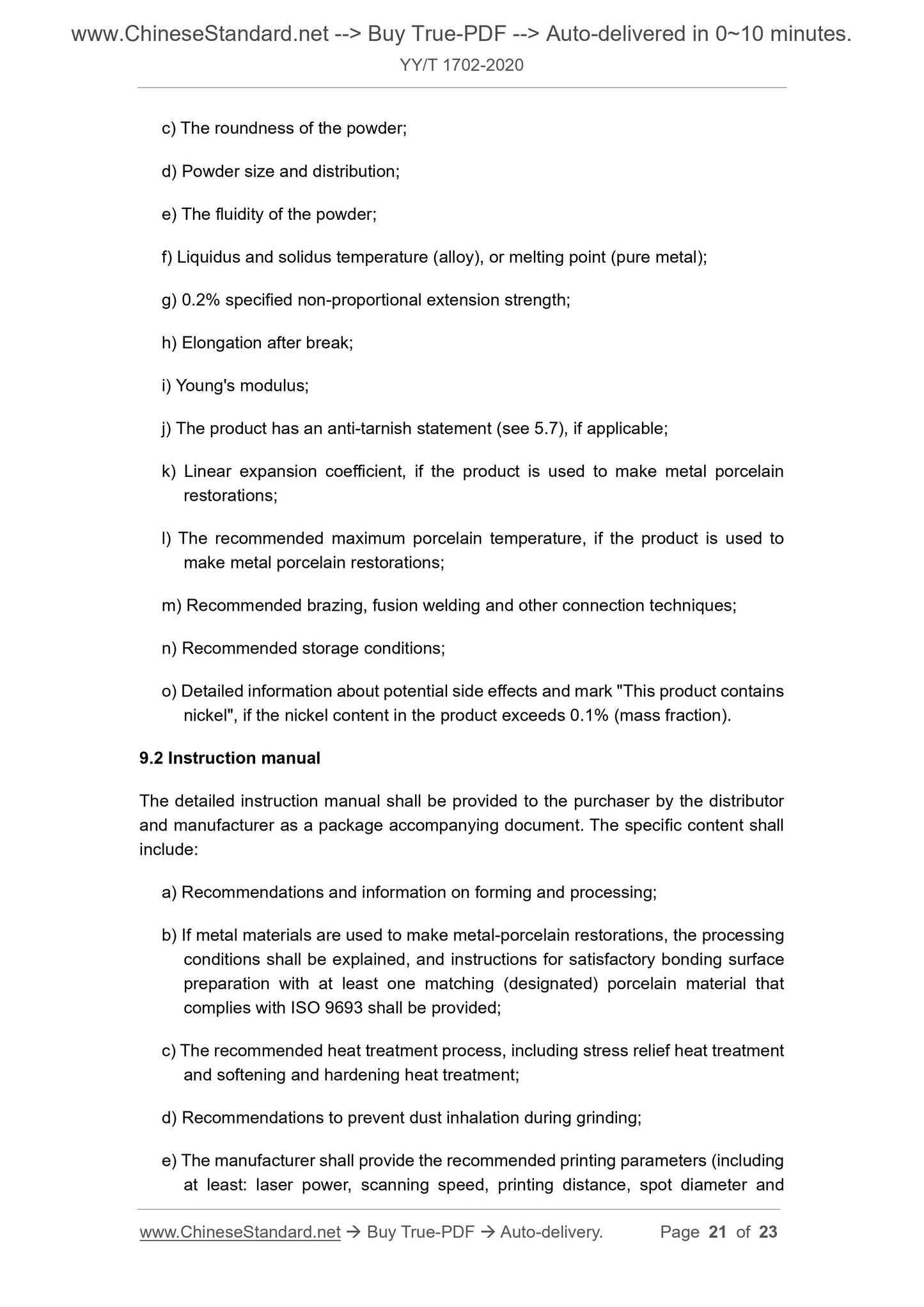